高熵合金是指由5种或更多的主元元素以等摩尔/近等摩尔比例组成的多组元合金。尽管由多元素混合而成,高熵合金却往往具有简单固溶体结构,并具备扩散迟滞、鸡尾酒效应、晶格扭曲效应、高熵混合效应等4种独特的性质。这些特质又使高熵合金进一步表现出高强度、耐摩擦磨损、耐腐蚀等优良性能,在工程领域表现出极为广阔的应用前景[1,2]。
大多数高熵合金具有单一相结构,如体心立方(BCC),面心立方(FCC)等。一般而言,BCC相具有较高的强度,但塑性相对较低;而FCC相则刚好相反,提升塑性的同时牺牲了强度。这种由单一相组成引起的强度-塑性矛盾,极大限制了高熵合金的发展。此外,单一固溶相可能会因为流动性差而加剧铸造缺陷。为了解决这一难题,Lu等[3]在2014年引入共晶合金的思想,提出了双相共晶高熵合金的概念,以期同时提高材料的强度和塑性。所开发的AlCoCrFeNi2.1合金具有高熵固溶状态的BCC和FCC双相结构。前者强度高,后者塑性高,两者呈现层片状交替出现,实现软硬相交替。较硬的沉淀相提高了合金的整体强度,而沉淀相和基体相的协同变形则提高了合金的整体塑性,因此兼具共晶和高熵的优点,表现出了极为优异的强度和塑性结合[3]。AlCoCrFeNi2.1合金室温下即表现出高达944 MPa的抗拉强度和25.6%的延伸率,而当温度升高至600和700 °C时,该共晶高熵合金仍能表现出806 MPa-33.7%和538 MPa-22.9%的高强度和塑性结合[3]。此外,共晶高熵合金具有极为优异的铸造性能。合金在铸造制备过程中具有良好的流动性,凝固后的组织、成分相对均匀,且铸造缺陷少,从而实现大尺寸零件制备。即便是冷却速率较低的铸造方式,仍能获得大量纳米级层片状结构。上述优势,使得共晶高熵合金在工程领域有着极为广泛的应用前景[4]。
1 共晶高熵合金的结构、分类及腐蚀问题
共晶高熵合金可以通过熔铸、溅射沉积等手段合成块体或涂层。第一代共晶高熵合金由铸造方式制备,成分为AlCoCrFeNi2.1。双相典型结构如图1[5]所示。FCC (L12)和BCC(B2)相的成分含量可在20%~80%范围内变化[6],每个相的宽度则在几百纳米到几微米范围[7]。随后,研究人员通过调整各主元素比例,又开发出了诸如Al1.5CoCrFeNi、Al16Co41Cr15Fe10Ni18等其他五元合金[8,9]。出于降低成本、促进推广的考虑,也有研究者提出无Co的四元高熵合金,如AlCrFeNi3.1和AlCrFe2Ni2.1等[10]。此外,还可以通过添加少量Mn、Cu等过渡元素,Ti、W、Nb等难熔金属,以及Si等小原子半径元素,进一步调控合金微观组织结构和性能,形成多元共晶高熵合金。而随着发展,共晶高熵合金的组织也演化出层片状、棒状、向日葵状等形貌[11]。未来研究,应探索3D打印等更为先进的制备手段,并明确制备工艺与结构演化的关系[12~14]。
图1 共晶高熵合金AlCoCrFeNi2.1的组织与相分析[5]
Fig.1 SEM image (a), EBSD image (b), EDS elemental mappings (c) and XRD pattern (d) of eutectic high entropy alloy AlCoCrFeNi2.1[5]
经过后续不断发展,共晶高熵合金的成分及组元已经极为丰富[11]。按组成化学元素的个数分类,可分为四元、五元、六元和多元共晶高熵合金。按照组成相分类,共晶高熵合金则可以分成FCC相 + BCC相[15],FCC相+Laves相[16,17],双重BCC相 (BCC1 + BCC2)[18],HCP相 + BCC相[19],L12 (FCC)相 + BCC相[20],FCC相 + 金属间化合物相[21]等。由于凝固过程的复杂性和扩散限制特征,目前已报道的共晶高熵合金大多为双相结构,少量为三相结构。共晶高熵合金的系统分类可以参照其他文献[11,22,23]。
由于实现了微米级别的双相交替复合分布,共晶高熵合金具有极高的强度和塑性。部分高熵合金的抗拉屈服强度可达700~800 MPa,而抗拉断裂强度则可高达1200 MPa以上;同时大部分合金断裂应变能保持在10%以上,部分合金甚至超过20%[20,24,25]。双相结构一方面可以提高材料的力学性能,另一方面,则可能影响材料的抗腐蚀性能。合金抗腐蚀主要依靠在腐蚀环境中形成的表面氧化膜。致密、连续、均匀的氧化膜能够有效阻止腐蚀介质进一步侵蚀基体,从而起到保护作用。对于单一物相的材料,在腐蚀的过程中容易形成均匀的氧化膜。对于多物相的材料如共晶高熵合金,则很可能在不同相的表面形成化学成分不尽相同的氧化膜,造成整体表面氧化膜化学成分不一致,形成电偶腐蚀和微电池,从而削弱抗腐蚀能力。
从已有研究报道可知,低温液相腐蚀中,双相结构的确会影响共晶高熵合金抗腐蚀能力,且受测试环境(温度、时间、离子类型和浓度等)和材料本身(结构、热处理过程、表面状态等)等因素影响[6]。但这种双相结构在高温环境下如何影响腐蚀行为,则尚不明确。高温下,共晶高熵合金表面形成何种氧化物?是否因多相结构而形成异质氧化膜?氧化膜的稳定性和保护性如何?又会如何随时间、温度、测试环境而变化?一些相关高熵合金研究组已经开展了相关的研究工作,但到目前为止,仍缺乏一个系统的归纳和梳理。因此,本文系统总结了多种共晶高熵合金的高温腐蚀行为,梳理了对共晶高熵合金腐蚀的关键影响因素,分析共晶结构对高温氧化膜的影响,揭示相关高温氧化机理,旨在为共晶高熵合金的设计和高温应用提供参考和指导。
2.1 高温腐蚀分类及研究现状
高温腐蚀广泛发生于能源动力、石油化工、航空航天等领域[26~28]。按腐蚀介质,可分为高温气相腐蚀和熔盐腐蚀。高温气相腐蚀源自气体分子与金属的反应。氧气通常存在于上述高温环境中,与合金发生氧化反应后,在合金表面生成氧化物,消耗基体元素。除了氧气之外,环境中还可能存在H2O,CO2,HCl,H2S,SO x,NO x 等气体参与反应,影响高温腐蚀过程。一般认为,高温水蒸气不但可以氧化金属,还能引起合金表面氧化物的挥发,以及通过扩散进入氧化膜内部,改变扩散动力学,使得氧化膜疏松多孔[29,30]。CO2除了可能参与氧化反应,还可能通过扩散进入基体引起碳化反应:C原子与Cr、Fe等元素结合,消耗本该参与氧化膜生成的金属,同时大量析出的碳化物会使得合金变脆,塑性降低[31]。而HCl,H2S,SO x,NO x 等气体,则可能不但加剧氧化,还会分别引发合金的氯化、硫化、硝化,加剧腐蚀[32]。目前已有较多关于共晶高熵合金高温氧化行为的报道。
除了气相腐蚀,另一类高温腐蚀是熔盐腐蚀。熔盐作为储热和传热介质,在太阳能热发电、核反应堆等能源动力系统有着大量应用[33]。此外,作为燃烧产物,也在火电厂锅炉管道、航空发动机等系统中广泛存在。熔盐成分包括氯盐、硫酸盐、碳酸盐、氟盐、硝酸盐、氢氧化物以及其他各类熔盐混合物[34]。由于处在高温熔融状态,熔盐离子活度高,与金属反应剧烈,能造成严重腐蚀。共晶高熵合金因其双相结构,更容易受到熔盐攻击而发生电偶腐蚀。但目前,只有少量报道共晶高熵合金的熔盐腐蚀行为[5],后续研究尚需开展。
2.2 高熵合金高温氧化原理
当合金材料暴露在高温空气或其他含氧环境时,合金中活泼且含量较高的元素(Cr,Al等)更容易通过选择性氧化参与成膜。生成的氧化膜能够极大程度地影响合金后续氧化行为。基于气体分子在合金表面吸附、解离、及在氧化膜中的扩散等热力学和动力学行为,Wanger[35]曾在理论上推导氧化增重随时间的变化可遵循线性、抛物线型、立方型、指数型等规律[36]。高温下,高熵合金仍遵循相关热力学和动力学规律。但在具体氧化过程上,又与传统的铁基、镍基高温合金有所差异。具体则包括如下几个方面。
2.2.1 氧化膜成分复杂
在氧化过程,高熵合金不再是单一活泼元素、而是多主元元素参与氧化反应,所形成的氧化膜成分也更为复杂。随着时间延长,往往呈现出多层、多相的特征。合金元素的种类和含量、所形成的氧化物的种类和性质、基体合金的物相结构等因素都会影响氧化过程。
2.2.2 高温腐蚀受多重因素影响
尽管高熵合金因晶格扭曲而具有迟滞扩散效应,但缓慢的扩散速率既能阻止O2-的内扩散,也可能阻碍金属离子外扩散参与保护性氧化膜的生成。特别是对于共晶高熵合金,其双相结构往往导致不同物相生成不同种类的氧化物。而合金元素的种类和活度、氧分压、环境温度、生成物种类、不同氧化物的互扩散等因素,会进一步加剧氧化过程的复杂性。
2.2.3 元素对腐蚀影响较大
前期研究表明,Al和/或Cr两种元素能够通过氧化形成致密的氧化物,并阻碍氧离子的内扩散和金属离子的外扩散,是极为重要的抗氧化元素[37]。Mo,W,V等元素的存在,可能会在一定温度下转变成挥发性氧化物,使得氧化膜变得多孔疏松[38]。精准控制几种关键元素的含量,通过生成特定成分氧化膜,可以起到更好的抗氧化效果。
3.1 已有研究总结
共晶高熵合金起始于AlCoCrFeNi体系,并以此为基准,添加Mn,Mo,Cu,Ti,Si等元素,或减少部分元素,开发出一系列新型合金。同时,研究者们还以AlNbTi体系为基准进行合金设计。相关合金发展示意图如图2所示。元素的添加或减少,很可能影响合金的高温氧化行为。因此,本节总结了AlCoCrFeNi以及AlNbTi体系共晶高熵合金的成分、结构、氧化行为,分析了氧化过程的主要影响因素(温度、气氛、时间),并对主要发现进行了总结。
图2 共晶高熵合金研究路线及添加元素的作用
Fig.2 The research outline of eutectic high entropy alloys and effects of added alloying elements
3.1.1 AlCoCrFeNi体系
作为最经典的成分,AlCoCrFeNi2.1是目前被研究最多的共晶高熵合金。该共晶高熵合金在多个温度区间的氧化行为都得到了系统研究。例如,Saha[39]测定了AlCoCrFeNi2.1在950和1000℃空气中的氧化动力学和腐蚀产物。在两个温度下,合金在100 h后均发生加速腐蚀,腐蚀产物主要为Al2O3和Fe2O3。随着氧化时间的增加(25~500 h),主要腐蚀产物在Al2O3和Fe2O3之间转换。
Vo等[40]则分析了该合金在500~900℃初始阶段(0~10 min)的氧化行为,主要腐蚀产物变成了Al2O3和Cr2O3。Al2O3在BCC相表面,Cr2O3在FCC相表面,且往往在开始氧化的几分钟内就会产生。在温度≤ 700℃时,FCC相和BCC相表面的氧化物生长速率并不相同。而在800℃或者更高温度时,由于高温促进扩散,两相在氧化速率上的差别不再明显。在随后的摩擦磨损实验中,Cr2O3作为主导氧化物,能在氧化初期就通过基体磨损而促使基体表面形成硬化磨床,进而提高基体随后在稳定期的抗磨损和破坏能力[40]。
Jadhav等[41]研究了FeCoCrNiAl和FeCoCrNi2Al合金在1050℃空气中的氧化性能,并与传统NiCrAlY合金对比。两种共晶高熵合金均为FCC + BCC结构。由于在氧化过程中生成了致密、连续、且更薄的Al2O3氧化膜(< 2 μm),两种高熵合金的抗腐蚀能力均优于NiCrAlY合金(氧化膜厚度为4 μm)。研究者认为,基体中Al含量> 9%之后,将有助于形成Al2O3氧化膜[41]。
一定条件下,Cr和Al都会通过氧化参与共晶高熵合金AlCoCrFeNi2的氧化膜生成,且相比之下,Al提升抗腐蚀能力的效果更为明显。Kumar等[42]通过控制Al和Cr的含量,制备出AlCoCrFeNi2、Al1.5CoCrFeNi2、AlCoCr1.5FeNi2和Al1.5CoCr1.5FeNi2 4种共晶高熵合金。经过1050℃下10次热循环氧化,Al1.5CoCrFeNi2合金表现出最小的腐蚀速率。提高Al或Cr的含量,有助于形成薄且连续的Al2O3或Cr2O3,但相比之下,Cr2O3氧化膜更容易脱落,故其保护性弱于Al2O3[42]。
稀土元素同样有助于提高合金的抗氧化性能。AlCoCrFeNi2.1合金在1000~1100℃形成了以Al2O3为主的氧化膜[43],但该氧化膜极易剥落。原因在于,如此高温下,金属离子外向扩散较快,会在氧化物与合金基体界面附近产生明显的Kirkendall孔洞,破坏了氧化膜与基体的连接[43]。加入0.05%(原子分数)的Y能有效抑制界面处孔洞的生成,从而提高氧化膜与基体的连接附着能力。而当0.025%(原子分数)Y-Hf共掺杂后,通过O内扩散生成的柱状Al2O3生长速率显著降低,同时Al2O3与金属基体界面的缺陷浓度也降低,氧化层与基体的附着度增加[44]。进一步研究表明,降低合金晶粒界面的S浓度和缺陷生成是调控共晶高熵合金抗腐蚀的关键因素[44]。
除了高温气相腐蚀,也有学者研究了熔盐腐蚀行为。在450和650℃的NaCl-KCl-MgCl2共晶熔盐中,AlCoCrFeNi2.1共晶高熵合金的抗熔盐腐蚀能力远高于双相钢DSS 2205[5]。在450℃,前者的腐蚀速率仅为1 mm/a,而后者高达8 mm/a。当温度升高到650℃,两者的腐蚀速率差则进一步拉大,分别为9和20 mm/a。在高温熔盐含Cl环境中,双相钢表面倾向于形成富Cr或富Fe的氧化物,但二者极易在熔融氯盐中溶解。而对于AlCoCrFeNi2.1合金,尽管其Cr含量与DSS 2205基本持平(20%左右),但因其含有更多的Al作为牺牲元素与Cl反应,阻止了Cr的流失,进而降低了合金腐蚀速率。此外,扫描Kelvin探针(SKP)分析表明,AlCoCrFeNi2.1合金中FCC相(Fe-Cr-Co)和BCC相(Ni-Al)之间的电位差 (50 mV)小于DSS 2205中FCC相(γ-Fe)和BCC相(α-Fe)之前的电位差(65 mV),因而电偶腐蚀效应更弱[5]。
3.1.2 AlCrFeNiTiMn体系
由于Co价格较高,Nong等[45]尝试用相对便宜的Ti和Ti + Mn替代,并通过真空电弧熔炼制备了AlCrFeNiTi和AlCrFeNiTiMn0.5合金。XRD结果表明,所制备的合金含有双重BCC相(BCC1 + BCC2),以及少量Laves相。900℃下氧化100 h后,两者氧化增重均呈现指数增加。AlCrFeNiTi合金的主要氧化产物为外层TiO2和内层Al2O3。AlCrFeNiTiMn0.5合金则还多了Mn2O3中间层[45]。Mn2O3的存在削弱了TiO2和Al2O3的键合力,从而加速了氧化物剥落。因此,Mn的存在似乎并不利于提高共晶高熵合金的抗氧化能力。
3.1.3 AlCoFeNiMo体系
有研究人员将AlCoCrFeNi中的Cr替换为Mo,并分析了Mo含量变化对Al19Fe20 - x Co20 - x Ni41Mo2x (x = 0, 1, 2)合金的影响[46]。该合金表现出B2 + FCC的双相结构。B2相富含Al和Ni,而FCC相富含Fe、Co和Mo。腐蚀研究表明,x = 0时(无Mo),合金生成了疏松多孔的(Fe, Co, Ni, Al)3O4尖晶石型氧化层,表现出最高的氧化速率。而随着2%Mo (x = 1)的加入,Al的选择性氧化变得明显,合金表面生成了两种更为致密和具有保护性的含Al尖晶石。但当Mo含量达到4% (x = 2)时,由于Mo本身高温稳定性差,形成挥发性氧化物,破坏了氧化膜的完整性,导致腐蚀增加,伴有CoO的生成。因此,可以推论,添加适量Mo有助于提高抗腐蚀性能。
3.1.4 AlCoCrFeNiCu体系
针对AlCoCrFeNiCu体系,有研究人员电弧熔炼了Al x CoCrFeNiCu (x = 0, 0.5, 1, 1.5, 2)系列合金。研究表明[47],Al的增加促进晶粒细化,并使合金结构由FCC(FCC1 + 富CuNi的FCC2)相向BCC相转变。经过1000℃/100 h氧化后,合金表面形成4种氧化物,分别是Al2O3、Cr2O3、(Co, Ni, Cu)(Al, Cr, Fe)2O4以及(Co, Ni, Cu)O。几种合金均遵循抛物线氧化规律。Al含量的增加,提高了Al2O3在氧化物中的比例。鉴于Al2O3比Cr2O3更具有保护作用,合金氧化抛物线速率常数显著降低,抗腐蚀性能得到提高。
3.1.5 AlCoCrFeNiTiSi体系
在AlCoCrFeNi体系中添加了0.1%的Ti和Si后,合金仍为FCC + BCC的双相结构,但抗氧化性能得到进一步提升[41]。在FeCoCrNiAl中,0.1%Ti的加入使得富Fe-Cr的FCC相和富Ni-Al的BCC相均发生晶粒细化,进而促进Al向外扩散形成Al2O3,提高抗氧化性能。而在FeCoCrNi2Al中,0.1%Ti和0.1%Ti + 0.1%Si并没有产生细晶作用,但却通过增加混合焓稳定了固溶相,进而提高抗氧化能力。值得注意的是,0.1% Ti和Si的加入还同时提高了合金的机械强度并降低了热膨胀系数[41]。
3.1.6 CoCrFeNbNiSi体系
有研究组通过激光熔覆在Cr-Mo-V钢上制备了CoCr2FeNb0.5Ni/CoCr2FeNb0.5NiSi0.2涂层,并研究了其在800℃的N2-44%CO2-6%H2O环境中的腐蚀行为[48]。共晶高熵合金涂层包含富Cr的FCC相和富Nb的Laves相。由于激光熔覆工艺的急速效应,两相实现了纳米级别的层片状排布。由于Cr相对含量较高,且热力学上更容易被氧化,两种合金的主要氧化物均为Cr2O3。Cr向外扩散参与Cr2O3生成的过程中,会生成Cr3O副产物,并在氧化物/基体界面留下Kirkendall孔洞。这些孔洞中的气体会参与氧化基体。添加Si后,Cr与Si会共同形成无定形(Cr, Si)O x 氧化层,抵抗Kirkendall孔洞引起的腐蚀,降低了合金的氧化增重。同时,Si会与Cr一起形成(Cr, Si)O氧化层,进一步提高抗高温腐蚀能力。相关高温腐蚀机理如图3所示。
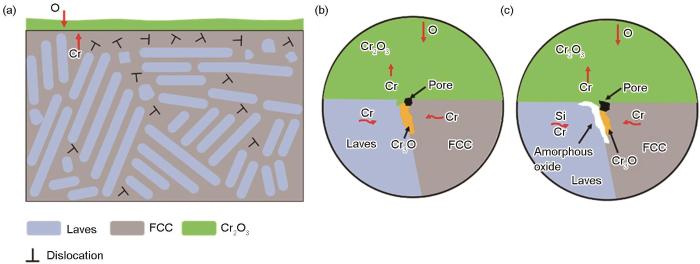
图3 CoCr2FeNb0.5NiSi0.2在800℃下N2-44%CO2-6%H2O气氛中的氧化机理图[48]
Fig.3 Schematic diagrams of oxidation mechanism of CoCr2FeNb0.5NiSi0.2: (a) growth of oxide scale, (b) formation of CrO3 at the scale/substrate interface, (c) formation of pores[48]
3.1.7 TiNbMoAlSi体系
Li等[49]研究了TiNbMo0.5Al0.225Si x (x= 0.1, 0.25, 0.4, 0.55)在1000℃空气中的氧化行为及Si含量对腐蚀的影响。由于MoO3挥发或Nb2O5引起的氧化膜内应力,TiNbMo0.5Al0.225 (物相为BCC + (Nb, Ti)5Si3)共晶高熵合金在氧化超过36 h后出现明显的裂纹和氧化物剥落。而随着Si的加入,合金的抗氧化能力提高,氧化动力学遵循抛物线规则。氧化层TEM截面分析和理论计算表明,硅化物(Nb, Ti)5Si3的存在及分布状态对抗氧化性能影响极大。整个氧化物形成过程如下:初始阶段,O通过BCC相及BCC/(Nb, Ti)5Si3相界面向内扩散,并与合金中的Al和Ti等活泼金属反应,生成零散分布的Al2O3与连续成膜的TiO2。随着氧化进行,(Nb, Ti)5Si3中的Ti2+和Nb5+也会参与氧化并与TiO2反应,生成TiNb2O7 + TiO2/TiNb2O7 + Nb2O5等内层氧化物。Mo的氧化物会在氧化膜/金属基体界面富集[49]。最终的氧化膜结构如图4所示。
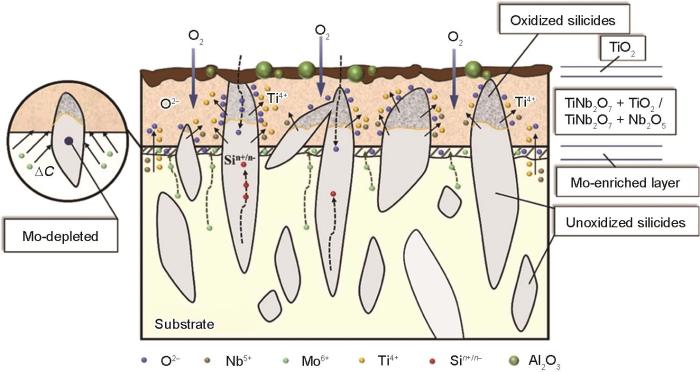
图4 TiNbMoAlSi共晶高熵合金在1000℃的氧化机理示意图[49]
Fig.4 Schematic diagram of oxidation mechanism of TiNbMoAlSi at 1000oC[49]
3.1.8 AlCrNbTiZr体系
Yurchenko等[50]制备了AlCrNbTiZr系列共晶高熵合金(Al23Cr20Nb15Ti32Zr10,Al28Cr20Nb15Ti27Zr10,Al33Cr20Nb15Ti22Zr10),均由富Nb-Ti的B2相和富Al-Cr-Zr的C14 Laves相构成。随着Al和Ti的增加,一方面,氧化层中Al2O3及TiO2含量增加,抗腐蚀性提高;但另一方面,Laves相含量同样增加,氧化膜生长应力增高,剥落的几率增大。在800~1000℃,Al23Cr20Nb15Ti32Zr10表现出近似抛物线的氧化行为。腐蚀过程由Ti的外向扩散和O的内向扩散共同控制。3种共晶高熵合金的腐蚀产物主要为TiO2,同时包含少量Al2O3、CrO2、Ti0.4Al0.3Nb0.3O2和Zr0.5Al0.5O2。
为了方便检索以及对比分析相关数据,表1列出了目前已有的不同体系共晶高熵合金高温腐蚀研究数据。
表1 不同体系共晶高熵合金的高温腐蚀总结
Table 1
Material | Preparing Method | Phase | ToC | th | Corrosion product | Direct mass change mg·cm-2 | Environment | Ref. |
---|---|---|---|---|---|---|---|---|
AlCoCrFeNi2.1 | Casting | B2 + L12 | 950 | 500 | Fe2O3 + Al2O3 | 51 | air | [39] |
1000 | 500 | Fe2O3 + Al2O3 | 133 | |||||
Al0CoCrCuFeNi | Arc | FCC | 1000 | 100 | Cr2O3 + spinel + (Co, Ni, Cu)O | 1.32 | air | [47] |
Al0.5CoCrCuFeNi | melting | Al2O3 + Cr2O3 + spinel +(Co, Ni, Cu)O | 0.73 | |||||
Al1CoCrCuFeNi | FCC + | Al2O3 + Cr2O3 + spinel +(Co, Ni, Cu)O | 0.33 | |||||
BCC | ||||||||
Al1.5CoCrCuFeNi | Al2O3 + Cr2O3 + spinel +(Co, Ni, Cu)O | 0.25 | ||||||
Al2CoCrCuFeNi | Al2O3 + Cr2O3 + spinel +(Co, Ni, Cu)O | 0.235 | ||||||
FeCoCrNiAl | MAS and | FCC + | 1050 | 100 | Al2O3 | 0.38 | air | [49] |
FeCoCrNiAlTi0.1 | hot | BCC | 0.37 | |||||
FeCoCrNiAlTi0.1Si0.1 | pressing | 0.34 | ||||||
FeCoCrNi2Al | 0.4 | |||||||
FeCoCrNi2AlTi0.1 | 0.36 | |||||||
FeCoCrNi2AlTi0.1Si0.1 | 0.31 | |||||||
MCrAlY | 0.63 | |||||||
Al19Fe20Co20Ni41 | Arc | B2 + FCC | 800 | 100 | spinel1 + spinel2 | 4.25 | air | [46] |
Al19Fe19Co19Ni41Mo2 | melting | spinel2 + spinel3 | 1.95 | |||||
Al19Fe18Co18Ni41Mo4 | spinel2 + spinel3 + CoO | 1.3 | ||||||
AlCoCrFeNi2.1 | Arc melting | BCC + | 500 | 0.17 | Cr2O3 + Al2O3 | - | air | [40] |
+ chill | FCC | 600 | - | |||||
casting | 700 | - | ||||||
800 | - | |||||||
900 | - | |||||||
AlCoCrFeNi2.1 | Arc melting | FCC(L12) + BCC(B2) | 450 | 24 | CrCl2 + AlCl2 | 20 | Molten NaCl-KCl-MgCl2 | [5] |
650 | 39 | |||||||
TiNbMo0.5Al0.225Si0.1 | Vacuum |
BCC + γ- (Nb, Ti)5Si3 |
1000 | 60 | TiO2 + TiNb2O7 + SiO2 | 68.5 | air | [49] |
TiNbMo0.5Al0.225Si0.25 | melting | 110.93 | ||||||
TiNbMo0.5Al0.225S0.4 |
Si+BCC+ γ-Nb,Ti)5Si3 |
TiO2 + TiNb2O7 + Al2O3 | 75.71 | |||||
TiNbMo0.5Al0.225Si0.55 |
BCC + β- (Nb,Ti)5Si3 |
102.64 | ||||||
FeCoNiAlCrB | Ball | BCC + | 1000 | 6 | spinel + α-Al2O3 + Cr2O3 | - | air | [51] |
milling + | borides | 48 | - | |||||
FeCoNiAlCrBY0.1 | SPS | 6 | - | |||||
48 | - | |||||||
Al23Cr20Nb15Ti32Zr10 | Arc | B2 + | 800 | 100 | Al2O3 + CrO2 + | 8 | air | [50] |
melting | C14 Laves | 900 | 100 | Ti0.4Al0.3Nb0.3O2 + TiO2 + | 22 | |||
1000 | 10 | Zr0.5Al0.5O2 | 20 | |||||
Al28Cr20Nb15Ti27Zr10 | 800 | 100 | -59 | |||||
900 | 100 | -62 | ||||||
1000 | 10 | -15 | ||||||
Al33Cr20Nb15Ti22Zr10 | 800 | 100 | -18.5 | |||||
900 | 100 | -38 | ||||||
1000 | 10 | -29 | ||||||
AlCoCrFeNi2 | Arc melting | FCC + BCC | 1050 | 55 | Al2O3 + Cr2O3 + Fe2O3· AB2O4 | -0.07 | air | [42] |
Al1.5CoCrFeNi2 | FCC + B2 | (A = Fe/Co/Ni, B = Al/Cr) | 0.36 | |||||
AlCoCr1.5FeNi2 | FCC + BCC | 0.29 | ||||||
Al1.5CoCr1.5FeNi2 | BCC/B2 | 0.56 | ||||||
CoCr2FeNb0.5Ni | Laser cladding | FCC + Laves | 800 | 320 | Cr2O3 + Cr3O | 1.55 | N2-44CO2-6H2O gas | [48] |
CoCr2FeNb0.5NiSi0.2 | 1.34 | |||||||
AlCrFeNiTi | Arc melting | BCC1 + BCC2 + Laves | 900 | 100 | TiO2 + Al2O3 + Mn2O3 + complex | 1.31 | air | [45] |
Fe-O (Fe2TiO5, Mn(FeTi)) | ||||||||
AlCrFeNiTiMn0.5 | BCC1 | 1.66 | ||||||
BCC2 + | ||||||||
Laves | ||||||||
AlCoCrFeNi2.1 | Arc melting | FCC (γ') + BCC (β) | 1000 | 500 | Al2O3 + spinel | - | air | [43] |
1100 | Al2O3 | - | ||||||
AlCoCrFeNi2.1 | Arc melting | L12 (γ') + | 1100 | 1008 | Al2O3 | - | air | [44] |
B2 (β) | 1200 | - | ||||||
NiCoCrAlYHf | 1100 | - | ||||||
1200 | - |
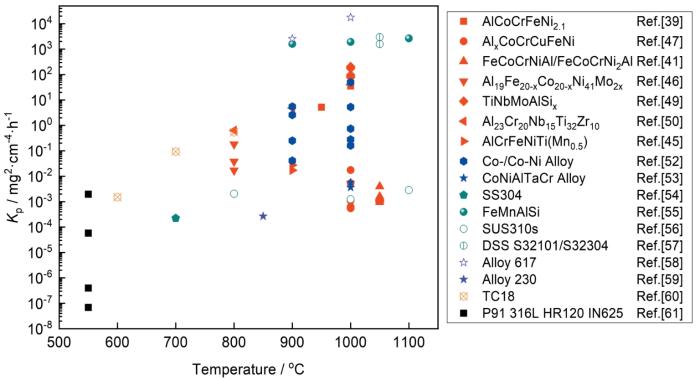
图5 多种共晶高熵合金以及Co基、Fe基、Ni基、Ti基合金在550~1100℃下静态空气中的氧化速率常数对比
Fig.5 Comparison on oxidation rate constants of some EHEAs and Co-based, Fe-based, Ni-based and Ti-based alloys in static air at 550-1100oC
4 总结和展望
4.1 总结
高熵合金的发现开启了一个巨大的多组元合金库。而这其中,共晶高熵合金因其双相复合结构,实现了强度-塑性的双重提高和优良的力学性能,在工程领域具有广阔的应用前景。本文从共晶高熵合金发展、分类、高温腐蚀基本特征、腐蚀产物、环境(化学成分、温度、时间等)影响、合金元素调控作用和高温腐蚀机理等方面,总结了共晶高熵合金高温腐蚀的研究进展。
一般而言,共晶高熵合金表现出与不锈钢/镍基合金相近甚至更为优异的抗氧化行为。这种抗腐蚀性能的主要根源还是在高熵合金所独有的4个效应,即高熵效应、迟滞扩散效应、晶格扭曲效应、鸡尾酒效应。进一步研究表明,共晶高熵合金的腐蚀行为在很大程度上受合金成分以及所形成的表面氧化膜影响。共晶高熵合金中,对抗腐蚀其主要作用的元素为Cr和Al。同时,适当添加其他合金元素(Si、Ti、Cu、Mo、稀土元素等)有助于改善组织结构、影响氧化膜成分,进而提高抗腐蚀效果。添加Mn会产生负面效果。一般认为,合金元素主要从以下几个方面起到改善腐蚀性能的作用:提高混合焓进而提高固溶相稳定性,细化合金基体晶粒进而促进氧化膜生成,促进形成更为稳定的氧化物(Cr2O3,Al2O3,尖晶石等),减少所生成的氧化膜的缺陷等等。需要注意的是,不同体系的合金成分不同,在不同环境下生成的主要氧化产物也不尽相同。因此,合金元素的加入对腐蚀的调控作用也需要具体分析。此外,共晶高熵合金的双相结构往往形成不同的氧化膜,且其生长速率随着温度升高而不再明显。与Fe基、Ni基、Co基等传统合金相比,共晶高熵合金整体上表现出较低的氧化速率,因而在高温领域具有潜在的应用价值。
4.2 未来研究方向展望
对于未来共晶高熵合金的高温腐蚀研究,本文提出如下建议:
(1) 拓宽腐蚀环境。目前大多数研究集中于共晶高熵合金在空气中的高温氧化。然而实际高温应用场景包括多种气氛以及熔盐环境。未来应围绕这些具体应用环境,开展更多研究,以探索不同气体分子(H2O, CO2, SO2, HCl等)以及熔盐(氯盐、硫酸盐、硝酸盐等)对共晶高熵合金的作用机制。
(2) 扩大合金范围。目前已开发的共晶高熵合金,只有少部分开展了高温氧化研究。未来应该扩大合金研究范围,将更多合金成分纳入,明确不同合金元素、不同物相结构对共晶高熵合金腐蚀的影响。
(3) 借助先进手段表征腐蚀产物。目前研究手段多集中于XRD物相分析,以及通过SEM/EDS分析氧化物截面。未来可在更小尺度上开展分析表征,利用FIB制备样品,并开展透射电镜,电子背散射衍射(EBSD),透射菊池衍射(TKD),三维原子探针(APT)等高分辨表征,从而获得更多腐蚀信息,明确氧化物生成过程,更好地揭示腐蚀机理。
(4) 借助理论模型进行合金开发和性能预测。高温氧化过程涉及到气体分子在合金表面的吸附、解离、反应、扩散等一系列过程,往往过于微观而无法直接观察。可以采用第一性原理、分子动力学等理论方法,对上述过程进行分析,进而促进理解关键过程、推导反应机理、并帮助开发新型抗高温腐蚀合金。
(5) 开展腐蚀-应力协同作用研究。材料在实际高温服役环境,往往同时受化学与力学作用而加速恶化。但目前共晶高熵合金的相关研究尚属空白。应力腐蚀开裂(SCC)、腐蚀疲劳(CF)、腐蚀蠕变(CP)等相关实验应积极开展,以便明确共晶高熵合金的优异力学性能是否在腐蚀-应力协同作用下继续保持。
免责声明:本网站所转载的文字、图片与视频资料版权归原创作者所有,如果涉及侵权,请第一时间联系本网删除。
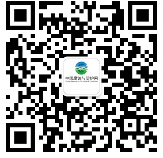
官方微信
《腐蚀与防护网电子期刊》征订启事
- 投稿联系:编辑部
- 电话:010-62316606
- 邮箱:fsfhzy666@163.com
- 腐蚀与防护网官方QQ群:140808414