
高速水流在流动过程中由于局部压强降低而出现空泡,空泡随水流移至高压区后,其周围的压强一般是不平衡的,压力高的一侧开始变形,形成微型液体射流穿透空泡,在空泡溃灭的瞬间,微射流达到极高的速度,并以极大的冲击力作用于边壁表面,多个空泡连续溃灭的冲击作用致使边壁材料产生疲劳而剥落破损,这种现象称为空蚀[1-2]。空蚀是空化的后果,几乎会发生在任何一种流体机械中,空化产生的空泡会堵塞流道、破坏流动,引起振动和噪声,空蚀过程严重危害系统的安全稳定运行[3-4]。
在航空发动机铸铝燃油泵工作时,系统中不同部位间的压强变化大,易发生空蚀损伤,影响安全稳定运行。随着对航空发动机功率及转速的要求越来越高,对铸铝燃油泵材料展开空蚀相关研究具有重要的实际意义[5-7]。ZL101铸铝合金容易熔炼和铸造,气密性好,适合铸造薄壁、大面积和形状复杂的各种零件,常用于航空发动机燃油泵壳体的制造。王维夫等[8]对航空发动机供油系统铝合金涡壳的气蚀特点和失效机制进行了分析,发现微观气蚀表面由大量尺寸在40~60 μm的气蚀凹坑相互叠加组成,单个气蚀凹坑内壁光滑,边缘呈波浪状。任奕等[9]对ZL101铸铝合金在不同介质中的空蚀行为进行了研究,探讨了用去离子水代替航空煤油快速筛选航空用耐气蚀材料的可行性,结果发现ZL101铸铝合金在航空煤油中表现出更加优异的抗空蚀性能。YANG等[10]开展了铝合金在电势作用下的空蚀试验,分析了电流密度、质量损失和表面损伤深度,结果表明铝合金在极化区(-1.0~-0.8 V)具有良好的抗空蚀性能。当压力场振荡作用于储层中液体的自由表面并且振荡幅度足够大时,液体内便会出现空化泡[11]。振幅是超声振动空蚀装置的重要参数,调整振幅可以改变试验环境的超声波强度,从而探究不同空泡产生和溃灭数目下的空蚀程度。徐仲斌[12]探究了低合金铸铁试样在不同振幅振动下的空蚀破坏程度,发现空蚀破坏程度会随着振幅的增大而加重,减小振幅是减轻空蚀破坏程度的有效措施之一。LI等[13]研究发现,在气泡与空化泡相互作用的范围内,气泡与空化泡的相对距离、大小和数量对空化泡的迁移方向、振荡时间和溃灭声压有较大影响。吴书安等[14]研究了超声振幅对材料表面粗糙度以及硬度的影响,结果发现材料表面粗糙度和硬度随着超声振幅的增大先增大后减小,在超声振幅为10.8 μm左右达到最大空蚀效果。CHENG等[15]研究发现,气泡云结构适合解释空化侵蚀,试样的侵蚀面同时受到大量气泡的破坏,气泡的最优耦合强度随气泡初始半径的减小而增大。YUSUF等[16]通过双视角高速成像和声学探测对不同尖端振动振幅下由超声喇叭产生的空化活动进行了研究,发现振幅会对输入功率和总冲击波造成影响。
由此可见,振幅作为超声振动空蚀装置的重要参数,直接影响空泡产生和溃灭的数量,会对金属的空蚀破坏程度造成重要影响。但是,目前关于空泡产生和溃灭数量对空蚀破坏程度的影响研究大多停留在数值模拟的阶段,缺少相关试验数据的支撑。开展不同振幅下的空蚀试验有助于研究空泡溃灭数量对空蚀破坏程度的影响,并促进对不同空泡溃灭数量下空蚀行为的认识。航空发动机燃油泵广泛采用的ZL101铸铝合金易受到空蚀的损伤破坏。笔者以ZL101铸铝合金作为研究对象,为快速评价抗空蚀性能,选择去离子水作为空蚀介质[9],对铸铝合金在不同振幅下的空蚀行为进行对比研究和分析;借助扫描电子显微镜(SEM)、三维光学表面轮廓仪等测试设备,研究振幅对ZL101铸铝合金空蚀行为的影响,分析其空蚀表面形貌和材料移去机理,以期为铸铝合金机械设备在空蚀条件下的安全运行提供参考。
1. 试验
1.1 试验材料
试验材料为ZL101铸铝合金,通过线切割获得尺寸为10 mm×10 mm×10 mm的试样。采用400号、800号、1 200号、1 500号、2 000号砂纸对试件进行逐级打磨,除去ZL101铸铝合金表面氧化物并保证表面光滑平整。依次采用1.5 μm和0.5 μm金刚石喷雾抛光剂将试样抛光至镜面,采用无水乙醇清洗并烘干,最后用精度为0.1 mg的分析天平进行称量并记录数据。
1.2 试验方法
1.2.1 空蚀试验
超声振动空蚀装置示意如图1所示,由超声波空蚀发生器、隔音箱、恒温装置、水槽和升降台组成,超声波空蚀发生器包括智能数控超声波发生器、换能器、变幅杆和工具头。智能数控超声波发生器与换能器相连,换能器一端连接变幅杆,变幅杆另一端连接工具头,工具头随变幅杆伸入带有空蚀介质的水槽内,工具头端面正对试样表面。智能数控超声波发生器将电信号传递给换能器,换能器受到激励后将电信号转变为超声频机械振动,机械振动经变幅杆放大传递给工具头端面,带动端面在空蚀介质中高频振动,从而完成对金属试样的空蚀试验[17-18]。振幅(A)是指连接换能器和变幅杆的工具头端面中心振动位移幅度的轴向分量,是超声振动空蚀装置的关键指标,在空蚀试验中起到很大的影响。
利用超声振动空蚀装置对制备好的ZL101铸铝合金试样进行不同振幅(60,70,80 μm)下的空蚀试验。将试样固定在工作台上,工具头下端面直径为16 mm,试样表面距离振动顶端的间距为1 mm,空蚀试验介质采用去离子水溶液,以快速评价其空蚀性能,试样表面浸入介质的深度为(12±4)mm。通过恒温水浴装置将空蚀试验环境温度控制在25 ℃,试验时间为480 min。试验后,对试样进行清洗、烘干,并用精度为0.1 mg的天平对其称量并记录数据,计算试样的质量损失量和质量损失率。
1.2.2 物相及形貌分析
利用X射线衍射仪(XRD)分析ZL101铸铝合金试样的物相组成。通过扫描电镜和三维光学表面轮廓仪观察试样的空蚀表面形貌,对试样进行切割并通过SEM观察空蚀的截面形貌。
2. 结果与讨论
2.1 物相组成
由图2可以看出,ZL101铸铝合金主要由Al相及少量的Fe、Al0.5Fe3Si0.5相组成。由于Fe、Si元素在一定程度上存在偏析现象,含有Fe、Si元素的增强相主要存在于晶界处,而Al相主要存在于晶粒内部[9]。其中Al相为较软的相,相对增强相其抗空蚀能力较差,会在空蚀过程中被更早破坏。
2.2 质量损失量和质量损失率
由图3可见:ZL101铸铝合金试样在不同振幅下的空蚀质量损失量随空蚀时间的延长不断增加,3条曲线近似呈线性增长趋势,曲线斜率随振幅的增大而增大;空蚀480 min后,在60,70,80 μm振幅下的累计质量损失量分别为51.4,65.7,81.9 mg,呈现不断增大的变化规律。由此可见,ZL101铸铝合金试样在去离子水中的空蚀破坏程度随振幅的增大而加重。超声振动空蚀装置通过固体振动,使临近的液体受到压缩和拉伸,压力发生波动从而产生空泡。振幅是衡量振动强度的主要参数之一,随着超声振幅的增大,试验环境的压力波动也越大,空泡产生和溃灭的数量增多[12],ZL101铸铝合金的空蚀破坏程度逐渐加重。
空蚀过程可分为空蚀孕育期、上升期、稳定期和衰减期四个阶段。由图4可见:不同振幅下ZL101铸铝合金试样的空蚀质量损失率曲线呈现出大致相同的变化趋势;空蚀试验初期,质量损失率快速上升,并很快达到最大值而趋于稳定,之后呈现出略微减小的趋势。ZL101铸铝合金空蚀过程不同阶段的质量损失率均随着振幅的增大而增大,说明振幅的增大增强了空蚀的破坏程度。当振幅为60 μm时,在0~120 min阶段内ZL101铸铝合金试样的质量损失率逐渐增大,是质量损失率达到最大值之前空蚀的孕育期和上升期。当振幅为70 μm和80 μm时,此阶段时间为0~60 min,更短的空蚀孕育期和上升期代表材料受到的空蚀破坏强度增大。当空蚀过程进行到300 min后,不同振幅下的空蚀质量损失率缓慢降低并逐渐稳定。
2.3 空蚀表面形貌
如图5所示,空蚀30 min后,ZL101铸铝合金试样表面已完全被破坏并深入到材料内部,导致材料表层剥落并呈现出较粗糙的表面。空蚀过程中会有相选择行为,机械作用在空蚀过程中占主要地位,硬度较小的相会在冲击作用下被优先空蚀破坏[19]。而ZL101铸铝合金中各元素的分布不均匀,含有Si、Fe、Mn元素的增强相主要存在于晶界处,硬度较低的Al相主要分布在晶粒内部[9]。因此,在液体空泡的反复冲击和溃灭作用下,ZL101铸铝合金晶粒内部较软的Al相优先被空蚀破坏,相邻晶粒内部被损伤后,晶粒边界对空蚀的抵抗能力变弱,随即晶粒边界也被破坏产生小的空蚀坑。空蚀坑的形成会诱导更多的空泡聚集,加剧空蚀坑扩大的趋势。在冲击波和微射流的共同作用下,空蚀坑尺寸不断扩大,同时相邻的空蚀坑连接到一起,进而产生更大尺寸的空蚀坑,最终显著恶化了ZL101铸铝合金的抗空蚀性能。
空蚀30 min后材料表面产生了尺寸达几十μm的空蚀坑,并且蚀坑尺寸和深度随振幅增大出现增大的趋势。原因是振幅的增大会增加空泡产生和溃灭的数量,材料表面的空泡密度增大,受到更严重的冲击波和微射流破坏,加快空蚀坑尺寸扩大和深度增大的发展过程。由图5还可见,空蚀表面出现了明显的塑性变形和脆性断裂。在微射流的作用下,空蚀表面塑性变形明显,出现了内壁光滑的空蚀凹坑,同时产生微裂纹并向铝合金内部扩展,裂纹不断发展并相互连接,使金属材料承受不住空化泡冲击的作用,造成材料的剥落。部分内壁光滑的空蚀坑呈波浪状形貌,表现出“坑涌”特征,表明受到多次空蚀冲击的作用[8]。空蚀表面在承受微射流的冲击时产生新的裂纹,从而使空蚀损伤过程连续不断进行。
由图6可见,空蚀480 min后,ZL101铸铝合金试样表面损坏程度十分严重,出现了明显的蜂窝状空蚀形貌和裂纹扩展现象,部分区域表层脱落产生了较深的蚀坑。可见,ZL101铸铝合金在去离子水中的空蚀存在明显的打孔和掏空行为,空蚀孔间有相互连通形成裂缝的趋势,这种现象对材料的破坏十分严重。
利用三维光学表面轮廓仪捕捉空蚀表面1 mm2的表面形貌。由图7可见:由于冲击波和微射流的作用,ZL101铸铝合金试样表面产生大量空蚀坑;空蚀480 min后,原始表面被完全破坏,在60,70,80 μm振幅下,表面粗糙度分别为48.2,50.0,68.4 μm,孔洞深度分别达322.7,381.9,389.0 μm,孔洞深度的增大和表面粗糙度的急剧增加反映出空蚀破坏程度加重。
2.4 空蚀截面形貌及最大声压
由图8可见,随着振幅的增大,ZL101铸铝合金试样表面空蚀坑的尺寸并无明显变化,但其深度不断增大,在60,70,80 μm振幅下深度分别达到293.8,331.3,525.0 μm。由于ZL101铸铝合金的开裂韧性较低,微裂纹扩展的阻力较小,当空蚀时间达480 min时,蚀坑内可以发现很多以一定角度向深度发展的裂纹,裂纹的发展和交叉导致材料脱落。由图8(d)可以发现,即将发生剥离的颗粒尺寸可达十几μm,颗粒脱落后在空泡溃灭产生微射流的挟带下起到加速作用,此时带有高动量的颗粒也会在一定程度上对金属表面起到冲击作用。图8(f)所示空蚀坑内壁的凸起部分会更容易受到空蚀的破坏,从而凸起顶部的材料发生脱落,形成新的蚀坑形貌。由于蚀坑内更容易产生空化泡的聚集,已经产生的空蚀坑内部会产生更大的应力集中,容易形成更多的微裂纹,并加速裂纹扩展,形成如图8(d)~(f)所示较为明显的裂纹。此过程循环反复进行,导致空蚀损伤不断向空蚀坑的内部深处发展,最终形成深度达几百μm的空蚀坑。
超声波强度直接影响空化效应,当空化阈值未达到饱和时,空化强度会随着超声波强度的增大而增大;空化阈值达到饱和后继续增大超声波强度则会产生大量无用气泡,从而增加散射衰减,阻碍空化强度的继续增大。声压是介质压强的变化量,声压越大,压力波动越大,空化程度越强。不同振幅下空蚀试验的超声波强度(I)和最大声压(F)可由式(1)和(2)计算。
|
(1) |
|
(2) |
式中:η为功效系数,一般取0.5;P为功率;S为超声探头面积;ρ为空蚀试验介质密度;c为超声波在介质中的速度。
经计算,当振幅分别为60,70,80 μm时,超声波强度分别为31.35,35.33,39.31 W·cm-2,最大声压分别为0.975,1.035,1.092 MPa,均随振幅的增大呈现增大的趋势。在25 ℃环境中,当振幅为60~80 μm时,振幅的增大导致超声波强度和最大声压增大,介质中的压力波动变大,空泡溃灭增多,ZL101铸铝合金受到的空蚀破坏加剧,空蚀质量损失量增大,蚀坑深度增大。
3. 结论
(1)在超声空蚀条件下,当振幅分别为60,70,80 μm时,ZL101铸铝合金在去离子水中的空蚀质量损失量、蚀坑深度和表面粗糙度均随着振幅的增大而增大,振幅增大导致试验环境的压力波动增大,空泡产生和溃灭的数量增多,铸铝合金的空蚀破坏程度加重。
(2)在不同振幅下,ZL101铸铝合金在液体空泡的反复冲击和溃灭作用下发生了明显的塑性变形和脆性断裂,晶粒内部较软的Al相率先被空蚀破坏,相邻晶粒内部被损伤后,晶粒边界对空蚀的抵抗能力变弱随之被破坏,铸铝合金在去离子水中的空蚀破坏具有明显的打孔和掏空行为。
(3)蚀坑内更容易产生空化气泡的聚集,受到更大的应力集中,产生微裂纹并加速裂纹扩展,使空蚀损伤不断向空蚀坑的内部深处发展。振幅的增大导致超声波强度和最大声压增大,加剧了空蚀破坏,材料脱落更迅速。
免责声明:本网站所转载的文字、图片与视频资料版权归原创作者所有,如果涉及侵权,请第一时间联系本网删除。
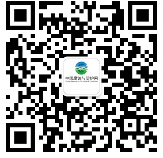
官方微信
《腐蚀与防护网电子期刊》征订启事
- 投稿联系:编辑部
- 电话:010-62316606
- 邮箱:fsfhzy666@163.com
- 腐蚀与防护网官方QQ群:140808414