摘要
采用电解充氢的方法对Ti70合金试样充氢,并用气体分析仪和金相显微镜 (OM) 对其氢含量和显微组织进行表征,以探究微观组织、扩散方向以及比表面积对吸氢行为的影响。结果表明:Ti70合金的吸氢能力随β相的连续程度增大而升高,原因在于具有bcc结构的β相提供了更多的四面体间隙,成为H更易扩散的通道;进入试样的H在宏观上呈非均匀分布,含量由试样表面向心部迅速降低,且H沿轧制方向的扩散能力明显大于板厚方向,这是由于沿板厚方向扩散时,拉长的α晶粒成为氢扩散的阻力,而在轧制方向狭长的连续β相更利于H的渗入;随试样比表面积增大,吸H量显著上升,进一步表明H沿表面吸入后难以充分向内扩散,导致单位体积对应的表面积越大吸氢能力越强。
关键词: Ti70合金 ; 显微组织 ; 扩散方向 ; 比表面积 ; 吸氢能力
钛合金具有耐蚀性好、比强度高、高温服役性能优良等优异的综合性能[1,2],被广泛应用于航空、航天、航海等领域。然而,Ti本身是一种活泼元素,与H、O等元素具有极高的亲和力[3],因此钛合金也常作为优异的储氢材料。这也导致了钛合金在熔炼、热加工和焊接等工艺环节以及腐蚀析氢的服役环境中会发生吸氢现象[4-6],致使力学性能显著下降,即产生氢脆。Lenning等[7]研究发现,α-Ti的冲击韧性会随着氢含量的增加而急剧下降。Kessler等[8]研究了加载前不存在氢化物的α+β型钛合金Ti-2Fe-2Zr-2Mo,结果表明,氢含量小于320 μg/g时,Ti-2Fe-2Zr-2Mo的断面收缩率会随氢含量的升高而下降。由此可见,氢含量对钛合金的性能影响显著,探明吸氢行为,对找到控制氢含量的方法和深入理解钛合金氢脆机理具有重要意义。
有研究[9]证明,α+β型钛合金的吸氢能力与其显微组织密切相关,吸氢行为受到β相的数量、连续性的显著影响,但关于近α型钛合金的吸氢能力与其显微组织的研究未见报道。Yan等[10]认为H的引入会导致α-Ti表层形成氢化物,引起块状材料中的氢分布不均匀,但未详细描述合金中氢富集部位。因此,为了较为系统地认识近α型钛合金与氢之间的作用规律,本文从微观组织、扩散方向以及比表面积三个方面来研究Ti70合金的吸氢行为,为实际应用过程中控制氢含量从而降低氢脆风险提供参考。
1 实验方法
实验材料选用Ti70 (Ti-2.5Al-2Zr-1Fe) 合金板材,板材规格为300 mm×150 mm×10 mm,原始氢含量约为12~17 μg/g,根据多次金相显微组织统计,Ti70合金中β相含量的约为7%~15%。1~4#试样分别为未经处理、在800 ℃下保温20 min并空冷、在900 ℃保温20 min并空冷以及在1000 ℃下保温20 min并空冷的Ti70合金板材。
Ti70合金试样充氢采用电解法,碳棒为阳极,钛合金试样为阴极,在充氢过程中,轧制面正对碳棒,并以轧制面作为参考面设置充氢电流,电流密度为10 mA/cm2。电解液为5%H2SO4 (质量分数)+0.6 g/L 硫脲,硫脲作为催化剂可加速H向钛板中的扩散,充氢量由充氢时长和电流密度共同控制。
氢含量检测所用仪器为ONH2000气体分析仪,参照ASTM E1447-09 (R2016) 标准采用惰性气体熔融热导法进行检测,实验过程中的氢含量检测在未特殊说明的情况下,均选取表面处大小约为2 mm×3 mm×2 mm的试样。金相显微组织检测所用设备为ZEISS Observer.Z1m金相显微镜,参照GB/T 5168-2008和GB/T 6611-2008检测中选用的侵蚀剂为硝酸、氢氟酸和水的混合溶液。
2 结果及分析
2.1 组织与氢含量的关系
4种板材的表面金相组织如图1所示。由图1a和b可以看出,Ti70合金板材由等轴和拉长的α相以及晶间β相组成,以拉长的α相为主,等轴α相较少;由图1c和d可以看出,其组织与原始板材相近,由等轴和拉长α相以及晶间β相组成,不同的是此时等轴α相占据主导地位,且在此温度下试样组织已发生部分再结晶,晶间β相的形态与分布也开始发生变化 (图1d),晶界开始变粗,有平直化的趋势,晶间β相开始出现层状转变的迹象,但未见完全转变的区域;由图1e和f可以看出,Ti70合金板材由等轴α相和含片状α相的转变β相组成,在此温度退火时,温度达到α→β转变温度 (882 ℃[11]) 以上,试样显微组织已经发生明显变化,此温度与800 ℃退火后相比,部分等轴α转变为片状α,部分片状α转变为β,在图1e和f中已可见到小范围的呈片状转变组织;由图1g和h可以看出,Ti70合金板材由片状α相、晶界α相和晶间β相组成,在1000 ℃保温过程中,大部分α相转变为β相,但在空冷过程中,转变β相在共析温度以下又开始转变为α相,室温时的组织为魏氏组织。
图1 不同温度退火后的试样金相组织
将4种组织的试样加工成规格为50 mm×100 mm×6 mm的试样,在充氢前和充氢48 h后对各试板的氢含量进行检测,结果如表1所示。可以发现,在充氢前具有连续β相的4#试样氢含量最高,达到43 μg/g,2#、3#试样氢含量接近原始板材的氢含量,说明试样在热处理过程中已发生不同程度的吸氢,低于900 ℃热处理时,试样的吸氢不明显,但在高于900 ℃时,试样的吸氢量明显上升。4组试样充氢后,同样是4#试样的氢含量最高,达到1120 μg/g,其他3种组织试样的氢含量处在190~320 μg/g的范围内,证明当Ti70试样在相变温度以上发生相转变后,吸氢能力会显著增加。处于组织过渡状态的3#试样的氢含量高于1#和2#试样,4种试样充氢后吸氢量的顺序为:4#>3#>2#>1#,同时由图1可知,随着热处理温度的升高,β相的连续程度逐渐增大,连续程度的顺序为:4#>3#>2#>1#。可见,四种组织试样的吸氢量与β相连续程度呈正相关。另外,虽然试样在1000 ℃热处理过程中的吸氢量 (43 μg/g) 与充氢过程的吸氢量 (1120 μg/g) 相比可以忽略,但43 μg/g的氢含量足以对材料性能造成影响[12],热处理过程中并未人为引入H,H的来源仅可能是有机沾污或者潮湿的空气等,因此,Ti70合金在900 ℃以上进行热加工或者服役时,需要重点关注周围环境对其吸氢的影响。
表1 充氢前后不同组织Ti70试样的氢含量 (μg/g)
2.2 扩散方向与氢含量的关系
将规格为120 mm×150 mm×10 mm的板材充氢170 h后,分别沿轧制方向 (L) 与板厚方向 (S) 的截面取一系列大小相同的试样检测其相应位置的氢含量,取样方法如图2所示,其中图2a为沿试样L向由表面至心部连续取样,图2b为在10 mm厚试样上沿S向由上表面至下表面每下降1 mm取一个测氢试样,不同位置测氢样的氢含量数据如表2所示。
图2 不同位点处氢含量变化示意图
表2 不同位点处试样的氢含量 (μg/g)
对比L向中7个取样点的测试结果可见,表面的l1处氢含量最高,达到980 μg/g,次表面的l2试样的氢含量为55 μg/g,心部的l7处氢含量仅为13 μg/g,相当于未充氢板材的氢含量;对比S向中的八个取样点,同样可以发现表面s1、s8两处的氢含量最高,分别为194和242 μg/g,远高于其他部位,心部的s4、s5氢含量为原始氢含量,证明H主要集中在试样表面,氢含量由表面至心部迅速降低。L向试样中距表面2 mm处的l2样品氢含量为55 μg/g,而S向中距表面2 mm处的s3和s6样品氢含量分别为14和13 μg/g,远低于L向距表面相同距离处的氢含量,可见充氢过程中H在L向的扩散距离更长。
2.3 比表面积与氢含量的关系
为了研究比表面积 (表面积/体积) 与试样吸氢能力的关系,将板材加工为具有不同比表面积的系列试样,实验时,选用的充氢电流密度为10 mA/cm2,以正对碳棒的面作为参考面设置电流参数,试样经过相同充氢过程后 (65 h),进行氢含量测试,比表面积分别为0.36,0.55,0.76,1.00,1.19,1.30,1.34和1.69 m2/m3,试样充氢后的氢含量分别为:210,170,460,720,680,1170,960和1280 μg/g,图3为氢含量随比表面积不同而变化的示意图。
图3 氢含量随比表面积变化
图中的趋势线是利用最小二乘法对数据点进行回归分析得到的。从图3中可见,比表面积越大,氢含量越高。图中虽有个别比表面积较大试样的氢含量略低于比表面积较小的试样,但从散点图中拟合得到的趋势线来看,不影响整体规律,异常点的原因可能与取样点或者测样之前打磨掉的厚度有关。在2.2节中已经证明H的扩散主要集中在试样表面,越靠近心部氢含量越低,由此可见,取样点接近表面或者试样测试前打磨掉的厚度较薄,都会使氢含量较高,反之则会较低,但打磨厚度差异造成的误差相对较小,影响氢含量高低的因素主要还是比表面积。比表面积为样品表面积与体积的比值,比表面积越大,单位体积试样拥有的表面积则越大,在充氢过程中单位质量的Ti70合金接触到的电解液就会更多,得到氢的机会也会更大,氢含量也会更高。
3 讨论
原子在金属中的扩散可以通过多种方式进行,如体扩散和晶界扩散。一般情况下,对于原子半径较大、迁移能力较弱的原子,主要以晶界扩散为主;而对于原子半径较小、迁移能力较强的原子,主要以体扩散为主。H原子的原子半径极小,只有0.037 nm,迁移扩散能力极强,Ti70合金中的晶界面积又占比较小,所以即使存在晶界扩散,晶界的通道效应也会极弱,因此,H在Ti70合金中的扩散以体扩散为主。室温下,H原子以体扩散的方式向钛合金内部扩散时,如表3所示[13],β相所需的扩散激活能 (Q) 约为20~30 kJ/mol,小于α相所需的扩散激活能,此外,室温下氢在β相中的扩散系数 (D) 相较于α相中的要高出2~5个数量级,因此H原子会优先向β相中扩散。
表3 氢在Ti中的扩散系数[13]
在钛合金中,β相的晶体结构相较于α相的晶体结构在吸氢方面也具有一定优势[14,15]。α相在300 ℃时吸氢能力最强,但也仅达到约7% (原子分数),随着温度下降到室温,吸氢能力还会进一步减弱,室温时,α相中的最高氢含量约为0.04%;β相的吸氢能力非常强,温度高于600 ℃时,β相中的氢含量可高达50%,室温下的吸氢能力虽有所减弱,但仍远高于α相。二者吸氢能力的不同与其晶体结构有着密不可分的关系,α相为hcp结构,每个晶胞有12个四面体间隙和6个八面体间隙,β相为bcc结构,同样拥有12个四面体间隙和6个八面体间隙,但hcp中每个晶胞占有的原子数为6,是bcc中每个晶胞占有原子数的3倍,因此,相同个数的Ti原子所对应的四面体间隙与八面体间隙的数量,bcc为hcp的3倍。钛合金吸氢时,H倾向于占据四面体间隙,而相同数量Ti原子中,β相中的四面体间隙数量远多于α相中的,所以β相相较于α相的晶格结构在吸氢方面更有优势。除此之外,有一些金属的原子堆垛结构是一种较为“开放”的结构[16],这类金属的离子与原子的半径比与“正常”的金属相比异常的大,某些原子通过间隙机制在“开放”金属中可以迅速溶解并异常快速的扩散[17],α-Ti与β-Ti都属于这类金属,且β-Ti的bcc相对于α-Ti的hcp具有更加开放的结构[18]。α-Ti的hcp是一种最紧密堆积,如图4a所示,四面体间隙较少,当H原子处于hcp中的四面体间隙上时,原子可能跳跃的间隙不仅少,且跳跃所受的阻碍也较大。而H在bcc中跳跃时,则较为容易,如图4b所示,处于位点1处的H原子通过间隙机制向临近的四面体间隙位点处跳跃时,除了向体心处被Ti原子阻挡的间隙处跳跃时可能会比较困难,向相邻的间隙处跳跃时基本不受阻碍,所以氢在连续的β相中进行扩散较为容易,图4b中1→2→3→……→10→11为四面体间隙中的氢原子从一个晶体结构向另一个晶体结构扩散的可能路径。由此可见,少量β相即可显著影响近α型钛合金中H起作用的方式[2]。在近α型钛合金中β相是H的主要扩散通道,但在浓度梯度的作用下,H也会向α与β相的相界以及α相中扩散,但由于α相溶氢能力较差,H可能会更倾向于在α与β相的相界偏聚。
图4 四面体间隙在密排六方结构中的分布图及氢原子在体心立方结构中的扩散路径示意图
由2.2节可知,在相同充氢条件下,S向中H的扩散深度约为1 mm,L向中H的扩散深度约为2 mm,不同方向中H扩散深度的不同与沿不同方向上得到的显微组织有关。图5为实验所用试样的显微组织三维示意图,H沿L向扩散时,表层处的晶间β与H的扩散方向一致,分布在晶间的狭长β相相当于H的扩散通道,H沿此向扩散时受到阻碍较小;而H沿S向扩散时,扩散方向垂直于拉长的α和晶间β,H沿S向朝β相中扩散时需要转变为沿T或L向来实现,此外,在此向中拉长的α相呈层状堆叠分布,由于其较低的溶氢能力,在H的扩散道路上也会形成较大阻碍,因此,H在S向中的扩散较为困难,这与实验得到的数据一致,即扩散较为困难的S向扩散深度较小,扩散较为容易的L向扩散深度较大。由于检测手段有限,接近表层范围内的氢含量变化趋势无法测得,但根据Fick第二定律可知,原子或分子在物质内部进行扩散时,表面的浓度最高,浓度由表面至心部逐渐降低,因此,S、L两向中H的扩散在一定范围内可能呈现出逐渐降低的趋势。而在图2a和b中的氢含量发生骤降,可能是由于势垒的作用,经典力学认为,粒子运动如果遇到高于本身能量的势垒,在这个势垒的作用下粒子不可能运动到势垒的另一侧,所以H的扩散集中在表层附近,极有可能是由于H原子向内扩散,遇到高于自身的能量势垒。Ti70合金是一种近α合金,α相含量极高,可达85%以上,一旦富集的氢浓度等于可容纳氢的临界值,氢化物就会形成,氢化物的存在,对于向合金内部扩散的氢原子来说,就是一个不可逾越的势垒,除此之外,由于浓度梯度作用在α/β相界偏聚的高浓度氢原子,也可能是势垒形成的原因之一。
图5 Ti70合金试样的微观组织示意图
4 结论
(1) 随退火温度升高,Ti70试样的组织会发生变化,800 ℃左右试样发生部分再结晶;900 ℃时部分α相已转变为β相;1000 ℃时大部分α相已完全转变为β相,室温下的组织为魏氏组织。β相连续程度增加,试样的吸氢能力升高。
(2) 采用电化学充氢,氢含量从试样表面到心部迅速降低;H沿轧制方向的扩散能力明显大于板厚方向。
(3) 随着试样比表面积增大,吸氢量显著上升,表明单位体积对应的表面积越大吸氢能力越强。
参考文献
1 Gilbert J L, Mali S A. Medical implant corrosion: Electrochemistry at metallic biomaterial surfaces [A]. Eliaz N. Degradation of Implant Materials [M]. New York: Springer, 2012: 1
2 Chattoraj I. Stress corrosion cracking (SCC) and hydrogen-assisted cracking in titanium alloys [A]. Stress Corrosion Cracking: Theory and Practice [M]. Cambridge: Woodhead Publishing, 2011: 381
3 Chang Y H, Breen A J, Tarzimoghadam Z, et al. Characterizing solute hydrogen and hydrides in pure and alloyed titanium at the atomic scale [J]. Acta Mater., 2018, 150: 273
4 Xu J J, Yan K, Zhu Z Q, et al. Research on hydrogen brittleness of T225NG Ti-alloy [J]. China Mech. Eng., 2005, 16: 1018
4 徐济进, 严铿, 朱正强等. T225NG钛合金氢脆行为的研究 [J]. 中国机械工程, 2005, 16: 1018
5 Qu G J, Yu D H, Miao Y. Application of titanium and its alloys and hydrogen embrittlement corrosion and protection of titanium [J]. Chlor-Alkali Ind., 1996, (4): 33
5 曲广杰, 于德海, 苗艳. 钛与其合金的应用及钛的氢脆腐蚀与防护 [J]. 氯碱工业, 1996, (4): 33
6 Wang Z C. Hydrogen behavior during welding of titanium and titanium and titanium alloys [J]. Rare Met. Mater. Eng., 1986, (5): 11
6 王者昌. 钛及钛合金焊接时氢的行为 [J]. 稀有金属材料与工程, 1986, (5): 11
7 Lenning G A, Craighead C M, Jaffee R I. Constitution and mechanical properties of titanium-hydrogen alloys [J]. JOM, 1954, 6: 367
8 Kessler H D, Sherman R G, Sullivan J F. Hydrogen affects critical properties in commercial titanium [J]. JOM, 1955, 7: 242
9 Liu S, Wang Y G, Sun S. Effect of microstructure on room-temperature hydrogen absorption behavior of Ti-6Al-4V alloy [J]. Rare Met.Mater. Eng., 2017, 46: 2240
9 刘松, 王寅岗, 孙胜. Ti-6Al-4V钛合金组织对其室温吸氢行为的影响 [J]. 稀有金属材料与工程, 2017, 46: 2240
10 Yan L, Ramamurthy S, No?l J J, et al. Hydrogen absorption into alpha titanium in acidic solutions [J]. Electrochim. Acta, 2006, 52: 1169
11 Tal-Gutelmacher E, Eliezer D. The hydrogen embrittlement of titanium-based alloys [J]. JOM, 2005, 57(9): 46
12 He L. Review of corrosion protection and bio-fouling prevention for titanium alloy pipes [J]. Dev. Appl. Mater., 2017, 32(3): 121
12 何磊. 钛合金海水管路腐蚀与污损防护研究进展 [J]. 材料开发与应用, 2017, 32(3): 121
13 Chu W Y, Qiao L J, Li J X, et al. Hydogen Embrittlement and Stress Corrosion: A Typical System [M]. Beijing: Science Press, 2013: 966
13 褚武扬, 乔利杰, 李金许等. 氢脆和应力腐蚀: 典型体系 [M]. 北京: 科学出版社, 2013: 966
14 Tal-Gutelmacher E, Eliezer D. Hydrogen-assisted degradation of titanium based alloys [J]. Mater. Trans., 2004, 45: 1594
15 He X, Shen B L, Cao J L, et al. Effects of hydrogen on strength and plasticity of two types of new titanium alloys [J]. Rare Met. Mater. Eng., 2003, 32: 390
15 何晓, 沈保罗, 曹建玲等. 氢对两种新型钛合金强度和塑性的影响 [J]. 稀有金属材料与工程, 2003, 32: 390
16 Mishin Y, Herzig C. Diffusion in the Ti-Al system [J]. Acta Mater., 2000, 48: 589
17 Hood G M. Diffusion in α-Zr, HCP and open metals [J]. Defect Diffus. Forum, 1993, 95-98: 755
18 Mishin Y, Farkas D. Monte Carlo simulation of correlation effects in a random bcc alloy [J]. Philos. Mag., 1997, 75A: 201
免责声明:本网站所转载的文字、图片与视频资料版权归原创作者所有,如果涉及侵权,请第一时间联系本网删除。
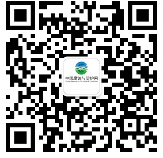
官方微信
《中国腐蚀与防护网电子期刊》征订启事
- 投稿联系:编辑部
- 电话:010-62316606-806
- 邮箱:fsfhzy666@163.com
- 中国腐蚀与防护网官方QQ群:140808414