元素 | C | Si | Mn | P | S | Cr+Ni+Cu+Mo |
---|---|---|---|---|---|---|
质量分数/% | ≤0.150 | ≤0.500 | ≤1.50 | ≤0.010 | ≤0.010 | ≤2.0 |
与普通碳钢相比,耐候钢最突出的优点就是可以裸装使用,这不仅可以降低装涂的费用而且具有环保优势。现有研究表明,稳定的耐候钢表面锈层主要由连续致密的内锈层和疏松多孔的外锈层组成,其耐蚀性主要源自合金元素富集和致密的内锈层[1-8]。但是耐候钢要完成锈层的稳定化需要3~10 a以上的时间,在形成稳定化锈层之前,常常出现早期锈液流挂与飞散污染周围环境的现象[9-13]。锈层的稳定化处理是指耐候钢在使用之前对其表面进行化学转化膜涂装和特种有机涂层预处理,解决耐候钢在锈层稳定化初期产生的锈液流挂和飞散等问题,短期内促进表面稳定致密锈层的形成。表面涂膜预处理技术的核心是涂膜具有一定的透气性,加速形成稳定致密锈层后涂膜易于自风化和自消失性,不对锈层长期稳定产生进一步的负面影响。
目前国内外针对耐候钢表面锈层的稳定化处理研究工作主要有氧化物涂膜处理[14]、耐候性膜处理[15]、氧化铁-磷酸盐系处理[16-19]和新型无铬表面稳定化处理等[20-21]。有研究表明,锈层中α与γ*(α为α-FeOOH的含量,γ*为Fe3O4、γ-FeOOH、β-FeOOH的总含量)的比值与钢的腐蚀速率密切相关,在工业大气环境中,当锈层中α/γ*>1时,腐蚀速率小于0.01 mm/a,因此该比值可用于评估锈层的防护性能[22]。虽然以上技术对耐候钢锈层起到一定的稳定化效果,但这些处理技术仍存在操作工艺复杂,处理成本过高等诸多不足,例如需要多歩工序处理和高温固化,或固化时间过长难以在实际现场施工。目前国内还没有开发出成熟的能够工程化应用的耐候钢表面锈层稳定化处理技术[23]。因此,笔者结合以上问题,又考虑到Mo具有绿色无污染且可以生成难溶性氧化物的特点,开发了一种环境友好、效果优良、成本低廉、工艺简单且适合现场使用的锈层稳定剂(该稳定剂以钼酸钠作为促进剂,以水性聚氨酯作为成膜剂),并采用实验室模拟大气腐蚀试验,研究了该锈层稳定剂装涂后耐候钢的腐蚀行为和涂层防护机理。
1. 试验
1.1 材料与试样
采用首钢集团有限公司生产的厚28 mm的SQ460FRW耐火耐候钢作为试验钢,其化学成分见表1。试验前用精密线切割机床将试验钢分别加工成40 mm×60 mm×2 mm(周期浸润腐蚀试验)、15 mm×15 mm×2 mm(表面微观形貌和锈层横截面观察)和10 mm×10 mm×2 mm(电化学测试)的试样,表面粗糙度为0.8 μm。其中用去离子水加去油剂去除周期浸润腐蚀后试样和微观形貌和锈层横截面观察试样的表面油渍,再用自来水冲洗,酒精擦拭,冷风吹干,最后用丙酮擦拭,自然晾干后保存于干燥皿中。将电化学试样除油洗净后,用焊锡焊将直径为1.5 mm的导线接到试样表面,再用环氧树脂封样处理,裸露面积为10 mm×10 mm,经水磨砂纸(至600号)打磨,最后放入干燥皿中备用。
1.2 锈层稳定化处理
锈层稳定剂的主要成分如表2所示,该锈层稳定剂以水性聚氨酯为成膜剂,钼酸钠为促进剂,四氧化三铁为诱导剂,三氧化二铁为调色剂,磷酸氢二钠为复配剂,水为溶剂。将各组分混合并充分搅拌,均匀地涂刷在耐候钢试样表面,自然风干24 h,制成涂覆锈层稳定剂耐候钢试样(以下简称涂覆试样),然后与耐候钢裸钢试样(以下简称裸钢试样)一起进行对比腐蚀试验。涂覆层厚度为30~50 μm。
成分 | 水性聚氨酯 | Na2MoO4 | Fe2O3 | Fe3O4 | Na2HPO4 | 水 |
---|---|---|---|---|---|---|
质量分数/% | 10~30 | 1~10 | 1~15 | 1~15 | 0.1~5 | 余量 |
1.3 试验方法
本研究采用周期浸润腐蚀试验,腐蚀溶液为2%(质量分数)NaCl溶液,液槽温度为(25±2)℃,相对湿度RH为(70±10)%,循环周期为60 min,其中浸润时间10 min,分别进行72,120,168,360 h周期浸润腐蚀试验,同一周期浸润时间的每种试样采用3个平行样。腐蚀后的样品先进行机械除锈,再进行酸洗除锈,洗净吹干后用电子天平称量,记录并拍照。
利用Hitachi S3400N型扫描电镜(SEM)对试样腐蚀表面微观形貌和锈层横截面进行观察,其中横截面观察的试样需要在腐蚀后进行冷镶处理。利用JINCAx-actSN57014型能谱仪(EDS)对锈层中所含元素进行扫描分析。利用德国Bruker AXS生产的D8-Focus型X射线衍射测试仪(XRD)对锈层的结构及成分进行分析。利用美国Thermo Scientific生产的ESCALab250型X射线光电子能谱技术(XPS)对腐蚀产物中的元素价态进行分析。
采用CHI660A电化学工作站对试样进行极化曲线测试,取2%(质量分数)NaCl溶液置于烧杯中,以周期浸润腐蚀试验后的带锈试样为工作电极,以Pt片为辅助电极,以饱和甘汞电极(SCE)为参比电极,组成电解池,静置一段时间,再进行测试。测量电化学阻抗谱的频率范围是0.01~100 000 Hz,施加5 mV的电位扰动。Tafel极化曲线测量时,扫描范围为自腐蚀电位±500 mV,扫描速率为10 mV/s。
2. 结果与讨论
2.1 宏观形貌
由图1可见,涂覆试样表面呈巧克力色,裸钢试样表面呈现金属光泽。
由图2可以看出:两种试样在周期浸润腐蚀试验的条件下,在腐蚀72 h后表面均生成锈层;随着腐蚀时间的延长,腐蚀都逐渐加深,锈层变得粗糙;在120 h时裸钢试样表面出现锈层脱落现象,168 h后裸钢试样锈层出现锈液流挂现象,但是涂覆试样未出现该情况;在整个腐蚀过程中,裸钢试样的表面腐蚀情况均比涂覆试样严重。
2.2 锈层微观形貌
由图3可见:在腐蚀72 h后,两种试样表面锈层都出现了针尖状物质,根据DE LA FUENTE等[24]的报道,针尖状产物为FeOOH,涂覆试样表面针尖状产物更细密,呈致密沉淀状,这是稳定剂中聚氨酯尚未完全脱落的结果;随着腐蚀的进行,裸钢试样表面的腐蚀产物呈块状堆积,腐蚀产物尺寸增大,块状间距变大变深,而涂覆试样表面针尖状产物更细密,呈致密沉淀状。总体来说,与裸钢试样相比,涂覆试样表面锈层更加致密。
如图4所示:周期浸润腐蚀后,裸钢试样和涂覆试样表面均生成明显的外锈层和内锈层,其中外锈层疏松多孔,内锈层紧实且致密;随着腐蚀时间的延长,两种试样表面的锈层厚度都呈增加的趋势,但是涂覆试样表面内锈层厚度均小于裸钢试样的内锈层厚度。
2.3 腐蚀速率
对去除表面腐蚀产物后的两种试样进行称量,取其平均值,按照公式推算腐蚀速率和腐蚀质量损失,结果见图5。
由图5(a)可见:涂覆试样的腐蚀速率明显低于裸钢试样,约是裸钢试样的1/2;两种试样的腐蚀速率都随着腐蚀时间的增加逐渐降低并趋于平稳,到腐蚀360 h时,涂覆试样的腐蚀速率仅为裸钢试样的52%左右。由图5(b)可见:两种试样的腐蚀质量损失都随时间的延长而增加,但是涂覆试样的腐蚀质量损失明显低于裸钢试样,只有其1/2左右。
2.4 腐蚀产物结构与成分
图6为裸钢试样和涂覆试样经不同时间周期浸润腐蚀试验后锈层的XRD谱,表3为锈层物相的半定量结果。由于Fe3O4和γ-Fe2O3的晶格参数相似,其XRD衍射峰的位置非常接近,很难用XRD对它们进行区分,因此计算了两者的总含量。由图6可见:裸钢试样锈层主要由α-FeOOH、γ-FeOOH和Fe3O4/γ-Fe2O3组成,涂覆试样锈层主要由α-FeOOH、γ-FeOOH、α-Fe2O3和Fe3O4/γ-Fe2O3组成,其中α-Fe2O3是稳定剂带入的,不计入半定量计算结果。由表3可见,随着腐蚀时间的延长,两种试样锈层中γ-FeOOH的含量均显著增加,但是涂覆试样锈层中的γ-FeOOH含量整体上远低于裸钢试样,且α-FeOOH与γ-FeOOH的含量比值更大。
时间/h | w(γ-FeOOH)/% | w(α-FeOOH)/% | w(Fe3O4+γ-Fe2O3)/% | |||
---|---|---|---|---|---|---|
裸钢试样 | 涂覆试样 | 裸钢试样 | 涂覆试样 | 裸钢试样 | 涂覆试样 | |
72 | 29.3 | 21.6 | 16.5 | 14.6 | 54.2 | 63.7 |
120 | 28.0 | 20.6 | 16.6 | 13.8 | 55.4 | 65.6 |
168 | 47.8 | 29.0 | 13.8 | 13.0 | 38.4 | 58.0 |
360 | 58.8 | 42.0 | 17.9 | 17.7 | 23.3 | 40.3 |
如图7和图8所示:图中黄色纵线为锈层与基体分界线,纵线左侧为锈层,右侧为基体;在腐蚀初期,Mo元素在涂覆试样和裸钢试样的锈层中均未出现聚集峰值;在腐蚀360 h后,Mo元素在涂覆试样锈层与基体界面处产生富集,而在裸钢试样的锈层与基体界面处未产生明显富集。
由图9可见,经360 h周期浸润腐蚀试验后,涂覆试样表面锈层中含Mo、Fe、C和O元素,且锈层的主要成分是Fe和O元素;Mo3d峰对应的结合能在232.3 eV附近。这表明试样经过稳定剂处理后,Mo元素确实存在于锈层中,其中C元素可能由测试系统带入或者源自耐候钢材料本身。已知经过钼酸盐处理后试样锈层中生成了不溶性的钼酸盐和稳定的氧化物MoO3。对锈层中的Fe元素进行XPS分析,如图9(c)所示,可以看到其峰值主要集中在709~712 eV。
2.5 电化学测试
由图10和表4可见:随着腐蚀时间的延长,两种试样的腐蚀电位总体呈现正移的趋势,裸钢试样的腐蚀电流密度逐渐减小,而涂覆试样在低于120 h腐蚀时间下的腐蚀电流密度逐渐增大,当腐蚀时间大于168 h时逐渐减小。通过表4还可以看出,涂覆试样的腐蚀电流密度较裸钢试样更小,说明锈层稳定剂对基体具有更强的保护作用。
腐蚀时间/h | 试样 | Ecorr/V | Jcorr/(μA·cm-2) |
---|---|---|---|
72 | 裸钢试样 | -0.537 | 106.11 |
涂覆试样 | -0.631 | 67.32 | |
120 | 裸钢试样 | -0.532 | 98.55 |
涂覆试样 | -0.501 | 83.34 | |
168 | 裸钢试样 | -0.413 | 76.77 |
涂覆试样 | -0.440 | 72.06 | |
360 | 裸钢试样 | -0.367 | 58.39 |
涂覆试样 | -0.261 | 54.94 |
由图11可见,在不同的腐蚀时间下,涂覆试样的阻抗模值总体比裸钢试样更高。这说明涂覆试样的锈层电阻和电荷转移电阻均更高,腐蚀更难以进行,耐蚀性更好。耐候钢试样表面锈层和溶液之间有两个双电层,一个由渗透到金属基体表面的电解质和基体金属组成,另一个由体相电解质和锈层组成。可以用图12所示的等效电路来模拟带锈试样在NaCl溶液中的腐蚀状态。其中,Rs,Rr,Rct分别代表溶液电阻,锈层电阻和基体溶解反应的电荷转移电阻,Qrust代表锈层与溶液构成的双电层,Qdl代表金属基体与渗入其表面的电解液构成的双电层,Zt为扩散阻抗。锈层电阻Rr反映了锈层对腐蚀介质传播的阻挡能力,可以用来作为金属基体耐蚀性的评判指标。
由图13可见:从整个过程来看,涂覆试样的锈层电阻都要大于裸钢试样,说明涂覆锈层稳定剂对基体的保护性更强;涂覆试样的锈层电阻在腐蚀72 h时较大,在腐蚀120 h时略微降低,而裸钢试样的锈层电阻则随着腐蚀时间的延长持续增大,但其锈层电阻依然低于涂覆试样。
2.6 讨论
由图6可以看出,在整个腐蚀过程中,两种试样的腐蚀速率都呈现随腐蚀时间的延长而逐渐减小的趋势。这是因为在腐蚀初期,腐蚀介质和基体直接接触,基体表面会迅速生成一层薄锈层,这层薄锈层在一定程度上阻隔了腐蚀介质的传递,减小了基体活性阳极面积;随着腐蚀时间的延长,锈层厚度增加且更加致密,活性阳极面积越来越小,腐蚀速率随之降低。
纵观整个腐蚀过程,涂覆稳定剂试样的腐蚀速率和腐蚀质量损失均仅为裸钢试样的1/2左右,说明锈层稳定剂可以提高耐候钢的耐腐蚀能力。
通过表3可以看到,随着腐蚀时间的延长,两种试样锈层中的γ-FeOOH含量均显著增加,但是涂覆试样锈层中的γ-FeOOH含量整体上远低于裸钢试样。γ-FeOOH作为一种不稳定的氧化物,其越容易生成,表示腐蚀越容易发生。涂覆试样锈层中α-FeOOH的含量增加比裸钢试样更加明显,表明Mo元素可以促进α-FeOOH的生成。其原因是具有一定的氧化性,可以将Fe3O4氧化为Fe2O3,与此同时,在溶液中氧气的作用下,促进不稳定的γ-FeOOH向稳定的α-FeOOH转变,
则转化为稳定的MoO3。但是,涂覆试样锈层中的α-FeOOH含量比裸钢试样低,原因之一是稳定剂的阻挡作用导致生成的γ-FeOOH含量较少,而α-FeOOH是由γ-FeOOH转化而来,所以γ-FeOOH含量较低的涂覆试样转化成的α-FeOOH更少;二是腐蚀时间太短,还未到达锈层进行大量还原和再氧化的稳定阶段,这与图5(a)中腐蚀速率曲线规律相吻合。
通过EDS对锈层截面进行的线扫描元素分析,可推测Mo是锈层中主要的富集元素,在腐蚀初期已分散在锈层中,随着腐蚀的进行,Mo元素逐渐向基体转移,与基体溶解产生的Fe2+发生反应,生成具有保护性的FeMoO4,使得锈层结构更加稳定致密,阻碍了锈层对腐蚀介质的传递,提高了耐候钢的耐蚀性。
利用Shirley基线与洛伦兹-高斯比相结合,采用非线性最小面积法把Mo3d5/2谱分解为两部分。图14(a)是涂覆试样在360 h周期浸润腐蚀后腐蚀产物中Mo3d5/2的XPS分峰拟合图,Mo3d5/2可以分解为232.5 eV和232.2 eV两个能谱峰。由文献[25]得知,MoO3和Na2MoO4中Mo的3d5/2的结合能依次为232.6 eV和232.1 eV,与Mo3d5/2分峰的结合能很接近,说明Mo是以六价态(MoO3或)存在于锈层中的。由此可见锈层中生成了难溶性MoO3,对腐蚀起到了阻碍作用。图14(b)为涂覆试样在360 h周期浸润腐蚀后腐蚀产物中Fe2p3/2的分峰拟合图,其峰值主要集中在709~712 eV,表明Fe在锈层中主要以Fe2+和Fe3+两种价态存在。Fe2p3/2可以分解为711.8,710.5,710.3,709.4 eV四个峰,分别与FeO(OH)、Fe3O4、Fe2O3和二价铁的化合物相对应,其中709.4 eV处的能谱峰推测是铁的钼酸盐化合物的存在导致的。
裸钢试样和涂覆试样的腐蚀电位总体呈现正移的趋势,这是因为在腐蚀初期,试样表面生成了一层具有一定厚度的保护锈层,且随着腐蚀的进行,锈层越来越厚,试样发生腐蚀的倾向降低,腐蚀电位下降;裸钢试样的腐蚀电流密度是逐渐减小的,这是因为随着腐蚀的发生,锈层厚度逐渐增加,腐蚀发生的阻力增加。而涂覆试样的腐蚀电流密度在120 h之前逐渐增大,在168 h后逐渐减小。这是因为在腐蚀反应的初期阶段,稳定剂中的聚氨酯膜对锈蚀有明显抑制作用,腐蚀难以发生,随着腐蚀反应的进行,聚氨酯膜逐渐脱落,腐蚀电流密度增大,当腐蚀时间进一步延长时,锈层厚度增加,另外涂覆试样生成了难溶性的MoO3和FeMoO4,对基体的保护作用增强,腐蚀电流密度降低,涂覆试样锈层电阻的变化趋势也解释了该机理。通过Bode图可以看出,在不同的腐蚀时间下,涂覆试样的阻抗模值总体要比裸钢试样更高,说明涂覆试样的锈层电阻和电荷转移电阻更高,腐蚀更难以进行,耐蚀性更好。
3. 结论
(1)制备了一种Mo系耐候钢表面锈层稳定剂,该锈层稳定剂以水性聚氨酯为成膜剂,钼酸钠为促进剂,四氧化三铁为诱导剂,三氧化二铁为调色剂,磷酸氢二钠为复配剂,水为溶剂。
(2)锈层稳定剂可以避免耐候钢在腐蚀过程中产生锈液流挂现象,具有低毒无公害的特点,符合绿色环保的要求,并且可以将耐候钢的腐蚀速率降低至裸钢试样的1/2左右。
(3)锈层稳定剂对腐蚀介质具有阻挡作用,可减缓γ-FeOOH的产生。Mo元素在涂覆试样的锈层与基体界面处产生富集,并且促进了α-FeOOH的生成,在实验室加速腐蚀360 h时涂覆试样锈层中α-FeOOH/γ-FeOOH的含量比值由30.4%(裸钢试样)提升至42.1%。另外锈层中生成了稳定的氧化物MoO3和不溶性的FeMoO4,有效阻断金属离子的迁移,锈层电阻提高,从而提高了耐候钢的耐蚀性。
免责声明:本网站所转载的文字、图片与视频资料版权归原创作者所有,如果涉及侵权,请第一时间联系本网删除。
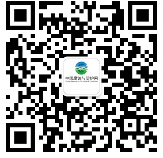
官方微信
《腐蚀与防护网电子期刊》征订启事
- 投稿联系:编辑部
- 电话:010-62316606
- 邮箱:fsfhzy666@163.com
- 腐蚀与防护网官方QQ群:140808414