随着世界经济高速发展,煤炭、石油和天然气这些不可再生资源正日渐枯竭,人类社会面临着资源短缺、环境污染等问题。实现氘氚可控聚变能的使用,被认为是解决上述问题的一项关键技术[1-2]。但氚在反应堆内部包层容易泄露,而在包层内壁结构表面制备一层阻氚涂层,是解决该难题的一个有效措施[3-4]。Al2O3涂层具备高的熔点、稳定的化学性质、较高的氚渗透降低因子以及能够自修复涂层中微裂纹等优点[5],是氧化物阻氚渗透涂层中的代表,特别是富含α-Al2O3的涂层,其阻氚性能更优。近年来,Cr2O3和石墨烯等作为添加剂制备阻氚涂层得到了极大的关注。Wallin等[6]研究发现,在基材表面预制备一层Cr2O3,然后在500 ℃下溅射一层Al2O3时,涂层中检测出α-Al2O3和Cr2O3相,而直接溅射一层Al2O3时,涂层中只检测出γ-Al2O3相,证明Cr2O3对α-Al2O3有促进作用。He等[7]通过MOCVD法在316不锈钢表面制备了Al2O3/Cr2O3双复合涂层,通过阻氚实验测试,发现其阻氚渗透降低因子较单层的Al2O3或Cr2O3涂层提高数倍。石墨烯对气体的渗透有着很强的抵御作用[8],杨浩[9]通过溶胶-凝胶法在氧化铝溶液中添加石墨烯,制备出氧化铝/石墨烯复合阻氚涂层,其阻氚性能较单一氧化铝涂层提升数倍。为了获得富含α-Al2O3成分的氧化铝涂层,降低铝合金中Zn元素对α-Al2O3形成的影响,本工作采用1060纯铝作为基材,利用微弧氧化(micro-arc oxidation,MAO)技术原位生长适合复杂形状工件加工、氧化膜结合力好、涂层综合性能优、成膜效率高、工艺简单、生产环保的优势特点[10],通过在微弧氧化电解液中同时添加Cr2O3和石墨烯,在1060纯铝表面制备微弧氧化涂层,研究Cr2O3和石墨烯的共同作用对涂层性能及物相构成的影响,分析影响机理,以期对后续微弧氧化制备核聚变的阻氚涂层提供一定的理论依据和技术储备。
1 实验
1.1 微弧氧化涂层制备
使用线切割将1060纯铝加工成50 mm(直径)×1 mm(厚度)的圆片,以减少强电场环境下尖端放电引起的涂层不均匀现象[
11]。在圆形工件的边缘处打一个直径为2 mm的通孔,用于微弧氧化处理时悬挂试样。1060纯铝化学成分如
表1所示。用丙酮水溶液清洗加工好的标准尺寸试样,去除表面油污,然后用400#的水砂纸打磨平整试样边缘,再依次用600#,1000#,1200#,1500#,2000#的水砂纸逐渐打磨试样表面,最后依次用去离子水和酒精超声清洗试样,吹干备用。
表1 1060纯铝化学成分(质量分数/%)
Table 1 Chemical compositions of 1060 pure aluminum(mass fraction/%)
|
Si |
Fe |
Mg |
Cu |
Mn |
Zn |
V |
Ti |
Al |
≤0.25 |
≤0.35 |
≤0.03 |
≤0.05 |
≤0.03 |
≤0.05 |
≤0.05 |
≤0.05 |
Balance |
采用50 kW双极脉冲微弧氧化设备(核工业西南物理研究院)对试样进行微弧氧化表面处理。微弧氧化装置主要由交流脉冲电源、电解槽和冷却系统组成。采用恒电流模式在1060纯铝表面制备微弧氧化涂层,电流密度为12 A/dm2,频率为500 Hz,占空比为10%,时间为20 min。在微弧氧化过程中,控制电解液的温度不超过35 ℃。实验基础电解液配方为36 g/L Na3PO4,30 g/L (NaPO3)6,25 g/L Li2B4O7和6 g/L Na2WO4。杨涵等[
12]前期对微弧氧化电解液中掺杂石墨烯和Cr2O3的实验研究发现,石墨烯和Cr2O3添加剂的浓度分别为1 g/L和3 g/L较为合适。微弧氧化实验步骤:先将称量好的石墨烯加入到20 mL的异丙醇溶液中,进行30 min的超声分散处理,再添加到基础电解液中,然后把称量好的Cr2O3直接加入到电解液中,混合搅拌30 min,至两种颗粒完全分散在电解液中。实验项目分组如
表2所示。
表2 实验项目分组
Table 2 Grouping of experimental items
|
Sample |
Concentration/(g∙L-1) |
Graphene |
Cr2O3 |
1 |
0 |
0 |
2 |
0 |
3 |
3 |
1 |
0 |
4 |
1 |
3 |
1.2 性能测试及组织观察
采用Gemini 300型扫描电子显微镜(SEM)分析涂层表面微观结构;使用SEM自带的X射线能谱仪对涂层表面的微观区域进行元素与含量分析;采用Smart Lab型X射线衍射仪(铜靶,Kα射线扫描范围为5°~90°,扫描速率为2 (°)/min)分析微弧氧化涂层的相组成;采用ED-300数字型涡流测厚仪测定微弧氧化涂层厚度,精确度为0.01 μm,在试样涂层表面随机选取9个点进行测量,并计算其平均值;采用HV-1000A型维氏硬度计,在试样表面随机选取5个不同位置的点,对涂层的硬度进行测量,并求其平均值,加载力为0.98 N,加载时间为10 s;采用MS-T3001型摩擦磨损试验机测量涂层的耐磨损性能,对磨工件为半径3 mm的GCr15对磨球,实验载荷4.9 N,转速100 r/min,对磨时间30 min,温度为室温;采用CHI-660E电化学仪器,在3.5%(质量分数)的NaCl水溶液中检测样品的动电位极化曲线。实验采用三电极测量体系,试样为工作电极,暴露面积为1 cm2,参考电极为饱和甘汞电极,辅助电极为尺寸10 mm×10 mm的铂电极,扫描速率为0.01 V/s。
2 结果及分析
2.1 微弧氧化涂层形貌和元素分布
图1为在电解液中掺入不同添加剂时在1060纯铝表面所制备的微弧氧化涂层表面微观形貌。结果发现,较大的孔洞(直径d>4 μm,孔径标注见图)类似于“火山口”,其周围布满着大量凸起的熔融“堆积物”,并向四周铺垫。较小的孔洞(直径<2 μm)周围呈现出“盆地”形状,四周高,中间低,且多数的裂纹都是以小孔洞为中心,向四周扩散、延伸。
图1(b),(c)相比
图1(a),涂层表面微孔数量减少,微孔直径处于0~13 μm之间。涂层表面“火山口”状结构数量减少,出现较大面积的平坦区域,存在部分细小的放电微孔。
图1(d)相比图
1(b)和
1(c),涂层表面孔洞直径无明显变化,但微孔数量和涂层表面凸起结构数量减少。这是因为,加入石墨烯可使电解液的电导率升高,涂层两端的加载电压升高,涂层表面放电火花数量急剧增加,导致单个火花放电的持续时间变短、体积变小。火花放电产生的热能仅能熔融部分在涂层与基体截面处形成的新氧化物,导致在涂层表面形成的微孔尺寸变小、数量下降[
13-
15]。另外,纳米Cr2O3颗粒在微弧氧化反应过程中被吸附和填充到涂层微孔中,导致涂层击穿需要更大的反应能量,因此微孔尺寸略微增加、数量减小[
16]。说明Cr2O3和石墨烯混合掺杂与未掺杂、单独掺杂石墨烯或Cr2O3相比,其涂层表面更为致密。
图2为不同电解液添加剂所制备微弧氧化涂层的截面形貌。从
图2(a)可知,微弧氧化涂层和基体紧密嵌合,无明显的断裂现象。
图2(b),(c)为在电解液中单独添加3 g/L Cr2O3和1 g/L石墨烯的涂层截面形貌,与未添加添加剂时相比,添加Cr2O3后涂层截面变得更加致密,而添加石墨烯所制备的涂层截面更加连续。由
图2(d)可以看到,涂层更加致密且连续。
根据4组实验的元素分布结果,发现元素分布没有明显区别,且涂层表面元素分布都较均匀,反映出微弧氧化过程的稳定性。
图3为样品4微弧氧化涂层表面元素分布,可以发现,涂层中主要元素为Al和O,此外还含有少量的Cr和C元素,且4种元素都均匀分布在微弧氧化涂层表面,表明微弧氧化涂层中主要生成物应是Al2O3。证明石墨烯和Cr2O3均参与了微弧氧化成膜过程,并促进了涂层中氧化物的形成。
2.2 微弧氧化涂层物相组成
图4为不同电解液添加剂所制备微弧氧化涂层的物相组成。可知,未添加纳米颗粒制备的微弧氧化涂层的主要成分为α-Al2O3,γ-Al2O3和Al,是典型的铝微弧氧化涂层物相组成结构[
17-
18]。衍射峰Al主要来自铝基体或者涂层中未完全融化的Al[
19],α-Al2O3和γ-Al2O3来自微弧氧化涂层,γ-Al2O3主要存在于膜外层,α-Al2O3主要存在于膜内层,这是由于熔融的氧化铝在涂层内外的冷却速率不同导致的[
20]。在基础电解液中,单独添加1 g/L石墨烯和3 g/L Cr2O3后,微弧氧化涂层中的α-Al2O3和γ-Al2O3相的衍射峰强度都有所增加,证明α-Al2O3和γ-Al2O3在涂层中的含量增多,结晶度较好。石墨烯和Cr2O3均促进微弧氧化涂层中α-Al2O3和γ-Al2O3的生成,但Cr2O3的促进作用明显大于石墨烯。其中在电解液中添加Cr2O3后,存在较弱的Cr2O3衍射峰,说明Cr2O3进入了微弧氧化涂层,但在电解液中添加石墨烯后,并未发现碳物相衍射峰,这可能是涂层中石墨烯含量较少所导致[
11]。在电解液中同时添加石墨烯和Cr2O3后,Al的衍射峰强度明显减弱,α-Al2O3和γ-Al2O3的衍射峰强度更高。这是因为混合掺入石墨烯和Cr2O3后,石墨烯的加入引起加载到涂层两端的电压有所升高,当涂层表面火花数量一定时,单个火花的能量增加,使得火花放电瞬间产生的热能也就越多,涂层中氧化物相的含量相应增加,同时石墨烯颗粒作为第二相离子,促进了晶体的形核过程[
21]。Cr2O3和α-Al2O3具有相同的晶体结构,可以在低温条件下为α-Al2O3的形成提供模板,稳定促进α-Al2O3的生成[
22]。同时添加石墨烯和Cr2O3对促进α-Al2O3和γ-Al2O3的生成,较单一添加石墨烯或Cr2O3更好,微弧氧化涂层变得更厚且致密。
2.3 微弧氧化涂层厚度
图5为不同电解液添加剂所制备微弧氧化涂层的厚度。可以看到,在电解液中单独添加石墨烯,Cr2O3以及同时添加石墨烯和Cr2O3都能促进微弧氧化涂层厚度的增加,其涂层厚度分别为22.8,24.7 μm和25.3 μm,较未添加时涂层厚度明显增加。研究表明,混合掺杂对促进涂层厚度的增长效果最明显,其次是浓度为3 g/L的Cr2O3,最后是浓度为1 g/L的石墨烯。这是因为,石墨烯的加入使电解液中移动的粒子数目增多,增强了溶液的电导率,促进微弧氧化反应,使微弧氧化涂层的厚度增长。Cr2O3可在微弧氧化反应过程中被吸附、沉积到涂层中,在微弧氧化产生的高温下[
23],一部分Cr2O3将与氧化物发生共融,冷却后形成涂层,另一部分Cr2O3将被熔融的氧化物包裹,冷却凝固后成为涂层的一部分。
2.4 微弧氧化涂层表面硬度和耐磨性
图6为不同电解液添加剂所制备微弧氧化涂层的硬度。可以看出,随着不同添加剂的加入,所制备微弧氧化涂层的硬度均显著提高。未加入添加剂所制备微弧氧化涂层的平均硬度为448.83HV,单独添加石墨烯所制备涂层的平均硬度为533.59HV,单独添加Cr2O3颗粒所制备涂层的平均硬度为709.73HV,同时添加石墨烯和Cr2O3所制备涂层的平均硬度为763.01HV。
微弧氧化涂层的硬度与涂层的组织结构和物相组成密切相关,其中涂层的物相组成起着主导性作用。结合
图4涂层的物相组成分析可知,未添加纳米颗粒所制备的涂层中,α-Al2O3在涂层中的含量较低,涂层硬度值较小。分别在电解液中单独加入石墨烯和Cr2O3后,均能促进α-Al2O3的形成,涂层硬度明显提高。当在电解液中混合加入石墨烯和Cr2O3后,α-Al2O3的含量进一步提升,涂层硬度值达到最大值763.01HV。
图7为不同电解液添加剂所制备微弧氧化涂层的摩擦因数。可以看出,4种微弧氧化涂层的摩擦因数随时间的变化趋势基本相同,均为先升高后降低,最后缓慢上升至平稳阶段。磨损的初始阶段摩擦因数迅速增加,这是因为微弧氧化疏松层被破坏。当涂层的疏松层被磨穿之后,含有硬质相的内层与对磨球相接触,摩擦因数开始进入稳定阶段。可知,未添加添加剂时,涂层平均摩擦因数为0.5377。这是因为,此时微弧氧化涂层具有较多的孔洞,α-Al2O3含量较低且涂层结构较疏松,耐磨性较差。当分别加入石墨烯和Cr2O3后,平均摩擦因数分别减小至0.5150和0.5067,涂层表面受损程度降低。而同时添加石墨烯和Cr2O3后,平均摩擦因数为0.4781,达到最低。这是因为,石墨烯和Cr2O3都能够促进α-Al2O3的提升,使涂层硬度提高,且均能填补涂层表面孔洞,涂层变得更加致密。研究表明,同时添加石墨烯和Cr2O3后涂层的耐磨性能更优。
2.5 微弧氧化涂层耐腐蚀性
动电位极化曲线表示的是电极电位与极化电流或极化电流密度之间的关系曲线。利用极化曲线能够解释腐蚀现象和分析金属材料的电化学耐腐蚀性能,也能够反映材料的致密性和使用寿命。自腐蚀电流密度表示材料腐蚀的速率,自腐蚀电位表示材料腐蚀的倾向性,通过对两者的分析可直观反映出材料的耐腐蚀性能。
图8为不同电解液添加剂所制备微弧氧化涂层在3.5%NaCl溶液中的动电位极化曲线。根据动电位极化曲线拟合结果,其相关电参数如
表3所示。极化电阻R corr可由Stern-Geary公式[
24](
式(1))确定:
(1)
式中:β a和β b为阳极和阴极的Tafel斜率,V;I corr为腐蚀电流密度,A·cm-2。1060铝基材的自腐蚀电位为-0.285 V,自腐蚀电流密度为3.128×10-8 A·cm-2。在电解液中未添加纳米颗粒、单独添加3g/L Cr2O3、单独添加1 g/L石墨烯和同时添加3 g/L Cr2O3和1 g/L石墨烯所制备的微弧氧化涂层的自腐蚀电位分别为-0.237,-0.188,-0.251 V和-0.185 V。可以发现,经过微弧氧化处理后,微弧氧化涂层的自腐蚀电位都比基材大,表明微弧氧化涂层发生腐蚀的倾向性小;从腐蚀电流密度方面分析,未添加纳米颗粒所制备的微弧氧化涂层,虽然其腐蚀电位比基体高,但是自腐蚀电流密度(5.641×10-8 A·cm-2)却较基材低。这是因为,经过微弧氧化处理后,微弧氧化涂层表面存在较多的孔洞等缺陷,影响涂层的耐腐蚀性能。在电解液中单独添加3 g/L Cr2O3、单独添加1 g/L石墨烯和同时添加3 g/L Cr2O3和1 g/L石墨烯所制备微弧氧化涂层的自腐蚀电流密度分别为2.356×10-9,1.294×10-8 A·cm-2和1.095×10-9 A·cm-2,涂层的耐腐蚀能力得到提升。可以得出,在电解液中同时添加Cr2O3和石墨烯所制备的微弧氧化涂层自腐蚀电位最大,为-0.185 V,自腐蚀电流密度最小,为1.095×10-9 A·cm-2,涂层的抗腐蚀能力最好。这是因为,Cr2O3本身也具备一定的防腐蚀能力,结合物相组成分析,当在电解液中添加Cr2O3颗粒后,能够极大地促进α-Al2O3在纯铝微弧氧化涂层中的生成,而α-Al2O3是氧化铝家族中的最稳定相,具有优良的耐腐蚀能力。石墨烯是一种具有单原子、单层石墨层的二维材料,本身具有良好的疏水性和抗渗透性,是一种优良的防腐蚀材料[
25]。在电解液中添加石墨烯后,石墨烯会被熔融的氧化物包裹,冷却凝固后存在微弧氧化涂层中,提高了微弧氧化涂层的耐腐蚀能力。综上所述,在石墨烯和Cr2O3的共同作用下,微弧氧化涂层的耐腐蚀能力最佳。
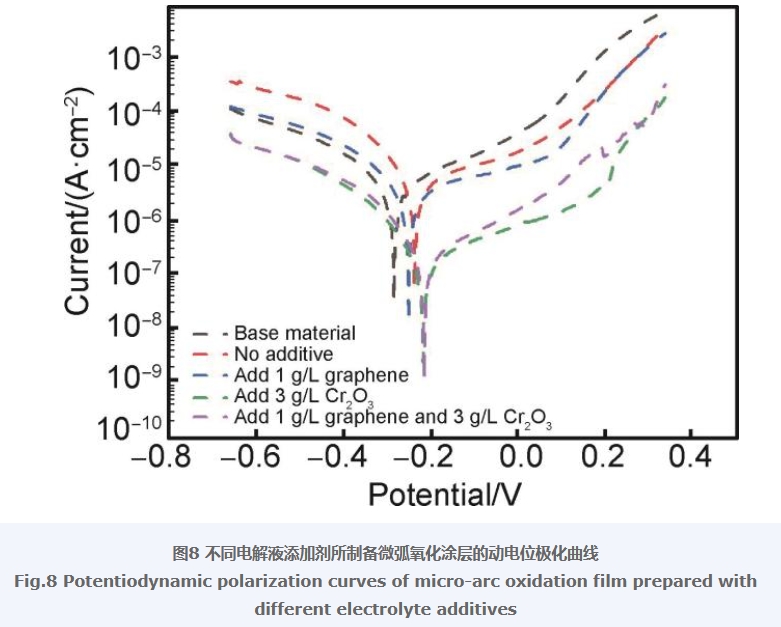
表 3 1060基体和微弧氧化涂层动电位极化曲线拟合结果
Table 3 Fitting results of potentiodynamic polarization curves of 1060 matrix and micro-arc oxidation film
|
Sample |
E corr/V |
I corr/(A·cm-2) |
β a/V |
β b/V |
R corr/(Ω·cm2) |
Base material |
-0.285 |
3.128×10-8 |
0.227 |
0.165 |
1.326×106 |
No additive |
-0.237 |
5.641×10-8 |
0.332 |
0.125 |
6.99×105 |
Add 1 g/L graphene |
-0.251 |
1.294×10-8 |
0.350 |
0.147 |
3.473×106 |
Add 3 g/L Cr2O3 |
-0.188 |
2.356×10-9 |
0.235 |
0.111 |
1.389×107 |
Add 1 g/L graphene and 3 g/L Cr2O3 |
-0.185 |
1.095×10-9 |
0.260 |
0.112 |
3.104×107 |
3 结论
(1)在基础电解液中同时添加3 g/L Cr2O3和1 g/L石墨烯所制备的微弧氧化涂层相比于单独在电解液中添加石墨烯或Cr2O3所制备的涂层孔径减小,孔和裂纹数量减少,涂层更加致密,涂层中α-Al2O3和γ-Al2O3的占比及涂层厚度、硬度得到提高,耐磨损性能更优,其涂层厚度最大为25.3 μm,硬度最大为763.01HV,平均摩擦因数最低为0.4781。
(2)在3 g/L Cr2O3和1 g/L石墨烯的共同作用下涂层自腐蚀电位为-0.185 V,自腐蚀电流密度为1.095×10-9 A·cm-2,涂层的耐腐蚀能力较未添加纳米颗粒和单一添加纳米颗粒的涂层显著提升。
(3)混合掺杂石墨烯和Cr2O3所制备的微弧氧化涂层表面形貌、硬度、α-Al2O3在涂层中的含量、耐磨性以及耐腐蚀性均比未掺杂或单独掺杂石墨和Cr2O3较好,基本上满足阻氚涂层的服役要求,证明微弧氧化掺杂制备阻氚涂层的可行性。