钢板梁桥是中小跨径钢结构桥梁主要形式之一,具有构造简单、施工便捷、养护方便等优点,经济效益较其他形式钢桥更高,能够满足我国城市化交通建设日益增长的需求[1]。钢板梁桥末端伸缩缝部位,长期受到车辆冲击荷载作用,易造成构件损坏、雨水渗漏,导致腐蚀环境恶化[2]。同时,梁端受底部支座反力作用,应力集中现象明显,较其他部位更易发生腐蚀[3]。随着钢板梁桥运营时间的增长,梁端支座腐蚀问题日益突出,亟待解决。
钢材腐蚀会使构件截面变薄[4],直接导致结构承载力下降,影响结构的耐久性与安全性。支座部位主要以局部腐蚀为主,相较于均匀腐蚀,腐蚀速率更快,危害更大[5]。钢板梁桥支座部位腐蚀问题,主要研究对象包括腹板、翼缘和加劲肋[6]。相关研究结果表明[7],不同腐蚀部位对梁端承载力的影响方式存在显著差异。腹板部位锈蚀主要影响结构抗剪屈曲强度[8],使结构发生屈曲变形,改变应力分布,降低承载性能[9];翼缘腐蚀病害主要表现为受压翼缘在锈蚀后,强度、刚度与稳定性均降低,先于腹板出现较大变形,使钢梁屈曲发生在弯剪段[10];加劲肋局部腐蚀主要影响结构的抗压性能,当腐蚀损伤达到一定范围时,可能会使结构发生压碎性破坏[11]。实际运营过程中,往往是多部位腐蚀,如腹板与加劲肋腐蚀损伤复合作用下,结构极限承载力下降幅度较单部位腐蚀更大,结构破坏模式从屈曲变形变为破坏断裂[12]。上述研究总结了钢板梁桥支座附近不同腐蚀部位对结构受力的影响规律,但研究采用的腐蚀模型多为简化模型[13],腐蚀形貌也多为简单的规则形状。然而实桥支座部位构造和腐蚀情况都较为复杂,使用简化模型得到的结果并不能真实地反映结构受力情况[14]。
针对现有研究的不足之处,笔者研究了钢板梁桥支座部位腐蚀前应力变化情况,采用数值模拟的方法并结合实桥统计结果,提出几种可能的腐蚀形貌。在此基础上,分析各部位腐蚀形貌、腐蚀面积和腐蚀深度对结构受力的影响,并给出最不利的腐蚀部位与腐蚀形貌,该研究结果可为钢板梁桥后期腐蚀维护提供指导。
1. 有限元模型
支座部位应力集中现象显著,会促进腐蚀进程,表明应力与腐蚀存在一定联系[15]。本节主要分析支座部位腐蚀前应力分布状况,探讨应力分布与腐蚀形貌之间的关系。实际情况下,翼缘与腹板并不是完全刚性连接,横向荷载作用下会使腹板产生弯矩,且加劲肋的位置和数目对结构性能影响较大。为确保恒定剪切与较小的挠度,建立了四面板板梁有限元模型。模型尺寸按照钢板梁桥通用设计规范AASHTO LRFDBDS-9. AASHTO LRFD Bridge Design Specifications,9th Edition,如图1所示,梁长l 4 200 mm、宽d 300 mm,腹板高hw 1 000 mm、厚度tw 4 mm,翼缘厚度tf 12 mm,加劲肋厚度ts 8 mm。钢材型号为Q345qD,密度ρ 7 850 kg/m3,弹性模量G 2.1×105 N/mm2,泊松比ν=0.3。对支座部位网格进行加密划分。对于加劲肋数量,若按照规范规定取用多根加劲肋,则会使模型计算量过大,且本文主要研究目的是探究支座部位应力分布与腐蚀形貌之间的关系。因此,为简化计算过程,仅考虑单加劲肋,采用对称模型,建立的有限元模型如图2所示。
模型加载工况如图3所示。工况一和工况四荷载面积均为400 mm×200 mm,面荷载集度为1.25 N/mm2;工况二和工况三线荷载集度均为1×103 N/mm。
2. 结果与讨论
2.1 支座部位应力分布
图4为不同工况下支座处腹板未腐蚀的应力云图。由于存在应力集中,应力最大值点位于支座端部上方腹板,云图表现为以该点为中心点的半椭圆形,工况二下外侧腹板为1/4椭圆形。以每组工况下得到的应力最大值点为准,沿该点横向、竖向提取Mises应力。可以发现,工况一、二、四下,横向、竖向应力分别在距离应力最大值点约168 mm、53 mm处趋于平稳;加载工况三下,横向、竖向应力分别在距离应力最大值点约53 mm、16 mm处趋于平稳。通过上述分析,可以初步推断荷载作用下的内腹板应力分布形状为半椭圆形,外腹板应力分布形状为1/4椭圆形,长短轴比均为3左右。
按照规范给出的翼缘类型,改变钢板梁翼缘厚度,取tf=4,7,9,12,20 mm五种情况,施加工况二荷载,研究翼缘厚度对结构应力分布的影响。图5为不同翼缘厚度下,各方向上Mises应力变化规律,应力路径长度取100 mm。从图5中可以看出,各路径上应力随距离变化曲线趋势相同,均随翼缘厚度减小呈增大趋势。根据路径1应力变化曲线可以看出,在距离支座约10 mm处出现应力极值,除tf=4 mm情况下的曲线,其余曲线均在45 mm处左右趋于平缓,应力极值点与平缓点距离约35 mm。在路径1应力极值点(距离支座10 mm)垂直方向上提取应力,可得该应力曲线在距离极值点约12 mm处趋于平缓。对比可知,路径1上应力极值点与平缓点之间的横向距离是垂直方向上的3倍左右。验证上述所得内腹板处半椭圆形应力分布形状长轴与短轴比约为3。根据路径2应力变化曲线可以看出,在距离支座26 mm和38 mm左右时,应力曲线出现拐点,取平均值32 mm,在距离支座约95 mm处应力曲线趋于平缓,应力极值点与平缓点的距离约为63 mm。根据路径3应力变化曲线可以看出,在距离支座约3 mm左右时,应力曲线出现峰值,在距离支座约25 mm处时曲线趋于平缓,应力极值点与平缓点的距离约为22 mm。对比可知,路径2上应力极值点与平缓点距离是路径3上的3倍左右,这与上述得到得外腹板1/4椭圆形应力分布形状长轴与短轴比约为3的结果相印证。
图6和图7分别为不同工况下加劲肋和下翼缘未腐蚀应力云图。可以看出,两部位应力极值点均位于支座上方,并从该点向外扩展,应力分布形状主要呈1/4椭圆形和矩形。进一步对比各工况下加劲肋和下翼缘处的应力值大小,可以发现,两部位应力分布形状均随应力升高而增大,从1/4椭圆形向矩形过渡,最终稳定为矩形。采用与腹板相同的方法,分析加劲肋与下翼缘应力曲线,可以发现,加劲肋应力平稳边界大致在距下翼缘垂直方向25 mm,加劲肋一侧长150 mm;下翼缘应力平稳边界大致在距腹板垂直方向150 mm,下翼缘一侧长225 mm。
2.2 支座部位腐蚀特征
钢板梁桥支座部位实际出现的部分腐蚀情况如图8所示。可以看出,内侧腹板腐蚀形貌为半椭圆形,外侧腹板腐蚀形貌为1/4椭圆形,加劲肋与下翼缘腐蚀形貌均为矩形,各部位腐蚀形貌与上节得到的应力分布形状相吻合。
为进一步验证腐蚀形貌与应力分布形状的对应关系,以日本某项对钢板梁桥支座部位腐蚀的统计调查[16]为例,如图9所示。调查结果显示,三种典型腐蚀类型占钢板梁桥腐蚀类型的60%以上,主要分布在腹板、下翼缘和支撑周围的加劲肋上,腐蚀形貌主要为矩形和三角形。对各部位腐蚀情况统计汇总后发现,腹板部位内外侧腐蚀案例数量相当,主要以矩形和三角形腐蚀形貌为主;加劲肋和下翼缘部位腐蚀主要发生在内侧,均以矩形腐蚀形貌为主。结合上文分析可知,腹板部位应力分布形状为半椭圆形和1/4椭圆形,分别与实例矩形和三角形腐蚀形貌相似;加劲肋与下翼缘部位应力分布形状随应力的增大而增大,从1/4椭圆形过渡为矩形,与实例矩形腐蚀形貌相对应。综上所述,可根据支座部位应力分布形状假定可能出现的腐蚀形貌。
2.3 支座局部腐蚀对结构承载力的影响
根据上文分析结果,采用的腐蚀形貌按以下规则选取:假定内腹板和外腹板的腐蚀形貌分别为半椭圆形和1/4椭圆形,长短轴比均取3,并补充日本调查统计采用的三角形和矩形。按照等面积原则,每种腐蚀形貌考虑三种不同尺寸;加劲肋腐蚀形貌假定为长150 mm、宽25 mm的矩形,考虑三种腐蚀尺寸;下翼缘腐蚀形貌假定为长225 mm、宽150 mm的矩形,考虑三种腐蚀尺寸,具体参数见表1。建立的部分腐蚀形貌有限元模型如图10所示。有限元模型与上节相同,加载方式为跨中加载,荷载集度为50 N/mm2,作用面积为300 mm×100 mm。对腹板、加劲肋和下翼缘进行单部位腐蚀损伤模拟,腐蚀损伤通过改变钢板厚度来实现,腐蚀率选取25%、50%、75%,腐蚀深度等于腐蚀率与钢板厚度的乘积。
腐蚀部位 | 矩形-J(l为长,d为宽) | 三角形-S(m为长边,n为短边) | 椭圆形-T(a为长半轴,b为短半轴) | |||
---|---|---|---|---|---|---|
编号 | 尺寸/mm | 编号 | 尺寸/mm | 编号 | 尺寸/mm | |
内腹板-NF | NF-J1 | l=100, d=100 | NF-S1 | m=200, n=100 | NF-T1 | a=138, b=46 |
NF-J2 | l=150, d=100 | NF-S2 | m=300, n=100 | NF-T2 | a=168, b=56 | |
NF-J3 | l=200, d=100 | NF-S3 | m=400, n=100 | NF-T3 | a=195, b=65 | |
外腹板-WF | WF-J1 | l=100, d=100 | WF-S1 | m=200, n=100 | NF-T1 | a=195, b=65 |
WF-J2 | l=150, d=100 | WF-S2 | m=300, n=100 | NF-T2 | a=240, b=80 | |
WF-J3 | l=200, d=100 | WF-S3 | m=400, n=100 | NF-T3 | a=276, b=92 | |
加劲肋-J | J-J1 | l=150, d=25 | — | — | — | — |
J-J2 | l=150, d=75 | |||||
J-J3 | l=150, d=125 | |||||
下翼缘-Y | Y-J1 | l=175, d=150 | — | — | — | — |
Y-J2 | l=225, d=150 | |||||
Y-J3 | l=275, d=150 |
以内腹板50%腐蚀率情况为例,研究腐蚀形貌、腐蚀面积对结构承载力的影响。绘制梁中心点处荷载位移曲线,如图11所示,其中H表示未腐蚀试件。从图11中可以看出,未腐蚀试件屈服荷载约为1 370 kN,对应的中心点处竖向位移约为7 mm。不同腐蚀形貌下,结构中心点荷载位移曲线趋势与未腐蚀试件相同,均符合双线性应力-应变曲线[6],且当中心点处位移达到7 mm左右时,各腐蚀试件均达到屈服状态,验证了该腐蚀模型的合理性。
比较各腐蚀形貌下的结构荷载位移曲线,当腐蚀形貌假定为矩形时,NF-J3试件屈服荷载最小,约为1 130 kN,较未腐蚀试件下降约17.52%;当腐蚀形貌假定为三角形时,在中心点位移小于7 mm的弹性阶段内,NF-S3试件屈服荷载下降最大,在中心点位移大于7 mm的塑性阶段内,NF-S2试件荷载下降最大,两组试件交界点荷载为1 250 kN,较未腐蚀试件下降约8.76%;当腐蚀形貌假定为半椭圆形时,各试件荷载位移曲线无明显差异,NF-T3试件屈服荷载最低,约为1 280 kN,较未腐蚀试件下降约6.57%。上述分析过程中,当腐蚀形貌为三角形时,由NF-S2与NF-S3试件荷载位移曲线可知,结构承载力并未随腐蚀面积增大而降低,这可能是因为三角形腐蚀区域附近存在应力集中;取三组试件三角形较小锐角,NF-S1、NF-S2、NF-S3试件较小锐角分别为29°、42°、30°,可估计当腐蚀面积为三角形,较小锐角在42°左右时,应力集中效应影响较小。综上所述,当内腹板腐蚀形貌为矩形时,结构承载力受腐蚀面积影响最为明显;在弹性阶段时,三种腐蚀形貌下,结构承载力随腐蚀面积增加而减小,表明此时应力集中对结构承载力影响较小。
取不同腐蚀形貌的内腹板试件各两个,即NF-J2、NF-S2、NF-T2三组试件,研究腐蚀深度对结构承载力的影响。绘制梁中心点处荷载位移曲线,如图12所示,图中D1、D2、D3分别表示腐蚀率为25%、50%、75%时的腐蚀深度,腹板未腐蚀深度tw为4 mm,则D1=1 mm、D2=2 mm、D3=3 mm。由图12可见,相同腐蚀面积下,不同腐蚀形貌试件的承载力随腐蚀深度增加而减小。假定的矩形、三角形和椭圆形腐蚀形貌下屈服承载力最低分别为1 167 kN、1 230 kN和1 301 kN,较未腐蚀试件屈服强度分别下降了14.82%、10.22%、5.04%。可见,腐蚀形貌受腐蚀深度影响从大到小为矩形、三角形、椭圆形。
按上述方法分析外腹板、加劲肋以及下翼缘处腐蚀形貌、腐蚀面积和腐蚀深度对结构承载力的影响,可以发现,外腹板、加劲肋以及下翼缘处荷载与位移曲线均符合双曲线模型,结构承载力均随腐蚀面积和腐蚀深度的增大而减小。外腹板处假定的三种腐蚀形貌的荷载与位移曲线与未腐蚀试件曲线相近,表明外腹板处腐蚀形貌以及腐蚀面积对构件承载力的影响较小;进一步研究腐蚀深度的影响可以发现,对于矩形与三角形腐蚀试件,承载力降幅约为2%,椭圆形腐蚀试件承载力降幅约为4.6%,椭圆形腐蚀形貌对承载力影响相对较大。加劲肋处假定为矩形腐蚀形貌,根据荷载与位移曲线可知,弹性阶段,腐蚀面积与腐蚀深度对承载力影响较小;进入塑性阶段后,腐蚀面积越大,结构承载力越小;腐蚀深度对加劲肋承载力的影响主要在塑性阶段,且较未腐蚀试件承载力出现明显降低,屈服荷载最大降低约35%。主要原因是加载初期,加劲肋对结构刚度影响较小,在腹板受剪屈服后,加劲肋腐蚀对结构承载力影响作用才会显现。下翼缘处假定为矩形腐蚀形貌,腐蚀面积与腐蚀深度对结构承载力的影响接近,屈服荷载最低下降约17%。
综上所述,支座部位腐蚀对结构承载力的影响效果从大到小分别为加劲肋、内腹板、下翼缘、外腹板。内腹板腐蚀对结构承载力的影响相较外腹板腐蚀影响更为明显,且外腹板腐蚀对结构承载力影响很小。内腹板部位假定的三种腐蚀形貌,对结构承载力影响效果从大到小分别为矩形、三角形、椭圆形;外腹板部位假定的三种腐蚀形貌中,椭圆形对结构承载力影响效果最大,矩形与三角形影响效果接近。
3. 结论
(1)钢板梁桥支座部位未腐蚀前,内、外腹板应力分布形状分别为半椭圆形和1/4椭圆形;加劲肋与下翼缘处应力分布形状随应力的增大,从1/4椭圆形过渡为矩形。
(2)结构处于弹性阶段时,结构承载力随腐蚀面积、腐蚀深度的增大而减小。不同腐蚀部位对结构承载力的影响从大到小分别为加劲肋、内腹板、下翼缘、外腹板。
(3)对于腹板部位,在腐蚀面积和腐蚀深度相同的情况下,内腹板腐蚀形貌假定为矩形或外腹板腐蚀形貌假定为1/4椭圆形时,结构极限承载力下降幅度最显著。
免责声明:本网站所转载的文字、图片与视频资料版权归原创作者所有,如果涉及侵权,请第一时间联系本网删除。
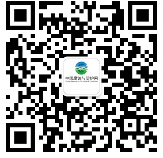
官方微信
《腐蚀与防护网电子期刊》征订启事
- 投稿联系:编辑部
- 电话:010-62316606
- 邮箱:fsfhzy666@163.com
- 腐蚀与防护网官方QQ群:140808414