熔模精密铸造技术是一种近净成形技术,被广泛应用于制造高精度、复杂结构铸件,如航空发动机涡轮叶片、燃气轮机叶片、涡轮机匣等[1-3]。在精密铸造过程中,型壳的制备是至关重要的工序,型壳质量不仅决定着铸件的尺寸精度和表面粗糙度,还直接影响着铸件的制造成本和生产效率[4]。理想的型壳应具有以下性能[5]:①足够的湿强度,保证型壳脱蜡焙烧过程中保持完好;②足够的高温强度和抗热震性能,保证浇注过程中型壳的完好;③较低的残余强度,方便铸件的型壳清除;④化学稳定性高,与铸造金属反应活性低,以保证铸件的表面粗糙度;⑤足够的透气性和热导率,以保证型腔中的气体迅速排出,铸件的热量顺利通过型壳壁散失,加速金属液的凝固与冷却速度;⑥低的热膨胀系数,以避免型壳和最终铸件的尺寸超差。
型壳中干燥后的浆料、砂粒和空隙共同决定型壳的强度和透气性,熔模精密铸造型壳的强度往往与透气性相互制约。透气性是指气体通过型壳壁的能力,精密铸造用型壳透气性的优劣对金属液的充型能力有重要的影响,并直接影响到铸件质量[6]。传统的型壳具有室温强度低、干燥时间长和破损严重等问题,通常采用增加型壳的厚度以保证其强度[7-8]。然而,增加型壳的厚度会导致型壳透气性变差,一方面使得金属液充型困难,另一方面,型壳散热困难,使得铸件晶粒粗大。并且,型壳厚度增加会带来铸件容易产生气孔、铸件清理困难、型壳废气物排放增大等问题,对环境污染严重[9-10]。Jones等[5]通过向硅溶胶涂料中掺混尼龙纤维(直径为20 μm,长为1 mm),型壳的透气性得到了明显的改善(提高了3倍);室温测试下,型壳的湿强度和经1000 ℃焙烧60 min处理后的型壳强度略有降低,得到综合性能良好的陶瓷型壳。胡蓉[10]研究加入聚丙烯纤维对精铸型壳性能的影响,发现掺混纤维(直径为40 μm,长为5 mm)后型壳湿强度明显增强,当纤维掺混比为1.6%时,型壳室温强度最大为3.60 MPa,较普通型壳的室温强度提高约32%。
熔模铸造用黏结剂主要有水玻璃和硅溶胶。其中,硅溶胶是一种新型优质水基黏结剂,具有黏度低、分散性好和润湿性好的特点,广泛应用于熔模铸造,硅溶胶制备的铸件具有尺寸精度高、表面质量好等优点[3,11-12]。常用的耐火材料主要有锆英粉(砂)、电熔刚玉粉(砂)、莫来石、熔融石英、高铝矾土等。其中,电熔白刚玉具有熔点高(2050 ℃)、密度大(3.99~4.02 g/cm3)、导热性好、结构致密、热膨胀系数小(8.6×10-6 ℃-1)和价格低廉等优点,是优质的熔模铸造用型壳耐火材料[13-14]。莫来石(3Al2O3·2SiO2)晶须具有优良的耐高温性能(熔点2000 ℃以上,最高使用温度达到1500~1700 ℃)、热膨胀系数小(5.3×10-6 ℃-1,20~1000 ℃)、荷重软化温度高、高温抗蠕变性能好、耐腐蚀、抗热震性好、较高的高温力学强度(在1300 ℃时强度不会下降)和室温力学强度[15-16]。根据莫来石的化学式和Okada等[17]的研究,氟化铝(AlF3)和三水合氟化铝(AlF3·3H2O)可以诱导氧化铝和二氧化硅,生成莫来石晶须。近几十年来,一些学者利用不同的铝、硅源,以AlF3或AlF3·3H2O为诱导剂,制备得到了莫来石晶须[17-29]。然而,目前为止,有关原位诱导莫来石晶须改善陶瓷型壳性能的报道较少。
综上所述,基于硅溶胶和电熔刚玉粉在熔模精密铸造型壳制备中的广泛应用、莫来石晶须优良的理化和力学性能以及AlF3和AlF3·3H2O可以诱导氧化铝和二氧化硅生成莫来石晶须的理论和事实,本研究拟在硅溶胶和电熔刚玉体系背层浆料中添加AlF3·3H2O(简称AlF3·3H2O组)作为诱导剂,高温焙烧下诱导型壳中的氧化铝和二氧化硅原位反应生成莫来石晶须,最终获得透气性和强度综合性能良好的陶瓷型壳。
1 实验材料与方法
1.1 实验材料
面层和背层浆料所用原料主要有嘉兴凤翼特种材料科技有限公司提供的低钠硅溶胶(1030C,其中SiO2的质量分数为30%)、低钠电熔刚玉粉(325目)、低钠刚玉砂(面层砂90目、过渡层砂54目、背层砂24目)、乳胶、润湿剂、分散剂和消泡剂,高岭土(内蒙古天之娇高岭土有限责任公司,1600目),AlF3·3H2O粉(中国医药集团有限公司,240目)。型壳分为空白组和AlF3·3H2O组,其面层、过渡层和背层浆料的配方见表1和表2。
表1 面层(空白组和实验组)浆料配方Table 1 Composition of surface layer (blank group and experimental group) slurry |
Mass/g | ||||||
---|---|---|---|---|---|---|
Silica sol | Al2O3 | Latex | Kaolin | Wetting agent | Dispersing agent | Defoamer |
500 | 1600 | 5 | 32 | 2.1 | 2.1 | 2.1 |
表2 过渡层和背层浆料配方Table 2 Composition of transition layer and back layer slurry |
Group | Mass/g | |||||
---|---|---|---|---|---|---|
Silica sol |
Al2O3 | Kaolin |
AlF3· 3H2O |
Dispersing agent | Defoamer | |
Blank | 300 | 958 | 19.2 | 1.3 | 1.3 | |
Experimental | 321 | 958 | 19.2 | 69.2 | 1.3 | 1.3 |
1.2 实验方法
1.2.1 实验设计与样品制备
通常,型壳的制备是将蜡模或光敏树脂原型通过沾浆淋砂的方式逐层粘叠而成,型壳一般包含1层面层、1层过渡层、多层背层和1层封浆层,如图1(a)所示。以“硅溶胶+刚玉”体系为例,型壳面层(图1(b))、过渡层(图1(c))和背层(图2(a))由浆料和不同粒度的Al2O3砂粒构成,在分散和聚集的砂粒周围有不同大小的空隙;型壳的封浆层(图1(d))虽然没有经过淋砂,但浆料本身包含Al2O3和SiO2粉体,在陶瓷颗粒周围也有微小的空隙。通过沾浆淋砂工艺制备得到由1层面层、1层过渡层、5层背层和1层封浆层组成的陶瓷型壳。
本研究拟在硅溶胶和电熔刚玉体系背层浆料中添加AlF3·3H2O(简称AlF3·3H2O组)作为诱导剂(图2(b)),通过调整焙烧温度和保温时间等工艺参数,在型壳背层中原位生成莫来石晶须(图2(c)),最终获得透气性和强度综合性能良好的陶瓷型壳。
1.2.2 分析与表征
为确保AlF3·3H2O组型壳样品中诱导生成莫来石晶须,将样品放入马弗炉中,以5 ℃/min的速率升温至1200 ℃,保温5 h。采用X射线衍射仪(D8 DaVinci)分析样品的物相组成;采用配有能谱分析系统的扫描电子显微镜(RISE-MAGNA)分析样品的微观形貌;利用型壳高温透气度测定仪(DTQ-II)测试样品的透气性;利用阿基米德排水法测试样品的密度;利用激光导热仪(LFA 467)测试样品的热扩散系数;采用热膨胀仪(DIL 402 Expedis)测试样品的热膨胀系数;采用型壳高温变形试验仪(TBK)测试样品的高温自重变形;利用型壳高温抗弯强度试验仪(TKW)测试型壳的室温和高温强度。
2 结果与分析
2.1 型壳成分和微观组织分析
1200 ℃焙烧5 h空白组样品和实验组样品的XRD图谱如图3所示。从图中3可以看出:AlF3·3H2O组中有明显的莫来石相衍射峰,而空白对照组莫来石相衍射峰不明显,这说明相对空白组,AlF3·3H2O诱导氧化铝与二氧化硅反应生成莫来石相的效果明显,其反应机理如式(1 )~(4 )[17,22]:
1200 ℃焙烧5 h后空白组和添加AlF3·3H2O组型壳样品的显微结构如图4,5所示。由图4,5可以看出:空白组样品中无莫来石晶须生成;添加AlF3·3H2O组型壳样品背层中有莫来石晶须生成,晶须长度约10 μm,直径约1 μm,长径比约10∶1。需要说明的是,一方面,莫来石晶须主要集中在原始AlF3·3H2O颗粒处,这是因为只有当硅溶胶和刚玉粉同时聚集在AlF3·3H2O处,诱导生成莫来石晶须的反应才能发生。另一方面,影响莫来石晶须形貌尺寸的因素为焙烧温度和保温时间,焙烧温度决定莫来石晶须能否生成。另外,保温时间影响莫来石晶须生长的尺寸,如将保温时间减少为0.5 h,型壳样品中仅有少量莫来石晶须生成,晶须长度约1 μm,直径约0.1 μm(如图6(b)所示)。背层中生成的莫来石晶须尺寸明显小于背层砂尺寸。
2.2 型壳性能测试
2.2.1 透气性
型壳透气性测试依据HB 5352.4—2004标准,计算公式如式(5) 所示。空白组和AlF3·3H2O组样品的高温透气性如图7所示,从图7可以看出:在800~1000 ℃范围内,AlF3·3H2O组型壳的透气性明显高于空白组型壳的透气性,前者约是后者的2倍,1000 ℃时二者透气度分别为20.04 m4/(N·min)和10.47 m4/(N·min)。利用阿基米德排水法测试了型壳的密度,空白组型壳密度为3.41 g/cm3,AlF3·3H2O组型壳密度为3.36 g/cm3,相比之下,AlF3·3H2O组型壳密度有所降低。AlF3·3H2O组型壳透气性增加而密度降低的原因不难理解:晶须周围的空隙相对于颗粒周围的空隙更大(图2(c)),随着莫来石晶须的不断生成和长大,型壳中莫来石晶须之间以及莫来石晶须与型壳基体间的空隙逐渐增加;型壳的透气性随着空隙的增加而增加,型壳的密度则随着空隙的增加而减小。显然,AlF3·3H2O组型壳透气性增加而密度降低有益于型壳性能的改善。
2.2.2 热扩散和线膨胀系数
空白组和AlF3·3H2O组型壳的热扩散系数如图8所示。从图8可见:两组型壳的热扩散系数在3.0×10-6~0.5×10-6 m2/s,热扩散系数均随着温度的升高而降低;在25~500 ℃测试范围内,添加AlF3·3H2O型壳的热扩散系数高于空白组的热扩散系数。AlF3·3H2O组型壳热扩散系数较高的原因也与型壳中莫来石晶须有关:如前所述莫来石晶须的生成导致型壳中空隙的增加,空隙中填充着空气,相比陶瓷基体,空气的热扩散能力更强。
空白组和AlF3·3H2O组型壳的热膨胀系数如图9所示。从图中看出,25~1500 ℃温度范围内,两组型壳的热膨胀系数随着温度的升高的变化趋势基本一致,均随着温度的升高而增大;两组型壳的热膨胀系数都很小,不足14×10-3。25~1485 ℃时,AlF3·3H2O组型壳的热膨胀系数略高于空白组型壳,1485~1500 ℃时,AlF3·3H2O组型壳的热膨胀系数略低于空白组型壳。AlF3·3H2O组和空白组热膨胀系数的这种关系应该与型壳的孔隙率和型壳中各组分的熔点有关:总体上,型壳的热膨胀主要受基体控制,因此两组样品的热膨胀系数基本相同;25~1485 ℃时,具有较高孔隙率的AlF3·3H2O组型壳样品较易受热伸长;1485 ℃以上时,由于型壳在高温烧结过程中会产生玻璃相,而玻璃相的软化温度较低,随着温度升高,型壳基体中玻璃相发生软化充塞型壳中的空隙,导致AlF3·3H2O组型壳样品热膨胀系数有所降低。
3 结论
(1)以电熔刚玉粉体为原料、硅溶胶为黏结剂、氟化铝为莫来石相转化促进剂,设计了涡轮叶片定向凝固成型用陶瓷型壳背层浆料配方,通过调整焙烧工艺参数,在型壳中成功生成莫来石晶须,生成的晶须长度约10 μm,长径比10∶1;莫来石晶须的生成和长大与焙烧温度和保温时间密切相关。
(2)随着莫来石晶须的生成和长大,型壳中孔隙率逐渐增大,型壳的透气性增加了约1倍,如1000 ℃时AlF3·3H2O组和空白组的透气性分别为20.04,10.47 m4/(N·min);同时型壳的密度有所降低。
(3)相比空白组型壳,AlF3·3H2O组型壳的热扩散系数得到提高,高温热膨胀系数有所降低;型壳的室温和高温抗弯强度略有降低,但仍具有足够的强度保持型壳不被破坏,并有利于改善型壳的高温退让性;型壳的刚性得到提高,1500 ℃时变形量分别为0.19,0.20 mm。
(4)通过AlF3·3H2O诱导硅溶胶和刚玉粉原位生成莫来石晶须,获得了透气性、热变形性和强度综合性能优良的陶瓷型壳。
免责声明:本网站所转载的文字、图片与视频资料版权归原创作者所有,如果涉及侵权,请第一时间联系本网删除。
相关文章
无相关信息
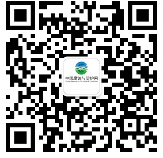
官方微信
《腐蚀与防护网电子期刊》征订启事
- 投稿联系:编辑部
- 电话:010-62316606
- 邮箱:fsfhzy666@163.com
- 腐蚀与防护网官方QQ群:140808414
点击排行
PPT新闻
“海洋金属”——钛合金在舰船的
点击数:10028
腐蚀与“海上丝绸之路”
点击数:7814