元素 | C | Mn | Si | S | P | Fe |
---|---|---|---|---|---|---|
质量分数/% | 0.15~0.20 | 0.32~0.65 | ≤0.30 | ≤0.05 | ≤0.042 | 余量 |
传统的涂料体系中含有一定量的挥发性有机化合物(VOCs),会造成严重的环境污染。与传统涂料相比,水性环氧涂料更加环保,已成为有机涂料的主要研究对象。但是,在固化成膜的过程中,由于水和溶剂的蒸发,会形成细小的孔隙,为腐蚀介质提供通道,加速腐蚀。纳米颗粒由于体积小,常被用于解决水性涂料的微孔问题[1]。Fe3O4纳米颗粒由于成本低、耐腐蚀、导电性好等优点,在防腐蚀涂料领域得到了广泛应用。但单一纳米Fe3O4容易团聚,体系分散性差。因此,合成分散性良好的Fe3O4纳米复合材料成为研究热点。当金属基体暴露在水、氧等腐蚀性介质中时,由于聚苯胺(PANI)在酸性溶液中具有可逆的氧化还原活性,可以激发聚苯胺的电化学活性,并在腐蚀反应中进行电荷转移,促进氧化膜的形成,从而有效提高涂层的耐蚀性[2-4]。氧化石墨烯(GO)由于其片状结构,与Fe3O4结合时具有较大的表面积和良好的分散性,可有效防止腐蚀介质在涂层中的渗透,发挥良好的屏蔽作用[5-8]。聚苯胺和石墨烯的导电性在一定程度上有利于提高涂层的耐蚀性,但当导电性较高时,电化学腐蚀过程中的电子转移会加速,从而加速金属基体的腐蚀[9]。ZHOU等[10]研究了石墨烯/铜复合材料防腐蚀后期情况。结果表明:石墨烯的高导电性使阴极反应从铜表面扩散到石墨烯导电网络,传质阻力的降低进一步加速了阴极反应,导致铜的腐蚀更加严重。因此,Fe3O4的加入可以有效降低材料的电导率。同时,Fe3O4能减弱聚苯胺由中性向碱性的转变,增强聚苯胺在溶液中的电化学腐蚀性能[11]。EL-MAHDY等[12]将Fe3O4纳米颗粒加入交联丙烯酰胺-丙烯酸钠基体中制备复合材料。结果表明,Fe3O4纳米颗粒与聚合物在分子水平上发生了相互作用,提高了Fe3O4纳米颗粒的分散性和基体的耐蚀性[13]。BAGHERZADEH等[14]通过苯胺原位氧化聚合在Fe3O4纳米颗粒表面制得Fe3O4/PANI纳米复合材料,填充环氧树脂后纳米复合涂层的耐蚀性明显增强。以Fe3O4/PANI纳米复合材料为基础,通过添加还原氧化石墨烯(rGO)纳米片,将球形核壳结构转变为三维层状结构。结果表明,rGO表面的疏水性和大比表面效应在一定程度上增强了涂层的纳米阻隔效果。此外,PANI优异的导电性也促进了金属表面的钝化[15]。ZHU等[16]采用苯胺原位氧化聚合法制备了rGO/Fe3O4/PANI三元纳米复合材料,并将其添加到氨基丙烯酸树脂中制备纳米复合涂层,分析了复合涂层的防腐蚀机理。结果表明,纳米复合涂层的耐蚀性得到了很大的提高,复合涂层具有独特的物理屏障作用和阳极钝化机制[13]。
Fe3O4纳米颗粒由于具有小尺寸纳米阻隔效应和耐蚀性,已被广泛应用于金属防腐蚀涂料领域。为了进一步提高其金属防腐蚀活性和分散性,笔者采用具有电化学防腐蚀活性的PANI对其复合改性,构建了具有核壳形态的二元纳米复合材料。在此基础上,引入氧化石墨烯负载Fe3O4纳米颗粒,并以水性环氧树脂(EP)为填料,采用苯胺原位氧化聚合法制备了水基rGO/Fe3O4/PANI三元纳米复合材料。采用Tafel极化曲线、电化学阻抗谱和中性盐雾试验研究了该腐蚀涂层的防腐蚀性能和机理,以期为替代有毒重金属防腐蚀材料提供理论依据。
1. 试验
1.1 试验材料及表面预处理
试验基体材料为马口铁工件,其化学成分如表1所示。将其加工成尺寸为120 mm×50 mm×0.5 mm的试样,采用高温(200~300 ℃)除油,用砂纸抛光,然后在丙酮和乙醇溶液中超声处理以脱脂,干燥后备用。
主要试验试剂有四氧化三铁(山东国化化学有限公司),乙酸(济南广宇化工有限公司),氧化石墨烯(常州第六元素材料科技股份有限公司),苯胺(济南银润化工有限公司),过硫酸铵(APS)(济南金昊化工有限公司),正丁醇(南京卓诚石油化工有限公司),环氧树脂(E-44)(广州共富化工有限公司),吡啶(C5H5N)(南京华曦化工有限公司),固化剂(T-31)(山东优索化工科技有限公司),分散剂D-346(广州共富化工有限公司)。
1.2 纳米复合涂层的制备
1.2.1 纳米复合材料的制备
将0.25 g氧化石墨烯和0.25 g Fe3O4加入200 mL蒸馏水中,倒入容量为300 mL的三颈烧瓶中。加入0.5 g苯胺,100 ℃下反应3 h冷却至20 ℃。加入乙酸使溶液pH为1,加入0.5 g苯胺,冰浴使温度稳定在0~5 ℃。用电子天平称量2.72 g过硫酸铵溶于50 mL蒸馏水中,通过滴液漏斗匀速加入三颈烧瓶中,氧化聚合10 h。经过滤后,用乙醇和水各洗涤3次,80 ℃真空干燥24 h,得到rGO/Fe3O4/PANI复合材料。图1为rGO/Fe3O4/PANI复合材料制备工艺示意,可以看出氧化石墨烯薄片首先被超声波分散,而Fe3O4则在铁氧配位的驱动力下被加载到氧化石墨烯薄片上。其次,以苯胺为还原剂制备rGO,形成rGO/Fe3O4复合材料。然后苯胺在Fe3O4和rGO表面进行原位氧化聚合,最后用聚苯胺涂覆rGO/Fe3O4复合材料,制备出了具有多层结构的rGO/Fe3O4/PANI三元复合材料。
1.2.2 纳米复合涂层的制备
将0.6 g rGO/Fe3O4复合材料(rGO、Fe3O4质量比为1∶1)与0.225 g分散剂D-346掺入10 g蒸馏水中,超声分散均匀。称取环氧树脂15 g,加入15 mL稀释剂,机械搅拌至均匀分散。1 h后,加入促进剂吡啶(2.5 mL),搅拌20 min。加入固化剂T-31(3.0 mL),搅拌30 min。将分散好的rGO/Fe3O4复合材料加入环氧树脂中,室温超声2.5~3 h。将rGO/Fe3O4/EP涂料均匀涂覆在抛光干净的马口铁试样上,在180 ℃下固化1 h,制备得到填充量为2.5%的rGO/Fe3O4/EP涂层。同样的,采用上述方法制备填充量为2.5%的rGO/Fe3O4/PANI/EP涂层(rGO、Fe3O4和PANI的质量比为1∶1∶4)。
1.3 rGO/Fe3O4/PANI复合材料的分散性
分别取10 mL rGO/Fe3O4/EP和rGO/Fe3O4/PANI/EP涂料倒入离心管中静置48 d,结果如图2所示。从图2中可以看出,rGO/Fe3O4/EP涂料静置48 d后发生分层,上层为环氧树脂,下层为rGO/Fe3O4二元纳米颗粒。这是因为氧化石墨烯还原后,表面活性基团消失,其表面与树脂基团相互作用的活性点大大减少,疏水性增加,因此rGO/Fe3O4复合材料不易分散在环氧树脂中。对于rGO/Fe3O4/PANI/EP涂料,表面PANI可与环氧树脂中的环氧基团发生开环反应生成羟基,极大地促进了其在树脂中的分散。因此,与二元纳米材料相比,三元纳米材料具有更好的分散稳定性。
1.4 表征与测试
1.4.1 电化学测试
在CHI660A电化学工作站上进行电化学试验。试样用HY914胶水密封。工作电极为涂覆纯环氧树脂涂层、rGO/Fe3O4/EP和rGO/Fe3O4/PANI/EP复合涂层的马口铁试样(以下分别简称纯环氧涂层试样,rGO/Fe3O4试样,rGO/Fe3O4/PANI试样),工作面积为10 mm×10 mm,参比电极为饱和甘汞电极(SCE),辅助电极为1.0 cm2铂网,腐蚀介质为室温3.5%(质量分数)NaCl溶液,试验时间为1,7,14,21,28,35,42,49,56,70 d,溶液pH为7。在N2下稳定10 min开始测试,试验在室温下进行。在开路电位稳定后,测试电化学阻抗谱(EIS)和Tafel极化曲线。在3.5%(质量分数)NaCl溶液中,pH为1和9条件下,试验时间为1,7,14,21,28,35,42,49,56,70 d,对rGO/Fe3O4/PANI试样进行EIS测试。
Tafel极化曲线测试参数如下:扫描范围为开路电位±500 mV,扫描速率为5 mV/s。EIS测试参数如下:频率范围为0.01~ 105 Hz,交流电压幅值为0.01~1 V。为了避免杂散电流和外部干扰,系统被放置在一个自制的法拉第屏蔽笼中。利用电化学分析仪软件对试验数据进行外推。用Zsimp Win软件进行数据拟合。
1.4.2 中性盐雾试验
根据GB/T 10125-2012《人造气氛腐蚀试验盐雾试验》,采用HDYW-120盐雾箱进行中性盐雾试验,试验介质为5%(质量分数)NaCl溶液,试验材料为纯环氧涂层试样、rGO/Fe3O4/EP试样和rGO/Fe3O4/PANI/EP试样。具体方法为将涂层以倾斜角度15°放置在盐雾腐蚀试验箱中,连续喷5%NaCl溶液,试验时间为168 h和360 h。
1.4.3 透射电子显微镜(TEM)
将样品分散在乙醇中,用移液枪取少量样品滴在铜网上烘干,通过TecLiiG20型透射电子显微镜(TEM)观察样品的微观形貌。
2. 结果与讨论
2.1 微观形貌
如图3所示:Fe3O4纳米颗粒负载在rGO薄片上;rGO/Fe3O4/PANI三元共聚物中,Fe3O4与PANI形成了核壳结构,且PANI覆盖在rGO薄片上。
2.2 涂层耐盐雾腐蚀性能
由图4可见:连续盐雾168 h后,纯环氧涂层试样表面整个区域都发生了鼓泡和腐蚀,腐蚀程度比较严重,说明纯环氧涂层的耐盐雾腐蚀性能较差;rGO/Fe3O4/EP试样表面起泡面积达到1/3以上,少数部位生锈,说明rGO/Fe3O4复合材料的加入提高了涂层的耐盐雾腐蚀性能;相比之下,rGO/Fe3O4/PANI/EP试样表面几乎不起泡,说明rGO/Fe3O4/PANI/EP涂层的耐盐雾腐蚀性能最好,涂层阻隔腐蚀介质效果明显;rGO/Fe3O4/PANI/EP试样在连续盐雾360 h后开始起泡,这是由于涂层中rGO/Fe3O4/PANI三元共聚物多层结构的物理阻隔效应。
2.3 涂层电化学性能
2.3.1 Tafel极化曲线
由图5可见:在3.5%NaCl溶液中浸泡21 d后,纯环氧涂层试样的自腐蚀电位为-513 mV,而rGO/Fe3O4/EP和rGO/Fe3O4/PANI/EP试样的自腐蚀电位分别为-368 mV和-257 mV。这是由于rGO/Fe3O4/EP和rGO/Fe3O4/PANI/EP涂层的阻挡作用避免了阳极反应,阳极电位升高,说明两者在3.5%NaCl溶液中都具有良好的阻挡作用。rGO/Fe3O4/PANI/EP试样的自腐蚀电位最高,自腐蚀电流密度最低;rGO/Fe3O4/PANI/EP试样的自腐蚀电流密度比rGO/Fe3O4/EP试样低一个数量级,因此rGO/Fe3O4/PANI/EP涂层具有最好的耐蚀性[17]。
由表2可见,rGO/Fe3O4/PANI/EP涂层的防护效率为99.85%,这主要是由于涂层中rGO/Fe3O4/PANI复合材料的阻隔作用。具有层状自组装结构的rGO/Fe3O4/PANI纳米复合材料增加了腐蚀性介质在涂层中的扩散和弯曲程度,对金属基体起到良好的防腐蚀效果。
|
(1) |
式中:Jcorr,0为纯环氧涂层试样的腐蚀电流密度;Jcorr,i为其他涂层试样的腐蚀电流密度;QEPE为涂层的防护效率。
试样 | Ecorr/V | Jcorr/(A·cm-2) | QEPE/% |
---|---|---|---|
纯环氧涂层 | -513 | 3.19×10-7 | — |
rGO/Fe3O4/EP | -368 | 3.37×10-9 | 93.20 |
rGO/Fe3O4/PANI/EP | -257 | 1.85×10-10 | 99.85 |
2.3.2 电化学阻抗谱
由图6(a)和(b)可见:纯环氧涂层试样的|Z|0.01 Hz值从浸泡1 d时的3.67×108 Ω·cm2快速下降到浸泡21 d时的3.46×105 Ω·cm2,此后涂层基本失去防护性能;而浸泡21 d时rGO/Fe3O4/EP试样和rGO/Fe3O4/PANI/EP试样的|Z|0.01 Hz值分别为2.76×107 Ω·cm2和3.45×108 Ω·cm2,说明rGO/Fe3O4和rGO/Fe3O4/PANI纳米复合材料提高了涂层的防腐蚀性能;其次,rGO/Fe3O4/EP试样的|Z|0.01 Hz值在浸泡49 d时下降到5.32×105 Ω·cm2,此时涂层已失去防腐蚀效果[18];而rGO/Fe3O4/PANI/EP试样在浸泡70 d时的|Z|0.01 Hz值仍有2.31×107 Ω·cm2,说明rGO/Fe3O4/PANI/EP涂层的阻隔性能优于rGO/Fe3O4/EP涂层。这是由于自组装的rGO/Fe3O4/PANI复合材料使腐蚀性介质在涂层中的扩散路径更长,所以腐蚀性介质到达金属基体的时间也更长[19-20]。由图6(d)~(f)可见:浸泡初期,涂层的单容抗弧半径明显减小,甚至低频处出现尾弧,这表明腐蚀性介质开始穿透涂层,涂层阻抗逐渐减小,涂层电容逐渐增大,耐蚀性逐渐降低;随着腐蚀介质的继续渗透,浸泡21 d后纯环氧涂层试样的Nyquist图出现了明显的双容抗弧,这表明腐蚀介质已穿透涂层到达金属基体,基体表面发生了电化学腐蚀反应;rGO/Fe3O4/EP涂层的保护时间比纯环氧涂层延长了28 d,即rGO/Fe3O4/EP涂层的耐蚀性优于纯环氧涂层;而rGO/Fe3O4/PANI/EP涂层处于单容抗弧状态,在浸泡70 d后,rGO/Fe3O4/PANI/EP涂层仍起到了良好的保护作用。这是因为,除了rGO/Fe3O4/PANI复合材料具有良好的阻隔效果外,PANI在中性溶液中具有氧化还原活性和良好的耐电化学腐蚀性能,可在金属基体上形成致密的氧化膜。在浸泡初始阶段,采用图7(a)所示的等效电路拟合,随着浸泡时间的延长,腐蚀性介质在涂层中不断扩散,直至与金属基体接触,此时采用图7(b)所示的等效电路拟合。其中:Rs为工作电极和参比电极间溶液电阻;Rc为涂层电阻;Cc为涂层的常相位角元件;Cd为双电层的常相位角元件;Rcorr为电化学电荷转移电阻。
由图8可见:当pH为1时,rGO/Fe3O4/PANI试样在浸泡1 d后的|Z|0.01 Hz为2.49×109 Ω·cm2,浸泡21 d后为5.99×107 Ω·cm2;浸泡56 d后,|Z|0.01 Hz还稳定在2.5×106 Ω·cm2,Nyqusit图仍然显示单容抗弧;当pH为9时,浸泡49 d后,rGO/Fe3O4/PANI试样的|Z|0.01 Hz降至106 Ω·cm2以下,浸泡56 d后,Nyqusit曲线出现双容抗弧,说明涂层在碱性介质中已基本失去防护功能。结合图6和图8可知,rGO/Fe3O4/PANI/EP涂层在中性和酸性溶液中具有良好的防腐蚀性能。
2.4 防腐蚀机理讨论
由图9可见:在浸泡初期,两种涂层由于疏水性好,都能起到很好的阻隔作用,O2和H2O等腐蚀性介质被阻隔在涂层的外表面;随着浸泡时间的延长,腐蚀性介质逐渐渗透到涂层中,与图9中的纯环氧涂层相比,加入rGO/Fe3O4和rGO/Fe3O4/PANI复合材料可以填充环氧树脂的孔隙。这可在涂层中引起“迷宫效应”,即腐蚀性介质在涂层中渗透路径的弯曲程度增大,涂层的耐蚀性得到进一步提高[21]。
在浸泡过程中,涂层电阻降低,对应的涂层电容(Cc)增大。当腐蚀性介质穿透涂层并到达金属基体表面时会与其发生腐蚀反应,此时界面处会出现双电层电容(Cd)和电荷转移电阻(Rcorr),rGO/Fe3O4/EP涂层在界面处的电荷转移电阻较低,金属基体在腐蚀介质H2O和O2等的作用下容易生锈,造成表面腐蚀。对于rGO/Fe3O4/PANI/EP涂层,聚苯胺和石墨烯都具有一定的导电性,可以将电子转移到涂层表面,发生阴极反应O2+2H2O+4e-→4OH-。当基体接触到腐蚀性介质时,发生电化学腐蚀产生Fe3+,聚苯胺本身被还原为还原态聚苯胺(LS),而Fe3+与O2-反应生成稳定氧化物Fe2O3[22]。LS在O2和H2O共存环境中被氧化成本征态聚苯胺(EB)。由于PANI的还原氧化活性具有可逆性,在腐蚀介质不断渗透的过程中,反应可以循环进行,从而逐渐形成致密的氧化膜。致密氧化膜的存在大大增加了界面Rct,延缓了金属表面的腐蚀速率。因此,与rGO/Fe3O4/EP涂层相比,rGO/Fe3O4/PANI/EP涂层不仅具有更好的阻隔效果,而且在腐蚀性介质渗透过程中可以激发聚苯胺的电化学防腐蚀性能,从而形成涂层的智能防腐蚀机制。
3. 结论
(1)与纯环氧涂层和rGO/Fe3O4/EP涂层相比,rGO/Fe3O4/PANI/EP涂层的耐盐雾腐蚀性能最佳,分散性好,稳定性好。腐蚀介质通过涂层发生电化学腐蚀时可激发聚苯胺的还原氧化活性,形成致密的氧化膜。rGO/Fe3O4/PANI/EP涂层在中性和酸性溶液中具有良好的耐蚀性,优于rGO/Fe3O4/EP涂层。
(2)rGO/Fe3O4/PANI纳米复合材料的防腐蚀机理是层状的微观结构产生的有效物理屏障作用和聚苯胺在腐蚀性介质渗透过程中激发的电化学防腐蚀性能,二者协同作用形成智能防腐蚀机制。
免责声明:本网站所转载的文字、图片与视频资料版权归原创作者所有,如果涉及侵权,请第一时间联系本网删除。
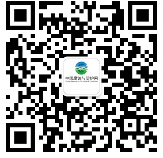
官方微信
《腐蚀与防护网电子期刊》征订启事
- 投稿联系:编辑部
- 电话:010-62316606
- 邮箱:fsfhzy666@163.com
- 腐蚀与防护网官方QQ群:140808414