摘要:简要分析了飞机在沿海及海岛等严酷环境下使用面临的腐蚀问题,通过列举国内外典型飞机腐蚀,阐明了环境腐蚀对飞机的危害性。简要介绍了美军飞机腐蚀防护对策与控制措施。针对我国现役飞机的严酷使用环境、腐蚀特点研究制定了外场条件下飞机腐蚀防护对策与措施,主要包括有针对性的腐蚀检查、表面清洗、除湿干燥、机载电子电气设备防护措施、易腐蚀部位涂覆缓蚀剂、动部件活动部位涂覆润滑脂、腐蚀损伤修复的原则与措施等。
关键词:飞机;严酷环境;外场;腐蚀防护;表面清洗;除湿干燥;缓蚀剂
1背景情况
飞机腐蚀与其使用环境密切相关。与内陆地区一般环境条件相比,沿海及海岛环境更为严酷,具有高温、高湿、高盐雾和高强度太阳辐照的“四高”特点, 飞机结构腐蚀速度及故障率可能会成倍增加。铝合金、高强度钢、蜂窝等结构对环境腐蚀敏感,严酷环境与疲劳载荷的共同作用会加剧疲劳损伤发生与发展,导致疲劳寿命下降。地面停放时密封较差的飞机内部结构(“死角”),渗入的腐蚀介质会长期存留,与地面环境相叠加形成恶劣的局部腐蚀环境,使得结构更容易产生严重的腐蚀问题。机载成附件、电气系统的腐蚀/老化问题会更加突出。
笔者对 2008-2013 年某系列飞机电子设备在宁夏和广东地区典型机场的故障情况进行了统计,结果表明,广东某地的机载电子设备故障率为宁夏的 1.9倍。张友兰等人[1]针对环境对机载电子设备的影响, 用 3 年时间跟踪了 6 种机型 200 多台套机载电子设备的故障情况。结果发现,在海南地区机载电子设备的故障率是内陆的 2~3 倍。同一机型的同一种导航设备,在海南的故障率是沧州的 3 倍,其中一个分机在沧州使用从未发生故障,而在海南使用的故障率为100%。
飞机腐蚀防护与控制(CPC)涉及到全寿命期的 诸多环节,包括结构选材、抗腐蚀设计与工艺、腐蚀 修理、外场使用维护、腐蚀监控等[2-22]。迄今为止, 我国现役飞机的腐蚀问题还没有得到很好解决,主要 存在三方面的问题[2-3]:设计阶段结构选材与防腐工 艺抗腐蚀性能的环境考核验证并不充分,飞机结构的 抗腐蚀品质存在“先天不足”;防腐改进及腐蚀修理有 效性验证还缺少深入研究,即使在大修中对腐蚀部位 实施了修理,但交付使用后仍然会再次发生腐蚀;外 场使用维护与腐蚀监控方面缺少有效的技术措施。现 有的飞机外场检查与使用维护规程、修理项目与措施 等有关技术文件大多是针对一般环境条件编制的。如 果将其照搬用于严酷环境下飞机,不可避免地出现严 重的腐蚀问题,从而会影响飞机结构的完整性。
笔者认为,飞机在严酷环境下使用,腐蚀很可能 会成为影响和制约其安全飞行、正常维护和经济修理 的重大问题。就现役飞机而言,研究制定外场条件下 的 CPC 对策十分必要,对于减轻腐蚀对飞机的危害, 降低故障率,避免出现重大腐蚀故障,保障飞行安全 具有重要意义。
2飞机腐蚀的危害性
2.1诱发飞机重大故障甚至导致飞行安全事故
飞机严重腐蚀问题不仅会导致重大故障,而且还会诱发重大事故,下面列举几个典型案例说明。
案例一:2002 年美国一架 F15 飞机由于尾翼结构腐蚀断裂导致空中解体;2007 年 11 月,在密苏里
州又一架服役 30 年的 F15 飞机由于腐蚀疲劳导致空中解体,全球 768 架 F15 飞机全部停飞检查,并发现一架F15 飞机机翼大梁和座舱盖骨架严重腐蚀/裂纹, 导致 472 架该型飞机再次停飞。据报道,有 180 多架F15 飞机因此而退役,损失巨大[2]。
案例二:2007 年美空军 67%的 F-22A 飞机出现结构腐蚀,其主要原因是结构材料、涂料和一些部件的材料匹配性不好。解决的方法是将原铝制构件换为钛合金构件。这不仅导致费用大幅增加,而且更换部件将增加 F-22A 飞机雷达波反射率,从而显著降低其隐身性能[3]。
案例三:2008 年 10 月和 12 月俄罗斯在赤塔地区接连发生两起米格-29 飞机坠毁事故后,俄空军对近 300 架在役的米格-29 飞机进行全面检查时发现, 30%以上的米格-29 飞机存在严重腐蚀,对飞机飞行安全构成很大隐患,因而造成了米格-29 机群 291 架飞机提前退役,而其中一些飞机飞行时间还不足 150 飞行小时,腐蚀问题是导致这些飞机退役的直接原因[3]。
案例四:我国 X1 系列飞机先后发生了多起严重的腐蚀故障。例如,2001 年该系列飞机 42 框下半框发生腐蚀断裂导致 1 架飞机报废(如图 1a 所示),幸好发现及时,未酿成严重事故。随后检查发现多架飞机存在不同程度的腐蚀问题,造成大批飞机停飞抢修。2002 年该系列飞机机翼前梁和油箱下壁板等部位又发现严重腐蚀 (如图 1b 所示),因而导致两架飞机提前返厂大修[2]。
案例五:2011 年,笔者在对 X2 型飞机检查评估时发现,机体结构及机载成附件普遍存在严重腐蚀和老化问题,已成为飞机严重的安全隐患。为切实摸清飞机腐蚀状况,抽调了一架飞机返厂进行分解检查评估。结果表明,机体结构的腐蚀问题非常突出,其中75%以上的机身、机翼、平尾、垂尾等结构部位桁条与蒙皮之间胶接点焊部位出现了严重腐蚀损伤,多处桁条腐蚀断裂;机翼后梁、平尾后梁、机身地板梁等关键结构也出现严重腐蚀,如图 2 所示[6]。
图1 X1 系列飞机结构严重腐蚀部位
图2 X2 型飞机结构的严重腐蚀情况
2.2大幅增加修理费用和使用成本
美国空军 CPC 办公室(AFCPCO)研究表明,在空军基地超过 50%的工作量与腐蚀有关。根据美国防部《CPC 计划指导手册 2007》,军用飞机寿命周期使用成本的 65%~80%与腐蚀有关。美空军每年直接用于飞机腐蚀维修费用的统计结果表明,1990 年超过 7.18亿美元,1994 年接近 8 亿美元,2002 年超过 10 亿美元,2004 年 14.97 亿美元。2009 年 AFCPCO 向国会提交的空军腐蚀成本报告,美空军腐蚀维修费用年增长率高达 5.23%[3]。
2001 年我国 X1 系列飞机因 42 框下半框发生腐蚀断裂导致 1 架报废,随后又对该系列飞机进行大规模的紧急抢修、相关的评定及试验验证等一系列工作,由此带来了重大经济损失。
3美军飞机环境腐蚀对策与措施分析
美国作为一个超级大国,奉行全球战略及霸权政策,其军用装备不可避免地必须经受全球最严酷环境的作用。就美军飞机而言,不仅总体数量多,而且机场分布广,环境条件复杂,特别是一些基地环境条件十分严酷。美军对军机环境腐蚀及环境适应性问题极为重视,先后投入了大量经费开展研究。就总体技术现状而言,美国针对飞机环境 CPC 方面的相关研究计划、技术动态、采取的配套技术措施具有先进性和代表性,值得借鉴。下面简要介绍美军在飞机 CPC 的有关情况。
3.1相关的组织机构及其职能
美军飞机的使用经验和研究结果均表明,严酷环境下使用的飞机机体结构是 CPC 的最重要对象,必须建立全寿命期内 CPC 的高效组织管理体系[4,7-8]。包括如下几个方面。
1)设计、制造和使用维护等各阶段 CPC 的组织管理机构 CPCAB--CPC 咨询委员会;CPC 指导组 (CPCGG)和 CPC 任务组(CPCTG)等,明确各级组织管理机构的职能。
2)视情修正/更新 CPC 总体技术要求/大纲等CPC 顶层指令性或指导性文件。
3)建立和完善飞机概念设计、工程设计、生产 制造和使用维护等各阶段的 CPC 技术实施程序,并针对机体各类关键结构及腐蚀损伤关键技术开展CPC 专项技术分析与试验研究。
美国国防部在检查、总结原有 CPC 技术状态及其在几个航母舰队中的实施情况的基础上,近年来又在全面、系统地开展起始于顶层的 CPC 技术的改进工作。规划并执行可有效降低腐蚀对武器装备效能影响的战略性措施,制定、实施更加有效的 CPC 总体技术目标和策略[4,8]。
3.2腐蚀防护与控制策略及相关的标准体系
美国空军为了降低飞机腐蚀总成本,提高使用性能和系统安全性,先后研究制定了与腐蚀相关的一系列标准。编制了军用飞机的 CPC 设计规范/标准、指南/要求及使用维护手册。在飞机结构抗腐蚀设计、性能评定方面,形成了系列化的设计、工艺、评价标准。在理论分析和广泛试验研究的基础上,先后制订了 CPC 标准。如《飞机结构通用规范指南 JSSG-2006》、《飞机结构完整性大纲通用指导方针 MIL-HDBK-1530B》、《航空航天武器系统 CPC 中的材料和工艺 MIL-STD-1568》、《空军武器系统中的材料与工艺要求 MIL-STD 1587》等, 已明确将飞机结构 CPC 作为一项长期战略在顶层设计、制造、修理和使用维护等阶段贯彻和执行。美国1985 年在美军标准中明确提出要考虑热、化学和气候环境对飞机结构耐久性、损伤容限分析与试验验证的影响,制定了 MIL-STD-810《环境试验方法和工程导则》, 并经过多次修改和扩充,对飞机环境试验增加了可靠性要求[3-4]。
3.3抗腐蚀设计与环境适应性分析及试验评价方法
美军从飞机设计、试验、制造、使用维护和修理的全寿命周期对腐蚀防护和环境适应性进行了深入系统的研究,并建立了一套基于飞机结构完整性大纲CPC 措施,环境适应性评价方法与对策。
美国国防部将环境对飞机影响作为 11 项国防核心技术之一重点研究,考虑单一环境因子进而考虑多 因子复合对材料(包括涂层)腐蚀影响的模型、仿真研 究。在建立大气腐蚀因子、气象因子、大气污染因子与腐蚀时间之间的数学模型和函数关系上已取得一定成果;拥有全球的、成套的立体环境数据库,根据环境因子的作用对飞机的定检日历周期提出了“基地 环境腐蚀分级法”,按气候、大气污染和地理条件评 定每个空军基地的腐蚀严重性程度对机场进行评级。并按此等级来确定或调整基地飞机的清洗、腐蚀定检 和重漆的周期[2-3]。
美国洛克希德公司对 F-18 飞机结构防护层体系的有效期在大量的试验研究基础上,制定了试验技术 要求。美国海军在 20 世纪 80 年代未进行了舰载机外场服役环境试验和结构加速腐蚀模拟试验研究,建立 了海军舰载飞机加速试验环境谱,以确定化学、热和气候等多种环境要素的影响,并形成了由典型样件、构件、组合件,直至部件构成的积木式加速腐蚀试验技术方法,综合评定飞机抗腐蚀设计细节的环境适应 性,主要包括结构选材、构型设计、结构排水设计、结构整体密封设计等,在环境/载荷条件下验证寿命评定分析结果的可靠性[2-3]。
由美国空军负责建立的麦金利气候环境试验室投资巨大,被认为是美国机械工程的里程碑。美国空 军的主要装备及相关设备都应通过麦金利试验室的环境试验考核。F/A-22 整机已通过冷冻、淋雨、暴雪、吹风、盐雾和湿热等一系列的严酷环境试验的验证。F/A-22 飞机的试验方案主要是先查阅以往其他飞机的试验记录,并考虑 F/A-22 预定的一系列特殊环境条件,根据经验制定。参与该试验的人员来自空军和 承包商的技术员、工程师、维修人员和飞行员[2-3]。
3.4新防腐技术的研发与应用研究
提高涂层的服役寿命,可减少重新涂漆次数带来 的人力、物力消耗,同时可减少停飞维修时间。美空军重视飞机新型或改进涂层技术的研发与应用,试图 追求寿命达 30 年以上的环保涂层。对预处理和底漆而言,主要集中在导电高分子、溶胶-凝胶法、等离子体聚合物、改性的金属氧化物颗粒等。面漆首选氟化多羟基化合物、改进的紫外线吸收剂或光稳定剂。涂层体系研究得较多的有:纳米复合涂层、有机/无机杂化涂层等[2]。
对军用飞机涂层而言,需要考虑抗紫外线辐照、盐雾、湿度与温度循环、应力和磨损等。新涂料必须满足军用标准规定的各项性能指标,若表现得比现有涂层 好,则通常涂在一架飞机的试验区,通过较长时间观察, 若效果良好,则可涂在多架飞机上。在经过至少 1 年的观察后,对照空军飞机涂层标准进行评定,然后确定是否接受新涂层在空军飞机上推广使用[2-3]。
3.5外场使用维护中的腐蚀防护与控制措施
美军非常重视军用飞机外场 CPC,根据不同的机型制定了有针对性的检查维护措施,明确了飞机结构 部位及各系统的腐蚀检查内容、方法及周期,制定了 以表面清洗、除湿干燥、腐蚀防护、腐蚀修理等技术 措施为核心的 CPC 技术体系[6-21],并研发出了配套的清洗剂,水置换型的硬模和软膜缓蚀剂(如 AV-15, ACF-50 等),铝合金和钢制零部件去腐蚀产物膏及对应的技术标准,如 MIL-DTL-85054D(AS),MIL-PRF-81309F 等。美军飞机外场维护中 CPC 的主要措施归纳如下。
1)使用缓蚀剂进行表面防护提高飞机结构及元 器件的抗环境腐蚀品质。美军飞机普遍使用缓蚀剂, 达到了提高飞机结构的抗腐蚀品质的效果。其中应用 较为普遍的缓蚀剂均是水置换型,这类缓蚀剂具有良 好的渗透性和水置换性,能迅速脱除金属表面和结构 缝隙中的水分,同时沉积上一层保护膜,有效延缓金 属材料的腐蚀[16-19,22]。美海军针对飞机结构连接部位在结构设计时除充分考虑密封、排水外,在日常维护中使用水置换型缓蚀剂作为控制腐蚀的一种方法已使用 多年。例如,航母使用的 ES-3A 型反潜机、大西洋舰队和太平洋舰队服役的 S-3B 型反潜机使用 ACF-50 型缓蚀剂后,飞机腐蚀速率大幅度降低[16-19]。美军缓蚀剂应用表明,外场维护采用缓蚀剂,可明显降低费用、缩短工时、减轻劳动强度。
2)制定严格的定期检查和清洗措施。定期检查和清洗是飞机日常维护中的一项主要内容[11-15],并规定清洗前要密封所有开口包括门、口盖等,防止清洗液进入飞机内部,用胶带纸覆盖通气孔等;清洗后在接头、关节处注油嘴添加润滑剂;对于易腐蚀区域喷涂缓蚀剂。例如:C-130 运输机的清洗,襟翼、起落架每 2 周 1 次,机身每月 1 次;H-25 直升机机身外表面的清洗,每周 1 次。
3)除湿干燥是美军飞机使用维护的一项重要措 施。美军在飞机使用维护保养中,对飞机除湿干燥高 度重视[6-7,11-12]。根据美军的经验除湿干燥措施有三 方面的突出优点:除湿干燥设备操作简便,适用于机 库内和外场条件下使用,可在 5 min 内连接或移除, 无需增加机务人员太多的工作量;除湿干燥效果明显,可在 1 h 内将相对湿度降到 40%以下,从而可明显改善飞机进气道、设备舱、座舱等部位的环境条件, 大幅度降低结构发生腐蚀和诱发电子电气设备故障的概率;可提高飞机完好率 20%,可减少电子电气设备 24%的故障率和 15%的维护费用。
3.6电子设备腐蚀防护与控制措施
美国对机载航空电子设备的 CPC 技术同样予以重视[4,8,11]。通过制订专用标准对航空电子元件和组件CPC 设计进行了明确的规定,对电子元件的材料选择、金属镀覆层的选择、各种连接方法的选择、电路连接和接地以及密封[19]等进行了详细的研究,并研发了相应的产品。美军针对机载航空电子设备所采取的CPC 措施主要有如下三方面:
1)为防止舰载机电连接器插头、插座的腐蚀, 电连接器表面喷涂 MIL-C-81309 电气专用缓蚀剂,线缆与插头插座连接部位采用 Avdec SLG 密封剂/Av-DEC 自平绿色密封剂(HT3326-5-50)和 Avdec 惰性聚氨酯胶带进行加强防护。电连接器与飞机结构接触表面采用导电密封胶垫进行密封,对于易于维修区域的区域门采用热缩工艺进行防护。
2)天线安装部位采用 Av-DEC 导电聚氨酯密封垫或聚氨酯密封剂进行防护。
3)做好设计中的材料选择、设计配置来减少腐蚀/湿气、设备密封技术、电连接器和印刷电路板的装配、排水孔和积水洼、冷却系统、电搭接和接地、设备清洗要求等(美国 NAVMAT P4855-2)。
4严酷环境下我国飞机外场腐蚀防护策略与控制措施
4.1总体思路
严酷环境下我国现役飞机 CPC 需要破解大量的关键技术难题,然而国内以往并没有针对严酷环境下 使用的飞机的腐蚀问题开展有针对性的系统研究[11], 技术基础薄弱。本着轻重缓急的原则,需要在现有相 关研究的基础上,针对严酷环境的腐蚀特点,优先开 展现役飞机结构防腐体系梳理、外场腐蚀检查与腐蚀 预防、腐蚀修理与防腐改进等研究,其总体思路归纳 如图 3 所示。
图 3严酷环境下飞机腐蚀防护策略与控制措施总体框图
4.2主要对策措施
4.2.1针对性的外场腐蚀检查措施
以具体机型为对象,收集整理飞机在使用和大修中发现的腐蚀问题,对飞机的防雨、防潮、防腐蚀设计与工艺措施进行分类梳理,分析判别飞机腐蚀部位、腐蚀程度及腐蚀原因,进而确定易腐蚀部位、易受环境影响的机载附件和系统、腐蚀关键件 (部位)等,在此基础上制定有针对性的外场腐蚀检查措施,明确检查内容、重点部位、方法、周期及要求等[11-12]。
4.2.2清洗
清洗是一种简单、有效的外场腐蚀防护措施,能有效地去除不断在飞机表面上沉积的腐蚀性介质,以保持飞机表面洁净,减少腐蚀产生的外在因素,从而起到抑制或减缓腐蚀的作用[13-15]。
可选用水基清洗剂(AHC-7,TFQX-1)和溶剂型清洗剂(RJ-1,TFQX-3)对飞机进行日常清洗,以减少因盐雾造成的腐蚀。对于飞机外表面首先采用水基清洗剂进行定期清洗、擦干后,采用除湿设备吹风干燥处理。对于内部可达部位、半封闭结构可达部位、设备舱、起落架舱、进气道等不宜进行大面积清洗的局部位置,采用溶剂型清洗剂清洗。先用小毛刷轻轻刷洗或用绢布沾少许清洗剂擦洗、晾干,然后采用除湿设备吹风干燥处理。
4.2.3干燥除湿
雨水疏漏和潮湿空气是导致飞机结构腐蚀、机载 设备工作不正常以及各系统故障率高的主要因素。国 内外大量研究表明,在相对湿度低于 60%的环境下, 绝大多数金属结构材料基本上不发生腐蚀,电子元器 件的故障率很低;而相对湿度大于 80%的金属结构材料的腐蚀速度会显著加快,电子元器件的故障率会明 显上升[2-3,6,11]。因此,需要特别强调的是,除湿干燥是严酷环境下飞机预防性措施的一项重要措施,对减 少飞机结构腐蚀、机载设备故障率,提高飞机完好率 具有重要作用。
对座舱、设备舱、起落架舱、外翼内腔、进气道等部位,可采用空调车或其他除湿干燥设备进行除湿 干燥处理。除湿时应将过滤净化处理后的干燥空气, 通过送风管对准水分和潮湿空气容易渗入的缝隙和“死角”进行持续吹风。需要注意的是,吹风干燥过程 中应将温湿度表的湿度传感器放置吹风部位,待相对 湿度下降至 60%以下时方可停止干燥除湿。
4.2.4电子电气设备防护
若检查中发现,电子电气设备及电缆插头、插针、插座、电缆接头出现老化、损坏等失效现象,要及时采取如下补救修复措施[4,8]:对电缆插头、插针、插座、接头芯部等选用 DJB-823 固体薄膜保护剂进行修复处理;对电子电气设备的壳体,电缆、导线及插头、插针连接部位外部可采用 TFHS-20 湿膜润滑缓蚀剂进行修复处理。
4.2.5连接部位涂覆缓蚀剂
对于不经常拆卸部位的螺栓、铆钉、结构缝隙等连接部位清洗干燥后涂覆硬膜缓蚀剂;对于可拆卸的活动部位的螺母、螺纹、锁销、销轴等涂覆软膜缓蚀剂进行保养。
4.2.6动部件活动部位涂覆润滑脂
对液压作动筒、活塞杆、轴承、转轴、伸缩拉杆、起落架支柱等动部件活动部位,按飞机维护规程规定 涂覆润滑脂。
4.2.7金属导管、支架、卡箍、夹板、保险丝等零部件
若发现可达部位的金属导管、支架、卡箍、夹板、保险丝等零部件出现腐蚀现象时,先去除腐蚀后涂覆 软膜缓蚀剂或硬模缓蚀剂。
4.2.8密封材料的及时补充
填充于机体结构中诸多大小不等、形状各异的窗口或口盖、沟、槽以及所有间隙和连接缝隙处的密封剂、密封带等,能够阻止雨水等腐蚀介质的进入,有效地抑制和减缓腐蚀。检查中若发现密封材料老化失效或缺损,要及时进行更换和填充。
4.2.9特殊部位清洁保养
对于油箱区等容易污损的特殊部位,用溶剂型清洗剂清洗去除微生物沉积物后,采用除湿设备吹风干燥处理。对于座舱盖有机玻璃透明件,应按飞机维护规程规定进行保养。
4.3腐蚀损伤外场修复措施
4.3.1基本原则和要求
通过适时的检查确认腐蚀损伤后,必须采取临时防护和有效的补救性措施对腐蚀损伤部位实施维护和修理,需遵循以下基本原则[6,11]。
1)涂覆硬膜缓蚀剂和软膜缓蚀剂可作为飞机外场临时维护和修补的有效手段。
2)软膜缓蚀剂常用在飞机清洗后,适用于螺母 、螺纹、锁销、销轴等可拆卸活动部件短期防护。
3)硬膜缓蚀剂适用于飞机上不拆卸部位如起落 架舱、减速板等,以及紧固件、接缝、调整片、焊缝、裸露的金属等表面涂覆,可作为涂层破坏后的临时修 补手段,涂覆在涂层破损、脱落部位。
4)外场腐蚀损伤修复的具体要求是,腐蚀修复后应不破坏原结构的可检性,要保持机体内外表面洁净和防护涂层完好、确保结构中不残留腐蚀产物,腐蚀损伤修复时不应引起二次腐蚀。
5)当检查确认腐蚀损伤程度(深度、面积)超出 修理容限,或者对飞行安全构成潜在威胁时,应按照相关程序上报进行专题研究解决。
4.3.2针对性的腐蚀损伤修复措施
1)结构钢或不锈钢零件发生腐蚀时,使用 BT-2G钢去腐蚀产物膏进行腐蚀产物的去除并在零件表面形成磷化膜,再喷涂底漆,最后涂覆硬膜缓 蚀剂或软膜缓蚀剂[4,19]。
2)铝合金零件发生腐蚀时,先使用 ALT-1 铝合金去腐蚀产物膏去除腐蚀产物,再使用 LYG-2 铝合金局部化学氧化膏在零件表面形成氧化膜,然后喷涂底漆,最后涂覆硬膜缓蚀剂[4,19]。
3)铜及铜合金零件发生腐蚀时,打磨去除腐蚀产物后喷涂底漆,最后涂覆硬膜缓蚀剂。
4)钛合金零件发生腐蚀时,采用打磨方法去除腐蚀产物,然后喷涂底漆,最后涂覆硬膜缓蚀剂。
5)飞机漆层起泡、开裂、剥落时应修补脱落漆层。先打磨去除漆层失效部位,再采用溶剂型清洗剂清洗,待表面晾干后涂刷配套的底漆和面漆,最后涂覆硬膜缓蚀剂或软膜缓蚀剂[4,6,11,19]。
6)飞机镀层失效时,采用溶剂型清洗剂清洗, 待表面晾干后涂覆硬膜缓蚀剂或软膜缓蚀剂[19]。
参考文献:
[1]张友兰, 李树华。 海洋环境条件对机载电子设备的影响[C]// 中国电子学会电子产品防护技术 1998 研讨会论文集。 庐山, 1998.
[2]陈群志。 典型飞机结构日历寿命评定方法与延寿技术研究[R]. 沈阳: 中国科学院金属研究所, 2005.
[3]陈群志, 康献海, 刘健光, 等。 军用飞机腐蚀防护与日历寿命研究[J]. 中国表面工程, 2010, 23(4): 1-6.
[4]孙志华, 汤智慧, 李斌。 海洋环境下飞机的全面腐蚀控制[J]. 装备环境工程, 2014, 11(6): 35-39.
[5]张栋。飞机结构的腐蚀和腐蚀控制[M]. 北京:国防工业出版社, 1993: 10-85
[6]黄昌龙, 万小朋。 老龄飞机面临的问题及解决思路[J]. 航空维修与工程, 2009(4): 40-42
[7]陈群志, 王逾涯, 崔常京, 等。 老龄飞机结构的腐蚀问题与对策[J]. 装备环境工程, 2014, 11(6): 1-9.
[8]刘世兴, 杜洪增, 白杰。 老龄飞机腐蚀问题研究[J]. 中国民航大学学报, 2004, 22(S1): 72-76
[9]张晓云, 李斌, 汤智慧。 清洗剂和缓蚀剂在飞机维护中的应用[J]. 化学清洗, 1999, 15(3): 27-29.
[10]汪定江, 潘庆军, 夏成宝。 军用飞机的腐蚀与防护[M]. 北京: 航空工业出版社, 2006.
[11]陈群志, 房振乾, 康献海。 军用飞机外场腐蚀防护方法研究[J]. 装备环境工程, 2011, 8(2): 72-76.
[12]曹宏涛, 李雪亭。 基于海洋环境的紧固件腐蚀防护要求及技术措施[J]. 表面技术, 2013, 42(1): 105-108.
[13]BIN L, ZHANG X, ZUO X, et al. Application Research on AHC- 1 and AHC-5 Water-based Cleaning Compounds for Aircraft Surface[J]. Cleaning World, 2007, 23(1): 4-10.
[14]陈跃良, 王安东, 卞贵学, 等。 海军某型飞机表面清洗技术[J]. 清洗世界, 2014, 30(4): 1-6.
[15]李斌。 飞机系列清洗剂概述及技术要求综合分析[J]. 清洗世界, 2009, 25(2): 24-28.
[16]李斌, 师华, 张晓云, 等。 YTF-1 飞机硬膜脱水防锈剂理化性能和使用性能研究[J]. 材料工程, 2009(8): 26- 29.
[17]阚伟海, 陈莉荣, 姜庆宏, 等。 复合缓蚀剂对碳钢腐蚀率的影响研究[J]. 表面技术, 2015, 44(4): 127-131.
[18]黄昌龙。 飞机腐蚀与防腐剂的使用[J]. 航空工程与维修, 2001 (1): 35-36.
[19]姜国杰,杨勇进,王强,等。 YTF-3 硬膜缓蚀剂应用研究[J].装备环境工程, 2016, 13(1): 19-23.
[20]陈群志, 杨蕊琴, 房振乾, 等。 胶体密封防水新技术在典型飞机结构中的验证[C]// 第六届全国腐蚀大会论文集。 银川, 2011: 69-73.
[21]CHEN Qun-zhi, FANG Zhen-qian, CUI Chang-jing, et al. Research on Aircraft Corrosion and Protection[C]// Catic Mro Formu 2011 Proceedings. 2011: 49-63.
[22]阚伟海, 陈莉荣, 姜庆宏, 等。 复合缓蚀剂对碳钢腐蚀率的影响研究[J]. 表面技术, 2015, 44(4): 127-131.
免责声明:本网站所转载的文字、图片与视频资料版权归原创作者所有,如果涉及侵权,请第一时间联系本网删除。
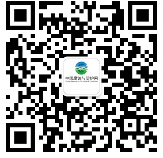
官方微信
《中国腐蚀与防护网电子期刊》征订启事
- 投稿联系:编辑部
- 电话:010-62316606-806
- 邮箱:fsfhzy666@163.com
- 中国腐蚀与防护网官方QQ群:140808414