摘要
对提升钛合金零件的疲劳强度,已有相关技术的试验研究,但缺乏对技术的系统介绍,阻碍了该技术的产业化应用。 通过整理大量试验数据及其结果,就激光冲击强化对钛合金零件的疲劳特性的影响展开分析。简要介绍激光冲击强化技术的发展状况,分别从表面形貌、残余应力、微观组织、硬度、表面粗糙度等方面进行分析总结。结果发现,当激光脉冲能量为 7 J 时,材料塑性变形量最大;当激光功率密度为 3 GW / cm2 时,材料表面残余压应力值最高;当冲击次数达到 5 次以上时, 材料表层的位错密度不断增大;当在工件表面覆盖一层高强度的光滑金属接触膜时,材料表面粗糙度将降低。综合数据可知激光功率密度及冲击次数对钛合金疲劳寿命的影响最大。整理了大量试验数据,可为得到最佳的激光冲击强化效果及提升疲劳寿命提供理论参考。
关键词: 激光冲击 ; 钛合金 ; 疲劳强度 ; 表面形貌 ; 残余应力 ; 力学性能
0 前言
钛合金具有强度高、韧性好、抗腐蚀性好、耐高温等特点,在航空和航天工业中的应用日益广泛。目前,先进航空发动机中的压气机叶片、风扇叶片及零件设备由钛合金制造而成,逐步实现了压气机钛合金化[1]。然而,钛合金具有耐磨性差、疲劳强度低、切削加工困难等缺陷,尤其是疲劳性能的影响大大限制了它的一系列应用。在实际工作过程中,航空发动机产生的热应力、离心力和异物吸入等复合作用,使得钛合金叶片发生疲劳断裂。在过去的一些事故统计中,我国80%空军现役飞行事故的发生与发动机叶片的疲劳断裂有关。据报道,2014年,我国南航CZ3739航班由于压气机风扇的叶片断裂导致飞机引擎在航班飞行中着火; 2015年,达美航空1288航班由于发动机叶片断裂导致发生严重的事故;2018年,美国西南航空1380航班由于发动机叶片断裂导致发动机爆炸。这三起重大事故是由叶片的疲劳断裂引起的。为提高钛合金构件的疲劳性能,提高其使用寿命,常采用的传统表面强化技术有高速喷丸[2]、滚压[3]、低塑性抛光[4]等。
高速喷丸采用高速弹丸流连续向材料表面喷射使其发生塑性变形,从而产生残余压应力层,能有效地改善工件的抗疲劳和抗应力腐蚀等性能[5]。然而,当零件长期处于室温或高温的条件下,易承受交变应力,其残余应力会逐渐减小,组织晶粒逐渐变大,因此喷丸强化的零件在使用一段时间后,需再次进行喷丸强化后使用。滚压强化是利用滚压零件形成的压力作用,使金属表面产生加工硬化以提高零件性能、质量和使用寿命。然而,滚压设备的问题主要在于加工时工件的尺寸稳定性不好,而且对机床的力较大,慢慢被其他设备取代。低塑性抛光是通过球形工具在工件表面自由的滚动,从而产生累积的塑性应变,从而降低工件表面粗糙度,并在工件表层产生残余压应力,能大幅度提高材料的疲劳强度[6]。然而,该技术工艺复杂,高强压力会导致材料发生较大程度的扭曲变形。
激光冲击强化技术(Laser shock processing/peening,LSP)[7],是一种将光能转化为机械能的简单有效的材料表面改性技术,能够显著改善材料表面形貌、微观组织及残余应力等性能,提高材料的耐磨性、耐腐蚀性和疲劳性能等[8-10]。相较于其他传统的表面改性技术,激光冲击强化技术因具有强化效率高、可控性良好、被处理工件表面完整性好等特点成为表面改性领域的研究热点。激光冲击强化技术基本原理如图1所示,一束强短脉冲激光束作用于工件表面的吸收层,当吸收层充分吸收了激光能量时,将在短时间内汽化电离成等离子体向外喷射。由于在吸收层上会覆盖一层约束层,约束层会限制等离子体的膨胀喷射,使得等离子体压力迅速升高,产生超强冲击波。冲击波的压力高达数GPa,远高于工件材料的屈服强度,使材料的表层产生高幅值残余压应力,并使材料表面产生塑性变形,从而改善材料的疲劳性能等。
图1 激光冲击强化原理图[11]
1 激光冲击强化技术的发展
20世纪60年代,NEUMAN等[12]首次发现脉冲激光可以诱导形成冲击波。1972年,美国Battelle Columbus实验室成功研制出大功率激光冲击试验设备,并利用冲击波冲击铝合金试样,发现激光冲击强化可以改变材料的微观组织,提高力学性能,展现了激光冲击强化技术的前景[13-14]。1978年, FORD等[15]与美国空军实验室共同进行研究,发现激光冲击强化可以有效地控制材料裂纹扩展的速度,提高材料使用寿命。同年,法国FABBRO和PEYRE等[16-17]对激光冲击强化技术进行比较全面的研究,并提出约束模式下激光冲击波峰值压力的估算式。1990年,GREVEY等[18]进行激光冲击诱导合金钢中马氏体相变的研究。FORGET等[19]研究发现激光冲击强化在镍基合金内部诱导压应力,能够提高材料的抗磨损性能和疲劳寿命。
1960年,我国曾提出激光冲击强化的概念,但受到国内技术落后和试验设备缺乏的限制,并无实质性进展。2001年,江苏大学的张永康和周建忠等[20-21]首次提出激光冲击成形的新概念,并依照此理论进行大量试验研究。2008年,在西安我国建立了第一条激光冲击强化实际应用的生产线,并不断在航空发动机等零部件上展开应用[22]。2010年,刘会霞等[23-24]结合激光冲击成型技术提出基于激光冲击波的高速冲裁方法,并结合试验与有限元模拟分析激光冲击的工艺。2010年,SEALY等[25]利用激光冲击波技术,在Mg-Ca表面成功制备出微凹坑,以此获得织构的表面。随后,DAI等[26-27]在原有激光冲击波技术的应用上进行改进,提出激光冲击波微压印等技术,并展开大量试验研究。2011年,中国科学院沈阳自动化研究所[28-30]研制了我国首台整体叶盘激光冲击强化系统,进一步突破了激光冲击强化的实际应用限制,可将航空发动机叶片的疲劳寿命提高达6倍以上。2014年,江苏大学通过对激光冲击强化的深入研究进行试验,在铝箔表面打出呈规则排列的凹坑,将激光冲击强化成功引入到微机电系统器件领域的应用[31]。随后,温州大学的陈希章等[32-34]利用激光冲击强化技术,在不同材料表面进行试验,发现微观组织和残余应力是影响焊接效果的两个关键因素,证明了激光冲击加工是一种很有潜力的提高机械性能的方法。
2 激光冲击强化对钛合金疲劳性能的影响因素
机械零件在交变载荷的作用下,虽然应力水平低于材料的屈服极限,但经过长时间的应力反复循环作用后,也会发生突然脆性断裂,这种现象叫做疲劳。疲劳裂纹和疲劳断裂经常发生在零件的使用过程中,目前常用激光冲击强化技术提高金属零件的疲劳性能。激光冲击强化会引起钛合金表面形貌、残余应力、微观组织、硬度、表面粗糙度等变化,这些力学性能可以有效地抑制疲劳裂纹的萌生,提升疲劳极限进而提升激光冲击强化的效果。
2.1 表面形貌
汪军[35]深入研究激光冲击强化过程中不同吸收层对TC4合金板料表面形貌的影响。试验发现,激光冲击强化处理后在吸收层为铝箔和黑胶带上存在激光烧蚀的痕迹,而在激光冲击后除掉吸收层并用无水丙酮清洗后的试样表面无痕迹,结果说明用铝箔和黑胶带作为吸收层具有良好的保护作用。在激光功率密度、光斑大小直径、搭接率等因素均相同的情况下,试验证明,黑胶带相比铝箔作为吸收层,材料表面经激光冲击强化后会产生更大的塑性变形进而导致残余应力变大,可更有效地提高试样疲劳寿命。王学德等[36]将TC6钛合金进行热处理后随炉冷却,试样经过双面约束激光冲击强化之后平直无弯曲,表面可以观察到分布均匀且连续光滑的微凹坑,结果表明激光冲击强化技术会使钛合金试样发生塑性变形,随着塑性变形的增大,材料疲劳极限也增大。
孙汝剑等[37]通过改变脉冲能量的大小对TC17合金进行激光冲击强化试验。图2所示为TC17钛合金激光冲击强化后的三维形貌,由图可知,当脉冲能量为3J时,试样塑性变形量最小,当脉冲能量为7J时,试样塑性变形量最大。结果表明,不同的激光冲击能量会使试样的塑性变形发生明显变化,且随着激光脉冲能量的增加,试样表面的塑性变形增大,但由于金属材料在最初阶段的塑性变形要比后续任何阶段的塑性变形都容易,所以塑性变形的增加量会慢慢变少。
图2 TC17钛合金激光冲击强化后的三维形貌[37]
由此看出,激光冲击强化钛合金后发生塑性变形,当激光冲击强化时,吸收层材质的不同、激光脉冲能量的变化、材料热处理工艺的不同等会导致钛合金表面形貌产生较为明显的变化。当激光脉冲能量达到7J时,试样塑性变形量最大,可以达到一个较大的极限疲劳强度。
2.2 残余应力
何卫锋等[38]对钛合金不同激光冲击次数下的残余应力分布进行试验分析。图3所示为不同次数冲击下TC17钛合金的残余应力分布图,结果表明,由一次冲击到三次冲击要比由三次冲击到五次冲击后产生的残余应力值增加幅度要高,随着冲击次数的增加,材料发生塑性变形,其残余压应力的深度变化呈非线性增加。
图3 不同次数冲击下TC17钛合金的残余应力分布[38]
除不同冲击次数会影响钛合金的残余应力外,激光功率密度的大小对钛合金的残余应力值也会产生影响。FABBRO等[16, 39]认为,在试验中选取合适的激光功率密度,使诱导形成的高强冲击波峰值压力介于2~2.5倍雨贡纽弹性极限内,在此条件下能获得较好的残余压应力值。张永康等[40]进行试验结合有限元分析,对激光冲击强化TC4钛合金的残余应力场分布进行分析,系统模拟不同功率密度下, 激光冲击过程中材料残余应力场的分布。结果表明,当冲击波峰值压力达到并大于材料雨贡纽弹性极限时,材料表层将产生残余压应力,并且残余压应力越大,材料的疲劳极限越高。杨丰槐[41]研究发现,激光脉冲宽度、光斑直径和光斑形状都会影响残余应力的大小。从仿真结果来看,激光脉冲宽度越大,表面形成的残余压应力越大,但在实际生产加工过程中,考虑到脉冲宽度的不断增大会导致零部件的表面过热发生烧蚀,从而材料表面的残余压应力会减小,起到了相反的效果,因此需要选择合理的激光冲击强化工艺参数。
FABBRO等提出激光冲击强化在材料表层诱导的残余压应力与激光的功率密度成正比关系,何卫锋等[42]以TC6钛合金为研究对象,分别采用2.5、 3、4、5GW/cm2 这4种功率密度对试样进行激光冲击强化试验,图4为不同功率密度下冲击后沿深度方向的残余应力分布,结果表明,当功率密度为3GW/cm2 时,表面残余压应力值最高,并且冲击影响层的深度更深,表面压应力值在深度为0.1mm时达到–690MPa。由残余应力而引起的材料疲劳极限的变化
为:
(1)
图4 不同功率密度下激光冲击试样沿深度方向的残余应力分布[42]
由式(1)可知,激光冲击后试样表面形成的残余压应力会使材料的疲劳极限提高,统计发现,当功率密度为3GW/cm2 时表面残余压应力值最高,可以有效地提高钛合金材料的疲劳寿命。
2.3 微观组织
朱颖等[43]采用不同冲击次数对TA15钛合金进行激光冲击强化试验,研究不同冲击次数对材料微观组织的影响。对比未经激光冲击和经过1次激光冲击后的晶粒状态的TEM像,如图5所示,1次激光冲击后的TA15合金晶粒明显变细且分布均匀,较未经过激光冲击前,试样的位错密度也有所提高,但也只是出现在少量的 β 相附近;2次激光冲击后TA15合金在 α 相和 β 相的位错都十分密集,且可以看出有位错塞积、增殖、缠结等现象。昝垚旭等[44]采用扫描电镜对激光冲击Ti834合金显微组织进行了研究。结果表明,当Ti834合金经过1次冲击后,试样表层位错密度增加,组织相界处有位错塞积,经过2次冲击后,试样的位错密度较第一次有更明显的增加,相界处出现大规模的位错积塞,冲击强化效果明显。钛合金经过激光冲击强化后发生塑性变形,使其微观组织结构也随之发生变化,从而造成一定程度疲劳性能的改变。
王学德等[45]利用激光冲击强化技术对TC11合金进行处理,分析了TC11合金激光冲击前后微观组织变化,图6a中可以看出TC11合金原组织的相界非常清晰,图6b、6c、6d分别是激光冲击1、3、5次后的微观组织。图6b中发现存在大量的高密度位错和亚晶结构;图6c和6d中出现了纳米层晶粒且纳米晶随着激光冲击次数的增加变得更细小、均匀。结果表明,表面微观组织在不同冲击次数下呈现出位错密度-位错胞-纳米晶的细化过程,这是因为晶粒细化后能够使滑移形变抗力得到提升,循环滑移带构建与扩散得到抑制,裂纹蔓延的晶界阻抗得到提高,而且会改变裂纹方向,提升疲劳强度;晶粒极细纳米表层中的问题较少,不易发生裂纹; 纳米层内严重的塑性形变部分及其高密度位错,则使疲劳裂纹的生成与蔓延得到有效控制。显微组织对材料疲劳性能的影响,除了与各材料组织自身的力学性能特征有关以外,还与材料组织晶粒度的分布特征有关,细化组织晶粒可提高材料的疲劳强度。位错密度由 ρ 表示:
(2)
图5 TA15合金TEM像[43]
图6 不同冲击次数下表面透射电镜图和衍射花样[45]
由式(2)可知,位错密度 ρ 随着压力√p 的变化而变化,激光功率密度增加,形成的激光冲击波压力越大,进而导致材料表层的位错密度越大。对于钛合金材料,位错强化导致的强度增量与材料中位错密度的平方根呈正比,位错密度增大,微观组织越细,材料的疲劳抗性提高越明显。
2.4 显微硬度
朱颖等[43]对兼有 α 型和 α+β 型的TA15合金进行激光冲击强化,不同冲击次数下TA15的表面显微硬度变化趋势如图7所示,试验结果表明,激光冲击次数的增加影响试样显微硬度的增加,且2次冲击后,显微硬度有明显提升,说明激光冲击强化可以有效提高材料的表面显微硬度,进而提升钛合金的疲劳极限。周建忠等[46]研究了经激光冲击强化后TC6钛合金表面强度的变化。不同功率密度下激光冲击强化的试样深度方向显微硬度分布如图8所示,可以看出,试样的显微硬度随着功率密度的增加而增大。高功率密度的激光束冲击钛合金,冲击波从材料表面到内部的传播过程中会发生衰减,到一定深度后硬度不再增强[47]。罗学昆等[48]对激光冲击强化处理Ti-6Al-4V合金的试验进行研究,主要探讨激光功率密度的不同对Ti-6Al-4V合金显微硬度的影响。图9是激光冲击强化前后Ti-6Al-4V合金距表面不同厚度层的显微硬度分布。由图可知,经激光冲击强化后的试样显微硬度明显高于未经激光冲击强化的显微硬度,这说明激光冲击强化技术能够提高Ti-6Al-4V合金的硬度。结果表明,激光功率密度越大,激光冲击强化后试样表面的硬度值越高,在107 循环周期下,原材料的疲劳极限较激光冲击强后后提升了33.3%,可知激光冲击强化技术可以有效地提高Ti-6Al-4V合金的疲劳极限。据研究表明,激光冲击强化后,材料位错密度不断增加,使得被冲击区域的硬度也随之增大,这些高密度位错会形成大量的位错胞,可以抑制位错运动的扩展,从而提高材料的硬度。由材料微观组织分布可知,位错密度越大,显微硬度越大,材料的抗疲劳性能越好。
图7 不同冲击次数下TA15的表面显微硬度变化趋势[43]
图8 显微硬度分布图[47]
图9 激光冲击处理前后Ti-6Al-4V合金距表面不同厚度层的显微硬度分布[48]
2.5 表面粗糙度
表面粗糙度是材料表面完整性的一个重要指标,对材料的疲劳性能有着很大的影响,进而会影响零部件使用寿命。MAAWAD等的研究表明,随着表面粗糙度的增加,激光冲击强化后Ti-54M钛合金的疲劳强度甚至从650MPa降低到了550MPa[49],SUN等的研究表明,对激光冲击强化的试样进行后处理抛光工艺后,其疲劳寿命相较未抛光前比基体提高约6.7倍[50],但多数是在常温条件下进行激光冲击强化试验的。任旭东等[51]研究中高温条件下激光冲击强化对Ti-6Al-4V钛合金表面完整性的影响,如图10所示,随着温度的不断升高,在两种状态下,材料表面粗糙度均逐渐增大,且相比于未激光冲击强化的试样,激光冲击强化后试样的表面变得更加粗糙。材料表面的粗糙度值变大,表面残余压应力值变小,从而缩短零部件的疲劳寿命[52]。杨丰槐等[41]应用有限元模拟分析计算激光冲击TC4合金的表面粗糙度,发现激光冲击次数、冲击峰值压力、光斑形状这些参数会对钛合金的表面粗糙度产生影响。模拟结果表明,当激光冲击次数和峰值压力增加时,材料的表面粗糙度逐渐增大;当其他参数均相同,光斑形状不同时,圆形光斑冲击后材料的表面粗糙度小于方形光斑冲击后材料的表面粗糙度。吴俊峰等[53]试验对比分析了不同强化工艺下 β 锻TC17钛合金的表面粗糙度变化规律,如表1所示,激光冲击强化后试样的表面粗糙度比喷丸强化和复合强化后的表面粗糙度低。
图10 不同温度下Ti-6Al-4V合金的表面粗糙度[51]
表1 不同强化工艺TC17合金表面粗糙度[53]
OCANA等[54]采用铝箔作为吸收层,发现激光冲击强化使Ti-6Al-4V合金的表面粗糙度从0.1 μm增大到0.82 μm;YELLA等[55]发现,激光冲击强化采用黏性胶带获得的表面粗糙度远小于采用黑漆获得的表面粗糙度;SALIMIANRIZI等[56]发现,通过改变光斑的搭接方式和搭接率,可以有效降低材料表面粗糙度;江苏大学戴峰泽等[57]尝试在激光冲击强化中工件表面覆盖一层高强度的光滑金属接触膜,降低表面粗糙度。不同的表面粗糙程度会对材料产生不同的疲劳性能影响,材料疲劳强度随其表面粗糙度的提升而降低,因此降低材料的表面粗糙度能有效提高其疲劳寿命。
表面粗糙度对疲劳强度的影响用表面加工系数 β 来表示:
(3)
式中,σ β 为某种表面状态下标准光滑试样的疲劳极限,σ β 0 为磨光标准光滑试样的疲劳极限。可见,激光冲击强化可以有效地提高疲劳强度。以此形式看来,钛合金试样表面粗糙度越大,对疲劳强度的降低影响就越大。
激光冲击强化技术可以显著改变钛合金的表面形貌、微观组织,有效提高材料的残余应力和硬度,降低材料的表面粗糙度,这些力学性能的变化对钛合金疲劳寿命起着重要的影响,其中残余应力的大小起着关键的作用,残余应力的增大导致材料硬度增大,其疲劳极限值也增大。
3 结论
激光冲击强化相比传统强化工艺效果更佳、可操控性强、适用性好,在航空航天行业中得到了越来越广泛的应用与研究,对提升部件疲劳性能和延长材料使用寿命具有重要意义。首先介绍了激光冲击强化技术的研究背景和发展概况,分别从激光冲击强化钛合金表面形貌、残余应力、微观组织、硬度、表面粗糙度等力学性能的变化对钛合金疲劳性能的影响进行分析与总结,并对其发展前景进行了展望。
(1)激光工艺参数是影响激光冲击强化效果的重要因素,选取合适的激光功率密度、不同冲击次数、光斑形状与大小等,可以有效地改善钛合金的残余应力分布,提高材料疲劳性能。然而目前对于钛合金表面改性技术的研究不多,很多是基于单一工艺参数进行试验对比,无法全面概括激光冲击强化钛合金的最优参数。未来研究,可以将不同激光工艺参数结合起来分析,有利于总结出更能显著提高钛合金强化效果的工艺参数。
(2)激光光斑的形状、大小以及搭接率均会影响钛合金表面性能,目前激光头只能做到一种光斑冲击,在试样不变的情况下,激光头光斑形状与大小的切换可以有效地提高冲击试验的效率,得到最有效的强化效果。目前的激光器存在脉冲能量较低、光斑质量差、重复率低等问题,极大限制了激光冲击强化技术的发展,未来新型激光器的开发,应着重于研究高质量激光束,抑制自发辐射光,提高散热性能等。
(3)目前针对不同型号的钛合金,主要以激光冲击试验为主,未来可以大幅度加入模拟仿真数据,不同型号的钛合金制定不同密度的网格数,更加有利于验证激光冲击强化对钛合金表面改性技术的研究。
参考文献: 略
免责声明:本网站所转载的文字、图片与视频资料版权归原创作者所有,如果涉及侵权,请第一时间联系本网删除。
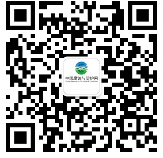
官方微信
《腐蚀与防护网电子期刊》征订启事
- 投稿联系:编辑部
- 电话:010-62316606-806
- 邮箱:fsfhzy666@163.com
- 腐蚀与防护网官方QQ群:140808414