
埋地管道是我国油气运输的主要方式之一,在服役过程中土壤腐蚀是埋地管道需面临的安全问题之一,管道腐蚀泄漏会造成经济损失[1-4]。因此对埋地管道土壤腐蚀的研究不可或缺。然而我国地域广阔,土壤成分复杂,土壤含水量、温度、溶解离子种类和含量等因素都会影响埋地管道的腐蚀。
国内外学者针对不同地域土壤中埋地管道的腐蚀情况进行了研究。现场土壤埋片试验法是将管线钢材料长时间埋于典型土壤中,并分析得到其腐蚀情况的一种传统研究方法。王鸿膺等[5]在川气东送管道沿线典型土壤中选取了110个埋片试验点,对X70管线钢进行了200 d的埋片试验,得到X70管线钢在不同地区的腐蚀情况;美国国家标准局和200家协作商,经过45 a的时间完成了333种材料在128个站点的埋片试验[6]。虽然传统的现场埋片试验法得到的结果最接近管道实际腐蚀情况,但是其整个试验周期长,投入大,需要消耗大量的人力和物力。相较于传统的现场土壤埋片试验法,模拟土壤溶液试验法具有加速腐蚀、缩短腐蚀周期、节省试验成本的特点,被广泛用于管线钢的土壤腐蚀试验中[7-8]。CONTRERAS等[9]以pH 8.5的模拟地下水溶液作为腐蚀环境,研究了力学和环境作用对X52管线钢应力腐蚀开裂敏感性的影响。QIN等[10]以大港土壤浸出液为腐蚀介质,研究了交流电频率对X80管线钢腐蚀行为的影响,发现交流电可改变腐蚀产物的成分比例。WANG等[11]以酸性土壤模拟溶液为基础,分析了pH和溶解氧含量对X80钢腐蚀行为的耦合作用和腐蚀机理。徐立等[12]以武汉市石化园区内典型土壤浸出液为基础,研究了、Cl-、
、
等不同离子含量下Q235钢的腐蚀规律。
“川气东送”是我国继“西气东输”之后又一大型跨地区天然气输送工程,该工程自川东北达州地区至上海地区,途径6省2市。作者结合实际工况,以西南油气田川东北地区土壤模拟液为腐蚀介质对X65管线钢进行不同时间的浸泡腐蚀试验,通过扫描电镜(SEM)和X射线衍射仪(XRD)观察腐蚀产物和腐蚀形貌,并结合失重法分析了X65管线钢在川东北地区土壤模拟液中的腐蚀行为,为该埋地管材在川东北地区的应用提供数据支持。
1. 试验
1.1 试验材料与试样
试验材料为西安向阳航天材料股份有限公司提供的X65管线钢,其化学成分(质量分数)为:0.100% C、0.280% Si、1.450% Mn、0.006% P、0.002% S、0.062% V、0.026% Nb、2.80% Mo、0.013% Ti,余量Fe。
依据国家标准GB/T 18175-2000《水处理剂缓蚀性能的测定 旋转挂片法》、GB/T 19291-2003《金属和合金的腐蚀 腐蚀试验一般原则》,将X65管线钢制成10组30 mm×15 mm×3 mm的挂片试样,然后依次用200号、400号、600号、800号和1000号砂纸对试样工作表面进行打磨,再用无水乙醇和去离子水对试样进行超声清洗,吹干后备用。试验开始前,用精度0.000 1 g的天平对试样进行称量。
1.2 试验溶液
土壤中的阴离子是材料发生腐蚀的主要因素,“川气东送”川东北地区土壤中阴离子含量分别为0.014 64%(质量分数,下同)、0.014 2%Cl-、0.034 56%
,pH为7.1。为加速腐蚀,试验溶液为阴离子含量放大100倍的土壤模拟液,采用分析纯试剂和去离子水配制,具体成分如下:2.341 g/L NaCl、2.016 g/L NaHCO3、5.110 g/L Na2SO4,用0.01 mol/L HCl和NaOH将模拟液的pH调整至7.1。
1.3 试验过程与表征
参照JB/T 7901-2001《金属材料实验室均匀腐蚀全浸试验方法》在25 ℃的ZBRTD-211电热恒温水浴锅中进行静态浸泡试验,研究浸泡时间对X65管线钢腐蚀行为的影响。采用绝缘细丝固定试样并将其竖直浸泡于土壤模拟液中,为研究材料在不同时间段的腐蚀特性,10组试样的浸泡时间分别为24、48、72、96、120、144、168、240、480、720 h。整个浸泡试验过程中,试样均处在(25±1)℃温度下,且每24 h更换一次试验溶液。
依据GB/T 16545-2015《金属和合金的腐蚀腐蚀试样上腐蚀产物的清除》对试样进行除锈。用500 mL盐酸、5 g 1,3-二丁基-2-硫脲和蒸馏水配制成1 000 mL的除锈液,将除锈液放入25 ℃的恒温水浴锅中,再将试样放入除锈液中,使用玻璃棒剧烈搅拌5 min,得到除锈后的试样。采用失重法计算试样在不同阶段的腐蚀速率,如式(1)所示。
|
(1) |
式中:vcorr为试样的腐蚀速率,mm/a;S为试样的表面积,m2;m1为腐蚀前试样质量,g;m2为腐蚀后试样质量,g;t为试验时间,h。
采用ZEISS EV0 MA15型扫描电子显微镜(SEM)观察试样表面腐蚀产物和腐蚀形貌,采用DX-2700型X射线衍射仪(XRD)分析试样表面腐蚀产物的物相。
2. 结果与讨论
2.1 腐蚀产物宏观形貌
图1为在土壤模拟液中浸泡不同时间后试样表面腐蚀产物的宏观形貌。结果表明,浸泡24 h后,试样表面仅仅生成少量棕红色腐蚀产物;在48~120 h随着浸泡时间的延长,棕红色腐蚀产物逐渐增加,直至完全覆盖住试样表面;当浸泡时间延长至144~168 h时,试样表面锈层局部出现深褐色和黑色条状腐蚀产物,且随着浸泡时间延长,黑色条状腐蚀产物面积逐渐增加,试样表面层次感分明;当浸泡时间延长至240~720 h时,试样表面腐蚀产物趋于平坦,试样表面被深褐色腐蚀产物完全包裹,黑色腐蚀产物分布面积进一步扩大。
2.2 腐蚀产物的微观形貌和成分
图2和图3为试样在土壤模拟液中浸泡不同时间后的微观腐蚀形貌。结果表明:浸泡24 h后,试样表面几乎没有腐蚀产物,仅出现少量颗粒状腐蚀产物;浸泡48 h后,腐蚀产物明显增加,并出现了细小的蚀坑;浸泡时间延长至72 h后,试样表面出现大量絮状腐蚀产物,并伴随着产生裂纹;浸泡96 h后,絮状腐蚀产物进一步增加且变得密集,并逐渐出现了少量团簇状腐蚀产物,如图3(a)所示;浸泡120 h后,腐蚀产物几乎覆盖整个试样表面,腐蚀产物呈絮状,少量呈花瓣状,并且腐蚀产物出现分层现象,表层腐蚀产物不均匀且存在一定的孔洞及空隙;浸泡144 h后,试样表面出现较为明显的单层腐蚀产物膜,腐蚀产物更加紧密,放大后可见腐蚀产物主要呈絮状、团簇状与花瓣状,而非单一密集的絮状,如图3(b)所示;浸泡168 h后,腐蚀产物发生分层现象,并有大量针状腐蚀产物生成,如图3(c)所示;浸泡时间延长至240~720 h后,腐蚀产物膜分层明显,外层腐蚀产物呈现单一的絮状且逐渐变得密集,如图3(d)所示,但外层腐蚀产物不够致密,会出现剥落的情况。
对浸泡时间为24、96、240、480、720 h的5组试样进行XRD分析,如图4所示。从图4中可以看出,当浸泡时间为24 h时,由于腐蚀产物的量极少,因此XRD只检测到基体纯Fe相;当浸泡时间延长至96 h时,腐蚀产物主要为Fe3O4、Fe2O3、FeO(OH);随着浸泡时间进一步延长,腐蚀产物并没有发生变化,但腐蚀产物峰不断升高,说明腐蚀产物含量不断提高。
2.3 表面腐蚀形貌
对经过不同时间浸泡的试样进行除锈、干燥,其表面腐蚀形貌如图5所示。当浸泡时间为24 h时,试样表面开始出现鼓泡,此时并无腐蚀坑出现;当浸泡时间达到48 h时,鼓泡现象进一步加剧;当浸泡时间延长到72 h时,试样表面鼓泡数量减少,并出现少量的小蚀坑;当浸泡时间达到96 h时,试样表面出现大量蚀坑,相较于72 h时蚀坑有逐渐变多加深且逐渐相互扩展的趋势;当浸泡时间延长到120 h时,蚀坑进一步扩大,部分蚀坑相连,形成了外部较大但内部有多个深度不同蚀坑的复合蚀坑;当浸泡时间达到144 h和168 h时,蚀坑的深度变深;当浸泡时间延长到240 h时,除了腐蚀坑进一步扩展外,试样表面整体出现腐蚀,表面减薄,呈均匀腐蚀的趋势。通过分析不同浸泡时间试样的腐蚀形貌可以发现,随着浸泡时间的延长,试样首先出现不均匀的蚀坑,蚀坑进一步发展,试样逐渐呈均匀减薄的特点,当浸泡时间进一步延长时,试样整体表现为均匀腐蚀。
3. 腐蚀过程分析
图6为试样在土壤模拟液中浸泡不同时间的腐蚀速率。结果可见,随着浸泡时间延长,腐蚀速率呈现出先增加后降低的趋势,当浸泡时间为120 h时,腐蚀速率最大,为0.850 mm/a。
在本研究中,土壤模拟液为pH 7.1的弱碱性溶液,此时溶液中的H+达到饱和含量,并不会参与析氢反应,因此阴极只会发生去氧反应[13]。土壤模拟液中还含有大量的和
,这些离子会加速阳极反应,甚至使试样表面预先形成的氧化膜失效[14],同时,试样表面也没有形成致密的钝化膜,试样基体与土壤模拟液直接接触发生反应,反应过程如下:
阳极:
|
(2) |
阴极:
|
(3) |
由于以上反应的进行,土壤模拟液中存在大量的OH-,OH-与阳极反应产生的Fe2+生成难溶的Fe(OH)2,见式(4)。
|
(4) |
此时Fe(OH)2继续被土壤模拟液中的溶解氧氧化生成深褐色的Fe(OH)3,见式(5)。
|
(5) |
Fe(OH)3并不稳定,会转变为FeO(OH),并进一步转变为黑色的Fe3O4,见式(6)~(7)。
|
(6) |
|
(7) |
川东北土壤模拟液中含有大量,
会与阳极析出的Fe2+生成不稳定的FeCO3,并最终生成稳定的铁氧化物,反应式见式(8)~(11)。这在XRD分析结果和试样形貌中得到了印证。
|
(8) |
|
(9) |
|
(10) |
|
(11) |
随着浸泡时间延长,絮状腐蚀产物在试样表面形成,然而此时附着在试样表面的腐蚀产物并不能形成稳定的钝化膜,如图2(c)所示。由于土壤模拟液中含有大量的,
会抑制表面腐蚀产物的生长,此时腐蚀产物的溶解快于生成,因此试样表面发生局部不均匀腐蚀,如图5(c)所示。同时,土壤模拟液中还存在Cl-,其在金属表面的吸附能力比氧更强,腐蚀开始时,Cl-在阳极区富集,占据了阳极区表面氧的吸附位置,形成了不稳定的可溶性氯化物。由于氯化物和阳极区表面反应较快,局部不均匀腐蚀加速[15],因此当浸泡时间为24~120 h时,腐蚀速率不断变大,从0.139 mm/a增加至0.850 mm/a。当浸泡时间延长至144~168 h时,试样表面形成覆盖住基体的单层腐蚀产物膜,该产物膜对基体表面具有一定的保护作用,且Cl-更易吸附在腐蚀产物膜表面[16]。因此当浸泡时间为144 h和168 h时,腐蚀速率分别降为0.778 mm/a和0.751 mm/a。但此时产物膜表面仍然存在大量的裂纹和孔洞,如图2(f)和图2(g)所示,Cl-可以穿过腐蚀产物膜到达基体表面并腐蚀基体,导致蚀坑的尺寸不断加大,如图5(e)和图5(f)所示。当浸泡时间超过240 h后,试样表面形成了外层为单一絮状,内层致密的腐产物蚀膜,如图2(h)所示。虽然Cl-能穿过外层腐蚀产物膜到达内层,但由于内层腐蚀产物膜致密且贴合于基体表面,Cl-无法穿过内层腐蚀产物膜与基体接触,对局部蚀坑的长大起到抑制作用,因此腐蚀速率大幅下降至0.436 mm/a,且随着浸泡时间的延长,内层腐蚀产物膜越来越致密,对基体腐蚀的抑制效果也越来越明显,其腐蚀速率不断降低,最终达到0.301 mm/a,试样整体呈现为均匀腐蚀的形貌。
4. 结论
(1)在川东北土壤模拟液中,当浸泡时间为24~120 h时,X65管线钢的腐蚀产物以单层红棕色产物为主;浸泡168 h后,腐蚀产物出现分层现象,呈条状深褐色和黑色;当浸泡时间大于240 h后,X65管线钢表面完全被腐蚀产物包裹且腐蚀产物分层明显,腐蚀产物主要由Fe3O4、Fe2O3、FeO(OH)组成。
(2)在川东北土壤模拟液中,X65管线钢首先发生以不均匀腐蚀为主的局部腐蚀。当浸泡时间为24~120 h时,其腐蚀速率不断提高,由0.139 mm/a增加至0.850 mm/a;浸泡168 h后,单层腐蚀产物对基体起到一定保护作用,腐蚀速率下降至0.751 mm/a,但腐蚀产物缺陷较多,蚀坑仍会扩大;当浸泡时间大于240 h后,双层腐蚀产物膜对基体的保护性较好,腐蚀速率下降至0.301 mm/a,且腐蚀形貌从局部腐蚀转变为均匀腐蚀。
免责声明:本网站所转载的文字、图片与视频资料版权归原创作者所有,如果涉及侵权,请第一时间联系本网删除。
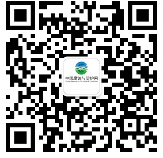
官方微信
《腐蚀与防护网电子期刊》征订启事
- 投稿联系:编辑部
- 电话:010-62316606
- 邮箱:fsfhzy666@163.com
- 腐蚀与防护网官方QQ群:140808414