镁合金是最轻的结构材料之一,其密度低(仅为1/4铁密度)、比强度高,在航空航天、计算机、交通工具、通讯等领域具有广阔的应用前景[1]。然而,镁的标准电极电位极低(仅为-2.37 V),在海水中的腐蚀电位为-1.6~-1.5 V[2],容易产生侵蚀。暴露在空气中的镁会自发产生氧化膜[3],但氧化膜疏松多孔,并不能阻碍腐蚀的进一步发展,所以保护性很差。由于镁的耐蚀性极差,在实际应用中并不能体现其各方面的优异性能[4]。热处理不仅可以消除合金内部的残余应力,还可以改变合金的微观结构。WANG等[5]研究发现,T4热处理可以消除Mg-Zn-Y-Zr合金在热锻过程中形成的不均匀MgZn2析出相,从而提高合金的耐蚀性。LIU等[6]研究发现,在T4和T6热处理过程中形成的长周期堆垛有序相(LPSO)是提高镁合金耐蚀性的主要因素。相较于传统镁合金,以锡为溶质原子的新型镁合金有着更为优异的热变形性能和更高的强度[7-9]。锂的添加能够改善镁合金的延展性[10-13],因此锂镁合金在航天航空和国防等领域有着巨大的发展潜力。作者将锂元素添加到镁合金基体中,并对其进行不同工艺的热处理,研究了铸态、时效态和固溶态Mg-3Sn-2Al-1Zn-5Li合金在3.5% NaCl溶液中的耐蚀性能,为新型高性能镁合金的开发和应用提供支持。
1. 试验
1.1 合金制备及热处理
试验材料为工业纯镁(纯度99.95%)、工业纯铝(纯度99.95%)、工业纯锌(纯度99.95%)、工业纯锡(纯度99.95%)和纯锂(纯度99.95%)。Mg-3Sn-2Al-1Zn-5Li合金(以下称合金)的化学成分(质量分数)为:3.17% Sn、2.07% Al、1.08% Zn、5.23% Li、余量为Mg。按照设定的合金成分,将原材料进行切割、称量、打磨去除表面氧化皮。合金在真空感应炉中进行熔炼,保护气体为0.3% SF6+99.7% CO2,具体过程如下:将熔炼炉加热至150 ℃使其干燥,再迅速将所有原材料放入熔炼炉中的坩埚;对感应熔炼炉进行抽真空使气压不超过1×10-2 Pa,再充入保护气体至0.03 MPa,加热熔炼炉进行熔炼;待所有原材料熔化后,在720 ℃保温静置30 min,加大保护气体的通入量,使炉膛内压力升高;将熔体压入经300 ℃预热的ϕ90 mm×180 mm圆柱形钢模中得到合金铸锭。将铸锭去头尾,车削至表面光滑,再用电火花线切割机将铸锭切割成ϕ11 mm×150 mm的圆棒,随后将圆棒封装在真空石英玻璃管中先进行固溶处理(400 ℃×48 h,水淬),再进行时效处理(260 ℃×12 h,炉冷)。
1.2 试验方法
利用车床将不同热处理状态的合金加工成ϕ10 mm×5 mm电极试样。用由粗到细(1200号砂纸)的砂纸逐级打磨试样表面,并在合金试样表面打一个直径为1 mm的小孔,用于插入铜导线;然后,用环氧树脂进行冷镶,试样暴露尺寸为ϕ10 mm。测试在电化学工作站并采用三电极体系进行。工作电极为不同热处理状态的合金,参比电极为氯化银电极,辅助电极为铂片电极。3.5%(质量分数,下同)NaCl溶液为电解液。极化曲线测试时,扫描电位为±500 m V(相对于开路电位),扫描速率为1 m V/s;电化学阻抗谱(EIS)测试时,交流激励信号幅值为20 m V,测试频率为10 m Hz~100 k Hz。
将固溶态合金加工成ϕ10 mm×2 mm的试样,每个工作表面经砂纸打磨,无水乙醇洗涤以及温热空气干燥。在3.5% NaCl溶液中对试样进行全浸试验,并用失重法计算其腐蚀速率。浸泡试验温度为室温,时间为12、24、48、72、96 h。试验后,使用光学显微镜观察试样的腐蚀形貌。
采用XRD-6000型X衍射分析仪(XRD)对合金的腐蚀产物进行分析。采用Merlin Compact型扫描电镜(SEM)对合金腐蚀前后的形貌进行观察,利用能谱仪(EDS)对腐蚀产物和第二相进行元素分析。
2. 结果与讨论
2.1 极化曲线
从图1中可以看出:不同热处理状态合金的极化曲线都遵从Tafel规律,其中阴极分支对应析氢过程,阳极分支对应基体的溶解[11];固溶态合金的自腐蚀电位最正,时效态其次,铸态最负,这说明热处理改善了合金的耐蚀性能,其中固溶处理的效果最为显著;此外,3种热处理状态合金的阴极区塔菲尔斜率差别不大,表明不同热处理状态合金在3.5% NaCl溶液中的腐蚀机理相似。
2.2 电化学阻抗谱
在3.5% NaCl溶液中,镁合金的电化学阻抗谱通常分为3个部分:高频区对应的是表面钝化膜的阻抗和双层电荷转移电阻[12];中频区存在一个非常小的阻抗且重现性非常差[13];低频区对应的是点蚀起始过程中的腐蚀形核。从图2中可以看出,在3.5% NaCl溶液中固溶态合金的容抗弧最大,说明固溶态合金最耐蚀。
根据极化曲线与电化学阻抗谱分析可知,热处理对改善合金的耐腐蚀性能起到了积极作用。
2.3 腐蚀速率
对固溶态合金进行了浸泡试验,其腐蚀速率如图3所示。从图3中可以看到:浸泡初期,合金的腐蚀速率较高,但是随着浸泡时间的延长,合金表面被腐蚀产物覆盖,腐蚀速率明显下降;当浸泡时间为72 h时,腐蚀速率最低,为0.41 mg/(cm2·h)。
2.4 腐蚀形貌
图4为在3.5% NaCl溶液中浸泡不同时间后固溶态合金表面的腐蚀形貌。由图4可见:浸泡后合金表面几乎失去金属光泽,多处发生腐蚀并产生蚀坑,出现丝状腐蚀特征,随着浸泡时间的延长,腐蚀产物增多且呈小片状和颗粒状,厚度不均匀,而裸露在外的多处基体呈现出层状剥落的痕迹,并且在层状剥落处有明显的裂纹产生。在浸泡过程中,整个试样表面都有氢气泡产生,试样表面出现蚀坑,蚀坑随浸泡时间的延长而变大,连接组合形成一片,由于试样表面有腐蚀产物阻挡,氢气气泡的生成速率有所降低[14]。
图5为在3.5% NaCl溶液中浸泡72 h后固溶态合金表面腐蚀产物的能谱分析结果。由图5可见,腐蚀产物中含有大量的镁元素和氧元素。图6为浸泡不同时间后固溶态合金表面腐蚀产物的XRD谱。由图6可见,腐蚀产物的主要成分均为Mg(OH)2,这说明合金中的镁是发生腐蚀的主要成分。此外,腐蚀前期(浸泡时间不超过48 h),腐蚀产物中有少量的Al2O3,随着浸泡时间的延长,Al2O3最终完全溶解。在XRD谱中并未出现含锂的化合物,说明锂元素在合金中以较为稳定的形式存在,具有一定的耐蚀性。LI等[12]研究发现,锂易在镁合金表面形成氧化膜,从而降低镁合金的腐蚀速率。在腐蚀产物的XRD谱中没有出现锌,这是由于锌以Mg-Zn固溶体的形式存在于镁合金中,不易发生腐蚀。镁合金在溶液中的腐蚀是镁与水发生电化学反应生成氢氧化镁和氢气的过程[15]。
3. 结论
(1)经固溶处理和时效处理后,Mg-3Sn-2Al-1Zn-5Li合金的耐蚀性能有所提高,并且固溶态的Mg-3Sn-2Al-1Zn-5Li合金有着最佳的耐蚀性能。
(2)固溶态Mg-3Sn-2Al-1Zn-5Li合金在腐蚀过程中出现丝状腐蚀特征,镁是发生腐蚀的主要成分,同时有少量的铝发生溶解。镁合金在溶液中的腐蚀是镁与水发生电化学反应生成氢氧化镁和氢气的过程。
免责声明:本网站所转载的文字、图片与视频资料版权归原创作者所有,如果涉及侵权,请第一时间联系本网删除。
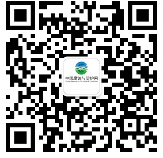
官方微信
《腐蚀与防护网电子期刊》征订启事
- 投稿联系:编辑部
- 电话:010-62316606
- 邮箱:fsfhzy666@163.com
- 腐蚀与防护网官方QQ群:140808414