核能发电以其燃料能量密度高、基本零排放和土地占用少等优势已经成为一些发达国家的首选和我国能源发展的重要趋势之一。根据国际原子能机构(IAEA)统计,截至2023年10月,中国的在运核电机组规模居世界第三,居于世界领先地位;《中国核能发展报告2023》指出,未来我国核能发电占比将会逐步提高,保证核电产出的高效和安全是当前国家发展战略之一。核电站的安全运行始终是扩大核电规模的重要前提,反应性控制、余热排出和包容放射性物质是核电厂三项基本安全功能,其中“包容放射性物质”这一项对核电关键性结构材料在苛刻工况中服役的稳定性和可靠性提出了极高的要求。锆合金具有力学性能优良、耐腐蚀强、中子吸收截面小和热导率高等优点,广泛应用于核反应堆的燃料包壳和堆芯结构部件的制造[1]。其中,重水堆中的重要结构部件压力管就由Zr-2.5Nb合金制成。压力管作为重水堆中燃料棒束和冷却剂的容器,是重水堆一回路燃料通道的重要组成部分[2]。
19世纪70年代,研究人员首次在加拿大重水铀反应堆(CANDU)中发现了压力管内部氢化物引起压力管内容物泄漏现象。研究表明,压力管的破裂是由一种现在被称为延迟氢化物开裂(DHC)的裂纹扩展造成的[3,4]。在反应堆运行过程中,压力管与重水发生腐蚀会反应产生大量的氢原子,由于锆金属与氢结合力较强,氢原子极易进入压力管内部。在应力场的作用下,氢原子易向高应力区(如微裂纹尖端)扩散,当高应力区的氢含量超出其极限固溶度时,难以继续溶解的氢原子就会以氢化物脆性相的形式析出并稳定存在于锆合金基体中。氢化物脆性相的存在会降低压力管材料的断裂韧性,当氢化物在应力作用发生断裂时就会导致原有微裂纹的扩展或产生新的微裂纹,上述氢扩散、氢化物形核和生长、氢化物断裂过程的反复发生,就会导致宏观上DHC裂纹的扩展,最终致使重水冷却剂的泄露,对重水堆的安全运行造成影响。目前,DHC被视为压力管服役过程中最重要的潜在风险之一。来自加拿大、韩国、阿根廷和印度等国家的研究者均对重水堆压力管用Zr-2.5Nb合金的DHC行为开展了大量研究,其中既包括DHC机理、模型构建及可靠性验证,也较为系统的研究了温度、氢含量、热循环方式以及锆合金本身微观结构和力学性能等因素对DHC行为的影响。DHC扩展速率(DHCR)作为评估压力管是否符合“破前漏”(LBB)准则的重要指标之一[5,6],是评价压力管DHC行为的重点。此外,DHC作为一种受环境影响的亚临界裂纹扩展[7],其萌生条件之一为应力强度因子达到DHC的门槛值KIH[8],为了预防和抑制DHC的产生,KIH测定是评价压力管DHC失效的另一个重点。
当前我国仅有秦山三期建造的两座重水堆核电站。秦山三期重水堆核电站自2003年7月建成投产以来,已服役超过20年(CANDU6型重水堆核电机组设计寿命为40年),根据加拿大标准协会相关标准CSA N285.4的要求,应定期对压力管取样并进行服役性能测试(其中包括DHCR测试和KIH测试),从而为压力管的老化评估和寿命预测提供必要的数据支撑。此外,根据秦山三期重水堆设计文件手册及最终安全分析报告,机组运行中期需更换压力管。为提高核电站中国产零部件的比例,降低压力管更换的经济成本,减少进口依赖,近几年我国陆续开展了国产压力管的研制工作。在国产压力管正式投入使用前,需对其抗DHC性能进行测试和验证。目前国内对压力管DHC行为的相关实验研究较少,因此建立DHC行为相关测试方法,厘清各因素对DHC行为的影响,对压力管的寿命评估与延寿以及国产压力管制造和性能测试有重要意义。本文就常用DHC测试方法、DHC相关机理以及各种因素对DHC行为的影响等方面进行综述,指出当前的研究不足,并对未来的研究趋势进行了展望。
1 DHC行为研究方法
为模拟压力管服在富氢环境下大量吸氢的现象,需在DHC实验前对压力管材料进行预充氢实验,通常用的充氢方法有气体充氢、高压釜渗氢、电解充氢等[9~11]。其中,电解充氢所需设备简单易得、操作便捷且可重复性高,应用最为广泛。由于压力管材料的各向异性,研究者结合压力管的形状和实际服役工况,通常采用两种不同的试样分别用于研究压力管轴向和径向DHC行为。其中,测试径向DHC行为采用的是悬臂梁(CB)试样;测试轴向DHC行为采用的是弯曲紧凑拉伸(CCT)试样,其取样方式如图1所示。为促进DHC裂纹的萌生,缩短加载与裂纹萌生之间的孕育期,通常需要在CCT试样上预制疲劳裂纹;受限于CB试样的形状,在CB试样上引入疲劳裂纹较为困难,因此在加工试样时尽量降低缺口底部几何形状的直径。图2为测试过程中两种试样的受载示意图,除图2中所示的基本受载条件外,DHC实验还需要高温炉等能精确控制温度变化的设备加以辅助,常采用声发射法(AE)或直流电位降法(DCPD)监测裂纹的萌生与扩展[12~14]。由于DHCR和KIH是评估压力管服役性能的重要指标,目前中国科学院金属研究所已经建成了压力管轴向DHCR和KIH的测试方法,并联合上海核工程研究设计院股份有限公司、中核核电运行管理有限公司、广东腐蚀科学与技术创新研究院和核工业标准化研究所编制了针对压力管轴向KIH和DHCR测试的中国核学会团体标准3项,预计将于近期发布实施。
图1
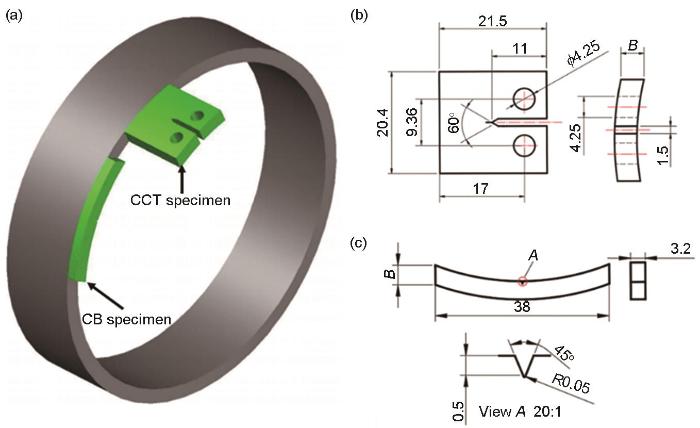
图1 试样取样及尺寸示意图
Fig.1 Schematic diagrams of sampling (a) and dimensions of CCT specimen (b) and CB specimen (c). B is thickness of pressure tube in Fig.1b and 1c, the unit is mm
图2
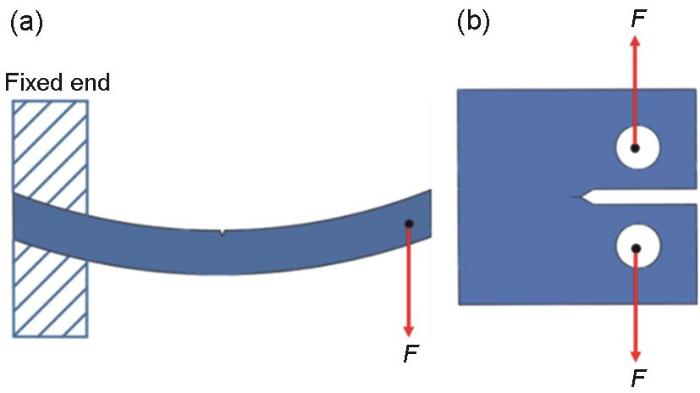
图2 试样加载示意图
Fig.2 Schematic diagrams of loading for CB specimen (a) and CCT specimen (b). F is the external load
1.1 KIH 测试
由于升K法测KIH时,先施加的较小载荷虽不会引起裂纹扩展,但可能会导致裂纹尖端发生钝化[16],从而降低了裂纹尖端的应力集中程度,因此一定程度上会造成所测的KIH值偏大;而降K法实验过程中,施加初始载荷初期就使裂纹尖端产生DHC扩展,可避免裂纹尖端的钝化,保证了KIH测试值的准确性。因此,通常采用降K法测试KIH。当采用降K法测试KIH时,判定所测的KIH是否有效,除需满足DHC裂纹保持24 h以上不发生扩展外,还需满足两个条件:(1) 试样断口表面,靠近试样两侧自由表面的韧性断裂区域的面积小于试样表面总的断裂区域面积的10%;(2) DHC扩展过程中,在试样的厚度方向,裂纹扩展的前沿近似均匀、平直,厚度方向大多数位置的裂纹扩展长度与利用九点法测得的平均裂纹长度之间的偏差小于10%。
1.2 DHCR测试
如前文所述,DHCR是评价材料抗DHC性能和是否符合“破前漏”要求的重要指标之一。如图3所示,DHCR随KI的变化可分为3个阶段,当位于Stage II时,DHCR几乎不随KI的变化而改变[17,18]。因此,在DHCR测试实验中,对试样施加适当恒载荷,使KI处于Stage II阶段。KIH一般小于10 MPa·m-2,KIC大于30 MPa·m-2,因此初始KI通常设置在15~20 MPa·m-2的范围内。在此条件下,虽然KI随着DHC扩展而增加,但DHCR基本不受KI改变的影响。实验结束后,通过九点法或面积法测量断口的DHC裂纹长度,裂纹扩展时间则通过DCPD或AE信号的变化获得。由于在Stage II阶段,DHCR对KI无明显依赖性,因此通常将实验过程中的裂纹扩展视为匀速扩展,将裂纹长度与裂纹扩展时间的比值作为DHCR的测试值。
图3

2 锆合金中氢化物析出行为和氢固溶度
2.1 氢化物在锆合金中的析出行为
氢在锆合金中的扩散和聚集是发生DHC现象的首要原因,因此对氢化物在锆合金中析出行为的研究是明确DHC机理的基础。如上文所提到的,压力管在高温高压的服役过程中与重水发生腐蚀反应而产生大量的氢原子:
(1)
当进入材料内部的氢原子数量超出氢固溶度时,氢原子会以氢化物的形式析出,造成锆合金部件局部或整体力学性能的下降。Zr为密排六方结构,目前在Zr及其合金中观察到的氢化锆有δ-ZrH1.66、γ-ZrH、ε-ZrH2和ζ-Zr2H[20,21],最为常见的是前两种。其中δ-ZrH1.66结构最为稳定[22],为面心立方结构,在锆合金中沿特定的惯习面析出[23~25];近期,西安交通大学在Zr-Zn-Nb-Fe合金中观察到应力诱发δ-ZrH1.5在Zr晶体的柱面析出,取向关系为<10
在工程使用前,压力管经历了高温挤压、冷加工和去应力退火等过程,压力管用Zr-2.5Nb合金由α-Zr相和β-Zr相两相组成。α-Zr相被沿压力管轴向方向拉长,β-Zr相呈薄片状分布在两个相邻的α-Zr相晶粒之间[14]。δ-ZrH1.66多在α-Zr和β-Zr相界处形核,并由相界处向α-Zr相内部生长形成穿晶氢化物片[29]。Zr-2.5Nb合金中观察到的δ-ZrH1.66析出惯习面多近似平行于(0001) α-Zr[30]。Perovic等[29]研究表明无外加应力条件下,氢化物片沿压力管切向堆叠,在宏观上呈现出氢化物长度方向与压力管切向平行的现象;有外加应力条件下,氢化物片沿压力管径向堆叠,在宏观上呈现出氢化物长度方向与压力管径向平行的现象。切向氢化物通常对压力管影响较小,而外加应力作用下产生的径向氢化物会显著降低锆合金管材的力学性能,其破裂直接导致DHC的萌生和扩展[31,32]。
2.2 锆合金中的氢固溶度
锆合金中氢的极限固溶度(TSS)直接影响氢化物能否析出和溶解氢的含量,后者还是氢原子扩散速率的重要影响参数。获得准确的TSS有助于预测压力管的DHC行为,因此许多研究者用差示扫描量热法和红外热导法等测量了不同锆合金在不同温度下的TSS[33,34]。锆合金的TSS通常有两种表示方法:一种是在升温过程中锆合金中所能溶解的最高氢含量,称为溶解极限固溶度(TSSD);另一种是在降温过程中氢化物恰好不析出的最大溶解度,称为析出极限固溶度(TSSP)。Motta等[35]总结了以上两种条件下测得的极限固溶度数据。如图4所示,TSSD固溶曲线和TSSP固溶曲线并不重合,相同温度下,TSSP固溶度高于TSSD固溶度。造成TSSD和TSSP差异的原因主要是析出的氢化物与锆基体的晶格失配度较大。降温过程中,氢原子从基体中脱溶导致晶格应变能的降低并不足以抵消氢化物析出造成晶格应变能的增加,因此氢化物析出受到抑制,氢在锆中过饱和溶解,导致TSSP高于平衡条件下的TSS;在升温过程中,氢化物发生溶解,由于已经析出的氢化物在其周围造成了塑性变形,消耗了由于氢化物析出造成的多余晶格应变能,降低了氢化锆溶解进锆基体的倾向,使TSSD低于TSSP[36]。
图4
3 DHC行为机理及模型
图5为DHC裂纹扩展的基本过程示意图。如5a所示,氢原子在应力诱导作用下向高应力区(裂纹尖端或缺口前端)扩散并富集;当裂纹尖端氢浓度高于氢的固溶度时,氢化物形核析出并长大(图5b);位于裂尖的氢化物在应力集中的作用下断裂,且裂纹与原有的裂纹尖端相连,引起原有裂纹扩展一小段距离后止裂(图5c);随后氢原子向新的裂纹尖端扩散,并形成新的氢化物(图5d)。以上过程不断重复进行就导致了DHC裂纹的扩展[40]。目前,不同研究者对上述的DHC裂纹扩展过程基本认同,但对氢原子向高应力区扩散的根本驱动力还存有争议。国内外研究者针对DHC裂纹扩展机理建立了多种模型,其中比较具有代表性的是Dutton-Puls模型[41,42]和Kim's模型[36],下面就两个模型进行讨论。
图5
3.1 Dutton-Plus模型
Dutton-Puls模型(D-P模型)认为发生DHC的第一步是氢原子向裂纹尖端等应力集中区域的扩散[43]。拉应力使锆的晶格常数增加,更易容纳氢原子,即拉应力的存在使氢原子在锆基体中的化学势降低[44]。在应力集中的作用下,裂纹尖端受拉应力最大,因而氢原子在裂纹尖端的化学势最低,相当于在裂纹尖端形成“氢阱”[43,45]。位于低应力区的氢原子在化学势梯度的作用下向裂纹尖端扩散,造成氢原子不断在裂纹尖端富集,直至达到平衡状态。由上述分析可知,氢原子扩散的直接原因是化学势梯度,而化学势梯度是由应力梯度造成的,因而D-P模型中认为氢原子扩散的根本驱动力是应力梯度。如果达到平衡时裂纹尖端的氢含量高于TSSP,则在氢扩散至平衡状态前,裂纹尖端处会因氢含量达到TSSP而析出氢化物,从而导致裂纹尖端的溶解氢浓度降低;由于未达到平衡状态,氢原子持续向裂纹尖端扩散,从而导致裂尖区氢化物的生长,生长至临界尺寸后发生断裂。反之,若达到平衡所需的氢含量低于TSSP,则裂纹尖端无氢化物析出,DHC现象也就不会发生[46]。
(2)
(3)
(4)
(5)
(6)
其中,DH = α-Zr中氢扩散常数(m2/s);C
从表达
3.2 Kim's模型
Kim's模型认为DHC现象发生的第一步是氢化物的析出[43],DHC裂纹扩展的驱动力是裂纹尖端处氢化物析出后导致裂纹尖端与其他位置的氢浓度差ΔC[36]。Kim等用TSSD和TSSP曲线对该模型进行了解释,如图6所示,当温度升高至300 ℃时,试样中的溶解氢含量处于A点,此时裂纹尖端和基体没有浓度差。当再降温至250 ℃时,由于TSS的“滞后效应”,基体的溶解氢含量会降至B点,但此时基体中的溶解氢含量未达到析出值。裂纹尖端处应力较大,诱发了氢化物的析出(Kim's模型认为[36],应力集中使裂纹尖端产生塑性变形,能降低氢化物析出产生的晶格应变能,使氢化物更易析出),溶解氢含量降至C点。至此,裂纹尖端和基体产生了氢的浓度差ΔC。为证明DHC裂纹扩展的驱动力是ΔC而非D-P模型中的应力梯度,研究中通过将试样加热到不同温度后再降温的方法获得具有不同ΔC的试样,并对这些试样施以相同的应力强度因子。结果表明,在应力强度因子相同的情况下,ΔC越大,试样的DHCR越大,ΔC可达到的最大值为测试温度下的TSSP减去TSSD[36]。
图6
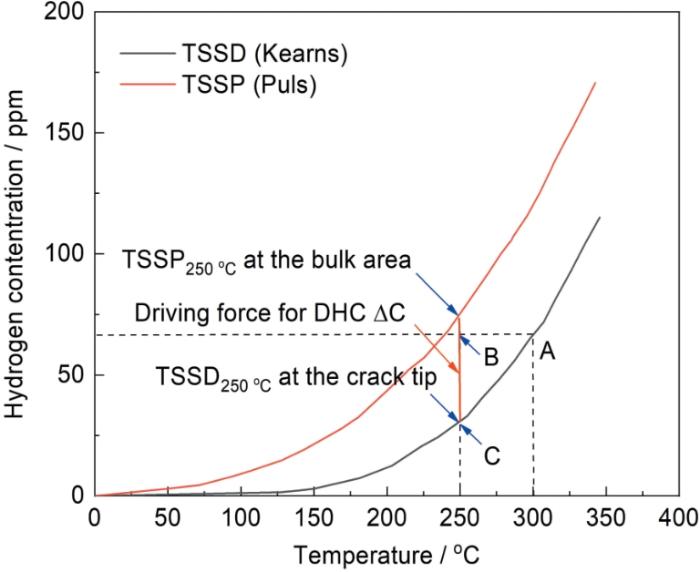
基于以上分析,Kim还提出了DHCR计算公式:
(7)
其中,k =与材料有关的系数;JH =氢扩散通量(kg/(m2/s));ΔC =基体和裂纹尖端的氢浓度差(mg/kg);DH =氢扩散系数(m2/s);ΔX =裂纹尖端塑性区尺寸(m);KIH =裂纹扩展临界应力强度因子(MPa·m-2);σYS =屈服强度(MPa)。
3.3 其它模型
不同于以上两种模型对DHC过程进行大量简化和假设,Varias 模型将含有氢化物的锆合金视为弹性复合材料,引入连续的扩散-热力学-机械耦合场,模拟DHC过程中真实的应力和温度[50,51]。Jernkvist等在Varias模型中引入氢化物相转变动力学,以更精确的描述氢化物的析出和溶解行为[52,53]。Shmakov模型采用了与D-P模型相似的物理原理,不同的是该模型认为氢原子扩散是非稳态的,并用分步数值计算的方法获得氢原子扩散通量[54]。Shmakov模型能较好的预测DHCR随KI变化的3个阶段和接近临界温度时DHCR降低的现象。上述模型各具特色,但仍难以统一共识。随着模拟计算能力和微观分析检测能力的不断提升,相信未来的模型会越来越准确。
4 不同因素对DHC行为的影响
4.1 材料微观结构和力学性能的影响
压力管在服役过程中受到高温和辐照的双重影响,其微观结构和力学性能会发生变化,进而对DHC行为产生影响。
前文已经提到,Zr-2.5Nb合金中含有α-Zr相和β-Zr相两相,α-Zr相晶粒沿压力管轴向被拉长,β-Zr相呈连续或半连续状态沿轴向分布在α-Zr相晶粒之间[14]。由于微观结构的各向异性,DHC行为也表现出各向异性。Kim等[14]研究表明氢在β-Zr相中的扩散速率较快,当裂纹扩展方向与β相分布方向一致时,会形成氢扩散的快速通道,裂纹起裂要求较低,因此轴向DHCR是径向DHCR的1.8~2倍,轴向KIH也高于径向KIH。研究结果表明,400 ℃热处理会使原本在轴向上连续分布的β-Zr相发生分解,热处理时间越长,β-Zr相分解程度越高[55]。随着热处理时间延长,轴向和径向的DHCR均降低。Jovanovic等[12]认为β-Zr相的分解降低了氢原子在压力管轴向的扩散速率,这是热处理导致轴向DHCR降低的主要原因;此外,材料的屈服强度随着热处理时长的增加而降低,有效缓解了裂纹尖端的应力集中程度,降低了裂纹尖端氢化物的断裂倾向,一定程度上抑制了DHC裂纹的萌生和扩展,这是导致轴向DHCR随热处理时长的延长而降低的另一个原因。对于径向DHCR,轴向氢扩散速率的下降对其基本没有影响,导致径向DHCR降低的主要原因是屈服强度的降低,因此径向DHCR下降幅度也小于轴向DHCR,且随着热处理时间的延长,轴向DHCR与径向DHCR的比值减小[55],压力管DHC行为的各向异性程度降低。除热处理外,辐照也能显著提高材料的屈服强度,从而导致较高的DHCR,使代表氢化物断裂尺寸的断口条纹宽度降低[56]。
4.2 KI 的影响
KI对DHC行为的影响可根据KI与KIH和KIC相对关系大致分为3个阶段(图3):在Stage I,KI略大于KIH,DHCR随KI的增加而急剧上升;Stage I的KI范围较小,随后进入DHCR对KI不敏感的Stage II;当KI继续增加至KIC附近时,DHCR再次随着KI的增加而急剧增长,即进入Stage III。在Stage III发生裂纹失稳扩展的现象较易理解,但对Stage I和Stage II所呈现的规律的机理以及这两个阶段的具体的分界点仍不清晰。
Yan等[57,58]重点关注了KI在KIH附近时氢化物的生长及断裂情况。结果表明,当KI < KIH时,裂纹尖端的氢化物尺寸随KI的增加而增加且不发生断裂;当KI > KIH时,氢化物断裂,其断裂尺寸随KI的增加呈先降低后趋于稳定的趋势。氢化物的生长是一个自限性过程,随着氢化物尺寸的增加,氢化物生长的驱动力逐渐减弱,因此在达到临界断裂尺寸前,氢化物就已经停止生长,即DHC不发生。随着KI的增加,裂纹尖端氢化物所受的应力增加,这会导致氢化物更易断裂,即临界断裂尺寸减小;裂纹尖端塑性区尺寸随KI增加,这为氢化物提供了更大的生长空间和驱动力。因此,在KI增加的过程中,必然存在一个临界点,使氢化物的实际尺寸等于临界断裂尺寸,该临界点对应的KI即KIH[41]。在KI略大于KIH的小范围内,KI的增加使氢化物临界断裂尺寸继续减小,氢化物更易断裂;并且KI的增加促进了氢原子向裂纹尖端扩散和氢化物的生长速率,因此在该范围内DHCR随KI的增加而急剧升高(Stage I)。
图7
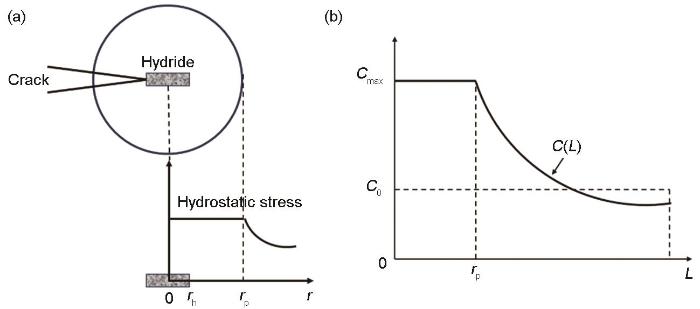
图中,C0为无应力区原始氢浓度,rp为静水应力开始降低的转折点(在裂纹尖端附近),L ≫ rp,C(L)为r=L处的氢浓度,Cmax为应力作用下裂纹尖端所能达到的最高氢浓度(并非裂纹尖端实际的氢浓度,若Cmax > TSSP,则在实际氢浓度到达Cmax前就有氢化物析出,导致氢含量降低)。从图中可知,当r < rp时,即在裂纹尖端及其附近的范围内,静水应力保持恒定,氢浓度也保持恒定。C0与C(L)以及Cmax的关系,如
(8)
(9)
(10)
(11)
其中,Φ(r)为应力势能;
裂纹足够尖锐的条件下,塑性区内P(r)的表达式如下:
(12)
(13)
其中,σy为屈服强度(MPa);KI为应力强度因子。
将
(14)
将
(15)
由
4.3 温度的影响
DHC裂纹扩展是一个热激活过程[41],其中,氢原子扩散、氢化物析出和氢化物断裂等均受到温度的影响。虽然压力管的实际服役温度较为稳定,但停堆检修期间涉及到温度的变化,因此明确温度对DHC行为的影响有助于寻找降低压力管泄漏风险的措施。
对于固定的氢浓度,温度过高会使氢浓度低于或略高于TSSP,从而导致氢化物不析出或析出困难,因此DHC现象的发生存在临界温度。Sagat等发现当温度升高至350 ℃时,压力管不产生DHC现象[61]。
在DHC现象能发生的温度范围内,DHCR通常是随着温度的升高而增大。许多研究者[61~63]在100~300 ℃的范围内测量了Zr-2.5Nb压力管轴向的DHCR,结果表明,该温度范围内DHCR和温度呈现出正相关,并符合Arrhenius规律[63]。随着温度的升高,断口的条纹特征也变得更加明显[13],条纹宽度也增大[56]。根据Kim's模型,DHCR主要由氢扩散速率和氢浓度梯度决定,其中氢扩散速率占主导地位;当温度增大到300 ℃以上时,氢扩散速率不再是DHCR的决定性因素,DHCR会随着温度的升高而降低[61],DHCR和温度之间不符合Arrhenius规律。Sunil等[64]认为,DHCR的降低和存在DHC裂纹扩展临界温度的原因是温度升高使材料发生蠕变,导致裂纹尖端的应力松弛,使氢化物的断裂变得困难;也有研究认为[65],在加载的过程中只有锆合金基体的屈服强度大于氢化物的断裂应力,氢化物才会发生断裂,而随着温度的升高,基体的屈服强度降幅超过了氢化物断裂应力的降幅,使氢化物的断裂变得困难。
Holston和Stjärnsäter[66]采用降载荷法测量了不同温度下Zr-4包壳管DHC的KIH,研究表明随着温度的升高,KIH值缓慢升高,但当温度超过300 ℃时KIH会急剧增加,Kim等[67]也观察到了类似的现象。这与上述关于300 ℃以上DHCR降低的现象相符合,即KIH越高,DHC裂纹扩展越困难。但同样采用降载荷法测量KIH值,Sagat等[68]研究表明,KIH值与温度的关联性并不大。Kim等[67]认为,裂纹尖端塑性变形区中产生的变形孪晶与氢化物的相互作用使氢化物断裂。同时,Kim还分别采用降载荷法和升载荷法获得了300 ℃以下不同温度的KIH值,发现使用降载荷法时,裂纹前端的塑性变形区较大,变形孪晶数量多[16]。虽然在300 ℃以下时,变形孪晶数量随温度的升高而增加,但在较低温度时变形孪晶数量并不是氢化物断裂的限制条件,所以KIH值与温度关联性不大;使用升载荷法时,裂纹前端塑性变形区小,变形孪晶数量较少,因此成为氢化物断裂的限制条件,温度越高,变形孪晶数量越多,氢化物越容易断裂,KIH值随温度的升高而降低[16]。当温度在300 ℃以上时,变形孪晶数量随温度的升高而减少,导致氢化物不容易发生断裂,使KIH急剧上升,也导致了DHCR的下降。
4.4 热循环过程的影响
在重水堆检修期间,压力管道不可避免的会经历升温或降温过程。因此,明确热循环过程对DHC行为的影响有助于改进检修方案,最大限度的降低DHC裂纹扩展对压力管的损伤。
升温、降温过程的重复会使氢化物反复溶解和析出。当氢化物第一次析出后会使析出周围的基体发生塑性变形,因而造成氢化物析出的“记忆效应”,再次降温时氢化物会更易析出,导致DHC发生的临界温度上升[69,70]。DHCR受裂纹尖端(高应力区)和低应力区的氢浓度梯度影响,但由于溶解氢含量受温度变化过程影响较大,材料经历的热循环过程会导致其中的氢含量产生差异,进而造成DHCR的不同。实验结果表明,升温至实验温度时所测的DHCR明显低于降温至实验温度时所测的DHCR[47]。对于具有相同氢含量的试样,如果升温到实验温度,则DHCR发生转折的温度比降温至实验温度时所测的转折温度低[18,71]。Shi等[46]利用D-P模型预测了不同热循环条件下所得的临界温度,结果表明,降温至实验温度条件下计算得到临界温度取决于氢含量,而升温至实验温度条件下计算得到的临界温度不受氢含量影响[46],该预测结果得到了实验数据的验证。
4.5 H含量的影响
研究认为,在一定温度下,裂纹尖端DHC行为发生的临界氢含量与TSSD接近,因此TSSD是裂纹尖端发生DHC现象的氢含量阈值[74]。Kim等[75]用升K法和降K法分别测量了280 ℃时不同氢含量试样的KIH值,结果表明,当实际氢含量高于该温度下的TSSD,且差值ΔC (ΔC =实际氢含量-TSSD)在25 mg/kg以下时,两种方式测得的KIH值均随氢含量的增加而降低;当ΔC超过25 mg/kg时,KIH值保持稳定[75]。Kim等[67]在随后的研究中还观察到氢化物尺寸越大,越容易与变形孪晶相互作用导致氢化物断裂,即ΔC越大,形成的氢化物尺寸越大,DHC越容易发生,这解释了KIH对氢含量的依赖性。同样,DHCR也是先随着氢含量的增加而增大,但是当氢含量增加至35 mg/kg后,DHCR趋于稳定[67]。Kim's模型[36]中DHC裂纹扩展的驱动力是裂纹尖端处与其他位置的溶解氢的浓度差,而裂尖处溶解氢含量为TSSD,因此在一定温度下,不同位置的溶解氢的差值最大为TSSP减去TSSD,所以当氢浓度差超过TSSP-TSSD的值时,氢含量的变化不会对DHCR和KIH产生影响。然而,也有研究发现当温度为250 ℃,氢含量在40~60 mg/kg的范围内,DHCR随氢含量的升高而增加[76]。
5 总结与展望
针对锆合金在高温环境中的延迟氢化物开裂行为已开展了大量的研究,为压力管等核电关键结构的锆合金部件的安全运行和老化管理提供了大量理论和数据支撑。但是,在研究中仍存在以下不足:(1) 由于锆合金的延迟氢化物开裂行为受温度、氢含量、受力和材料微观结构等因素的影响,其发生机理存在争议,氢化物的形核、生长和断裂过程以及影响氢化物断裂尺寸的因素仍不明确,对于不同因素间的耦合作用的影响有待进一步探索。(2) 氢含量对DHCR的影响趋势尚存在争议。(3) 普遍的锆合金DHC行为测试方法较为单一,且测试过程耗时长,效率较低。(4) 缺乏能实时监测DHC裂纹扩展长度的方法。(5) 缺乏模拟核用锆合金实际服役工况的实验设备,尤其是中子辐照的影响,使实验测试结果可能与材料实际服役结果有较大的出入。
针对上述的不足之处,未来要继续深入研究不同因素对DHC行为的影响。结合压力管的实际服役工况,不断改进实验方法,开发更接近实际服役状态的实验设备,尤其是针对中子辐照样品的自动化操作设备及热室。随着研究的深入和计算机技术的发展,模拟计算 被越来越广泛的应用到DHC行为的研究中。将模拟计算的结果与实验结果相结合,会极大的提高实验效率,有助于进一步探索DHC机理;还可以模拟压力管实际服役环境,为降低压力管的失效风险和延长使用寿命提供数据支撑。
免责声明:本网站所转载的文字、图片与视频资料版权归原创作者所有,如果涉及侵权,请第一时间联系本网删除。
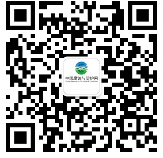
官方微信
《腐蚀与防护网电子期刊》征订启事
- 投稿联系:编辑部
- 电话:010-62316606
- 邮箱:fsfhzy666@163.com
- 腐蚀与防护网官方QQ群:140808414