近年来,随着国内航空业的迅猛发展,航空燃料的需求量与日俱增,航油管道建设也得到快速发展。作为航油供应的大动脉,航油管道肩负着从炼厂或码头到机场油库、机坪的航油输送任务。L360管线钢因其强度高、韧性好和耐腐蚀等特点,目前已广泛应用于新建机场项目配套的航油管道工程中。然而,复杂的沿线环境往往会引起航油管道腐蚀、失效,造成巨大的经济损失和生态破坏。在工程应用中,杂散电流、漏磁检查、发电机、电磁阀和各种地下电器均可引起复杂磁场,航油管道不可避免地会处于磁场环境中[1]。研究表明,常见的电磁设备会加速周围材料的腐蚀[2]。磁悬浮列车在管道交叉点附近产生约0.08 mT的弱磁场,该磁场明显加速了管线钢的腐蚀[3]。管道上方的高压电线会在埋地金属管道中诱发磁场,能影响埋地管道的电化学特性,并加速管道的腐蚀[4]。作为油气管道缺陷的主要检测手段,漏磁检测利用永磁铁、电磁铁等对管道施加外磁场进行饱和磁化[5]。其剩余磁场将在管道中保留数小时至数周[6]。复杂磁场的存在会影响埋地管道的腐蚀行为。
目前,关于外部环境磁场对金属腐蚀行为的影响尚未得到统一的结论。相关研究表明[7, 8],施加的均匀静态磁场会引起金属的腐蚀电位发生变化,腐蚀电流密度降低,金属表面形成的凹坑减少,金属腐蚀得到抑制。Obi等[9]研究表明外加电磁铁提供的磁场使低碳钢在酸性溶液中的腐蚀速率降低,且磁场对低碳钢腐蚀的保护效率随外加磁场的增大而增大,磁场的腐蚀防护机制主要归因于横向磁阻现象。姜超和马保吉[10]研究表明平行磁场作用会抑制低浓度NaCl溶液中的AZ31B镁合金腐蚀速率,增大高浓度NaCl溶液中AZ31B镁合金腐蚀速率。Hu等[11]研究表明平行磁场改变了铍铜腐蚀产物中氧的表面形态和分布,磁场作用加速了低浓度NaCl溶液中的腐蚀过程,抑制了高浓度NaCl溶液中的腐蚀过程。有些研究报告[12~14]结果则不尽相同,通过永磁铁引入的外部磁场加速了管线钢的腐蚀,且随着磁场强度的增加,腐蚀速率逐渐增大,表面表现出更加均匀的腐蚀。相同的磁场强度下,平行磁场对腐蚀的影响明显大于垂直磁场。杨永等[15, 16]通过自制的圆环状电磁铁模拟油气管道漏磁检测后的残余磁场,研究表明在3.5% (质量分数)NaCl溶液和模拟鹰潭土壤溶液中,磁场产生的Lorentz力对腐蚀的促进作用大于Kelvins力对腐蚀的抑制作用,总体上促进了电化学腐蚀。以上研究结果表明,不同方向、强度的磁场对特定金属在不同环境中腐蚀行为的影响不尽相同。磁场对管线钢及其焊接接头腐蚀行为的影响的研究有限,有必要进行深入研究。
本文以极化曲线、电化学阻抗谱(EIS)等传统的电化学测试方法结合宏观、微观腐蚀形貌分析,研究了磁场对3.5%NaCl溶液中L360管线钢母材及其焊接接头腐蚀行为的影响,并探讨了磁场对腐蚀影响的机理。
1 实验
实验材料选取现场用L360输油管道,尺寸为ϕ219 × 6 mm,L360管线钢化学成分(质量分数,%)为:C0.12,Mn 1.50,Si 0.25,Mo 0.02,Cr 0.07,Cu 0.08,Ni 0.04,余量Fe。管道焊接方式为钨极惰性气体保护焊,焊丝选用ER50-6,焊条选用J506。通过线切割方式将管道加工成10 mm × 10 mm × 2 mm的母材(BM)及其焊接接头(WJS)片状试样电极,工作面积为1 cm2。试样电极焊接铜导线,除工作面外其余部分使用环氧树脂封装。封装定型后,依次使用400、600、800、1200和2000#砂纸逐级打磨试样电极表面,并用1 μm的金刚砂抛光。最后使用丙酮去除油脂、无水乙醇脱水,冷风吹干后放干燥箱内备用。
用分析纯试剂和去离子水配置3.5%NaCl标准溶液作为实验介质,实验温度保持在室温,试样电极工作面垂直浸泡于溶液中。
实验装置如图1所示,使用亚克力板加工成电化学实验用电解池,电解池顶部盖板预留工作电极、参比电极、辅助电极以及高斯计探头的测量孔,外部使用镀锌铁皮作为屏蔽罩,避免磁场干扰。采用市面常见N52钕铁硼永磁铁引入磁场,通过改变磁铁的距离以及增加磁铁个数来设置不同大小的磁场强度(0、60、120 mT),并每日通过高斯计测量磁场强度,确保磁场强度的准确性。在电化学测试过程中,保持磁感线与工作电极金属表面方向垂直。
图1
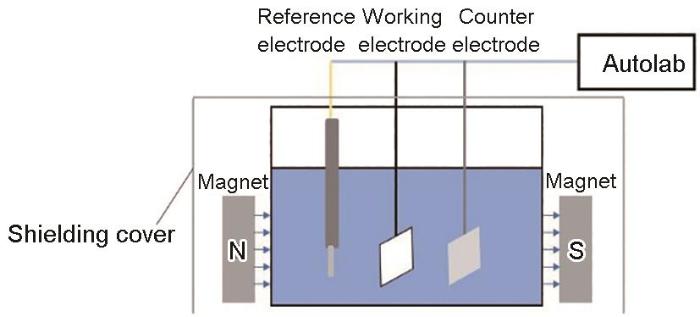
图1 实验装置图
Fig.1 Experimental device diagram
本实验使用Autolab PGSTAT302N电化学工作站进行电化学测试,L360管线钢母材及其焊接接头作为工作电极,饱和甘汞作为参比电极,铂片作为辅助电极,构建传统的三电极测试体系。首先对L360管线钢母材及其焊接接头制备的工作电极进行2000 s开路电位(OCP)测试,待OCP稳定后进行EIS测试,设置10 mV的正弦波信号为激励信号,扫描频率区间为105~10-2 Hz。实验最后进行极化曲线测试,扫描速率为0.5 mV/s,扫描范围为EOCP ± 100 mV。通过NOVA2.0软件对电化学测试数据进行拟合,得到对应电化学参数。
电化学测试完成后,用去离子水及无水乙醇对试样电极进行冲洗,放干燥箱内烘干。使用体式显微镜和扫描电镜(SEM, Phenom Particle XL)观察试样电极去除腐蚀产物前后的宏观形貌和微观形貌,采用自带能谱仪(EDS)分析腐蚀产物的元素组成及含量。采用化学清洗方法去除试样电极表面腐蚀产物,除锈液为500 mL盐酸(ρ = 1.19 g/mL),3.5 g六次甲基四胺,加蒸馏水至1000 mL配制而成[17]。
2 结果与讨论
2.1 极化曲线
图2为不同磁场强度下L360管线钢及焊接接头的极化曲线。由图可见,不同磁场强度下,L360管线钢母材及其焊接接头极化曲线的阳极、阴极分支基本不变,这说明磁场强度对母材及其焊接接头电极反应过程的影响基本相同;L360管线钢母材及其焊接接头极化曲线的形状相似,表明母材及其焊接接头腐蚀过程基本一致。阳极区以活性溶解为主,未见明显钝化。极化曲线可拟合得到不同磁场强度下的腐蚀电流和腐蚀电位,通常二者之间没有必然联系。腐蚀电位仅表示热力学性能,其无法准确反映出L360管线钢母材及其焊接接头在3.5%NaCl标准溶液的腐蚀规律。从图中可以看到母材和焊接接头处于120 mT磁场作用时腐蚀电位最正,其后依次是0和60 mT。
图2

图2 不同磁场强度下L360管线钢母材及焊接接头在3.5%NaCl水溶液中的极化曲线
Fig.2 Polarization curves of L360 pipeline steel in 3.5%NaCl solution under 0-120 mT magnetic fields: (a) BM, (b) WJS
本文主要围绕极化曲线的腐蚀电流密度及腐蚀速率分析L360管线钢母材及其焊接接头腐蚀行为。通过Tafel外推法拟合,得到不同磁场强度下L360管线钢母材及其焊接接头的电化学参数如表1所示。由表可知,阳极极化曲线的Tafel斜率(βa)小于阴极极化曲线的Tafel斜率(βc),说明腐蚀控制过程为阴极反应。试样电极的腐蚀电流密度与腐蚀速率成正相关。图3为不同磁场强度下L360管线钢母材及焊接接头的腐蚀速率。由图可知,L360管线钢母材在0、60和120 mT磁场强度下的腐蚀速率分别为0.09404、0.08356和0.09811 mm/a,焊接接头的腐蚀速率分别为0.09875、0.08933和0.10732 mm/a。随着磁场强度增大,母材及焊接接头的腐蚀速率均呈现先减小后增大的趋势,磁场的存在影响着微观层面的电化学腐蚀情况。在120 mT时,母材及焊接接头的腐蚀速率均达到最大,说明磁场能对二者的腐蚀起到一定促进作用;相同磁场强度下,焊接接头腐蚀速率均大于母材。相关研究表明,由于Fe、亚铁离子的磁矩不同,引入外部磁场会产生使亚铁离子吸附界面的力,抑制基体Fe的溶解;同时,亚铁离子作为铁磁性离子会降低水合作用,使其产生解吸界面力,加速基体Fe的溶解。Fe基体是否加速腐蚀溶解取决于这两种力的竞争结果[18]。
图3
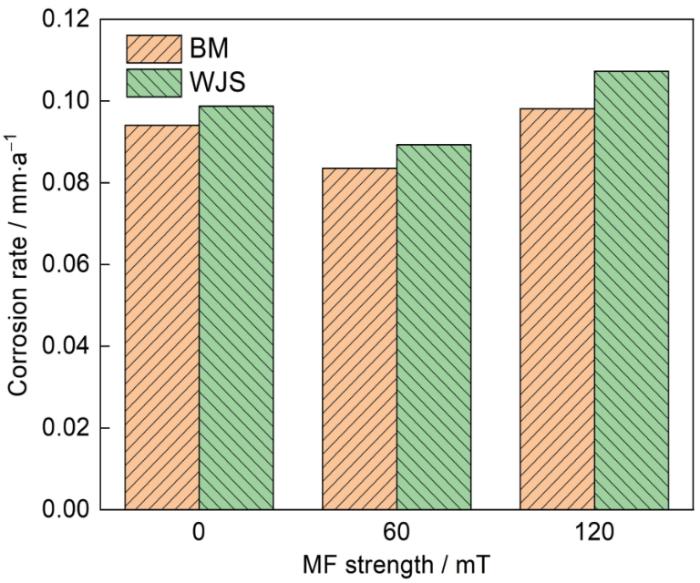
图3 不同磁场强度下L360管线钢母材及焊接接头在3.5%NaCl水溶液中的腐蚀速率
Fig.3 Corrosion rates of BM and WJS for L360 pipeline steel in 3.5%NaCl solution under different magnetic fields
2.2 电化学阻抗谱
图4为不同磁场强度下L360管线钢母材及焊接接头的EIS。由图可见,不同磁场强度下,L360管线钢母材及焊接接头的阻抗谱均为单一容抗弧,表明3.5%NaCl溶液中的腐蚀性离子受到的扩散阻力较小。随着磁场强度的增大,母材及焊接接头的容抗弧半径均呈现先增大后减小的趋势,反应体系阻力先增大后减小,即母材及焊接接头的腐蚀倾向先减小后增大。
图4
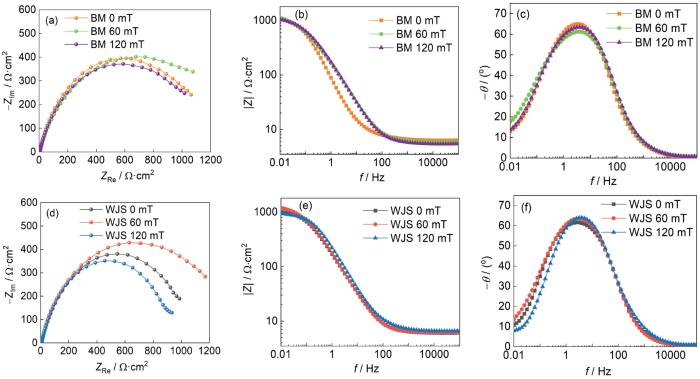
图4 不同磁场强度下L360管线钢母材及焊接接头的电化学阻抗谱
Fig.4 Nyquist (a, d), impedance module (b, e) and phase angle (c, f) plots of BM (a-c) and WJS (d-f) for L360 pipeline steel under different magnetic fields
用图5所示等效电路对不同磁场强度下L360管线钢母材及焊接接头的电化学阻抗谱进行拟合,拟合结果见表2。其中,Rs表示溶液电阻,Rct表示电荷转移电阻,CPE表示双电层电容,n为弥散系数(0 < n < 1)。n反映弥散效应强弱,n越接近于0表明弥散效应越明显,n越接近1表明体系越接近理想电容,由表可知该等效电路适合用于拟合该腐蚀体系的阻抗谱[19]。随着磁场强度的增大,L360管线钢母材及焊接接头的Rct均先增大后减小;当磁场强度为60 mT时,母材及焊接接头的Rct最大;120 mT时,Rct最小。这说明60 mT时,二者的腐蚀速率均达到最小值;120 mT时,均达到最大值。母材及焊接接头整体均呈现出先减小后增大的腐蚀倾向趋势。EIS分析与极化曲线得到的结果一致。
图5
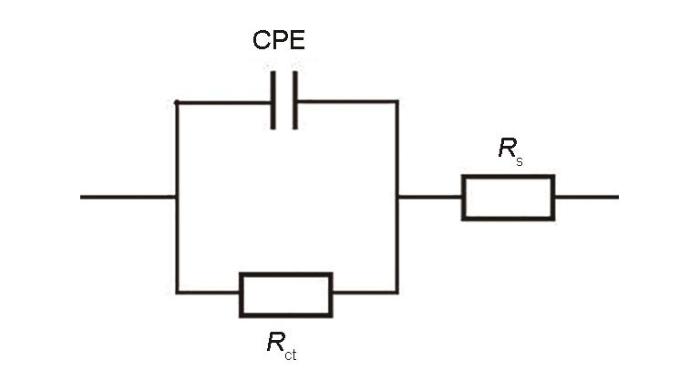
图5 等效电路图
Fig.5 Equivalent circuit diagram
2.3 宏观形貌
图6为不同磁场强度下L360管线钢母材及焊接接头试样去除腐蚀产物前的宏观形貌。由图可见,腐蚀产物明显分为黑色内锈层和表面的棕黄色锈层,黑色内锈层附着能力较强,难以去除,其紧密结合在试样电极的基体上,致密性、完整性均优于棕黄色锈层;试样电极基体上方的棕黄色锈层疏松多孔,未与基体紧密结合,容易脱落。相同磁场强度下,焊接接头试样电极表面的腐蚀产物明显多于母材,说明焊接接头更易腐蚀。随着磁场强度增大,母材及焊接接头试样电极表面的棕黄色腐蚀产物呈现先减少后增多的趋势,60 mT时棕黄色腐蚀产物最少,且黑色锈层均匀、致密覆盖在试样电极表面。0和120 mT磁场强度作用下的试样电极表面主要被棕黄色腐蚀产物覆盖,分布欠均匀,且部分已出现脱落现象。
图6

图6 不同磁场强度下L360管线钢母材及焊接接头试样宏观腐蚀形貌
Fig.6 Macroscopic morphologies of BM (a-c) and WJS (d-f) samples after corrosion under magnetic fields of 0 mT (a, d), 60 mT (b, e) and 120 mT (c, f)
图7为不同磁场强度下L360管线钢母材及焊接接头试样去除腐蚀产物后的宏观形貌。由图7a~c可见,无磁场作用时母材试样表面基本呈现均匀腐蚀,未出现明显的局部腐蚀现象,其表面腐蚀坑数量相对60 mT磁场作用下的母材试样较多,且腐蚀坑面积相对较大;120 mT时母材试样表面腐蚀坑数量最多和腐蚀坑面积最大。由图7d~f可见,无磁场作用下焊接接头试样相对60 mT磁场作用下的试样表面腐蚀坑数量更多、腐蚀坑面积更大,60 mT磁场作用下的焊接接头试样表面仅有零星分布的点蚀,腐蚀面积最小;120 mT磁场作用下,焊接接头试样表面呈现成片连接的腐蚀坑,腐蚀面积最大。通过比较相同磁场强度下的宏观腐蚀形貌,焊接接头试样表面的腐蚀坑数量、面积明显大于母材试样。随着磁场强度的增大,母材及焊接接头试样表面的腐蚀程度呈现先减小后增大的趋势。宏观形貌分析结果与电化学分析一致。
图7
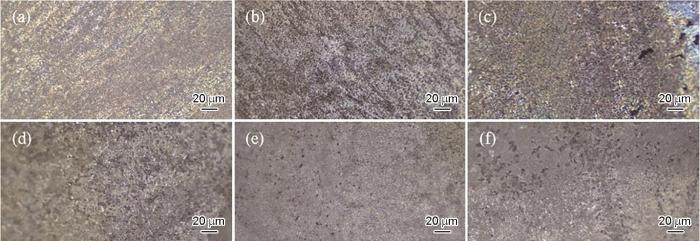
图7 不同磁场强度下L360管线钢母材及焊接接头试样去除腐蚀产物后的宏观形貌
Fig.7 Macroscopic morphologies of BM (a-c) and WJS (d-f) for L360 pipeline steel after removal of corrosion products formed under different magnetic fields of 0 mT (a, d), 60 mT (b, e) and 120 mT (c, f)
2.4 微观形貌
图8为不同磁场强度下L360管线钢母材及焊接接头试样去除腐蚀产物前的微观形貌。由图可知,无磁场作用时,母材及焊接接头试样表面未形成完整、致密的腐蚀产物膜,腐蚀产物多为疏松多孔结构,腐蚀性离子可以轻易渗入到试样基体表面造成基体腐蚀溶解;60 mT时,母材及焊接接头试样表面的腐蚀产物分层明显,底层的腐蚀产物膜均匀覆盖在试样基体表面,且未见明显的裂纹,致密度、完整性良好的腐蚀产物膜对试样基体起到有效保护,一定程度上避免了氯离子等腐蚀性离子接触到试样基体表面,抑制了母材及焊接接头试样的腐蚀;120 mT时,母材及焊接接头试样表面的腐蚀产物膜产生了明显的裂纹,相关研究表明这是由于磁场能够使单个氧化物晶粒沿择优取向生长,导致试样表面的产物膜发生破损和偏移[13]。腐蚀性离子可通过裂纹渗入到试样基体表面,从而引起试样进一步腐蚀。腐蚀产物膜的完整性遭到损坏,其对试样基体的保护作用随之下降,这说明增大到一定强度后的磁场会抑制完整腐蚀产物膜的形成,进而影响腐蚀过程。
图8
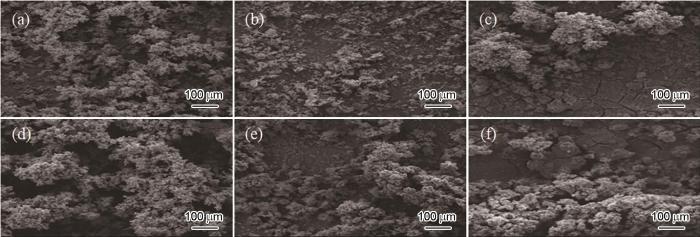
图8 不同磁场强度下L360管线钢母材及焊接接头试样去除腐蚀产物前的微观形貌
Fig.8 Microscopic morphologies of BM (a-c) and WJS (d-f) for L360 pipeline steel after corrosion under magnetic fields of 0 mT (a, d), 60 mT (b, e) and 120 mT (c, f)
图9为不同磁场强度下L360管线钢母材及焊接接头试样去除腐蚀产物后的微观形貌。由图9a~c可见,无磁场作用的母材试样相对60 mT磁场作用下的试样表面分布有更多的点蚀坑,60 mT时腐蚀程度最小;120 mT时,母材试样表面的点蚀坑明显增多,点蚀坑面积增大且呈现出成片连接的趋势。由图9d~f可见,无磁场作用时,焊接接头试样表面分布较多较大的点蚀坑,且开始出现聚集相连,表面腐蚀程度较大;60 mT时,焊接接头试样表面仅有零星分布的点蚀坑,腐蚀程度最小;120 mT时,焊接接头试样腐蚀明显最严重,点蚀区域最大,点蚀坑连接成片。通过比较相同磁场强度下的微观腐蚀形貌,母材试样腐蚀程度小于焊接接头。去除腐蚀产物后的微观形貌分析结果与前文分析得出的结论一致。
图9
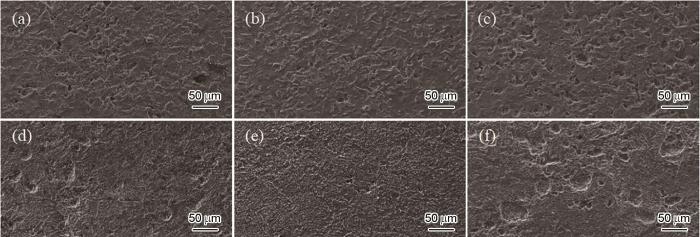
图9 不同磁场强度下L360管线钢母材及焊接接头试样去除腐蚀产物后的微观形貌
Fig.9 Microscopic morphologies of BM (a-c) and WJS (d-f) for L360 pipeline steel after removal of corrosion products formed under magnetic fields of 0 mT(a, d), 60 mT (b, e) and 120 mT (c, f)
2.5 腐蚀产物分析
图10为不同磁场强度下L360管线钢母材及焊接接头腐蚀产物膜的EDS分析结果。由分析结果可以看出,在点蚀坑及平整处,腐蚀产物均以Fe的氧化物为主。随着磁场强度的增大,母材及焊接接头试样表面的腐蚀产物中Fe的质量分数先增大后减小,氧的质量分数先减小后增大,即Fe的氧化物占比先减小后增大,60 mT时占比最少,120 mT时占比最多。这表明L360管线钢母材及焊接接头试样的阳极溶解随着磁场强度的增大呈现先减小后增大的趋势。为了更好地研究较高强度磁场作用下L360管线钢及焊接接头腐蚀产物的化学成分,利用XPS获得腐蚀产物的Fe 2p光谱。图11为120 mT磁场下L360管线钢及焊接接头腐蚀产物的XPS分析光谱。由图可知,在710.2和712.3 eV处的峰分别对应Fe3O4和FeOOH[20]。Fe的拟合结果表明,母材及焊接接头的腐蚀产物主要以Fe3O4和FeOOH的形式存在。这一结果也印证了电化学测试及形貌分析得到的结论。
图10
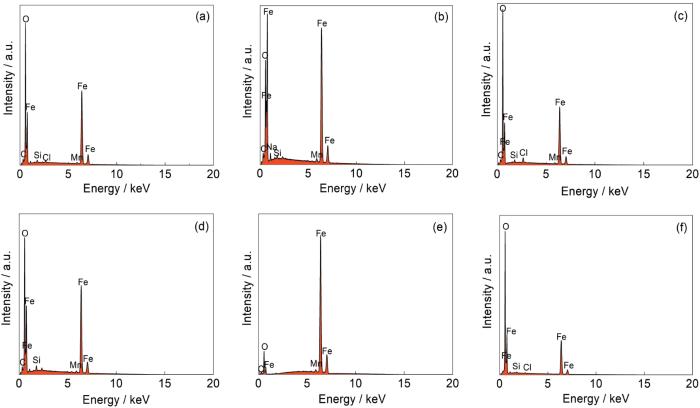
图10 腐蚀产物膜的EDS分析结果
Fig.10 EDS analysis results of corrosion product layers formed on BM (a-c) and WJS (d-f) under magnetic fields of 0 mT (a, d), 60 mT (b, e) and 120 mT (c, f)
图11
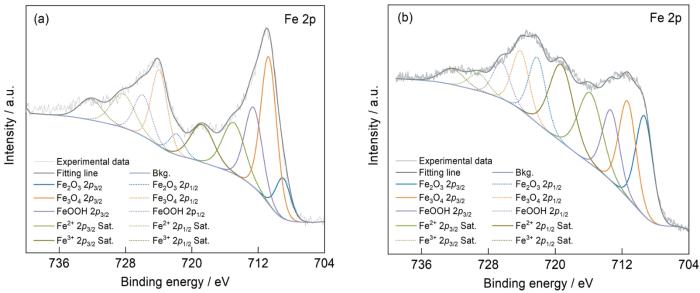
图11 腐蚀产物的XPS分析
Fig.11 XPS analysis results of corrosion products formed on BM (a) and WJS (b) under magnetic field of 120 mT
3 机理分析
在无磁场作用时,L360管线钢母材及焊接接头试样的腐蚀产物中以棕黄色的FeOOH为主,FeOOH为疏松多孔状结构[23]。外加磁场作用下,在试样与溶液界面会产生磁场梯度力和Lorentz力[24~26]。在磁场梯度力对Fe2+的集聚作用下,加速反应生成的腐蚀产物Fe(OH)2附着在试样表面,并在O2充足条件下缓慢生成更为稳定的Fe3O4[23]。当腐蚀产物的溶解与沉积平衡后,形成的黑色Fe3O4腐蚀产物膜稳固结合在试样表面,此时试样的腐蚀速率趋于稳定,其在一定程度上抑制了腐蚀的进行。磁场强度增大,Lorentz力也相应增大,其产生的涡流加速靠近基体的Fe2+等金属离子扩散或破坏腐蚀产物膜的完整性,即Lorentz力抑制完整腐蚀产物膜的形成,加速试样腐蚀。
不同磁场强度下,磁场梯度力和Lorentz力对试样腐蚀的影响程度不同。60 mT时,磁场梯度力加速腐蚀产物膜形成,且Lorentz力未对腐蚀产物膜造成明显破坏,试样腐蚀被抑制,腐蚀电流密度减小,腐蚀速率下降;随着磁场强度增大到120 mT,Lorentz力产生的涡流也随之增大,导致腐蚀产物膜出现明显裂纹、脱离界面,并加速Fe2+等顺磁性离子扩散到腐蚀介质中,此时试样腐蚀增强,腐蚀电流密度增大,腐蚀速率上升。由于化学成分、冶金结构和焊接结构内残余应力水平的变化,焊接接头较母材更易腐蚀[27]。
4 结论
(1) 在3.5%NaCl溶液中,随着磁场强度增大,L360管线钢母材及其焊接接头的腐蚀速率均呈现出先减小后增大的趋势。
(2) 磁场对L360管线钢母材及其焊接接头的腐蚀影响程度不同。相同磁场强度下,焊接接头的腐蚀速率大于母材,焊接接头具有更强的腐蚀敏感性。
(3) 磁场对L360管线钢电化学反应过程的影响由多因素综合决定。磁场梯度力诱导金属离子吸附于电极界面,形成腐蚀产物膜阻碍腐蚀的进行。当磁场强度增大到一定程度,Lorentz力能够破坏腐蚀产物膜的形成,加速离子扩散,进而加速金属腐蚀。
免责声明:本网站所转载的文字、图片与视频资料版权归原创作者所有,如果涉及侵权,请第一时间联系本网删除。
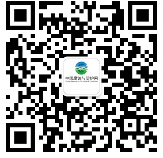
官方微信
《腐蚀与防护网电子期刊》征订启事
- 投稿联系:编辑部
- 电话:010-62316606
- 邮箱:fsfhzy666@163.com
- 腐蚀与防护网官方QQ群:140808414