湿气管道是一类将气井井口直接采出、未经脱水脱烃处理的天然气输送到处理站的管道,因其运行费用低、适应性强,常用于山地、海洋等恶劣环境下的天然气开采和输送。然而,湿气管道内苛刻的介质环境导致其面临严重的内腐蚀问题,据报道,某海底湿气管道的腐蚀速率高达0.73~1.5 mm/a[1, 2]。常规天然气采输中的夹带水、凝析液以及页岩气开采中的返排液都是管道中水的重要来源,当伴生的CO2等酸性气体溶于水,其腐蚀性比同等pH条件下的盐酸更强。在山地、海底等存在地形起伏的区域,液态水极易在低洼管段聚积[3],形成积液区,导致该管段的腐蚀较其它部分更为严重[4, 5]。
积液区管道腐蚀的复杂性表现在气液两相流动并不局限于典型的段塞流动,还包括分层波浪流等,积液在气流扰动下,还可发生液膜向抬升段下游的流动和回流[11],发生局部管段被不同状态的液膜周期性润湿的情况。段塞流条件下的腐蚀研究表明,气液交替流动或润湿条件会对管壁腐蚀失效起到促进作用[19]。此外,则少有研究提及壁面液膜的动态分布所带来的影响,且在气液交替流动条件上缺少一定的量化分析。杨雨[20]在气液两相流的CO2腐蚀中涉及到管壁润湿状态对CO2腐蚀机制的影响,该研究区分了完全浸泡和间歇浸泡条件下的CO2腐蚀机制。但腐蚀条件的营造手段并不能完全真实地反应管内的真实流动和腐蚀状况,也尚未说明动态液膜分布是否能够影响管壁的腐蚀行为及机制。当前,积液区复杂气液两相流动状态下的CO2局部腐蚀机制尚不明确,急切需要针对性研究的开展。
鉴于湿气管道积液区气液两相流动的复杂性,液膜在管壁上分布时间和空间的不确定性,本研究自行设计并搭建了一套可以模拟开展管道积液区CO2局部腐蚀腐蚀测试的试验装置。本研究以管道倾斜角、气体流速、腐蚀时间为主要研究变量,借助丝束电极测试、电化学阻抗谱测试等手段并结合气液两相流态观察、理论分析等,研究了X70管线钢在模拟积液区气液流动条件下的CO2局部腐蚀电化学机制及影响因素。
1 实验方法
实验介质采用为1% (质量分数) NaCl水溶液,溶液由去离子水 (电阻率为0.78 MΩ·cm) 和分析级NaCl试剂配置而成。实验前,采用99.99% CO2气体对溶液除氧 (CO2分压为0.1 MPa),除氧时间不低于4 h,然后密封待用。除氧后测得溶液pH为3.98。
设计并搭建了一套可模拟开展管道积液区CO2局部腐蚀测试装置,如图1所示。该装置是由蠕动泵、CO2储存箱、倾斜管路、循环风机、气体流量计、电加热台、丝束电极测试部分等主要部件构成,可以对管内气体流速、持液率、管路倾斜角度及管内温度等变量进行控制。
图1
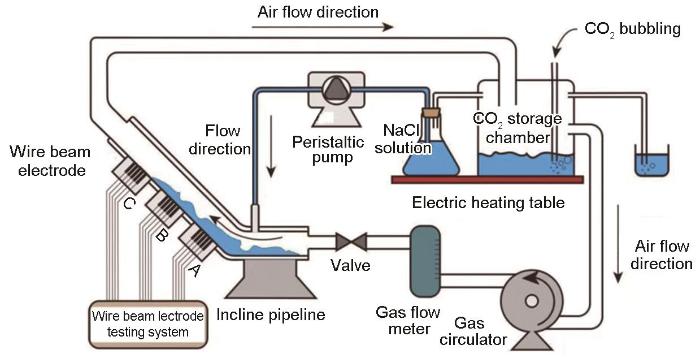
图1 模拟积液区CO2局部腐蚀试验装置示意图
Fig.1 Schematic diagram of CO2 local corrosion test device in the simulated water accumulation area
该装置通过综合调节风机档位及阀门开度实现对管内气体流速的控制。通过蠕动泵持续向管路中注入腐蚀溶液,以模拟湿气管道内液体持续稳定析出过程。参考低持液率输气管线内液体体积含量[7],结合测试管段的结构尺寸,通过预实验摸索确定了实现可控可重现波状流动的注液量 (气体流速为2、4和6 m/s时,注液量分别设为0.5、1和2 mL/min)。实验过程中持续向装置内通入CO2,以维持系统内部的微正压,杜绝外界空气的干扰。
实验测试部分包含3个测试用丝束电极,分别为丝束电极A、B和C,沿气液流动方向依次排布 (图1)。
每个丝束电极由5排×4列的工作电极丝和5排×1列的参比电极丝组成,具体布置见图2。工作电极丝直径1 mm,高度30 mm,由X70钢加工而成,其化学成分为 (质量分数,%):C 0.058、Si 0.425、Mn 1.418、Nb 0.049、Ti 0.009、Mo 0.146、Cr 0.146、Ni 0.038、P 0.011、S 0.002,剩余为Fe。参比电极丝为直径为1 mm的高纯锌丝99.998%。每根电极丝等间距排列,间距为2 mm。每个丝束电极之间间距为30 mm。
图2
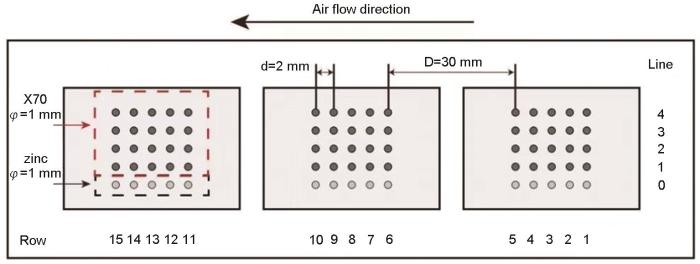
图2 实验丝束电极示意图
Fig.2 Schematic diagram of experimental wire beam electrode
制备丝束电极时,将X70钢电极丝及纯锌丝的一端与铜导线焊接,相互之间绝缘处理,按图2所示方式排布好后用环氧树脂封装成块。将丝束电极工作面由200#水磨砂纸逐级打磨至1000#,再用丙酮和蒸馏水清洗,经冷风吹干后放入干燥皿中备用。
实验所用丝束电极测试装置为实验室自行研制的微电极阵列电偶腐蚀测试系统,该系统采用LabVIEW 8.5编写测控软件,系统由PXI-2535、PXI-1033、PXI-4022以及PXI-4071等模块化仪器组成[21]。在测试时,将丝束电极的接线端与该系统连接,系统可依次测量每根电极丝的耦合电流。测试结束后通过Surfer软件对原始数据进行图像处理和分析。
电化学阻抗谱 (EIS) 测试采用Autolab系列PGSTAT302N型电化学工作站,测试过程激励信号幅值为10 mV,测试频率为10-2~105 Hz。测试结果采用Zview软件进行拟合。鉴于EIS测试中对电极放置位置有明确的要求,而在本研究中难以实现在对气液分层波浪流动无干扰的情况下开展原位EIS测试,故采用了与实验条件相近的静态溶液条件下的非原位测试。EIS测试中,工作电极丝为工作电极,高纯锌丝为参比电极,铂片作对电极,铂片与工作电极平行布置。
采用KUY NICE体视显微镜观察腐蚀后的电极表面形貌。
采用Sony-FDR-AX700 4K高清摄像机拍摄并记录倾斜管路内不同工况条件下的积液分布和流动状态。人工计数获得单位时间内流经不同电极位置处的波浪次数
2 实验结果
2.1 X70钢在不同管道倾角下的测试结果
测试获得气体流速为2 m/s,不同倾角下的耦合电流结果 (图3)。由图可知,在不同倾角下,电极表面耦合电流呈现非均匀分布。倾角为15°时,最大阳极电流为0.896 μA,在第10排;最大阴极电流为-1.43 μA,在第3排。倾角为30°时,最大阳极电流为2.43 μA,在第10排;最大阴极电流为-4.15 μA,在第6排。倾角为45°时,最大阳极电流为1.95 μA,在第8排;最大阴极电流为-1.29 μA,在第12排。电流的符号与阴阳极反应有关,其中负号表示发生阴极反应,电偶腐蚀过程中受到保护;正号表示阳极反应,即发生腐蚀。综合可知,在倾角为15°时,阳极反应主要发生在第7~第11排;在倾角30°时,阳极反应主要发生在第8~第10排和第12~第14排;在倾角为45°时,阳极反应主要发生在第6~第9排。
图3
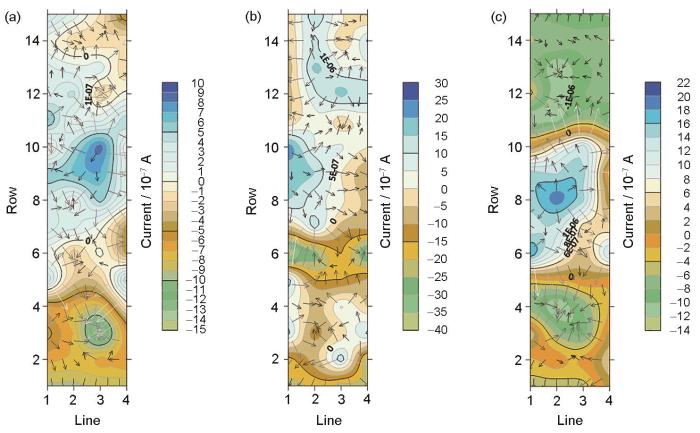
图3 不同倾角下的耦合电流测试结果
Fig.3 Test results of coupling current at different inclination angles: (a) 15°, (b) 30°, (c) 45°
拍照得到不同倾角下电极表面的液膜分布情况 (图4)。可知各倾角下管道内的流型都属于波状流。当倾角为15°时,电极表面的液膜厚度整体较薄,不同电极表面液膜厚度相差不大。倾角增大到30°时,整体液膜厚度则显著增厚,不同电极表面液膜厚度差别开始增大。倾角为45°时,电极表面液膜厚度有显著的差异,表现为上游电极表面液膜厚度较厚,而下游表面液膜厚度较薄。
图4
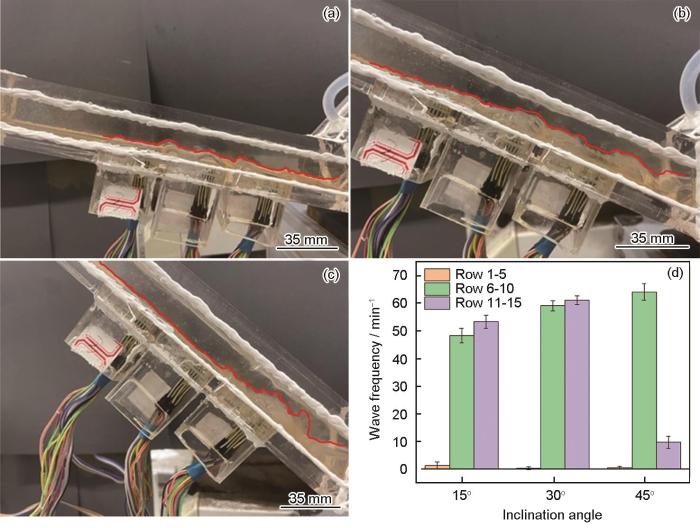
图4 不同倾角管内积液流动状态
Fig.4 Flow state of liquid accumulation in tubes with different inclination angles: distribution of water film in the pipe at 15° (a), 30° (b), 45° (c) and frequency of waves flowing through the electrodes at different inclination angles (d)
值得注意的是,液膜并非是静止的,而是在气流和重力的共同作用下,交替出现以波浪的形式出现向下游的流动和回流。分别记录了3个电极表面波浪的流经频次,如图4d所示。可知,电极A表面流经的波浪频次远小于电极B和C。随着倾角的增大,电极A表面波浪数量基本无区别,而电极B壁面经历的波浪数不断增加。对于电极C,其表面流经的波浪数量随着倾角的增大则表现为先增多后大幅减少。
2.2 X70钢在不同气体流速下的测试结果
测试获得倾角为30°,气体流速分别为4和6 m/s时的耦合电流结果 (图5)。由图可知,气体流速4 m/s时,最大阳极电流在第9排,为0.775 μA;最大阴极电流在第10排,为-1.2 μA。气体流速为6 m/s时,最大阳极电流在第14排,为0.43 μA;最大阴极电流在第6排,为-0.5 μA。随气体流速的增大,最大阴、阳极电流都呈减小趋势。
图5
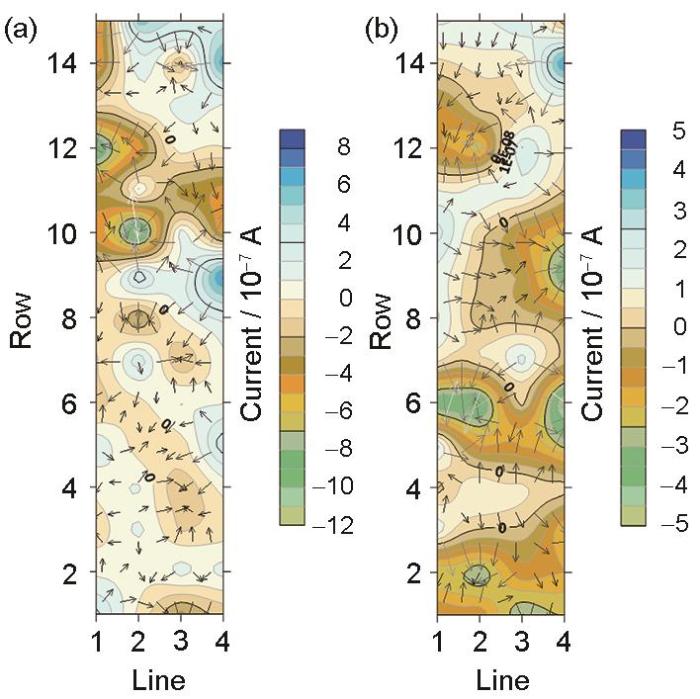
图5 不同气体流速下的耦合电流测试结果
Fig.5 Test results of coupling current at different gas flow rates: (a) 4 m/s, (b) 6 m/s
结合流动状态图和不同电极处气液交替频率分布图 (图6) 来看,随着流速的增大,相同位置不同流速下电极表面的液膜厚度整体呈减薄趋势,电极表面不同位置处液膜厚度差异逐渐增大。电极A所处的上游位置处液膜厚度整体较大,电极B和C表面液膜厚度较小,有波浪经过时将发生厚度的变大。图6c所示电极表面波浪的频次,可知电极A表面频次较低,电极B和C表面频次则较高。随着气体流速的增大,电极A壁面处的波浪频次增多,而电极B和C壁面处的波浪频次则逐渐减小。这是由于气体对液体有裹挟作用,气体流速越大,对液体的裹挟作用越大,导致更多的液相被带到下游,积液区整体积液量减少,因而电极表面整体液膜厚度较小。随着液体量的减小,气体裹挟作用下波浪的频次也相应地降低。
图6
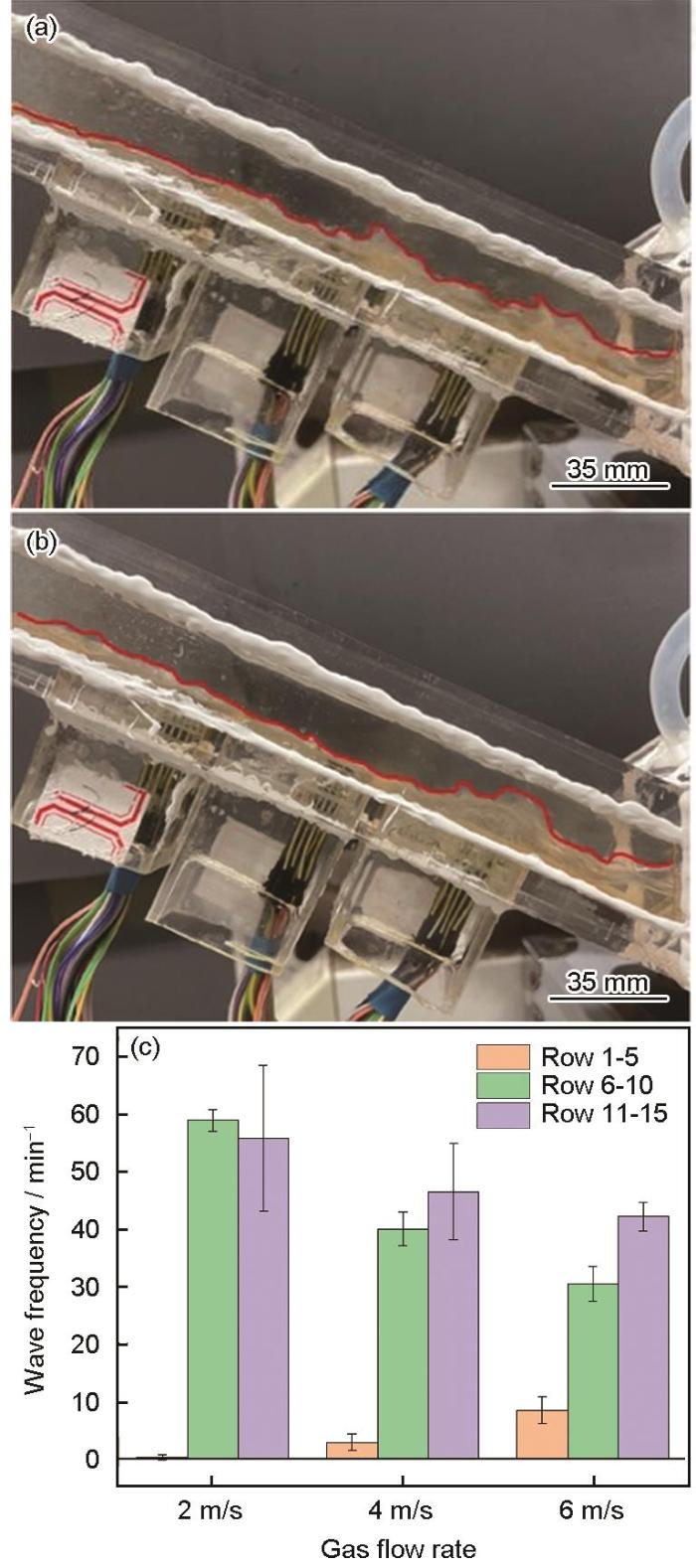
图6 不同气体流速管内积液流动状态
Fig.6 Flow state of liquid accumulation in pipes with different gas velocities: distribution of water film in the pipe at 4 m/s (a), 6 m/s (b) and frequency of waves flowing through the electrodes at different gas velocities (c)
2.3 X70钢在不同时长下的测试结果
测试获得气体流速2 m/s,倾角30°,不同时长下的耦合电流结果 (图7)。由图可知,实验24 h之后,最大阳极电流在第13排,为1.59 μA;最大阴极电流在第11排,为-2.3 μA。168 h之后,最大阳极电流在第13排,为1.504 μA;最大阴极电流在第11排,为-1.96 μA。
图7
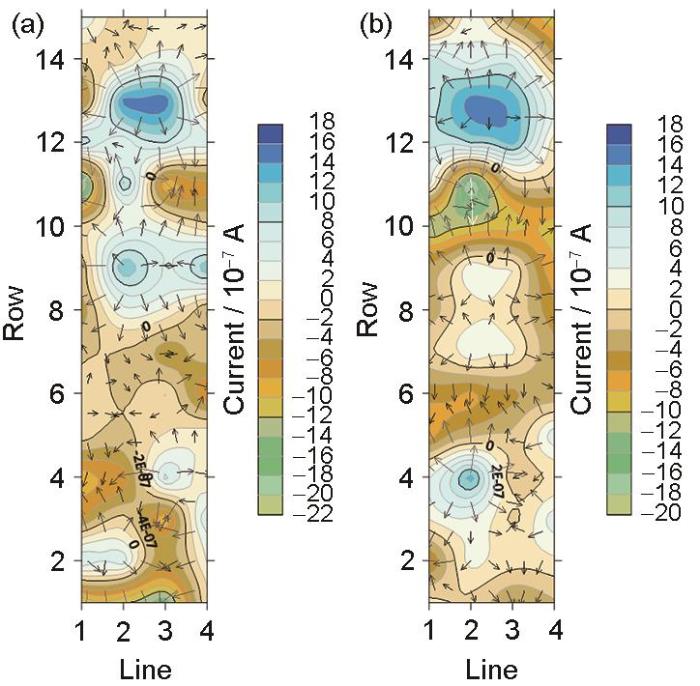
图7 不同腐蚀时间条件下耦合电流分布结果
Fig.7 Coupling current distribution under different corrosion time: (a) 24 h, (b) 168 h
对比可知,随着时间的延长,阴极电流微弱减小。与此同时,除12~14排阳极点的位置无显著变化外,其它位置的阴、阳极极性分布则发生了一定程度地转变,尤其是第8~第10排由阳极区转变为阴极区。阳极区随实验时间的延长而变得更为集中地分布于局部位置。
统计得到了电极表面的阴阳极面积比 (即阴阳极电极的数量比) 随时间的变化,得到12、24和168 h后的阴阳极面积比分别为32∶28、32∶28和31∶29。可见,阴极面积整体略大于阳极,且随着腐蚀时间的延长,阳极面积缓慢增加,阴阳极面积比呈小幅减小的趋势。
董泽华等[22]依据局部腐蚀指数 (LI)提出了可更好地表征丝束电极表面腐蚀非均匀性程度的局部腐蚀因子 (LF),即:
式中分别为丝束电极表面阳极区和阴极区的任一单电极的耦合电流值,Nc/Na代表丝束电极表面阴极区和阳极区单电极数量之比。根据
图8
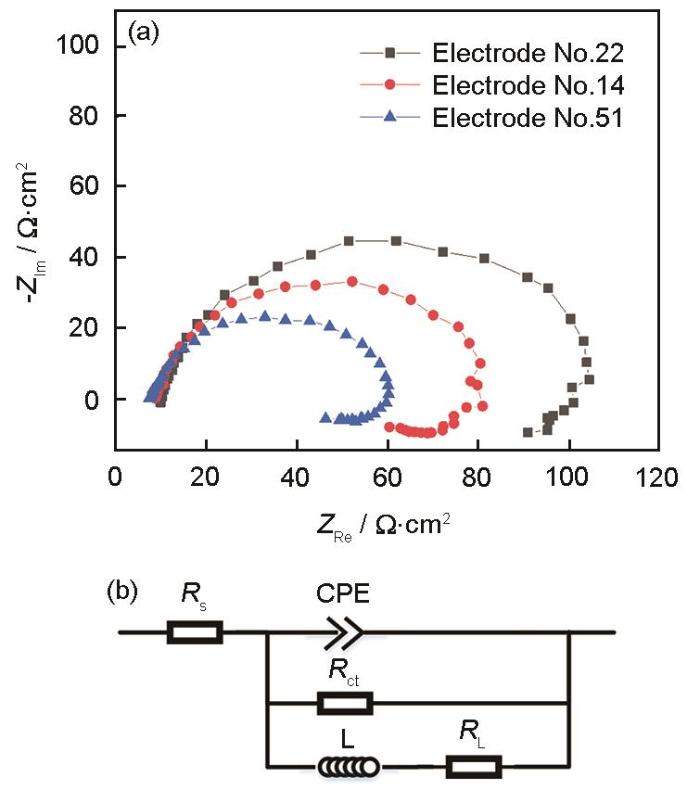
图8 典型位置处电极丝的EIS及其等效电路图
Fig.8 EIS of electrode wire at typical location (a) and equivalent circuit diagram (b)
由拟合结果可以看出,不同位置处电极丝的电荷转移电阻有明显差异,Rct(22)>Rct(14)>Rct(51)。由于电荷转移电阻跟腐蚀速率呈反比关系,对应第51根电极腐蚀速率最大,第14根次之,第22根最小。这与丝束电极测得耦合电流结果所反映的规律一致,即i(51)>i(14)>i(22),表明耦合电流测试结果具有代表性。
图9
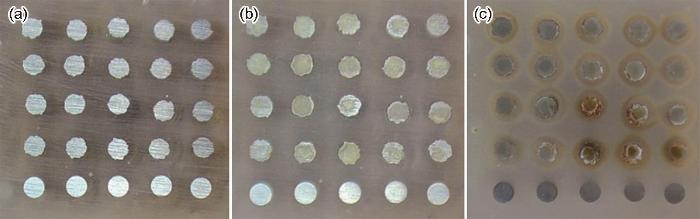
图9 丝束电极C在不同腐蚀时间后的腐蚀形貌
Fig.9 Corrosion morphology of wire beam electrode C after different corrosion time: (a) fresh surface, (b) 24 h, (c) 168 h
由腐蚀168 h后不同位置处的腐蚀形貌图 (图10) 可知,电极B表面不同位置处的腐蚀锈层形态较均匀,而电极A和C的不同位置处锈层形态差异则较明显。电极A锈层差异较大区域主要分布于左上角,而电极C则主要分布于右下角。电极丝周围环氧材料的颜色也一定程度地反映出腐蚀的严重程度,可知尽管电极B表面的腐蚀产物膜层比较均匀,但同样发生了较严重的腐蚀,膜层的分布可归因于气液流动对膜层的冲刷破坏。
图10
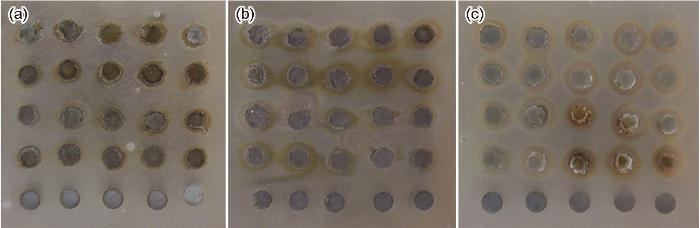
图10 腐蚀168 h后不同位置处电极丝腐蚀形貌
Fig.10 Corrosion morphology of electrode wires at different positions after 168 h corrosion: (a) electrode A, (b) electrode B, (c) electrode C
3 讨论
3.1 腐蚀电化学过程分析
CO2腐蚀体系下,阳极过程主要为Fe的氧化反应:
(2)
该反应又可细分为以下反应步骤[23],包括:
(3)
(4)
(5)
阴极过程跟溶液pH有关。当前100% CO2环境下的pH为3.98,阴极过程主要为H+和碳酸的还原反应[24]为:
(6)
(7)
式中,δ是边界层厚度,Re是雷诺数,d是水力直径。Re与流速成正比,因此流速越大,Re越大,δ数值则越小。相应地,传质也就越快。
CO2腐蚀体系下,腐蚀产物膜的生成是影响腐蚀速率和分布的重要因素。当金属壁面上Fe2+与
(9)
FeCO3在金属壁面的沉积成膜可抑制电化学反应物质向金属壁面的传质、减少金属壁面的活性区域,进而降低金属的腐蚀速率[28]。但FeCO3产物膜对腐蚀速率的有效抑制作用的前提是膜层较为致密,这就要求FeCO3的生成速率足够快,或者其过饱和度大于2[29]。其中,FeCO3的过饱和度 可表示为:
式中,分别为Fe2+、
为FeCO3的溶解度。尽管此前研究多指出,生成保护性腐蚀产物膜的通常要求温度大于60 ℃[30],这是本研究条件所不具备的。但薄层液膜下腐蚀产物膜也有希望生成[31],液膜越薄,溶液更新速率越低,产物膜生成速率越大。相反,液膜厚度大,流速快,波浪的频次高,溶液水化学更新速度快,腐蚀产物膜则越不容易生成。与此同时,在较快的流速冲刷和高频次的波浪冲击作用下,腐蚀产物膜在金属壁面的沉积速率及分布的完整性也将受到影响[32]。
3.2 积液区局部腐蚀的发生与演变行为机制分析
不难理解,腐蚀的不均匀分布与倾斜管道结构影响下的气液两相流动状态有关。模拟析出液体在重力的作用下主要积聚在管道低洼处。当高速气体流过,气流与液体之间的剪切作用导致液体被夹带着向下游流动。根据持液量、管道倾角、气体流速的不同,液体将以不同的流态向下游流动。本研究的流速条件下,液体主要表现为波浪流流型。液膜在管道壁面上的分布状态受到流型的影响,表现为液膜厚度从上游到下游主要表现为逐渐降低的趋势,同时有波浪不断从上游运动到下游。波浪初始流速高,携液量大,但在向下游运动过程中不断减小,甚至有一部分液体在重力作用下发生回流。
鉴于CO2腐蚀速率受阴极过程控制,阴极过程受到液膜厚度、液膜流速的影响,因而液膜厚度越薄、流速越快,腐蚀速率则越快。结合各流动条件下的液膜厚度分布可知,越往下游液膜厚度越薄,但流速也越低,上游厚度较大,而流速也较大。在液膜厚度超过边界层厚度时,往往流速的影响更为重要,因而上游的腐蚀速率理应更大。当波浪存在时,腐蚀速率还受到波浪的扰动影响。结合不同倾角、不同流速下的测试结果可知,波浪频次越高,测得耦合电流越大,这反映出了波浪对腐蚀速率的影响占据更主导的作用。因而,不稳定流动下的腐蚀,较于稳定流动,腐蚀问题突出。段塞流等流型下更为严重的腐蚀问题也说明了这一点。
波浪的存在不仅影响到腐蚀电化学阴极过程,对腐蚀产物膜的生成也会产生影响[33]。腐蚀产物膜的生成需要适宜的条件,同时需要较长时间的积累,所以往往腐蚀初始腐蚀产物膜的影响比较有限,随时间的延长才会比较突出。一方面,波浪会导致溶液化学环境的更新,通过不断注入新鲜低浓度的溶液,降低腐蚀产物膜的饱和度,降低腐蚀产物膜的生成速率和致密程度。另一方面,对于已生成的腐蚀产物膜,波浪的冲击导致金属壁面更大的剪切力,破坏腐蚀产物膜的完整性,降低腐蚀产物膜对腐蚀速率的抑制作用。由于不同位置波浪的频次、波浪的影响程度不同,腐蚀产物膜受到的影响也有不同,因而对不同位置的保护性就有所不同。波浪冲击和腐蚀产物膜共同作用下,导致不同位置处的腐蚀速率差异显著增大,并向局部位置集中,如倾角30°、流速2 m/s下的第13排。随时间的延长,该位置处的耦合阳极电流 (亦为电极表面最大阳极电流) 有所降低,但降幅很小并始终保持较大的电流数值,这与常规体系下均匀腐蚀速率随时间延长大幅降低的趋势有显著区别。对于这种电流数值的降低,阴极区面积减小而阳极区面积增大也会产生一定程度的影响。需要指出,CO2体系下碳钢的腐蚀形貌常表现为凸台状,并不会形成显著的大阴极小阳极。尽管如此,电极表面局部位置相较于其它区域维持着较高的腐蚀速率,腐蚀非均匀性程度随着腐蚀时间的延长不断增大。
由图10可知,短时间内并不能形成致密并具备良好保护性的产物膜,因而金属壁面的液膜状态成为影响腐蚀均匀性的重要因素,这包含液膜厚度分布的均匀性及液膜的运动状态。液膜厚度的不均匀性可导致腐蚀阴极反应速率及近壁面处液膜pH的差异。局部位置液膜不规律的运动,可加快反应物质的传质,稀释现有的饱和溶液,促进相应位置的腐蚀。
4 结论
(1) 对湿天然气管道,低洼段积液位置处将发生局部腐蚀,表现为局部位置处的腐蚀电位、耦合电流存在显著差异。在本文研究条件下,气体流速为2 m/s,管道倾角为30°时,局部腐蚀最为严重。
(2) 随着腐蚀时间的延长,阳极区将向局部位置集中,表现为更严重的局部腐蚀现象。
(3) 在管道结构、流动参数等的影响下,积液区局部位置处液膜厚度的不均匀分布、波浪流经的频次大小、腐蚀产物膜的生成情况等共同影响液膜下的局部腐蚀行为,其中波浪频次、腐蚀产物膜的影响更为显著。
免责声明:本网站所转载的文字、图片与视频资料版权归原创作者所有,如果涉及侵权,请第一时间联系本网删除。
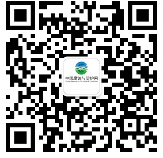
官方微信
《腐蚀与防护网电子期刊》征订启事
- 投稿联系:编辑部
- 电话:010-62316606
- 邮箱:fsfhzy666@163.com
- 腐蚀与防护网官方QQ群:140808414