元素 | 质量分数/% | |||||||||
---|---|---|---|---|---|---|---|---|---|---|
Al | Mo | Zr | Si | Fe | C | N | H | O | Ti | |
TC11钛合金 | 6.31 | 3.34 | 1.59 | 0.27 | 0.071 | 0.027 | 0.002 1 | 0.001 7 | 0.15 | 余量 |
标准值 | 5.8~7.0 | 2.8~3.8 | 0.8~2.0 | 0.2~0.35 | ≤0.25 | ≤0.10 | ≤0.05 | ≤0.012 | ≤0.15 | 余量 |
钛合金具有密度小,质量轻,比强度和比刚度高,耐蚀性好,韧塑性和加工性能良好等优点,在海洋油气开发中具有广阔的应用前景。但钛合金存在摩擦因数大,硬度低,耐磨性能差,高温条件下氧化严重等缺点,这又限制了钛合金在摩擦磨损场合的应用[1-7]。海洋油气开发中,由钛合金、铍青铜制造的随钻仪器零件,服役时在挤压、剪切以及交变接触应力的作用下易发生磨粒磨损、黏着磨损、接触疲劳等机械损伤[8];而在钻井液中腐蚀介质的作用下,随钻仪器零件还会发生化学损伤。实施表面改性是提升钛合金、铍青铜等随钻仪器零件耐磨性的有效途径之一,常用的表面改性技术包括化学热处理、离子注入、超声速火焰喷涂(HVOF)、激光熔覆等。其中,HVOF具有加工效率高、热影响区小、涂层与基材为机械结合、涂层厚度可控等优点,通过调控喷涂工艺参数以及涂层材料体系设计,可在钛合金等金属表面制备出耐磨性优异的涂层。
王成[9]采用HVOF在TC18钛合金试片上制备WC-12Co和WC-10Co4Cr涂层。结果表明,两种涂层无明显缺陷,孔隙率低,涂层与基体结合良好,以机械结合为主;摩擦磨损测试表明,两种涂层均显著改善了基体的耐磨性,其中WC-10Co4Cr涂层相对更优。张业勤等[10]采用两种不同粉末在TC27钛合金试片上喷涂耐磨涂层,对比分析了不同粉末对耐磨涂层的显微组织、孔隙率、显微硬度、结合强度及弯曲性能的影响。DU等[11]研究了喷丸、喷砂和HVOF制备的WC-17Co涂层的表面完整性对TC18钛合金疲劳性能的影响。关于HVOF金属陶瓷涂层的研究论文很多,研究方向多集中在涂层显微组织,涂层与基体的结合性,以及涂层的耐摩擦磨损性能和耐蚀性方面[12-17]。但是,在钛合金基材上采用HVOF制备陶瓷涂层,研究表面改性对基材组织和性能的影响较为少见。另外,发生过一起经激光熔覆处理的铍青铜随钻仪器零件早期疲劳断裂事件,而疲劳失效又与基体组织和性能受到激光熔覆的热输入影响密切相关。基于这两方面原因,有必要系统研究表面改性对钛合金基材组织和性能影响。
笔者采用HVOF在TC11钛合金试样和随钻仪器零件上制备WC-10Co4Cr金属陶瓷涂层,通过显微组织和显微硬度、冲击韧性和断口分析、湿砂胶轮磨粒磨损试验和电化学测试,系统研究了涂层的性能,以及HVOF工艺对基材组织和性能可能造成的影响,为后续随钻仪器零件表面强化的规模应用提供技术支持。
1. 试验
1.1 试样和涂层制备
委托试制工厂按照设计要求,完成钛合金试样和涂层制备。将ϕ50 mm的TC11棒材加工成尺寸为75 mm×25 mm×10 mm的TC11钛合金试样,共加工6件,其中3件采用HVOF工艺制备涂层。棒材为退火态,热处理制度是950 ℃×2 h,空冷+530 ℃×6 h,空冷,TC11钛合金成分见表1。
试样经过清洗和烘干、表面喷砂粗化和预热200 ℃,再进行HVOF。HVOF以航空煤油作为燃料,氧气作为助燃气,氮气作为载气,工艺参数为:煤油流量22 L/h,氧气流量52 m3/h,送粉量60 g/min,喷涂距离360 mm,最终涂层厚度200~250 μm。金属陶瓷粉末化学成分见表2。
粉末名称 | 质量分数/% | |||
---|---|---|---|---|
C | Co | Cr | W | |
WC-10Co4Cr | 3.5~4.5 | 9~11 | 3.5~4.5 | 余量 |
1.2 测试分析
有无涂层的钛合金试样(以下简称带涂层试样和无涂层试样)各取1件进行切割,制成尺寸为20 mm×25 mm×10 mm的试样,用于金相检验和硬度测试;试样经打磨和抛光后用HF+HNO3浸蚀剂显示组织,使用光学显微镜(OM)和扫描电镜(SEM)观察涂层和基体的显微组织,采用图像分析软件测量涂层的孔隙率。
利用能谱仪(EDS)和X射线衍射仪(XRD)分别测定涂层的化学成分和相组成,X射线源为Cu钯Kα射线,管压40 kV,管流40 mA,连续扫描,衍射角范围为20°~90°。
按照ASTM E384-2017《材料显微压痕硬度的标准试验方法》标准,使用维氏硬度计在2.94 N载荷下测定涂层和基体的显微硬度,结果取5个点的平均值,基体硬度测量始于涂层界面,近界面处每间距100 μm进行测量,之后间距1 mm测量;无涂层钛合金试样的硬度从近表面往芯部测量,间距1 mm。
将有无涂层试样各加工3件带“V”型缺口的标准冲击试样,尺寸为10 mm×10 mm×55 mm,使用摆锤冲击试验机进行冲击韧性试验,用SEM观察断口形貌。
使用湿砂胶轮磨粒磨损试验机测涂层的耐磨性,测试设备及测试参数见表3。参照ASTM G105-2020《进行湿砂/橡胶轮磨损试验的标准试验方法》,用称量法测定试样喷涂前后的磨损量,用SEM观察试样的磨损形貌。
设备 | 胶轮-湿砂磨粒磨损试验机 |
---|---|
胶轮 | 硬度60 HD,直径177.4 mm,宽度13 mm |
试样尺寸/mm | 75.6×25.4×10.4 |
砂 | 50~70目(212~270 μm)石英砂,平均粒径260 μm |
砂浆 | 1 500 g石英砂+940 g纯净水 |
胶轮轮速/(r·min-1) | 240 |
载荷/N | 240 |
磨程/m | 3 355 |
1.3 电化学测试
采用电化学工作站测试试样的耐蚀性,试样尺寸为10 mm×10 mm,采用标准三电极体系,用环氧树脂封装后的试样作为工作电极,铂片作为辅助电极,饱和甘汞电极(SCE)作为参比电极,在25 ℃的3.5%(质量分数)NaCl溶液中进行动电位极化曲线测试。动电位扫描范围为-700~100 mV,扫描速率为2 mV/s,自腐蚀电位的测试时间为3 600 s。无特殊说明,本文中的电位均相对于SCE。
2. 结果与讨论
2.1 显微组织
由图1可见:涂层平均厚度为230 μm,涂层截面呈较致密的层状结构,有零星分布的孔隙,孔隙率为2.55%,属于较低水平,涂层与基体为机械结合;涂层内部有断续分布的微裂纹,这在一定程度上降低了涂层与基体的结合力;界面处的TC11钛合金基体组织为暗黑色β相基体+白色等轴α相再结晶晶粒的双相组织,在涂层界面处有少量的白色细针状α相,β相内的α相呈片层结构;与未经喷涂的钛合金组织相比,涂层界面处的α+β双相组织形貌和比例没有明显差别。
与等离子喷涂、电弧喷涂、火焰喷涂等其他改性技术相比较,HVOF技术具有低热源温度和极高喷射速度,能够防止碳化物过分氧化和蒸发分解。工件预热温度不超过200 ℃,HVOF时基材的表面温度测量值不超过150 ℃,远低于TC11钛合金的退火温度530 ℃及β/(α+β)转变温度(约1 000 ℃)。因此,HVOF的热输入不会导致钛合金基体发生组织转变,影响材料性能。但需控制涂层内部裂纹的产生,裂纹容易造成涂层在使用过程中剥落,从而影响零件使用寿命。
2.2 涂层元素及相组成
由图2可见,涂层中各元素含量与WC+10Co4Cr基本一致。由图3可见,涂层含大量WC增强相及少量W2C和Co25Cr25W8C2相。涂层的性能在一定程度上取决于热喷涂过程中发生的物理化学过程。C在金属黏结相中的溶解将导致C含量的降低,WC相部分分解为W2C相,C进入黏结相形成含碳的金属固溶体基体,基体硬度升高;黏结相进入碳化物相,形成Mx Wy C型复合碳化物相(η相)。两者都将提高WC-金属陶瓷的脆性[18-19]。所以理想的WC-金属陶瓷涂层相结构应以WC相为主,并含有一定量的W2C相、CoCr黏结相和少量的η相,这样结构的涂层更致密、耐磨,同时具有较高的韧性。
2.3 显微硬度
测得WC-10Co4Cr涂层的显微硬度均值为1 391 H V,涂层表现出极高硬度。无涂层试样的硬度见图4,为343~363 HV,带涂层试样的钛合金基体硬度为336~360 H V,可见采用HVOF工艺没有使近界面的基体硬度发生显著改变,这一测试结果与显微组织的观察结果相一致。
2.4 冲击韧性与断口形貌
由表4可见,无涂层试样的冲击功为20.0 J,带涂层试样的冲击功为24.5 J,即经过HVOF制备涂层后的钛合金的冲击功略高于未经处理的钛合金。由图5可见:喷涂涂层前后试样的冲击断口形貌无差别,均为塑性断口,呈剪切韧窝的形貌特征;带涂层试样的冲击断口在涂层界面两侧呈现完全不同的断裂形貌,涂层断口表现为脆性断口,有许多的二次裂纹,解理小平面和层状结构,钛合金断口表现为塑性断口,呈剪切韧窝特征。
试样 | 冲击功/J | 冲击功平均值/J |
---|---|---|
无涂层试样 | 18.7 18.0 23.3 | 20.0 |
带涂层试样 | 21.0 20.2 32.2 | 24.5 |
2.5 湿摩擦磨损试验结果
带砂粒的湿摩擦磨损试验更加贴近随钻仪器零件在井下的工作状况,携带岩屑的钻井液连续冲刷仪器零件表面的耐磨涂层,使涂层发生冲刷磨损。当岩屑进入到随钻仪器零件之间的间隙,还可以引发磨粒磨损。经过湿砂胶轮磨粒磨损试验,无涂层试样被磨出深沟,而带涂层试样只有轻微的磨损痕迹,涂层表面的磨痕宽度和磨痕深度均远低于无涂层试样,见图6(a)。用卡尺测量无涂层试样表面最深的磨痕深度为1.34 mm,通过电子天平计算磨损量V,无涂层试样的磨损量为0.866 6 g,带涂层试样的磨损量为0.013 5 g。而材料耐磨性ε被定义为磨损量V的倒数,即ε=1/V,涂层显著改善了钛合金基体的耐磨性。
由图6可见,在摩擦试验部位,无涂层试样有大量的划痕和犁沟,呈现出磨粒磨损的典型特征,磨损表面还伴随材料的转移、黏着、塑性变形及流动,这是黏着磨损的典型特征。由此可见,钛合金的磨损机制包含磨粒磨损及黏着磨损两种形式。而带涂层试样则表现出优良的耐磨性,摩擦表面形貌比较平滑,只有细微的犁沟,未见到材料转移、黏着及塑性变形等黏着磨损特征。这是因为高硬度的WC颗粒均匀分布在柔韧的CrCo合金基体上,这样的涂层结构具有良好的耐磨性[20-21]。较硬的石英砂粒遇到更硬的WC颗粒会产生阻力,只会在涂层表面留下轻微的划痕犁沟及少许的磨屑而发生磨粒磨损。带涂层试样的磨损机制是磨粒磨损。
材料的磨粒磨损与磨粒的特征(硬度、粒度和尖角程度等),磨损工况条件(载荷、速度、温湿度等环境因素)和材料成分及组织性能有关。大量的现场观察分析和实验室试验发现,材料的磨粒磨损在很大程度上取决于磨粒的硬度Ha和金属材料的硬度Hm之比。石英的硬度为1 000~1 300 HV,WC涂层的硬度约1 400 HV,钛合金基体硬度为343~363 HV。根据硬度比值,钛合金的磨粒磨损处在高磨损区,即Hm<0.8Ha,磨粒的显微切削是材料磨损的主要机制;而涂层的磨粒磨损处在过渡磨损区,即Hm≈Ha。由于涂层中含有大量的高硬度碳化物,能够有效阻止磨料的显微切削和塑性变形犁铧作用,使涂层材料具有较高的耐磨性。
2.6 电化学性能
由图7可见:带涂层试样和无涂层试样的自腐蚀电位(Ecorr)分别为-432 mV和-548 mV,与无涂层试样相比,带涂层试样在阳极极化区和阴极极化区腐蚀速率均较小,带涂层试样和无涂层试样的自腐蚀电流密度分别为2.2 μA/cm2和12.2 μA/cm2。极化曲线测试结果说明,带涂层试样的耐腐蚀性能优于无涂层试样。
邓春明等[22]研究了Cr元素对WC涂层耐腐蚀性能的影响。结果表明:Cr元素在腐蚀性介质中浸泡后形成耐蚀性很好的Cr2O3钝化膜,可以有效提高涂层的耐腐蚀性能;同时,涂层致密的结构对腐蚀介质的扩散起到一定的阻碍作用。
3. 结论
(1)HVOF工艺对TC11钛合金的组织和性能影响较小,相较于无涂层试样,带涂层试样界面处基体的显微组织和显微硬度没有明显变化,冲击韧性稍有提高。
(2)HVOF工艺稳定可靠,涂层呈片层结构,致密度高,涂层的孔隙率为2.55%,硬度达到1 400 HV,涂层主要由WC和W2C相组成,其与基体结合良好,为机械结合。
(3)金属陶瓷涂层能够显著改善钛合金的耐磨性和耐蚀性,带涂层试样的磨损量只有无涂层试样的1.56%,带涂层试样的磨损机制是磨粒磨损,无涂层试样的磨损机制是磨粒磨损+黏着磨损。
免责声明:本网站所转载的文字、图片与视频资料版权归原创作者所有,如果涉及侵权,请第一时间联系本网删除。
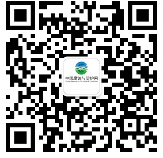
官方微信
《腐蚀与防护网电子期刊》征订启事
- 投稿联系:编辑部
- 电话:010-62316606
- 邮箱:fsfhzy666@163.com
- 腐蚀与防护网官方QQ群:140808414