失效样 | 防腐蚀层 | 管体 | 管端 |
---|---|---|---|
1号 | 防腐蚀层部分磨损脱落 | 管体外无明显划伤 | 弯管管端磨损严重,弯管内外弧处壁厚较薄 |
2号 | 防腐蚀层部分磨损脱落 | 弯管外弧侧有一长52 mm、宽8.2 mm凹槽,由内及外形成刺漏 | 管端连接处无明显损伤 |
3号 | 防腐蚀层严重脱落 | 短节内外表面腐蚀严重 | 短节螺纹腐蚀严重,螺纹不完整 |
4号 | 防腐蚀层严重脱落 | 管体腐蚀严重 | 断口处较齐平,一侧发生塑性变形,另一侧未发生明显的塑性变形,为裂纹的形成区 |
5号 | 防腐蚀层严重脱落 | 管体腐蚀严重 | 弯管与短节连接处有一尺寸为38 mm×7.9 mm的裂缝,螺纹腐蚀严重,裂纹的形成由内及外 |
放喷管线是井控装置的重要组成部分[1],是应急状态下节流管汇和压井管汇下游用来释放井内流体压力的管线。放喷管线中的高压、高速流体携带地层岩屑颗粒对管线冲蚀、导致管线刺漏失效,严重时发生井喷失控、爆炸、着火等事故[2-5]。受井场面积、设备布局、工艺要求等限制,井控管汇需要通过不同角度的弯管连接,而弯头处流体对管壁的撞击及流向的改变会造成流场分布(流速、压力等)不均,产生紊流和涡流等现象,因此冲刷磨损(磨损腐蚀)是放喷管线的一种常见失效形式。某井在井漏处理过程中出现溢流高套压,当放喷点火超过24 h时,放喷管线发生了严重的刺漏、断裂现象。为保障钻井作业的安全运行,减少经济损失,并防止此类事故再次发生,对放喷管线的失效原因进行了分析。
1. 理化检验与结果
1.1 宏观形貌分析
从现场共收集5件放喷管线失效样,详见表1。其中,1号样为一端带短节(短直管)的弯管,短节与弯管通过螺纹连接,弯管管端磨损严重,弯管内外弧处壁厚较薄。2号样为带法兰弯管,弯曲部分呈椭圆形,不圆度为87.1%,弯管外弧侧有一长52 mm、宽8.2 mm的沟槽,且沟槽由内及外逐渐扩大形成刺漏,其形成趋势具有方向性。3号样为带法兰短节,锈蚀严重,短节螺纹不完整。4号样为带法兰直管,锈蚀严重,初步判定其断裂形式为疲劳撕裂。5号样为两端带短节的弯管,弯管与短节连接部分有呈凹槽形态的裂缝,裂缝呈现由内及外的扩展趋势,具有方向性。
1.2 壁厚分析
为了分析管线不同部位的冲刷腐蚀情况,采用TMG-II型透涂层测厚仪测量样品的壁厚。检测位置如图1所示,A、B、C为测点所在截面,在每一个截面按顺时针方向1~12点方位分布12个测试点。管线失效件各区域壁厚测试结果如表2所示。相较企业标准Q/SYCQZ 231-2015《井控装置放喷管线技术要求和试验方法》规定的标准壁厚,失效件壁厚存在明显的减薄情况,且减薄不均匀。
样品 | 截面 | 壁厚/mm | |||||||||||
---|---|---|---|---|---|---|---|---|---|---|---|---|---|
1 | 2 | 3 | 4 | 5 | 6 | 7 | 8 | 9 | 10 | 11 | 12 | ||
1号 | A | 4.95 | 4.30 | 5.40 | 5.30 | 5.90 | 5.85 | 5.70 | 6.05 | 5.90 | 5.10 | 5.10 | 4.95 |
2号 | A | 14.7 | 14.7 | 14.8 | 14.8 | 14.9 | 15.0 | 14.9 | 15.0 | 15.0 | 14.9 | 14.9 | 14.7 |
B | — | — | 14.10 | 15.2 | 16.0 | 16.6 | 15.8 | 15.47 | 14.9 | — | — | — | |
C | 14.6 | 14.6 | 14.6 | 14.60 | 14.6 | 14.7 | 14.8 | 14.8 | 14.8 | 14.8 | 14.8 | 14.6 | |
3号 | A | 5.05 | 5.25 | 4.85 | 4.80 | 4.80 | 4.90 | 4.85 | 4.85 | 4.80 | 5.00 | 5.35 | 4.70 |
4号 | A | 6.20 | 6.15 | 6.35 | 5.70 | 5.60 | 5.60 | 6.40 | 6.65 | 6.40 | 6.50 | 6.20 | 6.20 |
B | 6.25 | 6.50 | 6.25 | 6.40 | 6.05 | 6.35 | 6.45 | 6.80 | 6.65 | 6.40 | 6.35 | 6.35 | |
C | 6.15 | 6.10 | 6..30 | 6.25 | 6.50 | 6.80 | 6.80 | 6.90 | 6.80 | 5.75 | 6.10 | 6.20 | |
5号 | A | 5.05 | 5.25 | 4.85 | 4.80 | 4.80 | 4.90 | 4.85 | 4.85 | 4.80 | 5.00 | 5.35 | 4.70 |
B | 6.45 | 6.55 | 6.65 | 6.00 | 6.45 | 6.55 | 6.75 | 6.70 | 6.35 | 6.55 | 6.60 | 6.80 |
1.3 化学成分分析
采用Test Master Pro型直读光谱仪对失效管线进行化学成分分析,结果如表3所示。结果表明:1号、3号、4号及5号失效样的碳含量均明显小于Q/SYCQZ 231-2015标准对于承压件的要求,这会导致管道表面硬度降低。
失效样 | 检测位置 | 质量分数/% | ||||||||
---|---|---|---|---|---|---|---|---|---|---|
C | Si | Mn | P | S | Cr | Mn | Ni | Cu | ||
1号 | 弯管 | 0.35 | 0.25 | 0.56 | 0.010 | 0.017 | 0.90 | 0.19 | — | — |
短节 | 0.21 | 0.27 | 0.49 | 0.011 | 0.012 | 0.02 | <0.01 | 0.03 | 0.01 | |
2号 | 法兰 | 0.27 | 0.25 | 0.63 | <0.005 | <0.005 | 0.89 | 0.20 | — | — |
弯管 | 0.29 | 0.24 | 0.62 | 0.011 | 0.008 | 0.87 | 0.20 | — | — | |
3号 | 法兰 | 0.39 | 0.23 | 0.64 | 0.013 | 0.020 | 0.89 | 0.19 | — | — |
短节 | 0.20 | 0.27 | 0.51 | 0.016 | 0.010 | 0.01 | <0.01 | 0.02 | 0.01 | |
4号 | 法兰 | 0.33 | 0.23 | 0.60 | 0.007 | 0.008 | 0.95 | 0.19 | — | — |
直管 | 0.23 | 0.09 | 0.64 | 0.014 | 0.009 | 3.05 | 0.41 | — | — | |
5号 | 弯管 | 0.21 | 0.23 | 0.59 | <0.005 | 0.006 | 0.95 | 0.17 | — | — |
左短节 | 0.14 | 0.19 | 0.65 | <0.005 | <0.003 | 0.03 | <0.01 | 0.01 | 0.01 | |
右短节 | 0.48 | 0.23 | 0.74 | 0.033 | 0.010 | 0.03 | <0.01 | 0.03 | 0.01 | |
标准值 | 0.26~0.45 | 0.17~0.37 | 0.40~0.80 | ≤0.025 | ≤0.025 | 0.80~1.20 | 0.15~0.25 | — | — |
1.4 硬度分析
采用EQUO TIP3型里氏硬度计对失效管线进行硬度检测,为便于同标准比较,将测得的里氏硬度转换为布氏硬度,结果如图2所示。根据Q/SYCQZ 231-2015标准,管体硬度应不低于140 HBW,法兰硬度应不低于174 HBW。结果表明:1号短节、3号短节、5号管体及左右法兰的硬度均不满足承压件材料硬度的最低要求。
1.5 力学性能分析
为分析管线失效后强度及韧性的变化情况,分别利用INSTORON UTM-HYD型电液式万能材料试验机及ZBC2302-C型金属摆锤冲击试验机进行拉伸试验和冲击试验,结果如表4所示。拉伸试验结果表明,1号、3号失效样的抗拉强度均不满足Q/SYCQZ 231-2015标准最低要求,2号、4号、5号失效样的断后伸长率亦不满足标准最低要求,可见失效件拉伸性能均不满足标准最低要求,抵抗断裂破坏的能力较小。冲击试验结果表明,1号、2号、5号失效样的冲击韧性不符合标准要求,说明管线变脆倾向变大,易发生脆性断裂。
失效样 | 检测位置 | 屈服强度/MPa | 抗拉强度/MPa | 断后伸长率/% | 冲击吸收能/J |
---|---|---|---|---|---|
1号 | 直管 | 328 | 470 | 21.5 | 63.8 |
弯管 | 388 | 679 | 23.0 | 12.8 | |
2号 | 弯管 | 624 | 953 | 18.5 | 17.0 |
3号 | 直管 | 310 | 471 | 25.5 | 82.7 |
4号 | 直管 | 590 | 757 | 17.5 | 158.0 |
5号 | 直管 | 429 | 699 | 16.0 | 10.3 |
加厚弯管 | 550 | 725 | 23.0 | 30.0 | |
标准值 | ≥310 | ≥483 | ≥19 | ≥27 |
1.6 金相检查
对管线失效部位进行取制样,并采用Zeiss Axio Vert A1型金相显微镜进行金相检查,结果如图3和表5所示。由图3可知,失效管线材料中存在非金属夹杂物,金属基体的连续性被破坏,管线钢的品质变差[6-7]。由表5可知,失效样均含有D类夹杂物,夹杂物均为0.5级,尺寸较小不足以导致开裂。1号样弯管与短节连接处磨损导致连接松动,而弯管直管段晶粒度为7.5级,显微组织为珠光体+铁素体,强度与硬度适中,并不脆[8]。2号样弯管外弧处发生刺漏,而外弧处晶粒度为9.5级,显微组织为贝氏体+铁素体,强度与硬度较高,韧性较小,且低温贝氏体组织中含有较多的残余奥氏体,如果服役过程中发生应变,会诱发马氏体相变,使表面呈现出脆性,影响使用寿命[6,9]。5号样弯管与短节连接处螺纹严重腐蚀导致泄漏,而螺纹腐蚀端直管晶粒度为6.0级,显微组织为珠光体+网状铁素体,强度、硬度较低,且网状铁素体严重割裂了珠光体之间的联系,使钢的强度低于正常值,塑性较低,极易变形断裂[6,10]。
失效样 | 检测位置 | 非金属夹杂 | 晶粒度 | 显微组织 | |||||
---|---|---|---|---|---|---|---|---|---|
— | A类 | B类 | C类 | D类 | DS类 | ||||
1号 | 弯管直管段 | 粗系 | 0.5级 | 0.0级 | 0.0级 | 0.5级 | 0.0级 | 7.5级 | 珠光体+铁素体 |
细系 | 0.5级 | 0.5级 | 0.5级 | 0.5级 | — | ||||
2号 | 焊缝处 | 粗系 | 0.0级 | 0.0级 | 0.0级 | 0.5级 | 0.5级 | 10.0级 | 贝氏体+铁素体 |
细系 | 0.5级 | 0.0级 | 0.5级 | 0.5级 | — | ||||
外弧处 | 粗系 | 0.0级 | 0.0级 | 0.0级 | 0.5级 | 0.5级 | 9.5级 | 贝氏体+铁素体 | |
细系 | 0.5级 | 0.5级 | 0.0级 | 0.5级 | — | ||||
3号 | 焊缝处 | 粗系 | 0.0级 | 0.0级 | 0.0级 | 0.5级 | 0.0级 | 8.5级 | 珠光体+铁素体 |
细系 | 0.5级 | 0.5级 | 0.0级 | 0.5级 | — | ||||
5号 | 左直管 | 粗系 | 0.0级 | 0.0级 | 0.0级 | 0.5级 | 0.0级 | 9.0级 | 珠光体+铁素体 |
细系 | 0.5级 | 0.5级 | 0.5级 | 0.5级 | — | ||||
右直管 | 粗系 | 0.0级 | 0.0级 | 0.0级 | 0.5级 | 0.0级 | 6.0级 | 珠光体+网状铁素体 | |
细系 | 0.5级 | 0.0级 | 0.0级 | 0.5级 | — |
1.7 腐蚀断口形貌分析
采用ZEISS EV0 MA15型扫描电子显微镜(SEM)对失效管线断口腐蚀形貌进行观察,结果如图4所示。由图4可见,2号样断口呈条状花样,这是流体冲蚀的痕迹,可判定腐蚀流体与金属表面间发生相对运动,管线内壁产生微小凹槽或沟,在流体不断冲蚀下微小凹槽或沟逐渐扩大并形成刺漏,因此该失效样发生了磨损腐蚀[11]。3号样断口表面被腐蚀产物堆积,故表面粗糙不平,腐蚀严重,除锈后仍然可见腐蚀产物堆积;4号样断口边缘存在裂纹,除锈后表面腐蚀严重,粗糙不平;5号样断口表面存在流体冲蚀的痕迹,介质长时间腐蚀连接处螺纹,结合宏观形貌可知,该失效样同样发生了磨损腐蚀。
1.8 腐蚀产物分析
从失效样表面腐蚀产物取样,采用能谱仪(EDS)对其元素成分进行分析,结果如表6所示。结果表明,失效样表面腐蚀产物中含有大量的氧元素,说明其表面发生的腐蚀反应为氧化反应,腐蚀产物应为铁的氧化物。
失效样 | 质量分数/% | ||||||||
---|---|---|---|---|---|---|---|---|---|
C | O | Al | Si | S | K | Ca | Fe | Ba | |
2号 | 9.75 | 34.28 | 2.34 | 5.66 | 1.15 | 1.38 | — | 38.65 | 5.71 |
3号 | 15.99 | 29.48 | — | 1.55 | 2.78 | 0.65 | 1.47 | 32.63 | 12.47 |
4号 | 16.57 | 32.81 | — | 1.74 | 0.63 | — | — | 47.59 | — |
2. 失效原因分析
按照相关标准对放喷管线进行了各项性能检测,结果表明失效管线理化性能不满足企业标准最低要求,管线变脆倾向较大,易发生脆性断裂;但放喷管线晶粒均较细,含有0.5级D类夹杂物,尺寸较小不足以导致开裂。此外,腐蚀形貌及腐蚀产物分析结果表明:2号样内壁存在凹槽或沟,具有方向性,微观形貌呈条状花样,为典型的磨损腐蚀形貌;5号样有凹槽形态且呈现由内及外扩展趋势的裂缝,为磨损腐蚀形貌;3号和4号样均腐蚀严重,腐蚀产物主要为铁的氧化物。基于以上测试与分析,推测管线发生腐蚀失效的主要原因为:恶劣的工况下高速流动的腐蚀介质与金属表面相对运动产生磨损腐蚀,引起金属加速破坏。
综合分析:由于长时间放喷,流体不断冲蚀丝扣连接部分,1号样和3号样连接处壁厚减薄,加之连接处两端金属的化学成分、硬度、拉伸性能及冲击韧性均不符合标准要求,抵抗塑性变形能力差,易发生脆性断裂,造成螺纹连接不稳,继而脱扣,导致泄漏;2号样、5号样管体均受到高速流动流体颗粒的冲击,管线变脆倾向增大,造成磨损腐蚀或湍流腐蚀,最终发生刺漏,这是流体力学和电化学共同作用对金属产生破坏的结果;直管刺漏、弯头断裂后,直管来回摆动,造成4号样(直管)断裂。同时4号样直管受到流体冲蚀导致壁厚减薄,其化学成分及拉伸性能均不合格,抗塑性变形能力差进一步促进脆性断裂的发生。
3. 结论与建议
综上,高速流动的腐蚀介质与金属表面相对运动产生磨损腐蚀,引起金属加速破坏,为此次泄漏的主要原因。为防止此类失效事故再次发生,提出以下建议[12-16]。
(1)改进设计:加大弯头曲率半径,适当增大管径,减小冲刷力,保证流体处于层流状态;采用以非金属为内衬的双层结构管道;对直管采用防紊流结构,对弯管易发生冲蚀部位进行加厚,或进行整体加厚。
(2)正确选材:防止出现采用碳钢替代合金钢的情况。
(3)加强科学管理:管道铺设、更换时必须严格按照操作规程,尽量避免产生各种应力,安装腐蚀监测设施,定期测厚及无损探伤。
免责声明:本网站所转载的文字、图片与视频资料版权归原创作者所有,如果涉及侵权,请第一时间联系本网删除。
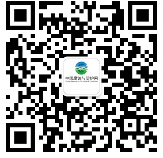
官方微信
《腐蚀与防护网电子期刊》征订启事
- 投稿联系:编辑部
- 电话:010-62316606
- 邮箱:fsfhzy666@163.com
- 腐蚀与防护网官方QQ群:140808414