摘要
分析讨论了带肋钢在不同工况下的锈蚀机理及影响因素,分别从风沙冲蚀、雨水冲刷、大气、淡水、海洋及核辐射6个方面阐述了带肋钢服役过程腐蚀现象。结合当前社会市场需求与已有防护技术,指出了带肋钢防护技术的主要发展方向。
关键词: 带肋钢 ; 工况 ; 腐蚀
热轧带肋钢俗称螺纹钢,是以低合金钢为原料,通过加热轧制而成的建筑“骨架”材料;冷轧带肋钢则是在热轧带肋钢基础上进行冷加工消除应力,如冷拉、拉拔等获得工程用带肋钢。带肋钢产品目前广泛应用于工业及民用建筑、道路、桥梁等重大建筑工程[1-3]。
材料腐蚀是材料基体与周围介质 (水、酸、空气等) 反应致使材料产生损耗与破坏的过程。Hou等[4]研究指出,2014年我国由于腐蚀产生的损失占全年国民生产总值的3.34%,材料腐蚀问题已经严重影响了社会发展。带肋钢作为建筑等常用材料,受地理环境、气候、服役工况等多因素影响而产生的腐蚀问题,直接影响国家及人民财产安全,其腐蚀现象一般发生在生产、运输、储运及服役等中间环节,具体体现于露天存放、保管不当及短期内材料表面产生影响材料外观和表面性能的表面锈蚀现象,以及在服役条件或环境中产生的腐蚀行为。因而研究带肋钢腐蚀机理及防腐措施等已迫在眉睫。
钢筋混凝土结构是带肋钢主要服役环境。腐蚀介质在钢筋混凝土结构中引起钢筋腐蚀的过程可以分为腐蚀诱导因子扩散进入混凝土结构中引起钢筋腐蚀、混凝土因钢筋腐蚀产物的产生出现裂纹和裂纹扩展致使钢筋与混凝土脱离,钢筋外保护层剥落3个阶段[5-7]。钢筋混凝土结构在腐蚀初期因钢筋腐蚀产物的出现,整体结构粘结度将更加密实,内部构件承载力会出现短暂升高的现象;后期随着腐蚀程度的加剧,不断增多的腐蚀产物使得钢筋与混凝土之间的膨胀应力加剧,当膨胀应力值高于钢筋混凝土结构抗拉强度时混凝土出现裂纹及脱落现象[8,9]。
带肋钢腐蚀作用机理主要有化学腐蚀、电化学腐蚀、微生物腐蚀及应力腐蚀开裂等形式,主要以化学腐蚀与电化学腐蚀为主。化学腐蚀即基体材料直接与周围腐蚀介质发生反应,加速表面氧化,产生疏松多孔的氧化铁复合物。电化学腐蚀多发生于潮湿环境中,材料基体内部铁素体、渗碳体及游离石墨等因组份差异形成电解池,发生电化学反应[10]。
带肋钢腐蚀是一个相对缓慢的过程,受工况环境 (风沙冲蚀、雨水冲刷、大气、淡水、海洋及核辐射等环境中砂砾刻蚀、酸、碱、盐、杂质介质构成的电化学腐蚀)、气候及材料成分等因素的影响,在服役、运输及储存过程中的腐蚀现象不可避免。
本文主要综述带肋钢在不同工况下的锈蚀机理及影响因素,分别从风沙冲蚀、雨水冲刷、大气、淡水、海洋及核辐射几方面阐述了露天大气环境锈蚀与服役环境腐蚀的国内外最新研究进展。结合当前已有的涂层技术、电化学处理技术、缓蚀剂等防护技术,以期探索了解满足当前苛刻工况下带肋钢新型防腐技术研究方向,为提高带肋钢存放、服役时限与优化生产工艺提供参考。
1 露天环境的带肋钢表面锈蚀现象与机理
1.1 风沙冲蚀环境中的损伤现象与机理
中国北方地区是沙尘暴高暴发活动区域[11,12],沙漠及周边的桥梁、输电塔和通信塔等钢筋混凝土结构因风沙冲蚀作用受到严重影响。风沙冲蚀过程主要是沙砾对材料的冲蚀磨损[13-15]。
冲蚀磨损是固体表面受流体或带有固体粒子的流体冲击材料表面发生损耗的现象[16,17]。冲蚀磨损受冲蚀环境、流体条件和材料性质等多种因素影响,具体体现于冲蚀角度、冲蚀速率、粒子流量与粒子形状等因素[18-20]。塑性材料与脆性材料的最大冲蚀角范围不同,分别是15°~30°与90°,一般材料的最大冲蚀角介于这两者之间。Finnie[21]根据冲蚀微切削理论指出了粒子低角度冲蚀损伤程度评价公式:
式中:V为材料流失的体积;M为固体粒子质量;v为冲蚀速度;α为冲蚀角度;P为弹性流体压力;c为粒子分数。
在低冲蚀角度时,具有动能的沙粒冲蚀到带肋钢的表面,钢筋表面受到沙粒撞击产生水平切削作用和竖直撞击作用,此时水平切削力大于竖直撞击力,钢筋表面的冲蚀破坏主要以斜向的切削破坏为主;在高冲蚀角度时,钢筋同样受到沙粒撞击产生的水平切削作用和竖直撞击作用,此时竖直撞击力大于水平切削力,钢筋材料因较大的撞击力撞击产生冲蚀挤压变形,发生疲劳而导致变形剥落。一般来讲,带肋钢的最大冲蚀率冲击角在15°~30°内,钢筋材料抗冲蚀效果取决于表面氧化铁皮良好的强韧平衡度。若带肋钢氧化铁皮结构组分与强韧度调控不当就会造成氧化铁皮在风沙冲蚀环境中受损破裂,在与外界环境相互作用发生锈蚀等问题,影响材料外观和及其服役性能[22]。
1.2 雨水冲刷下带肋钢的表面锈蚀损伤现象与机理
雨水冲刷过程中材料腐蚀以电化学锈蚀为主,基材表面形成以铁素体为阳极、渗碳体为阴极的锈蚀微电池。阳极铁失去电子形成Fe2+进入电解池,溶于电解池的O在阴极被还原生成OH-,两者相遇结合生成不溶于水的Fe(OH)2,产物进一步氧化生成Fe(OH)3。材料基体表面铁锈逐步锈蚀脱落,致使锈蚀面积逐渐增大,锈蚀现象愈加严重。图1是带肋钢雨水冲刷过程中的电化学锈蚀机理。
图1 带肋钢外部雨水冲刷过程中的电化学锈蚀机理[23]
雨水冲刷过程中,带肋钢材料表面存在以下现象[23]:(1) 同时存在化学锈蚀和电化学锈蚀两种类型。流动的水带有大量的溶氧化学物质促使钢筋表面发生化学锈蚀和电化学锈蚀。(2) 处于电介质水溶液包围的裸露钢筋,因钢筋内部物相组成 (铁素体、碳化物等) 差异性与晶粒边界/内部的能量差异性导致电化学不均匀性,产生红棕色质地疏松易剥落铁锈。(3) 基体表面形成外小内大、较为平滑的点状锈蚀坑现象。点锈蚀缺陷相互交迭形成凹坑缺陷。(4) 钢筋横肋部位形成断续分布的裂纹缺陷。带肋钢在雨水冲刷过程中使钢筋表面承受着一定的弯曲张应力,钢筋横肋部位局部应力集中,金属能量高,金属离子不稳定,在电介质中呈阳极状态,易产生电化学应力锈蚀,形成垂直分布于钢筋表面,并沿径向由金属表面沿晶或穿晶向基体扩展的裂纹,同时,裂纹缺陷也向周围生长,但其锈蚀速率低于垂直主应力方向的生长速率,即形成杆状裂纹缺陷。沿横肋部位断续分布的杆状裂纹相互贯穿,严重影响了材料的服役使用寿命。
1.3 大气环境中的损伤机理
钢材大气锈蚀是材料表面与周围锈蚀性气体介质相互反应的过程。大气锈蚀现象由来已久,1995年我国因大气锈蚀的钢材达5×106 t[24,25]。大气锈蚀现象较为复杂,在没有污染物及相对湿度高于70%的大气环境中,带肋钢与周围大气接触并发生以下反应[26-30]:
反应形成Fe(OH)2,沉积在金属表面:
Fe(OH)2再继续氧化生成铁锈Fe(OH)3。
然而,大气组成成分复杂多样,其中CO2、SO2、NOx、H2S、NH3、HCl污染性气体与煤烟、灰尘等含碳化合物、砂土、盐类固体颗粒均对带肋钢锈蚀速率产生了严重影响[31,32]。混凝土碳化与酸雨锈蚀是大气锈蚀最为典型的两种方式[33-36]。
混凝土一般在初期呈现强碱性,pH约为12~13,在钢筋表面生成一层防锈蚀的钝化膜层。大气中的酸性物质通过孔隙从混凝土表面渗入混凝土内部,与水泥石中的碱性物质发生中和反应,降低混凝土碱度使钢筋表面的钝化膜发生破坏,钢筋发生锈蚀现象。
酸雨锈蚀中以SO2、H2S、HCl气体对钢筋锈蚀影响最大。SO2吸附在带肋钢基体表面与铁反应生成易溶于水的FeSO4,FeSO4水解生成H2SO4,H2SO4继续与Fe反应,整个过程具有循环往复的特征,反应式[37]:
H2S气体溶于水中增加了H+的含量,使溶液酸化并提升了水膜导电性,加速带肋钢锈蚀。HCl气体溶于水中生成HCl,其中Cl-与阳极反应中产生的Fe2+结合生成可溶性FeCl,锈蚀现象循环进行,反应式[38,39]:
图2为带肋钢在大气锈蚀中形成的锈蚀产物。带肋钢锈蚀形成的第一相化合物是Fe(OH)2,后续氧化形成菱形结构的晶相γ-FeOOH;γ-FeOOH在外界因素作用下演变形成菱形结构 (α-FeOOH),锈蚀速率较低时形成立方结构γ-Fe2O3。四方结构β-FeOOH化合物在氯化物含量较高的环境中形成,在一定的湿度条件下转变为立方结构磁铁矿 (Fe3O4)。反应式如下[40,41]:
图2 带肋钢在大气中的锈蚀产物[41]
此外,带肋钢在污染物存在的锈蚀初期阶段,会在金属表面形成所谓的“绿色铁锈”。绿锈是铁 (II,III) 氢氧化物盐的混合物,化学式如下[42-46]:
1.4 带肋钢在淡水中的锈蚀损伤机理
近些年来淡水等水资源污染现象严重,给社会发展带来的危害也日益凸显,特别是对钢筋混凝土结构的锈蚀破坏。一般地,带肋钢在淡水中的锈蚀有电化学锈蚀与微生物锈蚀[48,49]。
淡水中一般包含有多种正负离子 (如Ca2+、SO42-等),离子的存在、运动及所带电荷的交换,使水库、河道水形成微导电电解池,发生电化学锈蚀[50]。在电解质溶液中,杂质电位较高为阴极,带肋钢电位较低为阳极,带肋钢表面形成许多微电池。微电池的阳极区,Fe释放电子,以水化离子形式溶解于水,自由电子沿带肋钢基体流向阴极区,在阴极区发生物质还原,如溶解氧得到电子后成为O2-,O2-再积水作用获得OH-。Fe2+与OH-结合生成铁锈化合物。淡水中电化学锈蚀受含氧量、淡水流速、pH及溶解元素成分等因素的影响[51-53]。
微生物锈蚀根据不同条件分为好氧锈蚀和厌氧锈蚀[54,55]。好氧锈蚀有氧差电池引起的锈蚀与代谢产物引起的锈蚀两种形式。氧差电池引起的锈蚀中,微生物附着处的O相对缺乏而成为阳极,附近的表面上氧含量相对高而成为阴极,金属在阳极溶解,电子则迁移到阴极处与O结合形成金属的氧化物及其水化物。代谢产物引起的锈蚀中,硫氧化菌氧化硫元素、硫代硫酸盐等产生代谢物H2SO4。锈蚀机理 (以硫氧化菌为例) 可表示为[55]:
好氧锈蚀:
在厌氧锈蚀中:
SRB去极化作用:
微生物锈蚀的整个反应过程由阴极去极化驱动,而阴极上H的消耗速度是限制反应的关键因素。因甲烷菌、硫酸盐还原菌和乙酸菌在生命活动中的生长代谢,消耗了电化学产生出的氢,将加速对材料的锈蚀过程。
2 服役环境腐蚀现象与机理
2.1 带肋钢在海洋环境中的腐蚀损伤机理
钢筋混凝土结构由于优异的性能,在港口码头等工程被大规模应用。然而随着服役时间的延长,钢筋混凝土结构受到严重的海洋腐蚀[56-60]。研究报道,高温、高湿、高盐的南海岛礁环境下钢筋腐蚀率是一般近海环境的31.7~125.8倍,钢筋起锈时间不足25 a,海水侵蚀现象尤为严重[61-63]。一般暴露于不同海洋区域环境条件的钢筋混凝土结构的腐蚀机理也不同。通常海洋腐蚀环境分为海洋大气区、浪花飞溅区、潮差区和海水全浸区,如图3所示[64]。海洋大气区中盐粒因风等作用沉积于钢筋混凝土结构表面,吸湿形成液膜后对建筑物产生污染破坏;潮差区的饱水部分与水下部位,以扩散和渗透为主,作用于钢筋混凝土建筑物;浪溅区和潮差区的非饱水部分,其主要以扩散、毛细管和渗透共同作用,海浪的强烈撞击,以及充足的有氧环境,使此区域的钢筋混凝土结构腐蚀最为严重[65]。
图3 海洋环境中混凝土结构不同部位受不同的侵蚀[64]
海洋环境对于钢筋混凝土结构的腐蚀主要分结构中的钢筋腐蚀,主要以氯致腐蚀为主;以及混凝土基体的腐蚀,主要为镁盐/硫酸盐侵蚀。目前研究人员往往将将两方面割裂开来进行研究,或是集中于钢筋的腐蚀,或是集中于混凝土基体的侵蚀,缺乏两者综合的系统性研究[62,63,66]。
混凝土基体腐蚀方面,混凝土基体成分中的Ca(OH)2与海水中镁盐 (MgCl2与MgSO4等) 发生化学反应。MgCl2与Ca(OH)2反应生成易溶于水的CaCl2与松散而无胶凝能力的Mg(OH)2,且Mg(OH)2难溶于水。MgSO4与Ca(OH)2反应不仅生成松散而无胶凝能力Mg(OH)2,亦生成对水泥产生腐蚀的硫酸盐 (CaSO4·2H2O),即产生镁盐与硫酸盐双重腐蚀。水泥中水化产物需在一定碱度下才能稳定存在,其中Ca(OH)2维持着水泥浆体的碱性,Ca(OH)2的消耗使得水泥浆体碱度低于其他水化产物稳定存在的pH,此时水化硅酸钙 (C—S—H) 等其它水化产物会随之发生分解以维持酸碱度平衡,长时间下不断发生的消耗使水泥石胶凝性降低,孔隙率增大,强度降低,最终致使混凝土基体损坏[67,68]。
混凝土结构中钢筋锈蚀主要以氯致腐蚀为主。氯致腐蚀有4种作用机理[69-73]:(1) 破坏钝化膜。初期高碱性混凝土在钢筋表面形成一层致密的钝化膜层,海水、水泥、水、骨料等中的大量Cl-通过孔隙网孔和微裂纹渗透到混凝土中,在钢筋表面产生局部汇集,致使钢筋表面钝化膜由于局部酸化而破坏。(2) 形成腐蚀电池。混凝土结构中钢筋表面钝化膜被Cl-积聚酸化破坏后,裸露的铁基体与钝化膜完好区域形成电位差,形成微电池。(3) 阳极去极化作用。Cl-可加速阳极反应过程。
Fe(OH)3失水后成为红褐色铁锈。反应过程中Cl-起催化作用,加速了钢筋的纵向腐蚀。(4) 提高腐蚀电流效率。Cl-能强化腐蚀电池中的离子通路,即降低阴、阳两极之间的电阻,提高腐蚀电流效率。
钢筋表面钝化膜被破坏后,混凝土中的钢筋与氧气、湿度等因素下形成的OH-反应产生更多的铁锈 (FeO·(H2O)x)。图4是带肋钢在混凝土中的腐蚀反应原理[74-77],反应式:
图4 带肋钢在混凝土中的腐蚀反应原理[75]
2.2 核环境中的带肋钢腐蚀现象与机理
核电设备常用钢铁材料为AISI304L不锈钢,长期服役于高温、高压、强腐蚀和辐射性极端环境中,导致核电设备关键部件及整机表面发生严重材料腐蚀行为,造成核电设备失效。压水反应堆核电设备的主要腐蚀机制为均匀腐蚀与应力腐蚀开裂[75]。
均匀腐蚀直接危害核电设备组件壁厚,有核泄漏等潜在危害。均匀腐蚀产物若随流动介质发生迁移,将间接引起部件局部腐蚀。例如支撑板间的环向缝隙因二回路腐蚀产物聚集而导致传热管凹陷等现象。均匀腐蚀现象在核电厂中极为普遍,碳钢与常规的低合金钢在高温高压水、酸碱溶液等环境中易腐蚀,反应堆压力容器合金及钢部件发生的硼酸腐蚀等。由于均匀腐蚀对核电厂设备的安全性影响不是很大,通过合理的选材及防腐处理可得到有效的缓解[79]。
应力腐蚀开裂 (SCC) 是指在机械、电化学和冶金等多种因素协同作用,致使材料产生局部萌生裂纹及亚临界裂纹扩展,长期积累的SCC就会导致核设备材料的突发性开裂。核电厂腐蚀失效机理主要以应力腐蚀开裂为主。应力腐蚀开裂类型较多,其包括辐照促进应力腐蚀开裂 (IASCC)、一次侧应力腐蚀开裂 (PWSCC)、二次侧应力腐蚀开裂 (ODSCC) 三类,均是因其有别于其他工业领域的特殊运行工况所致。由于应力腐蚀开裂中部件受腐蚀介质与拉应力的相互作用,既使两者分别处在较低水平都会引发裂纹萌生,裂纹一旦达到临界尺寸 (孕育期) 便会迅速扩展 (扩展期) 成穿晶或沿晶裂纹,最终导致材料发生脆性断裂。其中不锈钢材料以辐照促进应力腐蚀开裂为代表的辐照加速腐蚀失效是核电站安全高效运行的关键问题之一[80-83]。图5是发生应力腐蚀开裂的机理[78]。
图5 应力腐蚀开裂 (SCC) 机理[78]
目前国内外广泛采用A508III (Gr.3C1.1) 和16MND5等低合金钢作为反应堆压力容器材料,合金钢容器内壁堆焊不锈钢以防止与冷却剂的接触产生腐蚀。而蒸汽发生器则多采用690、800等镍基合金材料。反应堆内构件多采用奥氏体不锈钢及部分镍基合金,关于核设备用钢铁材料在高温高压水腐蚀疲劳损伤的研究,由于缺乏微观裂纹萌生和扩展过程的直接实验证据,到底是氢致开裂机制还是滑移溶解机制控制着钢铁材料环境疲劳损伤,尚存在较大争议[84]。对核电设备用钢铁材料服役弱 (老) 化机理及发生规律、寿命设计和预测模型的认识还十分缺乏,相关研究工作仍是核设施腐蚀的研究热点。
3 带肋钢在苛刻工况环境下的防腐蚀技术
目前,国内外带肋钢的生产普遍采用穿水冷却技术,该工艺是一种表面相变强化技术,在改善螺纹钢力学性能方面有很好的效果。然而穿水冷却生产的螺纹钢在服役、储存和运输过程中很容易腐蚀生锈,严重影响了螺纹钢的质量。腐蚀引起的混凝土结构失效给社会发展带来巨大损失。因而,采取有效的措施减缓螺纹钢的腐蚀变得尤为重要。截至目前,防止钢铁制品腐蚀的措施主要有改变钢铁内部结构与表面防腐蚀工程技术两种方法。
3.1 改变钢铁内部结构技术
3.1.1 改变材料中部分构成元素含量
金属材料中部分元素 (C、Mo、N、Cr、Ni等) 含量通常会对材料的抗腐蚀能力有极大改善。文献[85]研究指出,在金属材料中添加C、Mo和N可以降低材料表面活性,提升材料表面抗腐蚀效应。Barker等[86]研究了不同Cr含量钢的抗冲刷腐蚀能力,Cr含量8%以上的钢普遍具有马氏体、双相和亚稳奥氏体的混合结构,具有高加工硬化的潜力,有较强的抗冲刷腐蚀的能力。Ni可以稳定不锈钢的奥氏体相进而增强电极表面的钝化能力[84]。钢中γ相具有韧性好、形变强化能力高等特点,α相硬度也较低,σ相却具有较脆、硬度较高的特点[86]。王国华等[89]研究指出,不锈钢中提高Cr和Mo等铁素体形成元素的含量,既能缩短相形成的孕育期,同时提高了σ相稳定存在的上限温度。Wu等[90]研究认为,Mo含量的增加能提升电极表面钝化能力,增强其抗电化学腐蚀及冲刷腐蚀性能。Ilevbare等[87]研究了不锈钢中Mo对材料性能的影响,认为Mo可能以钼酸盐的形式融入金属的氧化膜中,改变了氧化膜的离子选择性,使得Cl-难以通过;同时,Mo的存在可以增加电极表面钝化膜的厚度。
3.1.2 调控生产工艺参数形成致密氧化铁皮
致密氧化铁皮是利用带肋钢在连铸和轧制过程中,钢材表面在环境介质 (空气、水蒸汽、氧气等) 的作用下生成Fe氧化物层的现象,通过调控铁氧化物层组分及组成,提升材料防腐、耐摩擦磨损性能[88]。带肋钢表面氧化铁皮由内向外由三层Fe的氧化物组成,依次是FeO层、Fe3O4层与Fe2O3层[91]。Fe2O3层呈红褐色且较致密;Fe3O4层呈黑色且致密而无裂纹;FeO层疏松多孔、易被破坏。这些氧化物的氧含量由外到内逐渐减小,并且外层致密,内层疏松多孔。文献[92-94]对Fe氧化层的演变过程研究证明,高于或低于570 ℃时,氧化层中的3种物相结构之间均存在不同程度的物相结构转变。通过合理调节FeO、Fe2O3及Fe3O4物相生成厚度的相对比例及表面缺陷,提高材料自身抵御风沙冲蚀和雨水冲刷等苛刻工况环境的抗腐蚀性能。
3.2 表面防腐蚀工程技术
表面防腐蚀工程技术主要包括:涂层技术、缓蚀剂技术、电化学防护技术等,各种防腐蚀技术相互联系、相互渗透。相比改变钢铁材料内部结构,表面防腐蚀工程技术简单高效、成本低廉,对碳钢等金属制品能起到很好的防护作用。
3.2.1 涂层技术
涂层技术即将涂料涂覆在钢铁材料的表面上,形成具有一定机械强度、一层或多层复合的固态薄膜,称为涂层。涂层具有防止或延缓构件的腐蚀、提高构件的耐磨性能、装饰构件等作用。特殊涂层还具有绝缘、屏蔽电磁波、防静电等功能。目前抗冲蚀磨损涂层按其抗冲蚀作用原理大致可分为硬质与超硬涂层、弹性涂层、自润滑涂层以及仿生涂层等。
硬质涂层起步较早且应用最广,一般为过渡族金属与非金属构成的化合物、金属间化合物等,涂层硬度均在10 GPa以上。除高硬度以外,高韧性也同样重要。保证自身的高硬度和高韧性同时具备并且达到一个最佳比例才能使涂层具有良好的抗冲蚀磨损性能。硬质与超硬涂层制备技术包含物理气相沉积 ( PVD)、化学气相沉积 (CVD) 以及热喷涂等。
文献[18]采用弹性涂层实现回避粒子接触的抗冲蚀设计理论,建立了弹性涂层冲蚀损伤的定量描述模型。由于涂层容易发生弹性形变,可将入射粒子的冲击能转化为本身的弹性应变,从而保护基材不受冲蚀,提升涂层的耐冲蚀能力。
混凝土表面涂层技术。通过混凝土表面涂层处理可以有效阻止Cl-及碳化物等侵蚀因子的危害。现有的混凝土表面涂层技术主要是聚合物改性水泥砂浆与渗透型涂层。
环氧涂层钢筋。通过借助环氧涂层与钢筋之间的强粘结度,保护钢筋不受外界腐蚀介质的侵蚀。美国材料研究协会数据显示,环氧涂层钢筋的使用寿命可延长20 a以上。
层状双金属氢氧化物 (LDHs) 是一类重要的阴离子型黏土材料[93]。目前LDHs应用在腐蚀防护中主要有两种路径,一是通过LDHs材料中阴离子可交换性使其成为缓蚀剂的微纳米级存储器,将其作为掺杂剂掺入涂层中,加强涂层对基体的主动防护作用。二是直接将其作为防腐薄膜,对金属基底起到短期防护作用;或是以此薄膜作为预处理层,后续涂覆有机涂层,起到长期防护作用。
3.2.2 缓蚀剂技术
缓蚀剂技术因用量小、缓蚀效率高、制备过程简单、可循环使用,对环境污染和人体危害性小而被广泛运用于工业锅炉、海洋工程、石油管道、蒸汽冷凝管线以及钢筋混凝土结构等领域的防腐蚀。常用的缓蚀物质有无机缓蚀剂、有机缓蚀剂以及蒸汽缓蚀剂等。
无机缓蚀剂一般包括硼酸盐、磷酸盐、硅酸盐以及钼酸盐等。无机缓蚀与钢材界面反应生成一层致密钝化膜,延缓钢铁腐蚀[94]。亚硝酸盐、铬酸盐虽然对钢材具有较好的缓蚀效果,但是其对环境污染大,对人体有毒害作用。钼酸钠缓蚀剂缓蚀效率高、稳定性好、低毒无公害,适用于高pH、高硬水和较高的温度条件。钼酸盐缓蚀作用是在钢筯表面形成Fe-MoO4-Fe2O3钝化膜,此膜十分致密,隔离了钢筋表面的Cl-的侵蚀。由于钼酸盐价格相对较高,现基本上与其他缓蚀剂混配使用。聚磷酸盐中广泛应用的为三聚磷酸钠和六偏磷酸钠。其缓蚀机理主要是在水中有溶解氧存在下,它在促进钢表面上生成γ-Fe2O3的同时,可与两种金属形成鳌合物沉积在钢表面形成保护膜,目前该类盐常与其他缓蚀剂混配使用。
有机缓蚀剂大多数含P、N、S、O等原子,比较常用的有吡啶类化合物、硫脲及其衍生物以及有机胺等。此类物质与钢铁表面的Fe通过络合吸附形成牢固的吸附膜,阻碍钢材基体与腐蚀介质的直接接触,从而起到缓蚀作用[48]。当AVMHT用量为100 mg/L,温度在60~100 ℃时,缓蚀率可达94.4%,但是此吸附膜与钢筋的结合力较差,弱于钝化膜与钢筋的结合力。文献报道了一种离子液体用作碳钢缓蚀剂的方法[95]。该离子液体由1-辛基-2-吡咯烷酮阳离子和无机或有机阴离子组成,其中阴离子为:HSO4-、NO3-、H2PO4-、CH3COO-、PTSA-以及Br-等,其中盐酸介质溶液浓度为0.1~3 mol/L,溶液温度为15~70 ℃,离子液体加入浓度为0.5~5 mol/L时,延缓碳钢腐蚀率高达90%以上。
蒸汽缓蚀剂。钢材在相对湿度小于40%的环境中腐蚀的可能性较小,相对湿度在40%~60%之间可以发生腐蚀,但速率较低;当相对湿度比例大于60%时,材料腐蚀速度急剧增长。因而控制空气湿度,特别是相对湿度,消除水分是抑制大气腐蚀速率的关键。相关实验研究证明[29],钢铁材料表界面使用蒸汽缓蚀剂 (VCI),可以使得金属和水之间面形成单分子膜的化合物。图6是蒸汽缓蚀剂原理[29]。在钢材表面的抑制剂薄膜中,分子的一端是亲水性的,另一端是疏水性的。蒸汽缓蚀剂的吸附能约为-10~14 kJ/mol,在金属表面具有很强的物理吸附性。蒸汽缓蚀剂中疏水端使得材料与腐蚀性物质的任何表面接触最小化,从而增强材料的抗腐蚀性能。
图6 蒸汽缓蚀剂原理图[29]
3.2.3 电化学防护技术
金属-电解质溶解腐蚀体系受到阴极极化时,电位负移,金属阳极氧化反应过电位减小,反应速度减小,因而金属腐蚀速度减小,称为阴极保护效应。电化学 (阴极) 保护法分两种:外加电流阴极保护和牺牲阳极阴极保护。
牺牲阳极阴极保护是将电位更负的金属与被保护金属连接,并处于同一电解质中,使该金属上的电子转移到被保护金属上去,使整个被保护金属处于一个较负的相同的电位下。该方式简便易行,不需要外加电源,很少产生腐蚀干扰,广泛应用于保护小型 (电流一般小于1A) 金属结构。对于牺牲阳极的使用有很多失败的教训,失败的主要原因是阳极表面生成一层不导电的硬壳,限制了阳极的电流输出。
外加电流阴极保护是通过外加直流电源以及辅助阳极,迫使电流从介质中流向被保护金属,使被保护金属结构电位低于周围环境。该方式主要用于保护大型金属结构。
4 带肋钢腐蚀防护未来发展的几点思考
美国科学院研究指出目前腐蚀领域存在4种亟待解决的问题:(1) 研究探索低成本环境友好型耐腐蚀材料及涂层;(2) 模拟研究现实服役环境中腐蚀的高保真模型;(3) 探索开发对现实服役环境中腐蚀行为进行定量关联可控的实验室加速实验方法;(4) 实现精确预测现有设备修理、更换及停用的寿命时限。结合带肋钢目前生产及苛刻工况下服役过程中存在的腐蚀现象,探索新型防护技术。具体为以下几个方面。
4.1 带肋钢腐蚀机理研究
有必要针对影响带肋钢在各服役环境中的腐蚀因子进行相关的研究,分析不同工况下带肋钢的腐蚀机理。根据不同工况环境下腐蚀发生的机理,分析腐蚀条件下防护的关键要素,为带肋钢的工业化生产及应用提供技术支持。
4.2 混凝土损伤机理研究
混凝土开裂破损致使钢筋与外界腐蚀因子接触,从而影响钢筋混凝土结构的耐久性。明确混凝土各项指标对钢筋腐蚀保护的关键因素,例如钢筋混凝土保护层的厚度、保护层混凝土的碱度、保护层混凝土的密实度与抗水、气渗透能力、抗裂性能的关联性等。明确混凝土损伤机理,探索混凝土损伤防护技术,为钢筋混凝土结构的实施应用提供新的技术支持。
4.3 带肋钢腐蚀的防护技术开发
针对不同苛刻工况环境腐蚀机理,研究带肋钢腐蚀修复技术。近年来发展的缓蚀剂抑制带肋钢腐蚀技术,通过利用缓蚀剂在金属表面吸附形成连续的薄膜阻隔介质腐蚀、改变金属腐蚀电位阻止电化学腐蚀反应中的阳极金属溶解及阴极H+放电析出氢气等效能,极大改善了带肋钢腐蚀现象;电镀、涂覆及沉积等表面涂层防护技术,涂料通过涂层处理技术在钢材基体上形成一层紧密结合的固化膜,阻碍了钢基材与有害介质因子的接触,有效延长了材料服役及储放期限;致密氧化铁皮防腐蚀技术中利用带肋钢在生产过程中产生铁氧化层的现象及铁氧化层组分Fe2O3、Fe3O4、FeO的物相性质,通过在钢筋生产线上调控带肋钢铁皮氧化层的物相组成及厚度比例,提升材料自防腐、耐摩擦磨损性能。然而当前主要应用的带肋钢防护技术已经不能满足风沙、雨水、海洋环境、淡水环境及核环境等苛刻工况下服役时限需求。因而研究新型带肋钢防护技术、引导带肋钢腐蚀防护产业的发展方向已迫在眉睫。
5 结语
随着社会的发展,带肋钢所面临的工况环境会愈加苛刻,未来材料的表面防护技术将朝着适应复杂多变的多种功能一体化、超长寿命的方向发展。这需要基础理论研究结合实际试验分析,从材料的设计、生产制备以及服役寿命与失效机制等方面,明确材料的结构与效能关系、表界面相互作用等,从而达到延缓材料锈蚀期限、减缓材料的服役失效行为。虽然当前防腐技术取得一些突破,但是在未来的发展中还需要研究防腐的新技术和新方法,降低锈蚀产生的损失。
参考文献
1 Su H Z. Study on the production process of HRB400 hot-rolled ribbed steel bar [D]. Chongqing: Chongqing University, 2007
1 苏鹤洲. HRB400热轧带肋钢筋生产工艺研究 [D]. 重庆: 重庆大学, 2007
2 Jin X, Song R B, Wang X Y, et al. Production process optimization of the hot rolling HRB400 rebar [J]. Henan Metall., 2013, 21(2): 45
2 靳熙, 宋仁伯, 王晓燕等. HRB400带肋钢筋生产工艺优化 [J]. 河南冶金, 2013, 21(2): 45
3 Zhou F G, Wu S J. Production practice of Nb-bearing HRB400 hot rolling ribbed reinforced bar [J]. China Metall., 2005, (9): 33
3 周福功, 吴绍杰. 含铌HRB400热轧带肋钢筋的生产实践 [J]. 中国冶金, 2005, (9): 33
4 Hou B R, Li X G, Ma X M, et al. The cost of corrosion in China [J]. NPJ Mater. Degrad., 2017, 1: 4
5 Wang J. Effect of concrete cover on corrosion mechanism and corrosion rate of steel bar [J]. Market Res. Inform., 2019, (4): 81
5 王建. 混凝土保护层对钢筋腐蚀机理及腐蚀速率的影响 [J]. 市场调查信息 (综合版), 2019, (4): 81
6 Li F M, Li Z J. Continuum damage mechanics based modeling of fiber reinforced concrete in tension [J]. Int. J. Solids Struct., 2001, 38: 777
7 Li Z, Jin Z Q, Shao S S, et al. A review on reinforcement corrosion mechanics and monitoring techniques in concrete in marine environment [J]. Mater. Rev., 2018, 32: 4170
7 李哲, 金祖权, 邵爽爽等. 海洋环境下混凝土中钢筋锈蚀机理及监测技术概述 [J]. 材料导报, 2018, 32: 4170
8 Al-Tikrite A, Hadi M N S. Mechanical properties of reactive powder concrete containing industrial and waste steel fibres at different ratios under compression [J]. Constr. Build. Mater., 2017, 154: 1024
9 Jin W L, Zhou Z D, Mao J H, et al. Experimental study on magnetic field distribution in the fatigue process of corroded steel bars [J]. Ocean Eng., 2016, 34(5): 65
9 金伟良, 周峥栋, 毛江鸿等. 锈蚀钢筋在疲劳荷载作用下压磁场分布研究 [J]. 海洋工程, 2016, 34(5): 65
10 Li J. Effect of negative difference rate and corrosion of hot rolled ribbed steel bar on steel bar performance [A]. Academic Seminar on Railway and Construction Steel [C]. Huangshan, 2013: 311
10 李军. 热轧带肋钢筋负差率及锈蚀对钢筋性能的影响 [A]. 2013年铁路和建筑用钢学术研讨会论文集 [C]. 黄山, 2013: 311
11 Liu J T, Zheng M Q. Climatic characteristics of strong and very strong sandstorms in the middle and west parts of Inner Mongolia [J]. Plateau Meteor., 2003, 22: 51
11 刘景涛, 郑明倩. 内蒙古中西部强和特强沙尘暴的气候学特征 [J]. 高原气象, 2003, 22: 51
12 Cai C X, Jiang W M, Huang S H, et al. Chemical characteristic of two duststorms in the south-east coastal area of China and its possible origin [J]. Plateau Meteor., 2000, 19: 179
12 蔡晨霞, 蒋维楣, 黄世鸿等. 我国东南沿海两次沙尘的化学特征及其源地探讨 [J]. 高原气象, 2000, 19: 179
13 Ma Z H, Wang J. Progress on study of erosion of military equipments by sand and dust [J]. Corros. Sci. Prot. Technol., 2005, 17: 112
13 马志宏, 汪浚. 砂尘环境中军用装备磨损腐蚀进展的研究 [J]. 腐蚀科学与防护技术, 2005, 17: 112
14 Hao Y H, Xing Y M, Zhao Y R, et al. Erosion mechanism and evaluation method of steel structure coating eroded under sandstorm environment [J]. J. Build. Mater., 2011, 14: 345
14 郝贠洪, 邢永明, 赵燕茹等. 风沙环境下钢结构涂层侵蚀机理及评价方法 [J]. 建筑材料学报, 2011, 14: 345
15 Hao Y H, Xing Y M, Feng Y J, et al. Research on anti-erosion mechanical properties of steel structure coating [J]. J. Build. Mater., 2013, 16: 1092
15 郝贠洪, 邢永明, 冯玉江等. 钢结构表面涂层材料抗风沙冲蚀力学性能研究 [J]. 建筑材料学报, 2013, 16: 1092
16 Li L, Wei T C, Liu M W, et al. Research progress on erosion wear mechanism and anti-erosion coatings [J]. J. Chongqing Jiaotong Univ. (Nat. Sci.), 2019, 38(8): 70
16 李力, 魏天酬, 刘明维等. 冲蚀磨损机理及抗冲蚀涂层研究进展 [J]. 重庆交通大学学报 (自然科学版), 2019, 38(8): 70
17 Yao M J, Li C F, He J B, et al. Progresses of anti-erosion coatings [J]. Mater. Rev., 2015, 29: 283
17 姚梦佳, 李春福, 何俊波等. 抗冲蚀磨损涂层的研究进展 [J]. 材料导报: 纳米与新材料专辑, 2015, 29: 283
18 Ren Y. Erosion wear mechanism and evaluation of steel-structure coating in sandstorm [D]. Hohhot: Inner Mongolia University of Technology, 2014
18 任莹. 钢结构涂层受风沙环境冲蚀机理和损伤程度评价研究 [D]. 呼和浩特: 内蒙古工业大学, 2014
19 Li S Z, Dong X L. Erosion Wear and Fretting Wear of Materials [M]. Beijing: Mechanical Industry Press, 1987
19 李诗卓, 董祥林. 材料的冲蚀磨损与微动磨损 [M]. 北京: 机械工业出版社, 1987
20 Ballout Y, Mathis J A, Talia J E. Solid particle erosion mechanism in glass [J]. Wear, 1996, 196: 263
21 Finnie I. Erosion of surfaces by solid particles [J]. Wear, 1960, 3: 87
22 Hao Y H, Ren Y, Duan G L, et al. Erosion mechanism and evaluation of steel structure coating eroded under sandstorm environment [J]. Tribology, 2014, 34: 357
22 郝贠洪, 任莹, 段国龙等. 钢结构表面涂层受风沙冲蚀机理和评价方法 [J]. 摩擦学学报, 2014, 34: 357
23 Yang S. The development of high-strength steel and the research of anti-corrosion resistance [D]. Xi'an: Xi'an University of Architecture and Technology, 2015
23 杨森. 高强度钢筋开发及抗锈蚀性研究 [D]. 西安: 西安建筑科技大学, 2015
24 Ding G Q, Zhang B. Research progress of atmospheric corrosion of steels in natural environment [J]. Equip. Environ. Eng., 2010, 7(3): 42
24 丁国清, 张波. 钢在自然环境中的大气腐蚀研究进展 [J]. 装备环境工程, 2010, 7(3): 42
25 Zhang Q C, Wu J S. Current status of R&D work on weathering steel [J]. Mater. Rev., 2000, 14(7): 12
25 张全成, 吴建生. 耐侯钢的研究与发展现状 [J]. 材料导报, 2000, 14(7): 12
26 Liu Z. Discussion on atmospheric corrosion of weathering steel and carbon steel [J]. China High-Tech Enterprises, 2015, (7): 85
26 柳喆. 耐候钢和碳钢大气腐蚀探讨 [J]. 中国高新技术企业, 2015, (7): 85
27 Zhang Q C, Wu J S, Yang X F, et al. Investigation of accelerated laboratory tests for weathering steel [J]. Mater. Prot., 2002, 35(3): 21
27 张全成, 吴建生, 杨晓芳等. 耐大气腐蚀用钢实验室加速腐蚀的研究 [J]. 材料保护, 2002, 35(3): 21
28 Yang X F, Zheng W L. Analysis on the corrosion rust of weathering steel and carbon steel exposed to atmosphere for two years [J]. Corros. Prot., 2002, 23: 97
28 杨晓芳, 郑文龙. 暴露2年的碳钢与耐候钢表面锈层分析 [J]. 腐蚀与防护, 2002, 23: 97
29 Bavarian B, Ikder Y, Samimi B, et al. Comparison of the corrosion protection effectiveness of vapor corrosion inhibitors and dry air system [A]. Corrosion 2015 Conference [C]. Dallas, Texas, 2015: 10
30 Wang X J. Research on the behaviors and mechanism of the rust layer evolution of the early stages of atmospheric corrosion for metals [D]. Beijing: China Academy of Machinery Science and Technology, 2013
30 王秀静. 金属材料大气环境早期腐蚀行为及锈层演化机制研究 [D]. 北京: 机械科学研究总院, 2013
31 Boden P J. Effect of concentration, velocity and temperature [A]. Corrosion [M]. 3rd Ed. New York: Elsevier, 1994
32 Liu J Z. A review of carbonation in reinforced concrete (1): Mechanism of carbonation and evaluative methods [J]. Concrete, 2005, (11): 10
32 柳俊哲. 混凝土碳化研究与进展 (1)—碳化机理及碳化程度评价 [J]. 混凝土, 2005, (11): 10
33 Li G, Yuan Y S, Geng O. Influences of climate conditions to the concrete carbonization rates [J]. Concrete, 2004, (11): 49
33 李果, 袁迎曙, 耿欧. 气候条件对混凝土碳化速度的影响 [J]. 混凝土, 2004, (11): 49
34 Papadakis V G, Vayenas C G, Fardis M N. Fundamental modeling and experimental investigation of concrete carbonation [J]. ACI Mater. J., 1991, 88: 363
35 Roberge P R. Handbook of Corrosion Engineering [M]. New York: McGraw-Hill, 2000
36 Smart N G, Gamboa-Aldeco M, Bockris J O M. Corrosion mechanisms of iron in concentrated acidic zinc chloride media [J]. Corros. Sci., 1993, 34: 759
37 Enke C G. Werkstoffe und korrosion [J]. Mater. Corros., 1972, 23: XLIII
38 Pacheco A M G, Teixeira M G I B, Ferreira M G S. Initial stages of chloride induced atmospheric corrosion of iron: an infrared spectroscopic study [J]. Br. Corros. J., 1990, 25: 57
39 Refait P, Benali O, Abdelmoula M, et al. Formation of 'ferric green rust' and/or ferrihydrite by fast oxidation of iron (II-III) hydroxychloride green rust [J]. Corros. Sci., 2003, 45: 2435
40 Legrand L, Sagon G, Lecomte S, et al. A Raman and infrared study of a new carbonate green rust obtained by electrochemical way [J]. Corros. Sci., 2001, 43: 1739
41 Refait P, Memet J B, Bon C, et al. Formation of the Fe(II)-Fe(III) hydroxysulphate green rust during marine corrosion of steel [J]. Corros. Sci., 2003, 45: 833
42 Géhin A, Ruby C, Abdelmoula M, et al. Synthesis of Fe(II-III) hydroxysulphate green rust by coprecipitation [J]. Solid State Sci., 2002, 4: 61
43 Ruby C, Géhin A, Abdelmoula M, et al. Coprecipitation of Fe(II) and Fe(III) cations in sulphated aqueous medium and formation of hydroxysulphate green rust [J]. Solid State Sci., 2003, 5: 1055
44 Hong N F. Corrosion in water environments and durability of concrete [J]. Corros. Prot., 2006, 27: 174
44 洪乃丰. 水环境腐蚀与混凝土的耐久性 [J]. 腐蚀与防护, 2006, 27: 174
45 Odokuma L O, Ugboma C J. Microbial corrosion of steel coupons in a freshwater habitat in the Niger Delta [J]. J. Ecol. Nat. Environ., 2012, 4: 42
46 Cao G, Gao C, Gan F X. Corrosion behaviors of carbon steel in fresh water [J]. Equip. Environ. Eng., 2006, 3(1): 46
46 曹刚, 高翠, 甘复兴. 碳钢在淡水环境中的腐蚀行为 [J]. 装备环境工程, 2006, 3(1): 46
47 Zhang W Y. Corrosion and prevention of hydraulic steel gate in freshwater environment [J]. Surf. Technol., 2001, 30(4): 20
47 张文渊. 淡水环境中水工钢闸门的腐蚀与防护 [J]. 表面技术, 2001, 30(4): 20
48 Yang Z K. Corrosion and its control of steel radiator [J]. Heat. Vent. Air Cond., 2001, 31(1): 21
48 杨志宽. 钢制散热器腐蚀与控制 [J]. 暖通空调, 2001, 31(1): 21
49 Zhu Y X, Zhu X C, Ge Y, et al. Study on corrosion behavior of steel in flowing freshwater [J]. Hydro-Sci. Eng., 2002, (2): 7
49 朱雅仙, 朱锡昶, 葛燕等. 流动淡水中钢的腐蚀行为研究 [J]. 水利水运工程学报, 2002, (2): 7
50 Beech I B. Biocorrosion: Role of sulfate reducing bacteria [A]. Encyclopedia of Environmental Microbiology [M]. New York: John Wiley & Sons, Inc., 2003
51 Dinh H T, Kuever J, Mu?mann M, et al. Iron corrosion by novel anaerobic microorganisms [J]. Nature, 2004, 427: 829
52 Hamilton W A. Microbially influenced corrosion as a model system for the study of metal microbe interactions: A unifying electron transfer hypothesis [J]. Biofouling, 2003, 19: 65
53 Lv H, Wei C F, Liang B F, et al. Analysis on causes of high corrosion rate in circulating water system of chemical fertilizer plant [J]. Petrochem. Technol. Appl., 2000, 18: 362
53 吕红, 魏存发, 梁宝锋等. 大化肥循环水系统腐蚀率高的原因剖析 [J]. 石化技术与应用, 2000, 18: 362
54 Gibson G R. Physiology and ecology of the sulphate-reducing bacteria [J]. J. Appl. Bacteriol., 1990, 69: 769
55 Zhu R X, Na J Y, Guo S W, et al. Corrosion mechanism of sulfate-reducing bacteria [J]. J. Air Force Eng. Univ. (Nat. Sci. Ed.), 2000, 1(3): 10
55 朱绒霞, 那静彦, 郭生武等. 硫酸盐还原菌的腐蚀机理 [J]. 空军工程大学学报 (自然科学版), 2000, 1(3): 10
56 Xu Q, Zhan S L, Zhang Q L, et al. Preparation and properties of nano-silicone marine reinforced concrete permeable protective coating [J]. Chin. J. Mater. Res., 2014, 28: 443
56 徐强, 詹树林, 张启龙等. 海洋工程钢筋混凝土纳米硅渗透型防护剂的制备和性能 [J]. 材料研究学报, 2014, 28: 443
57 Wu Q L. Research on flexural RC components exposed to marine environments: durability and life prediction [D]. Nanjing: Nanjing University of Aeronautics and Astronautics, 2010
57 吴庆令. 海洋环境钢筋混凝土受弯构件的耐久性与寿命预测 [D]. 南京: 南京航空航天大学, 2010
58 Tian H W, Li W H, Zong C Z, et al. Corrosion mechanism and research progress of anti-corrosion coatings for reinforced concrete used in marine environment [J]. Paint Coat. Ind., 2008, 38(8): 62
58 田惠文, 李伟华, 宗成中等. 海洋环境钢筋混凝土腐蚀机理和防腐涂料研究进展 [J]. 涂料工业, 2008, 38(8): 62
59 Morris W, Vazquez M. Corrosion of reinforced concrete exposed to marine environment [J]. Corros. Rev., 2002, 20: 469
60 Zhu H W, Yu H F, Ma H Y. Electrochemical study on effect of rust inhibitors on corrosion of reinforcing bar in concrete in marine environment [J]. J. Southeast Univ. (Nat. Sci. Ed.), 2020, 50: 109
60 朱海威, 余红发, 麻海燕. 阻锈剂对海洋环境下混凝土中钢筋腐蚀影响的电化学研究 [J]. 东南大学学报 (自然科学版), 2020, 50: 109
61 Yu Z T, Han D J. Method of carbonization reliability assessment for existing reinforced concrete bridges [J]. J. South China Univ. Technol. (Nat. Sci. Ed.), 2004, 32(2): 50
61 禹智涛, 韩大建. 既有钢筋混凝土桥梁碳化可靠度评估方法 [J]. 华南理工大学学报 (自然科学版), 2004, 32(2): 50
62 Song L Y. Study on chloride corrosion durability of reinforced concrete marine structures [D]. Dalian: Dalian University of Technology, 2009
62 宋立元. 海洋钢筋混凝土结构氯离子腐蚀耐久性研究 [D]. 大连: 大连理工大学, 2009
63 Liang Y N, Yuan Y S. Test study on bond behavior of corroded concrete and steel bars [J]. Concrete, 2008, (2): 20
63 梁咏宁, 袁迎曙. 受硫酸盐腐蚀混凝土与钢筋黏结性能的研究 [J]. 混凝土, 2008, (2): 20
64 Artigas A, Monsalve A, Sipos K, et al. Development of accelerated wet-dry cycle corrosion test in marine environment for weathering steels [J]. Corros. Eng. Sci. Technol., 2015, 50: 628
65 Melchers R E, Li C Q. Reinforcement corrosion in concrete exposed to the North Sea for more than 60 years [J]. Corrosion, 2009, 65: 554
66 Han J Y, Dai C, Gao Z H, et al. Microorganism corrosion of concrete [J]. Mater. Rev., 2002, 16(10): 42
66 韩静云, 戴超, 郜志海等. 混凝土的微生物腐蚀 [J]. 材料导报, 2002, 16(10): 42
67 Li J C M. Microstructure and Properties of Materials [M]. Singapore: World Scientific, 1996
68 Miller F M, Tang F J. The distribution of sulfur in present-day clinkers of variable sulfur content [J]. Cem. Concr. Res., 1996, 26: 1821
69 Ormellese M, Berra M, Bolzoni F, et al. Corrosion inhibitors for chlorides induced corrosion in reinforced concrete structures [J]. Cem. Concr. Res., 2006, 36: 536
70 Hussain S E, Al-Gahtani A S, Rasheeduzzafar. Chloride threshold for corrosion of reinforcement in concrete [J]. ACI Mater. J., 1996, 93: 534
71 Pavan I, Reddy K, Pai V. Repair and rehabilitation of concrete pavements [J]. Int. J. Eng. Res. Dev., 2015, 11: 2278
72 Mohammed T U, Otsuki N, Hamada H. Corrosion of steel bars in cracked concrete under marine environment [J]. J. Mater. Civil Eng., 2003, 15: 460
73 Skoglund P, Silfwerbrand J, Holmgren J, et al. Chloride redistribution and reinforcement corrosion in the interfacial region between substrate and repair concrete-a laboratory study [J]. Mater. Struct., 2008, 41: 1001
74 Quraishi M A, Nayak D K, Kumar R, et al. Corrosion of reinforced steel in concrete and its control: An overview [J]. J. Steel Struct. Constr., 2017, 2: 124
75 Mehta P K, Monteiro P J M. Concrete: Microstructure, Properties, and Materials [M]. 4th Ed. New York: McGraw-Hill, 2014
76 Isgor O B, Razaqpur A G. Modelling steel corrosion in concrete structures [J]. Mater. Struct., 2006, 39: 291
77 Raupach M. Corrosion of steel reinforcement in concrete [J]. Mater. Corros., 2009, 60: 77
78 He K, Xu Y F, Tan Y, et al. Review of corrosion behavior of typical nuclear power materials [J]. Shandong Chem. Ind., 2018, 47(22): 61
78 何宽, 徐芸菲, 檀玉等. 核电典型材料的腐蚀行为研究综述 [J]. 山东化工, 2018, 47(22): 61
79 Liu X, Zhao J C, Wang G G, et al. Failure analysis of pipelines and welding joints in nuclear power plant [J]. Fail. Anal. Prev., 2013, 8: 300
79 刘肖, 赵建仓, 王淦刚等. 核电厂管道及焊接接头失效案例综述 [J]. 失效分析与预防, 2013, 8: 300
80 Staehle R W, Gorman J A. Quantitative assessment of submodes of stress corrosion cracking on the secondary side of steam generator tubing in pressurized water reactors: Part 1 [J]. Corrosion, 2003, 59: 931
81 Andresen P L, Ford F P. Prediction of stress corrosion cracking (SCC) in nuclear power systems [A]. Stress Corrosion Cracking [M]. Cambridge: Woodhead Publishing, 2011: 651
82 Peng Q J, Hou J, Takeda Y, et al. Effect of chemical composition on grain boundary microchemistry and stress corrosion cracking in Alloy 182 [J]. Corros. Sci., 2013, 67: 91
83 Wang Y. Study on surface contamination and surface modification of nuclear grade materials [D]. Dalian: Dalian University of Technology, 2010
83 王永. 核级材料的表面污染及表面改性研究 [D]. 大连: 大连理工大学, 2010
84 Deng P. Irradiation assisted corrosion and stress corrosion of nuclear-grade 304 stainless steel in high temperature and high pressure water [D]. Hefei: University of Science and Technology of China, 2018
84 邓平. 核级304不锈钢辐照促进高温高压水环境腐蚀与应力腐蚀研究 [D]. 合肥: 中国科学技术大学, 2018
85 Hu X, Neville A. The electrochemical response of stainless steels in liquid-solid impingement [J]. Wear, 2005, 258: 641
86 Barker K C, Ball A. Synergistic abrasive—corrosive wear of chromium containing steels [J]. Br. Corros. J., 1989, 24: 222
87 Ilevbare G O, Burstein G T. The role of alloyed molybdenum in the inhibition of pitting corrosion in stainless steels [J]. Corros. Sci., 2001, 43: 485
88 Zheng Z B, Zheng Y G, Sun W H, et al. Erosion-corrosion of HVOF-sprayed Fe-based amorphous metallic coating under impingement by a sand-containing NaCl solution [J]. Corros. Sci., 2013, 76: 337
89 Wang G H. Influence of the sigma phase precipitation on the microstructure and properties in duplex stainless steel [J]. China Metall., 2011, 21(6): 15
89 王国华. σ相的析出对双相不锈钢组织性能的影响 [J]. 中国冶金, 2011, 21(6): 15
90 Wu X Q, Jing H M, Zheng Y G, et al. Resistance of Mo-bearing stainless steels and Mo-bearing stainless-steel coating to naphthenic acid corrosion and erosion-corrosion [J]. Corros. Sci., 2004, 46: 1013
91 Bertrand N, Desgranges C, Poquillon D, et al. Iron oxidation at low temperature (260~500 ℃) in air and the effect of water vapor [J]. Oxid. Met., 2010, 73: 139
92 Zhang B, Cao J, Guo Z, et al. Effect of cooling bed temperature on the corrosion resistance of surface oxide scale of rebar [J]. J. Anhui Univ. Technol. (Nat. Sci.), 2018, 35: 301
92 张波, 曹杰, 郭湛等. 上冷床温度对螺纹钢筋表面氧化铁皮抗锈蚀性能的影响 [J]. 安徽工业大学学报 (自然科学版), 2018, 35: 301
93 Chen R Y. Mechanism of iron oxide scale reduction in 5%H2-N2 gas at 650~900 ℃ [J]. Oxid. Met., 2017, 88: 687
94 Chen R Y, Yuen W Y D. Longer term oxidation kinetics of low carbon, low silicon steel in 17H2O-N2 at 900 ℃ [J]. Oxid. Met., 2016, 85: 489
95 Huang B H, Xu X L, Liu J, et al. A method for using ionic liquids as corrosion inhibitors for carbon steel [P]. Chin. Pat., 201010019346.8, 2010
95 黄宝华, 徐效陵, 刘军等. 一种离子液体用作碳钢缓蚀剂的方法 [P]. 中国专利, 201010019346.8, 2010)
免责声明:本网站所转载的文字、图片与视频资料版权归原创作者所有,如果涉及侵权,请第一时间联系本网删除。
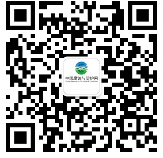
官方微信
《中国腐蚀与防护网电子期刊》征订启事
- 投稿联系:编辑部
- 电话:010-62316606-806
- 邮箱:fsfhzy666@163.com
- 中国腐蚀与防护网官方QQ群:140808414