钛合金具有高的比强度和良好的耐腐蚀性能,在航空航天领域得到了广泛的应用,现已成为航空发动机中的主要结构材料之一。钛合金的质量轻,故随着航空发动机推重比的提高,钛合金的使用量也在不断增大。对于大多数近α和(α+β)两相钛合金而言,为了获得较好的塑性,通常采用的都是常规的两相区锻造,而对于一些需要获得较高断裂韧性的零件,通常采用β锻或准β锻的方法。但在日常生产过程中,不正确的锻造工艺往往会使钛合金及其制品出现缺陷,钛合金常见的锻造缺陷有组织过热及不均、孔洞、裂纹等,这些缺陷将大大降低钛合金锻件的力学性能,进而给产品的使用带来潜在危险,因此,需要加强对钛合金的生产过程中的检验。在钛合金锻件的常规低倍检验以及金相检验过程中,经常会发现一些超标或标准未明确规定的目视缺陷,如某TC2环形自由锻件按照GJB 2744—2007 《航空用钛及钛合金锻件规范》检查其腐蚀后的表面低倍形貌,标准中没有对半清晰晶的允许情况进行说明,需要检测部门进行缺陷性质的判定,以便质检部门对产品作出合格与否的结论。
来自中国航发航空科技股份有限公司的刘卫东、张俊两位研究人员归纳总结了钛合金零部件在日常生产过程中发现缺陷的类型,并对不同缺陷进行了相应的金相检验,以供相关人员在日常检验检测过程中参考。
1 典型案例分析
1.1 TC1环形锻件的粗晶
TC1钛合金经过下料150mm(直径)→两相区加热→自由锻→退火,最终抽检1件产品,对其进行常规低倍检验,发现存在粗晶。
按照GB/T 5168—2008 《α-β钛合金高低倍组织检验方法》,用20% (体积分数,下同)硝酸+12%氢氟酸水溶液对锻件的低倍试样进行侵蚀,然后观察试样的显微组织形貌,结果如图1所示。
由图1可知,试样有明显的清晰晶缺陷,原始β晶界上存在连续且平直的晶界α相,其形成原因是该批原材料β相变点测试值偏高,锻造加热炉局部超温,导致了TC1钛合金锻造温度过高,从而产生了清晰晶。
1.2 TC2卡箍和整流叶片的锻造应变线
TC2卡箍和整流叶片经机加后进行金相检验,发现在零件表面存在周向和纵向的亮条缺陷显示,其宏观形貌如图2所示。
从TC2卡箍和整流叶片分别取样,并对其进行金相检验,结果如图3,4所示。
由图3可知,TC2卡箍亮条缺陷处的显微组织存在明显的方向性,放大后观察,可见其组织较细密。由图4可知,TC2整流叶片亮条缺陷处的显微组织同样存在明显的方向性,α和β相均呈拉长形貌,整流叶片周围正常区域的显微组织为等轴组织。
分别对TC2卡箍和整流叶片进行显微硬度测试和能谱分析,结果如表1所示,可见TC2卡箍和整流叶片亮条缺陷处与周围正常区域的显微硬度测试结果和能谱分析结果没有明显差异,因此可以判定TC2卡箍和整流叶片的亮条缺陷均为锻造过程中产生的应变线。
1.3 TC2导向叶片表面的富钛偏析
TC2低压进气导向叶片经机加工后进行金相检验,发现在零件表面存在纵向的亮条缺陷,其宏观形貌如图5所示,可见缺陷处组织较粗大,无机械变形特征,缺陷区域的长度约为35mm,宽度约为5mm。
从TC2低压进气导向叶片截取试样,沿叶片横截面制样,然后对其进行金相检验,结果如图6所示。由图6可知,缺陷处的组织与正常区域的组织存在明显差异,缺陷处的组织深度为0.3mm,为粗大的α晶粒组成的贫β相区。
分别对TC2低压进气导向叶片亮条缺陷处和周围正常区域进行显微硬度测试,结果显示缺陷处显微硬度为245HV,正常区域显微硬度为274HV,缺陷处显微硬度略低于周围正常区域。
采用电子探针对TC2低压进气导向叶片亮条缺陷处和周围正常区域进行成分分析,发现缺陷处钛元素质量分数为94.50%,铝元素质量分数为4.67%,而周围正常区域的钛元素质量分数为91.66%,铝元素质量分数为4.83%,判断亮条缺陷属于富钛偏析。这种缺陷的形成与原材料的冶炼过程有关,在合金熔炼时,合金元素扩散不充分,局部形成富集或贫化,导致元素偏析。改进原材料的冶炼工艺可以避免产生这种偏析缺陷。
1.4 TC6锻造叶片的β斑
TC6锻造叶片经机械加工后进行金相检验,发现零件表面存在暗条缺陷,其宏观及显微组织形貌如图7所示,可见暗条缺陷处初生α相含量明显低于周围正常区域。
对TC6锻造叶片进行显微硬度测试,发现暗条缺陷处显微硬度为289HV,周围正常区域显微硬度为311HV,暗条缺陷处显微硬度略低于周围正常区域。
采用电子探针对TC6锻造叶片暗条缺陷处和周围正常区域进行成分分析,发现缺陷处钼元素质量分数为4.12%,周围正常区域钼元素质量分数为2.78%,缺陷处钼元素质量分数明显高于周围正常区域。当β相稳定元素钒、钼等发生偏析后,降低了偏析区域的相变温度,合金在加热时易优先发生α相向β相转变,产生暗条缺陷,即所谓的β斑。这种缺陷的形成同样与原材料冶炼过程有关,可以采用改进原材料冶炼工艺的方法来避免产生这种偏析缺陷。
1.5 TC6叶片钎焊和抛光后的烧伤
某批次TC6叶片在阻尼台上钎焊耐磨硬质合金块后,发现阻尼台附近的叶身表面出现了“白斑”形貌(见图8)。对“白斑”区域及周围正常区域进行金相检验,结果如图9所示。由图9可知:在显微镜下无论如何调焦,“白斑”区域的组织均模糊不清;周围正常区域的显微组织为双态组织。
对钎焊后的TC6叶片进行显微硬度测试,发现“白斑”区域的显微硬度为363HV,周围正常区域的显微硬度为318HV,“白斑”区域的显微硬度明显高于周围正常区域,表明“白斑”缺陷是因焊接烧伤而形成的。
某批次TC6叶片在抛光后发现“白斑”形貌(见图10)。对“白斑”区域和周围正常区域进行金相检验,结果如图11所示。由图11可知,“白斑”区域和周围正常区域均为等轴组织。
对抛光后的TC6叶片进行显微硬度测试,发现“白斑”区域的显微硬度为313HV,周围正常区域的显微硬度为347HV,“白斑”区域的显微硬度低于周围正常区域。钛合金导热性差,故钛合金叶片在抛光时,如果操作不当,很容易造成零件表面产生的热量不能及时传导,使零件小范围内温度升高而形成抛光烧伤,较轻微的仅有表面烧伤,严重时会形成穿透性烧伤。
1.6 TC6叶片表面α层导致加工时发生断裂
α层是富集氧、氮、碳元素的稳定表面层,是一种硬脆相,一般认为其是有害相。
某批次TC6钛合金叶片在铣榫头装夹过程中,多件叶片发生断裂,叶片断裂处刚好位于夹具和叶片的接触点。叶片断口的宏观及微观形貌如图12所示,可见叶片断裂起源于叶背的装夹接触点,断口源区未见冶金缺陷,呈沿晶脆断特征。
从叶片断口截面处取样进行金相检验,可见叶背表面有多处微裂纹,裂纹内部未见氧化特征[见图13a)],叶背近表面可见α层,微裂纹均在α层之内[见图13b)]。叶片在装夹过程中夹具与叶片的接触点容易产生应力集中,又因α层具有硬而脆的特性,故在应力作用下容易萌生微裂纹,最终导致叶片断裂。
2 综合分析
2.1 常见缺陷的分类与特点
钛合金常见缺陷主要有3大类,包括冶金缺陷、工艺缺陷和表面缺陷。
冶金缺陷一般包括金属夹杂、非金属夹杂、化学成分偏析和孔洞等,这类缺陷在发生位置上一般是局部的,且形态不一,可能是块状、点状、线状或条状;工艺缺陷产生的范围则相对较广,在锻造、铸造、焊接、热处理、电加工、机械加工中都有可能产生,其形态也各不相同,需要在日常检验过程中多加鉴别;表面缺陷主要是因钛合金化学活性较高,容易与周围环境介质发生反应而产生的,其中危害最大的是氧、氮、氢等气体的污染,这类气体污染都会导致钛合金的硬度增加,在实际生产过程中也经常出现表面缺陷,比如刮碰、操作失误等造成的钛合金零件表面凹陷、裂纹、尺寸超差等,这类表面缺陷基本都伴随着宏观塑性变形,且缺陷表面都能看到明显的金属光泽。
2.2 常见锻造缺陷及其鉴别
钛合金的锻造缺陷主要有折叠、裂纹、变形不均匀等。一般情况下,锻造形成的折叠或裂纹内部有氧化物夹杂,特点是裂纹两侧呈现白亮带,组织为富氧的α层,β层则相对较少。变形不均匀的产生原因为:钛合金存在着严重的黏模现象,尤其是当模具表面粗糙度大或润滑不良时,都会阻碍金属流动,造成锻件表面与内部变形的不均匀;钛合金导热性差,锻件内部温度不均匀,高温区易变形,低温区难变形,导致了变形的不均匀。变形不均匀会导致锻件的晶粒度不同,变形量大的部位晶粒细小,反之晶粒较大,变形不均匀还会导致锻件的初生α相含量有所差别,高温区初生α相较低温区要少一些。
对于圆饼形模锻件,当其变形量较大时,锻件的轴径向剖面经低倍腐蚀后可见X型应变线,可将其分为剧烈变形区、一般变形区和变形死区,对应的显微组织和性能亦有差别;而对于较薄的模锻件,如叶片类零件,这种应变线会暴露在表面,腐蚀后可见沿纵向的亮条或暗条,这是经剧烈变形细化后组织的特征。一般来说,这种轻微应变线所形成的亮条或暗条对零件的使用性能影响不大,不作为组织缺陷处理,但在对其进行判断时,要注意与成分和组织偏析所形成的亮条缺陷区分开来,避免误判。
3 结语与建议
从上述案例分析结果可知,在实际制造过程中,钛合金在金相检验中的常见缺陷主要有清晰晶、应变线、偏析(富钛、β斑)、α层以及焊接、磨削和抛光等产生的过热过烧等,这些缺陷有因热加工过程操作不当而导致的,也有原材料遗留下来的,还有加工制造过程中因参数选择不当而产生的。
原材料缺陷可以由加强冶炼工艺控制来从源头上避免,而制造过程中发现的缺陷则需要考虑工艺是否安排恰当,或者工艺参数是否合理,从这些方面的改进来避免缺陷的发生。
免责声明:本网站所转载的文字、图片与视频资料版权归原创作者所有,如果涉及侵权,请第一时间联系本网删除。
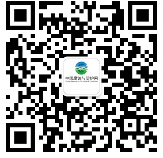
官方微信
《腐蚀与防护网电子期刊》征订启事
- 投稿联系:编辑部
- 电话:010-62316606-806
- 邮箱:fsfhzy666@163.com
- 腐蚀与防护网官方QQ群:140808414