石墨材料具有优异的耐高温性、热膨胀系数小、导电导热性、抗热震性等特性,因此在冶金、化工、航空航天及核工业中得到广泛应用。然而,石墨材料在高于 400 ℃开始发生氧化,这大大降低了石墨材料的使用性能。因此,解决石墨材料高温氧化问题是其作为高温结构材料的关键。抗氧化涂层技术是提高石墨高温抗氧化的有效方法之一。
碳化硅抗氧化性能较好且与碳材料具有较好的物理和化学相容性,是高温下保护石墨材料的一种有效涂层[3]。目前制备碳化硅涂层的方法主要有:包埋法[4]、化学气相沉积(CVD)[5]、化学气相反应[6]、等离子喷涂[7]、浸涂法[8]等。
这些方法制备的碳化硅涂层都可以有效地防止石墨材料的氧化,但是仍然存在一些问题,如:工艺复杂、成本高、抗热震性能差、涂层不致密等。此外,由于 SiC 涂层与石墨基体间热膨胀系数不匹配会导致高温过程中容易产生裂纹,这便提供了氧气进入石墨基体的通道[9,10],从而导致石墨基体的氧化。为了改善 SiC 涂层与石墨基体之间热膨胀系数不匹配的问题,应该制备具有C/SiC 过渡结构的致密 SiC 涂层,这对于改善其抗氧化及抗热震性能具有重要的实际应用价值。
本实验以 SiC、Si 和酚醛树脂为主要原料,通过浸涂和气相渗硅两步法在石墨表面制备厚度可控的SiC 抗氧化涂层。利用 XRD、SEM 研究涂层的相组成与形貌,并分析碳化硅涂层的形成机制及涂层的抗氧化、抗热震性能。
实 验
实验选用高强石墨为基体,其密度为 1.75 g/cm3,试样尺寸为 10 mm×10 mm×5 mm,试样表面用砂纸研磨并去除棱角,然后用去离子水和乙醇超声清洗、并放入 120 ℃烘箱中干燥 2 h 后备用。涂层原料主要为 SiC(纯度为 99%,d50=0.5 ?m),金属硅块(纯度为 99.4%,粒度为 5~10 mm),并采用实验室自制的酚醛树脂溶液(残碳率为 50%,质量分数)为碳源及粘结剂。
将 SiC 微粉、酚醛树脂和无水乙醇按照一定的比例混合后,经超声分散、磁力搅拌形成均匀的料浆。采用浸渍的方式在石墨试样表面形成均匀的预涂层,待其干燥后,置于 100~150 ℃烘箱中固化 1~3 h。固化后的样品放入在氮气保护的管式炉中于 900 ℃进行裂解 60 min,升温速率 5 ℃/min。裂解后的试样放入石墨坩埚中,坩埚底部放入足量的硅块,然后在真空状态下 1650 ℃保温 30 min 进行气相渗硅,使硅蒸气与碳反应生成 SiC 涂层。
恒温抗氧化性能测试在 1200 ℃的箱式电阻炉中进行,每隔 2 h 将样品从高温炉中取出并置于 25 ℃中冷却,用电子天平(感量 0.1 mg)称量氧化前后的质量,根据其质量变化来表征涂层的抗氧化性能。试样质量变化率(ΔM)与质量关系如下:
ΔM=(m2–m1)/m1×100% (1)
式中,m1、m2 分别代表涂层样品氧化前后的质量。
抗热震实验在电阻炉中进行,将炉温快速升至1000 ℃。然后放入样品,待温度稳定后保温 15 min,快速取出试样,降至室温后称量质量变化,以此循环实验。按照式(1) 计算试样热震前后的质量变化率。利用 X'Pert Pro MRD 射线衍射仪和 JSM-7001 型扫描电子显微镜测试物相组成及微观形貌。
结果与讨论
预涂层的微观结构
由图可知,预涂层表面较为平整且与石墨基体结合较好。如图 1a 所示预涂层表面存在一些微孔以及微裂纹,这是由酚醛树脂高温下裂解体积收缩所产生的,但是这些微观缺陷会有助于气相硅的浸渗过程。预涂层厚度均匀(图 1b),厚度约为 100 ?m,且主要为 SiC 颗粒,热解碳分散在 SiC 周围。
可以看出,经过气相渗硅后的涂层十分致密,表面无裂纹与孔洞出现。涂层由不同粒径的六方 SiC 及立方 SiC 组成,其中六方碳化硅是作为原料引入的,立方碳化硅为反应生成的(图 2a、2b)。
由图 2a 可以看出,六方 SiC 粒径约为30 ?m,和原料中的SiC颗粒相比尺寸增大了数十倍,这是由于高温下液相硅的存在促使了 SiC 晶粒的长大。颗粒尺寸较大的原料 SiC 与反应生成的尺寸较小的 SiC颗粒紧密相连,晶界处可见有部分硅残留(图 2a)。
从涂层的截面组织形貌(图 2c、2d)可看出,涂层的厚度约为 150 ?m,厚度均匀且与基体结合良好。图 2d 中线中间的区域为 C/SiC 混合的过渡区域,沿着涂层厚度方向至石墨基体,硅元素逐渐减少,碳含量逐渐增加,形成了良好的 C/SiC 过渡结构。
这是由于在高温下气态硅浸渗预涂层时会与酚醛树脂热解所产生的碳反应生成碳化硅,同时会有一部分硅蒸气进入到石墨基体并与之反应,生成的 SiC 过渡层附着于石墨基体,这一过渡层可增加石墨基体与涂层之间的结合力。
氧化前涂层主要由 α-SiC,β-SiC 和 Si 组成,其中硅(图 2a)是由于气相渗硅过程中残留的。氧化后涂层主要由 SiC及氧化生成的 SiO2 组成,在 1200 ℃空气条件下 SiC以及残余 Si 会与空气中的氧气反应生成 SiO2。反应式如下:
Si(s)+O2(g)→SiO2(s) (2)
SiC(s)+O2(g)→SiO2+CO(g) (3)
涂层的抗氧化及抗热震性能
由图可知,未经涂层处理的试样,1 h 之后试样质量变化率达到–100%,说明试样已被完全氧化,而具有碳化硅涂层的试样,经过 16 h 氧化后,样品增重量约为每小时 2.18 mg/cm2,说明涂层有效的保护了石墨基体。SiC 涂层的存在有效防止了氧气对石墨的侵蚀,提高了石墨在有氧环境下的使用寿命。
由图可知,碳化硅涂层在 1200 ℃氧化 16 h 后表面无裂纹与孔洞,氧化后形成了致密的表面。SiC 和 Si 的摩尔体积(12.47、12.02 cm3/mol)远小于 SiO2的摩尔体积(27.43 cm3/mol),因此,涂层中 SiC 和 Si 的氧化体积膨胀约120%,使表面变得致密[11]。高倍数下(图 5b)可以看出,大颗粒碳化硅形成了氧化层外壳,而细颗粒的碳化硅氧化后表面变得更加圆滑。在氧化过程中,涂层表面的残余硅首先被氧化成 SiO2,随后碳化硅也发生了不同程度的氧化。图 5c 为局部元素扫描分析,表面元素主要由 C、Si,O 组成。这与前边的 XRD 分析结果一致,氧化后的涂层主要由 SiC 和 SiO2 组成。
由图可知,试样在热震过程中质量变化率随热震次数的增加呈现先增大后减小的规律。这是由于在热震试验初期,涂层中 SiC 和残留 Si 的氧化使试样的质量增加,C/SiC 过渡层以及残余 Si 的存在减缓了石墨基体与涂层之间的热膨胀系数不匹配所产生的应力,减少了微裂纹的产生,同时,在高温下 SiC 和 Si 的氧化产物能愈合热震过程中产生的微裂纹[12],因此涂层保护了基体石墨的氧化;随着热震次数的增加,由于涂层中产生的微裂纹不能够自愈合而且逐渐扩大,为氧气进入并氧化石墨基体提供了通道,因此试样的质量变化率逐渐降低,循环热震15 次后试样质量变化率为–0.17%。
结 论
采用浸涂和气相硅浸渗法成功在石墨表面制备了 SiC 抗氧化涂层,涂层致密无裂纹,主要由粒径不同的 α-SiC,β-SiC 及少量残余硅组成。
涂层可有效防止石墨材料在高温条件下的氧化,1200 ℃空气条件下氧化 16 h 后试样每小时增重量约为 2.18 mg/cm2,提高了石墨在有氧环境下的使用寿命。
涂层具有良好的抗热震性能,经 1000~25 ℃循环热震 15 次后试样质量变化率仅为–0.17%。
免责声明:本网站所转载的文字、图片与视频资料版权归原创作者所有,如果涉及侵权,请第一时间联系本网删除。
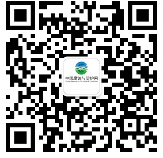
官方微信
《中国腐蚀与防护网电子期刊》征订启事
- 投稿联系:编辑部
- 电话:010-62313558-806
- 邮箱:fsfhzy666@163.com
- 中国腐蚀与防护网官方QQ群:140808414