高温合金具有优异的高温强韧性、良好的抗氧化和抗热腐蚀性能、显著的抗蠕变与抗疲劳性能以及优良的组织结构高温稳定性,被广泛应用于航空航天、石油化工等领域关键热端部件的制造[1~4]。其中涡轮动力系统关键热端部件(涡轮盘、涡轮叶片等)被誉为涡轮发动机的心脏,需长时间在高温、热腐蚀环境服役。因此,提高涡轮转子关键热端部件用高温合金的高温性能,始终是涡轮动力系统能效跃升、服役安全的核心保障[5,6]。随着高端航空发动机、重型燃气轮机研制技术的飞速发展,高品质涡轮转子用高温合金,更需在长期高温、疲劳环境下面临“高温强韧化”和“性能稳定性”的双重考验[7]。而强韧化设计与微结构热力学往往相互制约[8~10],成为先进涡轮系统研发的瓶颈之一[11]。
近年来,高能喷丸(shot peening,SP)、表面高速机械挤压(high-speed surface extrusion,HSE)、超声表面滚压(ultrasonic surface rolling process,USRP)和激光冲击(laser shocking processing,LSP)等表面冲击强化技术在两机涡轮转子抗疲劳制造领域的应用研究广泛深入地展开,显现出积极的效果和广阔的前景[12~14]。表面冲击强化通过在金属表层引入可观的塑性变形和残余压应力,诱导高密度位错、孪晶等表面微结构的改变[15~17],从而获得具有显著综合强化效果的梯度硬化层,有望成为高强金属材料有效的表面抗疲劳制造技术[16~21]。
然而,表面冲击强化在金属表面获得的高残余压应力硬化层[15],仍以垂直表面向内的冲击形变强化为主[12,15,17]。硬化层在剧烈塑性变形(severe plastic deformation,SPD)时产生的高密度位错、晶格畸变和亚稳界面,使表层获得可观残余压应力、显著强化效果的同时,也在表面引入了缺陷密度梯度分布的微结构亚稳层[18]。而对高温合金而言,600℃甚至以上的高温条件下,硬化层中的亚稳微结构易发生回复和退化,导致残余压应力的松弛甚至消失。这直接影响高温合金表面冲击硬化层高温强化作用的稳定性,也一直是制约表面强化技术在高温合金涡轮转子表面强韧化、抗疲劳制造中深入应用的瓶颈性问题[12,13],长期受到设计、制造和研究者的广泛密切关注。
迄今为止,关于高温合金表面冲击强化的诸多实际应用和研究报道中,表面硬化层高密度亚结构的回复推迟、残余压应力可保留的机理尚不明确。本文归纳了镍基高温合金表面冲击强化技术及应用的研究进展,在分析不同表面冲击强化技术提升镍基高温合金表面强韧性及抗疲劳作用规律的基础上,结合近年来本课题组的研究结果,探究了高温合金表面硬化层在高温下的显微组织、微结构演化机理。分析高温下维持表面强化作用的关键机制,展望镍基高温合金新型表面冲击强化技术和抗疲劳调控机制的未来发展方向,以期为具有更高承温能力的镍基高温合金关键涡轮转子强韧化与抗疲劳制造提供思路和参考。
1 高温合金的表面喷丸处理及喷丸强化
涡轮动力系统的高温合金关键热端部件,装机前需经多道次复杂机械加工,构件表面完整性易被破坏,表面粗糙度增大。加之机械加工难以避免在表层引起残余拉应力等,从而劣化了高温合金的高温疲劳性能[22]。尤其对于涡轮转子,其在长期服役过程中的高温抗疲劳性能,更是动力系统服役安全的关键[23,24]。因此,诸多金属材料的表面强化技术在高温合金转子构件的抗疲劳制造领域倍受关注[23~25]。表面喷丸处理,作为便于实施、低成本和冲击能量输入可准确调控的表面处理技术,较早被用于高温合金的表面强化[26,27]。喷丸处理采用硬质钢丸、铸铁丸、陶瓷丸等轰击工件表面,在表层引入残余压应力,可有效抵消机械加工的表面残余拉应力,提高材料的抗疲劳能力[28~31]。喷丸处理对高温合金构件的影响主要有:硬化层残余应力分布状态、表面形态和疲劳裂纹萌生阻力等[13,28]。
1.1 高温合金喷丸处理后的表面应力状态及分布
高温合金表面喷丸强化的研究[29~31]表明,喷丸处理可明显改变机械加工的残留表面拉应力,在合金表面引入了较为理想的残余压应力层,这对高温疲劳抗力要求很高的高温合金涡轮转子,无疑具有高的实用价值。钟丽琼等[28]的研究发现,对FGH97合金进行陶瓷弹丸90°喷射4 min处理后,次表层(距表面几十微米)处获得了较高的残余压应力,应力场深度可达280 μm左右。Wang等[30]对FGH96合金进行了车削、陶瓷喷丸和复合喷丸(高强铸铁弹丸和低强陶瓷弹丸)残余压应力场的对比研究,发现喷丸处理明显增加了表层残余压应力,并且应力最高值、深度均随喷丸强度的增加而增大(图1[30])。在铸造高温合金、变形高温合金的相关研究中也获得了相似的效果。K4169铸造高温合金喷丸处理后表面残余压应力由258 MPa增加至1079 MPa,进而显著提高了合金的疲劳寿命[32]。
图1
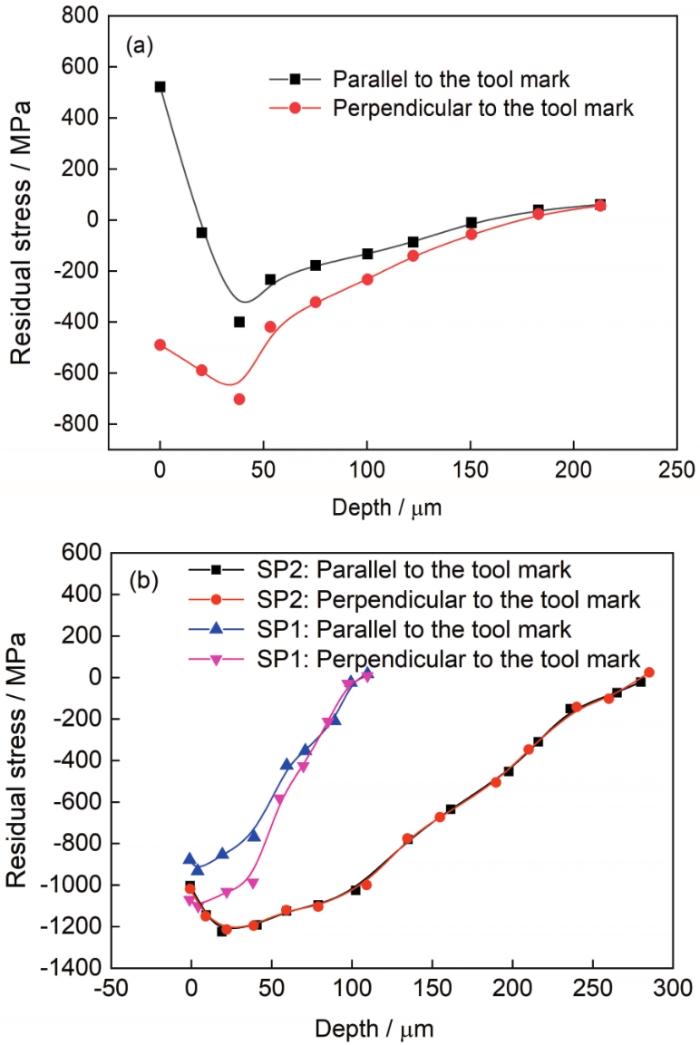
图1 喷丸处理对FGH96合金表面硬化层残余压应力分布的影响[30]
Fig.1 Effects of shot peening on the residual compress-ive stress distribution of surface hardened layer of FGH96 alloy[30]
(a) before shot peening (turning)
(b) ceramic bead peening and compound shot peening (SP1—parallel to the tool mark, SP2—perpendicular to the tool mark)
1.2 高温合金喷丸处理后的表面硬化层组织
喷丸处理过程中,高温合金表面产生了理想残余压应力的同时,显微组织亦发生了显著变化。Zhao等[33]对GH4169合金喷丸强化的研究发现,经过喷丸强化后合金表面形成厚度约96 μm的硬化层,而且表面形成平均尺寸约为9 nm的等轴纳米晶(图2[33])。在一定深度范围内还形成高密度形变孪晶,进一步细化了硬化层合金的显微组织,提高了合金的高温疲劳抗力。在IN718合金的研究[34]中发现,超声喷丸处理也可获得厚度约为90 μm、平均晶粒尺寸约为12 nm的表面纳米晶层,有效地提高了合金的高温疲劳抗力。喷丸处理中,高温合金表面产生显著塑性变形,必然引起位错密度增加,并在晶界处形成大量的位错塞积与缠结,这是喷丸处理获得表面硬化层的根本原因。
图2
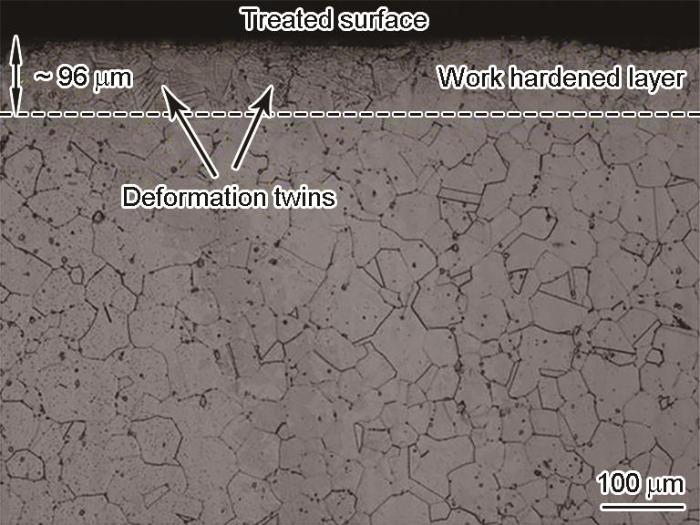
1.3 高温合金喷丸处理后的表面粗糙度
图3
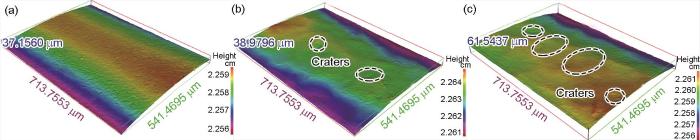
1.4 高温合金表面喷丸强化的抗疲劳作用及影响因素
图4
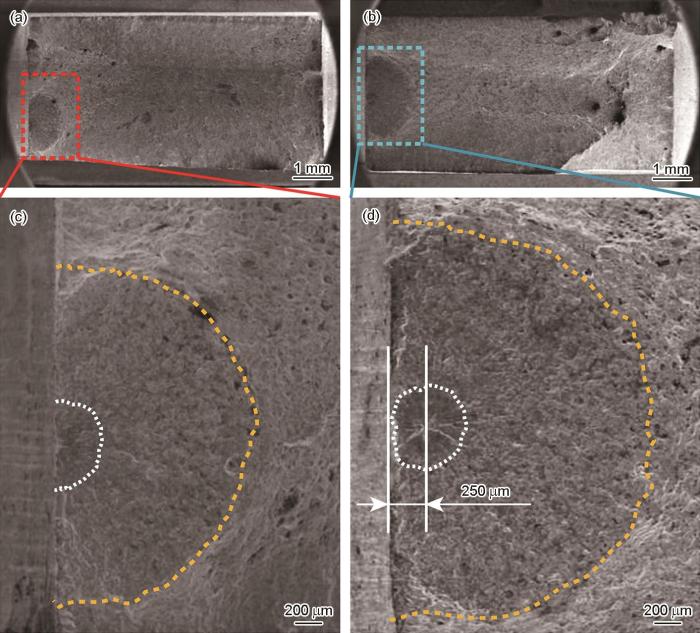
图4 喷丸处理对Udimet 720Li合金相同载荷幅条件下疲劳裂纹萌生位置的影响[35]
Fig.4 Effects of shot peening on fatigue crack initiation location of Udimet 720Li alloy before (a, c) and after (b, d) shot peening under the same load amplitude[35] (Fig.4c enlarged for red frame in Fig.4a, Fig.4d enlarged for the lake blue frame in Fig.4b)
亦有研究表明,高温合金喷丸处理的抗疲劳强化作用与应力状态、应力幅值均有关。Dong等[35]对Udimet 720Li合金的研究发现,与未喷丸合金相比,喷丸处理后合金的缺口低周疲劳寿命显著提高,其在1390和1070 MPa应力幅下的增幅分别为2.05倍和6.07倍。由此可见,喷丸处理在低应力水平下对提高疲劳寿命的作用更加显著。此外,应力状态还影响喷丸硬化层的残余应力松弛程度。高玉魁等[31]对FGH97合金喷丸前后的不同应力状态疲劳寿命进行对比,发现在630 MPa的低应力状态下,喷丸硬化层的残余压应力可有效延缓表面裂纹萌生,提高合金的疲劳寿命。而在740 MPa高应力状态下硬化层的残余压应力作用减弱,抗疲劳作用并不明显。Luo和Bowen[38]对Udimet 720Li合金的研究也证实了600℃高温条件下,在较低的应力幅范围内,喷丸处理可提高合金的疲劳寿命;而当处于高应力幅时,喷丸处理反而降低了合金的疲劳寿命。
图5

2 高温合金的表面机械挤压强化
2.1 高温合金机械挤压表面粗糙度
2.2 高温合金机械挤压硬化层组织及硬度
2.3 高温合金机械挤压硬化层的残余压应力
图6
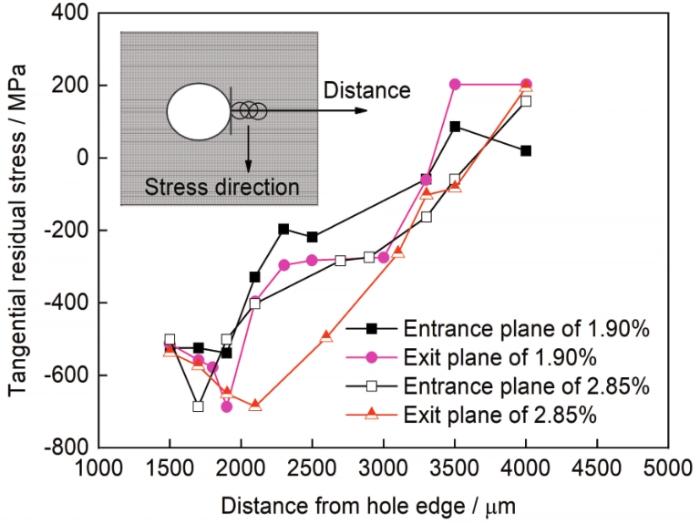
3 激光冲击处理高温合金表面强化
3.1 高温合金LSP处理的表面粗糙度
图7
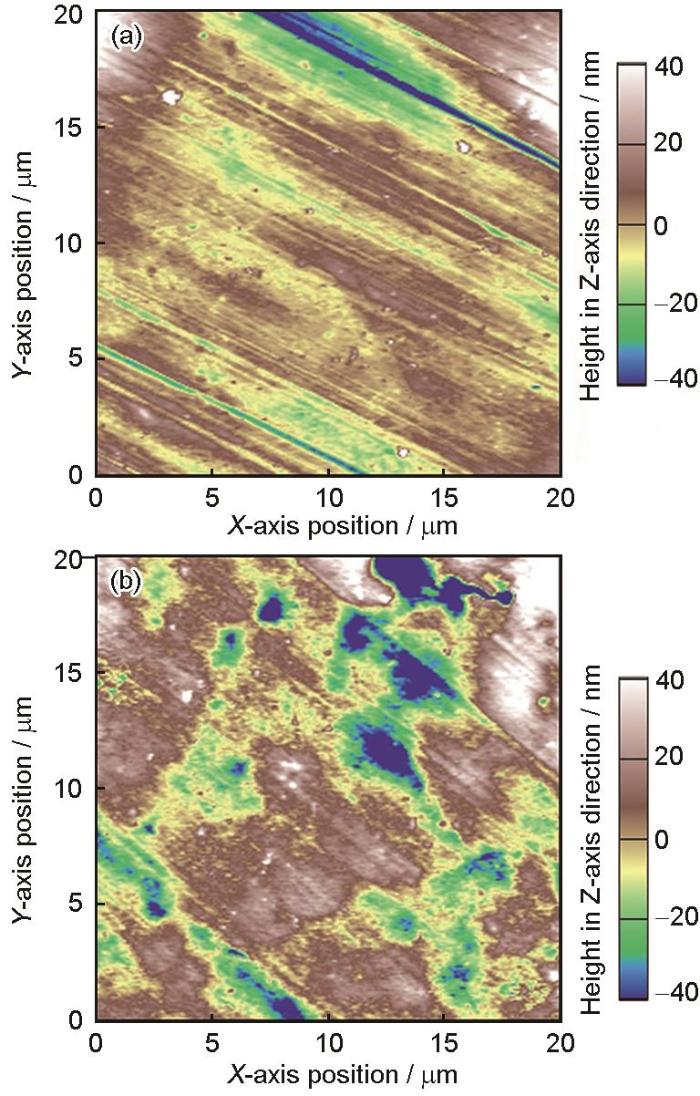
3.2 高温合金LSP处理的硬化层组织及硬度
Rozmus-Górnikowska等[49]对Inconel 625合金LSP处理的研究发现,LSP处理后合金表面形成较大塑性变形,产生高密度位错和密集分布的滑移带,表面形成呈梯度分布的冲击硬化层。Cao等[50]关于GH4586合金LSP处理的研究表明,LSP表面硬化层的位错密度显著增加,形成高密度缠结位错、位错壁和位错胞结构,LSP处理后合金的疲劳寿命增加了近1倍。而且,LSP硬化层表面的平均晶粒尺寸降低约43.6%,同时发现基体中形变孪晶数量亦明显增多,使GH4586合金LSP硬化层表面获得了明显的协同强化作用,硬度提高幅度达到27.4%。值得关注的是,经LSP处理的GH4586合金表层γʹ相中也观察到大量的层错以及高密度位错,这在传统机械作用表面处理的高温合金硬化层中未见报道。LSP处理后,GH4586合金硬化层中不同尺度、高密度微结构的形成与细化,有效抑制了疲劳裂纹的萌生和扩展,显著提高了合金的疲劳抗力。Luo等[51]对K417合金进行LSP处理的研究发现,激光冲击引入剧烈塑性变形,在合金表面产生更高密度的位错缠结,硬化层表面形成纳米晶,使表层硬度明显增加。此外,LSP处理后进行900℃、10 h的保温,K417合金硬化层中高密度位错、晶粒细化等微结构特征并未见显著变化,强化效果表现出了较好的高温稳定性,这主要与LSP硬化层的高密度位错与纳米晶复合结构有关。
研究者们[12,13,19]对如何在高温合金表面获得高温稳定的抗疲劳硬化层进行了大量的研究,发现引入温度场的温度辅助耦合激光冲击强化技术(warm laser shocking processing,WLSP),可获得高温强化增幅更显著的抗疲劳硬化层。本课题组[19,52]对比研究了LSP和WLSP处理IN718合金的表面硬化层微结构特征,发现WLSP作用下能够在高温合金表面获得强化相/高密度位错复合微结构(图8[52])。而且,值得关注的是,IN718合金WLSP硬化层中的γ′′相内部观察到高密度层错及纳米尺寸孪晶(图8b[52]中蓝色箭头所示)。硬化层中有序强化相内部纳米尺度微结构的形成和细化,显著提高了硬化层的强化效果和高温稳定性。
图8
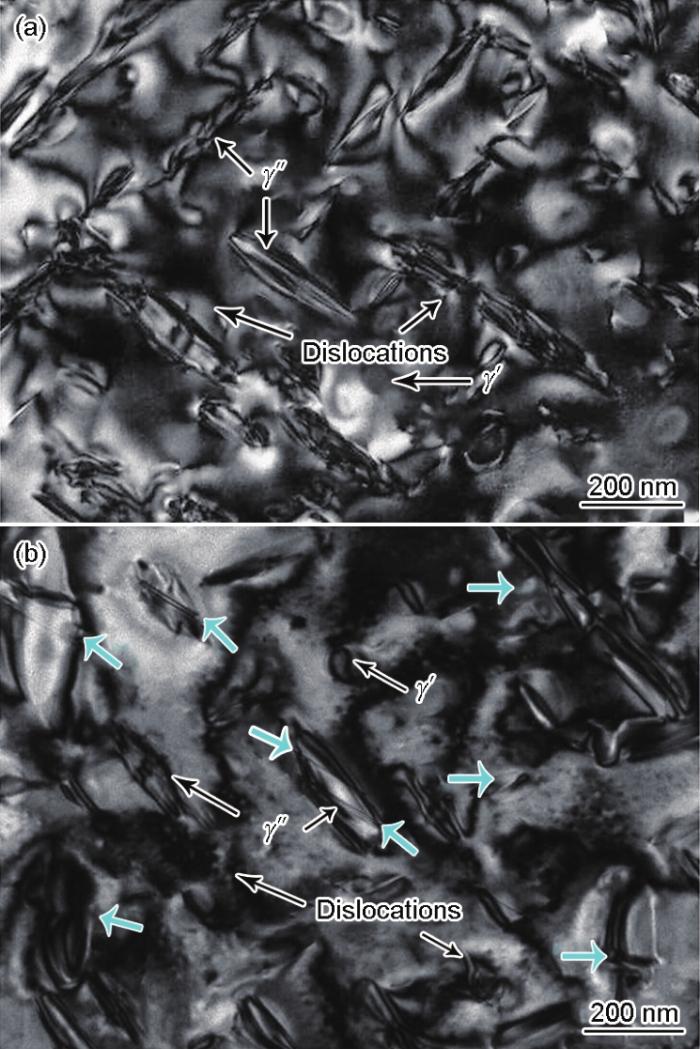
图8 IN718合金LSP、温度辅助耦合激光冲击强化技术(WLSP)硬化层中的γ″相及位错形态[52]
Fig.8 Morphologies of γ″ phase and dislocation patterns in the hardened layers of IN718 alloy treated with LSP (a) and warm laser shocking processing (WLSP) (Blue arrows show the γ″ phase/high-density dislocation complex structure containing stacking faults and nanosized twins) (b)[52]
3.3 高温合金LSP处理的硬化层残余应力状态
图9
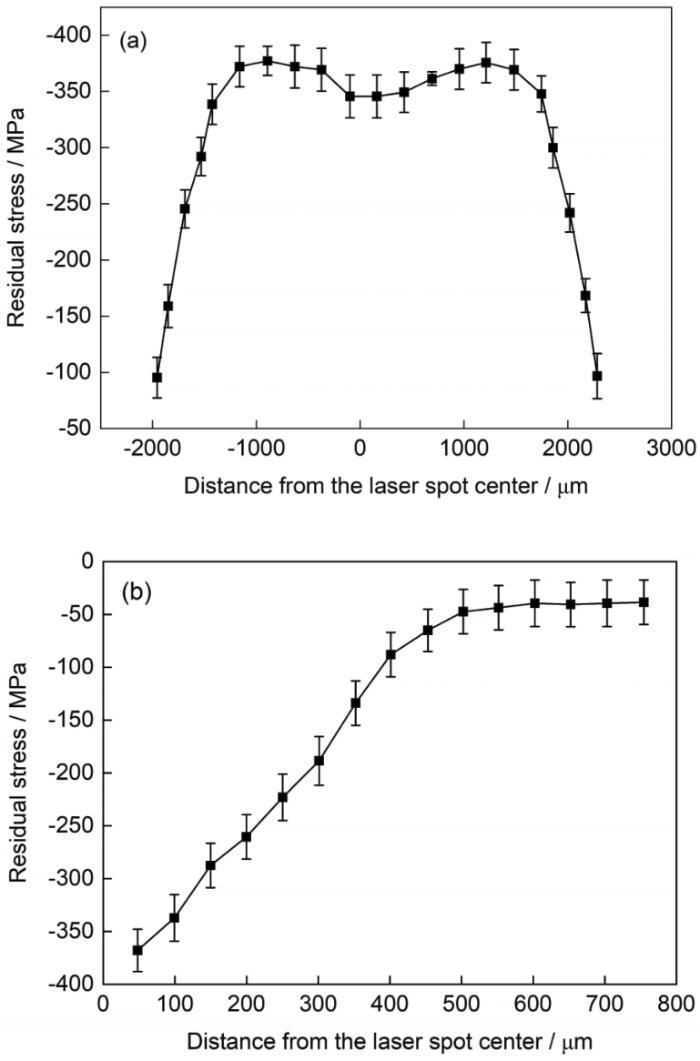
4 高温合金的表面冲击强化微观机制
4.1 喷丸及机械冲击表面硬化机理
高温合金表面喷丸、机械挤压处理硬化层的形成,主要是表面机械冲击过程中基体剧烈塑性变形的结果[32~34,54~59],塑性变形程度及影响层深度与弹丸、机械冲击的能量输入直接相关。孔挤压强化IN718合金孔内壁表面160 μm深度范围内可观察到明显的旋转塑性变形,越靠近内壁表面,变形程度越大[60]。RR1000合金经过喷丸处理后,表面硬化层剧烈塑性变形的晶粒比例明显增加,形成大量亚结构[61]。FGH96合金[30]、FGH97合金[28]经喷丸处理后,硬化层小角晶界比例显著增加。随表面喷丸或机械冲击能量输入的增加,高温合金硬化层表面发生了明显的晶粒细化。对K417合金的喷丸硬化层进行后处理,亦可形成较大深度范围的细晶硬化层,有效抑制表面疲劳裂纹的萌生[62]。
4.2 LSP和WLSP处理表面强化机理
图10
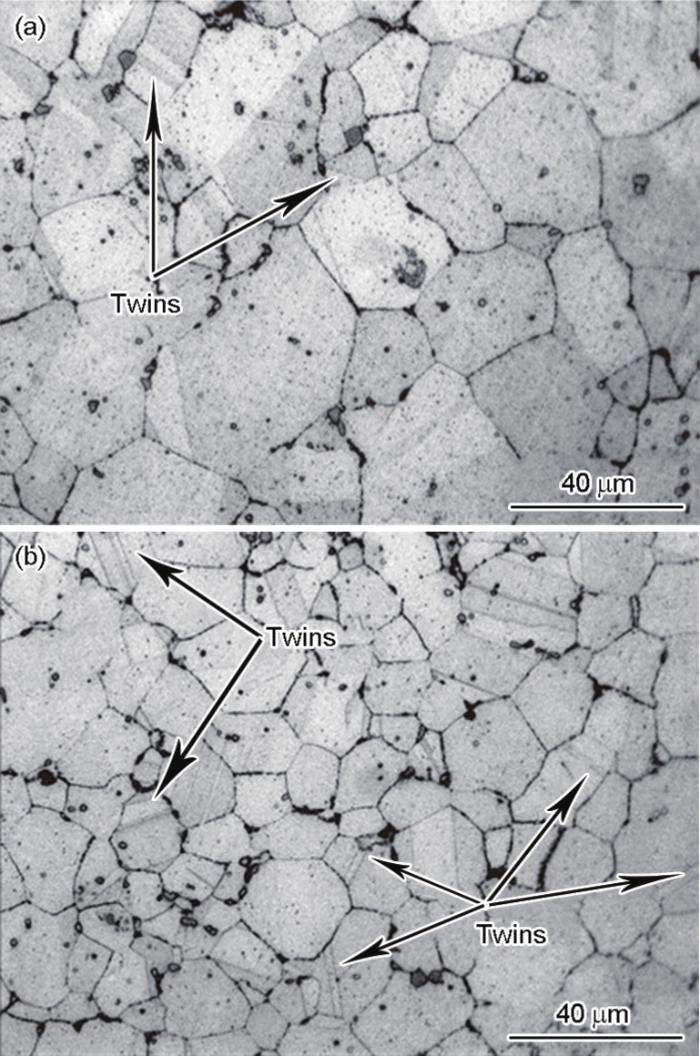
调整LSP处理参数可在高温合金表面硬化层形成不同的组织结构。Yu等[64]对GH4169合金利用高能LSP、低能LSP和飞秒LSP处理调控硬化层微结构,发现飞秒LSP硬化层深度基本小于100 μm,而低能LSP处理后,合金硬化层深度增加,表面可诱导形成高密度亚结构。但由于能量输入较低,低能LSP处理仅在距表面约100 μm范围内形成了致密的亚结构,在100 μm以下的区域,主要以位错的增殖或缠结为主,而未发现致密亚结构层。当提高输入能量时,高能LSP处理的剧烈变形影响层深可达几百微米甚至几毫米,层深1400~1600 μm时,仍可观察到致密亚结构。
图11
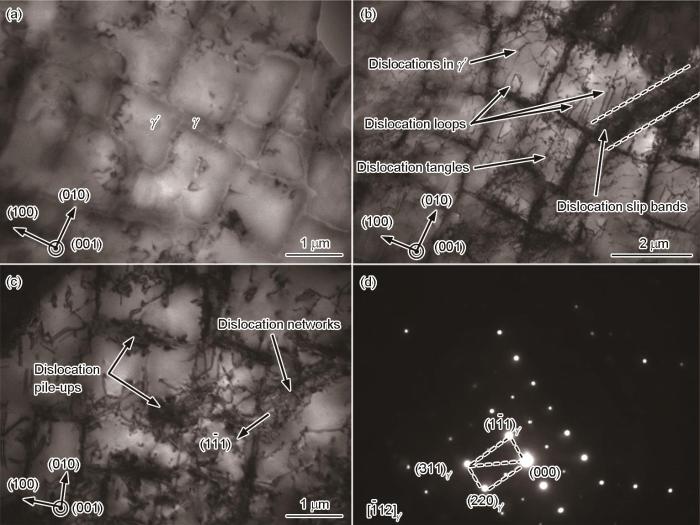
图11 LSP处理对某镍基单晶高温合金表面硬化层基体位错密度及γ′相内部微结构的影响[65]
Fig.11 Effect of LSP on the dislocation density of matrix and microstructure of γ′ phase in the surface hardened layer in nickel-based single crystal superalloy[65]
(a) untreated
(b-d) low (b) and high (c) magnified images of samples treated by LSP, and SAED pattern of Fig.11c (d)
图12
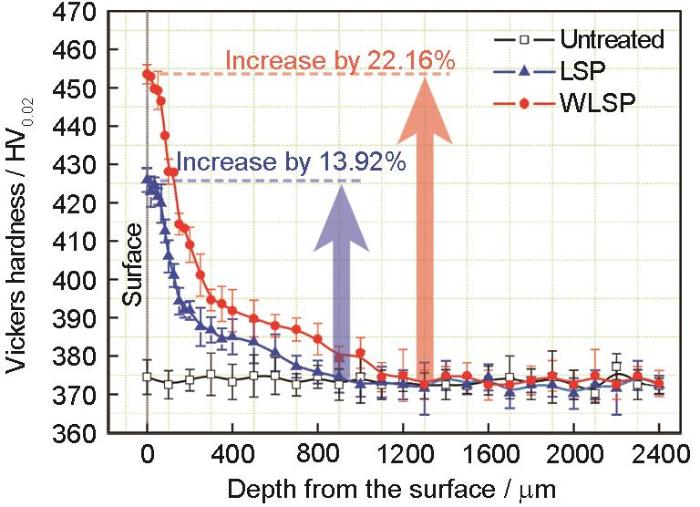
图13
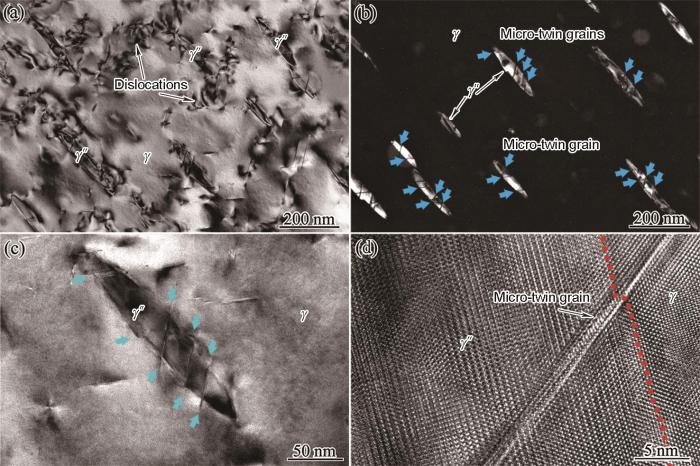
图13 WLSP处理后IN718合金表面硬化层γ″相/高密度位错复合体形态及强冲击作用下γ″相中出现的微孪晶[19]
Fig.13 Morphologies of complex structure of γ″ phase/high-density dislocation and micro-twins in γ″ phase induced by strong impact in the surface hardened layer of WLSP-treated IN718 superalloy[19]
(a) morphology of complex structure of γ″ phase/high-density dislocation
(b) dark field morphology of γ″ phase in Fig.13a (Blue arrows show micro-twins)
(c) micro-twins in γ″ phase induced by strong impact (Blue arrows show micro-twins)
(d) HRTEM image of micro-twins at the γ/γ″ interface
图14

图14 经WLSP处理后IN718合金表面硬化层中γ″/γ界面细节的HRTEM像[52]
Fig.14 HRTEM images of the details of γ″/γ interface in the surface hardened layer of WLSP-treated IN718 superalloy[52] (a, d) HRTEM images of γ″/γ interface (a) and γ″ phase (d) in the surface hardened layer (Insets show fast Fourier transform (FFT) diffraction patterns) (b, e) magnified parts in the red boxes in Fig.14a (b) and Fig.14d (e), showing HRTEM images and corresponding maps of the geometric phase images (GPA) strain component εxx (εxx —x-direction in-plane strain) (c, f) line profiles of strain maps scanned along lines 1, 2, and 3 in Fig.14b (c) and lines 4, 5, and 6 in Fig.14e (f)
WLSP处理IN718合金硬化层中这种特殊结构贯穿γ″/γ相界面,其改变了γ″/γ相界面形态,使得γ″相内部及其周围应变分布的复杂程度提高。这种特殊结构势必阻碍高温服役下位错反应和位错回复。同时,高温下这些高密度位错包裹、内含微孪晶的γ″相,其长大以及γ″→δ相转变的复杂程度均将加剧。
综上,高温合金表面LSP和WLSP硬化层的强化本质,除剧烈塑性变形在基体中引入的高密度缺陷及亚结构和大量形变孪晶外,还包括在γ'、γ″主要相内部诱导形成大量层错、微孪晶等特殊微结构。与传统喷丸处理和表面机械冲击/挤压强化相比,LSP和WLSP处理合金表面硬化增量更显著、硬化层更深,并且形成了稳定强化相/高密度位错复合结构和剧烈塑性变形亚结构,有利于提高高温合金的表面强化和抗疲劳能力。那么,如能利用耦合场在硬化层引入更多微纳尺度“异质结构(heterostructure)”[66~68]、“化学界面工程(chemical boundary engineering)”[69,70]等强化因素,有望在高温合金表面处理过程中收获更显著的强韧化效果。
5 高温合金表面强化的高温稳定性
5.1 硬化层高密度亚结构的演化与位错反应
王欣等[42]对比研究了孔挤压GH4169合金在400和600℃条件下抗疲劳强化的高温稳定性。发现,即使孔挤压合金获得了明显的强化;但高温下,位错运动激活能降低、位错运动能力增加,残余压应力易发生应力松弛,硬化层的疲劳抗力降低;当温度提高到600℃时,基体高密度位错的强化作用下降更加明显。
图15
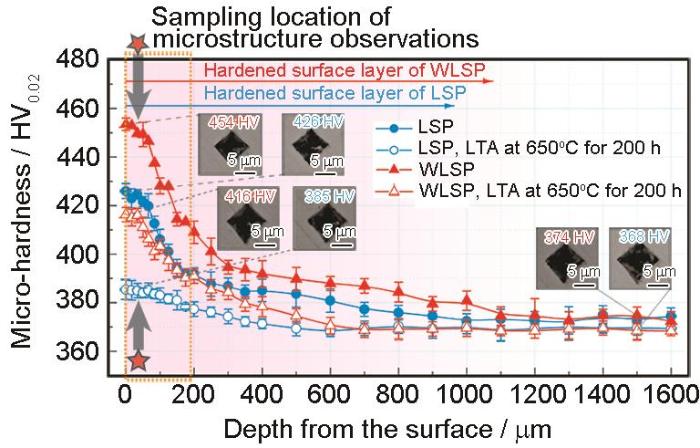
基体中高密度位错缺陷在高温下的快速演化,在经表面机械冲击/挤压、LSP和WLSP硬化层中普遍发生。机械冲击/挤压处理的高温合金硬化层,由于表面强化的主要微结构为高密度缺陷,高温下这些缺陷的减少,导致硬化层稳定性降低、强化作用退减。
5.2 高温下硬化层细晶组织及形变孪晶的演化
超细晶(纳米晶)层并非高温合金表面硬化层的普遍性微结构特征,多出现在高能机械冲击/挤压叠加硬化层和LSP硬化层表面,其分布深度也仅约100 μm。高温时效中,表面晶粒长大迅速,硬化层稳定性降低。而高温合金表面硬化层的形变孪晶比纳米晶更为常见,且生成深度达200~500 μm,是高能机械冲击/挤压处理高温合金硬化层的典型微结构特征。Zhao等[33]研究GH4169合金超声喷丸硬化层形变孪晶高温稳定性发现,350℃保温后硬化层形变孪晶无明显改变;当温度升高至650℃时,孪晶间距明显加宽,导致硬化层的硬度降低。
5.3 冲击诱导强化相内部微结构的高温稳定性
研究[65,81~93]发现,与机械冲击/挤压硬化层相比,LSP和WLSP处理硬化层在高温长期时效后的抵抗疲劳裂纹萌生、扩展方面更具优势。Buchanan等[82]对比研究了IN100合金的喷丸处理、LSP处理硬化层的高温应力松弛,发现650℃、100 h时效后,喷丸硬化层最大残余压应力下降约800 MPa,而LSP处理的仅下降200 MPa (图16[82])。可见,LSP处理除使表面强化幅度和硬化层深度明显增加外,硬化层高温服役的稳定性也更佳。Lu等[83]研究GH4169合金WLSP硬化层的高温长期时效组织、性能稳定性发现,WLSP硬化层的残余应力降低幅度明显小于LSP硬化层。而且,600℃的时效未观察到表面残余压应力的显著改变。但当时效温度升高至650℃时,LSP硬化层的残余压应力几乎完全释放,而WLSP处理的残余压应力仅降低约8%。当时效温度增加到700℃时,WLSP硬化层的残余应力在时效100 h后仍可保持在原来的50%左右,表现出极高的高温稳定性。
图16

本课题组[81]对长期时效后LSP和WLSP处理IN718合金的硬化层硬度进行了系统对比,发现600和650℃时效200 h后,LSP和WLSP硬化层硬度、深度均有所降低。但经过650℃及以下温度长期时效后,WLSP处理的IN718合金表面硬化层硬度、深度的降低幅度均小于LSP处理(图17[81])。尤其是,WLSP处理合金经650℃、200 h长期时效后表面硬度增量的下降幅度仅为40.79%,而相同时效条件下LSP处理合金表面硬度增量的下降幅度达71.69%。680℃、200 h时效后,LSP处理合金的表面硬化现象几乎完全消失,而此时WLSP处理合金表面硬度仍保持一定的增量。研究[81]还发现,表面硬化层的强化增量主要来源于LSP和WLSP处理后合金中的高密度位错增殖和塞积(图18[81])。尤其对于WLSP硬化层而言,更显著的强化作用主要来源于硬化层γ″相/高密度位错复合微结构。同样,WLSP硬化层的强化现象在600℃以上长期时效后仍得以保持,也主要取决于WLSP处理诱发的高密度位错和特殊亚结构。
图17
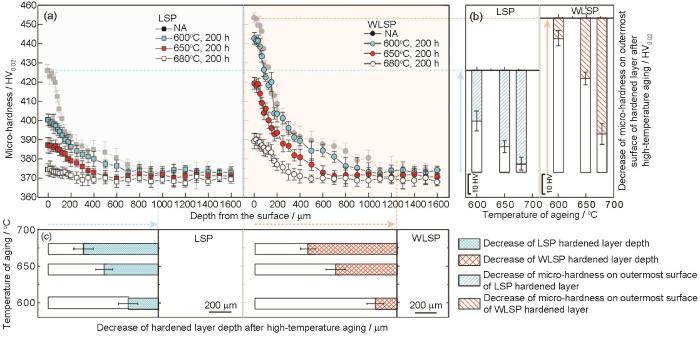
图17 不同温度长期时效后IN718合金LSP和WLSP硬化层硬度分布及硬化层深度变化[81]
Fig.17 Micro-hardness distributions and depth changes of the surface hardened layer of LSP and WLSP IN718 alloys after aging at high temperatures (NA—non-aging)[81]
(a) micro-hardness of surface hardened layer after aging at different temperatures treated by LSP and WLSP
(b) comparison of micro-hardness of hardened layer
(c) comparison of hardened layer depth
图18
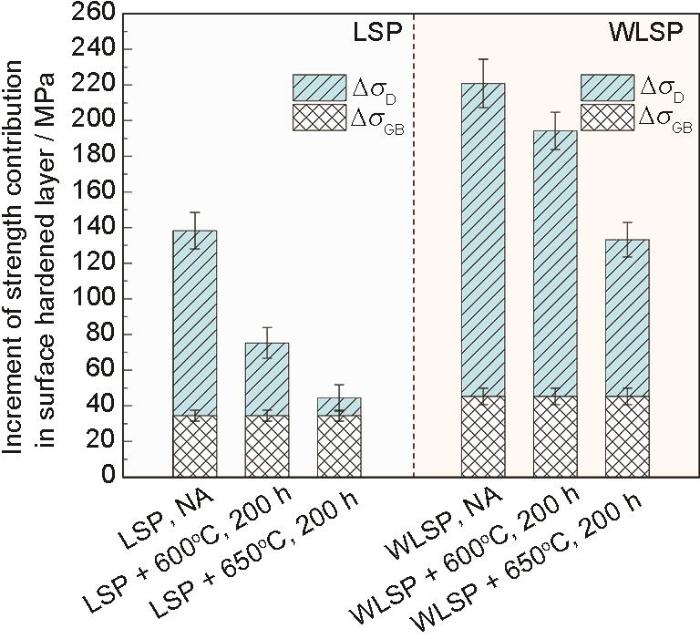
图18 长期时效对LSP和WLSP处理的IN718合金表面硬化层强化机制贡献增量的影响[81]
Fig.18 Effects of long-term aging on the contribution increment of strengthening mechanism of the surface hardened layer of LSP and WLSP IN718 alloys[81] (ΔσD—strength contribution from dislocation strengthening, ΔσGB—strength contribution from grain boundary strengthening)
本课题组[54]在研究长期时效后LSP和WLSP处理IN718合金表面硬化层的几何必需位错(geometrically necessary dislocation,GND)演化行为发现,WLSP硬化层的GND密度明显高于LSP处理,升高幅度约为248.71% (图19[52])。硬化层中GND密度的增加,除形成各向同性强化外,更重要的是可产生更加显著、稳定的背应力强化。经长期时效处理后,LSP硬化层中的GND密度明显降低,而WLSP硬化层的GND密度虽有降低,但降幅很小。而且长期时效后,LSP处理合金GND密度统计分布的相对频率峰位,向低位错密度方向发生了明显的移动,同时相对频率峰值也呈现出明显的上升趋势。但WLSP硬化层在长期时效后GND密度统计分布相对频率的峰值、峰位、峰宽无明显变化。这进一步说明,WLSP处理不仅仅使IN718合金获得了更高的GND密度,而且GND密度的集中程度和分布位置变化并不明显,WLSP处理合金均表现出了比LSP处理合金更显著的高温长期服役稳定性。
图19
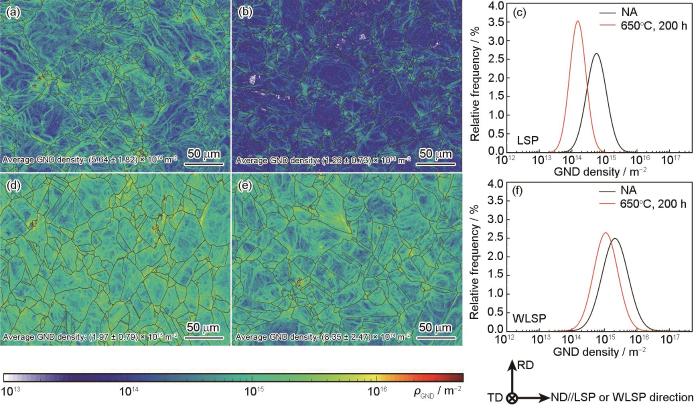
图19 650℃长期时效后LSP和WLSP处理IN718合金表面硬化层的几何必需位错(GND)密度分布图及正态分布统计图[52]
Fig.19 Geometrically necessary dislocation (GND) density (ρGND) maps (a, b, d, e) and corresponding normal distribution statistical diagrams of GND density (c, f) of the surface hardened layer of LSP (a-c) and WLSP (d-f) IN718 alloys before (a, d) and after (b, e) long-term aging at 650oC[52] (RD—rolling direction, TD—transverse direction, ND—normal direction)
6 总结与展望
本文基于先进涡轮动力系统用镍基高温合金的典型表面强化技术,以及强化作用高温稳定性的研究和应用分析,就镍基高温合金表面冲击强化总结与展望如下。
(1) 高温合金的表面机械喷丸、挤压/滚压强化处理,均可产生明显残余压应力和硬化层,有效阻碍裂纹在表面萌生,从而提高高温合金的疲劳抗力。但应用中需注意控制喷丸处理造成的表面粗糙度增大、挤压/滚压处理的残余压应力梯度调控以及表面机械强化超过500℃后的强化作用衰减。
(2) LSP和WLSP处理等表面高能冲击强化技术具有不受构件规格、形状限制的独特优势,同时其强化增幅及层深均优于机械表面强化处理,由此经其处理的高温合金显示出更高的疲劳抗力。WLSP处理在高温合金表面硬化层中形成的“有序强化相/高密度位错复合特殊微结构”,进一步提升了表面强化的作用效果。
(3) 硬化层微结构的高温、长时稳定性,是高温合金表面强化技术飞跃发展与深入应用的关键。高温合金表面剧烈塑性变形产生的基体微结构中,高密度缺陷的高温演化与回复显著,不具备高温稳定能力。表面细晶(纳米晶)层较浅,高温下长大倾向明显,稳定性亦不足。而形变孪生可在600℃以下保持一定的高温稳定性。耦合场高能强冲击(LSP和WLSP等)处理在获得上述基体微结构的同时,诱导γ′、γ″相内部形成内含大量层错、微孪晶的“强化相/高密度位错复合特殊微结构”,是使硬化层兼具强化作用、高温稳定性与长时稳定性的关键特殊微结构。
(4) WLSP处理在高温合金表面冲击强化作用高温稳定性方面所凸显的优势,启发人们应关注硬化层不同尺度关键微结构的综合调控。如能利用高能冲击耦合场将诸如“异质结构”、“化学界面工程”等微纳尺度强韧化理念引入高温合金的表面微结构精准设计,在硬化层精准诱导“有序强化相/高密度位错特殊微结构”的梯度分布,构筑具有更高高温强度与高温稳定性的表面硬化层,将有望开辟高温合金表面强化相关研究的新方向。
免责声明:本网站所转载的文字、图片与视频资料版权归原创作者所有,如果涉及侵权,请第一时间联系本网删除。
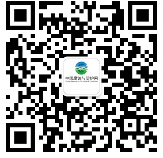
官方微信
《腐蚀与防护网电子期刊》征订启事
- 投稿联系:编辑部
- 电话:010-62316606
- 邮箱:fsfhzy666@163.com
- 腐蚀与防护网官方QQ群:140808414