
SiC/SiCf复合材料作为核反应堆燃料包壳候选材料,具有高温强度优良、高温化学性能稳定、熔点高、辐照稳定性好、高温蒸汽腐蚀动力低和抗高温蠕变能力强等优点[1-2]。SiC的中子经济性比锆合金高25%[3],也不存在锆合金的氢致破坏问题。SiC/SiCf复合材料能够在一定程度上弥补单相SiC的脆性问题,提高其断裂强度。
根据热力学理论,在轻水反应堆正常运行条件下,SiC会与高温水反应生成SiO2。由于SiO2不能形成有效的保护层,而是进一步溶解于水中生成硅酸和Si(OH)4,因此SiC质量减少。制备工艺是影响SiC腐蚀速率的主要因素,通过优化制备工艺来提高SiC/SiCf复合材料的致密化、晶粒度和纯度,有助于提高SiC/SiCf复合材料在核反应堆环境中的抗水氧腐蚀能力[4-9]。
在压水堆服役工况条件下,SiC/SiCf复合材料包壳管受到应力作用,应力主要来源于包壳管内外压力差、流体冲刷、流致振动和复合材料加工残余应力等[10]。高温高压水腐蚀环境与应力的共同作用可能导致材料失效以及运行安全风险。目前,国内外鲜见关于SiC/SiCf复合材料包壳管在高温高压水中的应力腐蚀开裂(SCC)试验研究。笔者针对SiC/SiCf复合材料包壳管,采用三点弯加载方法,在模拟压水堆一回路水化学工况下开展了SCC试验,并分析了该材料的应力腐蚀裂纹及微观组织,以期对SiC/SiCf复合材料包壳管在模拟压水堆水环境中的服役性能评价提供试验数据。
1. 试验
试验采用循环高温高压水腐蚀系统,系统中的电导率、pH、溶氧量可控。在水箱中通入高纯氮气(纯度99.99%),并通过减压阀、质量流量计调节氮气流量,实现溶解氧的控制。溶解氧含量通过高精度溶氧仪测定,并进行定期标定,以保证读数的可靠性,溶解氧显示值是高压釜给水中的溶解氧含量。循环水流速为10 L/h,系统运行性能稳定,可以较好地模拟核电厂一回路水化学工况。
采用三点弯加载方法开展SiC/SiCf复合材料包壳管试样(以下简称SiC/SiCf包壳管试样)在高温高压水中的SCC试验,试样尺寸为外径10 mm、内径8 mm、长度60 mm。SiC/SiCf复合材料包壳管整体为三层结构,内层为SiC涂层,中间层为SiC纤维,外层为SiC涂层。其中,SiC纤维中间层的制备方法为化学气相渗透法(CVI),内外SiC涂层采用化学气相沉积法(CVD)在纤维复合材料表面进行沉积,以填补SiC/SiCf复合材料间的空隙并形成一定厚度的涂层。将所有制备好的试样进行打磨和抛光后,用酒精超声清洗并用去离子水冲洗,干燥后备用。
采用625合金作为三点弯加载夹具的主体材料,耐蚀ZrO2陶瓷作为试样绝缘垫片,可夹持直径6~12 mm、长60 mm的管状试样。夹具设计及试样加载如图1所示。
试验过程中采用的水化学介质为用高纯去离子水配制的含1 200 mg/L H3BO3和2 mg/L LiOH的水溶液,水中溶解氧质量浓度为5 μg/L,水环境温度为(360±1)℃,水环境压力为(20±0.5)MPa,试验时间为6 440 h。
试验后采用扫描电子显微镜(SEM)、能量色散谱仪(EDS)对试样的应力腐蚀裂纹以及周围的微观组织进行观察和分析。
2. 结果与讨论
2.1 应力腐蚀形貌及成分
由图2可见:腐蚀前,SiC/SiCf包壳管试样表面涂层组织主要由多层胞状(或菜花状)晶组成,胞状晶分布较为均匀;原始试样表面还可以观察到一些尺寸较大的空隙,这些空隙可能产生应力集中而成为应力腐蚀裂纹萌生位置。
由图3可见:腐蚀后,SiC/SiCf包壳管试样的SiC涂层表面产生了较多的长裂纹,且涂层已发生表面层脱落现象;包壳管试样的SiC涂层表面存在大量丝状物和白色颗粒,且丝状物层发生了开裂,涂层表面形成了氧化物层,氧化物层在应力作用下形成裂纹并脱落。
由图4可见:腐蚀后,在SiC/SiCf包壳管试样表面SiC涂层中出现了单一的应力腐蚀裂纹,裂纹沿轴向扩展;在SiC涂层表面局部位置可观测到交叉裂纹,交叉裂纹的产生使表面层发生逐层脱落,已可见内部的纤维中间层;在应力和腐蚀的共同作用下,纤维已发生一定程度的腐蚀溶解和破裂。SiC/SiCf包壳管试样的外涂层在应力作用下发生了沿轴向的裂纹扩展现象,应力腐蚀裂纹的产生导致涂层内部基体和纤维层暴露于高温高压水中,促进了腐蚀溶解。
由图5可见:在靠近SiC/SiCf包壳管试样两端加载点的区域,可观察到氧化物层存在约300 μm长的微裂纹,该区域裂纹数量较少,裂纹长度较短,且SiC外涂层发生较严重的腐蚀溶解现象,表面层开始发生少量剥落,剥落处可见内层SiC纤维;在试样中部加载区域可以观察到SiC外涂层产生了长裂纹,裂纹在试样表面涂层不均匀位置或孔隙缺陷等应力集中处萌生,并沿轴向进行扩展。该区域裂纹长度可达到mm级;相比于靠近两端加载点的区域,试样中部加载区域的裂纹数量更多,长度更长。在外加张应力作用下,SiC外涂层局部区域出现较多的交叉裂纹,在高温高压水环境中,这些交叉裂纹的出现加速了外涂层的腐蚀溶解并发生明显的脱落现象,部分区域发生失效。
对图5(a)区域中SiC涂层表面(位置1)和裸露的纤维层(位置2)进行了EDS分析,结果如表1所示。可见,SiC涂层及裸露的纤维层表面主要元素为Si、C和O,不同位置均含有一定量的O元素,随着腐蚀的进行,SiC涂层及裸露的纤维层表面均会产生氧化物。相比于内部的纤维层,SiC涂层表面O含量更高,表明该涂层表面的剥落层应为氧化物层,氧化物层在应力作用下容易产生交叉裂纹从而引起脱落。
表面层 | 质量分数/% | ||
---|---|---|---|
Si | C | O | |
涂层 | 89.50 | 8.07 | 2.42 |
纤维层 | 78.95 | 20.51 | 0.54 |
由图6可见:由于SiC外涂层的剥落,SiC纤维暴露在高温高压水环境中;在应力和高温高压水腐蚀的共同作用下,SiC纤维层发生了严重的腐蚀溶解和裂纹萌生扩展现象。SiC纤维层的整体结构已经被破坏,其表面的交叉裂纹导致纤维层表面的氧化层发生剥落,随着裂纹不断扩展,纤维层破碎。这说明SiC纤维层的整体韧性较差,在应力作用下很容易发生开裂,从而加速材料失效。
由图7可见:SiC纤维层表面的裂纹扩展方向垂直于纤维层的轴向,从而导致纤维层的断裂;SiC纤维层表面还可观察到蜂窝状的腐蚀孔洞,说明SiC纤维在高温高压水中的应力腐蚀敏感性较高,极易发生腐蚀溶解;SiC纤维层表面的裂纹扩展方向平行于纤维层的轴向,导致纤维层表面的脱落;SiC纤维层表面的裂纹扩展没有明显的取向性。
SiC外涂层与水溶液反应会生成SiO2和Si(OH)4,具体反应见式(1)~(5)[11]。
|
(1) |
|
(2) |
|
(3) |
|
(4) |
|
(5) |
2.2 讨论
结合SEM形貌和EDS分析结果可知,SiC外涂层发生了明显的腐蚀溶解并生成氧化物,涂层表面出现了较多的微裂纹和长裂纹,这些裂纹在试样表面涂层不均匀位置或孔隙缺陷等应力集中处萌生和扩展。三点弯加载的最大应力均出现在试样凸形表面的中部,并线性下降至外支点处为零,相比于外支点区域,试样中部加载区域可观察到更多的裂纹,且裂纹长度更长。同时,涂层表面产生的交叉裂纹使表面氧化层发生脱落,说明SiC外涂层在高温高压水的腐蚀作用下易产生韧性较低的氧化层,氧化层在外加张应力作用下表现为明显的脆断现象。因此,在应力和水化学环境的耦合作用下,SiC外涂层部分区域发生了腐蚀脱落和完全失效,失去了保护SiC/SiCf复合材料内层结构的能力。
SiC外涂层部分区域脱落后,中间层SiC纤维暴露于高温高压水环境中,而SiC纤维具有较低的耐蚀性,在高温高压水中很容易发生腐蚀溶解。同时,在外加张应力的作用下,SiC纤维层表面出现了裂纹萌生和扩展现象,交叉裂纹的产生导致纤维层破裂。SiC纤维层表面的裂纹扩展没有明显的取向性,裂纹既沿垂直于纤维层轴向方向扩展,又沿平行于纤维层的轴向方向扩展,开裂的SiC纤维层进一步加剧了其在高温高压水中的应力腐蚀敏感性,从而导致纤维层表面腐蚀程度加重。
综上可见,SiC/SiCf包壳管试样受到弯曲应力,导致SiC外涂层在外加张应力和高温高压水环境耦合作用下发生腐蚀溶解,涂层局部出现交叉裂纹,交叉裂纹的产生使部分区域出现脆断和剥落现象,而涂层剥落又进一步加剧了外涂层的腐蚀溶解,导致外涂层过早失效和SiC纤维层暴露。在应力和高温高压水环境的耦合作用下,SiC纤维层出现严重的腐蚀溶解和裂纹扩展现象,SiC纤维层表面的裂纹扩展没有明显的取向性,交叉裂纹的不断产生,最终导致纤维层的断裂和整体失效。
总的来说,涂层表面的孔隙缺陷处易产生应力集中而成为裂纹萌生位置,可通过改进表面涂层的制备工艺,减少孔隙缺陷,抑制腐蚀溶解速率,从而提高涂层的抗SCC能力。
3. 结论
(1)在三点弯外加张应力加载和高温高压水环境作用下,SiC/SiCf包壳管试样外层涂层发生氧化及腐蚀溶解,部分区域出现裂纹扩展和剥落现象。
(2)SiC纤维中间层表面的裂纹扩展没有明显的取向性,交叉裂纹的不断产生最终导致纤维层的断裂和整体失效。
(3)在SiC/SiCf包壳管试样涂层表面的孔隙缺陷处易产生应力集中,进而成为裂纹萌生位置。
(4)涂层在高温高压水腐蚀作用下易生成易脆断的氧化层,为提升SiC/SiCf包壳管的抗SCC能力,需优化涂层制备工艺。
免责声明:本网站所转载的文字、图片与视频资料版权归原创作者所有,如果涉及侵权,请第一时间联系本网删除。
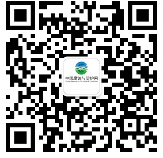
官方微信
《腐蚀与防护网电子期刊》征订启事
- 投稿联系:编辑部
- 电话:010-62316606
- 邮箱:fsfhzy666@163.com
- 腐蚀与防护网官方QQ群:140808414