近年来随着原油中硫、有机酸及各种重金属含量的增加,延迟焦化装置设备、管线腐蚀问题日益严重。加热炉作为延迟焦化装置的核心设备,其防腐问题也成为企业关注的焦点。
本文通过对延迟焦化装置存在的高温硫腐蚀和氧化腐蚀等反应机理进行分析,并结合延迟焦化装置的原料性质和主要操作参数,提出延迟焦化装置加热炉防腐问题的对策。供企业参考借鉴。
01 腐蚀原因
1 加热炉炉管高温氧化、硫化腐蚀
加热炉是焦化装置的核心设备,其发生腐蚀的主要形态为高温硫腐蚀。炉管材质为Cr9Mo,入口温度为285~310℃,出口温度为490~496℃,入口压力3.25MPa,出口压力0.10MPa。由于加热炉燃气(油)中含有微量的杂质硫及硫化氢,加热炉炉管将受到高温氧化、高温硫化腐蚀两个不同方式的腐蚀。
硫含量:硫含量越高,腐蚀越重。金属表面很难形成连续、完整的硫化物保护层,此时的硫化腐蚀受金属与环境界面化学反应所控制,高温硫化腐蚀速度与含硫量呈直线关系,几乎不存在临界硫含量。
氧含量:氧含量越高,氧化腐蚀越重,但氧含量超过一定的值后,氧化速度渐趋稳定。
2 加热炉炉管损坏形式
1、炉管鼓包、开裂失效
在热强度较高的部位,由于氧化腐蚀、硫化腐蚀及渗碳腐蚀的共同腐蚀作用下,炉管壁厚减薄而造成炉管鼓包,甚至开裂。
2、炉管壁厚减薄严重失效
因炉管严重结焦,导致管壁温度偏高,加速了氧化及腐蚀,使炉管壁厚减薄严重而失效。
02 对策
1 控制原料盐含量
为了降低延迟焦化装置原料中的盐含量,车间根据生产实际情况,与相关部门协调,加强对原料盐含量的监控,加强原油“一脱三注”的工艺管理,严格控制减压渣油中的硫含量、盐含量在车间要求的指标范围之内。
2 设备选材
材料的选择关乎装置能否长周期的运行,对延迟焦化装置而言,需将不耐硫腐蚀的碳钢材质更换为ASTM A335 P9或更高的新型材料,以减轻因腐蚀对设备的伤害。
3 防腐措施
严格工艺操作,禁止设备超温超压,尽量减少波动。
延迟焦化装置高温重油部位以材质防腐为主,低温轻油部位则要依靠选材、工艺防腐措施以及其他手段联合进行防腐控制。
总之,延迟焦化装置在加工处理高硫稠油时,所使用的管线、设备应选取防腐性较高的材质为宜。同时日常工作中应加强加热炉、各设备及管线防腐的管理和监控,将企业各项防腐制度落到生产实处,确保各项防腐措施工作有效的开展。
免责声明:本网站所转载的文字、图片与视频资料版权归原创作者所有,如果涉及侵权,请第一时间联系本网删除。
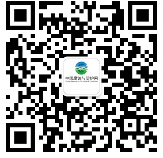
官方微信
《中国腐蚀与防护网电子期刊》征订启事
- 投稿联系:编辑部
- 电话:010-62316606-806
- 邮箱:fsfhzy666@163.com
- 中国腐蚀与防护网官方QQ群:140808414