
随着电网技术的不断发展,输电线路容量和输电距离的不断增加,对输电塔钢结构的可靠性和使用寿命的要求也越来越高[1-2]。作为输电线路的骨架,输电塔通常架设在各种自然环境中,会遭受到不同程度的腐蚀破坏[3]。一旦输电塔被腐蚀,其承载能力将大大降低,这会严重影响输电线路的安全稳定运行。因此,采取一定的防护技术来延长输电塔的使用寿命对于输电安全具有重要意义。
现阶段输电塔主要材料还是以低合金高强度钢和热轧低碳钢结构为主,各个钢结构部件通过焊接、螺栓等方式组合而成[4]。当介质(水、空气、二氧化硫等)作用于输电塔钢结构表面时就会发生腐蚀[5]。大部分输电塔腐蚀形式为局部腐蚀,少部分存在整塔腐蚀的情况[6]。局部腐蚀一般发生在一些特殊部位,如输电塔塔脚处、焊接处等。一般塔脚所处位置的空气比较潮湿,且SO2浓度较高,因此腐蚀速率会大大高于纯空气中,塔脚钢结构一般在1~2 a内就会减薄50%左右[7-8]。但是,在恶劣环境(如沿海高湿高盐环境、工业重污染区等)中输电塔会发生整塔腐蚀。
根据腐蚀介质、钢材腐蚀类型以及地质和气候条件的不同,一般采用钢材改性处理、热镀锌涂层、电镀涂层、涂装防腐蚀涂料等方法对输电塔进行防护。笔者对目前输电塔的腐蚀类型和输电塔腐蚀监测技术进行了概述,介绍了不同防腐蚀技术原理、使用过程和发展现状,并对输电塔的防腐蚀技术进行了总结和展望。
1. 输电塔腐蚀类型
随着输电容量的提升以及电力输送距离不断增长,“跨越高速公路、高速铁路、重要输电通道(三跨)”产生的安全问题也随之增加[9-11]。输电塔常见的腐蚀类型主要有表面腐蚀、节点腐蚀、底部腐蚀等。表面腐蚀可分为化学腐蚀、大气腐蚀、颗粒侵蚀等;节点腐蚀主要发生在输电塔的连接节点处,如焊接点、螺栓连接处等容易受到环境湿度、氧气含量等影响的位置;输电塔底部处于湿度较高的土壤环境,特别是在有盐分或化学物质的土壤中,易发生底部腐蚀。塔材锈蚀逐年积累造成倒塔隐患,这会对架空输电线路交叉跨越造成极大威胁,工业城市、沿海地区的这一问题尤为突出,因此对输电塔锈蚀程度的监测与控制尤为重要[12-13]。
2. 输电塔腐蚀检测技术
现阶段输电塔腐蚀检测方式主要有目视检查、人工勘察、腐蚀探伤、遥感监测等。目视检查主要是通过巡视或使用望远镜等工具对输电塔表面的氧化、锈蚀、剥落等腐蚀迹象;人工勘察一般使用便携式测量仪器,如电位差计或电化学腐蚀监测仪直接测量铁塔表面的电位或电流密度,以评估腐蚀程度;腐蚀探伤则使用超声波、磁粉探伤、涡流探伤等非破坏性检测技术,对铁塔的金属结构进行扫描,以检测隐蔽的腐蚀或金属缺陷。KANG等[14]利用激光超声导波对钢结构缺陷进行检测和实现可视化,主要通过激光照射使得钢结构表面温度突然上升,后续热能通过绝热膨胀以弹性能的形式在物体内部传播,而这种热弹性波可由压电传感器获取,它在超声波领域很敏感。若钢结构背面有缺陷,超声波传播的图像在缺陷区域将被扭曲,因此可以很容易在可视化图像中检测到缺陷。遥感监测是利用遥感技术,如卫星遥感或无人机航拍,获取高分辨率的输电塔图像,接着通过图像处理和分析,可以观测到表面腐蚀迹象,起到监测铁塔的腐蚀状况的目的。HAN等[15]提出了一种腐蚀图像检测方法,包括超像素分割、神经网络识别和腐蚀区域定位三个步骤。结果表明,两阶段检测方法可以获得腐蚀区域的比例和相对结构位置,所提出的方法可以通过与无人机的集成来促进钢结构沿线早期全面的腐蚀检测。无人机图像识别虽然可以监测输电塔钢结构外层的腐蚀状况,但不能识别内部缺陷,因此未来可以利用无人机搭载监测装置(一体化内外识别装置)来实现更加全面的监测。通过建立腐蚀监测数据库,记录铁塔腐蚀监测数据,进行分析和趋势预测,为后续的防腐蚀措施提供理论支撑。
3. 输电塔防腐蚀技术
3.1 钢材改性处理
钢材改性处理方法一般指钢的合金化,即在冶炼过程中加入Cu、Cr、Ni等金属元素制备得到耐候钢,以增强其对大气环境的抵抗力[16-17]。耐候钢Cor-Ten包括Cor-Ten A(Cu、P、Cr、Ni合金化)系列和Cor-Ten B(Cr、Mn、Cu合金化)系列[18]。耐候钢具有组织稳定,力学性能优异的特点,与普碳钢相比,其冲击性能大幅提高,从而杆塔的耐低温性能提高。在长期服役过程中,锈层的保护实现了耐候钢的防腐蚀免维护[19-20]。张瑞琦等[21]研究了4种不同Cr、Ni、Cu元素含量的输电塔用耐候钢在模拟海洋大气环境以及工业大气环境中的耐蚀性。结果显示,4种耐候钢的耐蚀性均优于Q345B钢,当Cr质量分数小于1.0%时,随着Cr含量的增加,耐候钢的耐蚀性没有实质性变化。罗义华等[22]研究了P质量分数(0.20%~0.39%)对耐候钢显微组织、力学性能以及耐蚀性的影响。结果表明,在一定含量范围内,P含量变化对该钢显微组织和力学性能影响均较小,P含量增加会增加D类球状氧化物。通常情况下,P含量增加会降低钢的低温性能,特别是温度低于-40 ℃时,其对冲击功影响更大。当钢中P质量分数为0.028%时,输电塔用耐候钢具有最佳的耐蚀性,室内加速腐蚀试样的锈层厚度约为10 μm。因为耐候钢在大气中能形成致密和黏附良好的稳定锈层,所以其耐蚀性比普通碳钢更好,将耐候钢应用于输电塔是未来防腐蚀技术的重要发展方向。
3.2 热镀锌涂层
热镀锌是将钢及其制品浸入熔融金属中形成金属镀层的一种方法[23]。涂层材料的熔点比基体低得多,高温下涂层会与基体反应形成冶金结合,使得涂层具有更好的耐蚀性[24]。经过近200 a的发展,热镀锌技术和其设备也日趋完善并已成为了重要的防腐蚀技术。王邦林等[25]以镀锌层厚度和最高硬度为指标,通过正交试验对钢质件的热浸镀锌工艺进行优化。结果表明,当镀前烘干温度为80 ℃,烘干时间为3 min,镀锌温度为440 ℃,镀锌时间为4 min时,镀锌层厚度可达138.2 μm,最高硬度为263 HV,耐腐蚀性能良好。但由于越来越多复杂工况的出现,单一的热镀锌涂层已不能适应高强度的腐蚀环境,为了提高镀层在海洋、工业大气环境等特殊情况下的耐蚀性,人们对镀层合金化进行了大量研究。20世纪80年代中期,日本钢铁研究中心研制出SuperZinc合金镀层,即在锌液中加入适量Al和Mg后形成Zn-Al-Mg复合镀层,测得其耐蚀性远远高于纯镀锌层。研究发现,将稀土元素掺入Zn-Al-Mg镀层中可进一步提升镀层的耐蚀性。HAN等[26]在Zn-Al-Mg涂层中添加不同含量的稀土La和Ce,并分析了Zn-Al-Mg-Re复合镀层的相结构,采用铜带乙酸加速盐雾试验评价了Zn-Al-Mg-Re复合镀层的耐蚀性。结果表明:掺杂La和Ce有利于生成新相如LaAl3或Al11Ce3和细化其晶粒,从而显著提高镀层的耐蚀性;经168 h铜带乙酸加速盐雾试验后Zn-Al-Mg-Re镀层仍未被腐蚀。
3.3 热喷涂涂层
由于热喷涂技术能够制备具有优异结合强度、高密度和低氧化物含量的涂层,因此该技术得到广泛应用[27]。在热喷涂过程中,金属、陶瓷和一些呈线、棒或粉末状的聚合材料被送入一个腔室、喷灯或喷枪中,在接近或高于其熔点的温度下加热,然后在基体表面加速沉积涂层,示意图如图1所示。GRINON-ECHANIZ等[28]在钢基体表面通过热喷涂技术制备了厚300 μm的Zn-15Al涂层,5%的表面缺陷被人工加工以暴露钢基体。结果显示,海水加速腐蚀试验6个月后涂层还未被腐蚀,表现出良好的耐蚀性。CHEN等[29]采用超声速电弧喷涂技术在喷丸处理后的Q345B钢表面制备了Al涂层和Al-Zn涂层,并分析了两种涂层的表面形貌、涂层结构和相组成。结果表明:两种涂层的厚度均为100 μm,在试验参数条件下,Al涂层和Al-Zn涂层的抗滑移系数分别为0.717和0.823,满足钢结构的服役要求,且表现出良好的防腐蚀性能;在水介质条件下,Al-Zn涂层的抗磨特性较为理想。
3.4 电镀涂层
电镀是将工件(阴极)和镀层金属(阳极)放入电解液中,镀层金属在直流电的作用下会沉积在工件表面[30],是制备金属镀层最经济、最常用的技术之一。ANWAR等[31]采用含柠檬酸盐浴的镀液在钢基体表面电沉积Zn和Zn-Ni镀层,并系统研究了镀液组成和电流密度等电镀参数对镀层相组成、耐蚀性的影响。结果显示:在Zn-Ni镀层的相结构中,γ相(γ-NiZn3)(815)的强度最高,γ-Ni2Zn11(330)(631)平面取向且表现出较好的耐蚀性;与Zn镀层相比,Zn-Ni镀层具有更低的腐蚀电流密度和更正的腐蚀电位。BHAT等[32]以水杨酸和明胶为添加剂,制备了一种稳定的氯化物镀液,并在低碳钢表面制备了Zn-Ni-Fe合金镀层。结果显示,该镀层在40 mA/cm2电流密度下的腐蚀速率最小,当Ni质量分数为19.61%, Fe质量分数为5.70%时,镀层的腐蚀速率较低,为26.4 μm/a。电镀涂层可以改善材料的表面特性,但涂层与基体之间的结合不是冶金结合,如果前处理不当,镀层可能产生脱落或起泡,且电镀过程中使用的化学品和重金属可能会造成环境污染,需要严格管理废水和废物。
3.5 涂装防腐蚀涂料
输电塔用钢在出厂前一般都会进行热浸镀锌处理以提高其防腐蚀性能,但热镀锌涂层厚度容易出现不均匀现象。特别是在南方和沿海城市,环境中的酸性气体和较高的盐度和水分含量均会加速镀锌层的消耗。目前,提高输电塔耐蚀性的方法主要有增加热镀锌层厚度和涂覆防腐蚀涂层。与增加热浸镀锌厚度的方法相比,涂覆防腐蚀涂层的工艺更简单,再涂覆技术难度更小,成本也相对较低[33]。ZHANG等[34]通过添加石墨烯和α-氧化铝,基于分步涂覆法设计了交替多层结构的多功能环氧树脂复合涂层。结果表明:当填料质量分数从0增加到0.15%时,该涂层的韧性和导热系数明显增加,而介电性能几乎为0;整个腐蚀过程受电化学反应控制,具有交替结构的填料有效阻隔了腐蚀介质,提高了复合涂层的耐蚀性。水性防腐蚀涂料耐水性差,容易导致涂层劣化和金属腐蚀。为了提高水性涂料的耐水性,ZHANG等[35]采用逐层施工法制备了聚四氟乙烯/二甲基硅氧烷/环氧树脂(PTFE/PDMS/EP)疏水防腐蚀涂料。结果显示:PTFE/PDMS/EP涂层的水接触角可达到141°,其防护效率高达98.62%;浸泡7 d后,腐蚀过程仍停留在初始阶段,这主要是由于PTFE/PDMS/EP涂层良好的密封性和阻隔性以及较高的防腐蚀效率。宁亮等[36]利用改性自制环氧固化剂,采用环氧树脂作为底漆,丙烯酸作为面漆,制备了一种高耐候长寿命防腐蚀涂料。结果显示,在残留少量浮锈、轻微潮湿或不明显油渍的基体表面仍可涂装使用,经酸/碱/盐溶液浸泡、人工加速老化、湿热、盐雾试验后,涂层外观无明显变化,附着力良好。
3.6 复合材料型输电塔
随着复合材料的快速发展,由于纤维(如玻璃纤维、碳纤维、超高分子量聚乙烯纤维等)增强复合材料具有质量轻、强度高、耐老化性能好、绝缘性能好等特点,被认为是未来传统输电塔的替代材料。ABU等[37]对玻璃纤维增强的输电横梁复合材料(GFRP)进行了耐久性评估。结果发现,与其他传统材料相比,GFRP具有更高的强度,耐蚀性,化学稳定性,以及在恶劣环境中的可持续使用能力,并可能延长使用寿命。GAO等[38]研究了输电塔用聚氨酯复合材料的老化性能,对其进行了5 000 h多因素加速老化试验。结果显示,老化试验后复合材料表面完好无损,无脆性、开裂、变形等现象。BHOWMIK等[39]根据碳纤维环氧复合材料塔架的现有设计方法进行建模分析,证实了复合材料塔架的可行性。庄开智[40]对复合材料杆塔与传统杆塔的经济适用性进行了对比分析,并以110 kV杆塔(带地线)为例进行造价分析。结果显示,复合材料杆塔在长远的运行维护、耐蚀性、经济性等方面占有优势。
4. 结束语
输电塔由于长期暴露在自然环境中,很容易发生化学、电化学等腐蚀。需使用较全面高效的监测手段,如采用无人机搭载内外层一体化测试装置对输电塔进行腐蚀监测。输电塔的防腐蚀方式主要有钢材改性处理、热镀锌涂层、热喷涂涂层、电镀涂层、涂装防腐蚀涂料、复合材料型输电塔等。随着电网设备精益管理的不断深入,电网企业也不断关注输电塔的全生命周期管理。
免责声明:本网站所转载的文字、图片与视频资料版权归原创作者所有,如果涉及侵权,请第一时间联系本网删除。
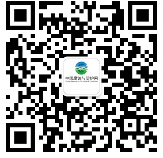
官方微信
《腐蚀与防护网电子期刊》征订启事
- 投稿联系:编辑部
- 电话:010-62316606
- 邮箱:fsfhzy666@163.com
- 腐蚀与防护网官方QQ群:140808414