起落架是航空器械下部用于起飞、降落或者滑行的支撑部位。飞机的起落架是飞机总体结构的重要部分,主要用于支撑机身和起降。它是飞机不可缺失的一部分;没有它,飞机便不能移动。
高速列车是我国战略性高端装备之一,高速车轮承受巨大动载荷和热负荷,易发生各类疲劳损伤,也是世界上公认的技术要求最高、生产难度最大的尖端车轮产品。
那么高速列车车轮用钢与飞机起落架用钢有何不同呢?
国内外高速列车车轮材料的研究
1 前言
在当下科学技术是第一生产力的启发下, 世界范围内铁路科学技术日新月异, 各国都投入了大量的人力物力财力对铁路运输进行大量研究。我国目前铁路也进行了大提速, 目标也朝着早上出发晚上归来, 晚上出发早上就可以到达方向发展。目前基本可以和发达国家相媲美甚至超过某些发达国家。高速列车的车轮作为列车不可或缺的一部分将直接影响列车的安全性和稳定性, 随着列车的大提速, 车轮踏面的剥离、裂损等对车轮的材料提出了很高的要求, 各国对车轮材料研究进行了大量研究并取得了一定的进展。
2 车轮及其损伤
2.1 车轮
车轮主要有在列车中所起的作用是: (1) 启动和制动列车运行; (2) 支撑列车的重量; (3) 列车在制动时车轮可以吸收摩擦热, 而且还可以散热。车轮从材料方面讲, 既要求高硬度、高强度和耐磨性, 因为在车轮制动时, 除与铁轨接触而产生摩擦而造成磨损和擦伤, 还会产生热裂纹。中高碳钢是各国生产车轮的主要材料 (如表1) , 里边还添加了点微量元素像Mn、Si等。
表1 我国辗钢客车轮标准与国外标准对比
对于车轮来说, 损伤是很常见的, 但是也分好几种类型, 像剥离、磨损塑性变形、车辆裂纹以及幅板裂纹等。踏面剥离是高速列车车轮常见损伤。研究结果认为, 造成这些损伤的因素是多方面的, 有材料的洁净度、车轮的使用环境、材料的性能因素相关。
3 铁路的高速化
铁路运输和其他运输方法相比有着明显的特征。首先, 铁路运输运量大, 节省燃料。其次, 对环境污染较少。所以世界范围内, 尤其发达国家都在大力发展本国铁路事业。1964年10月左右, 日本东海道新干线高速铁路通车最高时速达210km/h。在这之后, 德国的ICE、法国的TVG、西班牙的AVE以及英国的ART列车相继投放市场。1990年前后, 日本的新干线X300进行高速试验, 试验最高时速达到443km/h。
最近几年来, 我国高速铁路事业蓬勃发展, 在国际外交俨然成为一张耀眼名片, 在国内试验屡屡刷新纪录, 在国际市场上签回好多大单, 截止到2007年4月18日, 我国进行了第六次大提速。
4 国内外高速列车车轮新材料的开发
4.1 日本
日本新干线列车车轮用的材料为STY80的高碳钢, 其中含碳量为0.6%-0.75%, 在高速行驶时, 抗裂损性能不够。为了解决这个问题, 日本科研工作者又研发出了V2钢即SVTY75-ZR, 这种低碳加V钢成分见表2。
表2 V2钢车轮的规格
从表中数据可以看出V2钢将碳的含量由原来0.65%降到了0.55%。经过试验此种钢的拉伸特性与STY80没有明显变化, 但是可以明显提高断裂韧性和冲击特性。法国Valdunes公司于1998年又研制出了一种新的钢种, 强度最大值为886MP而RST的强度极限范围为860-980MP, 冲击功为24比RST的冲击功15要大许多。而且研究结果也得出, 一旦钢中含碳量达到0.42%, 车轮的的寿命就可以延长3年。
4.2 中国
随着列车速度一个一个被打破, 我国对车轮材料也进行了大量研究。2000年西安交通大学与马钢技术中心联合研制了微合金车轮。这种刚含碳量比原来刚种降低, 另外添加了合金元素, 并用V进行微合金化, 试验表明, 此种钢各项性能都优于原有钢种。
各种钢的化学成分
4.3 欧洲
欧洲很早就提出用低碳微合金材料作为用钢, 并且制定了标准碳的含量, 用于时速200km/h的车轮是1类钢像ER7和ERS, 这两类钢是被应用最广泛的。
5 结语
综上所述, 铁路运输的重要部件之一就是车轮, 但是近年来经济、社会、信息日新月异, 对解决车轮磨损提出的挑战屡屡创新高, 所以必须开发出一种质量过硬的车轮材料才是王道。
当然各国都在这方面进行研究, 而且都认为只有提高材料的韧性才有助于提高材料的抗损伤性能, 而提高材料韧性有必须适当降低材料的含碳量, 并且进行微合金化。这样在保证或者略微降低材料强度和硬度的情况下, 大幅度提高车轮材料的韧性, 从而可以提高车轮的抗损伤性能。这一思路对开发新材料是一种启发。
飞机起落架用超高强度钢应用现状及展望
作者:赵博,许广兴,贺飞,杨旭
沈阳飞机设计研究所,沈阳1 1 0 0 3 5
起落架是飞机在起飞和着陆过程中无可替代的装置,极大地影响飞机的使用与安全,但在飞机起飞后则不参与机体的结构和性能,对飞行无任何贡献。因此,起落架的设计思想和选材等方面与机体结构不同,希望得到最大的比强度和比刚度,并且体积尽可能小。钢具有高强度、良好的疲劳性能、耐磨性能、较低的裂纹扩展速率和加工工艺性能,同时钢制零件体积小、稳定性好,因此一直是设计制造起落架的主要用材,尤其是下沉速度较大的军用飞机的首选材料。当今世界上95% 以上的飞机起落架都是采用超高强度钢制造[1]。随着航空技术的发展和材料制造技术的不断进步,各类军用、民用飞机起落架越来越向轻量、长寿命、高可靠性方向发展。目前,世界上包括我国在内的航空业发达国家均已形成了起落架材料体系。现代飞机中,起落架用钢占全机用钢量的60% 以上,超高强度钢主要用于设计制造主承力构件和关键连接件:主承力构件有外筒、活塞杆、扭力臂、轮轴等;连接部件有转轴、扭力臂铰点连接轴等。
起落架的使用寿命考核指标是起降次数,现代飞机要求起落架的使用寿命和飞机的额定起降次数相同,即起落架与飞机同寿。起落架的首翻期不小于安全设计寿命的1/4。
本文介绍飞机起落架用钢的应用和研究现状,分析讨论国内外的应用差距及应用前景,指出我国飞机起落架用钢的发展方向。
1 飞机起落架用超高强度钢的发展和应用历程
飞机起落架用钢的发展过程与飞机设计思想、设计需求和材料制造技术的前进是同步的。起落架承受静载荷、动载荷以及重复载荷,核心设计思想是保证安全使用的前提下尽可能减轻其重量和缩小其尺寸,具体的设计原则不断完善进步。
(1 ) 早期飞机采用静强度设计,我国20世纪50年代飞机设计即强调静强度设计。结构的安全性主要通过选取适当的安全系数来保证,一般取材料的抗拉强度除以安全系数即为使用强度。起落架制造材料强调抗拉强度、屈服强度,并具有优良的塑性以及冲击韧性。起落架主承力构件主要由1175 MPa级高强度钢4130,30CrMnSiA等材料,经手工电弧焊等方法制造[2]。
(2) 随着各国采用静强度设计的飞机相继出疲劳破坏事故,在静强度基础上发展了对飞机疲劳强度的要求,即强调安全寿命设计。第二代战斗机开始全面采用安全寿命设计。安全寿命就是假定结构不存在初始裂纹或损伤。对制造材料S-N曲线,依据损伤累计理论,根据估算裂纹形成寿命或根据实验获得裂纹形成实验寿命,再用裂纹形成寿命除以分散系数即为使用寿命。起落架的安全使用寿命通常取起落架实验寿命的1/4 ~ 1/6。安全寿命设计尤其适用于结构复杂、造价高的起落架主承力结构,如起落架外筒、活塞杆、轮轴等。因此,此时起落架制造用钢不仅要求具有较高的强度和刚度,还要有优异的抗疲劳特性。较高的强度有利于获得较高的裂纹形成寿命,同时高强度/ 刚度可以减重和提高机体内空间利用率。随着超高强度钢技术的发展,超高强度结构钢制造大型飞机起落架主承力构件成为必然的选择。
起落架主承力件采用强度更高的1580~1760 MPa级超高强度钢 30CrMnSiNi2A,4330M ,4340等,采用焊接方法制造[2]。苏联主要采用30CrMnSiNi2A 钢,是在30CrMnSiA的基础上,加入1.4% ~1.8% 的N i和适量的Mn,增加了马氏体过饱和度、相变应变和位错密度,同时提高了马氏体基体的韧性,并降低点,提高淬透性。30CrMnSiNi2A 钢的 C 含量为0.27% ~ 0.34% ,容易产生焊接裂纹,因此需要焊前预热和焊后回火,多层焊时控制层间温度,焊接接头强度不低于母材的90% 。
随后相继开发了1800~1900MPa级的H11,D6AC,300M等超高强度钢,H11是最早的中合金二次硬化超高强度钢。300M钢是1952年美国国际镍公司在4340钢的基础上,添加了1.6% 的Si和0.1%的V,增加强度和回火抗力,提高回火温度而研制开发的1900 MPa级超高强度钢,与H11,D6AC,4340钢相比,具有更加优异的冲击性能和综合性能。因此,1964年美国C-5A大型军用运输机起落架首次使用300M 钢制造后,推广到各型飞机起落架,成为目前应用最广泛的起落架用超高强度钢,美国现役各型飞机90%以上的起落架采用300M钢制造。300M钢焊接性较低,所有300M钢制起落架均采用整体锻件设计制造。2 0世纪70年代,美国在300M 钢的基础上降低C含量,增加S含量,开发了HP31 0钢,当抗拉强度提高到2100MPa级时,韧性过低而未获应用[3]。
我国在20世纪60年代自主开发研制了无Ni少Cr型抗拉强度1860MPa的低合金超高强度钢40CrMnSiM〇VA(GC-4)钢,GC-4 钢具有良好的工艺性能和综合力学性能,可以采用焊接结构。在20世纪80年代,我国研制了双真空冶炼300M钢,与GC-4相比强度相当,但横纵向性能一致性、冲击性能、疲劳性能、抗应力腐蚀性能更加优异。由于采用精炼脱硫原材料,通过双真空冶炼,钢中S,P含量分别降低到0.002%~0.003%和0.005% ~0.008%,比GC-4钢降低1 倍以上,使材料疲劳裂纹形成寿命显著提高。在此基础上,根据双真空300M钢的特性,开发了起落架外筒和活塞杆锻件整体锻造、真空淬火、大长细比深孔加工、孔挤压强化、低氢脆镀镉钛表面处理等完整的抗疲劳制造技术体系,1990年300M钢制起落架首次应用,实现了起落架安全使用寿命与机体相同[2]。随后我国飞机起落架广泛采用300M钢制造。
( 3 )自1969年以来,美国F-lll,F-4等飞机虽然通过了全机疲劳实验,但在安全使用寿命期内仍旧发生了疲劳断裂事故,美国提出了飞机损伤容限设计思想,即考虑结构中存在的微小初始缺陷对使用寿命的影响,并于1974年颁布了飞机损伤容限设计要求MIL-A-83444。F-16是率先贯彻损伤容限设计要求的美国军机,但该设计要求指出损伤容限设计适用于飞机机体结构,不完全适用于起落架结构。我国1985年颁布的飞机强度设计规范中也规定,现阶段飞机设计应采用安全寿命与损伤容限相结合的设计原则。起落架主结构为单传力路线静定结构,如果强调损伤容限设计,那么必须设计成缓慢裂纹扩展结构,着重考虑起落架的疲劳损伤、断裂破坏和安全使用寿命,即用裂纹形成实验寿命确定使用寿命,用裂纹缓慢扩展实验寿命确定起落架的翻修周期。
此时对于起落架制造用钢提出了较小裂纹扩展速率和较高断裂韧度的新要求,强调材料抵抗裂纹失稳扩展的能力。高断裂韧度有利于获得高动态断裂韧度。由于起落架用超高强度钢一直强调强韧性匹配,而较高的强韧性匹配可以获得较小裂纹扩展速率和较高断裂韧度,所以以第3 代战斗机为代表的各型飞机起落架仍旧沿用之前的材料。苏联的苏-27等系列飞机起落架仍就采用30CrMiSiNi2A钢;法国的“幻影”、“协和号”等飞机起落架采用35NCD16钢[4];由于300M钢在所有低合金超高强度钢中具有小裂纹扩展速率和高断裂韧度,因此截至目前,以F-15,F-16,F-18A/B/C/D 型为代表的大部分军民用飞机起落架仍旧采用300M 钢。300M钢不属于损伤容限型材料,随着对疲劳断裂理解的深入,在原有指标基础上强调了断裂韧度的要求,不低于55MPa?m1/2。随着二次硬化高合金钢理论和高纯净冶炼技术的成熟,在H11钢、AF1410钢的技术基础上,美国在20世纪90年代初开发了1900MPa级的AerMetlOO超高强度合金钢[5],完成了飞机起落架用钢由低合金超高强度钢向高合金超高强度钢的跨越。AerMetlOO钢是第一款损伤容限型起落架用超高强度钢,断裂韧度、冲击性能、疲劳性能和耐腐蚀性能均显著优于300M钢:断裂韧度提高1倍以上,不低于110MPa?m1/2;冲击性能提高50% ;K=1时疲劳裂纹形成寿命提高20% ;K=2时疲劳裂纹形成寿命相当。美国的F-22和F-35飞机起落架为了实现不低于6000个起落的安全使用寿命,保证返修周期,采用AerMet100钢制造。虽然Aer-Met100钢具有优良的焊接性能,但为了保证Aer-Met100钢起落架的安全使用寿命,突出高合金钢的损伤容限优势,采用整体锻件设计制造。
我国突破了超纯净冶金、大锭型成分精确控制、大规格棒材开坯锻造等关键技术,完成了超大规格23Co14Nil2Cr3MoE(A-100)钢的研制,钢材纯净度国内首次达到99. 995%,确保断裂韧度等力学性能全面不低于Aermet100钢。起落架用钢强调强韧性匹配,均含有一定量薄膜状均匀分布的奥氏体,疲劳裂纹扩展速率差别不大,A-100钢和300M钢的疲劳裂纹扩展速率对比如图1 所示。并根据A-100钢损伤容限特性,突破了大型复杂模锻件成形成性、大型复杂零件精密热处理[6]、超音速火焰喷涂、复合喷丸强化[7]、低氢脆镀镉钛、低应力无烧蚀磨削[8]等关键技术,形成了起落架用高合金超高强度钢的抗疲劳制造技术体系。
18Ni类超高强度马氏体时效钢,虽然也可以通过二次强化达到1800 MPa以上,并具有较高的断裂韧度,但是这类超高强度钢由于采用金属间化合物强化,所以冲击性能和疲劳性能较低,缺口敏感性较高。高屈强比也不利于抑制裂纹扩展,因此这类超高强度钢没有用于起落架制造。
图1 A - 1 0 0 钢和3 0 0 M 钢疲劳裂纹扩展速率
Fig. 1 Fatigue crack growth rates of A -100 steel and 300M steel
(4)飞机结构开裂失效表明,不仅仅是载荷的作用,环境(腐蚀、摩擦/磨损等)也是影响结构开裂的重要因素,因此美国在1975年又提出了耐久性设计思想。耐久性就是结构在规定时间期限内,抵抗开裂(含i t 力腐蚀开裂等)、腐蚀、热退化、磨损和外界损伤的能力,即要求采用载荷-环境谱进行设计,经济寿命大于设计目标寿命s 我国在2 0 0 8年颁布的飞机强度设计规范中,也明确提出采用耐久性和损伤容限设计原则,在继承安全寿命设计的思想上,强调了经济寿命。
然而,对于起落架制造材料性能而言,耐久性的核心是强调材料耐环境的要求。 不仅仅考虑初始裂纹条件下的材料裂纹扩展性能,还要考虑在载荷和外界环境共同作用下的材料裂纹萌生和扩展性能。这种设计理念最直接体现在舰载机强调抗应力腐蚀设计,此时材料技术指标不再是简单考虑表面防护层下面基材初始裂纹的扩展速率和断裂韧度,而是在表面防护层破损后的材料抗应力腐蚀性能,包括腐蚀速率、应力腐蚀裂纹扩展速率、应力腐蚀断裂韧度、腐蚀疲劳等。目前舰载机发生的严重事故均为腐蚀导致,这也验证了舰载机起落架设计制造材料强调耐环境的必要性。美国F-18舰载机20世纪90年代初发生舰上300M 钢起落架腐蚀断裂事故,2002年F-14舰载机前起落架外筒发生腐蚀断裂,导致机毁人亡的灾难性事故的发生,造成156架该型飞机全面停飞[9];因此美国海军将300M 钢列为海上有限使用材料,提出用耐腐蚀更高的超高强度钢来制造舰载机起落架。美国20世纪90年代初发生F-18飞机300M钢起落架应力腐蚀断裂事故后,F-18E/F及F-35舰载型起落架均采用抗应力腐蚀性能更加优异的AerMet100钢制造[10]。AerMet100钢的KISCC是300M钢的2 倍以上,3.5% NaCl溶液中的应力腐蚀疲劳裂纹扩展速率降低50%以上,盐雾环境下AerMet100钢的腐蚀速率仅为300M 钢的10%。
2 飞机起落架用超高强度钢展望
同时提高超高强度钢的强韧性、损伤容限性能和耐久性对起落架设计的吸引力是毋庸置疑的,但是必须基于新的超高强度钢的强韧化理论,因此在一段时间内很难改变强度升高,塑性韧性降低的现状。结合飞机起落架的设计使用需求,起落架用超高强度钢有以下几个发展方向。
(1) 2200 MPa级以上超高强度钢
如果能将超高强度钢强度级别由现在的1900MPa级提高到2200 MPa级以上,即强度提高15%以上,对于起落架设计的减重效果还是较为明显的,对飞机设计师的吸引力更大。为此美国于2003年开始,公布了2100~2300MPa航空用超高强度钢的发展规划和技术方案,进一步研究高比强度超高强度钢。相继研发了 AerMet310钢(2100MPa级)和AerMet340钢(2300MPa级),但 AerMet310钢断裂韧度实测值为73MPa ?V1/2, AerMet340 钢断裂韧度实测值为37MPa ?V1/2[12-13];由于强韧性匹配较低,所以目前没有实际应用。国内目前也采用M2C、金属间化合物等沉淀强化理论,开展了2100~2300MPa超高强度钢的研制工作[14]。
2200 MPa级以上超高强度钢的应用关键是要在保证强度的前提下,塑性、韧性、疲劳性能、裂纹扩展速率和抗应力腐蚀等综合性能优于广泛应用的300M钢水平,才能体现出技术优势。
(2 ) 超高强度不锈钢
舰载机在整个寿命期内随舰船在海洋环境下执行任务,长期暴露于高温、高湿、高盐的严酷腐蚀环境中。除了 F-18和F-14舰载机起落架发生腐蚀断裂外,EA-6B“徘徊者”电子战飞机也发生过起落架腐蚀问题。因此,舰载机起落架要求采用抗应力腐蚀性能更高的超高强度钢设计制造。2002年美国QuesTek新技术有限责任公司承担美国防部战略环境研究与发展计划(SERDP)污染防止项目,该项目要求设计新型飞机起落架材料,开发研制出新型超高强度不锈钢Ferrium S53,用以代替AerMetlOO等超高强度钢[15]。FerriumS53抗拉强度达到1800MPa级,屈服强度1500 MPa级,应力腐蚀断裂韧度测试值不低于50 MPa ·m1/2。美国采用Ferrium S53钢试制了 A-10舰载攻击机起落架,进行了考核验证,2010年12月首次在T-38型教练机应用。
2002年以来,我国成功研制出新型的超高韧性与超高强度马氏体沉淀硬化不锈钢,典型代表是钢铁研究总院的F863钢、USS122G 钢和北京航空材料研究院的S280钢。这些钢是我国自主研发并具有自主知识产权的Cr-Ni-Co-Mo系马氏体时效不锈钢,其强度不低于1900MPa,屈服强度不低于1500MPa,断裂韧度不低于90MPa应力腐蚀断裂韧度测试值不低于70 MPa·m1/2[16]。
目前研发的超高强度不锈钢与AerMet100钢相比,屈强比和断裂韧度略低,应力腐蚀断裂韧度提高30%以上,盐雾环境下腐蚀速率降低10%以上。根据飞机结构设计强度规范要求,在使用载荷作用下,不超过材料的屈服强度;在设计载荷作用下不超过材料的抗拉强度。设计载荷除以使用载荷称为安全系数,通用的安全系数多为1.5。即要求起落架用钢的屈强比要大于0.67。超高强度不锈钢的屈强比为0.75~0.8,可以满足起落架设计要求。略低的屈服强度有利于通过塑性变形来降低裂纹扩展速率,提高裂纹临界长度,提高起落架的安全性;但是低的屈强比容易产生疲劳裂纹,不利于获得高的安全寿命。考虑到舰载机起落架的失效模式主要为应力腐蚀断裂,因此略低的断裂韧度不应该成为阻碍其应用的理由,进一步提高屈服强度更有吸引力。
综合考虑超高强度不锈钢的综合性能,可以作为下一代舰载飞机起落架的备选材料。
(3)低成本超高强度钢
低成本已经成为现代飞机设计制造中的一个重要指标,采用低成本、高性能材料是措施之一。降低起落架用超高强度钢成本的方法主要有2 种:一种是通过降低贵合金元素含量来降低成分成本,如降低Co等金属含量;另一种是通过非真空冶炼的方式,降低制造工序成本。
美国在2013年基于“材料基因组”技术开发了新型Co-Ni二次硬化超高强度钢— FerriumM54钢,目标是降低成本,代替AerMet100钢。FerriumM54钢通过降低Co含量,提高C,Mo含量,增加W,Nb等强化元素,来实现高强度、低成本。FerriumM54钢已经纳入到MMPDS手册,并获得美国汽车工程师学会颁发的材料规范AMS6516[10]。根据AMS 6516 和 AMS 6532(AerMet100钢规范)标准对比,二者的强度KIC相当,Ferrium M54钢的Kiscc显著提高。然而,实测值对比显示,二者总体性能相当,Ferrium M5 4 钢的KIC略低,KISCC略高,并不像规范中规定的那样存在较大的性能差距。目前试制了小350mm的棒材,美国采用Ferrium M54 钢试制了T-45舰载教练机拦阻钩杆和F-18E/F舰载机的拦阻钩头。从现有公布的资料可以认定,Ferrium M54钢是一款具有损伤容限特性、优良耐蚀性的低成本超高强度合金钢,具有较高的性价比,可以用于飞机起落架制造,但以目前公布的性能不足以全面代替AerMet100钢。
随着纯净化冶炼以及成分精确控制技术的提高,单真空冶炼的超高强度钢冲击性能、疲劳性能以及断裂韧度接近双真空冶炼的水平,但是成本大幅降低。这类超高强度钢可以用于制造下沉速度较低或者使用寿命较低的飞机起落架,如民用飞机、大型无人机等。
3 结束语
飞机起落架用钢已经形成了低合金超高强度钢和高合金超高强度钢并用的材料体系;基于各型超高强度钢的特性,建立了完整的抗疲劳制造技术体系。我国起落架用超高强度钢的研制和应用处于国际先进水平。300M钢和AerMet100钢目前应用最为广泛,一段时期内很难出现性能全面超越300M钢或AerMet100钢的同类起落架用超高强度钢。因此,起落架用超高强度钢的发展必须与各型飞机的特定需求相结合,才能发挥出最大的技术优势。
参考文献:
[ 1 ] 张慧萍,王崇勋,杜煦。飞机起落架用300M超高强度钢发展及研究现状[ J ] . 哈尔滨理工大学学报,2011,16(6) :73-76,(ZHANG H P,WANG C X,DU X. Aircraft landing gearwith the development of 300M ultra high strength steel andresearch[ J ]. Journal of Harbin University of Science andTechnology,2011 ,16(6) :73-76.)
[ 2 ] 刘天琦。飞机起落架用材发展[C] //大型飞机关键技术高层论坛暨中国航空学会2007年学术年会。深圳:中国航空学会,2007:1-6.
[ 3 ] MCEWEN L J. Combining strength and fracture toughness[J]. Metal Progress, 1975(3) :52-53.
[ 4 ] 康福伟,孙汝苇,张启凤。热处理工艺对35NCD16合金 钢组织和性能的影响[ J ] . 哈尔滨理工大学学报,2014,19(3) :10-12.( KANG F W,SUN R W,ZHANG Q F. Effects of heat treatment on microstructures and mechanical properties of 35NCD16 alloy steel [ J ]. Journal of Harbin University of Science and Technology,2014,19(3) :10-12.)
[ 5 ] 赵振业。超高强度钢中二次硬化现象研究[ J ] .航空材料学报,2002,22(4) :46-55.( ZHAO Z Y. Studying status on the secondary hardening phenomenon in ultra-high strength steels [ J ]. Journal ofAeronautical Materials,2002,22(4) :46-55.)
[ 6 ] 贺亚勇,赵勇。起落架用A -100钢热处理力学性能质量控制研究[ J ] .新技术新工艺,2016(6) :79-82.(HE Y Y,ZHA0 Y. Research on quality control of the aircraft landing gear A-100 heat treatment[ J ]. New Technology& New Process,2016(6) :79-82.)
[ 7 ] 赵勇,李博。A100钢零件复合喷丸工艺及质量控制研究[ J ] .新技术新工艺,2015(5) :147-149.(ZHAO Y, LI B. Research on compound shot peening process and quality control of A100 steel parts [ J ]. New Technology & New Process,2015(5) :147-149.)
[ 8 ] 樊建勋。AerMetlOO超高强度钢磨削工艺优化方法研究[ J ] .装备制造技术,2015(8) :191-193.( FAN J X. Research on the optimization method of Aer-MetlOO ultra high strength steel grinding process [ J ]. EquipmentManufacturing Technology,2015(8) :191-193.)
[ 9 ] 叶广宁,陈跃良。腐蚀和疲劳对飞机结构的挑战及解决思路[J ].航空工程进展,2011,2 (1) :67-69.(YE G N,CHEN Y L. Challenges and countermeasure investigation of corrosion and fatigue on aircraft structures[J ]. Advances in Aeronautical Science and Engineering,2011,2(1) :67-69.)
[10]赵振业,李春志,李志,等。一种超高强度不锈钢超细化组织TEM研究[J] .航空材料学报,2005,25 (2) : 1( ZHAO Z Y, LI C Z, LI Z^et al. Observation of the microstructure in an ultra-high strength and high toughness stainless steel [ J ]. Journal of Aeronautical Materials,2005,25(2) :1A. )
[11] 李松梅,吴凌飞,刘建华,等。应力比和腐蚀环境对超高强度钢AerMetlOO疲劳裂纹扩展的影响[J ] .航空材料学报,2014,34(3) :74-80.( LI S M, WU L F , LIU J H, al. Effect of load ratio and corrosion on fatigue behavior of AerMetlOO ultrahigh strength steel[ J ] . Journal of Aeronautical Materials,2014,34(3) :74-80.)
[12] 王飞。新型二次硬化钢相变组织与强韧性内在关系研究[D ].昆明:昆明理工大学,2016:3-7.( WANG F. Research on the internal relations between change organization and strong-toughness of new secondary- hardening ultra-high strength steel [ D ]. Kunming :Kunming University of Science and Technology, 2016:3-7.)
[13] 胡春东,孟利,董瀚。超高强度钢的研究进展[ J ] .材料热处理学报,2016,37(11) :178-182.( HU C D,MENG L,D0NG H. Research and development of ultra-high strength steels [ J ]. Transactions of Materialsand Heat Treatment,2016,37( 11) :178-182.)
[14] 吴迪,厉勇,王春旭,等。2200MPa级二次硬化型超高强度钢析出相及力学性能[J] . 钢铁,2016,51 ( 8) :60-63.(WU D,LI Y, WANG C \ ,e t al. Precipitates and mechanical properties of 2200MPa secondary-hardening ultrahigh strength steel [ J ]. Iron & Steel, 201 6 ,51 ( 8 ) :60-63.)
[15] 杨志勇,刘振宝,梁剑雄,等。马氏体时效不锈钢的发展[ J ].材料热处理学报,2008,29 (4 ) : 1 -5.(Y A N G Z Y , L I U Z B ,L IA N G ] X,et al. D evelopm ent of m araging stainless ste e l[ J ]. Transactions o f M a terials and H eat T re a tm e n t,2008 ,29(4) :l -5.)
[16]梁剑雄,刘振宝,杨志勇。高强不锈钢的发展与应用技术[ J ] . 宇航材料工艺,2013(3) :1-10.(LIANG J X,LIU Z B,YANG Z Y. Development and application of high strength stainless steel [ J ]. Aerospace Materials & Technology,2 0 1 3 ( 3 ) : 1 - 1 0 .)
免责声明:本网站所转载的文字、图片与视频资料版权归原创作者所有,如果涉及侵权,请第一时间联系本网删除。
相关文章
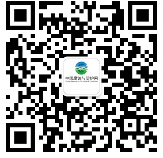
官方微信
《中国腐蚀与防护网电子期刊》征订启事
- 投稿联系:编辑部
- 电话:010-62316606-806
- 邮箱:fsfhzy666@163.com
- 中国腐蚀与防护网官方QQ群:140808414
点击排行
PPT新闻
“海洋金属”——钛合金在舰船的
点击数:7426
腐蚀与“海上丝绸之路”
点击数:5955