摘要
系统总结了碳钢的CO2腐蚀产物膜研究进展,重点介绍了CO2腐蚀产物膜的结构、化学组成、生长过程、电化学性质及力学性质。展望了对碳钢的CO2腐蚀产物膜研究发展趋势和重点。
关键词: CO2腐蚀产物膜; 生长过程; 电化学性质; 力学性质
目前大部分油田进入了注水开采的中后期,相继出现了进一步提高原油采收率的问题,而大气中过多的CO2会引起温室效应,带来严重的环境和经济问题[1,2,3]。为了解决上述问题,开展了CO2驱油提高采收率 (CO2-EOR) 技术的研发和工程应用。CO2-EOR技术可明显提高原油采收率,但CO2造成的腐蚀也不容忽视,在pH值相同的情况下碳酸的总酸度比盐酸还高,对油井管材与地面集输系统具有比盐酸更强的腐蚀性[4,5]。CO2对金属的腐蚀一般可分:均匀腐蚀、局部腐蚀和点蚀[6,7]。普遍观点认为[8,9,10,11]:CO2溶解于水中形成H2CO3,溶液中的H2CO3与Fe反应而导致腐蚀。
文献[6,12,13]通过研究腐蚀介质组成、腐蚀环境变化和金属材质来探讨CO2的均匀腐蚀规律和机理,得到了一些行业内一致认可的结论。例如:温度通过影响腐蚀产物膜的致密程度来影响腐蚀速率;腐蚀介质的流速通过冲刷作用影响腐蚀产物膜的形态来影响腐蚀速率;CO2分压通过影响腐蚀介质的pH来影响腐蚀速率。CO2局部腐蚀主要是由腐蚀产物膜上的缺陷所引起,但具体机理未达成一致认识。Ikeda等[14]认为CO2局部腐蚀是由于腐蚀产物膜在生成过程中存在缺陷,腐蚀介质穿过缺陷与基体反应所导致。Schmitt[15]则认为腐蚀产物膜的破坏是由流体流动引起的。Xia等[16]和Klesenfeld等[17,18]研究碳钢在含CO2的溶液中的腐蚀行为时都发现了点蚀,他们认为由于碳钢表面覆盖了FeCO3区域与处于裸露状态区域之间构成了电偶腐蚀而引起碳钢表面发生点蚀。因此,腐蚀产物膜是影响碳钢CO2腐蚀的关键因素,需对CO2腐蚀产物膜的结构、组成、生长过程和电化学性质进行深入了解。
1 CO2腐蚀产物膜结构与组成
对于碳钢的CO2腐蚀产物膜结构及组成的研究较多[19,20,21,22,23,24],CO2腐蚀产物膜的主要组分为FeCO3,其他组分因腐蚀介质和基体的组成不同会有所差异,在含Ca2+的腐蚀介质中腐蚀产物主要组成为CaCO3和FeCO3的混合物[24,25]。腐蚀产物膜的结构与腐蚀环境有关系,但目前未形成明确的结论。一般认为CO2腐蚀产物膜由内层膜和外层膜组成,内层膜的组成为FeCO3,外层膜的组成为FeCO3或FeC3以及二者混合物,内层膜对基体的防护效果更好。但Palacios等[19]认为腐蚀产物膜有三层,中间层膜具有保护作用,中间层膜破损后容易发生局部腐蚀。赵国仙等[20]同样认为腐蚀产物膜由三层组成,但三层膜之间有物质交换通道,对基体无保护作用。Sun等[21]观察了P110钢在温度为76 ℃、CO2分压为10.2 MPa、流速为1 m/s、不同原油含水率条件下腐蚀480 h后的腐蚀产物膜横截面。含水率为30%的条件下,腐蚀产物膜为单层膜 (图1a),腐蚀产物膜薄且少;含水率为75%的条件下,腐蚀产物膜为双层膜 (图1b),内层膜致密,外层膜少且不完整。在该条件下也观察到了三层腐蚀产物膜 (图1c),内层膜厚且致密、中间膜疏松、外层膜薄且不完整;含水率为50%的条件下,腐蚀产物膜有缺陷 (图1d),在缺陷处出现了点蚀。在相同的腐蚀条件下,出现不同结构的腐蚀产物膜,故腐蚀产物膜的结构可能与钢材表面微观性质有关。Wu等[22]研究了N80碳钢在CO2分压为0.5 MPa、温度为80 ℃、流速为1 m/s模拟地层水中浸泡72 h后的表面性质,研究表明,腐蚀产物膜的内层膜和外层膜的主要成分都是FeCO3,但在内层膜中发现了MnCO3,在外层膜中发现了α-FeOOH。Liu等[23]对X70碳钢表面CO2腐蚀产物膜进行了研究,同样发现腐蚀产物膜为两层,外层膜疏松,内层膜致密。Jiang等[24]研究Ca2+对N80碳钢的CO2腐蚀影响时发现不同腐蚀时期的腐蚀产物膜均为单层不完整的膜,腐蚀产物膜下有点蚀发生。Bai等[25]研究了不同CO2分压下30%原油/盐水体系对J55碳钢的腐蚀,研究发现CO2分压影响腐蚀产物膜的形态,腐蚀产物均为CaCO3和FeCO3的混合物。pCO2=0.5~1.5 MPa时J55碳钢表面产生分散腐蚀产物,pCO2=1.5~5.0 MPa时逐渐产生保护性腐蚀产物,pCO2=5.0~9.0 MPa时保护性腐蚀产物溶解,pCO2=9.0~15.0 MPa时再次产生保护性腐蚀产物。
图1 不同结构的腐蚀产物膜[21]
含Cr钢材的CO2腐蚀产物中一般都有FeCO3、Cr(OH)3和Cr2O3[26,27,28,29,30]。孙建波等[26]研究不同含Cr量的X65管线钢的CO2腐蚀产物膜的特征,结果表明,不同含Cr量的X65管线钢的腐蚀产物膜均为三层膜结构,且化学组成相同,外层和内层为FeCO3,中间层为FeCO3和Cr(OH)3。Bai等[27]研究4Cr钢和N80碳钢在CO2分压为1 MPa、温度为78 ℃、流速为1.2 m/s的条件下的腐蚀行为,N80钢表面的腐蚀产物为FeCO3,4Cr钢表面的腐蚀产物为FeCO3、Cr7C3和Cr2O3。
2 CO2腐蚀产物膜的生长过程
关于碳钢CO2腐蚀产物膜形成和生长过程也有不同的观点。Wei等[31]对比研究了X70钢在超临界CO2 (SC-CO2) 和低CO2分压条件下腐蚀产物膜的生成过程。研究发现在SC-CO2和低CO2分压条件下X70的腐蚀机理相同,但腐蚀产物膜的形成过程却截然不同。在SC-CO2条件下,碳钢表面优先形成非晶态层,逐渐演化为致密内FeCO3层,最终在该内层上方形成相对多孔的外FeCO3层。相比之下,在低CO2分压条件下,先形成致密的外FeCO3层,然后形成多孔但较厚的内层膜。且在低CO2分压下形成的外层膜比在SC-CO2下形成的外层膜具有更好的防护性能,而在SC-CO2下形成的内层膜比低CO2分压下形成的内层膜具有更好的防护性能。内层膜对基体起着主要的保护作用,特别是在SC-CO2条件下。而程远鹏[32]则认为:腐蚀产物膜由内层膜、中间膜和外层膜构成。腐蚀反应初始阶段,介质中的阴离子与基体直接反应生成被称作初生产物膜的FeCO3,同时由腐蚀生成的Fe2+与溶液中的CO32-反应生成被称为次生产物膜的FeCO3。在腐蚀初始时期,碳钢表面首先出现由初生膜和次生膜构成的中间产物层,然后溶液中的腐蚀性离子透过中间产物层与基体发生反应生成FeCO3内层膜。内层膜足够厚、防护能力足够强的时候,阳极生成的Fe2+穿过内层膜和中间膜后与CO32-生成的次生FeCO3膜在中间膜外沉积,最终形成外层膜。
Wei等[31,33]在CO2分压为9 MPa、温度为80 ℃条件下分别研究了P110钢和X70钢在3.5% (质量分数) NaCl中的腐蚀产物膜结构随浸泡时间的变化。P110钢表面在浸泡0.5 h后出现较为完整的薄腐蚀产物膜 (图2a),随后腐蚀产物膜变厚 (图2b),浸泡时间继续延长,腐蚀产物膜继续增厚,但也出现了缺陷 (图2c),浸泡12 h后缺陷增大 (图2d)。浸泡12 h后X70钢表面出现有孔洞、疏松的腐蚀产物膜 (图3a),与P110钢类似。随着浸泡时间的延长,X70钢表面腐蚀产物填充了孔洞,使得腐蚀产物膜变得密实 (图3b和c),浸泡时间继续延长,出现了单层腐蚀产物膜 (图3d),最终形成外层膜薄且少、内层膜厚且密实的双层腐蚀产物膜 (图3e和f)。说明在X70钢表面首先形成了内层腐蚀产物膜,然后再形成外层腐蚀产物膜。
图2 不同浸泡时间下P110钢的腐蚀产物膜形态[33]
图3 不同浸泡时间下X70钢的腐蚀产物膜形态[31]
3 CO2腐蚀产物膜的电化学性质
腐蚀产物膜的电化学行为研究是CO2腐蚀机理研究的必要过程。腐蚀产物膜的结构不同,电化学行为也必然不同。目前,主要的测试手段是电化学阻抗法 (EIS),即首先测定腐蚀产物膜的电化学阻抗谱,然后拟合等效电路。由于CO2高温高压原位电化学测试系统十分复杂,受实验设备限制,一般都采用常压离位测量,即在高温高压条件下生成腐蚀产物膜,然后在常压条件下进行电化学测试[34,35]。Tan等[36]和赵大伟[37]都采用该方法进行了腐蚀产物膜电化学性质的研究。陈长风等[35,38,39,40,41,42]采用该方法对CO2腐蚀产物膜的电化学性质做了大量的研究,研究材质包括J55碳钢、N80碳钢和多种低Cr钢,主要通过阻抗谱的形状来分析腐蚀产物膜的电化学性质,并从理论上推导了不同腐蚀产物膜覆盖度与阻抗谱形状的关系。然而,研究中并没有明确腐蚀产物膜生长过程和结构对腐蚀电化学的影响。
Wei等[33]研究X70钢在CO2压力为9 MPa、温度为80 ℃条件下3.5%NaCl中的腐蚀产物膜性质时,通过EIS测试数据拟合出不同产物膜下的等效电路,见图4。图中Rs为溶液电阻;Qi为恒相元件 (CPE) (24和50 h时,i=1;168 h时,i=2;1-内层膜,2-外层膜),用于表示腐蚀产物膜i的电容;Ri为腐蚀产物膜数i的电阻;Qdl为双电荷层电容的CPE;Rt为电荷转移电阻,代表碳钢基体溶解。R1、R2和Rt都随着浸泡时间的增加而增大,说明腐蚀产物膜对基体的保护性增强。由此可见在X70表面腐蚀产物膜是由内向外逐渐形成。
图4 不同类型腐蚀产物膜的腐蚀等效电路图[42]
Farelas等[43]研究了C1018碳钢在总压为0.1 MPa、CO2分压为0.054 MPa、流速为0.5 m/s的条件下浸泡在温度为80 ℃的3% (质量分数) NaCl溶液的电化学行为,不同浸泡时间下的腐蚀产物膜状态和腐蚀等效电路图见图5。暴露在CO2环境中C1018碳钢的溶解过程演变分为3个不同的阶段。初始阶段,铁素体的选择性溶解使渗碳体结构保持完整,腐蚀速率有所增加;随即渗碳体引起了电偶联效应,增加了阴极反应的可用性,并形成了较厚的多孔层;最终在碳化铁层的孔隙内形成一层FeCO3保护层,显著降低了腐蚀速率。表明了腐蚀产物膜是由外向内逐渐形成。
图5 不同浸泡时间下腐蚀产物膜状态和腐蚀等效电路图[43]
Zhang等[44]研究了N80碳钢暴露在CO2分压为8 MPa、流速为2 m/s的地层水中的腐蚀过程,见图6。在碳钢腐蚀初期,铁素体优先溶解,Fe3C保留在阴极。随着腐蚀的进行,更多的Fe3C积聚在碳钢阴极表面。残留的Fe3C松散、呈网状,并且对基体起不了保护作用,并作为阴极相加速碳钢的腐蚀。
图6 不同腐蚀时期的腐蚀等效电路图[44]
关于腐蚀产物膜结构和电化学行为的研究主要集中在CO2/盐水体系的腐蚀,且水溶液大都还是组成比较简单NaCl水溶液,与油田现场工况下油气水多相混合流体性质相差甚远。关于含原油条件下的CO2腐蚀产物膜的结构和生长过程的研究已有涉及,但文献数量很少。关于原油对CO2腐蚀产物膜的结构和电化学行为影响的研究还较为缺乏。
4 CO2腐蚀产物膜的力学性质
CO2腐蚀产物膜的力学性质和在基体上的附着情况影响着腐蚀产物膜对基体的保护作用,国内外对此研究较少。陈长风等[45]研究了N80油套管钢CO2腐蚀产物膜的力学性能,结果表明,腐蚀产物膜的弹性模量与硬度从内层到外层逐渐降低,内层膜与基体的粘附力要明显高于外层膜与内层膜之间的粘附力,腐蚀产物膜内应力可以导致外层膜破裂。任呈强等[46]研究了CO2分压、温度和缓蚀剂等因素对N80钢腐蚀产物膜的硬度和膜基结合强度的影响,并建立了腐蚀产物膜硬度、膜基结合强度与平均腐蚀速率间的定量关系。俞芳等[47]研究发现温度影响腐蚀产物膜的硬度和弹出模量,随着温度的升高,腐蚀产物膜的硬度和弹性模量都先降低后升高,在90 ℃时出现最低值。高克玮等[48]研究了流动状态下X65管线钢CO2腐蚀产物膜结构和力学性能,流动对膜的硬度以及杨氏模量影响不大,随着流速的增大腐蚀产物膜的断裂韧性先下降后上升。总体来说,碳钢的CO2内层腐蚀产物膜的硬度和粘附力较强,对基体起主要的保护作用。
5 总结与展望
随着CO2-EOR应用的规模逐年增大,CO2腐蚀造成井筒、集输管线失效的案例也在增加,CO2对油田管线的腐蚀问题已引起高度重视。研究和解决CO2腐蚀问题对碳捕获和碳埋存及油田安全运行具有重大意义。目前国内外对CO2腐蚀产物膜开展了大量的研究,但CO2-EOR和含CO2原油集输的腐蚀环境十分复杂,目前的研究体系较为简单,腐蚀时间较短。
未来对CO2腐蚀产物膜的研究应重点从以下几个方面考虑:(1) 模拟油田现场实际腐蚀环境,研究CO2/原油/采出水体系的腐蚀行为和腐蚀产物膜;(2) 研究碳钢在含CO2环境中长期服役和运行条件下腐蚀产物膜的组成、结构、电化学性质和力学性质,明确体系因素对腐蚀产物膜性质的影响机制;(3) 进一步改进和完善高温高压复杂体系条件下CO2腐蚀电化学原位测试系统,原位研究腐蚀产物膜生长过程中电化学性质。
参考文献
[1] Kuramochi T, Ramírez A, Turkenburg W, et al. Effect of CO2 capture on the emissions of air pollutants from industrial processes [J]. Int. J. Greenh. Gas Con., 2012, 10: 310
doi: 10.1016/j.ijggc.2012.05.022
[2] Zeng R S, Vincent C J, Tian X Y, et al. New potential carbon emission reduction enterprises in China: Deep geological storage of CO2 emitted through industrial usage of coal in China [J]. Greenh. Gases: Sci. Technol., 2013, 3: 106
doi: 10.1002/ghg.1314
[3] Luhar A K, Etheridge D M, Leuning R, et al. Locating and quantifying greenhouse gas emissions at a geological CO2 storage site using atmospheric modeling and measurements [J]. J. Geophys. Res.: Atmos., 2014, 119: 10959
doi: 10.1002/2014JD021880
[4] Pfennig A, Linke B, Kranzmann A. Corrosion behaviour of pipe steels exposed for 2 years to CO2-saturated saline aquifer environment similar to the CCS-site Ketzin, Germany [J]. Energy Procedia, 2011, 4: 5122
doi: 10.1016/j.egypro.2011.02.488
[5] Zhang G A, Cheng Y F. Localized corrosion of carbon steel in a CO2-saturated oilfield formation water [J]. Electrochim. Acta, 2011, 56: 1676
doi: 10.1016/j.electacta.2010.10.059
[6] Kermani M B, Morshed A. Carbon dioxide corrosion in oil and gas production: A compendium [J]. Corrosion, 2003, 59: 659
doi: 10.5006/1.3277596
[7] Li C F, Wang B, Zhang Y, et al. Research progress of CO2 corrosion in oil/gas field exploitation [J]. J. Southwest Petrol. Inst., 2004, 26(2): 42
[7] (李春福, 王斌, 张颖等. 油气田开发中CO2腐蚀研究进展 [J]. 西南石油学院学报, 2004, 26(2): 42)
[8] De Waard C, Milliams D E. Carbonic acid corrosion of steel [J]. Corrosion, 1975, 31: 177
doi: 10.5006/0010-9312-31.5.177
[9] Davies D H, Burstein C T. The effects of bicarbonate on the corrosion and passivation of iron [J]. Corrosion, 1980, 36: 416
doi: 10.5006/0010-9312-36.8.416
[10] Ogundele G I, White W E. Some observations on corrosion of carbon steel in aqueous environments containing carbon dioxide [J]. Corrosion, 1986, 42: 71
doi: 10.5006/1.3584888
[11] Linter B R, Burstein G T. Reactions of pipeline steels in carbon dioxide solutions [J]. Corros. Sci., 1999, 41: 117
doi: 10.1016/S0010-938X(98)00104-8
[12] Veawab A, Tontiwachwuthikul P, Chakma A. Corrosion behavior of carbon steel in the CO2 absorption process using aqueous amine solutions [J]. Ind. Eng. Chem. Res., 1999, 38: 3917
doi: 10.1021/ie9901630
[13] Zhang G A, Cheng Y F. Electrochemical characterization and computational fluid dynamics simulation of flow-accelerated corrosion of X65 steel in a CO2-saturated oilfield formation water [J]. Corros. Sci., 2010, 52: 2716
doi: 10.1016/j.corsci.2010.04.029
[14] Ikeda A, Ueda M, Mukai S. CO2 behavior of carbon and Cr steels [A]. 39st NACE Annual Conference [C]. Houston, 1984: 39
[15] Schmitt G. CO2 corrosion of steels an attempt to range parameter and their effects [A]. 39st NACE Annual Conference [C]. Houston, 1984: 1
[16] Xia Z, Chou K C, Szklarska-Smialowska Z. Pitting corrosion of carbon steel in CO2-containing NaCl brine [J]. Corrosion, 1989, 45: 636
doi: 10.5006/1.3579317
[17] Rlesenfeld F C, Blohm C L. Corrosion problems in gas purification units employing MEA solutions [J]. Petrol. Refiner, 1950, 29: 141
[18] Colet J L, Thevenot N, Nesic S. Role of conductive corrosion products in the protectiveness of corrosion layers [J]. Corrosion, 1998, 54: 194
doi: 10.5006/1.3284844
[19] Palacios C A, Shadley J R. Characteristics of corrosion scales on steels in a CO2-saturated NaCl brine [J]. Corrosion, 1991, 47: 122
doi: 10.5006/1.3585227
[20] Zhao G X, Chen C F, Lu M X, et al. The formation of product scale and mass transfer channels during CO2 corrosion [J]. J. Chin. Soc. Corros. Prot., 2002, 22: 363
[20] (赵国仙, 陈长风, 路民旭等. CO2腐蚀的产物膜及膜中物质交换通道的形成 [J]. 中国腐蚀与防护学报, 2002, 22: 363)
[21] Sun J B, Sun C, Zhang G A, et al. Effect of water cut on the localized corrosion behavior of P110 tube steel in supercritical CO2/oil/water environment [J]. Corrosion, 2016, 72: 1470
doi: 10.5006/1926
[22] Wu S L, Cui Z D, He F, et al. Characterization of the surface film formed from carbon dioxide corrosion on N80 steel [J]. Mater. Lett., 2004, 58: 1076
doi: 10.1016/j.matlet.2003.08.020
[23] Liu W, Dou J J, Lu S L, et al. Effect of silty sand in formation water on CO2 corrosion behavior of carbon steel [J]. Appl. Surf. Sci., 2016, 367: 438
doi: 10.1016/j.apsusc.2016.01.228
[24] Jiang X, Zheng Y G, Qu D R, et al. Effect of calcium ions on pitting corrosion and inhibition performance in CO2 corrosion of N80 steel [J]. Corros. Sci., 2006, 48: 3091
doi: 10.1016/j.corsci.2005.12.002
[25] Bai H T, Wang Y Q, Ma Y, et al. Effect of CO2 partial pressure on the corrosion behavior of J55 carbon steel in 30% crude oil/brine mixture [J]. Materials, 2018, 11: 1765
doi: 10.3390/ma11091765
[26] Sun J B, Liu W, Chang W, et al. Characteristics and formation mechanism of corrosion scales on low-chromium X65 steels in CO2 environment [J]. Acta Metall. Sin., 2009, 45: 84
[26] (孙建波, 柳伟, 常炜等. 低铬X65管线钢CO2腐蚀产物膜的特征及形成机制 [J]. 金属学报, 2009, 45: 84)
[27] Bai Z Q, Chen C F, Lu M X, et al. Analysis of EIS characteristics of CO2 corrosion of well tube steels with corrosion scales [J]. Appl. Surf. Sci., 2006, 252: 7578
doi: 10.1016/j.apsusc.2005.09.011
[28] Wu H B, Sun R Y, Wang L D, et al. Microstructure and CO2 corrosion resistance of low Cr X70 pipeline steel [J]. J. Shenyang Univ. Technol., 2012, 34: 273
[28] (武会宾, 孙锐艳, 王立东等. 低铬X70管线钢组织及其抗CO2腐蚀性能 [J]. 沈阳工业大学学报, 2012, 34: 273)
[29] Xu L N, Guo S Q, Chang W, et al. Corrosion of Cr bearing low alloy pipeline steel in CO2 environment at static and flowing conditions [J]. Appl. Surf. Sci., 2013, 270: 395
doi: 10.1016/j.apsusc.2013.01.036
[30] Yin Z F, Wang X Z, Liu L, et al. Characterization of corrosion product layers from CO2 corrosion of 13Cr stainless steel in simulated oilfield solution [J]. J. Mater. Eng. Perform., 2011, 20: 1330
doi: 10.1007/s11665-010-9769-z
[31] Wei L, Gao K W, Li Q. Corrosion of low alloy steel containing 0.5% chromium in supercritical CO2-saturated brine and water-saturated supercritical CO2 environments [J]. Appl. Surf. Sci., 2018, 440: 524
doi: 10.1016/j.apsusc.2018.01.181
[32] Cheng Y P. Research on CO2 corrosion characteristics of gathering pipeline steel in the medium containing crude oil [D]. Qingdao: China University of Petroleum (East China), 2016
[32] (程远鹏. 含原油介质中集输管线钢CO2腐蚀特性研究 [D]. 青岛: 中国石油大学 (华东), 2016)
[33] Wei L, Pang X L, Liu C, et al. Formation mechanism and protective property of corrosion product scale on X70 steel under supercritical CO2 environment [J]. Corros. Sci., 2015, 100: 404
doi: 10.1016/j.corsci.2015.08.016
[34] Li J, Sun D B, Yu H Y, et al. EIS characteristics of anodic dissolution for P110 steel under CO2 environment [J]. Electrochemistry, 2001, 7: 120
[34] (李静, 孙冬柏, 俞宏英等. CO2环境中P110钢阳极溶解过程EIS特征 [J]. 电化学, 2001, 7: 120)
[35] Chen C F, Lu M X, Zhao G X, et al. The EIS analysis of electrode reactions of CO2 corrosion of N80 steel [J]. Acta Metall. Sin., 2002, 38: 770
[35] (陈长风, 路民旭, 赵国仙等. N80钢CO2腐蚀电极过程交流阻抗分析 [J]. 金属学报, 2002, 38: 770)
[36] Tan Y J, Bailey S, Kinsella B. Mapping non-uniform corrosion using the wire beam electrode method. I. Multi-phase carbon dioxide corrosion [J]. Corros. Sci., 2001, 43: 1905
doi: 10.1016/S0010-938X(00)00190-6
[37] Zhao D W. Study on formation and characteristic of corrosion product layer of low-chronium steel [D]. Xi'an: Xi'an Shiyou University, 2010
[37] (赵大伟. 低Cr耐蚀材料表面腐蚀产物膜的形成和特性研究 [D]. 西安: 西安石油大学, 2010)
[38] Chen C F, Zhao G X, Yan M L, et al. Characteristics of CO2 corrosion scales on Cr-containing N80 steel [J]. J. Chin. Soc. Corros. Prot., 2002, 22: 335
[38] (陈长风, 赵国仙, 严密林等. 含Cr油套管钢CO2腐蚀产物膜特征 [J]. 中国腐蚀与防护学报, 2002, 22: 335)
[39] Chen C F, Zhao G X, Lu M X, et al. Study of CO2 corrosion scales on N80 steel [J]. J. Chin. Soc. Corros. Prot., 2002, 22: 143
[39] (陈长风, 赵国仙, 路民旭等. N80钢CO2腐蚀产物膜研究 [J]. 中国腐蚀与防护学报, 2002, 22: 143)
[40] Long F L, Zheng W J, Chen C F, et al. Influence of temperature, CO2 partial pressure, flow rate and pH value on uniform corrosion rate of X65 pipeline steel [J]. Corros. Prot., 2005, 26: 290
[40] (龙凤乐, 郑文军, 陈长风等. 温度、CO2分压、流速、pH值对X65管线钢CO2均匀腐蚀速率的影响规律 [J]. 腐蚀与防护, 2005, 26: 290)
[41] Chen C F, Lu M X, Zhao G X, et al. Electrochemical characteristics of CO2 corrosion of well tube steels with corrosion scales [J]. J. Chin. Soc. Corros. Prot., 2003, 23: 139
[41] (陈长风, 路民旭, 赵国仙等. 腐蚀产物膜覆盖条件下油套管钢CO2腐蚀电化学特征 [J]. 中国腐蚀与防护学报, 2003, 23: 139)
[42] Chen C F, Lu M X, Zhao G X, et al. Behavior of CO2 pitting corrosion of N80 steel [J]. J. Chin. Soc. Corros. Prot., 2003, 23: 21
[42] (陈长风, 路民旭, 赵国仙等. N80油管钢CO2腐蚀点蚀行为 [J]. 中国腐蚀与防护学报, 2003, 23: 21)
[43] Farelas F, Galicia M, Brown B, et al. Evolution of dissolution processes at the interface of carbon steel corroding in a CO2 environment studied by EIS [J]. Corros. Sci., 2010, 52: 509
doi: 10.1016/j.corsci.2009.10.007
[44] Zhang G A, Liu D, Li Y Z, et al. Corrosion behaviour of N80 carbon steel in formation water under dynamic supercritical CO2 condition [J]. Corros. Sci., 2017, 120: 107
doi: 10.1016/j.corsci.2017.02.012
[45] Chen C F, Lu M X, Zhao G X, et al. Mechanical properties of CO2 corrosion scale on N80 well tube steel [J]. Acta Metall. Sin., 2003, 39: 175
[45] (陈长风, 路民旭, 赵国仙等. N80油套管钢CO2腐蚀产物膜的力学性能 [J]. 金属学报, 2003, 39: 175)
[46] Ren C Q, Liu D X, Bai Z Q, et al. Study on mechanical properties of corrosion scale on surface of tubular steel N80 [J]. J. Mater. Eng., 2004, (8): 17
[46] (任呈强, 刘道新, 白真权等. N80油管钢腐蚀产物膜的力学性能研究 [J]. 材料工程, 2004, (8): 17)
[47] Yu F, Gao K W, Qiao L J, et al. Effect of temperature on the structure and mechanical properties of CO2 corrosion product films of N80 steel [J]. Corros. Prot., 2009, 30: 145
[47] (俞芳, 高克玮, 乔利杰等. 温度对N80钢CO2腐蚀产物膜结构和力学性能的影响 [J]. 腐蚀与防护, 2009, 30: 145)
[48] Yu F, Gao K W, Lu M X. Investigation of structure and mechanical properties of CO2 corrosion scale formed under various flow rates [J]. J. Chin. Soc. Corros. Prot., 2009, 29: 401
[48] (俞芳, 高克玮, 路民旭. 流动状态下X65管线钢CO2腐蚀产物膜结构和力学性能的评价 [J]. 中国腐蚀与防护学报, 2009, 29: 401)
免责声明:本网站所转载的文字、图片与视频资料版权归原创作者所有,如果涉及侵权,请第一时间联系本网删除。
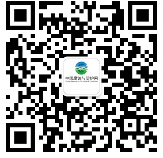
官方微信
《中国腐蚀与防护网电子期刊》征订启事
- 投稿联系:编辑部
- 电话:010-62316606-806
- 邮箱:fsfhzy666@163.com
- 中国腐蚀与防护网官方QQ群:140808414