随着全球能源向低碳化、无碳化、低污染的方向发展,氢能的开发和利用备受关注。现如今,氢能被视为综合能源供给系统的重要载体,是经济发展的助推剂,是新兴产业的催化剂,同时也是能源技术变革的方向标。因此,发展氢能有利于推进能源生产和消费革命,这对能源发展有着跨时代的意义[1]。
氢能储运是氢能产业链中的最为重要的一环。在现有氢能储运技术中,管道输送是实现长距离输运、氢能大规模利用的重要方式。利用已有天然气管网以掺氢天然气的形式输送氢气最具经济性[2]。美国、欧洲、日本等国现已开展了多个纯氢及天然气管线掺氢示范项目。近年来,我国也相继出台了一系列关于氢能发展规划,制订《能源技术革命创新行动计划》,在“十四五国家重点研发计划氢能专项”中明确指出要大力发展氢气的储运和氢能利用技术等[3]。截至2021年,我国长输天然气管线总里程近11 × 104 km,西气东输二、三线干线均采用高强度管线钢X80进行天然气输送,其中仅X80管线总长就列居世界第一,开展天然气管网掺氢输送可快速实现氢气的长距离输送[4]。一方面,我国纯氢/掺氢管道建设示范项目如火如荼;另一方面,掺氢管道服役安全保障技术需求迫切。将氢气掺入天然气管网进行混输带来一个潜在问题是钢制管道的氢脆。管内部输送介质中的氢分子可以吸附于管道内壁,分解成氢原子后可进入管材内部,导致管线钢发生氢损伤[5~8]。高强度管材由于其特殊组织结构和强化相的分布,在临氢环境中服役时的损伤敏感性要明显高于低强度管材。此外,长输埋地管道的铺设连接主要依靠环焊缝焊接工艺来完成,在焊接热循环过程中管线钢经历着一系列复杂的变化,微观组织及焊接残余应力的不均匀性使得焊缝及热影响区的氢渗透扩散动力学过程发生了变化,焊缝及热影响区易成为地下管线氢脆的薄弱环节。因此,了解并控制管材和焊缝的氢损伤行为,对氢气管道建设、选材及安全维护尤为重要。
本文综述了掺氢天然气与管材及其焊接区的相容性问题,氢渗透过程及研究方法,从氢渗透行为角度分析了氢在管材内的吸附和扩散以及氢原子进入到管材内部引发的多种氢损伤形式,并从影响因素等方面综述了掺氢管材及焊接组织的氢损伤形式和机理。研究结果可为掺氢天然气管材的选择、设计及安全服役提供理论基础,促进氢能经济的安全稳定发展。
1 氢气管道管材相容性研究
氢与输氢管材的相容性研究主要针对管线的服役状态,对输氢管材的力学性能进行评估,探究不同掺氢比与输送压力之间的相关性,以分析何种管材能满足不同输氢压力以及掺氢比。近年来,国内外制定了金属材料与氢相容性的相关标准,例如ANSI/CSA HGV 4.10和GB/T 34542.2-2018。这些标准明确指出测试过程均在气相充氢环境中进行,测试方法主要有慢应变速率拉伸(SSRT)试验、疲劳寿命试验、断裂韧度试验和疲劳裂纹扩展速率试验。此外,电化学充氢试验可以加快氢原子渗入管材,在短时间内提高管材的氢浓度,主要用于氢损伤研究[11]。其中,根据服役环境的不同,氢损伤主要分为气态氢损伤和溶液氢损伤。
1.1 气态氢损伤
自20世纪80年代以来,国内外学者对管道内环境氢脆试验开展了相关研究,测试了气态环境内充氢对管材的拉伸性能、断裂韧性以及疲劳裂纹扩展的影响。研究表明,X52、X60、X65和X70管线钢在富氢环境中的断面收缩率和抗拉强度均有所下降,并且随着氢分压的增大,断面收缩率逐渐下降[12,13]。Amaro等[14]在富氢环境中对X52和X100管线钢的疲劳裂纹扩展性能进行了测试,表明疲劳裂纹扩展速率随氢气压力的升高而加快,并基于试验结果建立了疲劳裂纹扩展预测模型。Nanninga等[15]在10 MPa纯氢环境中对不同强度等级的管线钢进行力学性能测试,结果表明X80管线钢韧性下降高达67%,氢脆敏感性随管线钢强度等级提高而显著增加。Lee等[16]对X65管线钢在20 MPa氢气环境中进行原位拉伸试验,相较于空气环境中的抗拉强度下降了3.4%,延伸率下降了4.1%。Meng等[17]在12 MPa压力下测试了不同掺氢比条件对X80管线钢力学性能的影响,结果表明随氢气体积分数增大,X80管线钢的疲劳裂纹扩展速率显著加快。An等[18]研究了X80管线钢在富氢环境中的低周疲劳和疲劳裂纹扩展特性,结果表明随着氢气压力的升高,疲劳裂纹扩展速率明显增加,管道失效周期呈指数下降。Wasim和Djukic[19]从微观尺度探究了氢原子导致金属基材原子结合能下降的机制,还有学者认为在高压富氢环境中,渗入的氢原子可以限制位错和晶格内部金属原子的运动,提高显微弹性模量及显微硬度,导致钢材发生脆性断裂。
1.2 溶液氢损伤
封辉和朱兴华[23]探究了不同应力三轴度下电化学充氢对X80管线钢力学性能的影响,结果表明电化学充氢能够降低材料的缺口试样抗拉强度和断面收缩率,随着应力三轴度的增加,缺口位置应力集中程度增加,氢更容易在该处聚集。Li等[24]探究了电化学充氢下温度对管线钢氢扩散和氢脆的影响规律,表明氢扩散系数D与温度T之间遵循Arrhenius方程,随温度的降低D呈现下降的趋势,其对应关系如图1所示。Asadipoor等[25]采用原位、非原位充氢拉伸试验和原位电化学微悬臂弯曲试验(图2b2),对X70管线钢的氢脆进行了宏观和微观尺度的研究,从图2b2中能够明显看出电化学充氢后悬臂根部有明显的裂纹,掺氢条件下的氢脆敏感性远大于未掺氢条件。
图1
对于输氢管道而言,管线钢处于气态氢环境,与电化学渗氢过程有所不同。氢气分子必须先分解成氢原子,才能渗入管线钢,这一过程受氢的溶解平衡控制。当管道压力不高时,根据西弗特定律,钢表面氢的溶解度很低。换言之,管道内表面的氢吸附与脱附平衡,使表面的氢浓度无法达到较高水平。相比之下,电化学“阴极渗氢”可以使氢原子在管道内壁建立高浓度,从而驱动表面氢原子向管线钢内部渗透。因此,电化学渗氢通常是单向的非平衡过程。
2 管材及焊接接头的氢渗透行为
2.1 氢渗透试验
张敬强等[29]探究了低碳钢焊接接头的氢吸附和扩散过程。研究表明,母材的稳态扩散电流大于焊缝,而氢扩散系数小于焊缝。Sun和Cheng[30]研究了X80焊接接头在弹性和塑性应力下的氢渗透过程,结果表明塑性变形有利于氢在焊缝的渗透和聚集,尤其是在热影响区,氢和应力的协同作用使得局部区域的氢致开裂敏感性增强。Gou等[31]采用电化学氢渗透测试,研究了不同热输入条件下X80钢的冲击断裂性能(如图3所示)。研究表明,当组织中含有较多的板条状贝氏体(LB)时,粗晶热影响区(CGHAZ)具有更强的抗冲击断裂能力。H原子能够削弱晶界处的Fe-Fe键,导致氢脆。与粒状贝氏体(GB)相比,含LB的微观组织需要更高的H浓度才能导致穿晶脆性断裂。还有研究指出,管线钢焊接接头区域的组织多为针状铁素体,铁素体相互交织形成晶界网络,为氢扩散提供路径,从而导致焊接接头区域相对于母材具有较高的氢渗透速率和表面氢浓度。但在焊接过程中,由于晶粒粗化、夹杂物和渗碳体增多,会阻碍氢扩散,导致焊接组织的氢渗透速率下降。其中,Dong等[32]研究表明,X100母材具有较低的氢陷阱密度,而热影响区(HAZ)则具有较高的氢陷阱密度,HAZ的氢扩散系数和氢渗透速率都低于母材。所以不能单一的去评价焊接区的氢渗透行为,应当找到影响氢渗透行为的主控因素,因此在进行氢渗透行为研究时要对材料的微观组织,晶体结构,力学参数乃至焊接过程中的热值参数都要逐一考虑。
图2
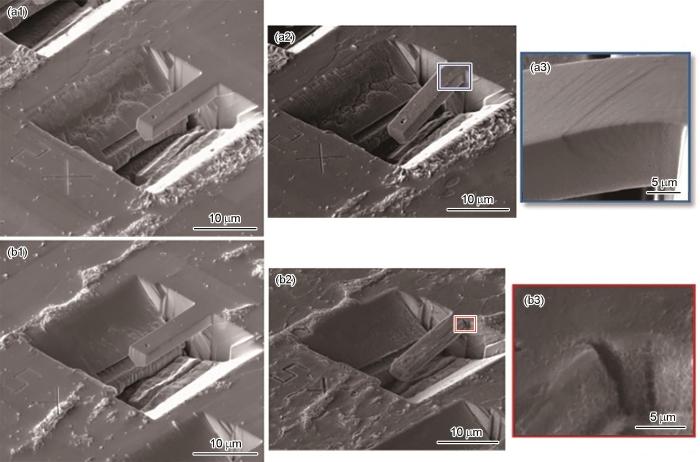
图3
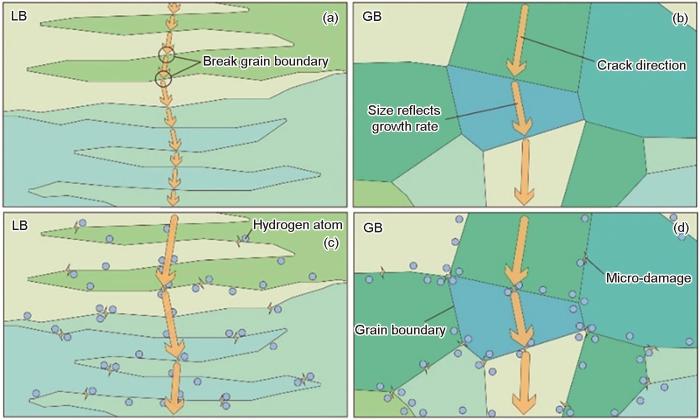
2.2 理论模拟计算
创建理论模型进行模拟计算可以有效弥补实验的不足,用以研究管材表面氢的覆盖度、吸附能以及吸附解离过程。主要的模拟计算方法包括分子动力学计算、第一性原理以及有限元模拟等。王春璐等[33]研究了H2在Fe金属(110)面的吸附解离过程,阐述了Fe(110)与氢分子之间的物理吸附关系,并基于密度泛函理论计算出解离后的H原子与铁之间是化学吸附关系,H2到H原子的解离吸附过程如图4所示。研究表明Fe对H2有极高的解离活性,Fe原子通过将外层d轨道的电子填入σ*,能够弱化H-H间的作用强度。Chohan等[34]采用第一性原理,计算了氢原子从吸附到扩散进入γFe(100)、(110)、(111)面的过程(如图5所示),其中(100)表面的势垒为1.4 eV,(110)表面的势垒为1.2 eV,(111)表面的势垒为1.7 eV,这说明(111)表面暴露在含氢环境中,其中奥氏体钢(111)密排面扩散能垒最高,扩散最难。薛景宏等[35]通过建立有限元模型,探究了有无残余应力时管材的氢浓度分布状态(如图6所示)。结果表明,残余应力改变了氢的分布状态,且经过热处理后管材的氢浓度分布与未经热处理时基本一致,但氢浓度值明显降低。张体明等[36]利用ABAQUS软件建立了X80钢螺旋焊管三维模型,并对焊接接头的氢扩散进行数值模拟。结果表明,残余应力和组织不均匀都会导致氢扩散的发生,并且发现残余应力的影响大于组织不均匀性的影响,存在残余应力的焊缝区的氢浓度是比不考虑残余应力时的2.7倍。
图4
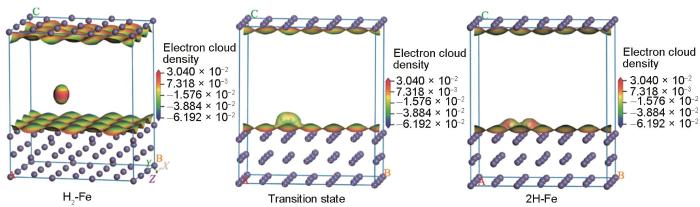
图5
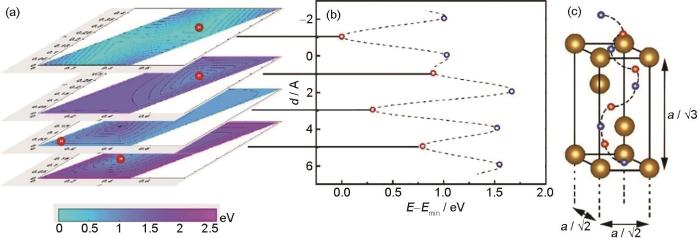
图5 氢原子从吸附到扩散进入γFe(111)表面势能变化过程[34]
Fig.5 2D potential energy surface at local minima for hydrogen diffusion through the (111) surface (a), energy profile for hydrogen diffusion through the surface (b), diffusion pathway from the surface through towards the bulk (c), dotted line between stationary points is only a guide to the eye[34]
图6
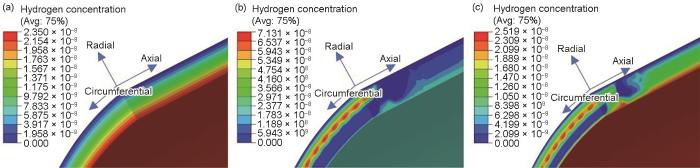
通过实验表征和多种模拟方法对氢在管线钢表面及焊接接头区域的吸附、解离以及扩散过程进行研究,有助于理解氢渗透过程及预防掺氢管材的损伤行为。这些研究不仅为管材在氢环境下的应用提供了理论基础,还为实际工程中的防护措施和材料改进提供了参考。
3 管材及焊接接头氢损伤影响因素
3.1 化学元素
管材及焊接接头中化学元素的差异会显著影响氢致损伤行为。合金化过程中,沉积硬化、固溶强化以及元素偏析均会引起显微组织的变化,进而影响材料的力学性能。在高强度管线钢中,C含量通常控制在0.1%以内。碳的主要作用是稳定力学性能,但随着C含量增加,碳化物含量也随之增加,形成更多氢陷阱,导致氢扩散系数下降和氢溶解度增加[37]。Si含量增加会降低氢在钢中的扩散系数,从而减缓氢致开裂扩展速率。焊接过程中,S和Mn可形成MnS夹杂物,这些夹杂物作为氢陷阱,诱导氢聚集并成为氢致开裂(HIC)形核的位置,因此应避免MnS的形成[38,39]。此外,P的偏析可能导致局部区域的硬化,增加对HIC的敏感性。尽管Cr通常被认为是有害元素,但Cr可以抑制氢致沿晶断裂的发生。而Ni则能促进奥氏体的生成,从而降低HIC敏感性。
3.2 显微组织结构
管线钢及其焊接接头的显微组织主要由铁素体和珠光体构成,这种条状组织结构会影响氢的扩散系数。在热处理过程中,部分铁素体-珠光体微观组织会转变为针状铁素体与贝氏体,从而提高管线钢的强度和韧性,并对氢扩散产生一定影响。氢原子在铁素体中的扩散速率高于奥氏体,而面心立方结构的奥氏体则会阻碍氢的扩散,因而HIC敏感性较低[40]。
然而,成片的马氏体组织对氢致开裂的敏感性明显高于其他显微组织。当管材中碳当量较高时,低温相变生成较大的马氏体或魏氏组织,增加了氢陷阱密度,诱导氢的聚集,为氢致裂纹的形成创造了条件,因此氢致开裂敏感性较高[41~43]。此外,当管材和焊接区域中含有较多缺陷、位错密度和M-A岛等硬化组织时,其氢脆敏感性也会显著增加[44]。Momotani等[45]研究了奥氏体晶界,发现氢更容易在奥氏体晶界处聚集,并产生明显的氢致裂纹(如图7)。Tian等[46]的研究显示,充氢过程中大角度晶界比小角度晶界对氢致开裂的敏感性更高,其主要原因是由于原始奥氏体晶界(PAGB)相对于板条界(LB)具有更高的氢结合能和较低的结合强度,因此能迅速达到开裂所需的局部氢浓度。此外,由图8还可见,PAGB捕获的原子更多,自由体积内的氢浓度相对较低,这也反应了大角度晶界氢致开裂敏感性更高。Zhu等[47]采用原子探针显微镜(APT)研究了QP980钢充氢后的元素分布,结果表明氢主要集中在C含量较高的区域,且氢在奥氏体中的质量分数(约3.4 × 10-3%)是马氏体的3倍。张体明等[36]通过高压气相氢渗透实验测定了焊接接头各区的氢扩散参数(如图9),结果显示CGHAZ区域的稳态氢电流密度最大,表明显微组织的差异会显著改变氢扩散参数。显微组织的差异性对于氢渗过程有重要影响,氢原子进入管材后会引发多种形式的氢损伤行为。其中,袁玮等[48]评估了不同显微组织下X100的氢致开裂敏感性,研究表明原始铁素体-贝氏体组织试样HIC敏感性最高(如图10)。
图7
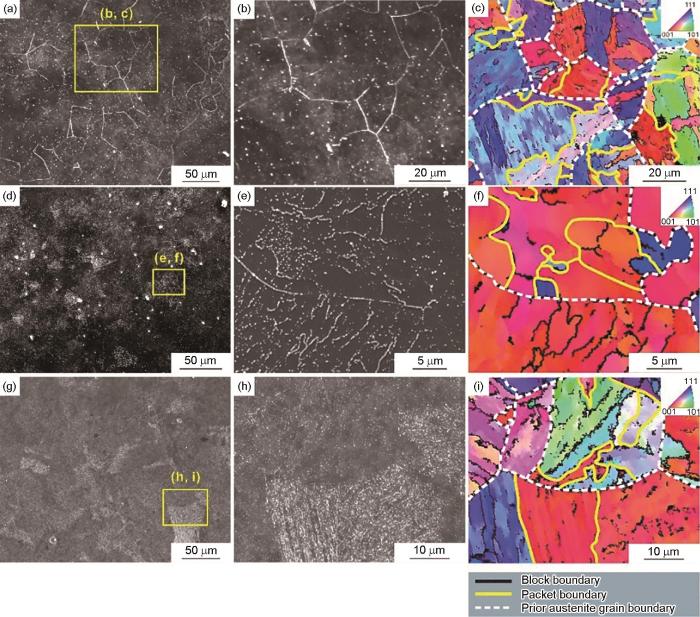
图8
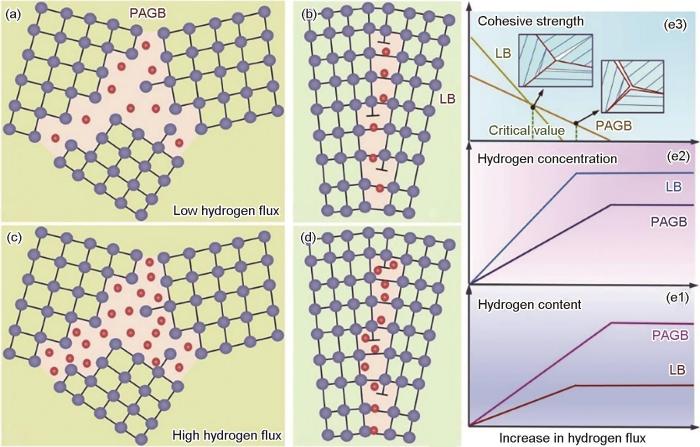
图9
图10
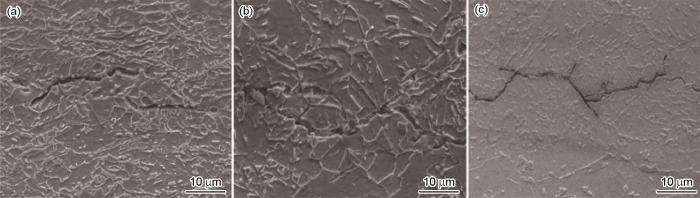
3.3 管线钢强度等级
王万里等[49]探究了X60和X70管线钢母材及焊接组织的氢损伤敏感性。研究表明,X60和X70管线钢断口均显示出明显的剪切韧窝,但在其焊接接头热影响区可见一定深度的氢脆区。此外,强度等级更高的X70焊接接头氢脆区出现了明显的准解理断裂形貌。李玉星等[50]以X52和X80钢为试验对象,分析了氢分压对材料屈服强度、抗拉强度、断面收缩率及氢脆指数的影响。研究表明,X52和X80钢的塑性逐渐下降,但强度等级更高的X80钢氢脆程度更为明显。王涛和王荣[21]采用电化学充氢方式研究了X70和X80钢中的氢扩散行为,发现充氢电流密度的平方根与表观氢浓度呈线性关系,并且强度等级更高的X80钢表观氢浓度高于X70钢。主要原因是高强度管线钢中晶界处往往会存在应力集中或缺陷,这些缺陷有助于氢原子的聚集,这使得强度等级较高的管线钢HIC敏感性更高。
3.4 应力
在采用天然气管网进行输氢时,管材一般会受到残余应力和拘束应力的影响。残余应力主要来源于焊接冷却收缩过程中低温区金属的约束力及局部组织相结构的转变。焊接组织的残余应力通常大于母材本身,在应力作用下氢容易在此聚集,特别是在热影响区(HAZ),该区域极易发生氢致损伤行为。此外,管材在服役过程中还会受到外部拘束应力(弹性应力和塑性应力)的影响。弹性应力作用下,晶格大小发生改变,原子间空隙增大,导致氢渗透电流密度增加。塑性应力则通过改变位错密度来影响氢渗透行为和氢脆敏感性[51]。在塑性应力的初始阶段,由于拘束应力的存在,材料会出现大量位错和不可逆氢陷阱,氢被捕获,导致渗透电流密度下降;随着塑性应力的增大,渗入金属内部的氢与位错交互作用,形成氢原子气团进入氢扩散通道,氢渗透电流密度开始增加。当氢陷阱中捕获的氢和位错中扩散的氢达到平衡时,测得的渗氢电流处于稳定状态[52,53]。
Birnbaum和Sofronis[54]探究了塑性条件下的氢扩散行为,表明由于应力集中形成大量位错,位错与氢一起运动,塑性应力会增强了氢促失效过程。而张统一等[55]认为,位错既可作为氢陷阱捕获氢原子而降低氢的渗透,又能降低扩散能垒,促进氢原子的扩散,且运动的位错可以作为氢扩散载体,即应力对氢渗透的影响具有两面性。Park等[56]以EH36钢为基础,预变形后进行电化学氢渗透研究,表明20%应变时,扩散系数是原来的十分之一,氢含量上升3倍。Sun和Cheng[30]对X80钢母材及热影响区在弹性应力和塑性应力下进行了电化学氢渗透试验,发现施加弹性应力时,氢渗透速率增加;施加塑性应力时,氢捕获密度增加,导致氢扩散速率下降。
3.5 环境影响因素
综上所述,环境中的氢原子解离和析出、氢环境、阴极保护及杂散电流等因素均对管材的氢致损伤行为有显著影响。理解和控制这些环境影响因素,对于提升管材在氢气环境中的耐氢脆性能具有重要意义。
4 氢损伤机制的多种解释
目前存在多种机制来解释氢损伤现象,主要包括氢压理论(IHP)、氢促进局部塑性变形理论(HELP)、吸附氢致位错发射机理(AIDE)、氢降低原子间结合力理论(HEDE)等[61]。由于各种机制均存在一定的局限性,因此在阐述氢致失效过程中,往往需要多种机制相互补充来解释氢促失效的复杂过程。
4.1 IHP
IHP指出,金属材料在阴极充氢(如酸洗、电镀或电解充氢)或硫化氢环境中服役时,大量的氢原子渗入材料内部,并在材料缺陷处富集[62]。缺陷捕获的氢原子在热力学转变下复合成氢分子,同时产生内应力,进一步促进裂纹的萌生和扩展。Chu等[63]通过透射电镜(TEM)对预充氢钢试样进行观察,证明了氢由于在材料缺陷处富集导致的氢鼓泡现象。Xie等[64]采用原位TEM对氢环境下铝金属/氧化物界面中的纳米级气泡进行研究,同样也证明了氢在氧化物界面处的富集以及内应力的产生。上述研究均为IHP理论提供了有力的证据。IHP机制主要说明缺陷处聚集的氢分压是导致氢鼓泡及氢致裂纹的主要原因,但无法解释材料在受力时发生的延迟断裂和塑性损失现象。
4.2 HELP
为了弥补IHP机制的不足,Beachem[65]提出了HELP。该理论认为,氢进入材料后,在裂纹尖端大量富集,导致尖端氢浓度升高,促使位错运动加剧,最终导致局部塑性变形。Ferreira等[66]采用原位透射电镜拉伸研究了310S和高纯铝在不同氢分压条件下位错滑移现象,该研究证明了施加载荷的样品在引入氢后会促进位错运动加剧。Huang等[67]通过自主设计开发定量原位瞬变电磁法力学测试工具,定量的揭示了氢对位错运动的影响。研究表明在2 Pa电子束激发的H2气氛中引发位错投影滑动距离大于真空环境7.0 nm,位错运动的临界应力比在真空环境中低27%~43%(图11d和e)。此外,该研究还表明循环加载和卸载可以提高氢的脱陷,使得位错恢复其无氢行为。此项研究为HELP机制提供了核心证据。HELP机制强调了氢对力学性能的改变,弥补了IHP机制在解释塑性损失方面的不足。
图11
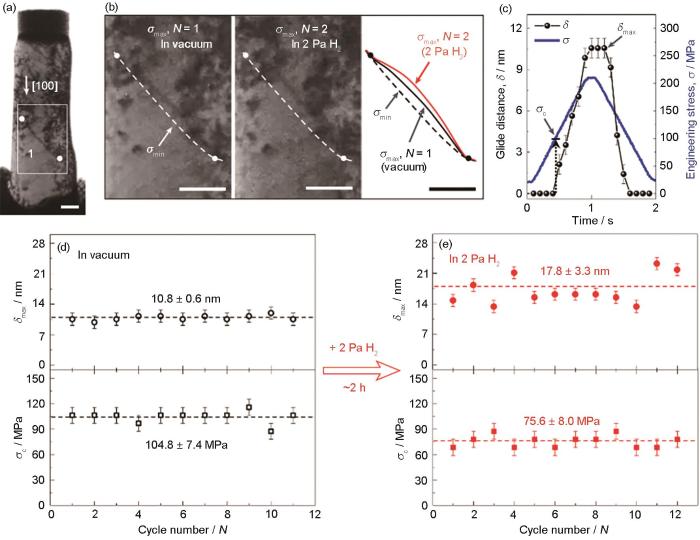
图11 氢化对螺位错弓出运动的影响[64]
Fig.11 Bright-field transmission electron microscope image showing the pillar after a series of cyclic compression loading and unloading sessions (a), configurations of dislocation 1 at σmax in vacuum (N = 1) and in 2 Pa H2 (N = 2) (b), the loading engineering stress σ and the digitally tracked projected glide distance σ of dislocation 1 in a typical load cycle are shown as a function of time (c), the measured σmax and σc of dislocation 1 as a function of loading cycle number in vacuum (d) and in 2 Pa H2 (e)[64]
4.3 AIDE
AIDE进一步扩充了HELP机制。该机制认为,吸附氢对位错的形核和运动起决定作用。在持续应力或交变应力作用下,材料裂纹尖端形成微孔和位错发射,共同促进裂纹的扩展。氢扩散到裂纹尖端或微孔并被捕获是该机制应用的前提。AIDE能解释位错从裂纹尖端形成的过程,而HELP则表明位错离开裂纹尖端的过程,两者相辅相成,互为补充。
4.4 HEDE
HEDE从键能角度分析氢损伤现象。HEDE的成立前提有两个:第一,氢原子在裂纹尖端处聚集,降低原子间的结合力;第二,原子之间受正应力拉断,导致裂纹的萌生和扩展,没有涉及塑性变形的影响。Djukic等[68]指出,HEDE与HELP的交互作用能更有效地解释氢致失效过程。Xue等[69]采用电化学充氢试验以及慢应变速率拉伸试验探究了氢原子对QP980激光焊接接头氢脆断裂机理。研究表明接头试样充氢后,断裂位置由母材区转移到不完全相变区,氢致裂纹主要由马氏体延晶扩展变为马氏体穿晶扩展和少量沿马氏体与铁素体界面沿晶扩展。这主要由于马氏体与铁素体变形不协调导致二者晶界处出现应变集中,进而出现氢原子偏聚现象。这种氢原子偏聚和位错的聚集促使二者晶界产生剧烈的塑性变形,并减弱界面原子间结合力,进而导致断裂位置和裂纹扩展路径的改变。此外,也有学者认为当掺氢管材在较小的拘束应力条件下服役时,HIC机制被认为是HELP诱发HEDE,但随着拘束力的提高,HEDE将成为主导机制。材料在发生氢损伤过程中的机制错综复杂,单一机制难以全面揭示氢损伤原理。因此,在开展相关研究时,需要根据实际服役环境结合宏观力学和微观表征相结合,综合运用多种机制,准确阐述氢损伤机制。
5 结论与建议
在过去数十年中,人们对长输管材及其焊接区域的氢促失效进行了广泛研究。这些研究涵盖了管材与氢气相容性、从原子氢到管材的吸附和扩散行为、氢渗透行为、微观组织和力学性能等多个方面,取得了大量的研究成果。例如,测试方法的改进、氢表征手段的革新,以及先进理论模型和机制的提出,都极大地丰富了我们对氢损伤现象的认知。
然而,目前对氢损伤行为的相应标准并未给出准确依据,特别是在同一体系下的氢促失效研究中,往往出现相互矛盾的结果。这些矛盾反映出不同机制之间的冲突和解释的不一致性。因此,亟需建立新的标准评价体系,以统一管线钢材料的氢致失效问题的评估标准。这将有助于减少不同实验和研究之间的结果差异,提高研究的可比性和可重复性。
此外,对氢与管材的相容性分析仍存在一些挑战。例如,同种材料在气态充氢和电化学充氢条件下的行为差异显著。电化学充氢通常会过度放大氢对管材的危害,而气态充氢过程则过于漫长,导致实际应用中的效能不足。因此,需要一种高效的机制将这两种方法合理关联,以更准确地模拟和评估实际应用中的氢损伤行为。
微观结构和金相组织对氢渗透过程的定量化研究也面临困难。虽然有限元方法和第一性原理计算可用于模拟氢在管材中的分布情况,但在复杂的实际环境中,多因素(如腐蚀、应力应变、富氢环境等)条件下,缺乏相应的参数进行修正。因此,需要进一步发展精确的模拟方法和参数校准技术,以便在复杂环境中更准确地预测和评估氢损伤行为。
为了应对上述挑战,未来的研究应关注以下几个方向:
标准化评价体系的建立:开发统一的评价标准和测试方法,以减少不同研究之间的结果差异,提高研究的可比性和可靠性。这将有助于建立一致的材料选择和评估标准,指导实际工程应用。
多尺度模拟和实验研究:结合多尺度模拟技术和实验研究,深入理解氢在管材中的渗透和扩散机制。利用先进的计算方法(如第一性原理计算和有限元分析)与实验数据相结合,建立更准确的氢损伤预测模型。
复杂环境条件下的研究:开展在实际服役环境下的氢损伤研究,包括腐蚀、应力应变、富氢环境等多因素条件的综合影响。通过现场测试和模拟实验,获得更接近实际应用的氢损伤行为数据。
材料设计和优化:基于氢损伤机制的深入理解,设计和开发具有高抗氢脆性能的新型管材和焊接材料。优化材料成分和显微结构,提高材料在复杂环境中的服役性能。
通过在以上几个方向的持续研究,将有望解决当前氢损伤研究中的关键问题,推动长输管材及其焊接区域在氢气环境下的安全应用。这不仅对能源输送和储存技术的发展具有重要意义,也将为氢能源产业的可持续发展提供有力支持。
免责声明:本网站所转载的文字、图片与视频资料版权归原创作者所有,如果涉及侵权,请第一时间联系本网删除。
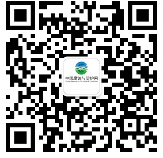
官方微信
《腐蚀与防护网电子期刊》征订启事
- 投稿联系:编辑部
- 电话:010-62316606
- 邮箱:fsfhzy666@163.com
- 腐蚀与防护网官方QQ群:140808414