摘要 钢材由于具有高强度和耐热性等优异性能而广泛应用于各种零构件,在服役过程中通常面临较为严重的腐蚀问题。CO2腐蚀是钢材应用领域中较为常见的一种腐蚀失效方式。通常,CO2对钢的腐蚀行为表现为其溶于水后产生的碳酸腐蚀,但在高温环境中,CO2可直接使钢表面氧化,同时伴随渗碳现象发生,钢的力学性能与耐腐蚀性能均会因此大幅下降。然而,目前关于钢在高温CO2环境中的腐蚀行为研究缺乏相关系统总结。综述有关高温CO2环境下钢的腐蚀机理,总结高温CO2环境中温度、压力以及环境中存在的其他杂质气体对腐蚀方式及机理的影响规律,归纳已有的高温CO2氧化与渗碳腐蚀模型的发展状况,概述目前关于抗高温CO2腐蚀的钢材涂层类型及其防护效果。研究表明,由于含Cr钢在高温CO2环境中形成的Cr2O3层相较于Fe氧化物层更加致密,Cr元素的存在通常有利于钢的耐腐蚀性能。而环境中,温度与压力的升高以及杂质气体的存在往往会加重钢的CO2腐蚀,但这些因素的影响规律会随着钢的种类及服役环境的变化而变化。目前关于钢的CO2腐蚀模型主要为单一的高温氧化模型或者渗碳模型,可预测氧化物层厚度或渗碳深度,但无法准确预测同时发生氧化和渗碳行为的钢的腐蚀寿命。综述相关研究现状不仅能指出现有研究的不足及未来研究的展开方向,还可为高温环境中钢材抗CO2腐蚀防护措施的选择及其长周期安全服务寿命评价提供全面理论依据。
前言 钢材由于其高强度、耐热性、相对成本较低等特点广泛应用于油气采集、CO2捕捉运输管道以及超临界CO2火电机组等诸多部件。然而,这些钢材部件通常是在CO2环境中服役,导致其使用寿命容易因CO2腐蚀而降低,特别是在高温下,CO2可在无H2O等其他物质参与的情况下对钢造成腐蚀。目前,有关高温下钢的CO2腐蚀的研究工作重点在于评估不同钢种在不同CO2腐蚀环境下的腐蚀动力学及机理,这些研究工作比较零散,缺乏系统总结。 高温环境下,CO2对钢的腐蚀表现为氧化与渗碳作用。具体而言,CO2会与钢表面的Fe、Cr元素反应生成Cr2O3 、Fe3O4、(Fe, Cr)2O3等氧化物,这些氧化产物层通常具备对钢的保护作用。而由于Cr2O3对于氧化与渗碳防护性能优于Fe3O4,不同钢种的Cr元素含量对其耐腐蚀性能至关重要。伴随氧化过程发生的渗碳作用会同时降低钢的耐腐蚀性能与力学性能:碳化物的形成会消耗参与形成保护性氧化层的合金元素(如Cr元素)以及氧化层与金属基体界面处存在的无定形碳累积层会导致氧化层与基体的附着力降低,进而导致保护性氧化层发生剥落;渗碳后产生的碳化物会降低钢的延展性,从而削弱钢的抗疲劳与抗蠕变能力。此外,CO2对钢的腐蚀作用受到服役环境中的诸多因素影响。其中,温度对腐蚀的影响在于能改变氧化速率或氧化层成分,而压力则主要影响渗碳作用,温度与压力的提升通常会促进CO2对钢的腐蚀作用。当腐蚀环境中存在其他杂质气体,如H2O、O2,钢的CO2腐蚀行为会不同于纯CO2环境下,且它们的影响规律会随着腐蚀环境条件和钢种的变化而变化 。 准确评估高温CO2环境下钢的腐蚀速率对设备的设计与维护十分重要:预设较低的腐蚀速率可能导致相关部件在服役过程中突然失效以及设备损坏,而过高的腐蚀速率的评估可能导致不必要的成本。然而,目前关于高温下金属材料CO2腐蚀行为的预测模型的研究进展较慢。部分研究人员分别针对氧化与渗碳作用进行研究,实现了对一定腐蚀时间的氧化物厚度或渗碳深度、浓度的预测计算,但尚未有研究考虑氧化与渗碳的耦合作用,从而无法准确预测钢的CO2腐蚀寿命。因此,高温下钢的CO2腐蚀预测模型亟待进一步系统研究。同时,由于高温下钢在CO2环境中的耐腐蚀性低于Ni基合金等材料,部分研究者试图通过优化钢的制备工艺或对钢材进行表面处理等方式提高其耐蚀性。涂层被认为是提高钢的耐蚀性而不显著降低其机械性能的一种经济有效的解决方案,因此大量科研人员成功采用可提高材料耐腐蚀性能的 Ni、Al、Cr等金属元素为主要成分制备了一系列涂层,有效提高了钢在高温环境下的抗氧化与渗碳性能。 鉴于以上研究背景,本文综述了高温下钢的CO2氧化渗碳腐蚀机理,阐述了腐蚀环境中多种因素包括温度、压力及其他杂质气体对钢的CO2腐蚀的影响规律,归纳了目前已有CO2腐蚀模型的发展状况及应用背景,总结了目前关于抗CO2腐蚀的钢材涂层类型及其防护效果,以期为高温环境中钢材的抗CO2腐蚀防护措施的选择及其长周期安全服务寿命评价提供全面理论依据。
2. CO2高温氧化渗碳腐蚀机理
当服役温度达到400℃及以上时,钢在CO2环境下的腐蚀行为通常是由氧化渗碳导致的。具体而言,CO2首先会与钢表面的Fe、Cr等金属元素(N)反应生成金属氧化物并释放CO或C,而CO可进一步分解为C和CO2或O。这些反应过程所产生的C往往积聚在氧化层与基体界面,在高温下可扩渗入钢体内部,形成碳化物。氧化渗碳相关反应式如下:
在氧化渗碳作用下,钢在高温CO2环境中腐蚀后会由外到内形成多层氧化层以及渗碳区。其中氧化层的成分与结构会强烈受到钢中Cr元素含量的影响,如图1所示。一般而言,当Cr元素含量为9wt.%~12wt.%以及更低时,氧化层主要由较为疏松的Fe3O4 、Fe2O3等Fe氧化物外层、Fe3-xCrxO4等FeCr复合氧化物内层以及内部氧化区(Internaloxidation zone,IOZ)组成,如图1a所示。然而,即使氧化物层的成分相同,钢成分中Cr元素含量更高往往会导致内层的FeCr氧化物层中Cr元素浓度更高,有效减缓钢基体中的Fe元素向外扩散,从而导致更低的氧化速率。当Cr元素含量大于17wt.%时,钢的氧化产物以表面Cr2O3层为主,而在更高的腐蚀温度或更长的腐蚀时间下,Cr2O3层部分区域会出现Fe氧化物或FeCr氧化物形核,如图1b所示。表1总结了相近腐蚀条件下不同Cr元素含量对钢氧化层的影响结果。对于渗碳层而言,碳往往与基体中的Cr元素反应产生Cr3C、Cr7C3和Cr23C6等碳化物,这一过程会阻碍Cr元素向外扩散,且这些脆性碳化物会使氧化层容易脱落,进而导致钢的耐腐蚀性降低。此外,在疲劳或蠕变载荷下,碳的沉积与晶间碳化物的形成会成为裂纹的潜在来源。可见,Cr元素含量很大程度上决定了钢在高温CO2环境中的耐腐蚀性能:高Cr钢所形成的Cr2O3层相较于Fe氧化物层更加致密,对氧化及渗碳作用的防护性更好。而钢中的Mn、Si等其他元素是否对其耐腐蚀性能存在一定影响,有待进一步研究。 3. 影响CO2腐蚀的因素 通常,影响高温CO2腐蚀的因素包括温度、压力以及服役环境中不可避免的H2O、O2等杂质气体。其中,温度和压力是影响CO2腐蚀最重要的参数,通常高温高压会促进氧化与渗碳作用,而 H2O这些杂质气体在较高温下可主导CO2腐蚀进程。然而,这些因素对钢的CO2腐蚀的影响规律并不确定,会随着钢的种类及服役环境的变化而变化。 3.1.温度 当温度低于400℃时,钢与纯净的CO2很难发生反应,只有在其他杂质参与下才会发生腐蚀。而当温度高于400℃时,纯净的CO2可直接腐蚀钢,且升高温度会促进腐蚀进程。例如,FURUKAWA等研究了400~600℃下12Cr钢在压力为20MPa的CO2环境中的腐蚀性能,发现尽管温度增加会加剧12Cr钢的氧化腐蚀程度,但是其表面氧化层结构变化甚微,主要由厚度为 50μm的Fe3O4外层、50μm左右厚的复合氧化物 (Fe1-x , Crx)2O3内层以及厚度小于10μm的IOZ组成。可见,对于12Cr钢而言,温度由400℃升高至600℃主要影响了钢的氧化速率,并未使得钢表面氧化层成分及结构发生明显改变。但有研究表明,温度对钢的CO2腐蚀的影响规律会随着钢中Cr元素含量变化而变化。如ZHU等通过研究Cr元素含量为2.25wt.%的铁素体钢T22与Cr元素含量为8.63wt.%的铁素体-马氏体双相钢P92在550和600℃、15MPa下的CO2腐蚀行为,发现在不同温度下两种钢的氧化层成分相似,均由外层Fe3O4和内层(Fe, Cr)3O4组成。不同的是,随着温度由550℃升高至600℃,具有更高Cr元素含量的P92钢中,FeCr氧化物内层的Cr元素会抑制Fe离子的扩散速度,降低氧化速率,表现出更好的耐蚀性能。但随着氧化时间的延长,P92钢表面氧化层出现局部脱落,钢被再次腐蚀氧化,所生成的氧化层仍由Fe3O4外层与(Fe, Cr)3O4内层组成。可见,对于主要氧化产物为Fe氧化物的钢,温度主要影响其腐蚀后的氧化层厚度,对其氧化层成分影响不大。而其中Cr元素含量相对较高的钢材受温度的影响较小,通常具备更低的腐蚀速率。同时值得注意的是,在更高的环境温度下,氧化物与基体之间较大的热膨胀系数差异会促进氧化层的脱落,进而导致钢材被再次氧化,显著增加其腐蚀程度。 对于高Cr(>17 wt.%)含量的钢种而言,其被腐蚀后形成的氧化层以Cr2O3为主,温度会显著影响氧化层成分。例如,在550℃下,316不锈钢的氧化腐蚀表面主要被较薄(<1μm)的单层富Cr氧化物覆盖,但局部区域会存在5μm 左右厚的Fe氧化物,而在750℃下,316不锈钢腐蚀程度明显加重,但其腐蚀产物主要为3~5μm厚的Fe3O4层,且部分区域存在成分为Fe氧化物与FeCr复合氧化物的双相结构形核。因此,尽管温度对钢腐蚀的影响主要在于温度升高会加快钢的氧化速率。但对于高Cr钢而言,较高温度下Fe3O4等Fe氧化物生长速度通常大于Cr2O3生长速度,其表面氧化物会由富Cr向富Fe转变。YANG等对比研究了500~600℃下T91钢与316钢的CO2腐蚀行为,发现在相同腐蚀时间下,温度升高会导致T91钢氧化层厚度增加以及更多孔洞和裂纹等缺陷形成,但对其氧化层成分影响不大,如图2所示。相比之下,316钢在500℃腐蚀后的表面氧化产物为50~80nm厚的Cr2O3层,仅部分区域存在少量簇状Fe氧化物,而316钢在600℃下的腐蚀产物是由成分为Fe2O3与Fe3O4的外层和含Cr2O3的内层组成的约2μm厚的双层结构。由于Fe2O3与Fe3O4等Fe氧化物层相较于Cr2O3层对基体防护作用较差,因此可根据钢在不同温度下的氧化行为决定其适用温度范围,并将钢的成分与工作温度作为参数纳入腐蚀模型以便后续研究。
对于高温CO2腐蚀过程中的渗碳行为而言,BRITTAN等发现P92钢在450℃下渗碳深度超过 200μm,而550℃下渗碳深度约为100μm。对于此,BRITTAN等提出这是因为较高温度下碳化物的析出与生长更快,从而导致碳元素难以扩散至更深位置。并且金属与氧化物界面附近的碳密度较高、碳化物粗化更明显,使得该区域容易萌生裂纹,进而导致P92钢力学性能明显下降。然而,由于温度对于CO2腐蚀的影响主要体现在改变氧化速率与氧化成分,因此目前有关温度对于渗碳行为的影响规律的相关报道较少,有待进一步展开。 3.2.压力 (PCO2) 高温腐蚀环境的压力(PCO2)对钢的CO2腐蚀也具有重要影响。通常,压力增加会促进渗碳作用,对氧化作用的直接影响较小 。例如,PINT等对比了同一温度不同压力(0.1、30MPa)下钢的CO2腐蚀行为,发现压力的改变对于氧化增重以及氧化层的厚度几乎没有影响。相比之下,通过研究0.1、5和10MPa下CrMoV钢的CO2腐蚀氧化行为,BIDABADI等发现,当环境压力从0.1MPa增加到5MPa时,CrMoV钢的氧化产物成分相似,外层均为Fe3O4,内层则为Fe3-xCrxO4与Fe2-xCrxO3。但5MPa条件下,其表面氧化物更加均匀致密,且碳沉积行为更加明显,进而降低了氧化速率。当压力10MPa时,CrMoV钢的表面氧化层由外层的 Fe2O3与Fe3O4 、内层的碳单质及少量Fe3-xCrxO4和Fe2-xCrxO3组成。此外,三种压力条件下CrMoV钢的渗碳区均存在非晶态碳,而石墨则主要存在于5和10MPa下的渗碳区,且氧化层内积碳通过限制Fe元素向外扩散与氧化气体向内输运而降低氧化速率。可见,随着压力的提高,钢的渗碳作用更加明显,碳积累加强,有利于阻止进一步腐蚀。此外,在较低的压力范围内,CO2压力提高可提供足够的氧分压,进而促进更具保护性与稳定性的氧化物生长 。然而,其他研究中却发现了不同结果,ROUILLARD等研究发现,随着压力从0.1MPa上升到25MPa,550℃下T91钢的氧化程度变化不大,但其渗碳速率则提高了50%~60%,进而导致氧化物层中有更多孔洞形成,如图3所示。该研究工作认为较高的孔洞密度与IOZ下方较高的碳化物密度有关。可见,在较低压力范围内,CO2压力的提升可通过促进形成保护性氧化物及基体内部少量碳累积而有效阻止氧化,但压力提高对于腐蚀的主要影响仍在于较高的CO2压力可促进钢基体与氧化物内部的渗碳作用,并且大量碳化物及非晶碳的累积会使得氧化层孔洞明显增加。此外,CO2作为碳单质的重要来源,CO2压力的增加会使氧化物/基体界面的碳积累更明显,但对渗碳深度的影响规律还有待进一步研究。
此外,温度与杂质气体等其他环境因素也可能改变压力对腐蚀的影响作用。BIDABADI等研究了温度(500~600℃)和压力(0.1、10MPa)对CrMoV钢渗碳行为的影响,发现在0.1MPa不同温度下CrMoV钢的内氧化层的碳沉积浓度相差不大,而10MPa下的碳沉积浓度随着温度从500℃增加至550℃而增加,但会随着温度继续升高至600℃时而降低。这是因为在550℃、10MPa条件下,CrMoV腐蚀产物中含有富Fe的M3C碳化物,且氧化物/钢界面下的钢晶粒也会被分解为富Fe颗粒,而M3C碳化物和富Fe颗粒会作为CO2分解产生碳反应的活性催化剂,促进碳沉积。总之,CO2压力增加会导致渗碳速率提高,而尽管渗碳累积在一定程度上会通过阻碍钢内部元素扩散而进一步降低钢的氧化速率,但渗碳行为会影响钢材本身性能以及可能导致氧化层脱落,因此较高压力下钢材的使用寿命反而会被较大程度缩减。此外,在高温环境下,压力升高至CO2的临界压力时,CO2状态将转变为超临界CO2,其物理性质也将发生一定改变,因此对于相关研究中所观察到的结果是否与CO2状态的改变有一定关联,仍有待进一步探究。 3.3.杂质气体 3.3.1 O2 O2可能主导钢的CO2腐蚀进程,但其影响规律较为复杂。通常,O2可以促进氧化物的生成,增加氧化层厚度。例如,在有无空气两种条件下,LEHMUSTO等发现尽管31钢表面形成的氧化层结构均为典型的Fe氧化物-FeCr氧化物双层结构,但少量空气的存在会使得316钢的氧化增重增加。同时,在纯CO2环境中,316钢的氧化内层与外层厚度比为1∶1,而存在残余空气时,外氧化层变得更厚,内层则变得更加均匀。与之相反,SS310钢在有无O2的CO2环境氛围下的氧化表面均覆盖较薄的Cr2O3层,且存在少量成分为Fe3-xCrxO4的氧化物,但含O2环境下形成的Cr2O3层更薄、FeCr氧化物较少。如图4所示,O2的存在使得渗碳深度由4μm 减少至 1.5μm,并导致氧化层与再结晶层界面处的碳层几乎消失。这是因为在纯CO2环境下形成 Cr2O3时,钢的晶界处存在碳偏析,进而限制了Cr2O3的生长,导致Cr2O3晶粒细化,从而有更多晶界为氧化性气体提供扩散路径,最终形成更厚的氧化层 。相比之下,CO2的存在会降低O2−空位的密度,这有利于表面均匀的Cr2O3形成,增加其稳定性,进而抑制表面氧化物形核。
3.3.2 H2O H2O的存在往往会促进高温下钢的CO2腐蚀进程。LI 等发现,高温下H2O的存在会使得SS310钢表面的腐蚀产物Cr2O3转化为易挥发的CrO2(OH)2 ,导致Cr元素损失,进而促进氧化以及渗碳,相关反应式如式(5)所示 ,但在仅含H2O作为杂质的CO2环境中,H2O可以阻断钢表面氧化层上对CO2/CO等物质的一些吸附位点,因此其对于渗碳作用存在一定抑制作用。此外,H2O的存在会对钢表面形成的Fe3O4氧化层存在破坏作用,如式(6)所示。而当O2与H2O同时存在时,钢的CO2腐蚀将变得更加严重。例如,通过研究9Cr钢、12Cr钢和316H钢在不同温度下(450~650 ℃)含有1%O2和 0.1%H2O的CO2环境中的氧化腐蚀行为,PINT等发现450℃下三种钢的氧化层成分与纯CO2环境下相同,但它们的氧化层变厚、氧化增重更加明显。而当温度为650℃时,三种钢的氧化层成分发生明显改变。其中,316钢表面的腐蚀产物由较薄的Cr2O3层转变为Fe2O3、Fe3O4等Fe氧化物层,而9Cr钢和12Cr钢表面的腐蚀产物则为内层Fe3O4 、(Fe,Cr)3O4和最外层Fe2O3层组成的三层氧化结构。相反,KUNG等发现在有无O2与H2O作为杂质气体的两种环境中,Grade 91(Gr. 91)钢表面的氧化层均由外层 Fe3O4和内层(Fe,Cr)3O4组成,且内外层厚度相近,但在含杂质气体的CO2环境下,该氧化层总厚度约为15μm,而在纯CO2环境中腐蚀300h后,Gr. 91钢氧化层总厚度增加至30μm,氧化增重与渗碳深度均有所增加。这是因为O2和H2O共存时,较高的氧分压有利于更多保护性氧化物的形成,进而导致氧化层厚度降低。然而,目前有关H2O的影响研究主要集中在H2O与其他杂质气体共存环境,而针对于单一H2O作为杂质气体存在于高温CO2环境中的研究较少,有待进一步展开。
3.3.3 SO2 SO2的存在对钢的CO2腐蚀也有重要影响。OLEKSAK等通过在含H2O 、O2的CO2环境中添加0.1%SO2研究了SO2对钢腐蚀的影响规律,发现SO2的影响机理会随着钢中Cr元素含量变化而变化。对于Cr元素含量低于9wt.% 的Gr. 91钢而言,其表面氧化层在有无SO2条件下均由外层Fe2O3/Fe3O4和内层Fe3-xCrxO4组成,而SO2的存在会使得氧化层内部存在少量硫化物,导致与H2O和CO2相关的腐蚀剥落、氧化以及渗碳行为程度有所降低,但其氧化速率并无显著变化。而对于Cr元素含量高于9wt.%的347H钢与310S钢而言,二者在不含SO2的腐蚀环境中会形成薄的Cr2O3层,而SO2的存在会导致硫元素通过氧化物的局部渗透Cr2O3层,进而促进Fe3O4等富Fe氧化物的形成,如图5所示。此外,通过对比不同SO2浓度下FeCr合金在CO2-H2O环境中的腐蚀行为, YU等发现在不含SO2环境下,FeCr合金内部较深处有晶间碳化物形成,并渗透到整个试样,而0.1%SO2的存在则会对合金渗碳行为有着明显抑制作用,但随着SO2浓度从0.1%增加至1% , FeCr合金氧化物层下的晶间渗碳速率略有增加,这是由于增加的硫化物 - 氧化物相界为碳扩散提供了更多路径。表2总结了部分钢在不同杂质气体环境中的氧化增重速率。
3.3.4 多种杂质气体环境 如前所述,O2、H2O 、SO2作为CO2高温腐蚀环境中主要存在的杂质气体,对腐蚀进程的影响并不相同。其中,O2主要作为氧化过程中氧元素的直接来源,能促进钢表面氧化层形成,但其作用会因温度升高而变化。将H2O作为单独的杂质气体进行讨论则较少,通常是将其与O2或SO2共同讨论。如式(6)所示,H2O对Fe3O4保护层可能存在破坏作用,并且QUADAKKERS等研究中提到,H2O对保护性Cr2O3氧化层形成的不利影响相较于CO2更为明显。同时,由于H2O气体分子在Cr2O3上的吸附趋势高于CO2,H2O作为杂质气体对渗碳作用存在抑制效果。相比之下, SO2对CO2腐蚀进程的影响主要体现在其对高Cr钢表面Cr2O3氧化层形成的阻碍作用:SO2的存在可促使氧化物由富Cr向富Fe转变,且在杂质气体含量较低的情况下,SO2对于钢的CO2腐蚀程度影响相较于H2O与O2更加明显。例如, OLEKSAK等发现在95%CO2、4%H2O、 1%O2 、 0.1%SO2的环境下,尽管SO2含量更低,但由于硫元素推动氧化物由富Cr向富Fe转变,显著提升了奥氏体钢的氧化速率,而H2O和O2对所有Fe合金氧化行为的影响相对较小。 事实上,在CO2腐蚀环境中,杂质气体往往多种并存,且由于气体间相互协同效应,其影响作用可能发生改变,甚至相反。如前所述,H2O与O2同时存在时可能发生式(5)代表的反应,进而破坏Cr2O3氧化层。类似地, YU等发现在CO2环境中单独添加H2O或SO2作为杂质气体, FeCr合金腐蚀程度均更为严重,而当加入H2O与SO2的混合气体时,FeCr合金表层的氧化层不再分离脱落,说明混合气体对其具备一定保护作用。这是因为当SO2作为杂质气体时,硫元素容易吸附于氧化层,晶界处CrSx的形成促进Cr元素向外扩散,加速氧化物层的形成,铬化物生长无法持续下去,进而造成铬化物氧化层分离。而气体环境中同时含有H2O和SO2时,H2O会与CO2和SO2竞争合金表面与氧化物晶界内的吸附位点,同时H2O的衍生物将进入氧化层,改变硫元素在氧化层中的化学性质,降低了硫元素的吸收程度。在此情况下,相应的CrSx形成水平会大幅降低,导致Cr元素向外扩散的增强作用非常小,因此氧化物生长较慢,合金元素的扩散可以支持氧化物的持续生长。但值得注意的是,该研究在对H2O与SO2的协同效应进行探究时,H2O含量高达20%,因此较低的H2O含量与SO2气体是否仍存在较为明显的协同效应有待进一步研究。对于三种气体共存作为杂质气体环境时,目前相关研究认为H2O与O2对CO2腐蚀进程具有一定促进作用,而SO2的加入则会导致氧化层中形成硫化物,从而阻碍腐蚀氧化进程及氧化层的脱落。 3.4.多条件综合影响因素 尽管O2、H2O 、SO2对钢腐蚀过程中的渗碳行为均存在一定的抑制作用,但这三种杂质气体对钢腐蚀的影响主要表现在作为钢的氧化过程中的部分氧元素来源,特别在杂质气体含量较低的条件下。例如,ROUILLARD等在550℃、 25MPa的CO2环境中对T91钢进行氧化试验时发现,环境中含有0.6×10−3%H2O与0.2×10−3%O2,而在T91钢表面形成的20µm厚的氧化层中,仅有约0.25µm 厚的氧化物中的氧元素来源于O2与H2O。此外,由于钢的氧化速率与表面氧化物生成速率在不同温度下差异较大,不同温度下杂质气体的影响作用可能完全不同。例如,在两种温度(350 、 650℃)与两种气体环境(研究级CO2(RG-CO2, > 99.999% )、工业级CO2(IG-CO2 ,>99.98% ))下对多种钢材进行的腐蚀试验中, WALKER等发现多种钢在两种温度条件下所得的氧化增重结果完全相反:350℃下钢在IG-CO2中质量变化略大于RG-CO2环境,而650℃下钢在RG-CO2中质量变化反而略大于IG-CO2环境。这可能是因为较低温度下杂质气体对钢腐蚀进程的促进作用更为明显,同时表明不同温度下杂质气体对钢的CO2腐蚀的影响与其含量也密切相关。此外,QUADAKKERS等发现在没有添加O2的CO2-H2O气氛中,310N奥氏体钢在550~700℃下腐蚀时均会有极薄且粘附良好的富Cr氧化层形成,而当加入3%的O2后,550与600℃下310N钢的腐蚀产物仍为富Cr氧化层,但其在650~700℃下的腐蚀产物则出现了局部富Fe氧化层。可见,即使杂质气体成分相同,由于气体间交互协同作用,多种气体共存情况下温度改变对钢腐蚀进程造成的影响也会存在差异。 如前所述,在纯CO2环境中,压力对钢腐蚀过程中的氧化行为影响较小,而当环境中存在较高含量的杂质气体时,压力对钢的氧化过程影响会变得更为明显,并且此时压力的影响也会随温度与钢材种类变化而变化。例如,在杂质气体含量较低的RG-CO2与IG-CO2环境中,PINT等发现304H、310H等多种钢的腐蚀速率与腐蚀产物随着环境压力从0.1MPa增加至30MPa并无明显变化,而在含有1%O2、0.25%H2O的CO2环境中,30MPa的环境压力下304H 、310H等钢材的腐蚀速率明显高于RG-CO2与 IG-CO2两种环境。此外,研究发现环境压力不仅能改变杂质气体对钢腐蚀过程中氧化行为的影响,较高的压力还会促进H2O与O2存在时Cr2O3的挥发行为,从而破坏致密的Cr2O3氧化层,这可能导致Cr2O3层无法有效阻碍CO2等气体渗入钢材内部,进而促进钢腐蚀过程中的氧化与渗碳行为。类似地,当环境压力达到CO2的临界压力,即在超临界CO2环境中,高温下部分杂质气体一定程度上能溶于CO2流体中,进而导致杂质气体对钢腐蚀进程的影响发生变化,而目前关于超临界环境或其他压力条件下杂质气体对钢的CO2腐蚀的影响研究仍然较少。综上所述,在多种杂质气体共存的高温CO2环境中,温度、压力和杂质气体含量等诸多因素对钢的CO2腐蚀的影响规律及机理仍不明晰,亟待进一步研究。 4. CO2氧化渗碳腐蚀模型 事实上,高温下钢的CO2腐蚀行为会涉及到氧化与渗碳同时发生。基于大量试验数据,科研工作者观察到氧化物生长速率与渗碳速率符合抛物线动力学,进而建立了高温氧化模型和渗碳模型等数学模型来预测钢的氧化与渗碳行为。 4.1.高温氧化模型 如前所述,高温下钢的CO2腐蚀过程中氧化行为通常是钢中的Fe和Cr元素被氧化,其氧化增重速率符合抛物线动力学。因此,通过在400~600℃下对9Cr钢和12Cr钢进行了长达8000h的氧化增重试验, FURUKAWA等将试验所得的增重数据与根据抛物线方程计算得出的近似曲线进行对比,观察到良好的一致性,相关抛物线方程如下:
式中, ∆W为增重(g/m2), K p 为氧化系数(g /(m2 · s−1/2) ),t 为时间(s)。氧化系数主要与温度有关,与压力无关:
式中, K0为常数, Q为表观活化能(J/mol), R 为气体系数(J/(K·mol)), T为绝对温度(K)。基于模型和试验结果, FURUKAWA等认为9Cr钢与12Cr钢表面的双层氧化层的外层是由金属元素向外扩散形成,而内层是由O2向内扩散形成,且体积扩散比为1:1。由于O2向内部扩散的腐蚀效果等同于钢表面氧化前的金属损失,因此认为可通过所测得的氧化增重来计算钢表面腐蚀量Lm,计算公式如下:
式中, Cp为重量增加与氧化物厚度之间的比例常数,Rc为金属损失厚度与氧化物厚度比值。虽然这一计算无法包括表面氧化层的渗碳与剥落引起的性能退化,但预测结果可作为初步设计的参考指标。值得注意的是,由于这一模型是基于试验中所观察到的增重数据符合抛物线方程的现象而建立的,因此当腐蚀环境中存在较高含量杂质气体影响腐蚀进程时,其预测结果可能存在偏差。此外,如前所述,当碳累积于氧化物层中,基体合金元素向外扩散的行为会受到阻碍,其氧化速率进而降低,而该模型中并未将这一因素考虑在内,模型准确性有待提高。对于氧化产物主要为Cr2O3氧化层的钢种,腐蚀寿命预测可以通过分离氧化时间tB评估,即Cr元素耗尽界面达到钢一半厚度界面的时间, GUI等认为可通过计算Cr元素的体积扩散系数和抛物线生长速率常数来计算分离氧化时间。在抛物线型氧化层生长动力学的前提下,可根据菲克第二定律推导出t时刻在氧化物与基体界面下z深度处的Cr元素浓度 C(t, z) ,计算公式为:
式中, Cc为试样一半厚度处Cr元素的浓度( wt.% ),Mcr为Cr的原子质量(kg), Ma为原子质量(kg),Vs为氧化物占合金的体积比, KC为氧化物生长速率(g/m2·s-1/2),Dcr为Cr元素的扩散系数,n为常数,z为深度(cm), w为试样厚度的一半(cm)。 GUI等利用该模型对两种钢不同深度的Cr元素浓度进行拟合并计算腐蚀量,拟合结果与试验结果误差较小,进而判断此模型可将分离氧化时间作为预估寿命进行预测。然而,由于较高温度下高Cr 钢的表面氧化物可能由富Cr向富Fe转变,因此该模型仅限于一定温度范围内使用。此外,即使钢表面主要形成氧化物为Cr2O3,但当其Cr元素含量较低时, Fe氧化物形成后同样具备一定保护性,而该模型仅考虑材料中Cr元素含量对于基体的防护作用,这将导致模型预测结果与实际寿命相差较大,仅可作为寿命极限的保守估计。 GONG等提出了如图6所示的氧化物生长模型(Oxide growth model, OGM)。图中,υmag 、 υsp为对应Magnetite 、Spine氧化物层界面相对于原始合金 / 气体界面的速度,C表示图中对应Fe、Cr、O元素的浓度。该模型认为Fe元素向外扩散形成外层Fe3O4层,O2向基体扩散形成内层尖晶石层,但由于O2分压较低,因此, CO2将替代O2在这一过程发挥作用。各氧化层厚度计算公式如下:
式中,Cki和Jki分别是i元素在相态k的体积固定参照系中的界面浓度(wt.%)与界面通量(kg/s ),且sp代表Spine层, mag代表Magnetite层,μki 为i元素对应 k 界面的化学势(J/mol ), A代表图中Spine氧化物层与合金界面,B代表气体与Magnetite层界面,Xmag 、 Xsp分别为对应Magnetite 、Spine氧化物层厚度(µm)。MO、 MFe为对应元素的相对原子质量,t为时间(s)。 同时,由于观察到的内层是多孔的, GONG等进一步提出气相分子输运可作为可用空间模型的一部分,且CO2通过气孔与分离气孔的氧化物晶界传输。该模型计算得到的氧化层厚度与试验结果较吻合,且由模型图可看出,该模型适用于形成双层Fe氧化物层的低Cr钢。
针对涉及到氧化物剥落的腐蚀行为, KUNG等进一步优化了已有的电力研究协会(Electric powerresearch institute, EPRI)氧化剥落模型 ,进而成功将用于S-CO2布雷顿功率循环的热交换器设计中常见参数作为模型的相关参数。这些参数包括额外的材料特性、流动通道的物理构型、相关的传热和流体流动标准。KUNG等通过模型成功预测了氧化膜脱落质量,进而认为在 S-CO2热交换器流道表面生长的氧化层是无应力的,但合金基体与氧化层之间的热膨胀系数差异会导致低温下二者之间存在应力。此外,合金几何特征引起的机械约束和系统压力变化也会导致应力产生。而当产生的应力超过某个临界值,且氧化产物足够厚时,氧化产物可能被破坏,进而发生剥落。目前,针对钢在高温CO2环境中的氧化模型主要是基于对其他环境中已有模型进行优化而得,较为依赖试验所得数据,因此后续相关研究中有待将温度、压力等环境参数与材料成分等因素纳入模型,以理论基础结合实际所得数据综合评估钢在高温CO2环境下腐蚀情况,进而较准确地进行寿命预测。 4.2.渗碳模型 ROUILLARD等提出高温下钢的CO2腐蚀过程中渗碳行为是由元素扩散控制的,通常发生在氧化物与金属界面,具体是由CO2/CO通过氧化物层的扩散速率和CO2与金属的反应速率共同控制。基于此, GHENO等采用局部平衡模型来描述碳氧活性,并将这一模型应用于氧势较低的氧化物/合金界面,成功预测出了足够高的碳活度值,进而提出CO2分子在氧化层的任意点存在热力学平衡。而内部渗碳深度可用稳态抛物线动力学描述:
式中, Xc为渗碳深度(cm),K(i)p为内部渗碳速率(cm2/s),t 为时间(s)。其中K(i)p的评估是基于所有Cr元素不进行扩散而均以碳化物形式析出的前提计算得到的,其计算公式如下:
式中, Dc为碳扩散系数(cm2/s),N(s)c为合金表面溶质碳的摩尔分数,N(o)Cr为原始合金Cr元素的摩尔分数, v为碳化物CrCv的化学计量系数, ε为扩散阻塞因子。而在外部氧化物层存在时,碳的表面分数N(s)c被界面分数N(i)c所替代。 然而,YOUNG等发现上述模型计算的低温下碳活度相较于试验测得数据高几个数量级,因此认为上述的热力学平衡并不存在。YOUNG等进而在氧化物 - 金属界面处增加了一个有限的碳注入速率,即碳注入金属的速率与平衡浓度和实际碳溶质浓度之间的差成正比,用来描述将碳的扩散考虑为碳化物析出时造成的损失,进一步作出结论:由于碳向金属相的转移相对缓慢,渗碳反应是一种非稳态行为。YOUNG等利用溶质碳在金属相内的正常扩散、碳化物的快速析出以及碳在金属相和析出相之间的平衡分配等规律,成功解释了观察到的碳渗透的抛物线动力学和碳转移的线性动力学:
式中,CMC溶质碳的浓度(wt.%), t为时间(s), D为扩散系数(cm2/s), Xc为渗碳深度(cm), β为常数。虽然该模型可根据氧化物/金属界面碳活度对形成碳化物数量进行一定准确度预测,但并未涉及对于渗碳深度的预测以及渗碳程度对钢性能的影响。目前针对S-CO2环境下渗碳的相关讨论较少,且大多数研究者关注点在于渗碳环境的产生以及碳转移通道等方面,因此,有关渗碳模型的相关研究亟待进一步展开,并且研究重点应在于渗碳程度对于钢材力学性能的影响以及由于渗碳导致氧化层脱落的临界点,进而打破由于渗碳作用而无法准确评估导致钢在高温CO2环境下腐蚀寿命的限制。 表3总结了上述高温下钢的CO2腐蚀氧化与渗碳模型及应用条件。可见,目前相关工作往往只建立了单一的氧化或渗碳模型。虽然这些模型可对氧化物层厚度、渗碳深度等进行预测,但由于腐蚀过程中氧化与渗碳同时发生,这些模型未能较为准确地预测高温CO2腐蚀环境中钢材的腐蚀寿命,因此建立同时涵盖氧化与渗碳共同作用的模型亟待进一步展开。 5. CO2腐蚀防护 涂层是提高钢在高温CO2腐蚀环境中服役寿命的有效途径。科研工作者对金属涂层的成分和制备工艺等因素进行了充分研究,并同时制备了复合涂层以达到更好的防护效果。由于Cr 、Al等元素在高温下形成的氧化物层可有效提高基体耐蚀性能,这些元素因而常被用作涂层的主要成分。 5.1.Al 涂层 镀Al是最常用的金属涂层之一。制备镀Al涂层过程中生产的氧化铝熔点高达2054℃,具备很好的高温稳定性,因此具有良好的抗高温腐蚀性能。例如, SCHULZ等采用溶胶-凝胶法在X20钢表面制备了氧化铝层,并分别在CO2-H2O-O2与空气环境下对其进行腐蚀测试,发现氧化铝层表现出良好的耐腐蚀性。然而,朱明等研究表明溶胶-凝胶法制备的防护涂层与基体的热膨胀系数不匹配,进而容易发生剥落和开裂,因此涂层与基体连接的紧密性也应作为涂层性能的重点因素进行研究。基于此, SCHULZ等提出可以考虑通过浸涂或喷涂的方式制备涂层。 KIM等采用磁控溅射法在一种氧化物分散强化铁素体-马氏体双相钢(Oxide dispersionstrengthened ferritic-martensitic, ODS-FM)表面沉积Al与Ni-Al两种涂层,并进行扩散热处理,发现两种涂层表面的Al2O3层均表现出良好的耐蚀性。其中Al涂层的氧化增重低于Ni-Al涂层,但Al涂层表面比较疏松且存在较多孔洞,导致Al2O3层易剥落,而Ni-Al涂层的表面较均匀,能够有效抑制Al元素向基体的扩散。KIM等在316不锈钢表面制备Al涂层与Ni-Al涂层过程中也发现类似结果,但由于650℃下形成氧化铝为过渡氧化铝,不能有效阻止渗碳反应的发生,导致碳可以穿透氧化铝层形成含碳层,如图7所示。基于此, KIM等对涂层进行了900℃的预氧化处理,使涂层内部在预氧化后形成更具保护性的α-Al2O3,进而获得耐腐蚀性能与防渗碳性能更优的涂层。相对于Al涂层,Ni-Al涂层中的Ni元素一定程度上可作为有效屏障而抑制Al元素向基体扩散,进而使得表面Al2O3更加稳定,显著提升涂层耐腐蚀性能,但有研究者认为通过在Ni-Al层与基体间添加中间层而制备的双层涂层可更加有效阻碍Al元素扩散。
ZHAO等和LI等采用电镀制备Ni-Al涂层,并添加一层Ni-Re层作为基体与涂层之间的中间层,以期抑制高温下Ni-Al层与基体之间相互扩散形成互扩散区(Interdiffusion zone , IDZ),进而避免涂层因Al元素含量过低而失效。在650℃下CO2环境中进行氧化试验后发现,无Ni-Re中间层的Ni-Al涂层中Cr和Fe元素的存在提高了Ni2Al3层与扩散区界面处Al元素的活性,导致内部Al2O3析出,同时脆性相(Cr, Al)、(Fe, Al)加速了裂纹与孔洞的形核和生长,从而加剧了扩散区(Diffusionzone , DZ)内部氧化的发生,导致涂层出现水平裂纹与断裂。而Ni-Re中间层起到了扩散屏障的作用,有效延缓了涂层与基体之间的相互扩散,减少了内部氧化物的形成,同时Ni-Re中间层的添加导致Ni-Al层与钢基体之间形成(NiAl)-Re结构,显著抑制了渗碳,如图8所示。因此,通过制备Ni-Al/Ni-Re涂层并进行预氧化处理,Al涂层的耐腐蚀性能有望进一步提高,但这种涂层与基体连接是否良好仍有待探究,同时可探究不同制备方式对涂层性能的影响。
图8 不同涂层在650℃CO2环境中腐蚀660h后的SEM截面图像与EDS元素线扫描结果 5.2.Cr涂层 镀Cr过程中产生的Cr2O3具有与氧化铝类似的性能特点,从而也广泛用作金属涂层制备工艺。NGUYEN等通过胶结充填法在T91钢分别制备了Cr 、Ni/Cr 、Al 和Ni/Al四种涂层,发现Cr2O3或Al2O3氧化层均能显著提高T91钢的抗氧化性,且在650℃下CO2-H2O环境中腐蚀1000h后,Cr涂层与Al涂层增重相近,但Ni/Cr涂层耐腐蚀性远远低于Cr涂层,而Al/Ni涂层性能则优于Al涂层。这是因为Ni/Cr涂层由外到内是由Ni-(Cr)、Ni-(Fe, Cr) 、 Fe-(Ni, Cr) 等多层组成,而 Ni-(Cr) 层中的Cr元素浓度会随着腐蚀时间延长降低到维持Cr2O3保护层增长所需的临界值以下,导致其性能相较于Cr涂层更差。相比之下, Al涂层中Al元素含量较高,提供于形成Al2O3层的Al元素损失可忽略不计,使得其与钢基体的相互扩散决定了反应过程中Al涂层的浓度,而Ni/Al涂层中的Ni中间层有效阻止了元素扩散,导致其性能优于Al涂层。此外,由于Al2O3的碳溶解度非常低,因此镀Al涂层抗渗碳作用明显优于镀Cr涂层。 利用磁控溅射法,KIM等在ODS-FM钢表面沉积制备了Cr涂层,发现其在进行热扩散处理后会形成一层约4μm厚的富Cr碳化物层及约20μm厚的扩散区。在650℃、20MPa下CO2环境中腐蚀500h后,无涂层的钢表面形成约100μm厚的氧化层,而涂层试样的氧化层仅为0.2μm,其扫描投射电子显微镜分析(STEM)如图9所示。同时,无涂层试样的氧化层下存在约370μm厚的渗碳区,导致钢几乎完全失去延性,而Cr涂层钢中并未观察到碳化物,可见Cr扩散涂层可以有效减少基体的渗碳。
5.3.其他涂层 除上述涂层外,其他涂层也对钢在CO2环境下耐腐蚀作用有明显提升作用。其中,通过在SS316LN不锈钢表面沉积Si涂层并在900℃对其进行热处理后, KIM等发现Si涂层在热处理过程中会与基体相互扩散,形成Fe5Ni3Si2相这一热力学稳定相,同时基体元素向Si涂层的快速扩散导致Si涂层中存在孔洞,而孔洞附近能观察到Mo元素的富集,但Si沉积涂层在S-CO2环境下形成了较厚的富Cr氧化内层与较薄的富Si氧化外层,二者仍能有效提高涂层耐腐蚀性。而针对钢在高温超临界CO2环境下的渗碳行为,BRITTAN等在316LN表面制备了不同厚度的Cu涂层,发现氧化腐蚀作用随涂层厚度增加而减弱,其中100μm以上的涂层可使得316钢氧化增重与Ni基高温合金相似,而连续完整的Cu涂层能将初始氧化行为转变为氧通过涂层的扩散行为,进而延迟了CO2对钢的氧化,最终减少了碳沉积总量。 可见,有关钢在高温CO2环境中腐蚀的研究工作仍集中于不同钢种及涂层的耐腐蚀性表现,但在实际服役过程中,涂层的其他性能同样至关重要。因此有关涂层力学性能及其对钢基体力学性能的影响研究有待展开,同时可通过理论计算与模拟优化涂层结构,为复合涂层制备提供一种新思路。 6. 结论与展望 CO2腐蚀是钢质结构件服役环境中较为常见的一种腐蚀失效方式。目前,钢在高温CO2环境中的腐蚀机理已较为明晰,但不同环境下或不同种类钢材的腐蚀程度或产物通常存在差异。针对此,科研工作者试图建立相关模型预测钢的CO2腐蚀行为,同时研究了不同涂层的制备工艺及防腐效果。综述了高温下钢的CO2腐蚀的相关研究进展,并进行以下结论: (1)温度与压力升高通常会加重钢的CO2腐蚀。其中,温度升高主要使氧化层更厚和高Cr钢氧化层成分发生改变,而压力主要影响其渗碳行为。钢的服役环境中存在的O2 、H2O 、SO2等气体杂质对其CO2腐蚀均存在不同程度影响,且这些因素的影响规律会随着钢的种类及服役环境的变化而变化。 (2)目前关于钢的CO2腐蚀过程中氧化与渗碳行为的腐蚀模型研究较少,且大多数模型是基于单一的氧化或渗碳动力学符合抛物线变化趋势的现象而建立的。虽然这些模型可对氧化物层厚度、渗碳深度等进行预测,但由于腐蚀过程中氧化与渗碳同时发生,这些模型未能较为准确地预测钢材的腐蚀寿命,因此建立同时涵盖氧化与渗碳共同作用的模型亟待进一步展开。此外,实际工况中的CO2可能处于流动状态,这将导致钢的腐蚀速率加快并促进氧化层脱落,因此未来的腐蚀模型须进一步考虑CO2流动状态(特别是含氧化物颗粒的CO2流)造成的侵蚀作用。 基于以上总结,为进一步提高钢在高温CO2环境中耐腐蚀性,针对目前已有防护涂层研究作出如下展望: (1)目前已有Al、Cr等涂层可有效提高钢在高温CO2环境中的抗氧化与抗渗碳性能,但钢材及涂层在腐蚀环境中的力学性能变化规律也将对其腐蚀行为有着重要影响,亟须深入研究。此外,相比于其他金属,Ni基合金往往表现出更优异的耐腐蚀性能,但其较为昂贵的成本限制了 Ni 基合金的大规模应用。因此,在对钢的涂层进行成分设计时,可选择Ni基合金为涂层主要成分。而引入纳米颗粒,并基于模拟计算对涂层成分及结构进行有效调控以改善涂层力学性能与耐蚀性的方法同样可作为涂层成分选择的一种研究方向。 ( 2)除改变涂层成分外,有关钢涂层防护的研究重点还在于提高涂层与钢材之间的附着强度和界面稳定性,进而确保涂层可牢固地附着于耐热钢表面,不易剥落,这离不开对更有效提高涂层的均匀性和致密性的制备工艺的探索。此外,开发可实时监测涂层损伤的系统方法有利于研究人员在合适时机采取恰当的维护措施。
免责声明:本网站所转载的文字、图片与视频资料版权归原创作者所有,如果涉及侵权,请第一时间联系本网删除。
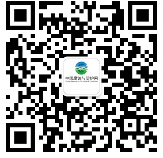
官方微信
《腐蚀与防护网电子期刊》征订启事
- 投稿联系:编辑部
- 电话:010-62316606
- 邮箱:fsfhzy666@163.com
- 腐蚀与防护网官方QQ群:140808414