区块编号 | pH | 密度/(g·cm-3) | 离子质量浓度/(mg·L-1) | 总矿化度/(mg·L-1) | 腐蚀速率/(mm·a-1) | ||||||
---|---|---|---|---|---|---|---|---|---|---|---|
K++Na+ | Ca2+ | Mg2+ | Cl- | ![]() |
![]() |
S2- | |||||
GS | 6.53 | 1.081 0 | 49 156 | 3 619 | 1 229 | 83 500 | 819 | 238 | 8 | 137 561 | 0.189 7 |
YJ | 6.95 | 1.060 0 | 75 527 | 978 | 393 | 118 051 | 1 307 | 558 | 10 | 393 633 | 0.203 5 |
JS1 | 6.37 | 1.085 0 | 46 313 | 4 532 | 1 931 | 80 788 | 843 | 209 | 6 | 133 096 | 0.162 8 |
KB | 6.95 | 1.028 7 | 7 982 | 410 | 92 | 24 901 | 1 068 | 116 | 12 | 45 892 | 0.074 9 |
WN | 7.32 | 1.042 6 | 24 052 | 1 134 | 196 | 38 868 | 810 | 345 | 34 | 65 404 | 0.282 5 |
HTG | 6.78 | 1.086 3 | 49 585 | 1 493 | 673 | 79 971 | 1 207 | 349 | 36 | 13 3278 | 0.342 8 |
西部某油田油水集输管道输送介质为含水原油和污水,其中含水原油输送管道运行温度为25~70 ℃,运行压力为0.1~2.5 MPa,污水输送管道运行温度为35~65 ℃,运行压力为2~32 MPa。管道材料主要为普通低碳钢,包括20号、20G、L245等。随着运行年限的增长,管道逐渐出现内腐蚀穿孔泄漏问题,这不仅严重影响了油田正常生产,还造成了较大的安全环保问题。
针对西部某油田集输管道内腐蚀问题,调研和分析了当前油气田管道主要的内腐蚀控制技术,开展了技术经济比选和现场试验及评价,确定了适用于该油田的金属集输管道内腐蚀控制策略。
1. 概况
1.1 腐蚀介质
水是导致油水集输管道腐蚀关键,分离前采出液含水率为15%~90%,管道含水率整体较高,给管道腐蚀创造了条件。同一区块不同油层和单井采出液成分存在差异,主要区块采出水(混合污水)的理化性质及腐蚀速率如表1所示。采出液pH为6.53~7.32,处于中性范围。Cl-质量浓度为24 910~118 051 mg/L,总矿化度为39 363~65 404 mg/L,采出液以CaCl2水型为主,部分单井采出液为MgCl2水型和Na2SO4水型。采出水特别是处理后污水普遍含硫,质量浓度为6~36 mg/L。根据硫酸盐还原菌(SRB)测试结果,污水及后续流程处理水中普遍含SRB,部分区块单井采出液含SRB,取样点SRB含量为20~300个/mL。采用腐蚀挂片装置对各区块介质的腐蚀性进行监测,大部分区块的装置为严重和极严重腐蚀程度,仅个别区块的装置腐蚀速率较低。
1.2 失效特征
管道失效形式为内部腐蚀穿孔[1],失效主要集中在管道中下部。管道内部特别是管道底部普遍存在垢质和泥沙沉积物,失效表现为垢下局部腐蚀穿孔。经X射线衍射(XRD)分析,腐蚀产物及沉积物主要成分为FeS, Fe2O3、FeOOH(铁的氧化物), CaCO3、BaSO4、SrSO4等(垢质)及SiO2(泥沙沉积物),典型腐蚀穿孔管道内外表面宏观形貌及腐蚀产物成分如图1所示。
1.3 失效影响因素
影响管道腐蚀的因素众多,主要包括含水率,Cl-质量浓度,S2-质量浓度和SRB含量,pH,矿化度及结垢,温度等,其对管道腐蚀影响如下。
(1)介质含水率:油田整体处于开发中后期,油水集输管道输送介质含水率普遍较高,油水分层及油水介质处于水包油状态,管道内壁可直接接触游离水介质,水不可避免对管道全线产生腐蚀[2]。
(2)Cl-质量浓度:油田采出水中Cl-质量浓度普遍较高,一般腐蚀速率会随着Cl-质量浓度升高而升高,Cl-对管道腐蚀起到加速作用[3-4]。
(3)S2-质量浓度和SRB含量:S2-来源一般有两个,一是部分油田埋藏较浅,其环境适于SRB繁殖,储层受注水影响导致SRB大量繁殖产生S2-,S2-随采出液进入管道;二是地面集输系统中,SRB大量繁殖,不断产生S2-。虽然采出水中SRB含量相对较低,但在垢下、死水区等位置SRB会聚集繁殖,浓度很高。S2-和SRB是导致管道腐蚀的直接因素[5-8]。
(4)pH:pH直接影响S2-对管道的腐蚀[9]。当pH较低时,H+会参与腐蚀反应,腐蚀速率大幅提高;当pH升高时,结垢的风险升高,甚至产生结垢堵管失效。另外,水处理工艺对采出液pH也有一定的要求。
(5)矿化度及结垢:采出水矿化度较高,在地面条件下,个别区块采出水甚至处于过饱和状态,需要掺淡水来防止采出水中盐类结晶析出堵管。一般认为,矿化度的升高会增大腐蚀速率[10],同时高矿化度伴随着高结垢风险。垢质对管道腐蚀具有明显影响,致密的垢质能够隔离腐蚀介质与管道内壁,保护管道,但疏松的垢质下会发生腐蚀,极大地提高管道腐蚀速率。
(6)温度:碳钢腐蚀速率与温度明显相关,油田集输管道运行温度处于高腐蚀速率温度范围内,且在工况温度范围内,腐蚀速率随温度升高而增大[11-12]。
2. 内腐蚀控制技术比选
2.1 内腐蚀控制技术
目前,主要的管道腐蚀防护技术如下。
(1)管道材料,如采用耐腐蚀合金钢、非金属管道或改变低碳钢结构等方法来提升管道耐蚀性。油田应用较多的耐蚀金属材料有不锈钢、镍基合金和双金属复合管等[13-14];非金属管道在油田中的应用也越来越广泛[15],主要有玻璃钢管、钢骨架聚乙烯管道、柔性复合管、热塑性塑料合金复合管等;抗硫钢等低碳钢主要通过改变管材组织结构来提升抗硫能力,一般与缓蚀剂配合用于含硫气田集输管道。
(2)对管输介质进行清洁,去除腐蚀介质等,从而降低管道腐蚀速率。如在含硫油气输送管道中添加脱硫剂,消除介质中的H2S[16]。同时,部分油田采用了生物竞争法[17-18]和加注杀菌剂[19]来降低输送介质中的SRB含量。
(3)添加化学药剂,如缓蚀剂、pH调节剂等,通过隔离腐蚀介质与管道接触[9]或改变介质腐蚀性来降低腐蚀速率。缓蚀剂、缓蚀阻垢剂在油气田集输系统中应用较广泛,具有较好的缓蚀效果[20-21]。pH调节剂在油田集输系统中应用较少,改变pH对结垢和污水处理影响较大,且会对集输系统产生其他不利影响。
(4)隔离保护,使用内涂层或内衬层隔离管道和腐蚀介质,避免管道腐蚀。隔离防护主要有金属镀层,内涂层和非金属内衬管等,目前油田应用较多的是内涂层[22-23]和非金属内衬管[24-25],均具有较好的防腐蚀作用。
2.2 经济性比选
在某油田WN区块和HTG区块已经开展了生物竞争法抑制SRB的试验和应用[17],取得了一定效果。但这只能有限降低污水处理后续流程中的S2-和SRB含量,同时随着激活剂的消耗,后续流程中仍存在SRB繁殖风险,需考虑其他腐蚀控制措施。
油田集输管道具有距离短、数量多、管径小、输量少等特点,均未设置清管阀,同时管输介质中氯离子含量高、矿化度高、易结垢。缓蚀剂在结垢、高含量Cl-环境中吸附效果差,且需要设置大量加注装置,大大增加了维护工作量和费用,该方法多用于高产气田集输管道,在油田集输管道中应用较少。金属镀层虽效果好,但其价格高、施工要求高,同时开孔、维护困难,且未在油区应用,因此也不推荐使用。
目前,在油气田集输管道应用较多的内腐蚀控制技术主要有耐蚀合金管、双金属复合管[4]、非金属管道和普通碳钢+内涂层或非金属内衬管[26]。表2是耐蚀合金管、非金属管道、内挤涂和内穿插技术比较。耐蚀合金管强度高、防腐蚀效果好,但费用高昂,造价是普通碳钢管材的9~10倍,一般用于高产、高含H2S和CO2油气田集输管道,在常规油气田集输管道中应用效益差。双金属复合管在某些油田也有应用,其制造和施工质量对其耐蚀性影响较大,曾出现过内层塌陷、焊缝处泄漏等问题[27],同时造价高,效益差。非金属管道目前在油气田集输管道中应用越来越广泛,特别是随着技术不断发展进步,柔性复合管、热塑性塑料内衬玻璃钢复合管等管材不断推陈出现。非金属管道具有防腐蚀性能好、质量轻、内壁光滑、价格适中等优点,但缺少质量控制及检测方法,存在管体抵御外部载荷强度低、制造、运输、存储和安装质量要求高、建成后不易开孔等问题。内挤涂和内穿插技术近几年广泛应用在油田集输管道,内挤涂技术是通过在线风送挤涂技术在管道内壁涂敷环氧涂层,可在新建或在役管道中应用,一次施工距离可达3~5 km,具有防腐蚀效果好、施工费用低、涂层附着力强、施工方便,短距离集输管道可一次全线施工等优点,缺点是对管道内壁质量要求高、施工后不宜增加支管、开孔等。内穿插技术是在金属管道内部穿插非金属管形成内衬层,一次施工距离为200~500 m,具有防腐蚀效果好、内衬管可少量承压等特点,施工费用相对内挤涂稍高,缺点包括检测及治理控制方法少,衬管与管道为机械结合,易发生坍塌、不宜开孔和连接支管等问题。
项目 | 耐蚀合金管 | 双金属复合管 | 非金属管道 | 内挤涂技术 | 内穿插技术 |
---|---|---|---|---|---|
施工方式 | 焊接 | 焊接 | 热熔连接、法兰连接、粘接、扣接等 | 在线刷涂 | 分段穿插 |
性能描述 | 强度高、耐蚀性能好 | 强度高、耐蚀性能好 | 重量轻、耐蚀性能好、水力摩阻小 | 可在在役管道施工,耐蚀性能好、水力摩阻小 | 可在在役管道施工,耐蚀性能好、水力摩阻小 |
内壁特性 | 表面较粗糙易结垢,输送能耗较高 | 表面较粗糙易结垢,输送能耗较高 | 内壁光滑、输送阻力小、不易结垢 | 内壁光滑、输送阻力小、不易结垢 | 内壁光滑、输送阻力小、不易结垢 |
耐蚀性能 | 耐蚀性能好,奥氏体不锈钢在氯离子环境中易发点蚀 | 耐蚀性能好,奥氏体不锈钢内衬层在氯离子环境中易发点蚀 | 有良好的耐腐蚀性 | 有良好的耐腐蚀性 | 有良好的耐腐蚀性 |
抗震性 | 好 | 好 | 一般 | 好 | 好 |
第三方破坏难易程度 | 不易 | 不易 | 容易 | 不易 | 不易 |
使用温度 | -20~450 ℃ | -20~450 ℃ | -80~-40 ℃,部分可达120 ℃ | -80~-40 ℃ | -80~-40 ℃ |
耐冲击性 | 好 | 好 | 差 | 较好 | 较好 |
使用寿命 | 长久 | 长久 | 30~50 a | 30~50 a | 30~50 a |
质量控制 | 技术成熟 | 技术较成熟 | 无损检测技术不成熟 | 试压,可检查表面质量和厚度 | 试压,无损检测技术不成熟 |
管道检修 | 点焊修补或换管 | 需分层焊接,难度稍大 | 一般需要换管并增加接头,费用较高 | 损坏后维护较为困难,需要将损坏点切除后重做接头,维护费用较高 | 损坏后维护较为困难,需要将损坏点切除后重做接头,维护费用较高 |
连接支管或开孔 | 方便 | 焊接要求较高 | 需断管增加三通 | 不宜 | 不宜 |
施工阶段 | 新建管道 | 新建管道 | 新建管道 | 新建管道或在役管道均可 | 新建管道或在役管道均可 |
造价(与普通碳钢管道相比) | 9~10倍 | 5~8倍 | 0.8~1.5倍 | 1.1~1.5倍 | 1.5~2倍 |
2.3 内腐蚀控制思路
针对西部某油田集输管道和输送介质特点,结合内腐蚀控制技术和经济比选结果,确定适用于输送高矿化度、高含水和含硫介质的中小口径、短距离集输管道内腐蚀控制思路如下。
(1)新建管道:推荐使用非金属管道,必须使用金属的管道采用内挤涂技术涂敷涂层。
(2)在役管道:对泄漏频繁且经检测评价无修复价值的在役管道进行换管,更换为非金属管道或普通碳钢+内挤涂管道。经评价或补强后评价强度合格的管道采用内挤涂或内穿插技术进行防腐蚀。
(3)采取措施降低介质中的SRB,从而降低S2-含量,提升水质。
3. 现场应用情况
2019年油田开展了管道高失效率区块治理试点工程,对内挤涂、内穿插和新型非金属管道进行试验应用和评价,共完成了23.8 km管道内挤涂、14.0 km管道内穿插、7.6 km 32 MPa柔性高压复合管,3.2 km聚乙烯内衬玻璃钢复合管的现场试验和评价。评价结果表明,这些管道在油田适用性良好,截止目前均未出现失效等问题,充分证明了这些技术在油田集输管道应用中的可行性。
2021年,油田在WN区块开展了无泄漏示范区建设试点工程,该区块95%以上管道失效均为碳钢管道内腐蚀穿孔泄漏。结合油田内腐蚀治理相关成果,在污水处理系统中进行了生物竞争法抑制SRB试验,制定了以非金属管道、内挤涂和内穿插为主的管道内腐蚀控制方案,具体方案如表3所示,目前已完成约50 km高失效集输管道的治理,管道失效率大幅降低。
管道类型 | 输送介质 | 设计参数 | 新建管道 | 在役管道 |
---|---|---|---|---|
单井采油管道 | 含水原油,含水率20%~80%(质量分数) | 2.5 MPa,30~50 ℃ | 玻纤增强预浸柔性复合管,硬质聚氨酯泡沫保温层;聚乙烯防腐胶带防护 | 更换为非金属管道,采用内挤涂或内穿插技术防护 |
集输支干线 | 2.5 MPa,30~50 ℃ | 聚乙烯内衬玻璃钢复合管、钢骨架复合管或钢制管道内挤涂 | 采用内挤涂或内穿插技术防护 | |
单井注水管道 | 净化污水,高矿化度、含硫 | 25~32 MPa,30~60 ℃ | 高压柔性复合管 | 更换为非金属管道或采用内挤涂技术 |
注水支干线 | 金属管道+内防腐蚀 | 采用内挤涂技术 | ||
供水管道 | 4.0 MPa,30~60 ℃ | 钢骨架聚乙烯复合管、玻璃钢管 | 采用内挤涂或内穿插技术 |
4. 结论
(1)西部某油田集输管道在结垢、Cl-、S2-和SRB影响下产生严重的垢下局部腐蚀,严重影响管道安全平稳运行。
(2)油田集输管道具有数量多、管径小、距离短、输量少等特点,从技术和经济性方面考虑,推荐采用非金属管道、内挤涂和内穿插等技术控制管道腐蚀问题。
(3)不同油田集输管道输送介质、运行条件、失效机制均不相同,其他油气田应根据自身特点优选内腐蚀控制方案。
免责声明:本网站所转载的文字、图片与视频资料版权归原创作者所有,如果涉及侵权,请第一时间联系本网删除。
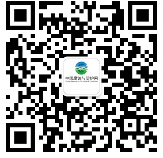
官方微信
《腐蚀与防护网电子期刊》征订启事
- 投稿联系:编辑部
- 电话:010-62316606
- 邮箱:fsfhzy666@163.com
- 腐蚀与防护网官方QQ群:140808414