热固性树脂因其固化后不溶不融、硬度高、比刚性大、耐高温且成品具有优异的尺寸稳定性,在防护涂料、轨道交通、航空航天等广大应用领域获得了认可。然而,随着材料技术的高速发展,传统热固性树脂的力学性能已难以满足各行各业选用材料的性能要求。针对此类问题,目前的解决方案主要围绕新型热固性树脂的研发和对传统热固性树脂进行改性两方面。改性后的热固性树脂综合性能得到了显著提升,且制备周期较短,在抗烧蚀、耐磨损和耐腐蚀等领域起着至关重要的作用。本文综述了近年来热固性树脂基复合材料在抗烧蚀、耐磨损和耐腐蚀等表面防护领域的研究现状,并对其材料种类、防护机理及环境对其性能的影响进行了梳理和总结,探讨了热固性树脂基复合材料未来的发展方向,可为其在接下来的研究中提供理论和技术参考。 引 言 热固性树脂材料因固化后能够形成稳定的、不可逆的高度交联网状结构而具有优异的尺寸稳定性,良好的耐腐蚀、耐高温、耐磨性和优异的力学性能,被广泛应用于涂料、胶粘剂、航空航天及汽车工业等领域 。目前应用范围较广的有环氧树脂、酚醛树脂、不饱和聚酯树脂、有机硅树脂等,其结构、制备方法、应用领域、力学和物理性能如表1所示,其中环氧树脂因其原料和制备工艺不同,有五种常见结构。 然而,热固性树脂固化后较差的力学性能是拓宽其应用面必须解决的短板问题。此外,对不同类型的热固性树脂来说,其阻燃性、抗冲击能力和固化收缩率等多方面特性各不相同,常见热固性树脂的性能见表1。如今,建筑、电子、航天等各个行业对材料性能有着越来越高的要求和标准,传统的热固性树脂的性能很难直接满足行业要求。对于上述问题,目前的解决方法可概括为以下两种:一是在传统热固性树脂的基础上添加其他增强相,从而实现对热固性树脂的改性;二是研发新的热固性树脂。目前,针对热固性树脂的改性已有了大量较为成熟的研究成果,改性后的热固性树脂可统称为热固性树脂基复合材料,其已成为抗烧蚀、耐磨损和耐腐蚀等功能防护材料首选材料之一。 本文针对热固性树脂树脂基复合材料,分别以抗烧蚀、耐磨损和耐腐蚀三种功能防护材料为对象,综述其防护性能和防护机理,对比了各增强填料对复合材料的影响,并指出了其在研究过程中的优缺点和未来发展方向。 抗烧蚀增强方法及机理 热防护系统(TPS)是一种位于超音速飞行器机身外部的结构,它能使机身结构在高速飞行过程中免受气动热损伤,是航空航天设备突破“热障”实现超音速飞行的必要条件。如今,抗烧蚀材料已成为航天器热防护系统的核心材料,通常作为航天器发动机的内部热绝缘层、火箭发动机的阻燃防护层使用。热固性树脂作为碳化型烧蚀材料,已成为应用极广的抗烧蚀材料之一,其主要依赖于树脂高分子材料在烧蚀过程中发生的碳化反应吸收部分热量,同时利用其分解产生的气体实现隔热作用。因此,对树脂材料而言,其抗烧蚀性能与碳化反应密切相关,典型热固性树脂的玻璃化转变 温度和开始降解温度如表2所示。然而,由于高分子材料本身性能的限制,其烧蚀过程是不可逆的,其耐高温性能和长期抗烧蚀能力已难以满足飞行器结构部件和机身外部日益恶化的热环境,因此提高树脂基复合材料的烧蚀耐热性能是十分必要的。 由于陶瓷材料优异的高温稳定性,利用陶瓷粉体增强树脂基体已成为提高复合材料抗烧蚀性能的常用手段,在高温条件下,陶瓷填料会转化为致密的陶瓷隔热层,降低复合材料的烧蚀率。其中碳化锆(ZrC)是目前常用的陶瓷填料之一。Wang等指出增加ZrC含量能够有效提高碳/酚醛(C/Ph)树脂复合材料的耐烧蚀性能,如图1所示,随着ZrC质量分数的增加,复合材料表面耐温性得到了显著提高,且烧蚀后背面温度逐渐降低。这是由于ZrC具有较高的熔点,其在烧蚀过程中氧化形成的氧化锆(ZrO2)能够充当隔热层并阻止热量进一步传递到样品中,且随着ZrC含量的增加,该层变厚,为样品提供了更多保护。 碳化硅(SiC)和硼化锆(ZrB2) 也具有类似的性质,Liu等利用双酚环氧树脂(BER)改性硅橡胶,并额外引入了二氧化硅(SiO2)和碳纤维作为增强填料,相较纯基体材料,改性后的复合材料线烧蚀率降低了54.7%。在烧蚀过程中复合材料发生了陶瓷化反应,生成了陶瓷质SiC,且BER的加入使热解过程中石墨结构更加有序,进而提高了陶瓷层的强度。Zhang等 指出加入 ZrB2-SiC复合填料能够使复合材料长时间处于烧蚀环境下而不损坏,同时详细分析了复合材料的烧蚀状态和烧蚀机理,如图2所示。对于Tmax=2480℃烧蚀100s的复合材料,由于氧化锆(ZrO2)相的粗化和玻璃态氧化硅(SiO2) 相的转变,试样表面形成了致密的ZrO2+SiO2层,中间则因SiO2的不完全融化形成了多孔ZrO2+SiO2层,最下方则由于SiC的活性氧化只留下了ZrO2层;当烧蚀时间持续到200s(Tmax=2465℃)时,表面SiO2挥发剥落,形成多孔ZrO2层,中间则由于玻璃态SiO2增加了ZrO2颗粒层的粘度而形成了致密的SiO2+ZrO2层,最下方为多孔ZrO2层;最后随着烧蚀时间延长至500s(2440℃),ZrO2颗粒在表面堆积烧结形成致密的ZrO2层,中间层由于玻璃态 SiO2扩散受到限制而形成了致密的SiO2+ZrO2层,最下方为多孔ZrO2层。这说明复合材料的烧蚀行为受微观结构、组分分布、烧蚀温度、烧蚀时间和形成的氧化层等多种因素的影响。 除了使用高温陶瓷之外,碳纳米管和炭黑等碳基纳米粒子也被证明是增强复合材料力学和烧蚀性能的有价值的候选材料,即使只添加很少量的碳纳米管,对复合材料的抗烧蚀性能的提升也十分显著。一方面,碳纳米管能够提高复合后材料的热导率。Park等对比了酚醛树脂(PR)、随机切碎的碳纤维增强酚醛复合材料(RCFPC)、编织碳纤维毡增强酚醛复合材料(MCFPC)和编织碳纤维毡/CNT增强酚醛复合材料(MCF/CNTPC)四种材料在1300℃下的烧蚀性能,碳纳米管的加入使复合材料的烧蚀性能提高了25%,相较纯酚醛树脂,其烧蚀率下降了78.6%。对比四种材料的热导率发现,碳纳米管的引入使复合材料的热导率显著提高,如图3所示。Ahmad等采用氧乙炔火焰测试进行烧蚀试验,结果表明复合材料的线烧蚀速率随碳纳米管含量的增加而降低,当样品中碳纳米管含量为0.4%时,烧蚀效果最好,且与不含多壁碳纳米管的原始复合材料相比,含有多壁碳纳米管的复合材料具有更好的导热性。另一方面,碳纳米管能够促进复合材料的石墨化过程,在烧蚀过程中形成具有优异性能的石墨结构,相较纯酚醛树脂,加入碳纳米管能够使复合材料抗烧蚀性提高30%以上,在烧蚀过程中,碳纳米管充当了成核剂的作用,作为碳化酚醛树脂石墨化的晶体生长核,其周围形成紧密的石墨结构进而提高了复合材料的耐高温烧蚀性能 。Natali等也得到了类似的结果。碳纤维/树脂基复合材料的烧蚀机理如图4所示,复合材料在烧蚀过程中可划分为碳化层和热解层。在氧⁃乙炔烧蚀的过程中,树脂最先发生降解,吸收一定热量并依附在纤维骨架上形成石墨结构,且在此过程中,树脂降解产生的气体向外逸出,在到达材料表面后形成气膜并作为反应屏障,阻止热量传输。 近年来,其他新型抗烧蚀复合材料也越来越多。郭慧等利用长度分别为6mm和3mm的纤维增强酚醛气凝胶,并对比了二者的抗烧蚀性能,研究发现以6mm 纤维为增强相的复合材料具有更低的室温热导率和更强的抗烧蚀能力。张鹏飞等利用陶瓷先驱体对纤维进行抗氧化防护,并在纤维骨架中填充酚醛树脂,制得了一种抗氧化三维纤维增强酚醛气凝胶材料,该材料在烧蚀过程中,熔融的先驱体陶瓷氧化物包覆在纤维表面,并填封纤维间隙,使复合材料能够在高温环境下长期存在。Cheng等制备的碳纤维毡⁃酚醛烧蚀材料(NCF-PR) 在电弧烧蚀过程中线烧蚀率低至0.029mm/s,在样品表面温度超过2000℃的情况下,样件内18mm处温度仅为150℃,其原因在于烧蚀过程中树脂降解吸收热量,且复合材料内部纤维能够很好地维持网状结构,防止降解后残余的碳被高速气流吹走,进而防止复合材料被进一步烧蚀。碳纤维/环氧树脂复合材料在接枝有机硅后其抗烧蚀性得到了显著提升,且有机硅含量越高其效果越明显 。烧蚀后烧蚀中心形成了多孔碳层,其主要由二氧化硅和碳组成,这是由于在烧蚀过程中有机硅会热解为类SiO2物质,并在表面形成保护层,且高温下树脂降解形成的熔融碎片会在热解气体的推动下不断向表面迁移,最终在表面聚结后形成致密的多孔炭层。 综上所述,抗烧蚀型复合材料的防护机理可归结为两点: (1)烧蚀过程中树脂基体降解产生的气体向外溢出,在材料表面形成气膜以阻止外部热量向内传递,且降解产物依附在内部增强纤维上形成高强度碳层,进一步保护复合材料; (2)类陶瓷或陶瓷填料在烧蚀过程中被严重氧化形成隔热陶瓷层,对复合材料起到良好的保护作用,如图4所示。但是,部分材料在受到高温或受到高温后冷却的过程中,其体积会发生变化,对复合材料造成进一步的损伤,因此在制备复合材料时应考虑避免此类现象 。此外,对纳米级别的填料来说,如纳米陶瓷颗粒与碳纳米管,其在高浓度下会出现聚集现象 。因此必须优化这类填料在复合材料中的含量,并且必须均匀分散,以便其与基体材料建立强相互作用,否则,随着添加量的增加,复合材料的性能将会恶化。对于有绝缘性、导电性等特殊服役要求的复合材料,大部分增强填料无法得到应用,因此开发新型抗烧蚀材料也是一种前景可观的研究方向。 耐磨损增强方法及机理 树脂基摩擦材料优异的耐磨性、低廉的成本且制备简单等优点使其得到越来越广泛的应用。然而,如今人们对飞机、汽车安全性能的要求不断提高,现有的传动、制动等摩擦材料势必要不断进行革新,且复合材料在摩擦过程中受到多种因素影响,发生的变化也非常复杂,因此开展树脂基复合材料的耐磨性研究是十分必要的。 目前,树脂基摩擦材料已被大量用作汽车、飞机、赛车及其他车辆的刹车片的组成材料。高质量的摩擦复合材料必须具备优异的性能,如高热稳定性、低磨损率、低噪音、稳定且足够的摩擦系数、可靠的抗衰退性以及生态友好性。然而,对纯树脂基摩擦材料而言,其在摩损过程中产生的摩擦热的作用下会发生严重的衰退现象,且在载荷的作用下磨屑不断剥落并在摩擦面留下大量凹坑和犁沟,导致摩擦材料表面的粗糙度和磨损率急剧升高。因此,向树脂基摩擦材料中引入增强填料以增强其承载能力和抗衰退能力是当下的主要研究方向。摩擦复合材料通常由热固性树脂基体和摩擦改性填料组成,其中树脂材料主要起粘合剂的作用,并通过纤维或颗粒增强复合材料的力学性能和摩擦性能。 纤维在摩擦复合材料界面制动过程中发挥着重要作用,并能够有效改善树脂基体耐热性差等缺点 。王亚楠等向硼酸酯改性后的酚醛树脂中引入玻璃纤维增强填料,较纯树脂而言,复合材料的摩擦系数降低了22%。王春红等将竹纤维(BF)引入环氧树脂(EP)中,制得了BF/EP 复合材料。相同测试环境下,复合材料的体积磨损量较纯环氧树脂而言最多可降低65%。其原因在于,当包覆在纤维表层的基体磨损脱落后,质地较硬的BF能很好地承受和传递接触面的大部分载荷,且纤维不易被拔出和拉断,有效提高了复合材料的耐磨性。此外,向树脂基体引入碳纤维能够有效提高复合材料的物理性能和耐磨性,且随着碳纤维含量的增加,其对复合材料的增强效果越来越显著。Ahmadijokani等指出,碳纤维加入树脂材料中后,复合材料的储能模量增加,因而复合材料的刚度有所提高。在磨损实验中,碳纤维的多层微结构及其固有的润滑作用有助于在磨损表面形成牢固且粘附的润滑膜,从而有效降低磨损率。然而,加入碳纤维加剧了复合材料的热衰退行为,且随着滑动速度和载荷的提高,摩擦热升高,衰退行为更加强烈。Rahmani 等对比了芳纶纤维(KFR)、玻璃纤维(GFR)和碳纤维(CFR)三种增强材料对复合材料耐磨性的影响,如图5所示。从图5可以明显看出碳纤维/树脂复合材料的耐磨性最好,玻璃纤维/树脂复合材料次之,对比它们的显微硬度可知,复合材料的硬度越高,磨损率越低。这是由于耐磨性是硬度和韧性这两种力学性能的函数,即实验时塑性变形越小的材料耐磨性越好。 除纤维填料外,陶瓷颗粒因其优异的力学性能和较低的温度敏感性而被广泛用于树脂基摩擦材料,其在磨损过程中能够在摩擦界面形成摩擦膜,极大地提高复合材料的耐磨性。Vlastimil等 研究了不同SiC颗粒尺寸条件下摩擦膜的形成,结果表明,摩擦膜的稳定性随着颗粒尺寸的增加而增加。Sun等在探究树脂基摩擦材料的摩擦膜力学性能与摩擦性能的关系时发现,摩擦材料表面粗糙度越高,其在低温下磨损率越低。这是由于摩擦过程中产生的磨屑更容易在粗糙颗粒周围聚集,加速摩擦膜的形成;然而,因摩擦面磨屑的主要成分是树脂基体碎屑,随着温度升高,摩擦材料的热衰退更加显著。由此可得,摩擦材料颗粒表面越粗糙,越有利于摩擦膜的形成,但会降低摩擦材料的抗衰退性。其他颗粒填料对树脂基摩擦材料的防护机理与陶瓷颗粒类似,如铜颗粒同样能以在摩擦面形成摩擦膜的形式降低摩擦材料的磨损率,但随着磨损的不断进行,铜颗粒会从摩擦材料表面脱落,导致其耐磨性有所下降 。 考虑到摩擦材料复杂的服役工况,学者对其摩擦过程中的磨损机理展开了研究,如表3所示。不同摩擦环境下复合材料的磨损机理不同。玻璃纤维/树脂复合材料在干滑动(Dry)、油润滑滑动(Oil)和惰性气体滑动(Argon)三种不同滑动环境下的磨损率如图6所示 。由图6可知,摩擦材料在惰性气体环境中的磨损率最大,这是由于气体会将玻璃纤维碎片分离并带离摩擦区域,使其无法在复合材料表面形成保护膜,加速材料的磨损。反之,油润滑剂则能够吸附摩擦时剥落的玻璃纤维碎片并在材料表面形成保护膜从而降低材料的磨损率。此外,随着摩擦速率的增加,油润滑环境下摩擦材料的磨损率反而有所降低,其原因是摩擦面温度的升高产生热扩散,软化树脂基体使玻璃纤维更容易破裂,加速表面保护膜的形成,摩擦系数减小。 不同温度下,复合材料的磨损机理同样不同。以热解碳改性碳纤维立体织物增强聚酰亚胺复合材料(PI-C/CF)为例,三种温度下该复合材料的磨损过程如图7所示。室温下,复合材料在磨损过程中增强相和基体产生磨屑并不断剥落,形成润滑膜,并在磨损过程中不断扩大。因此,室温下的磨损机理主要包括连锁效应、黏着和磨粒磨损;在380℃时,基体和增强相因摩擦和剪切而断裂,跑合磨损完成后,磨屑产生形变并粘附在复合材料表面,形成自润滑膜;同时,树脂基体在高温下会发生热解并被不断氧化,使复合材料表面出现微孔和微裂纹。因此,此时的磨损机理可断定为黏着磨损、磨粒磨损和氧化磨损;在RT~380℃~RT环境下,复合材料的磨损机理与380℃时类似,但由于周期性环境变化的影响,摩擦表面的润滑膜会不断被撕裂并从复合材料表面剥落,故可认为交变温度下的磨损机理为黏着磨损和氧化磨损。 在不同载荷下,试样与载荷的实际接触面积不同,材料的磨损率在实质上是由其承载面积控制的。低载荷下,复合材料表面出现大量微裂纹,如图8a所示 。在摩擦磨损过程中,试样表面的微凸点在周期性循环载荷作用下发生微形变和微熔化。由于复合材料中存在的孔隙、杂质等缺陷,在这种周期性形变的作用下,复合材料表面应力集中处分子链或分子间键断裂并形成裂纹,此时,磨损形式主要为疲劳磨损;随着载荷增加,磨损表面出现大量划痕,其主要磨损形式是磨粒磨损。这是由于树脂基体较软,此时,参与磨损的是复合材料表面的微凸块,其在载荷的作用下发生变形并产生微裂纹,并随着磨损的进行从复合材料表面脱离,在摩擦面堆积并造成磨粒磨损。 综上所述,树脂基摩擦材料在引入填料后的耐磨损机理如图9所示,在纤维和颗粒类填料的共同作用下,复合材料的承载能力和耐磨性得到了明显提高。各类填料对树脂基摩擦材料的影响如表4所示,可见,仅由单一类型填料增强的树脂基摩擦材料难以满足复杂工况对摩擦材料的性能要求,因此,使用混合填料已成为树脂基摩擦材料的普遍趋势。而摩擦材料的性能是一个多准则决策问题,在探究各类与性能相关的问题时,需要综合考量摩擦材料的耐磨性、力学性能等方面,且同一材料在不同环境下的磨损形式、磨损机理不尽相同。因此,对复合材料磨损机理的探究任重而道远,在不断的研究过程中形成系统、完整的理论体系对复合材料的发展具有重要指导作用。 耐腐蚀增强方法及机理 腐蚀是日常生活中最常见的材料失效形式。与地震、海啸等“惊天动地”的自然灾害不同,腐蚀会在无声无息中对材料造成极大的破坏。根据世界腐蚀组织的一项调查,每年全球的经济损失有超过4万亿美元是腐蚀造成的。此外,材料的腐蚀还会产生严重的环境污染与资源浪费 。由于涂覆有机防腐涂料具有施工简便、适用性广、成本低廉且性能优越等优点,树脂基复合材料在防腐领域主要以防腐涂层的形式存在,其防腐机理主要可分为屏蔽和抑制作用,在涂层内部,树脂材料主要起屏蔽作用以防止腐蚀介质向金属内部方向扩散;在金属基体表面,树脂基材料通过与金属基体的强粘结作用和化学作用防止金属基体发生腐蚀,从而实现防腐 。 然而,受热固性树脂材料高交联密度的影响,树脂基材料中会产生微裂纹和孔洞,在树脂基材料中形成针孔状孔隙,在实际应用中,腐蚀性介质分子(如水、氧和离子)会渗透到复合涂层中 。在湿热环境下,复合材料会吸水导致树脂基体胀大,使界面层结构遭到破坏,从而导致复合材料受力状态发生变化,如图10所示 。水分子在吸湿过程中影响了分子链间的折叠距离和破坏了分子间的范德华力。另外,水分子扩散到树脂基体中会引起基体中某些极性基团产生化学反应,使基体水解或破坏其中的链结构,削弱分子间化学键的结合力,从而降低其防腐性能。此外,树脂材料对紫外线的低稳定性也在一定程度上限制了它的应用。 此外,复合材料在湿热环境下的服役时间越长,其力学性能的损伤越显著 。在诸如海水等碱性环境中,复合材料除了受吸湿性影响外,还会受到水中碱性离子的影响。对比湿热和碱性环境下玻璃纤维/环氧乙烯基酯复合材料的吸湿速率可知,相同时间内,碱性环境中复合材料吸水率较湿热环境更大,如图11所示,即碱性介质促进了复合材料的吸湿速度。对比两种环境腐蚀后的复合材料表面形貌可发现,相同时间内,碱性环境对试样的破坏程度远大于湿热环境。可以判断碱溶液除了会对树脂基体造成严重腐蚀外,还会透过基体并进一步腐蚀其中的纤维,削弱纤维与基体界面的结合力,加剧纤维与树脂基体间界面的破坏。 为解决上述问题,目前主要从以下两方面提高树脂基复合材料的防腐性能:(1)减少树脂基复合材料中的孔隙,提高腐蚀介质向材料内扩散的难度;(2)降低腐蚀介质与复合材料间的亲和力。如Fihri等制备的纤维状二氧化硅改性环氧树脂材料表现出了优异的疏水性能,且在腐蚀环境中具有优异的耐久性,实验所用碳钢基体在涂覆该复合材料后,腐蚀电流密度降低了两个数量级,其疏水性能是由烃链的低表面能和Si-O-Si网状结构的协同作用决定的。Xia等将改性二硫化钼(MoS2)引入环氧树脂体系,与纯环氧树脂材料相比,改性后的复合材料在3.5%(质量分数)NaCl溶液中腐蚀35d后,其耐腐蚀性能提高了近三个数量级。Dagdag等以亚甲基二苯胺为固化剂制备了环氧树脂复合涂层,并以3% (质量分数)NaCl为腐蚀介质,测试复合涂层的耐腐蚀性。复合涂层的防腐蚀效率最高可达93%左右,这是因为完整的高分子环氧涂层可以抑制腐蚀环境中腐蚀性物质的进入。Situ等向环氧树脂中加入聚苯胺⁃氮化钛纳米填料,制得了具有高耐腐蚀性的复合材料,相较纯环氧树脂材料,复合材料的阻抗数量级提高了1~3倍。Yao等制备了聚乙烯醇/酚醛(PVB/PF) 复合材料,在3.5%(质量分数)的NaCl中浸泡30d后,复合材料的低频阻抗模量(|Z|0.01Hz)为2.41×107Ω·cm2,这是因为PVB和PF形成了均匀致密的结构,使复合材料具有良好的柔韧性、较高的机械强度和优良的阻隔性能。Li等在聚氨酯(PU)制备中合成了铜配合物(Cu(HD)2),加入Cu2+后形成的配位键改善了聚氨酯的力学性能,使其结构更加紧密,复合材料的|Z|0.01Hz值从6.033×106Ω·cm2提高到了7.943×107Ω·cm2,且复合材料具有释放Cu2+的抑菌作用,其在防腐防污领域具有很好的潜力。 向环氧树脂中添加导电聚合物也是提高复合材料耐腐蚀能力的可行方式之一。缺陷少、石墨化程度高的石墨烯纳米片(GO)也是有效提高树脂基复合材料耐腐蚀性的增强填料之一,适量 GO的加入不仅能有效提高树脂基复合涂料的耐腐蚀性,还能提高其韧性和结合强度,在10%(质量分数)NaCl腐蚀液中的对比实验表明,当GO质量分数为1.0%时,复合材料的防腐性能最好 。Dermani等向GO改性环氧树脂体系加入了活性辅助剂,增强了GO与环氧树脂间的相容性,并促进其在树脂体系中的分散。加入活性辅助剂后的复合材料中GO无明显团聚,且复合材料在3.5%(质量分数)NaCl溶液中腐蚀14d后,相较未加入活性辅助剂的材料,其质量损失减少了40%。此外,无机纳米功能填料能够均匀分散在基体中,堵塞树脂固化过程中产生的微孔道,提高复合材料的耐腐蚀性。Chang等利用纳米铸造技术制备了具有仿生疏水表面的环氧/石墨烯复合涂层 (HEGC),表面水接触角约为127°,与纯环氧涂层相比,HEGC涂层腐蚀电流密度降低,阻抗模值得到极大提高。Mo等研究利用功能化石墨烯(FG)和FGO提高PU涂层的抗腐蚀性能。研究表明,FG和FGO的引入均降低了涂层的腐蚀电流密度,提高其防腐保护效率,石墨烯复合防腐涂层的防腐蚀性能与纯PU涂层相比明显提高,这是因为具有润滑和阻隔性的FG和FGO片状填料分散在聚氨酯基体后,增加腐蚀介质的扩散路径的曲折程度,复合涂层的抗腐蚀性能大大提高。 近年来,随着对长期防腐能力要求的不断提高,研究人员开发出了受到机械损伤后能够自我修复的自愈合防腐材料。目前,材料的自愈合性能主要来自于向材料内部添加具有缓蚀效果的微粒,这些材料能够促进材料内部分子间的作用力并在材料受到损伤后为材料提供后续防腐能力。Kim等将碳纳米管(CNTs)嵌入溴丁基橡胶(BIIR)制备了CNT/BIIR自愈合复合材料,并将其涂覆在钢板上,在模拟叶轮工作环境下测试复合材料的耐腐蚀性能,经过40h的腐蚀后,钢板边缘出现锈迹,但几乎覆盖整个前表面的双层涂层并没有剥落,而是一直粘附在基底上,防止其生锈。另外,在150~170℃下测试复合材料的自愈合特性,结果表明材料表面的裂纹只需1h便能完全愈合。Liu等以聚丙二醇(D400)为交联剂,通过接枝嘧啶酮(UPy)将氢键引入环氧网络,所制得的自愈合环氧复合材料在没有任何干预的情况下,即使在水浸条件下,也能在5min内发挥自愈功能,且电化学阻抗谱测试结果表明,该自愈合涂层在NaCl溶液中浸泡60d后具有较高的|Z|0.01Hz值,为4.8×1010Ω·cm2 。其自愈合过程如图12所示,UPy⁃D400的引入能够确保分子链的高流动性,在室温下使损坏的涂层界面快速闭合。Wang等向纯环氧树脂中加入缓蚀剂苯并三唑(BTA),对比发现加入6%BTA的复合材料的耐腐蚀性能最好,其在3.5%(质量分数)的NaCl溶液中的耐腐蚀性提高了1.4倍,这是由于BTA具有优异的超疏水性能,可以在不破坏材料微观结构完整性的情况下延长腐蚀介质在材料中的扩散路径,且材料表面损伤后,BTA可以从其损伤区域释放出来,提高复合材料的自愈合性能。 综上所述,复合材料的腐蚀和老化是不可避免的,目前针对树脂基防腐材料的研究主要集中在添加增强相,阻止腐蚀介质向复合材料内部渗透,即主动防腐领域。近年来,尽管有学者展开了被动防腐(即自愈合复合材料)的研究,但目前针对这方面的研究尚浅,所研制的复合材料的自愈合作用不可逆,且承载能力受到空间的限制,其愈合性能和力学性能相互制约。此外,因为自愈合复合材料的分子间相互作用非常敏感,并且对水、酸、碱分子具有渗透性,所以其对酸碱腐蚀的抵抗力较低。同时,由于具有自愈性能的材料通常力学性能较差,自愈性能与材料力学性能之间存在相互限制。因此,有必要根据其物理和化学性质设计出合适的聚合物,合理利用填料优良的理化性能改善自愈合复合材料的综合性能,降低其成本,这将会是未来很长一段时间的研究方向。理想情况下,防腐材料应该具有高阻隔能力、良好的力学和自愈性能,能够适用于重型防腐应用。 结语与展望 改性后的树脂基复合材料在抗烧蚀、耐磨损和耐腐蚀等表面防护领域表现出了优异的性能,但综述国内外研究成果后发现,其在制备和使用中仍存在一系列问题,如填料与树脂体系无法紧密相容、某些填料在树脂体系中均匀分散难度大、改善某种性能的同时降低了其他方面的性能等。面对材料技术高速发展的趋势,未来应结合材料基因组计算技术对树脂基复合材料进行进一步组分和结构优化,结合有机与无机材料的工艺性能特点,笔者认为,在后续的研究工作中,应注意以下三个方面内容: 1 高性能、多功能、轻量化是基本性能要求复合材料的服役环境十分复杂,部分材料在满足功能材料要求的基础上,还需要充当承重结构件,有些部件在服役过程中还会受到严重的冲蚀作用,这意味着材料还应该具有高抗冲蚀性和一定的断裂韧性。此外,复合材料轻量化已成为近年来的热点问题,材料的质量越轻,设备运行速度就越快,续航时间就越长。因此,在提高复合材料性能的过程中,还应同时注意复合材料的轻量化问题。 2 规范、系统的理论指导是重要保障目前,针对增强改性后的树脂基复合材料的研究主要是为了提高复合材料的实用性,其机理方面的研究较少,尤其是对于服役环境复杂的树脂基摩擦材料,其磨损形式受多种因素影响,掌握其摩擦磨损机理至关重要。因此,研究树脂基复合材料的增强机理及复合材料在服役过程中的损伤机理,形成一套完善的理论体系,对树脂基复合材料的结构设计和改良有重要指导意义。 3 绿色、环保的材料特性是大势所趋热固性树脂固化后不溶不融的特性使其应用领域广阔,却也使其在循环回收方面给人们带来了极大的困扰。目前主要的处理方式有填埋、研磨、燃烧和热解等,这些方法不仅会消耗大量能源,造成严重的资源浪费,还会对环境产生一定污染。树脂基复合材料的回收利用已成为实现环境保护和社会可持续发展的重要挑战。因此,无论是开发新型复合材料还是改进现有材料时都应把其可回收性作为设计依据之一,此举不仅能够赋予树脂基复合材料可持续发展能力,还是降低其成本、扩大其应用范围的长久之计。
免责声明:本网站所转载的文字、图片与视频资料版权归原创作者所有,如果涉及侵权,请第一时间联系本网删除。
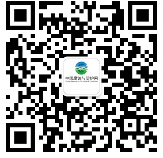
官方微信
《腐蚀与防护网电子期刊》征订启事
- 投稿联系:编辑部
- 电话:010-62316606
- 邮箱:fsfhzy666@163.com
- 腐蚀与防护网官方QQ群:140808414