前 言
石油炼制过程中分馏塔可以将反应后的油气混合物根据不同的馏程分馏为富气、汽油、轻柴油、重柴油、回炼油和油浆等馏分,分馏工艺常见于常减压、催化裂化和焦化等过程。分馏塔顶部循环系统是为了取走分馏塔顶部的过多热量,通过循环系统的换热量来控制顶部抽出物料的温度,从而确保分馏产品的纯度合格。分馏塔顶部循环的物料以液相状态经过换热和顶循泵加压后返回分馏塔顶部,该循环系统中的腐蚀越来越被人们所关注。
常减压是炼油工业的第一个加工装置,腐蚀问题最严重且最复杂。原油逐渐劣质化,电脱盐前的混合原油氯含量逐渐升高,电脱盐和脱水的难度逐渐增大,如果超过了电脱盐装置的设计要求,脱后原油的盐质量分数大于3μg/g,就很容易造成常压塔严重腐蚀结垢。
常减压蒸馏装置中的腐蚀介质是原油带来的,主要有氯化物、硫化物、有机酸、有机氯等。对于高硫、高盐、高酸的原油,常减压塔各部分的腐蚀主要有3种类型:常压塔顶及常一线抽出板以上低温轻油部分发生的是低温HCl-H2S-H2O型化学和电化学腐蚀;200℃以上柴油及蜡油部分则发生高温环烷酸化学腐蚀;常减压塔进料段与塔底则发生高温硫化学腐蚀和冲蚀。其中腐蚀现象最严重的是塔顶的HCl-H2S-H2O型化学和电化学腐蚀。
本研究工作针对常压分馏塔顶部循环油系统结盐腐蚀问题设计了一种在线除盐防腐工艺,并开发了与之配套的成套设备。在此工艺中,关键技术难题是如何将油品中微量腐蚀性介质从系统中去除。该技术采用微相分散-顺流萃取-油水深度分离的组合脱盐脱酸方法,通过注水洗脱油品中的腐蚀性介质并完成分离。该成套技术在国内千万吨级规模炼油厂的常减压装置中投入运行,效果良好,明显降低了分馏塔顶循系统的腐蚀速率。
1、工 艺 流 程
国内某炼油厂常减压装置常压分馏塔顶循环油的抽出量为593.96t/h,抽出温度为148℃,返塔温度113℃,采用换热后的约1/20~1/15循环油油量即30~40t/h进行除盐脱酸处理,然后再返回分馏塔顶部,以将整个顶循系统腐蚀速率维持在一个较低水平。具体工艺流程见图1,蓝色框线中为改造部分,分馏塔顶循回流油经过冷却器后,分出30~40t/h顶循回流油进入除盐成套设备,与2~4t/h净化水或电脱盐注水混合,注水在顺流径向萃取器内快速溶解顶循油中的盐,经油水分离器将溶解了盐类的废水除去后的顶循油与另一部分顶循油汇合回流返回塔顶,含油污水进入装置酸性水系统去下游污水汽提装置处理。
2、成 套 设 备 及 原 理
分馏塔顶循环油在线除盐设备主要由湍旋混合器、顺流径向萃取器和油水分离器三部分组成。技术原理如图2所示,首先通过湍旋混合器将水均匀分散到循环油中,油中的盐部分溶解到水中,然后经顺流径向萃取器深度捕获盐类离子,油水分离器利用粗粒化及波纹强化沉降,快速并高效地实现油水分离,溶水性盐溶于水中被带出,达到顶循油在线脱盐的目的。
降低顶循系统腐蚀的方案中,总是希望抽出的顶循油量和使用的水量最小,从而以最小的能耗实现这些目标,其中关键技术是使用高效的液液萃取和分离技术。顺流径向萃取技术是一种紧凑式的高效萃取方式,使用螺旋形混合元件产生高速的旋转流动,这样的流动促进了水滴的破碎,并且内部的变径结构产生多区域小尺寸涡流,强化了径向混合萃取。由于水滴产生高速自转,水滴自转表面的离子交换速度大大提高,宏观上表现出优秀的萃取能力。
纤维床油水分离使用特殊孔道的纤维层,可以有效地使分散在油中的细小水滴聚结长大,从而增加了油水两相沉降效率,在同一处理量下,纤维床可以有效地降低沉降空间,缩小油水分离设备的尺寸。液液萃取和液液分离结合点在于水滴尺寸的控制,通过计算除盐扩散速率来控制萃取后体系的水滴粒径di,根据di来设计纤维床参数。以最优化方案对分馏塔顶部循环油的无机盐、酸类物质进行高效脱除。
3、工 业 运 行 结 果 及 标 定
3.1 系统脱盐效果
该设备运行稳定后,常压分馏塔顶部循环系统总流量为594t/h,分馏塔顶循分出量为40t/h,注水量为4t/h,顶循分出量约为总循环量的1/15,注水量为顶循油分出量的10%,装置运行稳定后油水分离器界位分层清晰,切水不带油,返塔脱盐油不带水。现场开工标定持续了9d,每天取一组除盐装置进出口顶循油样进行分析,采用GB/T6532—2012电位滴定法测量进除盐装置前后顶循油中盐含量,这种方法的盐质量浓度单位为mgNaCl/L,代表了氯类离子在电解池中的电荷迁移量,具体电子迁移量如式(1)表示:Q=c/M。
(1)式中:Q为样品中含有的负电荷离子物质的浓度,mmol/L;c为测量的盐质量浓度,mg/L;M为NaCl的摩尔质量,g/mol。
图3为分馏塔顶循在线除盐设备的进出口油品中盐含量及脱盐效率曲线。由图3可以看出,设备进口顶循油盐的初始质量浓度为1.3mgNaCl/L,代表着顶循系统中的油品盐含量。每一组出口顶循油盐含量均比入口有一定下降,效率从5%至85%不等。由于设备进出口顶循油不断地在顶循系统中进行循环,因此盐含量不尽相同,每一组效率测试结果并不能代表设备每一天的脱盐效率,但从脱盐效率上来看经过设备的顶循油中盐含量均有降低,工艺路线的目的即是通过除盐设备长期运行将顶循系统中的盐类不断带出系统。
从图3可以看出,随着设备的长期运行,顶循油中盐质量浓度不断降低,在第9d时降低至0.5mgNaCl/L,虽然在盐含量较低时设备的脱盐效率略低,但通过长期运行仍可将常减压装置进料带入的盐类带出,控制顶循系统中盐含量处于较低水平,减缓了腐蚀的发生,可见除盐设备运行良好。
3.2 系统脱酸效果
图4所示为进出口顶循油中酸度测试值及脱酸效率曲线,在标定的同时进行了除盐装置进出口顶循油酸度的测量。从图4可以看出,设备投入运行初期酸度值高达40mgKOH/L,经过除盐设备洗脱后出口顶循油酸度均有降低,脱酸效率从8%至70%不等,和上述盐含量测试结果类似,每一组效率测试数据并不能代表设备长期运行的结果,但能反映设备运行对于顶循系统长期运行带来的变化趋势。
从图4可见,随着设备长期运行,顶循系统顶循油酸度不断降低,标定第9d时降低至18mgKOH/L,顶循油酸度降低是因为其中的腐蚀性介质被洗脱到净化水中了。对注入除盐设备的净化水和油水分离器水相出口切水进行了pH值的测量,分析结果如图5所示。
从图5可以看出,入口净化水平均pH值为9.57,切水的平均pH值为8.05,每一组的切水pH值均较注水pH值约下降1.5个数值,切水pH值的下降侧面反映了油品中的酸性腐蚀性介质转移到了水相中被带出了顶循系统,降低了分馏塔顶循环系统的腐蚀速率。
3.3 系统腐蚀速率标定
腐蚀探针是目前分馏塔顶循环系统长期运行的主要监测手段,该装置在顶循系统换热器入口处设置的腐蚀探针可监测整个顶循系统的腐蚀速率。一般认为控制腐蚀速率在0.2mm/a以下时则表明防腐措施使用得当,腐蚀速率在可接受范围内。
图6为该炼油厂在使用在线除盐装置前后常压塔顶循系统腐蚀速率曲线,第一次开工在5月5日,从图6中可以看出在线除盐装置投用前腐蚀速率较高,在0.2~0.6mm/a波动,装置投用后运行半个月腐蚀速率平稳控制在0.3mm/a上下波动,部分时间段低至0.2mm/a。投用半个月后出现分馏塔内腐蚀产物堵塞湍旋混合器的情况,造成在线除盐装置压力降增大、流量下降,最终停运。
停运后腐蚀速率逐渐上升至0.4mm/a。在切入过滤器进行流程优化后于9月底在线除盐装置再次投用,目前常压塔塔顶循环系统腐蚀速率稳定控制在0.2mm/a以内,处于0.1mm/a上下波动的状态,说明在线除盐装置运行效果良好,有效地将顶循系统内腐蚀性介质和盐类带出系统,缓解了塔顶腐蚀,提高装置运行的安全性和稳定性。
3.4 系统优化及建议
如3.3内容所述,分馏塔顶在线脱盐脱酸成套技术在投入运行初期,出现了湍旋混合器腐蚀产物堵塞、压力降增大、流量下降的问题。将湍旋混合器拆卸清洗时发现大量黑色堵塞物,如图7(a)所示。将堵塞物进行烘干后呈现鲜明的两种颜色,红褐色与黄色,见图7(b)。将两种颜色堵塞物分别取少量样品,黄色编号为1号,红褐色编号为2号,进行粒径分析及能谱分析。
从能谱分析结果中发现两种堵塞物主要元素都为Fe和O,分析认为主要成分为铁及铁的氧化物,剩下的主要是S元素和C元素,分析认为这两种元素分别构成FeS和环烷酸腐蚀产物,2号样品中S元素和C元素含量较1号高出许多,因此1号样品和2号样品的颜色差别也许是由于FeS和环烷酸腐蚀产物在总的堵塞物中含量差别造成的。另外1号样品中还存在少量的金属元素,比如Al,Si,Ca,Cr,它们形成的氧化物也可能造成1号和2号堵塞物的颜色差异。
将两种堵塞物分别进行了粒径分析,分析结果如图9所示,从粒径分布曲线中可以发现,两种堵塞物的粒径范围差不多,1号平均粒径比2号稍大,1号堵塞物粒径范围为0.2~50.0μm,分割粒径D50为8.5μm;2号堵塞物粒径范围为0.2~100μm,分割粒径D50为7.83μm。由于常减压装置油品中成分复杂,对在线除盐装置造成堵塞,因此在湍旋混合器前增设自动反冲洗过滤器作为分馏塔顶循环系统在线除盐工艺的预处理工序,开始依据粒径分析数据选取的过滤器精度为8μm,但在实际应用中发现腐蚀性产物颗粒被油品包裹形成团絮状,颗粒要明显大于粒径分析结果,因此选取自动反冲洗过滤器分离精度为15μm。自从设置了反冲洗过滤器后,该系统运行稳定。
4、结 束 语
常减压装置自投用在线除盐脱酸防腐成套技术后,设备运行安全平稳。在原先塔顶循环系统盐含量一直超标的情况下持续将顶循油中的酸性腐蚀性介质和盐类转移到净化水中带出系统,从标定结果来看,在线除盐设施出口顶循油相较于入口顶循油中盐含量降低,酸度降低,塔顶循环系统中盐含量逐渐降低,最终顶循油中盐含量及酸度分别稳定至1mgNaCl/L,20mgKOH/L以内,分馏塔顶循系统的在线腐蚀探针监测的腐蚀速率稳定控制在0.2mm/a以内。该成套技术设备流程简单,改造方便,投资较少,能耗低,免去了传统的注缓蚀剂、中和剂的工序以及洗塔作业产生的轻污油、污水,降低了系统因腐蚀而带来的材质升级费用,减少了装置运行成本及设备腐蚀带来的安全生产问题。
免责声明:本网站所转载的文字、图片与视频资料版权归原创作者所有,如果涉及侵权,请第一时间联系本网删除。
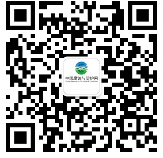
官方微信
《中国腐蚀与防护网电子期刊》征订启事
- 投稿联系:编辑部
- 电话:010-62316606-806
- 邮箱:fsfhzy666@163.com
- 中国腐蚀与防护网官方QQ群:140808414