元素 | C | Mn | S | P | Si | Al |
---|---|---|---|---|---|---|
质量分数/% | 0.076 | 0.45 | 0.008 | 0.015 | 0.026 | 0.033 |
为了减少资源消耗和缓解日益严重的环境污染问题,需开发更薄且耐蚀性更好的镀层,并使用更环保的物理气相沉积(PVD)工艺[1-5]。20世纪末,锌铝镁镀层钢板得到快速发展,目前已有7种不同成分的锌铝镁镀层钢板实现了商业化生产。
许多研究者对锌铝镁镀层的耐蚀性进行了研究,在汽车和屋顶的应用中[4-9],在镀锌层中添加适量的镁和铝可以有效提高镀层的耐蚀性和自愈性,从而减少锌的消耗。同时,与纯锌镀层相比,Zn-Mg合金镀层中的腐蚀电流也显著降低[6]。然而,通过长期(10 a)大气腐蚀试验发现,涂层中需要大量的Mg,至少0.04%(质量分数)Mg才能提高其耐蚀性[10]。相反,当镁质量分数超过8%时,Zn-Mg合金镀层的质量损失量会超过纯锌镀层[11]。一些作者提出Mg有利于形成作为阴极抑制剂的腐蚀产物[Zn5(OH)8Cl2·H2O、MgO和Mg(OH)2],同时防止形成非保护性腐蚀产物ZnO[6,11-14]。研究还表明,在锌的腐蚀产物下会形成富镁膜[11]。RYOUNG等[15]通过循环腐蚀试验(CCT,参考ISO14993和通用汽车标准GMW14872),对比研究热浸镀锌GI、PosMAC1.5和PosMAC3.0三种镀层出现红锈的时间。结果表明,当镀层厚度相同时,PosMAC1.5镀层的耐蚀性是GI镀层的4.2倍,PosMAC3.0镀层的耐蚀性是GI镀层的9.2倍。李锋等[16]研究了锌铝镁镀层在NaCl体系中的腐蚀行为。结果表明,锌铝镁镀层的耐蚀性约为热浸镀锌GI镀层的6倍,铝、镁的存在降低了锌的溶解速率和溶解氧的扩散速率,阴极区氧还原速率降低,从而合金镀层的耐蚀性提高。袁训华等[17]研究了锌铝镁镀层钢板的腐蚀行为,认为镀层中的共晶相使Mg元素在镀层中均匀分布,从而抑制阴极反应;镀层腐蚀后形成的Zn5(OH)8Cl2·H2O和Zn6Al2(OH)16CO3·4H2O是不溶性的胶状腐蚀产物,可以有效隔绝镀层与外界物质间的电子传输。
与传统热浸镀锌加工过程相比,锌铝镁材料加工过程更加简单高效,成本更低,但是存在成型部位镀层开裂和钢基材边缘暴露的风险。锌铝镁材料多用于公路护栏、光伏支架、货架等,导轨连接部分材料的切口直接裸露在大气环境中,这些都将对材料使用时的切边保护性能提出挑战。还有学者对比研究了Zn-6%Al-3%Mg合金镀层钢板和热浸镀锌钢板在加速CCT(JIS H 8502)后和实际车辆环境中的耐蚀性能,发现即使是在钢板裸露的地方(切口、折弯和点焊)Zn-6%Al-3%Mg也比热浸镀锌表现出更好的耐蚀性。杨忠等[18]对比研究了锌铝镁与热浸镀锌切口部位在加速腐蚀试验(GB/T 1771-2007)中出现红锈的时间,发现热浸镀锌切口从96 h开始出现红锈,锌铝镁切口从336 h开始出现红锈。
上述研究成果对热镀锌铝镁镀层的耐蚀性进行了评价,从腐蚀产物的形成机理、损伤后镀层的防护机理等方面说明了热镀锌铝镁镀层具有良好耐蚀性,对比了锌铝镁和热浸镀锌在切口位置的耐蚀性差异,但是没有深入研究镀层切口处腐蚀产物的组织特征和影响切口耐蚀性的因素。因此,笔者采用激光切割将不同厚度的锌铝镁镀层钢板加工成不同内外径的圆环形试样,以获得不同的切口与镀层面积比值,通过中性盐雾试验、扫描电镜(SEM)和X射线衍射(XRD)对其耐蚀性和腐蚀产物进行观察分析,确定了锌铝镁镀层切口的组织特征、腐蚀产物物相组成及其耐蚀性。
1. 试验
1.1 试样
试验用锌铝镁镀层钢板基板材料为S350GD,成分如表1所示。锌铝镁镀层名义成分为Zn-6%Al-3%Mg,镀层为双面镀锌275 g/m2,通过激光切割加工成圆环形状试样。尺寸如下:外径3 cm,内径分别为2.5,2,1.5 cm;外径5 cm,内径分别为4,3,2 cm。板材厚度分别为2,3,5,6 mm。
1.2 试验方法
切口腐蚀试验在Q-Fog中性盐雾实验箱中进行,按照ASTM B117-2019《盐雾试验仪的标准操作规程》进行加速腐蚀试验。试验条件如下:温度35 ℃,湿度100%,pH为7,NaCl质量浓度为50 g/L,盐雾沉降量为1.28 mL/h,去离子水电导率为12 μS/cm,切口耐蚀性用600 h中性盐雾试验后的切口红锈面积比衡量。
用HITACHI S-3400N Ⅱ型扫描电镜观察镀层的表面和切口形貌,加速电压为15 kV。采用德国布鲁克公司的D8 advance X型射线衍射仪[Co靶,电压35 kV,电流40 mA,步长0.03°,扫描速率2(°)/min]分析不同腐蚀程度腐蚀产物的物相。
2. 结果与讨论
2.1 镀层表面及切口形貌
由图1可见:锌铝镁镀层表面钝化膜较厚,覆盖完整;镀层切口存在三种不同的组织,粗大的灰色块状组织为Zn的初生相,较小的块状组织为Al的初生相,网状共晶组织是Zn-MgZn2二元共晶和Zn-Al-MgZn2三元共晶。
2.2 腐蚀产物形貌及物相
由图2可见:中性盐雾试验后,锌铝镁镀层钢板表面呈现出不同的腐蚀形貌;未发生明显腐蚀的部位,腐蚀轻微,形貌较为平整,有少许裂纹;白色锈蚀部位,产物较为整齐致密;腐蚀严重区域为红色锈蚀,产物蓬松,可见絮状物,且内部有明显的孔隙和裂纹。
分别对镀层未明显腐蚀、白锈和红锈部位进行XRD分析,结果如图3所示。未明显腐蚀区域的相组成为Fe、Zn、和MgZn2,共晶相为Zn-MgZn2二元共晶;白锈产物主要由氧化锌(ZnO)和氯水锌矿[Zn5(OH)8Cl2·H2O]等构成。[Zn5(OH)8Cl2·H2O]是不溶性的胶状物质,有效阻隔了镀层与外界物质的传输,增强了锌铝镁镀层的耐蚀性能;红锈产物主要由Fe、FeO、β-Fe2O3、Fe(OH)3等构成。
2.3 切口耐蚀性
同样的材料,相同的腐蚀环境和腐蚀时间,材料的形状对切口腐蚀状态有着很大的影响。如图4所示,随着切口和镀层面积比值的增大,试样切口的红锈面积逐渐增大,且当切口与镀层面积比值小于0.5时,切口的耐蚀性较好。
切口可以看做是一个可以进行腐蚀过程的金属材料M1(锌铝镁镀层)同电极电位较高的金属M2(钢基体)接触,接触后M1的腐蚀破坏速率增大。这种现象叫接触腐蚀,也称电偶腐蚀。M1的阳极溶解反应的过电位在其与M2接触后增大,M2的阳极溶解反应的过电位在其与M1接触后减小,表明这种接触使M2的阳极溶解反应速率(腐蚀速率)减小,即阴极保护效应。
若M1与溶液接触的面积为A1,M2与溶液接触的面积为A2,这一腐蚀原电池的外电路中的电流ig可通过式(1)计算。
|
(1) |
M1与M2电接触后的阳极溶解电流密度为Ig,故M1的阳极溶解电流密度为I1=Ig=ig/A1。
由式(2)可见,影响M1的阳极溶解电流密度I1的影响因素除Ecorr2-Ecorr1、βa1+βc2、Icorr1及Icorr2外,还有A2/A1,这个比值越大,I1值就越大[19]。本文研究的结论与两种互相接触的金属面积和一些动力学参数对接触腐蚀效应的影响规律是一致的。
|
(2) |
式中:Ecorr1为金属材料M1的腐蚀电位;Ecorr2为金属材料M2的腐蚀电位;βa1为阳极反应在较低过电势区域的Tafel斜率;βc2为阴极反应在较高过电势区域的Tafel斜率;Icorr1为金属材料M1的腐蚀电流密度;Icorr2为金属材料M2的腐蚀电流密度。
切口的自愈机制如图5所示。如图5(a)所示,在腐蚀初期,切口的所有表面都具有电化学活性,Al或Mg的加入均能使镀层的平衡电位负移,增加镀层热力学腐蚀趋势,MgZn2会优先溶解,一部分Mg从镀层表面溶解形成Zn的腐蚀产物,钢表面的氧还原被镀层溶解所抵消。
如图5(b)所示,由于pH升高应从钢与电解质界面开始,表面成核应占主导地位,因此在靠近镀层的钢基体表面会形成一层薄薄的锌基氧化膜,可防止该区域电解液的pH升高;反之,在远离镀层的区域,溶液中没有Zn2+、Mg2+,不会产生沉淀,pH升高;由于薄膜绝缘,会降低镀层的溶解速率。
如图5(c)所示,腐蚀继续进行,直到远离镀层的溶液中锌的腐蚀产物,尤其是Zn(OH)2的溶度积达到饱和,从而发生沉淀,并且在表面积累形成一条可见的沉淀物线。如图5(d)所示。随着时间的推移,沉淀物在新形成的线之外积累,由于它们的生长,没有Zn2+、Mg2+可以到达沉淀物线之外的钢表面,从而阻止了该区域形成锌基氧化膜。在镀层和和沉淀物线之间,由于pH不高,不会产生大量白色沉淀。在这部分钢上,锌离子的水解将pH控制在略低于中性值的范围[20]。因此,当A2增加时,未能被白锈覆盖的面积随之增加[21]。这也与本文结论一致,即当切口与镀层面积比值较小时,切口耐红锈能力较好。
3. 结论
(1)在中性盐雾环境中,锌铝镁镀层钢板的腐蚀产物主要是碱式碳酸锌[Zn4CO3(OH)6·H2O],Al3+和Mg2+的存在使纯锌相的面积减小,同时使碱式碳酸锌变得稳定,不易形成疏松的ZnO,并形成不溶的胶状物质氯水锌矿[Zn5(OH)8Cl2·H2O],阻隔切口与外界的物质传输,在动力学上增加了腐蚀阻力,保护切口不受进一步腐蚀。
(2)镀层未发生明显腐蚀区域的相组成为Fe、Zn、MgZn2和Zn-MgZn2的二元共晶。腐蚀后白锈产物主要为ZnO和氯水锌矿[Zn5(OH)8Cl2·H2O]等;红锈产物主要为Fe、FeO、β-Fe2O3、Fe(OH)3等。
(3)材料的形状对切口腐蚀状态有很大影响。当切口与镀层面积比值小于0.5时,切口耐红锈能力较好;随着该比值的增大,试样切口的红锈面积逐渐增大。
免责声明:本网站所转载的文字、图片与视频资料版权归原创作者所有,如果涉及侵权,请第一时间联系本网删除。
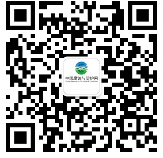
官方微信
《腐蚀与防护网电子期刊》征订启事
- 投稿联系:编辑部
- 电话:010-62316606
- 邮箱:fsfhzy666@163.com
- 腐蚀与防护网官方QQ群:140808414