元素 | C | Si | Mn | Cu | Ni | Cr | Mo | Fe |
---|---|---|---|---|---|---|---|---|
质量分数/% | 0.37 | 0.416 | 1.36 | 0.021 | 0.018 | 0.048 | 0.01 | 余量 |
在石油和天然气开采行业中,N80钢因其优异的强度和成本效益而被广泛应用于油井管道和地下结构[1-3]。N80钢套管通常容易受到CO2和H2S气体腐蚀,这会对设备完整性和服役周期造成重大威胁。CO2溶解在含水环境中会形成碳酸,导致N80钢表面发生均匀或局部腐蚀[4];在高温高压条件下,CO2会转化为超临界CO2导致腐蚀速率加快[5-6];长期的CO2腐蚀可能导致套管出现微裂缝和孔洞,进而影响套管的结构完整性[7]。H2S与N80钢表面反应形成脆弱的硫化物膜,在应力作用下膜破裂从而导致应力腐蚀开裂[8-9];硫化物膜能起到一定保护作用,但这种膜往往不稳定,一旦破损,金属基体就会暴露,加速腐蚀进程[10]。当CO2和H2S共同存在时,CO2溶于水,电离出的H+会降低溶液pH,从而加速H2S对N80钢的腐蚀,N80钢具有较高的腐蚀速率并伴随明显的局部腐蚀[11-12]。同时,CO2和H2S的含量变化会直接影响N80钢表面腐蚀产物的组成和结构。H2S含量较低时,该钢表面的腐蚀产物以FeCO3为主,腐蚀速率受FeCO3产物膜致密性和厚度的影响;H2S含量升高时,该钢表面可能会优先生成FeS产物膜,FeS产物膜的存在会干扰FeCO3产物膜的形成,该钢表面膜层的致密性和保护性受两种膜层的结构和生成状况的影响[13]。
环空是指油管和油管套管之间的空间,环空保护液是一种专门设计用于保护油管和油管套管之间不受腐蚀和污染的流体,在油气开采中发挥重要作用[14-15]。在油气井中,环空保护液通过形成保护性屏障,减少金属与腐蚀性介质(如水、H2S、CO2等)的接触,从而延长金属的使用寿命[16-17]。此外,环空保护液还具有物理隔离、控制温度和压力和防止管道沉积堵塞等作用[18]。刘徐慧等[19]研制了适用于H2S/CO2环境的无固相有机盐类水基环空保护液,能在钢片表面形成以有机胺为主的保护膜。武俊文等[20]研制了一种密度为1.0~1.6 g/cm3的环空保护液,钢片在该环空保护液中的腐蚀速率低至0.045 mm/a。
目前,对于N80钢在腐蚀环境中的腐蚀行为研究较多,但针对N80钢在含H2S/CO2环境中的腐蚀行为研究不够充分,且对于其在环空保护液中的腐蚀特性认识仍然有限。为此,笔者采用高温高压反应釜,在模拟工况环境中通入含CO2和H2S的环空保护液,研究了N80钢在该环境中的腐蚀行为,并探讨其了腐蚀机理,以期为油气管道材料选择和腐蚀防护提供科学依据,进而提高油气开采的安全性和经济效益。
1. 试验
1.1 试验材料
结合某油田现场用油套管材料种类,试验材料选用N80钢,其化学成分如表1所示。按照现场腐蚀试验要求,将材料加工成尺寸为50 mm×25 mm×3 mm的试样。在试样一端距边线2 mm处钻1个直径为3.8 mm的孔,便于悬挂试件。
试验前,对N80钢试样进行清洗并脱脂;将试样分别放入石油醚、蒸馏水、无水乙醇中进行超声清洗各10 min,冷风吹干,记录试样尺寸并在分析天平上(精度为0.1 mg)称量后置于干燥皿中备用。
1.2 试验方法
试验采用高温高压动态腐蚀评价系统(设备工艺图如图1所示)。
使用淡水+0.2%烧碱+0.1%(轻质氧化镁)PF-ACA+2%(缓蚀杀菌剂)PF-CA101+0.2%(硫代硫酸盐)PF-OSY配制环空保护液。对高温高压釜进行充分清洗后,将试片系挂在试片夹具上,并加入2 L环空保护液,密封高温高压釜,然后向釜内通入N2除氧3 h。釜体安装后,关闭出气阀。升温至试验温度后,向釜内通入分压分别为8.930 8 MPa、0.000 616 MPa的CO2、H2S,待压力平衡不再变化后,向釜内通入高纯N2或环空保护液至目标饱和压力27.5 MPa后开始试验,试验周期分别为3,7,15,30 d,期间保持釜内温度、压力稳定。
采用失重法计算试样的腐蚀速率。根据国标GB/T 16545-1996《金属和合金的腐蚀腐蚀试样上腐蚀产物的清除》,分别使用蒸馏水、去膜液、乙醇清洗腐蚀试样。其中,1 L去膜液配方为:六次甲基四胺50 g、盐酸100 mL+去离子水。将试样放入干燥皿中干燥12 h后称量、拍摄照片,并按照NACE RP0775-2005《油田生产中腐蚀挂片的准备和安装以及试验数据的分析》计算平均腐蚀速率,公式见式(1)。
|
(1) |
式中:vcorr为试样的腐蚀速率,mm/a;m为试样腐蚀前后的质量损失,g;S为试样与试验介质接触的表面积,mm2;ρ为试样的密度,g/cm3;t为测试周期,d。
利用Quanta 650 FEG型场发射扫描电镜(SEM)、Bruker6130型能谱仪(EDS)对试样进行表面微观形貌观察和元素组成分析;采用HJY LabRAM Aramis型拉曼光谱仪、Panalytical Empyrean型X射线衍射仪(XRD)对试样表面腐蚀产物的成分与物相组成进行分析。
2. 结果与讨论
2.1 均匀腐蚀速率
如图2所示:在腐蚀3 d时,试样的腐蚀速率最高为0.165 1 mm/a;随着试验时间的延长,腐蚀速率缓慢降低,在腐蚀30 d时仅为0.085 6 mm/a,约为腐蚀3 d时的一半。这是由于随着试验时间的延长,挂片表面形成了一定厚度的膜层,其能有效阻碍环境中腐蚀介质对试样的侵蚀,对试样起到了一定的保护作用。
2.2 腐蚀产物
如图3所示:在腐蚀3 d时,试样表面腐蚀产物凹凸不平,且存在凹槽与裂纹,腐蚀产物边界模糊、颗粒度差;在腐蚀7 d时,试样表面均匀覆盖腐蚀产物颗粒,且存在腐蚀坑,相较3 d时的腐蚀产物结构更为致密,腐蚀产物颗粒形状完好,边界清晰,颗粒表面均分布有少量白色颗粒状物质结簇;在腐蚀15 d时试样表面腐蚀产物进一步生长,产物颗粒分明,尺寸明显增大,颗粒表面可见大量棒状结晶与未成形颗粒;在腐蚀30 d时,试样表面呈致密的胶泥状形貌,产物颗粒粘连,晶体表面被新生腐蚀产物均匀包裹。
由表2可见,在腐蚀3 d时试样表面腐蚀产物主要元素为Fe、O、C、S与少量Ca,表明此时CO2、H2S均参与了腐蚀进程;除腐蚀30 d外,其余时间下试样表面均检测到S元素。这可能是因为腐蚀7 d时CO2主导了腐蚀进程,与S相关的腐蚀产物覆盖在底层;腐蚀30 d时,腐蚀产物中Fe含量增大,并检测到少量S元素,试样表面生成大量新的腐蚀产物,可推测Fe迁移到试样表面参与腐蚀进程,与CO2、H2S形成新的腐蚀产物,因此Fe的含量达到较高的水平。
试验时间/d | 质量分数/% | ||||||
---|---|---|---|---|---|---|---|
Fe | Ca | Mg | O | C | S | 其他 | |
3 | 20.29 | 1.28 | — | 26.79 | 41.14 | 9.73 | 0.78 |
7 | 25.87 | 1.96 | 6.15 | 53.40 | 11.45 | — | 1.17 |
15 | 25.09 | 1.19 | 2.77 | 56.27 | 14.68 | — | — |
30 | 37.72 | 3.05 | 8.44 | 36.48 | 12.63 | 0.91 | 0.77 |
根据文献报道[21],在H2S和CO2共存的湿环境中,酸性气体溶于水电离出的S2-和CO32-与Fe2+结合生成FeS和FeCO3腐蚀产物。王嘉豪等[22]研究了硫化物等地质成分的拉曼光谱信号,指出硫化亚铁是深灰色矿物,拉曼效应较弱,主峰通常位于472 cm-1左右。潘启亮等[23]研究指出,FeCO3的拉曼位移约在218,392,1 314 cm-1处。结合图4可知,不同试验时间下试样表面的腐蚀产物成分以FeCO3、FeS为主,并可能含有少量的Fe3O4(304,681 cm-1)。腐蚀3 d时,可检测到较为明显的FeS信号;随着腐蚀时间延长,FeS的拉曼位移信号逐渐减弱,FeCO3拉曼信号增强,腐蚀产物中的FeS含量占比减小,FeCO3含量增高。这说明在腐蚀早期H2S和CO2都参与了腐蚀过程,随着腐蚀时间延长,CO2逐渐主导腐蚀过程,因此后期腐蚀产物以FeCO3为主。通过对比文献[20]发现,腐蚀产物中存在的少量Fe3O4应是在测试过程或保存过程中形成的,并非腐蚀产物。
如图5所示:不同试验时间下的XRD谱中均可见Fe、FeCO3的衍射峰;腐蚀3 d时,试样表面腐蚀产物整体较少,XRD谱中有较强的Fe基体特征峰,未检测到其他腐蚀产物信号;腐蚀7 d时,XRD谱中有明显的FeCO3信号,之后随着腐蚀时间的延长,腐蚀产物的特征峰位置基本一致。这表明从腐蚀7 d开始,试样表面腐蚀产物均以FeCO3为主,该腐蚀过程由CO2控制。XRD谱中均未见FeS的衍射信号,原因可能是FeS含量少,衍射强度低。
2.3 讨论
在含H2S、CO2的环空保护液中(114.5 ℃),N80油套管钢在腐蚀3 d时的腐蚀速率最高,随着腐蚀时间的延长,腐蚀速率逐渐降低,结合表面微观形貌和腐蚀产物分析结果可知,试样表面生成的FeS、FeCO3等腐蚀产物对CO2、H2S的扩散起到了阻隔作用,延缓了腐蚀进程,从而腐蚀速率降低。腐蚀3 d时,腐蚀产物以小颗粒的FeS、FeCO3为主,腐蚀产物膜层较为粗糙,且存在大量凹槽与裂纹,因此腐蚀速率较高。这与文献[11]和[12]的研究结果类似。白真权等[13]研究表明,在CO2和H2S共存条件下,随着CO2含量的增加,N80钢的腐蚀速率逐渐增大,以均匀腐蚀为主,表面膜层附着力较低,且较为疏松,存在较多缺陷。SRINIVASAN等[14]研究表明,H2S存在时,N80钢表面会优先生成一层FeS腐蚀产物膜,其会阻碍CO2腐蚀产物FeCO3的生成。
腐蚀时间从7 d延长到15 d时,腐蚀产物颗粒增大并且相互粘连,气体氛围中的H2S被消耗,CO2含量较高,腐蚀以CO2控制为主。腐蚀产物中FeS含量减少、FeCO3含量增多,试样表面腐蚀产物进一步增厚,颗粒尺寸增大,且均匀覆盖,整体更为致密,在腐蚀15 d时生成了少量的新腐蚀产物;腐蚀30 d时,腐蚀产物呈现更为致密的油泥状,底层腐蚀产物表面覆盖均匀的新腐蚀产物,并且检测到少量的S元素,说明Fe迁移到表面与CO2、H2S发生腐蚀反应。研究表明[24-25],110 ℃左右,CO2氛围下N80钢表面生成的FeCO3腐蚀产物膜层具有一定的保护作用,此时N80钢表面呈泥状,腐蚀产物为粘连的粗结晶,较为密实。N80钢表面形成的FeCO3膜阻碍了腐蚀阳极溶解与阴极还原过程,从而腐蚀速率降低。GAO等[26]研究也表明,H2S存在时,碳钢表面的腐蚀产物具有多层结构,最外层也存在FeS、FeS2、Fe1-xS,这与本文研究结果一致。
综上所述,以CO2为主的腐蚀过程中,N80钢表面腐蚀产物颗粒尺寸较大且能紧密粘连,并能均匀致密地覆盖在基体表面,有效阻隔腐蚀性物质。但当环境中存在H2S等杂质时,腐蚀进程受到H2S的影响,腐蚀产物出现粗糙、孔隙和腐蚀通道较多的情况,其对基体的保护作用减弱。因此,在含CO2的腐蚀防护工作中,应严格控制H2S等杂质气体的含量,可延缓腐蚀进程,避免腐蚀情况快速恶化。
3. 结论
(1)在含H2S、CO2的环空保护液(114.5 ℃)中,N80钢的腐蚀产物以FeCO3、FeS为主,腐蚀速率随着腐蚀时间的延长而逐渐降低。其早期腐蚀速率较高与N80钢表面腐蚀产物存在大量凹槽和裂纹有关。腐蚀后期表面产物膜层逐渐致密,产物颗粒尺寸增大,并对腐蚀性物质产生一定的阻隔作用。
(2)早期腐蚀进程受到H2S和CO2共同控制,后期腐蚀进程以CO2控制为主,且CO2腐蚀产物膜层更为致密,具有更好的防腐蚀能力。在CO2腐蚀防护过程中,应严格控制H2S等杂质气体的含量,延缓腐蚀发展。
免责声明:本网站所转载的文字、图片与视频资料版权归原创作者所有,如果涉及侵权,请第一时间联系本网删除。
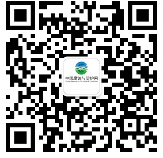
官方微信
《腐蚀与防护网电子期刊》征订启事
- 投稿联系:编辑部
- 电话:010-62316606
- 邮箱:fsfhzy666@163.com
- 腐蚀与防护网官方QQ群:140808414