取样时间/h | 24 | 72 | 240 | 336 | 720 | 1 008 | 1 440 | 1 680 | 2 160 | 2 880 | 3 888 | 4 560 |
---|---|---|---|---|---|---|---|---|---|---|---|---|
平行样数量/个 | 18 | 17 | 16 | 15 | 14 | 13 | 12 | 11 | 10 | 9 | 8 | 7 |
SiC具有耐高温(最高达1 650 ℃)、抗氧化、低热膨胀系数、中子吸收截面小等优点[1]。在此基础上发展起来的碳化硅和碳化硅纤维(SiCf)陶瓷复合材料SiC/SiCf不仅继承了SiC的优点,还具有比强度高、中子辐照下尺寸稳定性高等特点。因此,SiC/SiCf复合材料有望成为新一代压水堆核燃料包壳管材料[2]。SiC/SiCf复合材料包壳管整体为三层结构,内层为致密的SiC涂层,中间层为SiC纤维,外层为SiC涂层。其中,中间层SiC纤维采用化学气相渗透法(CVI)制备,内外的SiC层采用化学气相沉积法(CVD)在SiC纤维表面进行沉积,以填补SiC/SiCf复合材料间的空隙并形成一定厚度的涂层。
为确保SiC/SiCf复合材料作为燃料元件包壳材料的安全性与可靠性,对SiC/SiCf复合材料在高温高压水中的腐蚀性能进行研究显得尤为重要。国内外研究者对SiC材料在高温高压水中的腐蚀行为做了相应的研究分析和总结[3-9]。刘俊凯等[3]认为在轻水堆正常工况条件下,SiC会与高温水发生反应生成SiO2,而SiO2会进一步溶解于水中生成H2SiO3和Si(OH)4,从而导致SiC材料的质量损失。在高温高压水中,相比于其他方法制备的SiC,采用化学气相沉积法制备的SiC的腐蚀速率最低[4]。
目前,关于模拟压水堆一回路水环境中SiC/SiCf复合材料腐蚀行为的报道较少。因此有必要开展这方面的研究,分析SiC/SiCf复合材料在高温高压水环境中的腐蚀行为。作者在模拟压水堆一回路水化学工况下,研究了SiC/SiCf复合材料包壳管在高温高压水中的腐蚀行为。
1. 试验
试验采用循环高温高压水腐蚀系统模拟了压水堆一回路水化学工况,研究了SiC/SiCf复合材料包壳管的腐蚀行为。试样为管状,外径为10 mm、内径为8 mm、长度为20 mm。将试样进行磨抛后,用酒精超声清洗,再用去离子水冲洗,然后干燥备用。试验介质为含1 200 mg/L B和1 200 mg/L Li的水溶液,用分析纯H3BO3、LiOH·H2O和去离子水配制。向试验介质中通入高纯氮气(纯度99.99%),并通过减压阀、质量流量计调节氮气流量,使水中溶解氧质量浓度为5 mg/L(溶解氧含量通过高精度溶氧仪测定,并进行定期标定),压力为(20±0.5)MPa。循环水流速为10 L/h,水环境温度为(360±1)℃。将试样全浸于试验介质中,待试验条件达到预设值时开始试验。在试验进行至0、24、72、240、336、720、1 008、1 440、1 680、2 160、2 880、3 888、4 560 h时,取样观察并称量。在腐蚀试验过程中,取样时间以及所对应的平行样数量如表1所示。
将经过一段时间腐蚀后的试样取出,用去离子水洗净,待其干燥之后用精度为0.01 mg的分析天平称量,计算腐蚀后试样的质量损失,并采用式(1)计算其质量损失速率。
|
(1) |
式中:v为试样质量损失速率,mg/(cm2·h);w0和w分别为腐蚀前和腐蚀后试样的质量,mg;S为试样的表面积,cm2;t为腐蚀时间,h。
采用扫描电镜(SEM)观察腐蚀前后试样的表面及截面微观形貌,同时采用附带的能谱仪(EDS)进行成分分析。
2. 结果与讨论
2.1 腐蚀曲线
图1是腐蚀后SiC/SiCf复合材料包壳管试样质量损失和质量损失速率曲线。腐蚀试验总周期为4 560 h。根据腐蚀后SiC/SiCf复合材料包壳管质量损失可将腐蚀分为四个阶段:0~336 h阶段(质量增加);336~720 h阶段(质量加速损失);720~3 888 h阶段(质量稳定损失);3 888~4 560 h阶段(质量损失趋缓)。当腐蚀时间达到4 560 h时,SiC/SiCf复合材料包壳管在高温高压水环境中整体表现为腐蚀质量损失。
在0~336 h阶段,SiC/SiCf复合材料包壳管腐蚀后的质量损失不断减小且呈现负值,整体表现为腐蚀后质量增加,腐蚀336 h后,其质量损失速率为-2.2 μg/(cm2·h)。
在336~720 h阶段,SiC/SiCf复合材料包壳管由腐蚀后质量增加转变为腐蚀后质量损失,且随着腐蚀时间的延长,SiC/SiCf复合材料包壳管质量损失不断增大,质量损失速率呈上升趋势,腐蚀进程不断加快。腐蚀720 h后,SiC/SiCf复合材料包壳管质量损失速率为1.4 μg/(cm2·h)。
在720~3 888 h阶段,SiC/SiCf复合材料包壳管均表现为腐蚀后质量损失,且随着腐蚀时间的延长,腐蚀后质量损失持续增大,这说明在高温高压水中SiC/SiCf复合材料包壳管持续发生腐蚀溶解。在该阶段,质量损失速率随着腐蚀时间的延长变化不明显,表明SiC/SiCf复合材料包壳管在高温高压水中的腐蚀进程趋于稳定。腐蚀2 880 h后,其质量损失速率为3.4 μg/(cm2·h),与腐蚀720 h后的质量损失速率相比,显著增大。这说明随着腐蚀时间的延长,SiC/SiCf复合材料包壳管腐蚀程度逐渐加深。
在3 888~4 560 h阶段,SiC/SiCf复合材料包壳管仍表现为腐蚀后质量损失,但质量损失趋缓,质量损失速率略有下降。这说明随着腐蚀时间的延长,SiC/SiCf复合材料包壳管腐蚀进程有所减缓。
2.2 腐蚀形貌与化学成分
由图2(a)可见,未腐蚀(腐蚀时间为0)SiC/SiCf复合材料包壳管表面的空隙较少且空隙尺寸较小,但由于SiC纤维的厚度不同,在包壳管表面沉积的外层SiC涂层也呈现凹凸起伏的形貌,这增大了材料发生腐蚀的表面积,涂层表现为角状结构,角状晶分布较为均匀。从图2(b)角状晶放大后的形貌可见,SiC涂层表面存在明显的高度起伏。EDS分析结果表明,未腐蚀的SiC/SiCf复合材料包壳管表面涂层主要由硅和碳元素组成,并出现了微量的氧元素,见表2,这说明其表面发生了轻微的氧化。
腐蚀时间/h | 质量分数/% | ||
---|---|---|---|
Si | O | C | |
0 | 82.81 | 0.05 | 17.14 |
240 | 75.46 | 10.06 | 14.48 |
1 140 | 63.04 | 25.71 | 11.24 |
从图3(a)中可以看出,腐蚀240 h后,SiC/SiCf复合材料包壳管表面尖锐的角状结构更加平整。放大后可见,角状晶表面形成较多细小的凹坑,如图3(b)所示,这说明角状晶发生了腐蚀溶解,在其内部形成了细小密集的腐蚀坑。在角状晶表面可观察到纳米级的球状和棒状的白色颗粒,部分区域氧化物颗粒聚集形成了膜结构。由表2可知,腐蚀240 h后,SiC/SiCf复合材料包壳管表面除了含有硅、碳元素外,还含有较多氧元素,推测白色颗粒为富硅氧化物。这种富硅氧化物薄膜覆盖在角状晶表面,会在一定程度上减少基体与高温高压水接触面积,阻碍基体与高温高压水反应,降低腐蚀溶解,从而导致SiC/SiCf复合材料包壳管的质量在腐蚀240 h后发生了明显增加。
从图4(a)中可以看出,腐蚀720 h后,SiC/SiCf复合材料包壳管表面整体腐蚀程度加深,表面不平整度增加。从图4(b)所示放大后形貌可见,角状结构边界开始变得模糊,尖角也不再明锐,SiC/SiCf复合材料包壳管表面整体发生了明显的腐蚀溶解。
从图5(a)中可以看出,腐蚀1 008 h后,SiC/SiCf复合材料包壳管表面整体腐蚀程度进一步加深,在表面及晶界均形成了细小的腐蚀坑,表面不平整度增加。从图5(b)所示放大后形貌可见,试样表面整体发生了明显的腐蚀溶解,且在表面可观察到细小的白色絮状颗粒,在局部区域这些颗粒形成了疏松的膜状结构。
从图6(a)中可以看出,腐蚀1 440 h后,SiC/SiCf复合材料包壳管表面层发生了局部脱落。从图6(b)所示放大后形貌可见,表面层脱落后,内部涂层表面可观察到细小的白色絮状颗粒,且在内部的角状结构上存在微裂纹,这会导致腐蚀环境继续向材料内部侵入。通过EDS对图6中白色絮状颗粒进行分析,结果见表2。结果表明,白色絮状颗粒为氧化物,这说明内部涂层表面也形成了疏松的氧化物颗粒层,故涂层表面可能周期性地发生氧化物层产生-脱落-重新产生这一过程。这种周期性的分层和脱落导致腐蚀进程加快和腐蚀质量损失迅速增大。
从图7(a)中可以看到,腐蚀2 880 h后SiC/SiCf复合材料包壳管边缘缺陷处的涂层发生逐层腐蚀和脱落现象,使纤维层裸露出来。从图7(b)所示放大后形貌可见,表面层脱落后,内部涂层中存在细小的白色絮状氧化物颗粒以及微裂纹,内部涂层的角状结构被腐蚀成为细小的柱状结构,并继续发生逐层脱落。周期性的分层和脱落导致腐蚀质量损失迅速增大,而表面腐蚀产物在一定程度上减小了基体的腐蚀溶解面积,缓解了SiC/SiCf复合材料包壳管的腐蚀溶解,使腐蚀速率逐渐达到稳定。
从图8(a)中可以看出,腐蚀4 560 h后,SiC/SiCf复合材料包壳管涂层表面发生明显的逐层腐蚀和脱落现象。图8(b)是角状结构表面放大后的形貌图,可见内部角状结构表面的不平整度增大,角状晶的晶间腐蚀溶解更为明显。
图9为腐蚀不同时间后SiC/SiCf复合材料包壳管的截面微观形貌。可以看出,经不同时间腐蚀后SiC/SiCf复合材料包壳管涂层的厚度都较为均匀,但由于涂层是在纤维层上直接沉积制备的,所以涂层沿纤维的形状呈现凹凸起伏的趋势,这使得涂层表面平整度降低,从而增大了涂层表面与高温高压水的接触面积,促进了腐蚀的进行。
3. 结论
(1)在高温高压水环境中,SiC/SiCf复合材料的腐蚀主要分为四个阶段:质量增加阶段、质量加速损失阶段、质量稳定损失阶段及质量损失趋缓阶段。
(2)在质量增加阶段,SiC/SiCf复合材料包壳管中角状晶表面发生了一定的腐蚀溶解,而富硅的氧化物薄膜覆盖在胞状晶表面,会在一定程度上减小SiC/SiCf复合材料基体与高温高压水的接触面积,阻碍基体与高温高压水的腐蚀反应,降低了腐蚀溶解,从而导致SiC/SiCf复合材料包壳管质量在该阶段发生了明显的增加。
(3)在质量加速损失阶段,涂层表面和晶界不断腐蚀,形成较多的腐蚀坑,使更多基体裸露出来,发生腐蚀溶解。同时,试样表面的氧化物层或角状结构发生了局部脱落。腐蚀溶解和局部脱落的共同作用导致了该阶段内质量损失迅速增加,质量损失速率不断提高。
(4)在质量稳定阶段,在腐蚀溶解和氧化物颗粒层形成的共同作用下,质量损失速率随着腐蚀时间的增加而趋于平缓,但仍保持较高的质量损失速率,SiC/SiCf复合材料包壳管持续发生腐蚀溶解行为,腐蚀溶解程度逐渐加深,导致质量损失持续增加。
(5)在质量损失趋缓阶段,密集的氧化物颗粒在一定程度上减少了基体的腐蚀溶解面积,缓解了SiC/SiCf复合材料包壳管的腐蚀溶解,导致腐蚀进程减缓和质量损失速率降低。
免责声明:本网站所转载的文字、图片与视频资料版权归原创作者所有,如果涉及侵权,请第一时间联系本网删除。
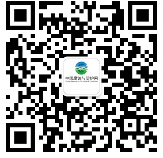
官方微信
《腐蚀与防护网电子期刊》征订启事
- 投稿联系:编辑部
- 电话:010-62316606
- 邮箱:fsfhzy666@163.com
- 腐蚀与防护网官方QQ群:140808414