碳捕集、利用与封存(CCUS)是实现国家双碳目标的重要途径。然而,CO2溶于水时存在强腐蚀性,输送、储存以及服役环境中金属材料的腐蚀问题不容忽视。尤其是在地下高温、高压、高矿化度的环境中,CO2呈超临界态,会对油套管造成严重腐蚀,从而影响油井的安全运行[1]。
一般情况下,超临界CO2环境中H2O的含量大于气态CO2环境中的,这使得金属表面积累了更多的H2O,碳钢腐蚀更加严重[2]。压力也会影响CO2在H2O中的溶解度,进而影响腐蚀产物的形成,改变腐蚀速率[3]。当致密的腐蚀产物层黏附在金属表面时,CO2腐蚀速率会显著降低[4-5]。在超临界CO2环境中,腐蚀产物层的形成过程和组成非常复杂,如在有CO2和水存在,无氧的情况下腐蚀产物主要成分是FeCO3。高矿化度水溶液中Ca2+、Mg2+等阳离子的存在也会影响水垢的组成,形成混合碳酸盐,从而影响腐蚀产物层的保护性能[6-7]。
根据形成动力学、形态、微观结构和化学成分以及其他性能,CO2腐蚀产物层可以为金属提供不同程度的保护[8]。目前大多数研究都集中在低分压CO2腐蚀机理及其影响因素等方面,温度、CO2分压和含水量对CO2腐蚀机理的影响也比较清楚[9]。在高CO2分压的地下环境中,腐蚀行为和机理会有所不同[10]。而且,注入气源、注入压力、不同位置的温度和压力不同以及腐蚀介质差异都会影响管道的腐蚀行为。因此,笔者以N80油套管钢为研究对象,通过模拟腐蚀试验和电化学测试,分析了其在CO2驱油的腐蚀环境(温度81.7℃、压力52.3 MPa)中的腐蚀行为,以期为CCUS工程的防腐蚀提供参考。
1. 试验
通过分析纯和去离子水配制模拟地层水溶液(CaCl2型),离子质量浓度分别为Ca2+ 1 046 mg/L,Mg2+ 183 mg/L,Na+ 14 357 mg/L,K+ 250 mg/L,Fe2+ 6.8 mg/L,Cl- 22 434 mg/L, 858 mg/L。通过冰醋酸和氨水调节溶液pH为7。试验装置如图1所示。试验前在高温高压反应釜内持续通入纯度为99.999%的CO2,以除掉模拟溶液中的其他气体杂质。试验时,持续通入CO2直至达到地层模拟压力,通过热电偶控制反应釜内的温度,通过旋转电动机形成转速来模拟CO2注入流速。选取现场CO2驱油区域井下相关参数开展试验,其中温度为81.7 ℃,压力为52.3 MPa,注入流速为4.7 m/s,此时井下CO2为超临界流体。
试验套管材料为N80钢,化学成分(质量分数)分别为C 0.36%,Si 0.31%,Mn 1.64%,P 0.01%,S 0.012%,V 0.12%。试验前,使用丙酮、去离子水和无水乙醇依次清洗材料后风干保存。将材料切割成尺寸为25 mm×25 mm×3 mm试样,通过800~1 200号防水砂纸依次打磨后抛光处理。
在高温高压反应釜中,等角度悬挂6个平行试样,试验周期设置为200,400,600,800,1 000 h。在每个测试周期取出试样,其中两个试样通过标准除锈液除掉表面腐蚀产物后进行质量损失测试,并通过三维显微镜观察表面形貌和测试最大蚀坑深度,计算点蚀速率。另外4个试样中,清除其中两个试样表面的腐蚀产物,与未清除腐蚀产物的试样做对比,通过电化学装置进行电化学测试,测量其开路电位EOCP、电化学阻抗谱(EIS)和极化曲线。测试采用三电极体系,N80钢试样为工作电极,饱和甘汞电极(SCE)为参比电极,Pt电极为辅助电极。极化曲线扫描电位区间为±250 mV(相对于开路电位),扫描速率为0.1 mV/s;电化学阻抗谱测试频率范围为10-2~105 Hz,电压为5 mV。在电化学测试装置中,试验溶液为模拟地层水溶液,持续通入CO2保证环境压力为52.3 MPa,温度为81.7 ℃,与高温高压反应釜环境相同。
2. 结果与讨论
2.1 模拟腐蚀试验
2.1.1 腐蚀速率
由图2可见:随着试验时间的增加,全面腐蚀速率和点蚀速率均呈现增大的趋势,并且点蚀速率大于全面腐蚀速率,尤其是在200 h时;此外,随着试验时间的增加,全面腐蚀速率增长趋势变缓,表现为对数变化趋势(R2=0.997),而点蚀速率一直处于较高水平,但是在试验时间为1 000 h时,点蚀速率迅速增大至1.782 mm/a,增长幅度达到了21.2%,远大于之前的增长幅度(<10%),说明此时点蚀显著加剧。
2.1.2 腐蚀形貌
如图3所示的左图:去除腐蚀产物后,在不同的试验时间条件下,试样表面均存在明显的点蚀坑,但是在试验前期(200 h和400 h),点蚀坑数量较少,尺寸较小;随着时间的增加,蚀坑的数量和深度均显著增加,尤其是在试验时间为1 000 h时,试样表面存在大量轮廓清晰的蚀坑,点蚀的严重程度远大于800 h时。
如图3所示的右图:去除腐蚀产物前,在试验前期(200 h),试样表面主要形成相对致密的黄褐色FeCO3腐蚀产物;随着时间的延长,试样表面腐蚀产物发生部分剥离,表面存在大量凸起,这成为了蚀坑发展的起始点,随后大量蚀坑萌生、发展,试样表面的FeCO3层被破坏,逐渐暴露出存在大量蚀坑的N80钢基体。推测其原因可能主要包含以下几个方面:(1)N80钢中含有一定量的Cr,形成的少量非晶态CrO3破坏了致密腐蚀产物层的完整性,产生了失效位点,Fe2+和Ca2+形成的复盐也有相同的作用[11-13];(2)在高矿化度地下水环境中,Cl-质量浓度高达22 434 mg/L,这对FeCO3产物层的破坏是致命的[12,14]。
由图4可见:在试验时间为200 h时,试样表面仅存在较少的蚀坑(红色)和局部腐蚀区域(黄色),随着时间的延长,试样表面的蚀坑大面积发展,蚀坑连接导致腐蚀面积增大,尤其当试验时间大于800 h时,试样表面的腐蚀形貌特征由点蚀逐渐转向全面腐蚀,这一现象在试验为1 000 h时非常明显。
2.2 电化学试验
2.2.1 开路电位
由图5可见,在开路电位测试时间范围(0~300 s)内,开路电位的波动几乎可以忽略不计,这说明在稳态条件下,整个体系处于平衡状态。取开路电位平均值开展分析,结果表明:随着模拟腐蚀试验时间的延长,带腐蚀产物和不带腐蚀产物的试样的开路电位均发生负移,负移幅度逐渐放缓,这说明随着时间的延长,腐蚀倾向性提高。此外,在相同的试验时间下,带腐蚀产物试样的开路电位略正于不带腐蚀产物试样,这说明表面的FeCO3产物层具有减缓腐蚀的作用。
2.2.2 极化曲线
由图6和图7可见:在不同试验时间条件下,有、无腐蚀产物试样的极化曲线特征均表现为活化腐蚀特性,即使试样表面存在难以脱落的FeCO3腐蚀产物层,极化曲线也没有表现出钝化特征;在试验时间逐渐增加的情况下,两种试样的腐蚀电流密度均增大,与不带腐蚀产物的试样的腐蚀电流密度Jcorr缓慢增大的变化趋势相比,在0~800 h,带腐蚀产物的试样的Jcorr小于不带腐蚀产物的试样,但当时间增加到1 000 h时,带腐蚀产物的试样的Jcorr由36.99 μA/cm2(800 h)瞬间增大到67.53 μA/cm2(1 000 h)。带腐蚀产物的试样的Jcorr的变化规律与全面腐蚀速率趋势相吻合,而不带腐蚀产物的试样的Jcorr与点蚀速率变化趋势相吻合。这说明对于裸露的N80钢来说,在地下高矿化度超临界CO2环境中的腐蚀形式主要为全面腐蚀,但是表面沉积腐蚀产物后逐渐转变为点蚀,并且点蚀电流密度约为全面腐蚀电流密度的1.56倍(1 000 h)。上述结果可以通过阳/阴极Tafel斜率比值r=βa/βc证实。随着试验时间的增加,r>1且不断增大,表明两者的腐蚀反应过程受到阳极过程控制,同时阳极极化程度增大;而在相同的试验时间条件下,在0~800 h时带腐蚀产物试样的r略小于不带腐蚀产物试样,而在1 000 h时,带腐蚀产物试样的r大于不带腐蚀产物试样,这与腐蚀电流密度的变化规律相吻合,说明此时带腐蚀产物试样的阳极过程更为剧烈。
2.2.3 电化学阻抗谱
由图8可见:两种试样的Nyquist图都呈现单容抗弧特征,且实部阻抗半径均远大于虚部容抗半径,说明在高矿化度的超临界CO2环境中,N80钢主要表现为电阻特征,即形成的腐蚀产物层具有一定的保护作用;但是在相位角-频率曲线的中频区存在两个明显的相位角峰值,当试验时间为1 000 h时,两个峰值特征逐渐消失。因此,选择Rs(Q(RpCdlRct)))进行拟合,其中Rs为溶液电阻,Q为常相位角元件(用Y0和弥散指数n表示),Rp为腐蚀产物膜层极化电阻,Cdl为双电层电容,Rct为电荷转移电阻,拟合结果如图9所示。
在试验时间为200 h时,带腐蚀产物试样的阻抗半径大于不带腐蚀产物试样,但随着时间的延长,两者的阻抗半径迅速减小,并且前者的减小速率大于后者,但是在时间达到1 000 h时,两者的阻抗半径基本相等,具体表现为电荷转移电阻随着试验时间的增大而逐渐减小,最后趋于一致,说明此时两种试样表面的腐蚀产物几乎没有保护作用。
在相位角-频率曲线中,带腐蚀产物试样的两个相位角峰值均随着时间的延长而逐渐向低频方向移动,而在时间为1 000 h时,明显的相位角峰值已经消失,取而代之的是在0.16~72.79 Hz的平台特征,平均峰值相位角为52.20°。不带腐蚀产物试样的两个相位角峰值频率在0~800 h时基本保持不变,但在1 000 h时变为一个特征峰值,为55.35°,与带腐蚀产物试样的相位角峰值基本相等,说明两者此时的表面反应过程基本一致。但不同的是,在低频位置(10-2 Hz),试验时间为800 h和1 000 h时带腐蚀产物试样的相位角为负值,说明此时表面腐蚀产物的生成与破裂的过程较为剧烈,表现为较大的双电层电容(Cdl = 2.71×10-4 F·cm-2,1 000 h)现象。
3. 结论
(1)N80钢的腐蚀速率随着试验时间的延长而增大,尤其是当试验时间由800 h增长至1 000 h时,点蚀速率由1.470 mm/a增大至1.782 mm/a。结合腐蚀形貌分析可以发现,初始时刻N80钢表面的腐蚀产物层具有一定的保护作用,随着时间的延长,腐蚀产物层破裂形成失效位点,蚀坑萌生并逐渐发展,这可能是非晶态CrO3、Fe2+/Ca2+复盐和Cl-共同作用的结果。
(2)与不带腐蚀产物试样的腐蚀电流密度缓慢增大的变化趋势相比,在0~800 h,带腐蚀产物试样的腐蚀电流密度小于不带腐蚀产物试样,但当时间由800 h延长至1 000 h时,带腐蚀产物试样的腐蚀电流密度由36.99 μA/cm2瞬间增大到67.53 μA/cm2,且Tafel常数比值呈现相同的变化特点,这与点蚀速率的变化特点一致。电化学阻抗谱分析结果表明,随着模拟腐蚀试验时间的增大,电荷转移电阻减小,腐蚀产物层的保护作用逐渐消失,时间常数由两个变为一个,并且有无腐蚀产物试样的相位角峰值基本相等,低频相位角特征说明带腐蚀产物层试样的表面腐蚀产物的生成与破裂过程更为剧烈。
免责声明:本网站所转载的文字、图片与视频资料版权归原创作者所有,如果涉及侵权,请第一时间联系本网删除。
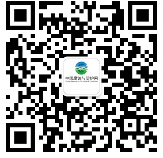
官方微信
《腐蚀与防护网电子期刊》征订启事
- 投稿联系:编辑部
- 电话:010-62316606
- 邮箱:fsfhzy666@163.com
- 腐蚀与防护网官方QQ群:140808414