
在福岛核电站事故中,锆合金包壳材料与高温蒸汽发生化学反应,释放出大量氢气,最终引起氢气爆炸,暴露出普通锆合金包壳材料在该事故工况下的缺点。之后,事故容错燃料(ATF)成为国内外研发热点。相较于传统锆合金包壳材料,ATF包壳材料在正常运行工况下可以维持或提高燃料性能,并以其良好的耐蚀性、优越的高温力学性能在事故发生后相当长的一段时间内维持堆芯的完整性,从而提供足够的时间裕量来采取事故应对措施[1]。
近年来,国内外学者针对ATF包壳候选材料开展了一系列的腐蚀试验研究,对该材料的腐蚀特性和机理有了一定的了解。RAIMAN等[2]选取FeCrAl合金作为包壳材料,在模拟沸水堆水化学条件下完成了9个月的试验研究,得到了FeCrAl合金的腐蚀特性,并认为该材料适用于沸水堆条件。JIANG等[3]研究了FeCrAl合金的氧化动力学特性、腐蚀过程及其影响因素,并与Zr合金进行了比较。BRACHET等[4]使用高压釜对涂覆金属涂层的Zr合金及涂覆陶瓷涂层的Zr合金开展了近60 d的腐蚀试验,得到了涂覆各类涂层的Zr合金的腐蚀特性。雷一明[5]探索了涂覆涂层的Zr合金的制备方法及其在高温高压水环境中的氧化腐蚀机理。崔越等[6]将涂覆Ti3SiC2涂层的管材放入静态高压釜中,分别开展了不同工况、不同水化学环境的腐蚀研究,并与Zr合金进行了比较,认为Ti3SiC2不适宜作为ATF包壳材料。周邦新[7]讨论了LiOH浓度对Zr合金腐蚀速率的影响,并对LiOH加速Zr合金腐蚀的机理进行了探索性分析。以上研究均使用高压釜容器进行静态腐蚀试验,较好地模拟了反应堆一回路的温度、压力和水化学环境,但是未考虑流体流速对材料表面腐蚀的影响以及包壳管内发热的条件,并且介质流动还会加速包壳壁面保护性氧化膜的分解和破坏。因此,在内置电加热棒(模拟芯块发热)的动水环境中对ATF包壳候选材料开展腐蚀试验会更加贴近实际工况。
笔者串联4个试验本体构成试验段,每个试验本体有21个腐蚀试样通道,对多根Zr合金、涂层Zr合金以及FeCrAl合金包壳管试样分别在空管条件和内置电加热棒条件下同时开展动水腐蚀试验,并对试样的腐蚀结果进行对比分析,以期为ATF包壳材料的选择及应用提供参考。
1. 试验
1.1 试验装置
试验装置由回路系统、测控系统、电气系统、仪表系统和加药系统等组成,如图1所示,主要设备有柱塞泵、主回热器、预热器、冷却换热器、多级降压单元和阀门等。试验介质从柱塞泵出来,依次经过主回热器(H-1)管程、预热器、喷射泵、试验段、主回热器(H-1)壳程和冷却换热器(H-2)。其中,高压流体由喷射泵喷射进入试验段,试验完成后大部分流体被引回喷射泵吸入端,构成循环回路,而小部分流体则通过主回热器(H-1)和冷却换热器(H-2)排出。
动水腐蚀试验参数:温度320 ℃,压力15.5 MPa,包壳外工作介质流速5.0 m/s。试验介质为含硼酸和氢氧化锂的水,水化学参数:B质量浓度1 000 mg/L, Li质量浓度3.5 mg/L,溶解氧质量浓度低于0.5 mg/L。
1.2 试样
试样为端部封闭的圆形包壳管,包括普通Zr合金、涂覆金属涂层(纯Cr,纯度99.9%以上,厚度为15μm)的Zr合金和FeCrAl合金,以下分别简称Zr合金,涂层Zr合金和FeCrAl合金。分别设置两种试样,即在试样内部分别放置一根电加热棒(内置加热棒)和一根不锈钢棒(空管),内置电加热棒用于模拟芯块发热的情况,电加热棒的发热功率约为3 kW;内置不锈钢棒用于模拟无芯块发热情况,不锈钢棒可支撑管件。试样长度为170 mm,外径约为9.5 mm,壁厚约为0.6 mm。
1.3 试验方法
采用柱塞泵与阀门配合的方式调节主流体流量和系统压力,通过调节预热器和电加热元件的电加热功率,以及冷却换热器的二次侧冷却水流量,控制流体温度。流体沿试验本体轴向进入试样的流通通道内,用动水持续冲刷试样,当装置内各项参数达到试验工况,且装置保持稳定运行时,开展长周期试验,腐蚀时间为28 d。
试验后,取出试样,采用ZEISS Gemini 500型扫描电子显微镜(SEM)表征试样微观形貌,用INCA型能谱仪(EDS)和Empyrean型X射线衍射仪(XRD)分析氧化产物的化学成分和物相。
2. 结果与讨论
2.1 腐蚀产物物相
由图2可见:在水化学环境中经动水腐蚀后,Zr合金包壳管外表面粗糙度较大,与腐蚀前试样表面形貌相似。
由图3可见:在水化学环境中,涂层Zr合金包壳管腐蚀前的表面质量较好,均匀致密,且表面粗糙度相对Zr锆合金较小;腐蚀后,包壳管外表面不平整,且表面弥散分布白色氧化物颗粒。
由图4可见:在水化学环境中,FeCrAl合金包壳管腐蚀前的表面组织呈纤维状,沿某一方向分布,表面相对较粗糙;腐蚀后,表面组织结构主要分为两层,上层为细小颗粒氧化物,下层为连续分布的氧化膜。
由图5可见:Zr合金包壳管(内含加热棒)在水化学环境中经动水腐蚀28 d后,外表面保持粗糙纤维状,与腐蚀前试样表面形貌相似;在相同环境中腐蚀后,涂层Zr合金包壳管(内含加热棒)外表面不平整,表面有白色氧化物颗粒。
2.2 腐蚀产物成分
由图6可见:腐蚀前Zr合金包壳管的物相主要为Zr,腐蚀后,XRD谱中只有Zr峰,并未发现氧化物的峰,原因可能是Zr合金包壳管表面氧化层很薄,氧化不明显;涂层Zr合金包壳管在腐蚀前后表面物相均为Cr;腐蚀前FeCrAl合金包壳管基体物相主要为α-Fe,腐蚀后,基体峰仍较强,并未发现氧化物的峰,原因可能是其表面氧化层很薄,氧化不明显。
由表1可见:腐蚀后Zr合金包壳管表面元素主要为Zr和O,并含有微量的Fe和Nb,说明腐蚀产物主要为ZrO2;腐蚀后涂层Zr合金包壳管表面白色颗粒应为包壳管的腐蚀产物,主要组成元素为Zr和O,大部分区域(如位置2和3)的组成元素主要为Cr和O,且O元素含量较低,说明涂层耐蚀性较强;腐蚀后FeCrAl合金包壳管表面含有大量的O和Fe,说明其表面生成了Fe氧化物,且下层连续分布的氧化膜中O元素含量略高于颗粒状腐蚀产物。
材料 | 位置 | 原子分数/% | |||||||
---|---|---|---|---|---|---|---|---|---|
Cr | Zr | O | Fe | Nb | Ni | Al | Ti | ||
Zr合金 | 1 | — | 37.26 | 61.58 | — | 1.16 | — | — | — |
2 | — | 35.59 | 63.45 | 0.96 | — | — | — | — | |
3 | — | 37.82 | 60.89 | 0.23 | 1.05 | — | — | — | |
涂层Zr合金 | 1 | 5.80 | 49.21 | 33.13 | 10.72 | 1.15 | — | — | — |
2 | 84.04 | — | 12.99 | 2.37 | — | 0.59 | — | — | |
3 | 83.06 | — | 13.57 | 2.77 | — | 0.60 | — | — | |
FeCrAl合金 | 1 | 12.23 | — | 18.93 | 59.27 | — | — | 8.33 | 0.37 |
2 | 13.12 | — | 25.75 | 55.05 | — | — | 5.03 | 0.33 | |
3 | 13.44 | — | 30.34 | 51.41 | — | — | 4.15 | 0.29 |
由图7可见:Zr合金包壳管(内含加热棒)腐蚀后的XRD谱仍以初始Zr峰为主,氧化不明显,但出现了一些其他的峰;涂层Zr合金包壳管(内含加热棒)腐蚀后,XRD谱中只有Cr峰,且强度很高,并未发现氧化物的峰,表明氧化层很薄,氧化不明显。
由表2可见:腐蚀后,Zr合金包壳管(内含加热棒)表面元素主要为Zr和O,并含有微量的Fe和Nb;腐蚀后,涂层Zr合金包壳管(内含加热棒)表面白色颗粒主要组成元素为Cr、Zr和O,应该为Cr涂层与Zr包壳腐蚀产物的复合,相对平坦的区域组成元素主要为Cr和O,且O元素含量极低,说明涂层耐蚀性较强。
材料 | 位置 | 原子分数/% | ||||||
---|---|---|---|---|---|---|---|---|
Zr | O | Fe | Nb | C | B | Cr | ||
Zr合金 | 1 | 87.80 | 9.64 | 0.24 | 2.32 | — | — | — |
2 | 82.80 | 12.91 | 2.31 | 1.99 | — | — | — | |
3 | 63.41 | 33.13 | 2.04 | 1.42 | — | — | — | |
4 | 74.22 | 23.30 | 0.07 | 2.41 | — | — | — | |
涂层Zr合金 | 1 | — | 3.06 | — | — | 5.25 | — | 91.69 |
2 | — | 4.09 | 0.52 | — | 7.25 | — | 88.14 | |
3 | 23.26 | 7.05 | 0.54 | — | 15.10 | 8.53 | 45.52 |
3. 结论
(1)Zr合金、涂层Zr合金和FeCrAl合金三种包壳管候选材料在水化学环境中经动水腐蚀28 d后表面均未产生明显的氧化膜,表明各材料均有较好的短期耐蚀性。
(2)与空管条件相比,在内置电加热棒条件下,Zr合金和涂层Zr合金表面的颗粒状氧化产物更密集,抗氧化性能更优。
(3)在空管条件和内置电加热棒条件下,涂层Zr合金相较于普通Zr合金具有更好的耐蚀性,但在内置电加热棒条件下,两种材料表面均检测到其他相,有待进一步研究。
免责声明:本网站所转载的文字、图片与视频资料版权归原创作者所有,如果涉及侵权,请第一时间联系本网删除。
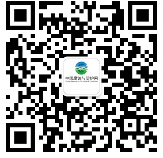
官方微信
《腐蚀与防护网电子期刊》征订启事
- 投稿联系:编辑部
- 电话:010-62316606
- 邮箱:fsfhzy666@163.com
- 腐蚀与防护网官方QQ群:140808414