
随着电子产品向轻薄化、微型化和高精度化的方向发展,表面组装技术(SMT)已成为电子组装行业的主流技术之一[1]。焊膏是SMT的主要材料之一,由85%~92%(质量分数)焊锡粉(焊粉)和一定比例的助焊剂配制而成。其中,焊粉由焊料合金熔体通过雾化工艺后,经分级筛选制得;助焊剂由溶剂、活性剂、成膜剂、触变剂及其他添加剂组成。理想的焊膏兼具储存稳定性和可焊性,然而这对指标却相互矛盾:良好的可焊性要求焊膏具有较高的活性,而高活性意味着焊膏中焊粉的腐蚀倾向性强,即焊膏的储存稳定性差[2]。
焊膏的储存稳定性由焊粉和助焊剂两者共同决定[3-4]。当焊粉与助焊剂接触,助焊剂中有机酸与焊粉表面氧化层反应,氧化层被逐渐腐蚀后,酸又进一步腐蚀暴露出的金属,这些化学反应使得焊膏黏度增大,焊膏储存稳定性变差。焊粉的腐蚀行为也受其自身特性的影响。优质的焊粉具有粒径小,粒度分布窄,球形度高,含氧量低等特点[5-6]。焊粉表面形貌对耐蚀性的影响也不容忽视。工业实践表明,即使两种焊粉的粒度、含氧量都相近,超声雾化焊粉配制的焊膏的稳定性比离心雾化焊粉配制的焊膏更好。对该现象最直观的解释是超声雾化焊粉表面比离心雾化焊粉表面更光滑。然而焊粉表面形貌会随腐蚀发生变化,从而影响焊粉的耐蚀性,进一步影响焊膏产品的存储稳定性,目前关于这方面深入细致的报道并不多见。
基于此,作者使用超声雾化焊粉和离心雾化焊粉制备焊膏,将焊膏放置在低温环境中储存不同时间后,利用扫描电镜和X射线光电子能谱研究了两种焊粉表面形貌及氧化层厚度随时间的变化,对两种焊粉耐蚀性的差异进行了分析。
1. 试验
超声雾化焊粉和离心雾化焊粉均为商用产品,取自云南锡业锡材有限公司,产品型号为YT-4a粉,对焊粉充氮密封。焊膏由新鲜焊粉和JJ400F-5助焊剂搅拌制得。焊膏在4~6 ℃恒温存放(焊粉在焊膏中腐蚀)7、15、45 d后分别取样清洗。清洗流程如下:取适量锡膏入离心管,加入适量丙酮后,超声清洗40 s并重复4次,待溶剂澄清后再用乙醇清洗1次。将清洗后焊粉用氮气吹干并迅速进行表征。
使用LECO RO600型氧分析仪测试焊粉含氧量,使用Horiba LA950激光粒度仪测试焊粉的粒度。使用Hitachi U8010型场发射扫描电子显微镜(FESEM)和IXRF system 550i型能谱仪(EDS)对焊粉形貌和元素进行分析。使用Thermofisher K-Alpha型X射线光电子能谱(XPS)对焊粉Sn化学价态进行表征。
通过氩离子溅射方式对焊粉表面进行刻蚀使其表层剥离,再用XPS分析剥离后表面Sn、O元素含量。由于焊粉表面氧化层较薄,离子刻蚀移除的单层应尽量薄。另外,氩离子刻蚀金属氧化物通常会产生择优溅射,改变氧化物本体的化学计量比。为尽可能降低氧化锡的择优溅射,选用的离子束能应尽可能低。本研究中,选择较“柔和”的刻蚀参数,即氩离子束能500 eV的低束流(1 μA)模式,经SiO2/Si标样标定的刻蚀速率为0.15 nm/s,设置单层溅射时长为20 s,每个样品刻蚀总时间为200 s。利用Avantage软件对XPS数据进行拟合、分析。
2. 结果与讨论
2.1 焊粉初始特征
由图1可知,超声雾化焊粉和离心雾化焊粉的初始粒径分布集中,且都符合高斯分布,中位粒径(D50)分别为32 μm和28 μm,符合4号粉特征(28~36 μm)。
由图2可知,超声雾化焊粉和离心雾化焊粉Sn 3d5的XPS高分辨图谱呈双峰结构,484.8 eV附近小峰对应于Sn0,486.8 eV位置的峰明显宽于Sn0的峰,这是因为Sn2+,Sn4+的峰叠加。通常,Sn2+和Sn4+的3d5峰结合能差值为0.5~0.7 eV,而商用单色化XPS设备的能量分辨率在0.5 eV左右(以Ag 4f7半峰宽标定),难以准确辨析Sn2+、Sn4+的子峰,因此将该峰归为Snx+。曲线拟合得到两种焊粉的Sn0、Snx+峰面积比均为22∶78,这说明两种粉体的初始表面被相同厚度的氧化层包覆。由文献[7]算得Sn 3d层光电子的衰减长度(λ)约为1.1 nm,初略估算表面氧化层厚度小于Sn 3d光电子的逃逸深度(3λ)即3.3 nm。该厚度的评估为XPS深度剖析刻蚀参数的确定提供了参考依据。测氧仪测得超声雾化焊粉和离心雾化焊粉的氧含量分别为0.072‰(质量分数,下同)和0.083‰。
由图3可见,超声雾化焊粉表面光滑平整,离心雾化焊粉表面布满橘皮状凸起。
以上试验结果说明两种焊粉的粒径分布、表面氧含量及氧化层厚度都相近,但其表面形貌存在差异,所以其储存稳定性也有明显差异。
2.2 腐蚀形貌和微区元素含量
由图4(a~c)可见,在焊膏中腐蚀7 d后,超声雾化焊粉中仅少量粉体表面出现零星的腐蚀坑,随腐蚀时间的延长,腐蚀坑数量明显增多。统计发现存储7、15、45 d后,出现腐蚀坑的粉体个数占比分别为7%,11%和11%。由图4(d~f)可见,在焊膏中腐蚀7 d后,离心雾化焊粉中所有粉体形貌均因腐蚀发生变化,粉体表面的橘皮状凸起已不明显,原本的凸起间隙处变为凹坑,随腐蚀时间的延长,凹坑有变深和扩大的趋势。
使用扫描电镜背散射模式对在焊膏中腐蚀45 d后两种焊粉形貌进行对比分析。在焊膏中腐蚀45 d后,两种焊粉表面都可观察到白色颗粒,见图5(a~b),但超声雾化焊粉表面白色颗粒弥散分布在整个样品表面,见图5(c),离心雾化焊粉表面的白色小颗粒则多分布在样品缝隙中,见图5(d)。由于背散射电子信息随原子序数变化比二次电子更敏感,原子序数越大的区域呈像越亮,推测这类颗粒为富Ag相。
使用能谱仪对图5中样品白色区域和灰色区域进行元素分析,结果如表1所示。结果表明:白色区域1,3为富Ag相;灰色区域2,4则未检出Ag。
区域 | 原子分数/% | ||
---|---|---|---|
Cu | Ag | Sn | |
1 | 0.79 | 17.31 | 81.90 |
2 | 1.03 | 0.00 | 98.98 |
3 | 1.79 | 11.20 | 87.01 |
4 | 0.78 | 0.00 | 99.22 |
2.3 锡和氧在焊粉深度方向分布
图6为在焊膏中腐蚀不同时间后Sn和O在焊粉深度方向的分布。氩离子溅射过程中,刻蚀深度随刻蚀时间延长而增加,因此图6中用刻蚀时间表示刻蚀深度。由图6(a)可见,两种新鲜(腐蚀时间为0)焊粉中O元素含量随刻蚀时间的变化曲线几乎重合,这说明两种焊粉初始氧化层厚度基本一致。由图6(b~d)可知,尽管两种焊粉初始表面的Sn,O含量都较接近,但在焊膏中腐蚀不同时间后,Sn,O含量在深度方向上分布却显示出差异。离心雾化焊粉中O含量随刻蚀时间延长显示出更陡峭变化趋势。使用双切线法对氧化层厚度进行考察[8],结果表明:超声雾化焊粉的双切线交点从36 s(腐蚀0 d)变为31 s(腐蚀45 d);而离心雾化焊粉的双切线交点则从35 s(腐蚀0 d)变为24 s(腐蚀45 d)。显然,随腐蚀时间延长,离心雾化粉体氧化层变薄明显,说明离心雾化粉体受到更剧烈的腐蚀。
为验证图6的推论,对腐蚀不同时间后焊粉的Sn 3d5高分辨图谱进行分峰拟合,由于焊粉的原始表面不可避免会吸附C,O等污染物,且可能有少量溶剂残留,因此以刻蚀20 s后的图谱为研究对象,结果如图7所示。图中484.5 eV处为金属锡Sn0,其半峰宽为(0.97±0.05)eV;486.5 eV处为氧化态锡Snx+,其半峰宽为(1.74±0.06)eV。由该图可知,随腐蚀时间延长,两种焊粉亚表面金属锡含量都呈增长趋势,说明在锡膏中焊粉表面氧化层都有所减薄。但离心雾化焊粉表面的金属锡含量显著增加,而超声雾化焊粉表面金属锡含量则相对较稳定。定量拟合结果表明,超声雾化焊粉中Sn0/Snx+原子比从1.22增加至1.33;而离心雾化焊粉中Sn0/Snx+原子比则从1.38增至2.19,见图8。该结果同样说明,在焊膏中离心雾化焊粉受到的腐蚀即与助焊剂反应比超声雾化焊粉更明显。但两种焊粉中Sn0/Snx+原子比并非随腐蚀时间延长单调递增。这是因为粉体制样时粉体表面不可能完全平整,而表面细微差异会引起Sn0/Snx+原子比变化。
2.4 讨论
离心雾化和超声雾化形成的液滴都经历了快速凝固过程。Pandat Scheil模拟结果表明液滴冷凝过程依次形成β-Sn主相→Cu6Sn5→三元共晶相,直至终止,而在实际冷凝过程中Ag3Sn与三元共晶相同时形成[9]。离心雾化液膜被甩出转盘后在气体氛围中快速凝固,首先析出β-Sn主相,过快冷凝收缩导致颗粒表面出现橘皮状凸起和凹坑,金属间化合物随后析出,并在凹坑区域富集[10-12]。β-Sn相和富Ag相具有不同的电极电位,在微区形成腐蚀原电池,导致电化学腐蚀,富Ag相的聚集会加剧电化学反应。另外,晶界和相界处缺陷和杂质较多,从热力学角度分析,腐蚀反应在此位置最易发生,然后向整个粉体扩展[13],因此离心雾化粉体最终出现整面腐蚀。在超声雾化过程中,凝固核心或枝晶在高频超声能量的作用下破碎,促进了粉末组织的细化,同时减弱了合金元素的凝固偏析[14],因而粉体表面相对光滑,富Ag相弥散在整个表面,在较大富Ag颗粒位置优先出现点状腐蚀,但多数颗粒仍保持表面光滑平整。
3. 结论
(1)虽然两种焊粉的粒径分布、含氧量都相近,但由于表面形貌不同,焊粉在耐助焊剂腐蚀性方面表现出巨大差异。离心雾化焊粉富含枝晶结构、晶界和相界,富Ag相在晶界、相界聚集,腐蚀由晶界向整个粉体蔓延;而超声雾化粉体腐蚀则优先在较大的富Ag相位置发生。
(2)两种焊粉初始表面氧化层厚度几乎一致,但制成锡膏后,离心雾化焊粉表面氧化层减薄更快。
(3)粉体表面合金相、晶界和相界分布,是决定焊粉耐腐蚀性的重要因素。
免责声明:本网站所转载的文字、图片与视频资料版权归原创作者所有,如果涉及侵权,请第一时间联系本网删除。
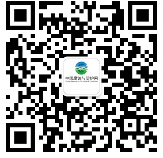
官方微信
《腐蚀与防护网电子期刊》征订启事
- 投稿联系:编辑部
- 电话:010-62316606
- 邮箱:fsfhzy666@163.com
- 腐蚀与防护网官方QQ群:140808414