热障涂层 (TBCs) 是一种高温防护涂层,主要由抗高温氧化的合金粘结层和起隔热作用的陶瓷面层组成。上世纪40年代末50年代初,美国宇航局 (NASA) 首次提出了这一概念。1963年普惠公司首次把TBCs用在JT8D型燃气轮机的火焰筒中。如今,TBCs已广泛应用于地面燃气轮机燃烧室、尾喷管和其他热端部件的高温防护。
6%~8% (质量分数,下同) Y2O3部分稳定的ZrO2(YSZ) 热导率低、热膨胀系数大、抗热冲击性能好,是目前广泛使用的TBCs陶瓷表层材料。但是,YSZ的使用一般仅限于清洁能源,并且工作温度高于1200 ℃时,相变形成约4%体积变化会导致涂层开裂失效。同时,YSZ极易烧结及晶粒长大,导致涂层热导率上升、杨氏模量增大,从而加速涂层的剥落失效。
研究表明,YSZ的热腐蚀已成为除高温氧化外导致TBCs失效的另一种主要因素。YSZ的热腐蚀主要有:S、V、Na熔盐腐蚀和CMAS腐蚀。现在的燃气轮机使用的燃料为天然气,不可避免地含有V、S、Na等杂质,以Na2SO4和NaVO3形式沉积在涡轮叶片上。高温下,YSZ中的Y2O3会与这些熔盐发生反应失去相稳定作用,产生相变应力,导致涂层开裂失效。因此,发展新型抗热腐蚀的陶瓷层材料是目前TBCs研究的一个重要方向。
本文基于稳定剂种类重点总结了不同氧化物改性的ZrO2陶瓷涂层抗Na2SO4+NaVO3热腐蚀性能,以及提高陶瓷层材料耐腐蚀性能的理论和方法,对设计长寿命、高可靠性的新型TBCs材料具有指导意义。
1 不同氧化物改性的ZrO2陶瓷涂层抗Na2SO4+NaVO3热腐蚀性能
基于传统YSZ涂层耐Na2SO4+NaVO3热腐蚀性能较差的情况,国内外研究人员针对ZrO2进行了大量的稀土氧化物或其他氧化物的掺杂改性研究,来提高其耐腐蚀性能。掺杂方式可分为单元掺杂、二元掺杂和多元掺杂,掺杂的氧化物主要包括CeO2,La2O3,Sc2O3,In2O3,Ta2O5,TiO2,Gd2O3和Yb2O3等。
1.1 单元掺杂
在Y2O3掺杂ZrO2的体系中,6%~8%Y2O3热循环寿命最好,如图1所示。Miller提出增加YSZ中Y2O3的含量,可以推迟m-ZrO2的形成,提高涂层耐熔盐热腐蚀能力。但是涂层力学性能较差,容易脱落。TBCs材料的选择有严格的限制,其中高温下的力学性能决定着陶瓷层材料的性能与实际应用。在过去的30多年里,6%~8%Y2O3稳定的ZrO2陶瓷涂层由于其综合性能最好,一直占据主导地位。
Jones等研究了CeO2-ZrO2(CSZ) 熔盐热腐蚀性能,认为CeO2在Na2SO4和NaVO3中的高温热腐蚀性能好于Y2O3,是因为CeO2的酸性更强。但是Ce4+容易变价,会加速涂层烧结,涂层产生裂纹的可能性增大。并且,有研究指出,CeO2稳定的ZrO2在NaVO3的作用下与YSZ发生相变失稳的速度相当。虽然CeO2与NaVO3不发生化学反应,但腐蚀后同样可以在陶瓷表面产生Ce的氧化物,因此NaVO3也能破坏CSZ的结构稳定性。这一作用被称为钒酸盐的矿化作用。矿化作用指的是一些化合物容易形成网状结构,如硼酸盐、氧化硅和钒酸盐,这些化合物在熔融状态下具有很强的溶解能力,能将很多稳定化合物溶解生成玻璃状的产物,温度越高矿化作用越强。
Jones研究了Sc2O3-ZrO2 (即稳定剂Sc2O3含量为100%) 分别在Na2SO4/SO3和NaVO3下的耐腐蚀能力,认为Sc不与这些熔盐发生化学反应,未检测到腐蚀产物,对熔盐的腐蚀作用有很好的抵抗能力。又通过改变Sc含量对Sc2O3-Y2O3-ZrO2(ScYSZ) 的抗NaVO3热腐蚀性能进行进一步研究,结果表明Sc2O3-ZrO2的耐腐蚀能力反而不如含少量Y2O3的,如图2所示。另外,Sc2O3价格昂贵,使用部分Y2O3替代Sc2O3作为ZrO2的稳定剂不仅能提高涂层的耐腐蚀能力,还能降低涂层的制造成本。同时由于多种稀土阳离子的声子散射作用,还能降低涂层的热导率。因此,ScYSZ有望成为新的TBCs陶瓷涂层的候选材料。
由于In2O3的酸性比Sc2O3更强,Jones等[14]也研究了In2O3的抗钒酸盐腐蚀能力,指出In2O3对钒酸盐有着最好的抵抗能力,但是In2O3在喷涂过程中易挥发,涂层稳定性降低,产生较多m-ZrO2。并且和CeO2-ZrO2一样,NaVO3对In2O3-ZrO2也有矿化作用。NaVO3与In2O3不发生化学反应,腐蚀后的In2O3-ZrO2涂层表面没有InVO4或其它明显的反应产物,但该涂层仍易失效破坏。另外,研究[15]表明,In2O3和CeO2这些结构稳定剂虽然耐腐蚀能力好于Y2O3,但它们对ZrO2的稳定能力不如Y2O3,CeO2-ZrO2或In2O3-ZrO2的力学性能也不如YSZ的。这表明,在稳定剂的选择上,Lewis酸碱理论可作为提高涂层耐腐蚀性能的理论指导,但在涂层的实际应用中还应对稳定剂的物理、化学性质以及复合氧化物的力学性质进行综合考量。
单元掺杂的涂层材料可能在耐腐蚀性能方面超过YSZ,但其他性能往往很差,而且优势往往无法弥补其缺陷。二元、多元稀土氧化物复合掺杂的ZrO2陶瓷能在一定程度上弥补单元掺杂的不足。
1.2 二元掺杂
Pidani等使用等离子喷涂 (PS) 制备了25% CeO2-2.5%Y2O3-ZrO2(CYSZ) 涂层,研究其在1000 ℃下耐45%Na2SO4+55%V2O5腐蚀性能,认为该涂层的耐腐蚀性能比YSZ更好,原因是CeO2有着比Y2O3更强的酸性而与酸性腐蚀环境反应倾向更弱;并且该体系的稳定剂含量高,故相稳定性相对较好。同时,该研究结果表明,YSZ在腐蚀12 h后m-ZrO2含量为90%,CYSZ腐蚀30 h后m-ZrO2含量达到86%,说明CYSZ相对YSZ有着更好的耐腐蚀能力,但实际上其耐腐蚀能力仍然较差。图3是YSZ和CYSZ在分别腐蚀12和30 h后的涂层表面的X射线衍射谱 (XRD)。从图3b可见,CYSZ腐蚀后在涂层表面检测到大量CeO2,可能与NaVO3对CeO2强烈的矿化作用有关,这与前面分析单元掺杂CSZ的结果一致。
由于良好的耐腐蚀性能和高温相稳定性能,Sc2O3的掺杂改性近年来受到国内外学者们的青睐。掺杂Sc2O3提高YSZ的抗Na2SO4+NaVO3热腐蚀性能可以概括为三方面的作用:(1) Sc2O3的添加可以显着提高YSZ的高温相稳定性。Liu等研究认为,8.8%Sc2O3-1%Y2O3-ZrO2在1500 ℃下保温300 h仍然保持优良的相稳定性。(2) 由于Sc2O3不与Na2SO4、NaVO3发生化学反应,热腐蚀后,有更多的稳定剂被保存下来,提高了ZrO2陶瓷的稳定能力,因此有更好的耐热腐蚀能力。Liu等[8]进一步研究了8.8%Sc2O3-1%Y2O3-ZrO2涂层在1000 ℃下抗Na2SO4+V2O5热腐蚀性能,腐蚀过程中未观察到腐蚀产物YVO4,ScYSZ具有优异的化学稳定性和相稳定性,ScYSZ与YSZ中的t′-ZrO2、m-ZrO2含量对比如图4所示。(3) ScYSZ与YSZ涂层在Na2SO4+V2O5高温热腐蚀环境下t′-ZrO2相失稳机制不同,对于ScYSZ,含V化合物 (NaVO3、V2O5) 的矿化作用导致稳定剂Sc2O3、Y2O3溶解,t′相发生相变产生应力;而YSZ是因为熔融盐与Y2O3发生化学反应生成腐蚀产物YVO4导致涂层破坏[8]。YSZ的相变既是一个热力学过程又是一个动力学过程,无论采用哪种结构稳定剂也无法将其长期相变温度提高到1200 ℃以上。ScYSZ具有更好的相稳定性及优异的抗熔融硫酸盐、钒酸盐腐蚀能力。该材料对耐高温腐蚀涂层的研究具有重要价值,但Sc2O3价格昂贵,进一步减少Sc2O3的用量或探索新材料的成分设计意义重大。
Habibi等研究了Ta2O5-Y2O3-ZrO2 (TaYSZ) 在1100 ℃下的Na2SO4+V2O5的热腐蚀机理。结果表明,TaYSZ样品经过80 h腐蚀后,只生成少量的腐蚀产物NaTaO3、TaVO5、Ta9VO25、和YVO4,而YSZ样品在腐蚀40 h后便开裂失效,表明TaYSZ比YSZ有更好的耐熔盐热腐蚀效果。研究表明,尽管Ta5+在ZrO2晶格中的固溶度非常有限,但在Ta2O5和Y2O3共掺杂情况下,Ta5+与Y3+在固溶体发生强烈的相互作用产生一种高稳定相YTaO4,YTaO4在ZrO2晶格中的固溶度比单独的Ta5+或Y3+大得多,因此大大降低了Y2O3与NaVO3/V2O5之间反应的可能性。另一方面,涂层成分与钒酸盐发生化学反应的酸碱规律符合Lewis酸碱理论,如表1所示,表中的氧化物和钒酸盐从上至下,从左至右酸性依次增强。Na2SO4与V2O5在高温下反应生成NaVO3,单独的NaVO3呈碱性,会与酸性最强的Ta2O5优先反应,也保留了Y2O3的稳定效果。这表明TaYSZ对Na2SO4+V2O5的热腐蚀也具有良好的抵抗能力,可对该体系作进一步研究。
Habibi等研究报道了TiO2-Y2O3-ZrO2 (TiYSZ) 中的t′相含量比YSZ中的高。TiO2是少有的不以牺牲相稳定性为代价,却可以提高固溶体中t′-ZrO2含量的掺杂剂。他们也分别研究了5.4%~7%Y2O3-ZrO2 (YSZ)、30%CeO2-4.1%Y2O3-ZrO2 (CSZ)、11.4% TiO2-18%Y2O3-ZrO2 (TiYSZ) 在1050 ℃下耐Na2SO4+V2O5热腐蚀性能。认为3种材料中TiYSZ的耐热腐蚀性能最好,虽然有腐蚀产物TiVO4生成,却没有出现YVO4和m-ZrO2。YSZ和CSZ经Na2SO4+V2O5热腐蚀后产生的腐蚀产物为体积粗大、数量多的棒状YVO4和CeVO4,而TiYSZ热腐蚀后产生的腐蚀产物为体积小,数量少的树突状TiVO4。值得注意的是,TiYSZ体系中Y2O3含量较高 (18%),却无腐蚀产物YVO4,说明该体系在Na2SO4+V2O5熔盐中有很好的化学稳定性。3种材料的腐蚀产物扫描电镜 (SEM) 形貌图如图5和6所示。至于掺杂高含量Y2O3却无腐蚀产物YVO4产生的原因还没有相关文献报道,因此TiYSZ体系的抗Na2SO4+V2O5热腐蚀机理仍需进一步明确。
1.3 多元掺杂
稀土锆酸盐和铈酸盐 (Re2(Zr/Ce)2O7) 材料因其很好的相稳定性、低热导率、抗烧结等特点成为国内外开发新TBCs材料的研究热点。尤其是La2(Zr0.7Ce0.3)2O7(LZ7C3) 有着非常低的热导率和优良的抗烧结性能。Xu等使用电子束物理气相沉积 (EB-PVD) 制备了3%Y2O3-LZ7C3涂层材料,并对该涂层进行900 ℃下100 h的Na2SO4+V2O5熔盐热腐蚀实验。研究表明,该体系对V2O5有着相对较好的耐腐蚀能力。稀土元素的原子半径和离子半径随原子序数的增加而逐渐减小的现象称为镧系收缩,从La到Y原子序数逐渐增加,原子失去电子的趋势减小,稀土的金属性从La到Y递减,故La2O3的碱性比Y2O3强,La2O3优先与酸性V2O5反应,保护了Y2O3。但是该体系在Na2SO4熔盐下反应生成腐蚀产物 (YxLa1-x)2O2SO4,在Na2SO4+V2O5混合融盐下反应生成腐蚀产物LaVO4、YVO4、m-ZrO2和CeO2,导致Y2O3和La2O3析出,涂层发生相变,因此3%Y2O3-LZ7C3在这两种腐蚀介质下耐腐蚀能力都很一般。这表明,涂层的耐腐蚀能力与腐蚀剂的相对酸碱度有关。
Guo等研究了2.7%Gd2O3-3%Yb2O3-6%Y2O3-ZrO2 (GdYbYSZ) 陶瓷块材分别在700,800,900和1000 ℃下保温4 h条件下的耐Na2SO4+V2O5热腐蚀性能。结果表明,温度对腐蚀产物几乎没有影响,但随着温度升高,m-ZrO2含量也随着增加。在相同腐蚀条件下,GdYbYSZ比YSZ生成更少量的m-ZrO2,有相对更好的耐热腐蚀能力,原因是Yb2O3酸性比Y2O3和Gd2O3更强,在酸性钒酸盐腐蚀环境中,Y2O3和Gd2O3更易和熔盐发生反应,从而保留了Yb2O3的稳定作用。
ZrO2涂层的掺杂改性研究已历经了半个多世纪,使用单元掺杂寻求综合性能优良的耐腐蚀涂层材料已不太可能。近年来研究者们将目光更多地投向了二元、多元掺杂,可以预测这也是未来TBCs掺杂改性的研究趋势。
2 TBCs耐Na2SO4+NaVO3热腐蚀机理
TBCs因其复杂的自身结构、微组织成分和服役环境,决定了其破坏机制的多样性。典型的YSZ热障涂层结构如图7所示。迄今为止,国内外研究人员对影响TBCs使用寿命的因素进行了大量的研究与报道,概括起来有:陶瓷表层与金属基底热膨胀失配、粘结层的高温氧化与腐蚀、陶瓷表层相变、金属基底的粗糙度及陶瓷表层高温烧结等。目前,对稀土复合掺杂YSZ在高温熔盐下的失效机制研究还不是很多,下面对TBCs的耐Na2SO4+NaVO3热腐蚀机理作一概述。
YSZ涂层作为综合性能最好的陶瓷涂层材料,可以显着提高燃气轮机的工作温度及热效率。但是,YSZ在1200 ℃以上容易发生相变,限制了其在更高工作温度下的使用。实际上,在1100 ℃以上,YSZ涂层的显微结构就已经发生明显变化。一方面,t′四方相在高温环境中会因为Y2O3的扩散而形成Y2O3含量高的c相和Y2O3含量低的t相,t相在随后的冷却过程中会转变为m相,导致晶格发生约4%的膨胀,产生相变应力。另一方面,YSZ中的结构稳定剂Y2O3会与燃气轮机中的燃料杂质硫酸盐、钒酸盐和钠盐反应,使Y2O3从ZrO2晶格中析出,降低了ZrO2的相稳定性,也会发生相变。目前,YSZ熔盐热腐蚀机理研究大多集中在稳定剂与Na2SO4、NaCl、Na3VO4或V2O5的化学反应规律。
研究人员指出,Na2SO4与Y2O3发生化学反应须满足10-3~10-4级别的SO3分解压,所以通常认为在大气环境中单独的Na2SO4不与Y2O3发生化学反应。众多研究表明,与Y2O3发生化学反应使涂层失去稳定性的是钒酸盐,反应方程式如下:
Y2O3也可与V2O5直接发生反应:
以上化学反应的发生,导致YSZ中的结构稳定剂Y2O3被消耗,ZrO2发生t→m相变,晶格产生巨大膨胀使涂层脱落。
在Na2SO4熔盐环境中,ZrO2也会和反应 (2) 中产生的Na2O或Na2SO4分解产生的Na2O发生反应,ZrO2被碱性溶解,反应方程式如下:
随后,Na2ZrO3溶解在熔盐中饱和后析出。由于YSZ被溶解,导致YSZ粉末颗粒出现松散现象;其次,Na2ZrO3也会在涂层的空隙与裂纹中结晶,产生应力导致涂层脱落。
另一方面,对合金基底起保护作用的热生长氧化物 (TGO) 致密层会被Na2O碱性溶解,反应方程式如下:
反应产物Na2NiO2和NaAlO2会溶解在熔盐中,反应方程式如下:
Na2CrO4是一种稳定的氧化物,不会再分解,因此可在一定程度上抑制其他氧化物的碱性溶解。
可见,TGO致密层被Na2SO4腐蚀后生成氧化物NiO、Al2O3和Na2CrO4。这些氧化物呈现疏松多孔的结构特征。疏松氧化层的增厚,以及冷却过程中的热膨胀不匹配,导致疏松层内部积累相当大的压应力,引起疏松氧化层的破碎,最终导致涂层脱落。
另外,Na2SO4熔盐也会通过YSZ-TGO渗透进入粘结层,与粘结层发生化学反应,导致粘结层硫化。尤其是EB-PVD制备的涂层,柱状晶之间存在的间隙和孔洞往往都是从涂层的表面延伸到其根部,使Na2SO4更易渗入,导致TGO层下生成疏松的硫化物层,TGO层与硫化物层之间存在裂纹。过厚的硫化物层将导致涂层剥落。
TBCs在制备过程中,表面会有空隙和裂纹。这些空隙和裂纹对涂层的热导率和应力释放有着积极作用。Na2SO4虽然不与Y2O3直接发生化学反应,但Ramachandra等和Batista等研究指出,熔融Na2SO4会沿着这些扩散通道进入涂层内部,冷却过程中发生凝固,热循环后Na2SO4膨胀系数较大,这些空隙和裂纹产生扩展应力,对涂层产生物理破坏。
矿化作用也是影响涂层耐热腐蚀性能的一个重要因素。这一机制最先由Tani等在CSZ体系中提出,认为CeO2可以与NaVO3发生矿化作用,破坏CSZ的结构稳定性。Liu等[8]在研究ScYSZ体系的抗Na2SO4+V2O5热腐蚀性能中指出,导致涂层性能退化有两个方面:一是与Y2O3发生化学反应,二是NaVO3和V2O5的协同矿化作用将Sc2O3溶解。Dong等研究Sr (Y0.05Yb0.05Zr0.9)O2.95(SrYbYSZ) 抗Na2SO4、V2O5、Na2SO4+V2O5热腐蚀机理时认为,SrYbYSZ陶瓷在900,950和1000 ℃均不与Na2SO4发生反应,认为是Na2SO4的矿化作用导致腐蚀层厚度随着腐蚀温度的升高而增加。但是迄今为止,对矿化作用导致涂层破坏的机理仍然了解的不够深入。
综上所述,涂层的腐蚀包括涂层成分与腐蚀剂发生化学反应或矿化作用,以及熔融态的腐蚀剂对涂层的物理破坏。由于TBCs自身的复杂结构和复杂的服役环境,决定了其在硫酸盐、钒酸盐下腐蚀机制的复杂性。不同的掺杂剂、不同的工作温度,占主导作用的腐蚀机制也可能不同。Lewis酸碱理论可以作为掺杂剂选择上的理论指导,但同时也需考虑燃料中杂质含量、种类、腐蚀介质的相对酸碱度、发动机的工作环境等因素。在设计TBCs材料时,这些都应系统考虑。
3 结论与展望
(1) 探索新的稀土复合掺杂ZrO2陶瓷材料,提高涂层的抗Na2SO4+NaVO3热腐蚀性能对未来TBCs的发展意义重大。目前,TBCs主要应用在航空燃气轮机上,在海面舰艇和陆地燃气轮机以及柴油动力方面应用得少,部分原因就是YSZ在这样的服役环境下不耐热腐蚀。研究新的耐热腐蚀涂层材料不仅可以扩大TBCs的应用领域,还能降低追求清洁燃料的使用成本。
(2) 由于YSZ的综合性能最好,提高TBCs的抗Na2SO4+NaVO3热腐蚀性能,仍需在此基础上对材料进行成分优化,可以预测二元、多元掺杂将会成为主流趋势。
(3) 二元、多元掺杂改性ZrO2陶瓷涂层具有更优异的耐Na2SO4+NaVO3热腐蚀性能。在改善涂层抗熔盐热腐蚀的掺杂剂选择上,可重点关注Sc2O3、Ta2O5或其共掺杂。
(4) 涂层与腐蚀介质的相对酸碱度是决定涂层抗热腐蚀性能的一个重要因素。燃料中杂质含量、种类和发动机的工作环境在研究稀土复合掺杂ZrO2陶瓷涂层抗Na2SO4+NaVO3热腐蚀机理以及掺杂剂选择上应充分考虑。
(5) 有必要更深入系统地研究稀土复合掺杂ZrO2陶瓷涂层的抗Na2SO4+NaVO3热腐蚀机理,特别是要明确熔盐矿化作用对ZrO2陶瓷涂层的破坏机制和影响因素。
免责声明:本网站所转载的文字、图片与视频资料版权归原创作者所有,如果涉及侵权,请第一时间联系本网删除。
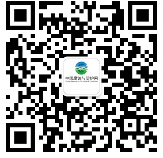
官方微信
《中国腐蚀与防护网电子期刊》征订启事
- 投稿联系:编辑部
- 电话:010-62313558-806
- 邮箱:fsfhzy666@163.com
- 中国腐蚀与防护网官方QQ群:140808414