摘要
构建了带破损点的剥离涂层管道腐蚀模拟实验装置,采用微电极技术研究交流干扰X80管线钢破损/剥离涂层下局部腐蚀行为及规律。结果表明:交流电干扰使涂层破损管线钢电位负向偏移;随交流电密度增大,X80钢的阳极溶解速率增大,腐蚀形态由均匀腐蚀逐渐向局部腐蚀转变;破损点处管线钢发生严重腐蚀,剥离区腐蚀程度稍有减缓;但施加100 A/m2交流电时,剥离区深处X80钢表面仍出现了较严重的点蚀坑。从交流干扰的整流效应、阳极反应不可逆性及交流电对钢/环境界面双电层结构影响等角度讨论了交流电干扰对涂层破损下管线钢腐蚀行为的影响。
关键词: 管道钢 ; 杂散电流 ; 防腐层 ; 阴极保护 ; 电干扰
随着我国高压/特高压输电线路、电气化铁路系统及油气管网的大规模建设,高压/特高压输电线路、电气化铁路等设施与埋地油气管道临近或并行情况越来越多。油气管道受杂散电流干扰以及由此引发的管线腐蚀及安全问题日益突出[1-3]。现代埋地管道防腐层绝缘性好,进入管道的杂散电流可以长距离传输后,从防腐层破损、剥落等缺陷处流出,局部腐蚀速率极大。例如,一条涂覆熔结环氧粉末 (FBE) 的X42钢管线21 km和500 kV高压交流输电线平行铺设,1 a后检测发现涂层破损处腐蚀速率高达10 mm/a[4]。三层聚乙烯 (PE) 防腐层在管道投产后短期内粘结失效的案例[5,6]近年也十分常见,一旦防腐层与管体失去粘结,产生阴极保护屏蔽,会导致一系列的点蚀、应力腐蚀和微生物腐蚀等[6],严重威胁管道运行安全。
交流杂散电流对高绝缘防腐层管道的影响复杂,国内外对交流干扰腐蚀进行了大量研究工作[7-14],结果表明,交流电干扰使钢的电位向更活泼方向偏移,加速管线钢的局部腐蚀[11];增大钝态电流密度,特别是交流电密度较高时,引发严重点蚀[12]。管线腐蚀程度随交流电流频率的降低而增强,频率也影响蚀坑形态、密度和钝态电流密度。管线交流干扰腐蚀影响因素众多,除了干扰强度、频率及阴极保护等因素外,还与管线涂层失效类型、形式、破损点大小等密切相关。例如,有文献调查表明,涂层绝缘性越好,电干扰倾向越大;管线的交流腐蚀强度随涂层破损点面积的减少而增强,破损点约6 cm2时腐蚀强度达最大[15]。在防腐层剥离情况下,管线钢的腐蚀和应力腐蚀的萌生和发展涉及众多过程,包括管线钢/溶液界面上的化学/电化学反应,物质在钢的表面和薄液层间的扩散,通过闭塞区的物质扩散和传质过程等,各种相关过程复杂,影响因素众多。如,有研究[8]表明在自然腐蚀条件下,封闭的涂层剥离区局部环境抑制管线均匀腐蚀过程:缝隙间隙下腐蚀主要发生在开放破损点处,尤其是拉伸试样,表面出现大量微裂纹,而封闭的剥离区内部腐蚀程度显著减缓。本工作构建了带破损点的剥离涂层管道腐蚀模拟实验装置,采用微电极技术电位测量、微观形貌等技术研究交流电干扰对剥离涂层X80管线钢的腐蚀行为影响,可为管线交流干扰腐蚀的评价指标和评价方法提供参考。
1 实验方法
1.1 管线钢和模拟土壤溶液
实验材料为API X80管线钢,其化学成分 (质量分数,%) 为:C 0.07,Mn 1.82,Si 0.19,P 0.007,S 0.023,Cr 0.026,Ni 0.17,Cu 0.020,Al 0.028,Mo 0.23,Ti 0.012,Nb 0.056,V 0.002,N 0.004,B 0.0001,Fe余量。实验前,所有试样用水磨砂纸逐级打磨至1000号,用丙酮和乙醇清洗后冷风吹干,干燥箱中保存备用。
实验介质为模拟涂层破损管线周围近中性土壤环境 (NS4溶液),其组成为:CaCl2 3.13 g/L,MgCl2 2.86 g/L,Na2CO3 2.98 g/L,NaCl 3.20 g/L,Na2SO4 4.00 g/L。实验前向模拟溶液中通入5%CO2+95%N2 (体积分数) 混合气体6 h调节溶液pH值至约6.8。
腐蚀电位测试采用10 mm×10 mm×5 mm的X80钢试样,预留10 mm×10 mm的工作面,在试样背部焊接导线并将除工作面外其余表面采用环氧树脂密封。
1.2 实验装置及方法
采用有机剥离 (PMMA) 板模拟3PE等屏蔽性剥离涂层,模拟剥离涂层缝隙实验装置如图1所示;模拟缝隙由PMMA、钢试样及矩形聚四氟乙烯 (PTFE) 垫片组装而成。缝隙尺寸250 mm×60 mm,缝隙厚度可由垫片调节,本研究采用1 mm的缝隙厚度,对应缝隙深厚比为250。PMMA板一端开10 mm×50 mm方口模拟防腐层破损点 (面积5 cm2),缝隙内环境通过该破损点与PMMA板上方储液槽中的本体土壤溶液连通,试样缝隙内外面积比为25.0。使用硅橡胶将缝隙内的独立试样电极粘到PMMA基板上。为模拟剥离防腐层下完整管道表面,PMMA基板试样间的空间由5块相同钢制成的辅助板填补,试样只有上侧面5 mm×60 mm的工作表面暴露于实验环境。实验过程中,所有钢试样和板材通过外部并行线连接。
图1 交流干扰管线钢剥离涂层下腐蚀模拟实验装置示意图
模拟缝隙实验装置封装前,试样工作面用金相砂纸逐级打磨至1000号,丙酮洗净,冷风吹干。实验开始时,为防止缝内存在气泡,缝内溶液用注射器注入,储液槽加注溶液后加盖密封。PMMA板上安装一系列毛细管盐桥以测量缝隙内各位置局部电位值。饱和甘汞电极 (SCE) 作为参比电极,辅助电极为储液槽中铂丝网。实验过程参见文献[5,16,17]。
交流干扰信号通过函数信号发生器施加于涂层破损点处,如图2所示。UTG-9000A函数信号发生器作为干扰电源,交流干扰信号为频率50 Hz的正弦波;大面积石墨电极作为辅助电极。实验采用的交流电流密度分别为0,20,50和100 A/m2。采用Fluke万用表和10 Ω标准电阻进行交流电流测量,参比电极为饱和甘汞电极 (SCE) ;电容用以防止电化学测试系统对交流电源产生干扰。
图2 涂层破损管线钢交流干扰施加及测试示意图
针对仅有破损点而没有剥离的防腐层失效情况,本工作同时进行了另外一组实验。取5 cm×10 cm X80钢试样由环氧树脂密封,仅暴露1 cm2的工作面模拟小面积涂层破损点。实验中,预先将试样浸泡一段时间使开路电位达到相对稳定,然后对试样施加交流电干扰约5 min,再断掉交流电干扰,测试施加交流电对试样电位的影响。
实验过程中,定期测量剥离区不同位置试样的局部电位。本工作中电位值除特别标明外均指相对于SCE参比电极的。实验结束后,用添加有缓蚀剂的盐酸清洗液 (500 mL HCl+500 mL去离子水+20 g六次甲基四胺) 去除腐蚀产物,依次用去离子水和无水乙醇清洗吹干,采用扫描电子显微镜 (SEM,XL30-FEG) 观察试样表面微观形貌。利用Rigaku-D/max-2500PC型X射线衍射仪 (XRD) 分析腐蚀产物。
2 结果与讨论
2.1 小面积涂层缺陷情况
暴露面积为1 cm2的X80管线钢施加不同电流密度交流干扰时的电位变化见图3。可见,无交流干扰时,X80钢的自腐蚀电位约为-700 mVSCE;交流电干扰对钢电位的影响较大,施加交流干扰瞬间X80钢的电位发生负向偏移;随所施加交流电流密度IAC增大,腐蚀电位负移量增大;IAC为10 A/m2时,自腐蚀电位下降至约-830 mVSCE;IAC为100 A/m2时,电位降至接近-860 mVSCE。几种条件下,断掉交流电干扰后,X80钢的电位迅速恢复至自腐蚀电位 (约-710 mVSCE)。断开前交流电密度越大,断开后的开路电位越正。这与大交流电密度下腐蚀严重,腐蚀产物相比较多,电极附近溶液、pH值改变较大有关。
图3 不同电流密度交流干扰下X80管线钢的腐蚀电位随时间的变化规律
由图3同时可以看出,交流电流干扰下,腐蚀电位随时间延长逐渐正移。这是由于交流电作用下试样阳极溶解加速,大量Fe2+溶出,致使腐蚀电位不断正移;但随着腐蚀产物对腐蚀反应的阻碍作用不断增强,腐蚀电位逐渐达到稳定。
2.2 剥离区局部环境
本实验条件下,防腐层破损点面积为5 cm2。图4a和b分别为交流电流密度为20和100 A/m2时剥离涂层下X80钢局部电位随时间的变化情况。图5示出了交流电干扰时X80钢的局部电位沿剥离区缝隙的分布情况。可见,无交流干扰时,X80钢在本实验环境中的自腐蚀电位约为-710 mVSCE;由图4a可见,施加20 A/m2的交流电后,破损点试样处电位很快降至约-750 mVSCE,负向偏移约40 mV;实验周期的前10 h,缝内各位置试样电位随时间逐渐负移,而后,各位置试样电位逐渐正向偏移,趋于体系的原始开路电位。施加交流干扰的整个实验过程中,破损点处试样电位始终为最负,随缝隙深度增大电位正移,剥离区缝隙尖端处试样电位最正。实验72 h后断掉交流干扰,涂层破损点处和剥离区245 mm处电位产生明显的正向跳跃。
图4 交流干扰电流密度分别为20和100 A/m2时剥离涂层下X80钢局部电位随时间的变化
图5 交流干扰电流密度分别为20和100 A/m2时破损防腐层下X80钢局部电位分布
由图4b可见,施加100 A/m2的交流电后,破损点处电位很快降至约-0.80 VSCE,负向偏移约60 mV。实验周期前10 h,破损点处电位大幅正向偏移,24 h后升至-735 mV,已经接近剥离区45 mm处试样的电位值,此过程中缝隙内各位置电位变化平缓,缝隙内各位置电位差异逐渐缩小。施加交流电24 h后,各位置试样电位逐渐正向偏移至高于体系的原始开路电位 (约-0.72 VSCE)。实验72 h断掉交流干扰后,各位置试样电位均产生明显的正向跳跃,特别是涂层破损点处电位由-711 mV跳至-650 mV。比较图4a和b可见,交流干扰水平为20和100 A/m2条件下,剥离涂层下X80钢局部电位随时间的变化规律大体一致。
2.3 腐蚀形貌观察
在20 A/m2交流电干扰下实验72 h后,涂层剥离区各位置X80钢试样的表面腐蚀产物形貌如图6所示。可以看出,试样表面腐蚀产物疏松,电流密度较大时,试样表面形成大块腐蚀产物结痂,XRD分析结痂的成份主要为γ-FeOOH和Fe3O4。大块腐蚀产物结痂下为圆形点蚀坑。现场调查表明,受交流电干扰管线涂层破损处常见由腐蚀产物和土壤混合而成的结痂,结痂的面积大于涂层破损面积,降低了干扰电流的扩散电阻。
图6 交流电流密度为20 A/m2干扰下涂层破损点及剥离区不同位置X80钢试样实验72 h后表面腐蚀产物形貌
图7为0,20和100 A/m2交流电作用下X80钢腐蚀72 h后的形貌。无交流干扰时,X80钢表面腐蚀均较轻微,破损点处试样发生均匀腐蚀,而剥离区试样存在少量轻微点蚀;交流电干扰实验组中试样表面存在均匀腐蚀、环状腐蚀和点蚀等腐蚀形式。球形凹坑为碳钢交流腐蚀的典型形状。交流电干扰为20 A/m2时,X80钢表面发生均匀腐蚀和点蚀;100 A/m2交流电流密度时,破损点和剥离区各位置试样表面均出现了大而深的点蚀坑。随交流干扰电流密度增大,腐蚀形态由均匀腐蚀向局部腐蚀转变,蚀坑密度、数量及腐蚀面积比均随电流密度的增加而增大。存在交流电干扰时,剥离区腐蚀程度稍有减缓,但施加100 A/m2交流电时,剥离区深处X80钢表面仍出现了严重的点蚀坑。
图7 不同交流电流密度干扰下涂层破损点及剥离区不同位置X80钢试样腐蚀72 h后的表面腐蚀产物和腐蚀形貌
2.4 分析讨论
存在交流电干扰时,涂层破损点X80管线钢电位负向偏移,随交流电密度增大,X80钢的阳极溶解速率增大,腐蚀形态由均匀腐蚀逐渐向局部腐蚀转变。交流电干扰下X80管线钢最严重的腐蚀区域出现在开放破损点处,剥离区腐蚀程度稍有减缓,但施加100 A/m2交流电时,剥离区深处X80钢表面仍出现了较严重的点蚀坑,这与交流电在剥离区缝隙内金属表面的整流效应产生的净阳极电流有关[18]。
交流干扰条件下,交流电正半周时对试样起阳极极化作用,金属表面离子处于活性溶出状态,且溶出的阳离子加速向溶液中扩散;负半周时则促进了阴极反应,包括氧还原反应或H+还原反应,而不仅仅包括金属离子沉积反应;这样,在交流电正半周期产生的金属阳离子在交流电负半周期没有完全重新沉积,导致金属阳极极化产生的总电流和阴极极化产生的总电流不相等,产生了净阳极电流[18],对腐蚀电化学反应起到催化促发作用。同时,因为阳极反应不可逆,即金属在交流电正极半周发生的阳极反应在负半周内不完全可逆,从而改变了电极表面双电层的结构,进而影响腐蚀电化学行为。
阴极保护条件下,阴极电流穿透到缝隙的有效距离仅有数厘米[16],脉冲信号在剥离涂层下的穿透能力更强。剥离涂层下,交流电在缝隙内穿透的深度与直流电是否类似有待进一步研究。
3 结论
(1) 构建了涂层剥离管道交流电干扰腐蚀模拟实验装置,采用微电极技术研究交流干扰下X80管线钢剥离涂层下的局部腐蚀特征。
(2) 交流电干扰下X80钢表面电化学活性增强:交流电使管线钢电位负向偏移;随交流电密度增大,X80钢的阳极溶解速率增大,涂层破损点处腐蚀形态由均匀腐蚀逐渐向局部腐蚀转变。
(3) 交流电干扰下X80管线钢最严重的腐蚀区域出现在开放破损点处,剥离区腐蚀程度稍有减缓,但施加100 A/m2交流电时,剥离区深处X80钢表面仍出现了较严重的点蚀坑。
参考文献
[1] Hu S X, Lu M X, Du Y X, et al.New opinions about the AC corrosion of pipelines[J]. Corros. Prot., 2010, 31: 419(胡士信, 路民旭, 杜艳霞等. 管道交流腐蚀的新观点[J]. 腐蚀与防护, 2010, 31: 419)
[2] Li Z L, Sun Y F, Chen S K, et al.Influence of alternating current electrified railway stray current on buried pipelines[J]. Corros. Prot., 2011, 32: 177(李自力, 孙云峰, 陈绍凯等. 交流电气化铁路杂散电流对埋地管道电位影响规律[J]. 腐蚀与防护, 2011, 32: 177)
[3] Wang X H, Liu J Y, He R Y, et al.Disturbed corrosion of buried gas pipe-lines induced by rail traffic dynamic stray current[J]. Corros. Prot., 2010, 31: 193(王新华, 刘菊银, 何仁洋等. 轨道交通动态杂散电流对埋地管道的干扰腐蚀试验[J]. 腐蚀与防护, 2010, 31: 193)
[4] Hanson H R, Smart J.AC corrosion on a pipeline located in a HVAC utility corridor [A]. Corrosion 2004[C]. Houston, TX: NACEInternational, 2004
[5] Yan M C, Yang S, Xu J, et al.Stress corrosion cracking of X80 pipeline steel at coating defect in acidic soil[J]. Acta Metall. Sin., 2016, 52: 1133(闫茂成, 杨霜, 许进等. 酸性土壤中破损防腐层下X80管线钢的应力腐蚀行为[J]. 金属学报, 2016, 52: 1133)
[6] Zhao J, Luo P, Teng Y P, et al.Survey and analysis of field application of 3PE pipeline coating[J]. Pipeline Tech. Equip., 2008, (6): 41(赵君, 罗鹏, 滕延平等. 管道三层PE防腐层现场应用调查与分析[J]. 管道技术与设备, 2008, (6): 41)
[7] Bosch R W, Bogaerts W F.A theoretical study of AC-induced corrosion considering diffusion phenomena[J]. Corros. Sci., 1998, 40: 323
[8] Weng Y J, Wang N.Carbon steel corrosion induced by alternating current[J]. J. Chin. Soc. Corros. Prot., 2011, 31: 270(翁永基, 王宁. 碳钢交流电腐蚀机理的探讨[J]. 中国腐蚀与防护学报, 2011, 31: 270)
[9] Wan H X, Song D D, Liu Z Y, et al.Effect of alternating current on corrosion behavior of X80 pipeline steel in near-neutral environment[J]. Acta Metall. Sin., 2017, 53: 575(万红霞, 宋东东, 刘智勇等. 交流电对X80钢在近中性环境中腐蚀行为的影响[J]. 金属学报, 2017, 53: 575)
[10] Fu A Q, Cheng Y F.Effects of alternating current on corrosion of a coated pipeline steel in a chloride-containing carbonate/bicarbonate solution[J]. Corros. Sci., 2010, 52: 612
[11] Lalvani S B, Lin X.A revised model for predicting corrosion of materials induced by alternating voltages[J]. Corros. Sci., 1996, 38: 1709
[12] Goidanich S, Lazzari L, Ormellese M.AC corrosion. Part 2: parameters influencing corrosion rate[J]. Corros. Sci., 2010, 52: 916
[13] Jiang Z T, Du Y X, Dong L, et al.Effect of ac current on corrosion potential of Q235 steel[J]. Acta Metall. Sin., 2011, 47: 997(姜子涛, 杜艳霞, 董亮等. 交流电对Q235钢腐蚀电位的影响规律研究[J]. 金属学报, 2011, 47: 997)
[14] Yang Y, Li Z L, Wen C.Effects of alternating current on X70 steel morphology and electrochemical behavior[J]. Acta Metall. Sin., 2013, 49: 43(杨燕, 李自力, 文闯. 交流电对X70钢表面形态及电化学行为的影响[J]. 金属学报, 2013, 49: 43)
[15] Wakelin R G, Sheldon C.Investigation and mitigation of AC corrosion on a 300 MM natural gas pipeline [A]. Corrosion 2004[C]. New Orleans, Louisiana: NACE International, 2004
[16] Yan M C, Wang J Q, Ke W, et al.Effectiveness of cathodic protection under simulated disbonded coating on pipelines[J]. J. Chin. Soc. Corros. Prot., 2007, 27: 257(闫茂成, 王俭秋, 柯伟等. 埋地管线剥离覆盖层下阴极保护的有效性[J]. 中国腐蚀与防护学报, 2007, 27: 257)
[17] Yan M C, Wang J Q, Han E-H, et al.Local environment under simulated disbonded coating on steel pipelines in soil solution[J]. Corros. Sci., 2008, 50: 1331
[18] McCollum B, Ahlborn G H. The influence of frequency of alternating or infrequently reversed current on electrolytic corrosion[J]. J. Franklin Inst., 1916, 182: 108
免责声明:本网站所转载的文字、图片与视频资料版权归原创作者所有,如果涉及侵权,请第一时间联系本网删除。
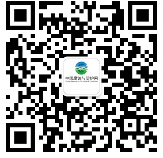
官方微信
《中国腐蚀与防护网电子期刊》征订启事
- 投稿联系:编辑部
- 电话:010-62316606-806
- 邮箱:fsfhzy666@163.com
- 中国腐蚀与防护网官方QQ群:140808414