滚动轴承是航空发动机的精密部件之一,其性能和寿命对航空发动机的稳定运行起着关键性作用。随着航空领域高端技术的发展,航空发动机滚动轴承要在持续过载、振动载荷、冷热交替等复杂环境下工作,其中载荷是滚动轴承早期失效和制约其使用寿命的关键影响因素。2009~2014年,因载荷引起的航空轴承失效比例达到40%。
某型号航空球轴承由内外套圈、滚动体和保持架组成,其外圈无挡边,内圈由双半内圈组成,无挡边,内含16粒滚珠。轴承内圈、外圈、滚动体材料均为8Cr4Mo4V钢,保持架材料为40CrNiMoA钢。在轴承上施加超载的径向载荷,每30min为一阶段,在轴承出现失效后停止施加载荷,整个过程中,外圈静止不动,内圈随轴转动。
向苹、胡宸等研究人员采用宏观观察、扫描电镜(SEM)和能谱分析、金相检验、硬度测试等方法分析了滚动轴承的损伤原因,研究了载荷对轴承材料组织与性能的影响规律,以防止该类问题再次发生。
01 理化检验
1.1宏观观察
滚动轴承各组件宏观形貌如图1所示,由图1可知:外圈和滚动体损伤最为严重,外圈表面存在1处长条形不规则的剥落区域,尺寸(长度×宽度,下同)为100mm×20mm,剥落凹坑最大尺寸为2.7mm×1.6mm,滚动体剥落区域的尺寸约为9mm×3mm,其余组件存在凹坑、麻点等轻微损伤,这些损伤产生的原因为航空发动机滚动轴承在高速运转的工作环境下,载荷施加过大时,外圈滚道与滚动体不断接触。外圈最下方位置在静止时的受力最大,易发生损伤。
1.2扫描电镜及能谱分析
采用场发射扫描电镜观察外圈滚道剥落区域,结果如图2所示。由图2可知:轴承外圈凹坑区域损伤主要以剥落坑为主,剥落坑坑底形貌凹凸不平;大部分滚道剥落区域呈现碾压磨损形貌,破碎且不连续,呈光亮磨损特征,损伤程度较凹坑区域小;局部区域呈疲劳条带特征。结合宏观形貌特征判断,外圈滚道表面剥落的原因为滚动接触疲劳。
剥落麻点滚珠以及严重剥落滚珠表面的SEM形貌呈碾压磨损特征(见图3),由图3可知:剥落滚珠源区位于外表面,且相较于外圈剥落区而言,剥落面积相对较小,深度较浅。在整个试验过程中,外圈为首先失效部件。在剥落的地方形成新的疲劳源,进而引起滚动体的非正常运转,循环往复的载荷会促进滚动体与外圈剥落区域的磨损,造成剥落。
对外圈滚道剥落区域的白色“蝶形”组织进行观察,“蝶形”组织SEM形貌如图4所示,由图4可知:“蝶形”组织内部含有较多微裂纹,内部裂纹沿着“蝶形”组织与基体的交界处或“蝶形”组织内的碳化物扩展,且随着“蝶形”组织的双翼扩展,多处裂纹存在树枝状分叉现象。
对白色“蝶形”组织与附近基体组织进行能谱分析,面扫描结果如图5所示。“蝶形”组织及附近基体元素质量分数如表1所示,由表1可知:“蝶形”组织元素组成与基体无明显差异,表明“蝶形”组织在形成过程中不存在元素的偏聚,基体之间无明显的元素迁移现象。
采用聚焦等离子束法(FIB),沿白色“蝶形”组织宽度方向制取试样,截取的试样包括基体材料和白色“蝶形”组织。基体与白色“蝶形”组织的透射电镜形貌如图6所示,可清晰地看出白色“蝶形”组织与基体是由约5nm到数十纳米的黑色纳米晶和灰色结构组成的,呈现多晶状态;白色“蝶形”组织的选区斑点衍射图表明白色“蝶形”组织是由纳米级的α铁素体颗粒组成的。
1.3金相检验
垂直于外圈剥落区周向方向以及滚珠和内圈的纵向方向截取试样,将试样镶嵌、磨抛后,置于4%(体积分数)的硝酸乙醇溶液中。在光学显微镜下观察试样,发现外圈滚道存在类似蝴蝶状的白色“蝶形”组织,长度为0.3~0.6mm,这些白色“蝶形”组织大多与滚道周向呈45°角,内圈以及滚动体的显微组织正常,由回火马氏体组织与细小碳化物组成。轴承组件的显微组织形貌如图7所示。
制取外圈、滚珠截面的金相试样,依据GB/T10561—2005《钢中非金属夹杂物含量的测定标准评级图显微检验法》进行非金属夹杂物含量的测定,结果均满足技术要求,夹杂物等级为0.5级。外圈与滚珠剥落区附近未见异常的夹杂物堆积,外圈与滚珠夹杂物微观形貌如图8所示。
1.4硬度测试
对“蝶形”组织和基体进行维氏硬度测试,结果如表2所示。由表2可知:“蝶形”组织的硬度比基体高160HV。载荷对组织的硬度也会产生影响,高硬度的“蝶形”组织会破坏基体之间的变形协调性,随着滚动体的运转,基体易形成疲劳裂纹,加快剥落的过程。
02 综合分析
滚动轴承的外圈以及滚动体表面发生严重剥落,损伤区域呈碾压磨损形貌,局部可见疲劳条带,轴承外圈以及滚动体发生接触疲劳剥落。接触疲劳剥落是零件的表面或次表面在周期性的接触应力下形成
裂纹,引起表面材料去除的现象,其形貌特征主要以剥落为主。疲劳条带是裂纹扩展至一定距离后形成的,因此在接触疲劳载荷作用下,接触区域形成的巨大切应力致使次表面形成微裂纹,在持续作用的循环应力下,次表面的裂纹不断扩展直至表面剥落。
金相检验结果发现,轴承外圈次表面区可见较多成片分布的“蝶形”组织,较大的“蝶形”组织长度可达0.2mm,部分“蝶形”组织上可见细小的微裂纹。在对白色“蝶形”组织进行分析时,发现“蝶形”组织由体心立方结构的α铁素体纳米晶以及非晶相组成,晶粒的细化增加了“蝶形”组织的硬度,维氏硬度测试结果进一步验证了白色“蝶形”组织的硬度远高于基体。“蝶形”组织与基体组织的成分未见明显差异,说明“蝶形”组织为基体的变异组织。
目前研究结果表明,以下两种因素均可能会导致“蝶形”组织:①轴承承受较大的接触应力;②轴承内部存在缺陷。白色“蝶形”组织是在载荷试验后产生的,且在对外圈滚道显微组织进行非金属夹杂物评定时,未见异常的夹杂物形态。此外,“蝶形”组织的长度方向与接触疲劳中的剪切应力方向(45°)接近,与载荷作用下次表面的循环交变剪切应力密切相关。因此,“蝶形”组织是在循环接触载荷作用下,由塑性应变累积形成的,每一次循环作用产生的塑性变形都会伴随着显微组织的滑移,并累积至一定程度,导致显微组织结构的变化。“蝶形”组织一方面割断了材料的连续性,降低了材料的抗疲劳能力;另一方面,“蝶形”组织的硬度高,脆性大,变形协调能力差,在外力作用下会引起应力集中,可能成为疲劳裂纹源,致使材料发生剥落。
03 结论
(1)载荷试验对轴承的外圈、内圈、滚动体、保持架都造成了一定程度的损伤。外圈以及滚动体发生剥落,内圈、保持架有周向划痕和凹坑,产生原因为塑性变形以及磨粒磨损。
(2)金相检验发现轴承外圈剥落区域存在白色“蝶形”组织,表明轴承材料组织受到了疲劳损伤。白色“蝶形”组织是具有高硬度的纳米细晶组织,与基体的硬度差异较大,导致在其边缘以及内部产生疲劳裂纹。“蝶形”组织是滚道次表面组织疲劳损伤的产物,其破坏了基体组织的连续性,降低了材料的均匀变形能力,在与基体组织的界面位置形成应力集中,降低了轴承的疲劳性能,萌生了疲劳裂纹,在循环往复应力的作用下,裂纹不断扩展,直至材料表面发生剥离,导致材料发生接触疲劳损伤。
(3)高载荷下的轴承失效模式以接触疲劳失效为主,还有塑性变形、磨损,在这些因素的共同作用下,轴承发生损伤。
免责声明:本网站所转载的文字、图片与视频资料版权归原创作者所有,如果涉及侵权,请第一时间联系本网删除。
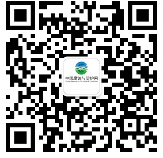
官方微信
《腐蚀与防护网电子期刊》征订启事
- 投稿联系:编辑部
- 电话:010-62316606
- 邮箱:fsfhzy666@163.com
- 腐蚀与防护网官方QQ群:140808414