项目 | 时间/h | 温度/℃ | 相对湿度/% |
---|---|---|---|
盐雾 | 2 | 35±2 | >95 |
干 | 4 | 60±2 | <30 |
湿 | 2 | 50±2 | >95 |
随着我国电力工业的快速发展,国民经济对电力的需求显著增加,相关电力设备的服役范围更广泛、环境更加复杂,涵盖了高温、高湿、高盐雾等严重腐蚀地区。同时,近年来清洁能源发展迅速,海上风电、光伏发电等使用比例大幅增加,因此变压器、钢构支架等面临严重的海洋腐蚀考验[1-2]。当前为提升输变电设备服役可靠性,延长其服役寿命,保障供电安全,多采用溶剂型防腐蚀涂料进行防护。电力系统应用的防腐蚀涂料主要为溶剂型环氧富锌涂料、溶剂型环氧云铁涂料和溶剂型丙烯酸聚氨酯面漆等[3]。上述防腐蚀涂层体系在维护电力设备安全可靠运行方面发挥了重要作用。值得注意的是,溶剂型涂料在涂装过程中会释放大量的挥发性有机物(VOCs),严重危害了人体健康和生态环境安全[4-5]。近年来,我国在环境保护方面出台了系列法律法规,要求推广应用低(无)VOCs排放的环保性防腐蚀技术。因此水性环保防腐蚀涂料体系得到迅猛的发展和极大的关注。
张志伟等[6]采用中性盐雾试验结合电化学阻抗谱(EIS)技术,研究了水性无机富锌涂料的耐腐蚀性能,发现制备的新型水性无机富锌涂料的含锌量为81.7%(质量分数,下同)、石墨烯纳米材料含量为0.8%时,涂层附着力、铅笔硬度和柔韧性均明显提高,涂层外观和成膜性完好,耐腐蚀性能大幅提升,该涂料可应用于沿海光伏电站钢结构支架。莫娟等[7-8]通过添加石墨烯等碳材料研制了一种高导热防腐蚀底漆,导热系数高达1.345 W/(m·K);随后又研制了新型高导热防腐蚀中间漆和面漆,并进一步通过变压器温升模拟试验和电化学阻抗谱技术验证了其散热性能和防腐蚀性能。李亮等[9]将氧化石墨烯(GO)和不含卤素的磷-氮阻燃剂均匀地分散到水性环氧树脂体系中,利用凝聚相阻燃和气相阻燃混合阻燃技术制备了防火防腐蚀一体化涂层,并通过电化学技术对其性能进行了测试。值得注意的是,目前大多数研究集中在新涂料配方的研制以及采用中性盐雾试验或者电化学技术对涂层性能进行评价等方面,对于电力设备的实际服役环境,尤其是近海环境,干湿交替与盐雾环境协同作用对涂层防护性能的影响机制报道较少。
为了进一步阐明电力设备用水性防腐蚀涂层体系在海洋大气环境中的防护机制,笔者采用循环盐雾试验结合电化学测试等,系统研究了涂层的老化机制,分析了涂层形貌、光泽度以及附着力等性能指标,旨在为电力设备水性防腐蚀涂层的开发、推广与应用提供理论依据。
1. 试验
1.1 试验材料
首先切取尺寸为150 mm×70 mm×3 mm的Q235碳钢板,并对其进行喷砂处理,使表面粗糙度达到Sa2.5,依次使用酒精、去离子水清洗并吹干备用。采用喷涂的方式依次涂装水性环氧富锌底漆、水性环氧云铁中间漆和水性丙烯酸聚氨酯面漆,涂装厚度分别为60 μm、140 μm和60 μm。将带有涂层的Q235碳钢板记为涂层试样。
1.2 循环盐雾试验
参照GB/T 20854-2007《金属和合金的腐蚀 循环暴露在盐雾、“干”和“湿”条件下的加速实验》标准,采用Q-LAB CCT-600循环盐雾试验箱对涂层进行模拟加速试验。试验采用5%(质量分数)氯化钠溶液进行喷雾,pH为6.5~7.2,试验具体参数见表1。试验周期分别为0,300,600,900,1 200 h。试验完成后,用去离子水冲洗涂层试样表面残留盐渍,风干后备用。
1.3 涂层性能测试
循环盐雾试验后,采用DeFelsko S/N ATC8229型涂层拉拔仪测试涂层附着力。通过光学显微镜观察涂层试样表面形貌。通过光泽计获取试样表面光泽度。为了保证获取数据的可靠性,上述测试次数不少于3次。
采用美国普林斯顿Parstat4000A型电化学工作站对经不同时间盐雾腐蚀后的涂层试样进行电化学阻抗谱测试,测试系统为三电极体系,铂片为辅助电极,饱和甘汞电极(SCE)为参比电极,涂层试样为工作电极。将内径为4 cm的有机玻璃管放置于工作电极表面,用橡胶圈对接触面进行密封,使用螺栓固定,隔离出12.56 cm2的面积为涂层试样工作面积,并向玻璃管中加入3.5%(质量分数)NaCl溶液作为电解质溶液。测试频率为0.01 Hz~100 kHz,施加的激励电位幅值为10 mV。电化学阻抗谱测试在法拉第电磁屏蔽箱中进行。
2. 结果与讨论
2.1 涂层附着力
如图1所示:试验前涂层的附着力为8.0 MPa,表明该水性防腐蚀涂料在碳钢基体表面具有良好的附着性能;随着循环盐雾时间的延长,涂层附着力表现出逐渐降低的趋势,当循环盐雾时间达到600 h时,涂层附着力不再继续下降。这可能主要归因于试验初期,随着盐雾等电解质溶液向涂层内部的渗入,涂层的内聚力降低,进而导致附着力下降;但随着试验时间进一步延长,由于干循环温度为60 ℃,这可能在一定程度上增加了涂层内部树脂的交联密度,进而弥补由于电解质渗入引起的涂层附着力降低,因此,在试验后期,涂层附着力并未继续下降。肖盼等[10]在研究用于带锈铁塔涂料防护性能的过程中发现了类似的现象。经1 200 h循环盐雾后涂层附着力仍高达6 MPa,满足HG/T 4770-2014《电力变压器用防腐涂料》技术要求中的I类性能指标。
2.2 涂层光泽度
如图2所示,随盐雾时间的延长,涂层光泽度呈逐渐下降的趋势。这主要是因为在盐雾与干湿交替环境中,涂层面漆发生了老化失光。这从循环盐雾试验后涂层表面的形貌变化也可以得到证实,如图3所示。依据GB/T 1766-2008《色漆和清漆涂层老化的评级方法》对涂层光泽度进行评估,发现在盐雾腐蚀600 h时涂层失光度等级为2级,900 h与1 200 h时涂层失光度等级为3级。
2.3 涂层电化学性能
低频(0.01 Hz)阻抗值|Z|0.01 Hz通常用来表征涂层的防护性能[11-12]。如图4所示:对于盐雾时间为0的涂层试样,低频阻抗值|Z|0.01 Hz为4.8×109 Ω·cm2;循环盐雾试验300 h后,涂层试样的低频阻抗值降低至1.6×109 Ω·cm2,这主要归因于电解质的渗透作用;随着循环盐雾时间的延长,由于锌粉的电化学反应形成的腐蚀产物在一定程度上堵塞了涂层孔隙,使得涂层试样的低频阻抗值表现出上升的趋势;当循环盐雾时间达到1 200 h时,低频阻抗值进一步下降,这主要是此时基体发生了腐蚀,涂层的防护性能下降所致。
对电化学阻抗谱数据进行了等效电路拟合。对于盐雾时间为0的涂层试样,Bode图仅显示一个时间常数,因此采用图5(a)所示等效电路进行拟合。其中Rs表示溶液电阻,Qc和Rc表示涂层电容和涂层电阻。在循环盐雾环境中,含氯离子电解质溶液逐渐向涂层渗透,其与环氧富锌底漆相接触会引发锌粉的电化学反应,此时Bode图表现出两个时间常数,并且由于涂层对电解质溶液的渗透具有阻碍作用,EIS图显示出韦伯阻抗特征,因此采用图5(b)所示等效电路进行拟合。其中Q1和R1表示锌粉发生电化学反应的双电层电容和电荷转移电阻,W为韦伯阻抗。随着循环盐雾时间延长,涂层对电解质溶液渗透过程的阻碍作用减弱,此时韦伯阻抗消失,且由于电解质逐渐渗透至试样基体,引发了碳钢的腐蚀,Bode图显示了三个时间常数,此时采用图5(c)所示等效电路进行拟合。其中Q2和R2分别表示基体金属发生电化学反应的双电层电容和电荷转移电阻。考虑到Nyquist图中圆弧偏离了规则半圆弧,表明电化学反应过程偏离了理想电容响应,这主要与试样表面的传质和驰豫过程的局部不均匀性以及表面粗糙度有关[13]。因此,在等效电路中采用常相位角元件(CPE)代替纯电容元件[14]。常相位角元件的阻抗可通过式(1)获得。
|
(1) |
式中:Y0为CPE常数;ω为角频率;n为CPE元件的指数,表示试样表面电容偏离理想电容的程度[15-16]。n=1,表示该元件为纯电容;n=0,表示该元件为纯电阻;n=-1,表示该元件为电感[17]。
极化电阻(Rp=Rc+R1+R2)通常用来定量分析涂层的防腐蚀性能[18-20]。根据图5所示等效电路计算获得涂层极化电阻如图6所示。可以看出:当盐雾时间为0时,极化电阻最大,高达7.5×109 Ω·cm2,表明涂层具有十分优异的防护性能;随着循环盐雾时间的延长,极化电阻显著降低,这主要归因于在循环盐雾环境中,电解质逐渐向涂层内部渗透,降低了涂层的电阻;继续延长循环盐雾时间,涂层的环氧富锌底漆中的锌粉发生电化学反应,形成的腐蚀产物在一定程度堵塞了涂层孔隙,阻碍了电解质的渗透过程,因此极化电阻略微上升;当循环盐雾时间达到1 200 h时,涂层发生明显的老化,抗渗透能力下降,电解质渗透至基体,引发了基体金属的腐蚀,因此极化电阻下降。
2.4 涂层孔隙率
涂层在老化失效过程中孔隙率通常会发生变化,可通过公式(2)估算涂层孔隙率(P)随循环盐雾试验时间的变化规律[21-23]。
|
(2) |
式中:Rc为涂层电阻;Rpt为涂层的孔隙率趋于“无穷”时的涂层电阻,Rpt可通过式(3)进行计算。
|
(3) |
式中:d为涂层厚度,μm,本研究取260 μm;A为测试试样面积,cm2,本研究试样面积为12.56 cm2;k0为溶液介质电导率,经测试本研究所使用的溶液电导率为3 S·m-1。
根据公式(2)和(3)计算得到涂层孔隙率随循环盐雾试验时间的变化关系曲线,如图7所示。整体来看,盐雾试验初期涂层的孔隙率最低,随着循环盐雾时间延长至300 h,电解质逐渐渗透,涂层的孔隙率增加;继续延长盐雾腐蚀时间,涂层的环氧富锌底漆中的锌粉发生电化学反应,涂层孔隙率降低;当循环盐雾时间达到1 200 h时,孔隙率达到最高。孔隙率随盐雾时间的变化规律与涂层极化电阻的变化过程相印证。
3. 结论
(1)涂层附着力在循环盐雾试验初期呈现逐渐减小的趋势,随后变化不明显;在1 200 h循环盐雾试验后,附着力仍高达6 MPa,可达到技术要求中的I类标准。
(2)涂层试样的极化电阻随盐雾时间的延长呈先急剧减小后略微增大,在循环盐雾1 200 h时,极化电阻又略微减小,此时涂层试样的低频电阻值仍高达108 Ω·cm2,表明该水性防腐蚀涂层仍具有良好的防护效果。
免责声明:本网站所转载的文字、图片与视频资料版权归原创作者所有,如果涉及侵权,请第一时间联系本网删除。
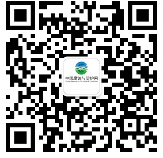
官方微信
《腐蚀与防护网电子期刊》征订启事
- 投稿联系:编辑部
- 电话:010-62316606
- 邮箱:fsfhzy666@163.com
- 腐蚀与防护网官方QQ群:140808414