摘要
在大陈岛海域围海养殖基地对新型HSn70-1铜围网进行应用研究。铜围网在各海洋腐蚀区带发生了明显不同的腐蚀行为。采用金相组织和形貌观察、成分分析、性能测试线扫描等方法,对不同腐蚀区带HSn70-1铜围网的腐蚀行为进行研究。结果表明,各海洋腐蚀区带中铜合金的腐蚀行为差异显著:潮差区发生局部腐蚀,点蚀、脱锌严重;全浸区腐蚀轻微,腐蚀产物膜对基体起到了一定的保护作用;该海域存在典型的冲蚀区,磨损腐蚀和脱成分腐蚀严重。
关键词: 新型HSn70-1合金 ; 铜合金网衣网箱 ; 海洋腐蚀区带 ; 腐蚀行为 ; 点蚀 ; 脱成分腐蚀 ; 腐蚀产物膜
铜合金网衣网箱具有优良的耐蚀性、抑菌性和力学性能以及容积率大、可回收等自然特性,在水产养殖的可持续发展中扮演着不可或缺的重要角色,具有不可估量的应用前景。近年来,我国开展了铜合金网衣网箱的研发和应用工作,但目前该领域的报道多集中在养殖探索方面,尚鲜有腐蚀方面的追踪研究。海洋环境复杂多变,影响铜合金腐蚀的因素众多[1,2,3,4,5],因此研究并解决应用过程中出现的实际问题,对推进铜合金网衣网箱在国内的发展进程有着重要的意义。
锡黄铜在海水中拥有高耐蚀性和良好的力学性能,被称作“海军黄铜”,原因是Sn容易富集在异相相界及α相晶界,起到强化晶界、细化组织的作用,从而抑制Zn的迁移和流失[6,7,8]。现有牌号的锡黄铜由于含有As,Pb和Sb等高危害化学成分[9,10,11],应用受到一定限制,因此寻求环保的替代元素以开发安全优质的铜合金便势在必行。Ni可扩大铜合金α相区,提高黄铜的抗脱锌、抗应力腐蚀能力及强度、韧性等性能;Si能够改善加工性能,提高耐蚀性和力学性等[12,13,14,15]。本文通过在70Cu-1Sn铜合金的基础上添加微量元素Ni和Si,制备出新型HSn70-1合金,采用水平连铸、真空退火、多道次冷拔等工艺,将该铜合金加工成线材,编织成网应用于大陈岛马道头海域围海养殖基地。为追踪了解铜围网的腐蚀状况并研究其海水腐蚀行为,将整网进行分区取样,并进行表层腐蚀形貌观察和外缘元素分布分析,研究铜合金在各海洋腐蚀区带的腐蚀机理[16]。
1 实验方法
新型HSn70-1合金的成分 (质量分数,%) 为:70Cu-0.9Sn-0.13Si-0.2Ni-Zn。生产采用水平连铸炉,在N2保护气氛中进行,连铸温度1150 ℃,速度100 mm/min,浇铸成Φ9 mm棒材,再经均匀化退火和多道次冷拉拔等工艺制成Φ4 mm线材。铜合金网衣为线材横竖交叉的编织网,在大陈岛马道头海域服役,圆形围海养殖基地分内外圈,内圈半径60 m,钢筋混凝土桩沿圆周均匀打入海底,相邻桩子以网衣相连,以年平均海面为界,上为尼龙网,下为铜合金网衣且入泥0.5 m;外圈为半径65 m的防撞网。使用2 a后显示,铜合金网衣在各海洋腐蚀区带发生了明显不同的腐蚀行为,从上至下依次为:潮差区、全浸区、冲蚀区和海泥区[17,18]。
为全面研究新型HSn70-1合金的海水腐蚀行为,首先测量竖向线径并依据该海域海洋腐蚀区带进行分区取样,然后先从铜合金基体,再从表层两部分来衡量材料的腐蚀状况。采用电火花线切割机取样,用XQ-1型金相试样镶嵌机进行热固性塑料压制,经机械磨抛后用FeCl3盐酸溶液侵蚀,使用Axio Imager A2m金相显微镜 (OM) 观察显微组织及宏观腐蚀形貌;将表层腐蚀产物用机械方法制成粉末样品,使用D8 ADVANCE 型X射线衍射仪 (XRD) 对粉末与基体进行物相分析;使用Quanta FEG 450型场发射环境扫描电子显微镜 (FE-ESEM) 观察表层显微腐蚀形貌及腐蚀深度;使用Aspex Explorer 型X射线能谱仪 (EDS) 表征腐蚀产物粉末与基体的化学成分。
2 结果与讨论
2.1 铜合金网衣腐蚀速率随海水深度的变化
观察使用两年铜合金网衣,可见腐蚀状况与其所处海水深度密切相关,且有明显差异[19]。因编织网竖向线材贯穿海面至海底,可通过定距离、高密度测量并绘制线径随深度的变化曲线,来反映新型HSn70-1合金的腐蚀程度与所处深度的关系。由图1曲线看出,最外表面腐蚀轻微;随深度增加,腐蚀加重,在300~1000 mm深度范围处于最大腐蚀速率;随深度继续增加,腐蚀速率迅速减小并一直保持基本稳定;到5400~6000 mm深度范围,再次发生加速腐蚀,但较300~1000 mm深度范围的要轻;最后腐蚀速率又减小到很轻微的程度。
图1 经过2 a腐蚀后新型70-1锡黄铜线径 (原始直径4 mm) 随海水深度的变化曲线
0~100 mm段线径之所以接近原始线径4 mm,是由于铜合金网衣上部与尼龙网连接,使其部分表面受到了尼龙的缠绕覆盖保护作用,但仍存在许多较大的蚀坑。300~1000 mm段腐蚀深度接近0.5 mm,是因潮汐与洋流的周期性运动使表面干湿交替,且表层海水中常夹杂着空气,拍击时浪花飞溅、气泡破裂,导致腐蚀相当严重。之后,随深度增加,线径逐步上升;至1500~5400 mm段腐蚀深度约为0.075 mm,腐蚀比较轻微,这是由于一直浸没于海水中,合金表面形成一层均匀致密、较为坚硬的腐蚀产物膜,说明该膜对基体能起到一定的保护作用[20]。值得注意的是,5400~6000 mm段再次出现加速腐蚀,腐蚀深度约为0.31 mm,是由于大陈岛位于椒江入海口,海底泥沙含量高,冲刷破坏力强,故腐蚀产物膜磨损严重,加快了腐蚀进程[21,22]。6000~6500 mm段腐蚀深度约为0.02 mm,因该部分埋于海泥中,所以腐蚀甚微。通常将海洋环境大体分为5个区带:最高浪溅位以上称作海洋大气区,最高浪溅位至平均高潮位称作海水飞溅区,平均高潮位至平均低潮位称作潮差区,平均低潮位至海底底面称作海水全浸区,海底底面以下称作海泥区。特别的,将海底底面上泥沙含量很高,腐蚀严重的区带称作冲蚀区[17]。据此,可大致划分铜合金网衣所处各区带的范围。由于海泥区腐蚀甚微,本文主要研究铜合金在潮差区、全浸区和冲蚀区3个区带的腐蚀行为。
2.2 不同海水区带腐蚀后铜合金成分与组织分析
从3个区带中分别取样,用XPS表征基体的元素种类和含量,检测结果如表1所示。可知,各区带腐蚀后,基体主要化学成分Cu,Sn,Si,Ni和Zn的含量变化均不明显。
表1 3个区带的HSn70-1铜合金基体化学成分
图2为偏光显微镜观察到的铜合金基体金相组织。可以看出,各区带组织分布均匀且没有缺陷,微量元素颗粒弥散分布于单相α基体中形成多元复杂固溶体,对强度指标和耐蚀性能都有增强作用[23,24,25];晶粒尺寸约为几微米,其中全浸区晶粒度最小,冲蚀区晶粒度最大,潮差区晶粒度居中。
图2 3个区带的HSn70-1铜合金丝横截面金相组织
考虑到添加元素总和只有1.23%,微量元素Sn,Si和Ni均可固溶于α相中。故可用Cu-Zn相图作基础,再考虑添加元素的“Zn当量系数” (Sn=2,Si=10~12,Ni=-1.5) 对α-α+β相界线的影响,Zn当量x用下式推算:
x=A+∑ci×kiA+B+∑ci×ki×100%
式中,A为Zn的实际含量;B为Cu的实际含量;ci为加入黄铜某一元素的含量;ki为该元素的Zn当量系数。将表1的值代入求得:x≈31.268%,处于α相区。但在实际生产中,不平衡冷却会使得含31%~32%Zn的黄铜出现少量β相。
为进一步确定铜合金中的相,从3个区带取样后,进行XRD谱分析,结果如图3所示。可知,各区带样的XRD衍射峰与Cu0.64Zn0.36(原子分数) 完全吻合,即均为α单相复杂黄铜合金。
图3 3个区带的HSn70-1铜合金的XRD谱
2.3 铜合金线腐蚀形貌观察
为了解各区带的腐蚀情况,从铜合金线对应的3个区带中分别取样,用偏光显微镜观测铜合金线表面宏观腐蚀形貌,见图4。
图4 3个海水区带腐蚀后的HSn70-1铜合金线表面宏观形貌
可知,在潮差区 (图4a),腐蚀产物基本无保留,大部分基体发生裸露、色泽金黄,表层存在很多直径数十微米的蚀坑,有的地方甚至产生了直径约500 μm的大蚀坑,蚀坑底部有乳白色腐蚀产物[26,27]。在全浸区 (图4b),铜合金表面均匀地覆盖着青绿色的致密腐蚀产物膜;在冲蚀区 (图4c),部分基体发生裸露,由泥沙冲击引起的磨损在腐蚀产物膜上造成了许多划伤,甚至在表层形成了条纹状沟槽,槽内青绿色腐蚀产物膜覆盖较好。
同时,用SEM观察了从3个区带中分别取样的铜合金横截面边缘微观腐蚀形貌,结果见图5。
图5 3个海水区带腐蚀后的HSn70-1铜合金线横截面边缘微观形貌
可知,在潮差区,铜合金线表面腐蚀产物保留很少,内部存在许多沟壑状空洞,点蚀与脱成分腐蚀非常严重;在全浸区,表面有一层平均厚度约3 μm、均匀致密且与基体结合牢固的腐蚀产物膜,基体组织保存良好,说明良好的腐蚀产物膜可以对基体起到一定的保护作用;在冲蚀区,表层腐蚀产物膜大部分被损伤,内部有较多直径不足1 μm的孔洞,且孔径沿线材径向由外向内逐渐变小,可见该区带冲刷腐蚀与脱成分腐蚀相当严重[28]。
2.4 铜合金线脱锌层厚度分析
在使用SEM进行显微组织形貌观察的同时,利用EDS对材料微区成分进行了分析。为探测铜合金中各种元素含量随深度的变化,从表层至基体做EDS线扫描,结果如图6所示。
图6 在3个海水区带腐蚀后的HSn70-1铜合金线横截面边缘EDS线扫描结果
分析可知,3个区带腐蚀后的铜合金线微量元素Ni,Si和Sn含量基本保持不变,而表层相对于基体Cu含量高、Zn含量低,因此可用以表征脱锌层深度。潮差区点蚀严重,脱锌层深度约6 μm[29,30];全浸区表层形成了完整的腐蚀产物膜,除去膜厚,脱锌层不到1 μm,进一步表明该膜具有一定的防护作用[31];冲蚀区腐蚀产物膜被冲刷磨损严重,发生严重的脱成分腐蚀,致使Zn优先溶解且由外至内不断流失,脱锌层深度接近10 μm[32]。
2.5 铜合金线表面腐蚀产物成分分析
在流水中分别清洗3个区带的HSn70-1铜合金线表面,先用软毛刷轻微除去不牢固、疏松的附着物,再在不损伤基体的前提下用机械方法制得腐蚀产物粉末,然后用EDS表征粉末中元素的含量和种类,结果如图7和表2所示。
图7 HSn70-1合金线在各海水区带形成的腐蚀产物EDS分析结果
表2 HSn70-1铜合金在3个海水区带浸泡形成的腐蚀产物EDS分析结果
由图7和表2可知,腐蚀产物粉末中除含有Cu,Zn,Sn和Si外,还有来自海水中的O,C,Cl,Ca,Mg,Al和Fe等元素。其中,Cu和Zn在各区带样品中的质量分数均超过10%,说明氧化物是腐蚀产物膜中的重要成分[1]。在潮差区,海浪潮起潮落、干湿交替,表层受浪花飞溅拍打,对腐蚀产物造成严重破坏,虽含氧量充足,却不利于腐蚀产物膜的形成。在全浸区,铜合金线常年浸泡于海水中,环境相对比较稳定,有利于形成完整的腐蚀产物膜。在冲蚀区,铜合金线处于海底,且该海域比较典型,泥沙冲刷剧烈,冲击磨损首先对腐蚀产物膜造成严重破坏,缺少了该膜的保护作用,进而使得部分元素由内向外持续流失,从而在基体内形成许多微孔,故其力学性能最差。
将在全浸区腐蚀后的铜合金线表面腐蚀产物粉末进行XRD分析,结果如图8所示。
图8 全浸区腐蚀产物粉末的XRD谱
可知,在扫描角度2θ为20o~50o范围内,主要存在5个高强度衍射峰,说明全浸区腐蚀产物膜中主要成分含有Cu2O,Cu(OH)Cl,CuC2O4和C等。该腐蚀层厚约3 μm,色泽为青绿色,均匀致密且与基体结合牢固,起到了阻止基体进一步腐蚀的作用[33]。Cu2O是Cu在金属-溶液界面发生阳极反应2Cu+H2O→Cu2O+2H+形成的[34];在铜合金腐蚀后期,阳极发生Cu的氧化,进一步生成Cu2+,阴极发生吸氧腐蚀形成OH-,与海水中Cl-结合发生反应2Cu2++2OH-+2Cl-→Cu(OH)2·CuCl2;CuC2O4应是海洋里生物体的代谢产物H2C2O4与Cu2+反应后形成的。
3 结论
铜合金线在各区带的腐蚀形貌和腐蚀机理差异显著。在全浸区,耐蚀性能最为优良;在潮差区,发生了严重的流体侵蚀、点蚀和脱成分腐蚀;在全浸区,铜合金表面形成了以Cu的化合物为主要成分的腐蚀产物膜,该膜均匀致密且与基体结合牢固,有效避免了局部腐蚀,降低了Cl-的渗透性和Cu+的扩散,因此对基体产生了一定的保护作用;在冲蚀区,磨损腐蚀严重,相应地脱成分腐蚀也最严重。
免责声明:本网站所转载的文字、图片与视频资料版权归原创作者所有,如果涉及侵权,请第一时间联系本网删除。
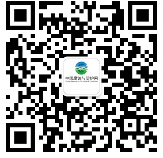
官方微信
《腐蚀与防护网电子期刊》征订启事
- 投稿联系:编辑部
- 电话:010-62316606-806
- 邮箱:fsfhzy666@163.com
- 腐蚀与防护网官方QQ群:140808414