
燃煤火力发电厂以朗肯循环为基础,以煤为能源通过水汽做功获得电能。为了提高能源利用率,并获得高质量的余热,热泵越来越多的应用于火力发电厂,尤其北方供热机组。溴化锂是余热回收的良好媒介,是热泵中常用的介质[1-2]。但是,溴化锂极易溶于水,热泵中的溴化锂在泄漏后,极易溶解于热网疏水中[3],从而进入机组凝汽器,若发现不及时或处理不当,会发生不可预估的事故。
某2×330 MW亚临界汽包炉供热机组,锅炉型号为SG-1215/17.5-M742,采用五段抽气对热网循环水进行梯级换热。供热期间,机组正常运行,某天上午9点,运行监督人员发现2号机组凝结水氢电导率异常上升(见图1)[4],大于10 μS/cm,而GB/T 12145-2016《火力发电机组及蒸汽动力设备水汽质量标准》要求小于0.2 μS/cm。监督人员及时开启定排并调大连排阀门开度,增加机组除盐水补水率,加强机组换水;1 h后,精处理高速混床失效,并且给水、炉水、过热蒸汽、饱和蒸汽、再热蒸汽的氢电导率均大于10 μS/cm(标准值小于0.2 μS/cm),为保护在线化学仪表,退出其运行。人工测量炉水pH为6.81,已达三级处理标准(GB/T 12145-2016规定的三级处理标准为小于8.0),运行人员为保护机组,及时加入氢氧化钠、磷酸三钠,调节炉水pH。经过锅炉换水及加药等措施,在第3天早上4点左右炉水pH达到9.0以上的合格范围,当天下午2点左右发生爆管事故;事故发生后,通过分析机组运行情况,确定事故原因是溴化锂进组机组水汽系统引起了水汽品质异常。
笔者通过一系列理化检验,分析了溴化锂对热力系统金属基体的腐蚀情况,并分析了亚临界汽包炉水冷壁泄漏的原因,以期避免类似事故的再次发生。
1. 理化检验与结果
1.1 宏观观察
在锅炉水冷壁管爆管处取样进行宏观观察。如图2(a)所示,爆口位于水冷壁管向火侧,爆口特征显示水冷壁管从内向外爆裂,并且爆口沿向火面纵向开裂,最大开口深度达到220 mm,垂直于水冷壁管横向最大开口深度达到60 mm。如图2(b)所示,对爆口附近管段进行检测发现,管段无塑性变形,爆口及附近区域受热面锈蚀严重且爆口边缘粗糙,爆口为脆性断口形貌,爆口附近水冷壁管区域无明显减薄。
1.2 微观形貌观察
在爆裂水冷壁管上取样进行金相检验,取样位置见图3。图3中1号环试样取自爆管爆口尖端附近,2号环试样位于爆口中部。采用金相显微镜对1号环和2号环试样进行检测分析。
1 号环微观形貌
如图4所示,在水冷壁管向火面内壁爆口尖端及中部均存在纵向小裂纹,小裂纹周围密集分布大量沿晶微裂纹,微裂纹深度约为2 mm;内壁大部分区域的氧化层已经崩落,仅在螺纹根部有少量残留,厚度约为182 μm[见图4(d)];试样经4%(体积分数)硝酸酒精溶液浸蚀后,内壁微裂纹所在区域已经完全脱碳成铁素体基体,无裂纹区域为正常组织,二者界限较清晰,脱碳区域分布范围较广,沿圆周占据水冷壁周长约1/3(向火面为2/3)。
综上可见,1号环内侧金属组织已经发生明显的破坏,而且组织中存在裂纹,这会导致金属强度的下降。
如图5所示:试样内测向火面组织为珠光体+铁素体,球化1.5级,背火面组织为珠光体+铁素体,球化1级;向火面外壁,背火面内壁和外壁均无明显脱碳及异常组织。由此可见,1号环内侧金属组织已经发生变化,而外侧金属组织无明显变化,说明爆管是由于水冷壁管内侧金属组织变化引起的。
2 号环微观形貌
2号环试样位于爆口中部,两端均接近鳍片位置。如图6所示:2号环试样向火面内壁爆口附近有小裂纹,长度约为1.2 mm,小裂纹周围密集分布大量沿晶微裂纹;试样经4%硝酸酒精溶液浸蚀后,小裂纹及微裂纹区域脱碳不明显,基体组织仍为珠光体+铁素体,球化1.5级。由此可见,爆口部位的金相组织内有大量裂纹,这会导致金属的强度明显下降,推测爆管的主要原因是金属强度下降引起的。
1.3 能谱分析
采用能谱仪,在管样爆口(1号环试样)处已经折裂但未脱落的残留部位取横截面试样,经打磨、抛光后观察。如图7所示:试样内壁微裂纹处的主要元素为Fe、Mn、C等;内壁氧化层呈双层形貌,外层主要元素为Fe、O、Si、C等,内层为垢下层,主要元素为Fe、O、C、Mn、S、Cl等,在垢下还发现少量S、Cl等活性阴离子。
1.4 室温拉伸性能
在水冷壁管爆口附近取样进行拉伸性能测试,结果如表1所示,其中试样编号,如向火21表示水冷壁管21号管的向火侧试样。
试样 | 屈服强度/MPa | 抗拉强度/MPa | 断后伸长率/% |
---|---|---|---|
参考值 | 275 | 485~640 | 20 |
向火侧21 | 261 | 362 | 8.0 |
向火侧23 | 269 | 371 | 9.0 |
背火侧22 | 324 | 539 | 17.5 |
背火侧24 | 331 | 547 | 19.0 |
向火侧11 | 295 | 384 | 8.0 |
向火侧12 | 235 | 355 | 8.0 |
由表1可见:向火侧12、21和23号试样的屈服强度明显低于参考值275 MPa的要求,最低为235 MPa,而背火侧试样的屈服强度均合格;向火侧试样的抗拉强度低于参考值485~640 MPa,最小值为355 MPa,而背火侧试样的抗拉强度均满足要求;向火侧试样的断后伸长率明显达不到参考值20%的要求,最大值仅为9.0%,而背火侧试样的断后伸长率略高,为17.5%和19.0%。由此可见,水冷壁管向火面的屈服强度、抗拉强度均不合格,且断后伸长率显著降低,而水冷壁管背火侧的拉伸性能基本满足要求。这是由于向火侧直接接触炉膛的火焰,在水质恶化的情况下,腐蚀性离子对向火侧金属基体的腐蚀效果更加明显
通过对爆口及爆口附近的水冷壁管进行取样分析,发现试样的显微组织发生了明显改变,而且部分区域发生了脱碳;此外,试样的力学性能也发生了改变,尤其向火侧力学性能明显下降,这是导致爆管事故发生的直接原因。
2. 溴化锂泄漏对机组水汽品质的影响
该机组凝结水和给水采用加氨全挥发处理,加氨后会发生如式(1)所示的可逆反应,保证了给水水质合格,pH为9.2~9.6,符合GB/T 12145-2016标准要求。
|
(1) |
当溴化锂进入炉水中后,因锂离子的极性大于氨,更容易结合水分子,促进反应(1)逆向发生,使给水和凝结水中的氨多以自由氨分子形式存在,这导致通过加氨提高给水和凝结水pH的方法失效。在高温条件下,溴离子和水中溶解氧分别发生如式(2)和(3)所示的反应。
阳极反应:
|
(2) |
阴极反应:
|
(3) |
炉水pH降低后,水中H+含量升高,其与OH-反应,加快反应(3)的进行;反应(2)中生成的单质溴(Br2)又会与水生成氢溴酸HBr[见式(4)],导致炉水pH快速下降,甚至低于7[5]。
|
(4) |
炉水pH的降低加快了水冷壁管基体的电化学腐蚀速率,电化学腐蚀的直接产物为Fe(OH)2,反应见式(5)~(7)[6]。
阴极反应:
|
(5) |
阳极反应:
|
(6) |
|
(7) |
在高温高压条件下,发生如式(8)所示的反应,生成大量Fe3O4[4,7]。
|
(8) |
溴化锂泄漏后炉水pH变化趋势见图1,最低达到6.7。机组停机后割管分析水冷壁管的结垢量达800 g/m2,99%的腐蚀产物为含铁氧化物[5,7];经化验汽包中97%的沉积物也为含铁氧化物,从而印证了该分析。
排除现场爆管前未有其他因素引起水质变化,从图1所示的炉水pH剧烈变化,且水冷壁管存在结垢可以判断,由于溴化锂进入热力系统,与水冷壁管受热面发生了反应,导致水冷壁管金属基体的力学性能发生了明显的降低[8-10],进而发生爆管事故。
3. 结论及建议
(1)溴化锂进入水汽系统后,高温引起的化学反应导致炉水pH降低,且短时间内通过加低浓度的氨水及氢氧化钠等碱化剂提高炉水pH比较困难。
(2)通过对水冷壁管样的扫描电镜、能谱及力学拉伸检验分析、能谱分析;管样向火面屈服强度及抗拉强度低于标准要求,尤其断后伸长率显著降低;水冷壁管样组织为珠光体+铁素体,老化级别合格。
(3)观察水冷壁爆口,水冷壁爆口从内向外爆裂;爆口处水冷壁管无明显胀粗、减薄,判断爆口为脆性断口。水冷壁管样内壁脱碳明显,且有大量沿晶微裂纹,断后伸长率显著降低。由于溴化锂在高温状况下的电化学反应,造成金属基体金相组织发生改变,大量沿晶裂纹导致金属强度降低,在高温及高压力作用下,水冷壁管爆裂。
(4)运行机组,尤其供热机组,应根据GB/T 12145的要求实时检测凝结水水质,防止供热疏水受污染时,不合格疏水进入凝汽器及热力系统,影响机组炉水、给水水质;凝结水水质不合格时,应及时排查原因,并增加机组补水,外排不合格凝结水,阻止不合格凝结水进热力系统。机组运行中,发生水汽品质劣化,应及时按照GB/T 12145-2016三级处理标准进行处理。溴化锂泄漏进入水汽系统,应及时停机进行处理,防止热力系统管材因溴化锂腐蚀造成不可逆损伤,并引发爆管等事故,并且停机后应及时对水冷壁、省煤器等受热面进行取样检测,分析垢量及材质是否满足运行要求,若材质由于溴化锂腐蚀发生变性,应及时更换不合格管材。
免责声明:本网站所转载的文字、图片与视频资料版权归原创作者所有,如果涉及侵权,请第一时间联系本网删除。
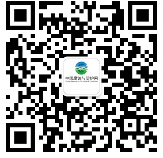
官方微信
《腐蚀与防护网电子期刊》征订启事
- 投稿联系:编辑部
- 电话:010-62316606
- 邮箱:fsfhzy666@163.com
- 腐蚀与防护网官方QQ群:140808414