摘要:主要综述了海洋环境抗磨蚀防护涂层及技术的发展现状,对比了喷涂、高能束表面改性、物理气相沉积(Physical vapor deposition, PVD)三种常用技术的优劣势,并归纳了不同涂层在海水磨蚀条件下的磨损率和腐蚀电流密度,发现PVD 制备的氮/碳基涂层呈现出更优的耐摩擦防腐蚀性能。进一步对海洋环境氮基与碳基抗磨蚀防护涂层的研究成果进行了重点阐述,探讨了组分、过渡层以及多层结构设计等对涂层微结构、力学及磨蚀性能的影响,剖析了涂层在海水磨蚀环境中的失效分析方法和损伤机理。最后,对海洋抗磨蚀防护涂层的未来发展方向进行了思考与展望。
关键词:海洋环境;物理气相沉积;氮基涂层;碳基涂层;磨蚀性能;失效机理
海洋战略是关系民族生存发展和国家兴衰安危的国家战略,党的十九大报告在实施区域协调发展战略中明确指出:“坚持陆海统筹,加快建设海洋强国” [1]。海洋工程装备是海洋经济发展的基础,特别是随着以南海为主的海洋重大战略工程实施,发展先进海洋工程装备和高技术船舶成为海洋开发的重点突破领域。船舶推进器轴承、潜艇浮力调节系统、水下机器人关节、海水液压系统柱塞泵、深海钻井升沉补偿装置等海工装备关键运动部件,不仅面临严重海洋腐蚀环境,其工作时还面临高静水压、高盐腐蚀等苛刻环境,这使材料服役性能极易退化失效(见图1)[2-6],严重影响海洋工程装备的使用寿命和运行稳定性,甚至可能引起灾难性事故。设计和发展高性能海洋环境抗磨蚀防护材料与技术,已成为材料科学与海洋学科领域的研究交叉前沿。
图1 海洋环境中摩擦部件面临的威胁[2-6]
鉴于海洋强腐蚀性环境特点,通常选择具有良好耐蚀性的合金材料作为海工装备零部件材料,如304、316L、904L 不锈钢以及钛合金等[7-10]。这些材料在作为摩擦运动部件时,面临更严重的磨损和腐蚀交互加剧失效的问题。为此,一系列高硬度的氧化铝、氮化硅、Ti(C,N)基等陶瓷材料也被应用在海洋环境摩擦部件中[11-13]。然而,在交变载荷工况下,陶瓷材料容易发生脆性断裂,尤其在柱塞、水润滑轴承等高精度装配的摩擦副部件应用中,脱落的硬质基体颗粒会进一步加剧磨损失效。
针对上述问题,一般有两种解决途径:一是通过加入碳纤维、石墨等优化基体材料[14-15];二是通过高值化和多功能化的表面工程技术,赋予基体材料更为优异的强化改性耐磨蚀润滑防护等性能。其中,在基材表面涂镀防护涂层,不仅可有效调节和控制运动部件的表面/界面行为,而且能够在不损伤基体固有特性的同时,大幅改善其防护性能,并延长使用寿命。本文主要总结了近年来海洋环境中抗磨蚀防护涂层材料与技术的发展现状,重点介绍了氮基与碳基涂层为代表的抗磨蚀涂层材料的研究进展,归纳了涂层的磨蚀失效机制,并对未来的发展方向进行了思考和展望。
1 海洋环境中耐磨蚀涂层的制备技术
目前,抗磨蚀涂层的制备技术主要包括喷涂、高能束表面改性、物理气相沉积( Physical vapordeposition, PVD)技术,不同技术制备的涂层性能各异。其中,喷涂技术涉及热喷涂、冷喷涂、等离子体喷涂和火焰喷涂等[16-19]。该技术利用喷涂枪将涂层粉末或熔融后的涂层材料喷射在基体表面,具有制备技术简单、沉积速度快、适用基材广的优势,涂层具有较好的摩擦磨损性能,但表面粗糙,且孔隙率较大(见图2a)[16]。高能束表面改性技术是利用激光束、离子束或电子束直接作用于基体,改变其表面的成分和结构。三种高能束均可提高基体的耐腐蚀和耐磨损性能[20-23],但激光束和电子束表面改性的涂层大面积效率受限,且涂层表面有大颗粒(见图2b、c),直接影响其摩擦性能[24-25],而离子束注入的厚度较浅,保护时效短。
PVD 方法主要包含电弧离子镀与磁控溅射技术[26-27]。电弧离子镀是通过在引弧针上通入大电流,实现气体分子电离,并点燃弧源,产生弧光放电,阴极弧靶产生大量弧斑,将阴极材料蒸发离化,并与反应气体离子在电场作用下沉积于样品表面[28]。其特点是高电流、高离化率、沉积速率快,所制备的涂层均匀,厚度大,膜基结合力高,耐磨性优异[29]。磁控溅射则是利用辉光放电,使氩气电离,靶材原子被氩离子轰击溅射至腔体内,在电场作用下沉积在基体表面。与喷涂和高能束改性相比,PVD 有以下优势:沉积过程在真空条件下进行,制备的涂层杂质少;辉光放电、弧光放电形成低温等离子体,使原料激发为离子和高能中性原子,涂层更加致密;控制制备参数能改变沉积厚度,可从多个原子层到数十微米,调控范围宽,更适合作为磨蚀工况下需要精准控制厚度的精密运动配副和工件材料的保护涂层[30-31]。
图 2 Zn/15Al 涂层(喷涂)、Ti-Al-TiB2 涂层(激光熔覆)以及Ti/SiC 涂层(高能电子束辐照)的表/截面形貌[16,24-25]
考虑在海洋严苛环境下,摩擦配副的失效主要源于腐蚀和磨损交互及耦合加剧的磨蚀失效,综合对比了近年来报道的海洋或模拟海水环境中典型抗磨蚀涂层的腐蚀电流密度和磨损率,如图3 所示。从图3中可以看出,与陶瓷和金属基复合涂层相比,氮/碳基涂层均具有较低的腐蚀电流密度和磨损率,表明PVD 技术制备的氮基/碳基涂层具有优异的耐磨耐腐蚀性,是未来发展阀门、柱塞、轴承等海洋装备运动配副表面防护涂层的理想选择。
Green area is the coatings prepared by spraying technology, yellow area is the coatings prepared by laser cladding technology, blue area is thenitrogen-based coatings prepared by PVD, and red area is the carbon-based coatings prepared by PVD
图3 抗磨蚀涂层在海水环境下磨损率和腐蚀电流密度比较[17,19,32-43]
2 氮基涂层抗海水磨蚀性能研究进展
氮基涂层包括过渡金属氮化物及其二元、三元、多元衍生物,如CrN、TiN、CrSiN 等。常见氮基抗磨蚀防护涂层以氮化钛和氮化铬化合物系列为主。由于Ti 和Cr 元素可以自发形成致密的钝化膜,因此涂层常呈现高硬度和优异的耐磨耐腐蚀性[44-47]。氮化物涂层在刀具领域研究始于20 世纪70 年代,相关材料基础理论和工程应用等方面研究相对成熟。下面首先从组分及多层结构两方面,介绍氮基涂层在海洋磨蚀防护方面的研究进展。
2.1 组分对氮基涂层磨蚀性能的影响
针对传统二元氮基涂层,单磊等[48]使用多弧离子镀制备了TiN 和CrN 涂层。通过对比研究发现,TiN择优取向生长更明显,CrN 涂层则没有体现择优取向,且柱状晶特征不明显,结构更加致密,耐蚀性能更优。但是由于CrN 沉积过程有大颗粒贯穿,在摩擦过程中,极易出现局部剥落和硬质磨粒磨损。因此,制备无择优取向且结构致密的涂层,是工艺过程中重要的调控方向之一。Shan 等[49]还通过控制氮气流量制备了CrNx 涂层,研究其在海水中的摩擦性能。研究发现,只有CrN 或Cr2N 相的涂层磨蚀坑更大,而含有Cr2N 和CrN 两相的涂层更加致密,其共同存在能抑制裂纹扩展,说明不同相含量的调控也对涂层性能具有重要影响。此外,Chen 等[50]研究了CrN 涂层在3.5% NaCl 溶液中的磨蚀失效行为。研究结果表明,摩擦后的涂层出现了分层失效和大量交叉裂纹,主要源于CrN 涂层具有较低的韧性。
Ni 元素由于具有良好的韧性,被用于改善过渡金属氮化物的硬脆性。Wo 等[51]使用磁控溅射技术,在工具钢基体上制备了不同Ni 含量(原子数分数高达47%)的CrNiN 涂层,对其力学性能和变形进行了研究。测试结果表明,随着Ni 含量的增多,涂层的1/(HE2)值增大了2~3 倍,代表其抵抗裂纹的阻力增大。同时,涂层塑性变形所需的能量Ep 值随着Ni含量的增加而增大,表明Ni 的加入提高了涂层的韧性。在二元氮基涂层中,添加其他非金属或金属元素也是提高其耐磨蚀性能的有效途径[52-55]。例如,掺杂C 元素可以细化晶粒,降低摩擦系数,提高抗磨损性[56-57];Si 元素也有细化晶粒的作用,同时对涂层有一定的增韧作用,并且在水环境中能改善涂层的润滑性能[58-59];Al 元素掺杂可提高涂层硬度和抗氧化性[60-61]。Wang 等[57]使用磁控溅射在CrN 涂层中掺入适量C 元素,涂层形貌更加光滑,摩擦系数由0.272左右降至0.193,结合力也由22.5 N 上升至26 N,但过多的C 掺入会使硬度大幅下降。Lee 等[62]利用磁控溅射制备了CrSiN 涂层,发现在CrN 中掺杂Si 元素后,抑制了Cr2N 的(111)晶面生长,且Si 在TiN 和CrN 涂层中以无定形态存在,使涂层结构趋于非晶化,变得致密,并且有细化晶粒的效果[55,63]。单磊等[52]利用多弧离子镀在CrN 涂层中添加金属Al,得到了CrAlN 腐蚀电流密度(1.5×10–7 A/cm2)比CrN 涂层小的结果。其原因推测为,海水易通过CrN 涂层中的晶界间隙接触并腐蚀基体,而CrAlN 中形成了AlN相,其与CrAlN 相竞相生长,可以一定程度上阻碍柱状晶的生长。从图4 可以看出,CrAlN 晶粒小,结构更致密,在一定程度提高了涂层的耐腐蚀性能。此外,AlN 相可与水发生反应,生成Al2O3 颗粒,在摩擦过程中具有润滑作用,降低了涂层的磨损率。
图 4 CrN 和CrAlN 涂层的截面形貌[52]
此外,通过Si、C、B、Mo 等元素的多元掺杂,也可以提高涂层的综合性能[64]。Cai 等[65]使用等离子体增强磁控溅射在CrN 涂层中掺杂Si 和C 元素,研究其对涂层微结构和腐蚀性能的影响。结果表明,适量掺杂Si 和C 元素后,涂层孔隙率(0.000 68)比CrN(0.0025)降低1 个数量级,且极化电阻比CrN高2 倍,代表其耐腐蚀性能较好。在CrSiCN 涂层中进一步引入Mo 元素,可以形成CrN、Mo2N 相和(Cr,Mo)N 固溶体,分散在SiNx、Si-C-N 和a-C 非晶基质的结构中。Fu 等[36]研究了不同Mo 含量对CrSiCN 涂层摩擦腐蚀性能的影响。结果表明,除Cr元素,Mo 元素也可以形成致密的MoO3 钝化膜,阻止海水的渗透。Mo 含量较少时,形成的钝化膜保护能力不足;Mo 含量过多,引起钝化膜的应力分布不均匀,导致表面产生了许多微裂纹,且涂层结构变疏松,硬度和韧性下降。当Mo 含量为10.1%(原子数分数,下同)时,CrMoSiCN 腐蚀电流密度最低,为2.57×10–8 A/cm2,摩擦后的涂层磨损率也最低,涂层具有良好的抗磨蚀特性,如图5 所示。
2.2 多层设计对氮基涂层磨蚀性能的影响
上述研究表明,磨损过程中造成的裂纹或者涂层本身存在贯穿性缺陷,会造成海水的渗透,加速涂层或基体的腐蚀。多层结构设计可以有效地阻止贯穿性缺陷,防止或减缓腐蚀介质到达基体,是提高涂层磨蚀防护性能的有效技术途径。
王永欣等[66]使用电弧离子镀制备了多层Cr/CrCN纳米涂层(见图6a),并对比了多层Cr/CrCN、单层CrN 和CrCN 的力学和耐磨蚀性能。发现Cr/CrCN 涂层具有最高韧性和结合强度,腐蚀电流密度最小,为1.75×10–5 A/cm2,分别比单层CrN 和CrCN 降低79%和65%。涂层中包含的硬质Cr-C 相和摩擦过程中形成的石墨润滑相能有效协同,提高涂层的抗磨蚀性能和润滑性能。除此之外,他们还对比了双层和多层Cr/CrxN 涂层的结构设计对涂层耐磨蚀性能的影响[41]。如图6b 所示的截面形貌,多层Cr/CrxN 涂层结构更加平整、致密。多层涂层由于增加了横向界面,具有更好的阻隔效应,抑制了涂层在腐蚀和磨蚀工况下的电化学腐蚀。Ma 等[67]使用磁控溅射制备了CrN/AlN纳米多层涂层(见图6c),并对比了多层和单层CrN的耐磨蚀性能。发现在磨蚀阶段,多层CrN 的开路电位最高为–0.19 V,且由于CrN/AlN 具有较高硬度和较好耐腐蚀性,在外加–0.19 V(vs. OCP)电压条件下,涂层的总损耗量比单层CrN 降低了30%,因此更适合作为海水中的耐磨蚀防护涂层,如图7所示。
图5 海水中不同Mo 含量CrMoSiCN 涂层的极化曲线和磨损体积[36]
图 6 CrN/CrCN 涂层结构、Cr/CrxN 涂层截面SEM 以及CrN/AlN 涂层截面TEM[41,66-67]
图 7 CrN 和CrN/AlN 纳米多层膜在海水中摩擦的极化曲线[67]
2.3 小结
对于氮基涂层来说,通过组分、结构调控,提高结构致密度,减少腐蚀介质渗透,可以改善其抗磨蚀性能。其本质原因是由于钝化膜的防护作用,使其在海水常压环境下表现出快速钝化耐腐蚀的同时,维持了涂层的良好耐磨损特性。在高压的海水环境中,腐蚀产物和腐蚀速度都与常压下明显不同。童辉等人[68]的研究表明,在高压环境中,阳极反应速度增大,导致生成的纯铝涂层钝化膜呈现疏松的状态,且点蚀倾向更加明显,更容易剥落。因此,深海环境下氮基涂层的钝化膜生成过程及点蚀形成机理,仍亟待研究。
3 碳基涂层抗海水磨蚀性能研究进展
在碳基涂层材料种类中,类金刚石碳基(Diamond-likecarbon, DLC)涂层是一大类亚稳非晶态物质体系,主要由sp3 杂化键构成的金刚石结构和sp2 杂化键构成的石墨结构组成[69]。根据涂层中sp2/sp3 含量的多少,也被称为类石墨碳基涂层(Graphite-like carbon,GLC)和四面体非晶碳涂层(Tetrahedral amorphouscarbon, ta-C)。由于具有高硬度、高热导率、低介电常数、优异的耐摩擦磨损性能、良好的光学性能和生物相容性,DLC 涂层在航空航天、汽车工业、海工装备以及生物医学,特别在海工装备防护涂层等领域,具有广阔的应用前景[70-71]。近年来,随着海洋经济的快速发展,诸多学者就DLC 涂层在海洋环境中的腐蚀、磨蚀等行为也开展了研究[72-74]。但是由于DLC 涂层在沉积过程中,存在高能碳粒子轰击作用,涂层中常形成较大的残余应力,导致与基体结合力差,易剥落失效,防护寿命缩短。为解决上述问题,通过理论计算和实验验证相结合的方法,在DLC 涂层中引入过渡层、掺杂金属或非金属元素复合以及设计多层结构,成为提高涂层使用性能和寿命的发展方向。
3.1 过渡层及掺杂复合对碳基涂层磨蚀性能的影响
Cr、W、Ti 等碳化物形成相的过渡层可以有效缓解涂层和基体的性能突变,并且可以和DLC 涂层形成较强的共价键,是有效提高膜基结合强度并降低残余应力的过渡层元素体系[32,75]。孙丽丽等[76]使用线性离子束混合磁控溅射技术,制备了DLC、Cr/DLC 涂层,研究了涂层的微结构变化和力学性能。结果表明,相较无过渡层的DLC,增加Cr 过渡层(250 nm)的涂层的残余应力下降了将近50%,划痕测试结合力高于70 N,代表过渡层降低了由于膜基不匹配引起的内应力,同时提高了DLC 涂层的结合力。李蕾等[33]进一步分别选择了Cr、Ti、W 三种金属元素作为类石墨非晶碳膜(GLC)涂层与不锈钢基体间的过渡层。发现Cr 作为过渡层时,Cr 不仅可以插入碳基涂层,形成特殊“咬合”结构,提高结合力,而且电子能量损失谱测试表明,Cr/GLC 涂层中的sp2 键含量由界面到表面逐渐降低,如图8 所示,表明Cr 有强的催化sp2 碳键形成的作用,这使得摩擦过程中出现了较多可减摩润滑的石墨化转移膜,显著降低了涂层的摩擦系数和磨损率,使涂层在人工海水中展现了优异的低摩擦润滑性能。
图 8 Cr/GLC 涂层的TEM 和EELS 结果[33]
考虑 DLC 涂层高的残余压应力主要源于涂层中sp3 碳键态结构的高畸变,在非晶碳本征结构中,掺杂异质金属元素形成纳米复合结构,是调控DLC 涂层应力的有效途径[77-81]。笔者所在研究组[82-84]通过基于密度泛函理论的第一性原理计算和分子动力学模拟,结合深入的实验验证,首先多尺度研究了金属掺杂DLC 体系中的投影态密度、最高占有分子轨道电荷密度分布和分子轨道图等,发现掺杂金属主要与C原子间形成非键、反键、离子键、成键等4 类的结合特征。例如,当掺杂Sc~Cu 后,随3d 电子数的增加,成键特征变化规律为:成键(Sc, Ti)—非键(V, Cr, Mn,Fe)—反键(Co, Ni, Cu)。与纯DLC 体系相比,不同微量的金属元素掺杂均降低了键角结构畸变,降低涂层应力的同时,保持了涂层优异的高硬度和低摩擦特性。值得指出的是,掺入少量Ti 或W 时,能协同减小非晶碳结构中的键角和键长的高度扭曲,大幅降低应力;而掺入Cr 时,仅对键长扭曲降低有贡献,因此降低应力程度相较稍弱[85]。基于单一金属与碳的成键特征理论,研究团队还提出了以成键/离子键组合的Ti/Al、非键/反键组合的Cr/Cu 为代表的双元金属掺杂复合DLC 涂层优化体系,并采用线性离子束复合磁控溅射技术, 实现了不同含量配比的Ti/Al-DLC、Cr/Cu-DLC 涂层的高质量可控制备[77-79]。其中,对于Cr/Cu-DLC 涂层体系,溅射电流为2.2 A时,Cu、Cr 含量分别为11.88%和6.57%,涂层呈现较低的残余应力(0.89 GPa)[78]。除此之外,团队发现在Ti/Al-DLC 复合涂层体系中,当控制Ti 含量为2.5%±0.19%、Al 含量为9.21%,即Al/Ti 比为4.0 时,涂层的残余应力最低,为0.46 GPa,比纯DLC 降低了76%;在3.5% NaCl 模拟海水中,涂层的腐蚀电流密度仅为7.4×10–10 A/cm2,比316 不锈钢基体降低了2 个数量级,理论计算和实验结果相一致[77]。另外,刘孟奇等[86]制备了Cr 和WC 掺杂的DLC涂层,探究了涂层在海水中的磨蚀性能。结果表明,纯DLC 的H/E 和H3/E2 为0.104、0.186 GPa;掺杂Cr 后,H/E 和H3/E2 分别增加至0.108、0.189 GPa;掺杂WC 后,H/E 和H3/E2 分别增加至0.114、0.215GPa。三种涂层的结合力分别为18、29.2、39.6 N,WC/DLC 具有最优异的韧性和最强的结合力,且在海水中的磨损率最低,如图9 所示。由此可见,涂层的结合力和韧性与涂层的耐磨蚀性能联系紧密。除此以外,B 元素掺杂使DLC 涂层周围无定形碳网络松弛,降低了残余应力[87]。刘健等[37]提出掺杂适量(7.23%)B 元素,涂层的致密度增大,在海水中摩擦后的磨痕最浅,磨损率最小(见图10 所示),从而提升了涂层在人工海水中的磨蚀性能。除此之外,Xu 等[88]在DLC 涂层中掺杂Ti 和Al 两种元素,研究了不同Al/Ti 原子比对DLC 在海水中摩擦性能的影响。发现当Al/Ti 原子比为2.0 时,涂层具有最低的磨损率,为 4.33×10–7 mm3/(N·m)。当Al/Ti 原子比从2.0 增大至6.6 时,磨损率逐渐增大,这可能与硬质颗粒Al2O3的生成有关。有研究报道,掺杂元素在改变涂层结构的同时,也可能给其磨蚀性能带来负面影响。王永欣等[89]指出,掺杂金属可使涂层呈疏松柱状结构,水分子在交变应力作用下更容易深入内部,从而影响涂层的防护性能。
图 9 DLC、Cr 和WC 掺杂DLC 涂层在大气及海水环境下的磨损率[86]
图 10 DLC、B-DLC 涂层在海水环境下的磨痕及磨损率[37]
3.2 多层结构设计对碳基涂层磨蚀性能的影响
多层结构涂层通过不同结构过渡层相互交叠,能够阻碍裂纹穿过界面,延长腐蚀液到达基体的路径,并且可以通过增加多层结构及顶层厚度优化,提高整体韧性与耐磨性,实现涂层强韧防护一体化的目标,成为碳基防护涂层的新发展方向[90-92]。Ye 等[90]为了提高涂层的承载力,使用磁控溅射系统制备了一种梯度过渡Cr-Cr/WC-WC-WC/a-C 涂层(见图11a)。发现磨蚀后的多层DLC 涂层形成微小的腐蚀坑,表面磨损痕迹光滑平整,机械磨损占主导地位。Li 等[91]通过复合磁控溅射方法制备了Cr/GLC 多层涂层(见图11b),研究了不同调制周期的涂层在人工海水中的摩擦腐蚀行为。发现调制周期从1000 nm 减小到250 nm时,涂层硬度上升,最高达到20.03 GPa。调制周期减小,能有效抑制涂层剥落面积,这是由于多层结构阻止了通孔的形成,限制了缺陷的延展。同时,通过增加顶层GLC 厚度的优化设计,改善了耐磨性能。Cui等[92]使用等离子体增强化学气相沉积制备了多层掺杂硅元素DLC 涂层,多硅层和少硅层相互交叠形成多层结构,顶层也采用加厚DLC 层设计,如图12a 所示。单层DLC 与基体结合强度差,在摩擦过程中发生局部剥落;多层DLC 的开路电位OCP 在整个测试过程中几乎保持不变,平均摩擦系数约为0.025,最低可达0.010,抗摩擦腐蚀性能显著提高,如图12b 所示。
图 11 Cr/WC/a-C 梯度涂层结构和Cr/GLC 涂层截面TEM[90-91]
图 12 Six-DLC/Siy-DLC 涂层截面形貌和基体、单层DLC、Si-DLC 多层涂层磨蚀过程中的开路电位与摩擦系数[92]
3.3 小结
与硬质抗磨损氮基涂层不同,碳基涂层是一类优异化学惰性的涂层材料,提高其致密性以及与基体的膜基结合力,被认为是改善其抗磨蚀综合性能的有效解决思路。针对碳基涂层应力大、与金属基体结合差、摩擦易受环境影响等瓶颈问题,通常采用第三异质元素掺杂、添加过渡层、多层调控等方法来解决,这为设计和发展海水抗磨蚀防护碳基涂层提供了设计依据。其中,多层结构不仅可以改善涂层的综合性能,还能够避免引入异质掺杂元素带来的晶界缺陷,阻断贯穿通道的形成,进而抑制腐蚀介质快速扩散,在海水环境下的防护应用表现出巨大的潜力。目前,碳基涂层在海水环境下的磨蚀行为研究才刚刚起步,尤其在高静水压、加载力及腐蚀介质耦合作用下,如何通过多层涂层体系的精细结构调控,构筑强结合界面,减缓腐蚀液渗入,阐明损伤失效机理等,仍需要进一步研究。
4 氮/碳基涂层的磨蚀失效机理研究
由于海洋环境的复杂性及磨蚀工况的多样性,且氮/碳基涂层材料的磨蚀行为检测分析手段有限,磨蚀失效机理研究目前还不够明晰,下面主要从分析方法和失效形式两方面归纳讨论。首先,在失效分析方法方面,由于腐蚀和摩擦的交互作用,不能以单一的摩擦或腐蚀工况分析。有学者提出通过数学计算方法分析摩擦、腐蚀和磨蚀在材料损伤中的百分比[67,91]。运用最多的计算公式为:
VT=Vm+Vc+ΔVcm+ΔVmc (1)
式中:VT 为磨蚀总的磨损量;Vm 为纯机械材料损失量;Vc 为纯腐蚀材料损失量;ΔVcm 为腐蚀增加的磨损量;ΔVmc 为因摩擦增加的腐蚀量。通过式(1)探讨了碳基和氮基涂层的摩擦腐蚀耦合损伤与单一摩擦或单一腐蚀损伤的不同规律,见表1。结果表明,在涂层磨蚀损伤中占比最大的为摩擦磨损,且摩擦腐蚀交互作用在材料磨蚀中的占比为21%~57.1%,表明摩擦和腐蚀之间具有明显的耦合加剧失效作用。
表 1 涂层的磨损量、腐蚀量以及磨蚀率[34,67,90-91]
其次,在涂层失效机理研究方面,氮基涂层体系主要存在涂层表面钝化膜的破环和再生成过程。当钝化膜被摩擦破坏后,露出具有较高电化学活性的新鲜表面,在海水溶液中和周围钝化表面形成原电池,进一步促进了涂层腐蚀失效[67]。Bayon 等[93]的实验结果也证明,摩擦过程中形成了表面阴极和阳极区,腐蚀集中发生在被摩擦区,且由于涂层存在缺陷,可以将电解液传导到基体上,引起腐蚀加剧。
对于不生成钝化膜但具有良好化学惰性的DLC涂层,在静止的海水腐蚀介质中,自身相当于“钝化膜”,涂层的理论腐蚀速度非常小,常可忽略。然而,真实涂层的腐蚀防护性能并不完美。研究人员发现,影响涂层腐蚀的最主要因素是,涂层在沉积过程中,出现无法避免的针孔等缺陷,海水可通过孔隙等本征缺陷或摩擦产生的磨坑和裂纹腐蚀通道,侵入涂层/基体界面,同时通道附近涂层、基体与海水介质形成原电池,发生电化学反应,在耦合滑动摩擦作用下,加快涂层失效,进而发生界面开裂或涂层剥落[33,67]。涂层磨蚀失效是一个受物理、化学及电化学等影响而动态变化的复杂过程,目前国内外在此方面的失效理论研究均相对匮乏。特别是基于上文提到的严苛耦合服役环境下,如何从微观尺度进一步明晰涂层磨蚀失效机理,并提出延寿防护新策略,仍是具有挑战性的研究新方向。
5 结语
综上所述,设计和开发海洋抗磨蚀防护涂层,对于支撑我国海洋工程装备的发展和应用具有重要的科学意义。目前,在防护涂层结构设计以及磨蚀失效机理探究等方面已取得一定的成果。然而,在海洋高盐雾、高湿、温度交变、载荷压力等多场耦合环境下,材料表/界面的摩擦、腐蚀、微生物污损等动态服役工况极为复杂,传统的实验测试方法和仪器设备难以模拟真实海洋使役环境。因此,在海洋极端工况下的耐磨蚀防护涂层仍需要深入研究。
首先,如何通过有效的组分/结构调控和优化设计,减少涂层表/界面的缺陷和膜基热力学不匹配特性,提高涂层的结合力,获得兼具强韧抗磨蚀一体防护的涂层材料是关键,这也是材料科学、机械工程、表面技术、海洋环境等交叉领域的前沿方向。例如,可以发展先进的涂层制备技术,通过对等离子体放电基础的理解,实现高离化稳定放电与光滑致密结构的涂层可控制备,调控PVD 涂层生长中出现的针孔、大颗粒、晶界等多尺度缺陷。其次,由于碳基等防护涂层本身的化学惰性,传统电化学测试方法并不适用,如何设计和开发具有空间高分辨率和高灵敏度、可无损快速检测、适合惰性涂层的测试仪器,并建立磨蚀检测标准方法和体系刻不容缓。当前新兴的一些电化学测试手段,如扫描开尔文探针、扫描探针电化学显微镜系统等,有望为深入揭示涂层严苛海洋环境下的电化学行为和损伤失效机理提供技术保障。另外,在复杂的海洋环境下,海工关键运动部件材料面临的工况也各有不同,目前围绕海水浸泡工况的磨蚀行为研究较多,而考虑温度、压力、海水冲蚀等耦合因素影响的基础理论和实验研究都较少,这极大地限制了高性能抗磨蚀涂层材料技术的开发。同时,由于模拟实际工况的服役测试平台和动态原位的结构表征手段还不成熟,如何设计制造海洋环境模拟测试装备仪器,实现涂层台架性能服役评价和寿命预测,并形成完善的海洋防护材料技术,也是未来科学研究和工程应用领域的重要方向。
参考文献:
略
免责声明:本网站所转载的文字、图片与视频资料版权归原创作者所有,如果涉及侵权,请第一时间联系本网删除。
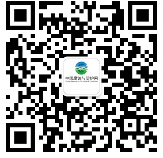
官方微信
《腐蚀与防护网电子期刊》征订启事
- 投稿联系:编辑部
- 电话:010-62316606-806
- 邮箱:fsfhzy666@163.com
- 腐蚀与防护网官方QQ群:140808414