常减压蒸馏装置作为炼油厂原油加工的龙头装置,其长周期稳定运行能力决定了炼厂是否能够“安稳长满优”运行。随着炼厂加工原油的劣质化趋势不断加重,常减压蒸馏装置,特别是常压塔顶系统低温部位的设备和管线,腐蚀现象尤为突出,已成为行业难题和痛点。 常减压蒸馏装置工艺流程
大量的工程经验和实践表明:高温腐蚀通过材质升级通常能够取得比较好的腐蚀控制效果,而低温腐蚀情况则比较复杂。由于低温腐蚀引起的泄漏事故频发,严重时甚至会引发非正常停工,再加上近年加工的原油含氯量越来越高,因此,低温腐蚀受到的关注程度更高。
常压塔顶常见的腐蚀类型 腐蚀控制综合设计技术 1 工艺流程的优化设计 塔顶回流设置 早期塔顶回流主要采用一级冷回流的方式,返塔温度约40 ℃,造成返塔部位局部过冷产生凝结水,致使塔盘、塔壁、支撑件等出现高浓度HCl,进而产生严重腐蚀。近几年,通过摸索、实践,新建装置均推荐采用两段冷凝冷却的二级热回流系统,取得了较好的防腐效果。 设备和管线对称布置 图1 某炼厂常压塔顶挥发线至换热器管线介质流向及支撑情况 图2 常压塔顶支线管线不对称 此类问题的最根本解决路线是要在今后的设计中采取常顶换热器和空冷器对称布置的结构,数量取2n台(n取1,2,3等),从设计源头上杜绝偏流的现象。目前,山东南山裕龙岛等项目中已经采取4台常顶换热器对称布置的结构,以期能够改善偏流对塔顶腐蚀造成的影响。 合理选择设备形式 缠绕管式换热器换热管直径小,易堵塞,且清洗困难,管内介质必须具有较高的清洁度。板式换热器污垢系数小,但板片薄、间隙小、易堵塞,在塔顶腐蚀较严重的位置不太适合选用。在选用板式换热器的炼厂已有发生多次腐蚀泄漏的案例。 合理布局设备种类 常压塔顶挥发线介质直接进空冷器对防腐不利,应在空冷器前设置换热器。 某炼厂最初常压塔顶回流系统采用换热器、空冷器、后冷器、回流产品罐后返塔的路线,2011年大检修时发现塔体和内构件基本良好,塔盘干净,仅顶循返塔处有蚀坑,部分塔盘脱落。此次大检修后,去掉了原来空冷器前的换热器。至2015年大检修时发现,塔体腐蚀较2011年明显加剧,塔壁、焊缝、回流管腐蚀严重,塔盘严重塌陷,溢流堰腐蚀掉光,整体蚀坑明显。如图5所示,去掉塔顶换热器后,塔顶腐蚀后移至空冷器、返塔系统中,在循环过程中加剧了整个塔顶系统的腐蚀。值得一提的是,空冷器泄漏为外漏,因此危害更大。 2 腐蚀流程图设计 塔顶腐蚀是一个系统问题,同一类型的腐蚀可能发生在设备和管道等介质流经的任何地方,因此提出了腐蚀流程的理念。基于上述对常压塔顶系统的工艺和腐蚀现状分析,可以取常顶作为一个闭环回路,简化工艺流程进行腐蚀回路分析,绘制腐蚀流程,如图6所示,图中不同颜色的线条代表不同的腐蚀机理。根据常压塔顶不同部位的温度(由图中的数字表示,单位为℃)、介质状态等,分析出每台设备、每段管线的腐蚀机理,将具有同一腐蚀机理的设备和管道用相同的颜色标识,可以将塔顶系统进一步分区细化,很直观地标示出不同部位的腐蚀机理,便于后续的腐蚀管理。 图6 常压塔顶腐蚀流程 经分析,常顶循系统、常压塔顶(含塔顶壳体及5层塔盘)、塔顶挥发线至原油-常顶油换热器前管线主要为低温HCl-H2S-H2O腐蚀和NH4Cl盐腐蚀。此段管线和设备正好处于盐酸露点温度范围内,在第一滴液相水出现位置可形成pH接近于1的高浓度HCl。加之此段管线水量较少且流态不均,所以HCl-H2S-H2O腐蚀比较严重。同时,管线和设备所处温度正好处于NH4Cl结盐范围,易形成铵盐沉积,堵塞换热器管束,使换热能力下降、压降升高。当水蒸气冷凝使铵盐潮解时,设备和管线又会形成垢下腐蚀。回流罐水包及含S污水线由于水相中溶解有大部分氯化物和部分硫化物,HCl-H2S-H2O腐蚀也比较严重。 原油-常顶油换热器至常顶回流罐间的设备和管线、常顶回流罐回流线、常顶气/油至轻烃回收线主要为低温HCl-H2S-H2O腐蚀和酸性水腐蚀。此段设备和管线仍存在HCl-H2S-H2O腐蚀,但是由于介质经过原油-常顶油换热器后,水相逐渐增多并且和介质混合均匀,使得介质的酸性减弱,对后续的系统主要造成均匀腐蚀。 塔顶“三注”系统管线和后冷器的管侧主要是水系统的腐蚀。由于注水、注剂以及换热器使用循环水水质较差,水质管理不达标,使得注水、注剂、循环水中的Cl-、NH+4等有害离子超标,造成原油中水相腐蚀。 3 材料选择流程图设计 材料选择流程图(MSD)是在工艺流程图、物料平衡、腐蚀流程图的基础上,对装置主要过流部件(静设备、管道、加热炉管、泵等)选材进行指导的一种示意图。目前,国外工程公司或专利商的MSD基本只做到选材这一步。 4 关键设备材料防腐 常压塔顶选材 早期常压塔顶材料选用410S、Monel及其复合板,但随着原油劣质化越来越严重,原来的塔顶选材已经不能满足目前加工劣质油品的要求。由于塔顶存在NH+4,易与合金中的Cu形成铜络合物,因此应尽量不选用含铜量高的Monel材料。 410S本身耐盐酸腐蚀能力较差,如果原油中Cl含量较高,会导致其出现腐蚀严重甚至脱落的现象,如图8(a)所示,未使用表面超高性能耐蚀抗焦膜层技术(CTS)的410S塔盘腐蚀严重,甚至无法使用一个周期。 因此,对于常顶的几层塔盘,应优先采用超级奥氏体不锈钢UNS N08367或合金625,顶部筒体和封头可采用其复合板形式。除采用高等级合金外,塔盘还可以采用不锈钢+CTS的表面处理技术。该技术能将表面天然形成的几纳米厚的Cr2O3膜增至500 nm,极大增加塔盘在常压塔HCl-H2S-H2O腐蚀环境的耐蚀能力。采用该技术处理后的塔盘能有效使用1~2个周期,已在几十家炼厂得到成功应用。使用CTS技术后的410S塔盘如图8(b)所示。 图8 某炼厂410S塔盘使用CTS技术前后腐蚀形貌对比 原油-常顶油气换热器选材 常顶空冷器选材 常顶后冷器及常顶回流罐选材 常顶后冷器和常顶回流罐腐蚀环境轻微,仅需适当考虑HCl-H2S-H2O腐蚀。后冷器的塔顶介质侧采用碳钢+6 mm腐蚀裕量(CA)+焊后热处理(PWHT),回流罐采用镇静钢(KCS)+410S复合板即可。由于后冷器循环水侧水质较差,换热器管束和管板材料仍需采用双相钢。 5 工艺防腐设计 电脱盐系统深度脱盐脱水 注水 为了缓解塔顶结垢和露点腐蚀,需要在塔顶系统连续注水,以稀释酸性腐蚀产物,缓解结垢堵塞、垢下腐蚀和酸腐蚀。塔顶腐蚀的控制情况与注水水质和注水量有很大的关系,设计单位应当对注水水质、注水位置、注水量及注水方式提出要求。 注水水质指标应满足中国石化《炼油工艺防腐蚀管理规定》实施细则(第二版)的通用要求,并需要炼厂定时进行分析和检测。 注水位置主要在塔顶中和剂和缓蚀剂后的挥发线总管上。有时系统中酸含量过高,或者塔顶设备和管线不对称布置导致介质偏流造成腐蚀,则需要在换热器或者空冷器的支管上注水。建议总管连续注水,换热器和空冷器支管根据偏流和腐蚀情况选择连续或间断注水。 常压塔顶操作温度约为140 ℃,塔顶注水大部分会汽化,为保证塔顶有足够量的液态水能够稀释酸和盐,注水量应以确保管道内留有25%的液态水为原则,注水流速则以不产生冲刷腐蚀为宜。 为了保证更加分散均匀的注水效果,推荐雾化喷头+过滤器的可在线拆装设计的注水系统,如图9所示,喷射角度以不直接冲击管壁为宜。同时,为了缓解塔顶换热器管束入口结盐沉积和垢下腐蚀,SEI联合国内知名喷头厂商共同研发了新型注水系统,该系统在换热器管程加装注水喷头,直接喷淋铵盐堵塞的换热管口,直击腐蚀最严重的部位。 图9 可在线拆装雾化喷头的注水系统 注中和剂和缓蚀剂 为了减弱塔顶系统的酸性,常常在塔顶挥发线的注水点之前选择注入中和剂和缓蚀剂。工业上推荐用有机胺作为中和剂,其能与盐酸反应形成低熔点的铵盐,降低pH值。缓蚀剂能在金属表面形成一层保护性的化学吸附膜,阻止腐蚀介质和金属内壁的接触,从而减缓腐蚀。 为了保障防腐效果的持续性,建议连续注入。由于注入量少,为了保证更加分散均匀的注剂效果,推荐采用雾化喷头+叶轮+过滤器的可在线拆装设计的注剂系统,如图10所示,逆向注入,喷射角度以不直接冲击管壁为宜。 6 在线除盐系统设计 在线除盐系统主要是为了解决塔顶循系统低温腐蚀的结盐堵塞问题。由于塔顶系统连续注剂并不断循环,使得氯化物、氮化物、硫化物等进入顶循系统,且抽出温度和返塔温度正好处于HCl-H2S-H2O腐蚀和铵盐结晶的温度范围内,易造成顶循系统及塔顶的结垢和腐蚀。 通过引入在线除盐系统,如图11所示,将一部分顶循介质抽入在线除盐系统,并将净化水通入混合器中,可以将顶循系统中的含Cl、含S油气与水充分混合。之后介质经过萃取器,Cl-、HS-被抽提到水相中,经过油水分离器后将盐洗出。干净油品从分离器抽出后继续返塔,可以对塔盘进行洗涤,减少塔盘和塔壁的结垢。 7 在线腐蚀监检测技术 在线腐蚀监检测技术对于及时发现隐患并预警,同时适时进行工艺操作和防腐方案的调整、实现装置“安稳长满优”运行至关重要。腐蚀监检测技术主要有管道测厚技术、介质腐蚀成分分析、腐蚀探针、腐蚀挂片等常规技术,也有电场矩阵测厚、电感探针、脉冲涡流、超声导波、声发射、氢通量等检测新技术。 设计阶段应该将在线腐蚀监测技术纳入考虑范围,在材料流程、腐蚀流程中推荐监测技术和位置,并在PDMS三维模型中体现,如图12所示。 电场矩阵测厚技术(FSM) FSM通过全周向矩阵方式排列的电极检测一切可能引起管道电阻变化的因素(减薄、裂纹等),外加电场根据电阻分布会呈现对应的分布特征,通过电场变化可识别管道区域腐蚀发展,监测管道剩余壁厚。 该技术适用于全周向管道风险监测和在线风险识别。FSM设备在管道的模拟布点和实物如图13所示。FSM技术能同时检测某一面积区域内局部腐蚀和裂纹的分布,这是其他技术无法比拟的。其安装简单、检测效率高、测量精度可达壁厚的0.5%。常压塔顶系统一般在注水/注剂点对侧的直管段、注水/注剂点后弯头、塔顶一级换热器出口弯头、塔顶空冷器出口弯头等位置实施FSM技术。推荐采用无线传输方式进行监测。 电感探针技术 电感探针是通过将探针插入流动介质中,将金属探针头的腐蚀损失转换成阻抗变化,实时测量探针腐蚀深度和速度,从而判断设备和管线的腐蚀速率、介质腐蚀性变化趋势和工艺防腐效果的一种测厚技术。 某炼厂使用的电感探针设备如图14(a)所示。其响应速度快,能较为准确地反映腐蚀速率的变化,常与腐蚀挂片连用。过去电感探针常用有线传输模式,在生产装置内需专门布线和搭建设备。随着传输技术的更新,传输模式逐渐由有线向无线迈进,并直接通过无线传输与DCS设备连接,方便全厂防腐蚀工作的统一管理,如图14(b)所示,目前这种模式在马来西亚项目已经投入使用。常压塔顶系统一般在注水/注剂点后、塔顶一级换热器出口直管段、塔顶回流返塔直管段、常顶循抽出管道直管段等位置实施电感探针技术。 8 其他腐蚀控制设计技术 控制流速 关注细节设计 结 语 常减压装置作为整个炼厂的龙头装置,其防腐工作的重要性可见一斑。其中常压塔顶系统的低温腐蚀尤为严重,应受到足够的重视。为了尽可能缓解塔顶系统的腐蚀情况,单一手段的防腐方案达不到理想的防腐蚀效果,应采用腐蚀控制综合设计技术,在设计阶段就考虑布局塔顶系统腐蚀控制方案,系统性、全方位、多维度地采取工艺防腐、材料防腐、监检测系统等综合控制手段,才能真正搭建起常压塔顶的防腐网络,帮助炼厂提质增效。
免责声明:本网站所转载的文字、图片与视频资料版权归原创作者所有,如果涉及侵权,请第一时间联系本网删除。
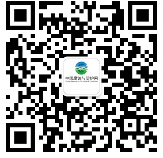
官方微信
《腐蚀与防护网电子期刊》征订启事
- 投稿联系:编辑部
- 电话:010-62316606
- 邮箱:fsfhzy666@163.com
- 腐蚀与防护网官方QQ群:140808414