导读:生产高强度金属对于节约资源和提高能源效率至关重要。然而,追求金属的高强度和延展性仍然是一个重大挑战。在本研究中,我们介绍了一种旨在提高金属材料强度-延展性协同作用的方法。采用激光粉末床熔合 (LPBF) 技术开发了微层压双相不锈钢 (DSS) 基复合材料,从而产生了四种不同的异质结构。316 L 奥氏体不锈钢 (ASS) 和 2507 DSS 粉末以及微米级 TiC 颗粒用于创建奥氏体和铁素体的微尺度层。交替形成具有双峰晶粒的奥氏体层和具有细晶粒的铁素体层。在这些层中发现了原位形成的 纳米颗粒,并且在铁素体层内和附近产生了双相晶粒。由于这些异质结构,微层压复合材料具有较高的极限拉伸强度(~1.06 GPa)和均匀伸长率(~21.9 %),与其他已报道的热处理 LPBF 制造的 2205/2507 DSS 相比,表现出增强的强度-延展性协同作用。
特别是,发现这些异质结构形成了强烈的异质变形诱导 (HDI) 应力,有助于增强强度-延展性协同作用。有趣的是,由于奥氏体和铁素体层的交替堆叠,微层压复合材料实现了良好的各向同性拉伸性能,并且很好地展示了未使用粉末的可回收性。这项研究可以为各种工业应用中的金属提供一种先进的制造方法。
鉴于全球变暖和能源危机的发生,开发高强度的金属材料以制造各种轻型部件是当务之急。激光粉末床熔合 (LPBF) 即将成为制造具有复杂几何形状的金属部件的最常用增材制造方法 。据报道,超快冷却速度和非平衡凝固过程能够创造独特的微观结构,从而显著改善金属的机械性能。
利用 LPBF 可以成功获得一些高强度的金属材料,但要避免延展性的减弱却很困难。例如,具有良好力学性能和耐腐蚀性能的铁素体-奥氏体双相不锈钢 (DSS) 已在各个工业领域得到应用,而 LPBF 制备的 DSS 也得到了广泛的研究 。虽然可以获得高强度,但由于超快的冷却速度,预期的平衡铁素体-奥氏体微观组织消失,导致其变脆 。不幸的是,强度和延展性之间的权衡困境是不可避免的 。晶粒细化被认为是同时提高强度和延展性的有效方法。然而,用于实现晶粒细化的制造方法容易降低合金的应变硬化能力,导致其延展性下降 。纳米颗粒增强体的引入已被证明可以提高金属的强度-延展性协同作用。但是,纳米颗粒在基质中很容易聚集。
因此,应探索新颖的设计和制造策略,以实现强度和延展性之间的巨大协同作用。
据报道,层压复合材料表现出优异的机械性能,工程聚合物层压板或分层天然材料(如珍珠层、木材和骨骼)就是证据。平衡软硬分层层压结构可以促进强化而不牺牲延展性。这种材料设计方法可以通过增材制造技术在合金中实现。具有异质结构的金属材料,如层压结构、双峰晶粒、金属基复合材料和双相合金,已被证明可以在保持或增强延展性的同时提高强度,这主要归因于异质变形诱导 (HDI) 强化和 HDI 加工硬化。
有趣的是,LPBF 制备的 316 L 不锈钢 (SS) 和 2507 超级 DSS (SDSS) 之间的硬度差异很大,而且 LPBF 制备的 2507 SDSS 形成了几乎全铁素体微观结构。因此,可以基于 LPBF 技术通过堆叠多个 316 L SS(软区)和 2507 SDSS(硬区)层来开发微层压 DSS。通常,软层和硬层的厚度应该足够薄以增加区域边界的密度,从而产生强的 HDI 效应。此外,这两层应该交替堆叠以进一步增强区域边界。然而,由于两层交替堆叠,薄层很难构建。因为薄层可能会在重熔过程中因 316 L SS 和 2507 SDSS 层之间的冶金反应而消失。因此,316L SS和2507 SDSS层厚设计时应足够厚,但过厚的层数会导致HDI效果减弱。
所以,本研究设计了多种异质结构,并将其引入 316 L SS 和 2507 SDSS 层中。对于硬质 2507 SDSS 层,采用微米级 TiC 颗粒形成原位 纳米颗粒增强铁素体基体复合材料。对于软质 316 L SS 层,通过重熔过程引起的 316 L SS 和 2507 SDSS 层之间的冶金反应引入双峰晶粒设计。此外,还发现在铁素体层中产生了一些双相晶粒。随后,制备了具有多种异质结构的微层状 DSS 基体复合材料。在我们之前的研究中,虽然已经获得并研究了由 TiC 颗粒增强的 LPBF 制备的 SDSS 基复合材料,但本研究的新颖之处在于使用 LPBF 制备的 SDSS 基复合材料作为铁素体层,使用 LPBF 制备的 AISI 316 L SS 作为奥氏体层,成功构建了具有优异强度-延展性协同作用的微层压 DSS 基复合材料。在 LPBF 过程中,仅消耗了一小部分 316 L 和 2507 粉末来制造微层压复合材料,但仍有大量未使用的粉末剩余。由于两种粉末交替堆叠,这些剩余粉末不能直接用于打印新部件。为了节省资源并降低生产成本,剩余粉末将用于制造 LPBF 制备的 DSS 基复合材料。最重要的是,相对于采用传统制造方法制造的异质结构 DSS,例如异质层状结构 (HLS) 的 DSS,基于该方法可以直接制造具有异质结构和复杂几何形状的高性能 DSS 部件。本研究开发的设计策略也可应用于更广泛的 LPBF 制造材料,以开发具有高强度和延展性的金属材料。
链接:https://www.sciencedirect.com/science/article/pii/S2214860425000119
(a)316 L SS 粉末,(b)粗 TiC 颗粒,(c)细 TiC 颗粒,(d)2507 SDSS 粉末和 TiC 颗粒的粉末混合物,(e)所有样品采用的扫描策略(TD:横向;BD:构建方向),(f)LPBF 制备的拉伸样品的示意图(水平),(g)粉末进料区域的粉末示意图。
为了设计微层压复合材料,我们分别研究了 316 L SS 和 SDSS 基体复合材料的微观结构。对于 316 L SS 的初始状态(图 2a 和 c),发现由于晶粒外延生长而产生了粗大的奥氏体晶粒 。如图 2b 所示,发现小角度晶界 (LAGB) 含量相对较高,其形成主要是由位错重排引起的 。在这些粗大的奥氏体晶粒内可以发现大量细小的亚晶粒(图 2d),并且由于反复加热和冷却过程引发的应力,沿亚晶粒边界形成了高密度位错网络 。在 SDSS 基复合材料中形成了许多细小的铁素体晶粒以及一些 纳米颗粒(图 2e-f),并且发现产生了一些位错。
(a)316L SS 状态 BD 中奥氏体的反极图 (IPF) 取向图(步长:0.5 μm);(b)奥氏体的晶界取向差图;(c)奥氏体的晶粒尺寸分布;(d)316L SS 状态中亚晶粒的 SEM 图像;(e)2507 SDSS 基体复合材料中细小铁素体晶粒的 SEM 图像;(f)相应的 TEM 明场 (BF) 图像。
在方案I中,未发现明显的奥氏体和铁素体层(图3a),且制备好的复合材料中铁素体相的质量分数仅为~23 wt%(图3d)。其次,为了增加铁素体相的含量,采用了另外两种方案。连续打印三层(方案II)或四层(方案III)316L粉末,然后打印五层2507-TiC粉末。最后,由于方案III中获得的铁素体含量相对较低(~29 wt%)(图3c和3f),因此选择了方案II(图3e),并且可以观察到两个具有不同对比度的不同层(图3b)。
(a)方案 I 中制备的微层合 DSS 基质复合材料的光学显微照片,(b) 方案 II 中制备的微层合 DSS 基质复合材料的光学显微照片,(c) 方案 III 中制备的微层合 DSS 基质复合材料的光学显微照片,(d) 方案 I 中复合材料的 XRD 谱,(e) 方案 II 中复合材料的 XRD 谱,(f) 方案 III 中复合材料的 XRD 谱。
图4a为方案二中制备的微层状复合材料示意图,如图4b所示,结果表明制备的微层状复合材料中铁素体层和奥氏体层交替生成,铁素体层厚度约为75μm,奥氏体层厚度约为90μm。此外,在这些铁素体层和奥氏体层之间可以发现两个过渡区(I和II)(图4b),过渡区I和II的厚度分别约为45和80μm。
(a)方案II中已构建微层压复合材料的示意图,(b)Y-Z平面上已构建微层压复合材料的相位图(步长:1.3μm)。
XRD 表征结果显示 (图 5) 材料中形成了铁素体和奥氏体相,铁素体和奥氏体的重量分数分别约为 36 wt% 和 64 wt%。特别地,在图 5 中还检测到了TiCxNy相的衍射峰。
方案 II 中制备的微层压复合材料的 XRD 谱
为了进一步研究成形后的微层状复合材料,进行了较小步长的EBSD表征(图6a-c),证实了奥氏体和铁素体晶粒的随机晶粒取向。对于过渡区I(TA-I),可以发现奥氏体相的熔池具有典型的“鱼鳞”形状(图6a),在奥氏体的晶界处生成了一些细小的铁素体晶粒。
在TA-I内或附近观察到包括相对较大的铁素体晶粒和晶间奥氏体晶粒(区域I)的双相晶粒(图6a和6d),它们的化学成分如表S2所示。如图6j所示,在铁素体晶粒边界处形成了一些细小的奥氏体晶粒,两种类型的晶粒中均产生了位错。
图 6a 中,对于铁素体层 (FL),有两个典型区域 (II 和 III)。在区域 II 中发现生成了细小的铁素体晶粒,这主要归因于原位形成的 纳米颗粒和超快冷却速度提供的异质成核位点。图 6e 显示了细小的铁素体晶粒以及一些 纳米颗粒。除了 纳米颗粒外,在铁素体的晶界处还发现了微小的 Cr 偏析 (图 6k 和图 S3b),这些偏析区域被证实由晶间 M23C6 纳米颗粒组成。在区域 III 中观察到某些具有环流特征的奥氏体晶粒 (图 6a 和图 6f)。此外,在图中6a和6g中,在过渡区域II(TA-II)中形成了一些包含相对较大奥氏体晶粒和晶间铁素体晶粒(区域IV)的双相晶粒,并且在奥氏体晶粒中证实了Ni元素的含量略高(表S2)。同样,在TA-II中也观察到一些具有环流特征的奥氏体晶粒。
在图6a和图6h中,在奥氏体层(AL)中形成了细小的奥氏体晶粒(区域V),并且还发现了一些由细小亚晶粒组成的相对较粗的奥氏体晶粒(区域VI)(图6a和图6i),这表明在AL中引入了双峰晶粒设计。对于AL中细小奥氏体晶粒的形成,详细解释可参见补充信息(图S5-6;注释S2)。特别地,在图 6a 中,我们发现在 AL 中的某些细小奥氏体晶粒的边界上形成了细小的铁素体晶粒,这会阻碍奥氏体晶粒的长大。此外,在 FL 中还发现了一些细小的奥氏体晶粒,这些晶粒呈随机分布,如图 6a 中的黑色虚线圆圈所示。
成品微层压复合材料:(a) Y-Z 平面上的相位图(步长:0.15 μm),(b) BD 中奥氏体的 IPF 对应的取向图,(c) BD 中铁素体的 IPF 对应的取向图,(d) TA-I 中或附近的双相晶粒的 SEM 图像,(e) FLs 中细铁素体晶粒的 SEM 图像,(f) 具有循环流动特征的奥氏体晶粒的 SEM 图像,(g) TA-II 中的双相晶粒的 SEM 图像,(h) ALs 中细奥氏体晶粒的 SEM 图像,(i) 粗奥氏体晶粒内的亚晶粒的 SEM 图像,(j) 显示 TA-I 中双相晶粒的 TEM BF 图像,以及一些选区电子衍射 (SAED) 图案,(k) 显示细铁素体的 TEM BF 图像FL 中的晶粒和 纳米颗粒,以及 EDS 表征。
对于方案 II 中的粉末回收,由于粉末混合物中 2507 粉末(5 层)的重量分数高于 316 L 粉末(3 层),因此应在粉末混合物中添加更多的 316 L 粉末以制备成品 DSS 基体复合材料。316 L SS 和 2507 SDSS 粉末的 XRD 图案如图 7a-b 所示。将粉末混合物筛分并混合后进行 XRD 表征(图 7c),基于 Rietveld 方法和 MAUD 软件估计铁素体和奥氏体相的重量分数分别约为 63 wt% 和 37 wt%。因此,确定 2507 SDSS 和 316 L SS 粉末在粉末混合物中的重量分数分别约为 68 wt% 和 32 wt%,并在粉末混合物中添加额外的 316 L 粉末以平衡两种粉末,相应地也添加了更多的 TiC 颗粒。随后,用 Inversina 滚筒搅拌机(混合时间:30 分钟;转速:100 rpm)获得约 46 wt% 316 L、52 wt% 2507、1 wt% TiC(~1 μm)和 1 wt% TiC(5-25 μm)的粉末混合物,相应的 XRD 图案如图 7d 所示。粉末回收制成的 DSS 基复合材料的工艺参数如表 S3 所示。由不同工艺参数下样品的相对密度图(图7e)可知,当施加的能量密度高于106.3 J/mm3时,可获得较高的相对密度(>99.2%)。考虑到高能量密度下DSS基复合材料的晶粒长大,确定最优的P为255 W,v为600 mm/s,对应的样品组织如图7f所示。
(a)316L SS粉末的 XRD 谱;(b)2507 SDSS 粉末的 XRD 谱;(c)筛分和混合后未使用的粉末混合物的 XRD 谱;(d)粉末回收制成的 DSS 基复合材料的粉末混合物的 XRD 谱;(e)不同工艺参数下粉末回收制成的 DSS 基复合材料的相对密度(实线是相对于 Y 轴的延长线,该线上的数值对应于 Y 轴的 99.2%);(f)相对密度最高的粉末回收制成的 DSS 基复合材料的光学显微照片。
(a)粉末回收制成的 DSS 基体复合材料的相图(步长:0.1 μm);(b)相应的 XRD 图案;(c)图 8a 对应的 Ni 元素分布;(d)粗大奥氏体晶粒的 SEM 图像;(e)具有环流特征的铁素体晶粒的 SEM 图像;(f)铁素体晶粒和一些奥氏体晶粒的 SEM 图像;(g)奥氏体晶粒和一些细小晶粒间铁素体晶粒的 SEM 图像。
图 9a 比较了成品微层压复合材料以及由回收粉末、2507 SDSS、2507 SDSS 基质复合材料、316 L SS 和 316 L SS 基质复合材料制成的成品 DSS 基质复合材料的工程应力-应变曲线。拉伸性能列于表 2 中。成品 316 L SS(RD:~99.8 %)的极限拉伸强度 (UTS) 和均匀伸长率 (UE) 分别约为 649 MPa 和 31.9 %。对于成品 2507 SDSS 基质复合材料(RD:~99.4 %),与其他 LPBF 制造的 2507 SDSS 相比,它们表现出 UTS(~1183 MPa)和 UE(~9.6 %)的优异组合(图 9b)。此外,与本研究获得的成品 2507 SDSS(UTS:~1175 MPa;UE:~6.5%;RD:~99.6 %)相比,成品 SDSS 基体复合材料的 UTS 和 UE 均有所提高,表明异质结构(微米级 TiC 颗粒和 TiCxNy 纳米颗粒)对 LPBF 制备的 2507 SDSS 的强度-延展性协同作用的有效性。特别是,对于由回收粉末制成的成品 DSS 基体复合材料,发现实现了优异的拉伸性能(UTS:~1092 MPa;UE:~17.9 %)(图 9b),相关的强化机制在补充信息中进行了讨论(注释 S5)。对于成品微层压复合材料,其 UTS 和 UE 分别确定为 ~1057 MPa 和 ~21.9 %。与一些经过热处理的 LPBF 制造的 2205/2507 DSS 和通过其他 AM 方法制造的 2507 SDSS 相比,发现成品微层压复合材料具有出色的拉伸性能。特别是,与通过传统热机械加工制造的具有 HLS 的 2507 SDSS 相比,本研究获得了大大增强的 UTS 和 UE(图 9b)。
(a)本研究中获得的样品的工程应力-应变曲线,(b)Ashby 图显示本研究和文献中获得的样品的 UTS 和 UE;拉伸方向沿横向
拉伸性能列于表2中。
各种样品的显微硬度值。
3.5 wt % NaCl 溶液中微层压复合材料的动电位极化曲线。
在变形阶段I,它们的ALM明显增强,且奥氏体的ALM略高于铁素体的ALM,尤其是细小的奥氏体(图12a,e,i和13a)。然而,与变形阶段 II 中的奥氏体晶粒相比,铁素体的 ALM 急剧增加至约 1.49◦(图 12b、f、j 和 13a)。
(a-d)不同变形阶段AL中细奥氏体晶粒的核平均取向差(KAM)分布图,(e-h)不同变形阶段FL中铁素体晶粒的KAM分布图,(i-l)不同变形阶段AL中粗奥氏体晶粒的KAM分布图。
在图 13a 中,随着应变的增加(变形阶段 III 和 IV),铁素体晶粒的 ALM 始终高于奥氏体晶粒的 ALM,这主要归因于细小的铁素体晶粒(图 13c 和表 S4)被证明比奥氏体晶粒具有更大的应变硬化能力。从双峰晶粒角度看,粗奥氏体晶粒尺寸明显大于细奥氏体晶粒(图 13c),因此在变形过程中,粗奥氏体晶粒可以先于细奥氏体晶粒发生屈服和塑性变形。但在图 13a 中,变形阶段 I 时细奥氏体晶粒的 ALM 高于粗奥氏体晶粒,表明细奥氏体晶粒的位错密度增加,这主要归因于细晶粒在塑性变形早期阶段比粗晶粒具有更好的应变硬化能力。特别是在变形阶段 IV,粗奥氏体晶粒的 ALM 与细奥氏体晶粒的 ALM 相当(图 13a)。
图 13.
(a)不同变形阶段铁素体和奥氏体晶粒的 ALM 值,(b)不同变形阶段双相晶粒的 ALM 值,(c)不同变形阶段铁素体和奥氏体晶粒的平均晶粒尺寸,(d)不同变形阶段铁素体、双相和粗奥氏体晶粒中 LAGB 和 HAGB 的分数。
相对于 BD 样品,TD 样品的屈服强度 (YS) 和 UTS 更高,而 TD 样品的 UE 较低(图 14a)。
图 14.
(a)微层压复合材料沿建筑方向(BD 样品)和横向(TD 样品)的宏观拉伸试验的工程应力-应变曲线,(b) 显示 Y-Z 平面上 BD 样品断裂的 SEM 图像,(c) 显示 X-Z 平面上 BD 样品断裂的 SEM 图像,(d) 显示 X-Y 平面上 BD 样品断裂的 SEM 图像,(e-h) 图 14d 中区域的放大图。
对于强度估算值与实验值之间的差异,值得注意的是,在 BD 样品的加载过程中,FL 可以产生机械约束,而硬 FL 可以限制软薄 AL 的横向收缩。随后,这种约束可以降低 AL 的有效应力,抑制 AL 的塑性变形。因此,对于 AL 的延性断裂,施加的载荷会增加,并且断裂可以穿过 AL(图 15a)。
在图 15b-c 中,在真实应变超过 ~2.7 % 之后,BD 样品的应变硬化率始终超过 TD 样品的应变硬化率,这使得 BD 样品具有更高的 UE。与 BD 样品相比,在真实应变超过约 2.7 % 之前,TD 样品的应变硬化率更高。当拉伸方向为横向时,在相同应变条件下,硬质铁素体层能够承受更大的应力,由于高应变硬化率的铁素体层的存在,微层状复合材料的应变硬化率可以提高(图15d)。然而,当真实应变超过2.7 %后,BD样品的应变硬化率高于TD样品。如图15d所示,当真实应变超过约3.2 %后,2507 SDSS基体复合材料(FL)的应变硬化率急剧下降,这会降低TD样品的应变硬化率。
图 15.
(a)BD 样品裂纹扩展示意图,(b-c) BD 和 TD 样品的真实应力-应变/应变硬化速率曲线,(d) 2507 SDSS 基体复合材料的真实应力-应变/应变硬化速率曲线
图 16.
沿横向变形的微层状复合材料:(a) 微米级 TiC 颗粒和TiCxNy纳米颗粒的示意图,(b) TEM BF 图像显示铁素体晶粒内 纳米颗粒周围的位错钉扎,(c) TEM BF 图像显示奥氏体晶粒内 纳米颗粒周围的位错钉扎以及变形孪晶的出现,(d) TEM BF 图像显示铁素体晶粒。
根据微层状复合材料断口的Y-Z(图17b)和X-Z(图17d)面可以看出,断裂的AL层高度大于断裂的FL层高度,并且可以发现AL层的局部颈缩。特别地,在FL层中发现了明显的微裂纹(图17b-c)。在铁素体层和奥氏体层的断口表面上都可以发现大量的韧窝(图17d-f),并且AL层的韧窝尺寸明显大于FL层的韧窝尺寸。因此,可以证明AL层与FL层相比(图17c)能够承受更大的塑性应变,并且奥氏体和铁素体层的交替分布可以产生适当的强度和延展性组合。
图 17.
(a)沿横向变形的微层压复合材料的示意图,(b) 显示在 Y-Z 平面上微层压复合材料断裂的 SEM 图像,(c) 显示微层压铁素体和奥氏体的示意图,(d) 显示 X-Z 平面上微层压复合材料断裂的 SEM 图像,(e) 断裂 FL 的 SEM 图像,(f) 断裂 AL 的 SEM 图像。
图 18.
(a)SDSS 基质复合材料和微层压复合材料的 LUR 曲线,(b)微层压复合材料的流动、HDI 和有效应力随真实应变的变化,(c)SDSS 基质复合材料的流动、HDI 和有效应力随真实应变的变化,(d)各种样品的真实应力-应变/应变硬化速率曲线。
图 19.
(a-b) 显示双峰晶粒和双层晶粒的示意图;变形微层压复合材料:(c) TEM BF 图像显示 FL 或 TA 中具有循环流动特征的奥氏体晶粒,(d) TEM BF 图像显示 TA-II 中的双层晶粒,(e) TEM BF 图像显示奥氏体晶粒中形成堆垛层错。
在本研究中,我们成功开发并展示了一种实现金属材料强度-延展性协同效应的有效方法。这是通过制造微层压 DSS 基质复合材料实现的,该复合材料结合了来自三种材料的多个异质结构,并利用了激光粉末床熔合 (LPBF) 技术。
(1) 通过精心设计和优化,成功获得了多种异质结构,形成了微尺度奥氏体和铁素体层的交替堆垛。
(2) 发现奥氏体层内生成双峰奥氏体晶粒,铁素体层内及附近生成细小的复式晶粒。特别是,微米级 TiC 颗粒和TiCxNy纳米颗粒的存在可以促进微层状复合材料在变形初期 HDI 应力的增加,而双峰和复式晶粒也可以促进复合材料中 HDI 应力的增加。
(3) 通过制备具有优异力学性能(UTS:~1092 MPa;UE:~17.9 %)的 DSS 基复合材料,证明了微层状复合材料中未使用粉末的可回收性。
(4) 微层压复合材料表现出优异的极限拉伸强度 (~1.06 GPa) 和较高的均匀伸长率 (~21.9 %),而且发现微层压复合材料具有良好的各向同性拉伸性能,非常有价值。
相信所开发的先进制造方法可以在其他金属材料中获得更重要的应用,实现其强度-延展性的协同作用的显著提高。
免责声明:本网站所转载的文字、图片与视频资料版权归原创作者所有,如果涉及侵权,请第一时间联系本网删除。
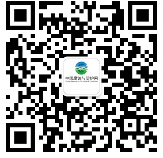
官方微信
《腐蚀与防护网电子期刊》征订启事
- 投稿联系:编辑部
- 电话:010-62316606
- 邮箱:fsfhzy666@163.com
- 腐蚀与防护网官方QQ群:140808414