先进单晶高温合金中难熔元素(Re、W、Mo和Ta)含量的增加引起了偏析加剧、共晶含量增多、元素扩散困难等一系列问题[1-3], 导致合金固溶处理的温度升高、时间延长, 成本显著提高。第三代单晶合金CMSX-10的标准固溶处理制度分为10级, 最高固溶温度达到1365℃, 共耗时45 h[4]。为了降低成本, 尝试对合金的固溶处理制度进行优化[4, 5], 但效果并不理想。传统的分级固溶处理制度为经验式方法, 虽然能够提高初熔温度以使合金达到均匀化, 但并不注重固溶处理过程中合金组织的变化。Hegde等[6]研究发现, 在γ‘相溶解温度以下固溶时合金中共晶的体积分数增加, 共晶的稳定性提高; 在γ’相溶解温度以上长时间等温固溶时共晶中合金元素发生反常的上坡扩散, 引起初熔的产生[6]。在研究CMSX-4合金的固溶处理时, Reed等也预测了共晶区域上坡扩散的发生[7]。由此可见, 在分级固溶处理过程中合金组织的变化尚有不确定性, 直接影响固溶处理制度的优化。本文研究第三代单晶高温合金DD33在分级固溶处理过程中组织的演变。
1 实验方法
实验用合金为第三代镍基单晶高温合金DD33, 其难熔元素的总含量(质量分数)(W+Mo+Re+Ta)为19.5%, C、B的含量分别为0.04%和0.003%。
先用真空感应炉熔炼母合金, 然后采用以锡为冷却介质的液态金属冷却(LMC)定向凝固技术制备[001]取向的单晶试棒, 凝固过程中的抽拉速率为8 mm/min。在直径为16 mm的单晶试棒上垂直于定向凝固方向切取10 mm厚的试样, 进行分级固溶处理实验。固溶处理的温度区间为1240-1340℃, 具体的固溶处理工艺如图1所示。固溶处理时, 将各温度段所需的样品一起放入箱式热处理炉中加热, 每个温度段结束后迅速从炉中取出一个试样在空气中冷却, 其它样品继续升温。
图1 合金的固溶处理工艺
使用Axiovert200MAT光学显微镜(OM)和S-3400N扫描电子显微镜(SEM)观察合金铸态和固溶处理不同阶段的组织。常规腐蚀所用的试剂为4 gCuSO+10 mlHCl+20 mlHO,观察碳化物演变所用的深腐蚀试剂为70%HCl+30%HO。用定量金相法测量合金中碳化物的体积分数,每个温度段采用10张200倍的扫描背散射照片进行统计。用电子探针(EPMA)测量固溶处理过程中共晶冠处粗大γ‘相的成分, 束斑直径为1 μm, 每个试样测3点取平均值。
2 结果与讨论
2.1 铸态组织
如图2a所示, 合金铸态为典型的枝晶组织, 枝晶间存在白亮的(γ+γ’)共晶。定量金相统计结果表明, 合金的一次枝晶间距约为140 μm, 共晶含量约为9.5%。图2b为枝晶间(γ+γ‘)共晶的形貌, 可以看出, 共晶为典型的葵花状, 共晶芯由细小的γ和γ’两相组成, 共晶冠为粗大的γ‘相。在枝晶干和枝晶间析出了两种不同尺寸和形貌的γ’相, 如图2c和d所示。枝晶干γ‘相尺寸较小, 呈立方状; 枝晶间γ’相尺寸较大, 呈蝴蝶形。草书体状碳化物分布于枝晶间(图2e)。从能谱(EDS)分析的结果(图2f)可以推断, 这些碳化物为主要含Ta和Ti的MC型碳化物。
图2 铸态合金的枝晶组织及析出相
2.2 固溶处理过程中的组织演变
图3给出了合金在1240℃/2 h和1260℃/2 h固溶后的显微组织。如图3a中箭头所示, 合金中最先固溶的区域为共晶前沿及碳化物周围, 在这些区域中出现了γ’相贫化区。随着温度的提高, 枝晶干γ‘相也开始逐渐溶解(图3b)。对比图3c和d的放大照片可见, 枝晶干γ’相的溶解与长大并存; 同时, 其它区域的γ‘相也长大了: 二次枝晶臂及枝晶间的γ’相相互连接, 形成近似筏化的形态; (γ+γ‘)共晶芯发生粗化, 共晶冠的大块γ’相相互合并形成一个整体。
图3 合金在1240℃/2 h和1260℃/2 h固溶后的显微组织
图4给出了合金在1280~1340℃各温度段固溶后的显微组织。由图4a可见, 在1280℃/2 h固溶后枝晶干γ‘相已经完全溶解, 二次枝晶臂上的γ’相也部分溶解。对比图4a、b和c可见, 随着固溶温度的升高枝晶间γ‘相并没有显著溶解, 反而在1310℃时明显长大, 共晶γ’相也有粗化的趋势。枝晶间γ‘相完全溶解的温度为1320℃, 此时共晶也开始溶解(图4d)。当温度达到1330℃时共晶基本消除, 只有少量的残余共晶存在(图4e)。进一步提高温度到1340℃, 合金中出现初熔, 初熔形貌如图4f所示。
图4 合金在1280~1340℃各温度段固溶后的显微组织
在分级固溶处理过程中, MC碳化物也发生了变化。图5给出了固溶处理过程中MC碳化物形貌的演变, 可以看出, 温度低于1280℃时MC碳化物还保持草书体状(图5b); 温度达到1280℃后草书体状碳化物逐渐破碎, 变得圆滑(图5c); 到1310℃时, 碳化物已经变为颗粒状(图5d)。EDS分析结果表明, 碳化物的成分并没有发生明显的变化, 说明碳化物的类型没有改变, 只是发生了溶解。图6为固溶处理过程中MC碳化物体积分数的变化曲线, 如图所示, MC碳化物的含量随固溶温度的升高逐渐降低, 到1310℃时, 已由铸态的0.55%降低到0.36%。
图5 固溶处理过程中MC碳化物形貌的变化
图6 分级固溶处理不同阶段MC碳化物体积分数的变化曲线
从γ’相的溶解过程可见, 在合金中不同区域γ‘相的溶解温度不同, 这是凝固偏析导致的成分差异造成的。在凝固过程中枝晶干的单相g 固溶体率先形成, Al、Ta等γ’相形成元素向枝晶间液相富集, 当剩余液相的溶质浓度达到共晶点时生成(g +γ‘)共晶[8]。合金的这种凝固特点导致Al、Ta含量从枝晶干到枝晶间逐步升高。研究表明, Ta能够提高γ’相的高温稳定性, 使其溶解温度更高[9]。因此, 合金中γ‘相的溶解温度由低到高依次为: 枝晶干γ’、枝晶间γ‘、共晶γ’。在低于1320℃时枝晶间γ‘相尚未达到溶解温度, 不发生溶解。但是为了降低界面能γ’相会长大, 其长大方式极可能为Ostwald熟化。同时, 在MC碳化物在界面能的作用下发生溶解[10], 并向枝晶间的基体中释放出大量的Ta原子。Ta为γ‘相形成元素, 能促进γ’相的长大。随着温度的提高Ta元素的扩散变得更加容易, γ‘相的长大速率增加。因此, 在1310℃恒温时枝晶间γ’相发生明显长大。同样, 共晶γ‘相在这期间也发生粗化, 这与Hegde[6]的实验结果一致。
2.3 共晶’成分的变化
图7给出了共晶冠处粗大γ‘相中各合金元素含量(原子分数)随固溶温度的变化曲线。从图7可见, 随着固溶温度的提高Al、Ta等γ’相形成元素的含量先升高后降低, 峰值温度为1310℃, 且Al含量的变化幅度更加显著; Co、Cr、Mo等元素的含量则先降低, 后逐渐趋于平稳; W的含量在1280℃前先缓慢升高, 之后又逐渐降低; Re的含量最低, 几乎没有变化。
图7 共晶γ’相中各合金元素含量随温度的变化曲线
随着固溶处理的进行, 合金中的微观偏析通常逐渐减轻。但是, 在本实验中共晶γ’相中的偏析却出现了反常的加剧。根据文献[6,7]的观点, 这一现象可能是上坡扩散引起的。以锡为冷却介质的LMC定向凝固技术, 其温度梯度达到70-100 K/cm[11], 合金的凝固速率可近似用抽拉速率表示。在拉速为8 mm/min的定向凝固过程中, 共晶的凝固无法在平衡条件下进行。由于凝固速率高, 共晶固液界面前沿的溶质还来不及充分扩散就已经凝固, 使共晶中g 和γ‘两相的成分偏离平衡状态。在固溶处理过程中未达到共晶溶解温度以前, 共晶γ’相的成分会自发地进行调整以降低系统的自由能。此时, 共晶γ‘相中过饱和的Cr、Co、Mo、W等元素向外发生上坡扩散, 从而导致Al、Ta含量的提高。由于Cr、Co、Mo的扩散系数相对较高, 其含量在温度较低时就开始降低; 而W的扩散系数较低, 其含量在1280℃以后才开始降低。此外, 共晶的粗化也可能导致共晶γ’相中成分偏析的加剧。在粗化过程中, 为了使共晶γ‘相的成分向所在温度下的平衡成分转变, 元素发生有选择地扩散, Al、Ta扩散到γ’相表面参与粗化, 从而提高了共晶γ‘相中Al、Ta的含量。
γ’相的溶解过程实质上是溶质原子的扩散过程, 而共晶γ‘相中Al、Ta含量的升高以及γ’相的长大会减慢这一过程。因此, 在确保不发生初熔的前提下应尽量缩短在共晶γ‘相溶解温度以下的固溶时间, 降低上坡扩散和γ’相长大的影响, 以提高固溶处理的效率, 降低固溶处理的成本。
3 结论
1. DD33合金铸态的析出相由枝晶干和枝晶间γ‘相、(g +γ’)共晶以及MC碳化物组成。在分级固溶处理过程中, 枝晶干γ‘相在1280℃/2 h固溶后完全溶解; 枝晶间γ’相在1310℃固溶时明显长大, 而在1320℃/2 h固溶后完全溶解; (g +γ‘)共晶在高于1320℃时才显著溶解。
2. MC碳化物在固溶处理过程中发生溶解, 由草书体状向颗粒状转变。随着固溶温度的提高共晶γ’相中合金元素的偏析加剧, Al、Ta的含量逐渐提高而Cr、Co等元素的含量降低, 这可能是上坡扩散引起的。
2013年11月12日收到初稿; 2014年2月14日收到修改稿。
免责声明:本网站所转载的文字、图片与视频资料版权归原创作者所有,如果涉及侵权,请第一时间联系本网删除。
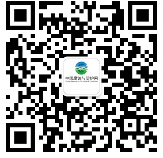
官方微信
《中国腐蚀与防护网电子期刊》征订启事
- 投稿联系:编辑部
- 电话:010-62313558-806
- 邮箱:fsfhzy666@163.com
- 中国腐蚀与防护网官方QQ群:140808414