随着传统汽车轻量化的发展和新能源汽车对结构减重的需求,以铝代钢已经成为汽车行业的发展趋势[1-3]。可时效处理强化的6×××系铝合金具有优良的成形性、良好的表面质量和较高的强度,是理想的汽车覆盖件用铝合金材料[4-6]。固溶处理能够显著改善合金的微观结构,从而影响合金的强度,但如果冲压、烤漆后6×××合金仍不能达到较高的强度,则会影响其使用性能[7-8]。因此,如何调控6×××系铝合金制备加工过程中的固溶处理工艺,成为汽车覆盖件用6×××系铝合金开发的关键。国内外的科研工作者围绕6×××铝合金的固溶时效过程开展了大量的研究工作。Lu等[9]发现,Al-Mg-Si合金在快速加热时会形成细小的近等轴状晶粒,而缓慢加热则形成粗大的拉长晶粒,使合金的强度和伸长率下降,造成弯曲变形早期应变局部化,形成强剪切带。Wang等[10-11]研究了固溶时间对Al-Mg-Si-Cu合金的影响,发现随着固溶时间的增加,平均晶粒尺寸逐渐增大,其中Al(Fe,Mn)Si粒子多的板材组织更均匀,再结晶晶粒生长速率较慢。Garrett等[12]通过对Mg2Si和Si粒子的回溶行为分析及模拟计算发现,随着时间的推移,析出相粒子会全部回溶进基体,并逐渐扩散到整个基体结构中,因此在525 ℃固溶处理温度下,固溶时间延长到一定程度后,AA6082铝合金的力学性能变化极小。这些工作很好地推动了汽车用6×××系铝合金的发展,并扩展了其应用范围。但其中关于固溶处理对最终再结晶组织影响的研究较为宽泛,尤其是对固溶时间的选择方面,还没有进行秒级固溶工艺的研究,不能很好地与工业化生产的连续退火线固溶过程相匹配。
固溶过程中伴随着再结晶的发生和元素的回溶。传统固溶处理炉的升温速率低、保温时间长(数十至数千分钟),而采用工厂连续退火线进行固溶处理时,板材在很短的时间内就可以发生再结晶和元素的回溶(数秒至数百秒)。合理的固溶时间可以有效地调控板材的再结晶程度和元素固溶程度,进而影响后续室温停放、烤漆过程中弥散相的析出规律和冲压过程中板材的成形性能。此外,合理地减少固溶时间还可以提高工厂连续退火线的生产效率。针对6×××系铝合金连续退火线固溶处理的工艺特点,本工作以6451铝合金冷轧板材为研究对象,采用升温速率高的盐浴炉对板材进行升温,研究固溶时间对板材再结晶规律及Mg2Si粒子回溶规律的影响,并分析板材经过T4P处理后的力学性能。此外,建立基于经典扩散理论的初始T4P态板材屈服强度与固溶量变化之间的函数关系模型,为汽车覆盖件用6451铝合金固溶工艺的优化及产业化提供理论依据和技术支持。
1 实验材料与方法
实验材料为6451铝合金,其化学成分如表1所示。合金铸锭经过均匀化处理、热轧、中间退火处理和冷轧加工后,制备成厚度为1.5 mm的冷轧态薄板。将板材在560 ℃下固溶不同时间(3,5,7,10,15,20,30,60,120,300 s和900 s),并将采温仪连接热电偶测试其在盐浴炉中的升温速率。6451铝合金板材升温曲线如图1所示。固溶处理后水淬,而后进行75 ℃保温7 h空冷预时效处理(T4P处理)。对不同固溶处理时间的试样进行组织观察和织构分析,并进行电导率和拉伸性能测试。最后对板材进行烤漆时效处理(预拉伸2%后进行185 ℃保温20 min的时效),以获得T6B态板材的力学性能。
金相(optical microscope, OM)显微组织观察在Leica DFC295光学显微镜下进行。根据GB/T 6394—2017计算合金板材平均晶粒尺寸,每种固溶制度选取3张100倍的金相照片进行统计。采用D2.069涡流电导仪对T4P处理后的试样进行电导率测定,以分析析出相的回溶行为。通过配备有X射线能量色散光谱 (EDS)系统JEOL JSM 7800F型扫描电子显微镜(SEM)观察合金中的第二相粒子,电压为20 kV,扫描步长为0.2 μm。SEM样品的磨制和抛光方法与金相样品一致。织构测试采用Empyrean锐影X射线衍射仪进行,管电压为40 kV,管电流为40 mA。使用Thermocalc相图计算软件对6451铝合金进行计算模拟,获得6451铝合金中第二相的种类及固溶温度T s。力学性能测试根据GB/T 16865—2023进行。拉伸实验在SHIMADZU AG-xplus100kN微机控制电子万能力学试验机上进行,拉伸速率为3 mm/min。每个测试点测量3个拉伸样,取其平均值,以保证实验数据的准确性。
2 结果与分析
2.1 冷轧态板材的微观组织
图2为6451铝合金板材冷轧态微观组织,表2为图2(b)中Al(Fe,Mn)Si相和Mg2Si 相的EDS分析。由图2(a)可见沿轧制方向拉长的均匀纤维状组织,这是典型的变形态组织。根据SEM形貌(图2(b))和EDS分析结果发现,板材中存在两种第二相粒子,黑色相为可回溶的Mg2Si粒子,灰白色相为难溶的Al(Fe,Mn)Si粒子。
2.2 固溶时间对板材晶粒组织的影响
图3为不同固溶时间处理的合金板材OM形貌。可知,固溶时间为3 s时,板材中形成大量等轴的再结晶晶粒,但仍然残留少量纤维状组织;时间延长至7 s,晶粒组织基本由等轴晶组成。板材的平均晶粒尺寸统计结果见图4。可以看出,随着固溶时间延长至10 s,板材的平均晶粒尺寸迅速增大,达到41 μm;固溶时间为30 s时,晶粒缓慢长大;固溶时间进一步延长,平均晶粒尺寸没有发生明显变化。根据平均晶粒尺寸随固溶时间变化的拟合曲线可以发现,固溶时间在10 s内,平均晶粒尺寸随固溶时间延长逐渐增大;固溶时间至30 s后,平均晶粒尺寸趋于稳定,晶粒基本不再长大。板材的平均晶粒尺寸主要与冷轧态合金内部储存的变形能和第二相分布有关,它会直接影响其力学性能。
2.3 固溶时间对板材织构的影响
图5为经不同固溶时间处理后板材的取向分布函数(orientation distribution functions,ODF)图,图中Φ,ϕ 1,ϕ 2为欧拉角,表征晶体取向。对其中的织构分布进行统计,结果见表3。可以看出,不同固溶时间的板材中均只存在Cube {001}〈100〉织构,表明固溶时间对织构类型没有影响。固溶时间为3 s时,已形成大量Cube织构,表明板材发生再结晶,且再结晶程度较高,此与晶粒组织观察结果相一致。随着固溶时间的延长,Cube织构的取向密度和体积分数略有增加;固溶时间延长至30 s后,Cube织构的体积分数稳定在18%左右,表明固溶时间对织构分布影响较小。
2.4 固溶时间对板材中第二相的影响
合金板材电导率随固溶时间的变化如图6所示。可知,冷轧态板材的电导率最高,为56.9%IACS。固溶时间延长至7 s,电导率迅速降低,这可能由于细小Mg2Si粒子的迅速回溶。随着固溶时间的进一步延长,电导率降低的趋势减缓,在60 s固溶时间后电导率趋于稳定。
为进一步明确固溶处理过程中第二相粒子的演变,对不同固溶时间的T4P态板材进行SEM形貌观察,如图7所示。可以看出,随固溶时间延长,板材中Al(Fe,Mn)Si粒子的分布无明显差异,Mg2Si粒子逐渐减少;当固溶时间延长至60 s时,Mg2Si粒子基本完全回溶。图8为合金板材中第二相粒子体积分数和数量密度随固溶时间的变化。由图8(a)可以看出,随固溶时间延长,Al(Fe,Mn)Si粒子的体积分数和数量密度变化很小,说明在560 ℃保温900 s以内,Al(Fe,Mn)Si相不发生回溶。由图8 (b)可知,与冷轧态板材相比,固溶时间延长至5 s时,Mg2Si粒子略有减少。随着固溶时间进一步延长,Mg2Si粒子的数量密度和体积分数均明显减小,固溶时间延长至15 s时,Mg2Si粒子的数量密度基本减小至最小值,表明Mg2Si粒子回溶速度减缓。固溶时间为60 s时,Mg2Si粒子基本完全回溶。板材的SEM形貌观察结果与电导率的变化规律一致。
结合图6~8可以发现,固溶处理时再结晶迅速发生,再结晶速率明显大于Mg2Si粒子回溶的速率,而Mg2Si粒子的回溶程度也会影响板材再结晶晶粒的尺寸和力学性能。因此,进一步对不同固溶时间下板材中Mg2Si粒子的尺寸和数量密度进行统计,如图9所示。固溶时间为3 s的板材和冷轧态板材中,Mg2Si粒子的尺寸和数量密度基本相同,表明Mg2Si粒子未发生回溶。固溶时间增加至7 s时,尺寸在0.8 μm以下的Mg2Si粒子显著减少,细小粒子对晶界的钉扎作用逐渐减弱,再结晶晶粒的生长阻力减小,晶粒更易长大,而尺寸在0.8~2.0 μm的Mg2Si粒子数量密度较冷轧板相差不大,2.0 μm以上Mg2Si粒子基本消失,表明固溶时间为7 s时,细小Mg2Si粒子迅速回溶至基体中,而大尺寸的Mg2Si粒子只能缓慢溶解,尺寸逐渐减小,并未完全消失,这也解释了固溶7~15 s时,Mg2Si粒子的数量密度显著减小,但其体积分数并未减至最小的原因。随着固溶时间进一步延长,Mg2Si粒子持续回溶,其数量密度和尺寸均进一步减小。固溶时间延长至60 s时,Mg2Si粒子完全回溶进基体中。随着Mg2Si粒子逐渐回溶,再结晶晶粒继续长大,但由于板材在前期均匀化和轧制过程中形成了大量细小的Al(Fe,Mn)Si粒子,会阻碍再结晶晶粒生长,因此在Mg2Si粒子完全回溶后,板材的晶粒结构依然相对细小,并最终趋于稳定。图10为6451铝合金的ThermalCal相图计算结果。可知,6451合金中Mg2Si的固溶温度为524 ℃。结合图1发现,合金在3 s时才达到固溶温度,因此Mg2Si粒子与冷轧态板材相比未发生变化。固溶时间在5 s时,Mg2Si粒子已经开始回溶,但达到固溶温度的时间过短,Mg2Si粒子固溶程度有限。固溶时间继续延长,Mg2Si粒子回溶速率显著增大。Al15Si 2M 4相和Al9Fe2Si2相在该合金中属于难溶相,基本没有变化,且Al15Si2 M 4相的量非常少;而Diamond-A4(Si)相和Q相在冷轧板材前期的中间退火过程中已完全回溶,因此本工作的温度范围中并不存在这两种相。
2.5 固溶时间对板材力学性能的影响
表4为T4P态合金板材的力学性能,其中R p0.2为屈服强度,R m为抗拉强度,A 50为伸长率。可知固溶时间为5 s时,板材的A 50最小。随固溶时间增加伸长率逐渐增大,在固溶时间延长至15 s后伸长率达到30%,趋于稳定。图11为不同固溶时间下T4P和T6B态合金板材的屈服强度对比,其中ΔR p0.2为烤漆后的屈服强度增量,即T4P和T6B态板材的强度差异。可以看出,固溶时间为3 s时,T4P态板材的屈服强度显著降低,从冷轧板的200 MPa减至65 MPa,根据图3的组织观察结果可知,这是由于再结晶在极短时间内的迅速发生。随着固溶时间延长至7 s,T4P态和T6B态板材的强度迅速增大。而固溶时间进一步延长后,T4P态和T6B态板材强度的增速明显减缓,烤漆后的屈服强度增量基本不变。结合表4的结果,固溶时间延长至60 s时,屈服强度和抗拉强度分别提升至125 MPa和247 MPa,且具有较好的伸长率(30%);固溶时间继续延长,板材的强度和伸长率均趋于稳定。
合金板材的力学性能与基体的晶粒分布、织构分布和第二相分布相关。经T4P处理后,6×××系铝合金的强化机制主要为析出强化、固溶强化和细晶强化[13-14]。根据Hall-Petch公式可知,随板材晶粒长大,其强度会降低,但6×××系铝合金的Hall-Petch斜率很低,通常为70 MPa·μm1/2 [15]。结合图4和图5可以发现,晶粒尺寸和织构分布对强度的影响有限。并且随着固溶时间延长至30 s,晶粒呈现持续长大的趋势,板材的强度也逐渐升高,表明晶粒尺寸不是影响板材强度的主要因素。因此,合金的强度增量主要源于析出强化和固溶强化,而晶粒尺寸的作用可以忽略,这与文献[14,16]的研究结果一致。由图6~8可知,固溶时间延长至7 s时,板材中大部分尺寸在0.8 μm以下的Mg2Si粒子已回溶,基于析出强化作用,板材的强度也不断提高。固溶时间进一步延长,Mg2Si粒子继续回溶,但由于大部分Mg2Si粒子已经回溶,大尺寸的Mg2Si粒子数量较少,回溶较慢,板材强度的增速减小。固溶时间增至60 s,晶粒尺寸变化较小,所有可回溶粒子均已完全回溶,强化效果较好,强度增大,固溶时间继续延长,板材的强度基本不变,表明第二相的回溶行为是固溶处理影响板材性能的主要作用机制。
由于本工作中合金仅在热轧及之后的冷却过程中析出部分Mg2Si粒子,远未达到平衡浓度,因此,在低于平衡浓度的固溶温度下,Mg2Si粒子已经开始回溶。根据图1中板材的升温曲线和表4的屈服强度测试结果分别计算不同固溶制度下的S,由此通过指数拟合建立屈服强度与S之间的对应关系,如图13所示,其拟合结果如式(6) 所示:
3 结论
(1)固溶时间为3 s时,板材中已发生再结晶;固溶时间延长至7 s,完全再结晶后形成等轴晶组织;固溶10 s内板材的平均晶粒尺寸随固溶时间延长迅速增大;固溶时间延长至30 s后,晶粒尺寸基本不发生变化。固溶处理3 s后,板材中形成Cube {001}〈100〉织构,固溶时间对织构分布的影响较小。
(2)固溶处理5 s时,板材中Mg2Si粒子少量回溶,变化很小;时间延长至7 s,尺寸在0.8 μm以下的Mg2Si粒子大量回溶,数量密度明显减小;时间延长至60 s时,Mg2Si粒子完全回溶。
(3)随固溶时间延长至7 s,T4P态和T6B态板材的强度迅速增大;固溶时间进一步延长,板材强度的增速明显减缓,烤漆后的屈服强度增量基本不变;固溶时间为60 s时,T4P态板材的屈服强度和抗拉强度分别提升至125 MPa和247 MPa,伸长率为30%。通过模拟固溶处理对板材屈服强度的影响,建立了基于经典扩散理论的T4P态板材屈服强度与固溶量之间的函数关系模型。
免责声明:本网站所转载的文字、图片与视频资料版权归原创作者所有,如果涉及侵权,请第一时间联系本网删除。
相关文章
无相关信息
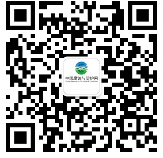
官方微信
《腐蚀与防护网电子期刊》征订启事
- 投稿联系:编辑部
- 电话:010-62316606
- 邮箱:fsfhzy666@163.com
- 腐蚀与防护网官方QQ群:140808414
点击排行
PPT新闻
“海洋金属”——钛合金在舰船的
点击数:10028
腐蚀与“海上丝绸之路”
点击数:7814