航空发动机被誉为飞机的“心脏”,其设计制造水平体现了一个国家的科技、工业和国防实力。新一代航空发动机具有高推重比、高可靠性、长寿命等重要性能指标,如何提高航空发动机的可靠性、延长其安全寿命是航空发动机研制、使用和发展的关键问题。 航空发动机关重件的寿命和可靠性直接影响航空发动机的安全性,其疲劳寿命试验是评估航空发动机寿命和可靠性的重要技术手段。由于航空发动机整机疲劳试验成本高、难度大,关重件的疲劳试验成为了评估整机疲劳寿命与可靠性的重要技术手段,甚至可以在一定程度上替代航空发动机的整机疲劳试验和可靠性试验。同时,关重件的疲劳寿命试验也是验证相应的理论模型和仿真算法的必要技术手段。因此,先进的航机关重件疲劳寿命试验技术对航空发动机的研发、定型及延寿有重要应用价值。 航空发动机关重件疲劳试验技术既包括试验设备方面的硬件技术,也包括试验方法及数据处理方面的软件技术,涉及加载、检测、试验结果统计分析等多方面内容,这些相关技术在不同领域、不同对象上都有不同的应用和发展。开展疲劳寿命试验及相关技术研究,对于全面掌握有关的试验方法与技术和发展先进的航空发动机关重件的疲劳寿命试验方法与技术有显著意义。 航机关重件疲劳试验技术研究进展 通过航机关重件的疲劳试验,能够有效评估其在复杂服役条件下的疲劳寿命和可靠性,为航空发动机的设计优化和安全保障提供重要的数据支持。 叶片疲劳试验 在现代航空发动机的生产、研制和使用中,叶片故障十分突出。由于叶片造型复杂、工作条件恶劣,叶片经常会发生断裂故障,给飞机和发动机造成严重事故。据统计,现代航空发动机中因叶片故障返厂检修的台数占检修总数的35%左右,疲劳断裂是导致叶片故障的主要原因。 Part.01 叶片振动疲劳试验 Braut等提出了一种基于一阶固有频率的涡轮叶片加速疲劳试验方法。研究表明,因气流燃烧及干扰产生的高声强噪声会对发动机叶片的振动疲劳寿命产生影响,当单频声频率与叶片的共振频率耦合或接近时,叶片会因产生共振而发生损坏。针对这一问题,王琰等对发动机转子叶片进行了声振疲劳试验,研究了不同的声振激励方式对叶片疲劳性能的影响。 Part.02 叶片高温疲劳试验 Chen等采用高频感应加热器对涡轮叶片进行加热,完成了涡轮叶片高温高低周混合疲劳试验。章的等采用开环式电磁感应线圈加热叶片,通过热传导模拟带温度梯度的涡轮转子温度场,在旋转试验台上完成了涡轮叶片低循环疲劳试验。 在高温环境下,涡轮叶片极易发生蠕变疲劳失效。针对涡轮叶片的蠕变疲劳问题,Yan等设计了一种基于涡流感应装置的叶片蠕变疲劳试验装置,完成了全尺寸涡轮叶片的低周蠕变疲劳试验。蠕变疲劳试验的载荷谱大多为梯形载荷谱,导致试验耗时过长,针对此问题,Shi等提出了一种加速低周疲劳-蠕变试验方法,在梯形载荷谱下完成了全尺寸涡轮叶片低周疲劳-蠕变试验。闫晓军等设计了涡轮叶片的高温蠕变疲劳加速试验,有效地缩短了试验周期。 热机械疲劳是涡轮叶片的主要失效模式之一。与恒定高温疲劳试验不同,热机械疲劳试验需要对试件施加循环温度载荷,即随时间变化的温度载荷,这对加热装置提出了更高的功能要求。 王洪斌设计了基于高频电感应加热器的涡轮叶片热机械疲劳试验装置,可以有效地模拟涡轮叶片在服役过程中受到的循环温度载荷和机械载荷。王荣桥等开发了涡轮叶片热机械疲劳试验系统(如图1所示),应用高频感应加热炉对涡轮叶片进行加热,能够同时模拟服役条件下 叶片考核截面的循环应力场和循环温度场,可以有效地再现真实涡轮叶片在服役过程中的失效模式,为涡轮叶片的寿命预测和失效分析提供技术支撑。 图1 涡轮叶片热机械疲劳试验系统 Part.03 叶片模拟件试验 部件级叶片疲劳试验有效地解决了材料级疲劳试验难以验证叶片疲劳寿命的问题,在设计初期进行叶片的部件级疲劳寿命试验可以提前摸清叶片的疲劳寿命,降低整机试验风险,节约研制成本。然而,部件级疲劳试验需要根据叶片的尺寸及实际受载情况设计专用的疲劳试验设备,导致试验的准备时间较长,且试验结果不具备通用性。 轮盘疲劳试验 Part.01 基于立式轮盘旋转 试验器的轮盘疲劳试验 真实轮盘寿命试验通常在立式轮盘旋转试验器上进行,试验器主要由试验台架、筒盖锁紧装置、机械驱动系统、电力驱动单元、供油系统、真空系统、开关控制系统、安全防爆环组、数字式自动控制系统、爆裂监测系统、计算机控制系统和加热系统等组成。 图3 立式轮盘旋转试验台 龚梦贤应用立式旋转试验器完成了某发动机Ⅰ级轮盘的高温低周疲劳寿命试验,确定了涡轮盘的考核部位,获得了涡轮盘的低周疲劳寿命,但其在试验中只控制了轮盘试验的转速与温度,忽略了涡轮盘在工作时所受的扭矩。对此,李伟等采用扭力盘加扭装置(如图4所示)有效地对转子试验件施加了10000 Nm级扭矩,完成了带扭矩涡轮盘的高温低周疲劳试验。 图4 扭力涡轮盘加扭装置 在考虑离心载荷的轮盘试验中,锥形轮盘的轴向变形往往难以控制,对轮盘试验的边界条件和变形有很大影响,导致试验工况和发动机的真实工作状态之间存在差异,轮盘的寿命预测结果具有较大的误差。针对此问题,刘大成等提出采用油缸式旋转试验器进行高压压气机轮盘试验的方案,通过调整油腔中油的体积实现轴向力的变化,完成了对压气机轮盘的疲劳寿命试验。 Part.02 轮盘高温疲劳试验 为了尽可能在试验中模拟发动机转子的真实工作环境,除对转子施加离心载荷外,还需要对其施加温度载荷。《航空涡轮喷气和涡轮风扇发动机通用规范》中明确规定涡轮转子试验应在第一级涡轮转子进口最高允许燃气温度下进行,在试验过程中,轮盘的内孔或盘心应达到最高设计温度。 李现玲等研制了一种轮盘加温冷却一体装置,能够长时间保持轮盘径向方向的温度梯度。高仁衡等针对试验中轮盘热应力难模拟、寿命考核位置多等问题,提出了以离心载荷补偿热载荷、以损伤程度定考核位置的解决方案,设计了高温度梯度轮盘试验件设计方案,完成了轮盘高温低周疲劳寿命试验。 Part.03 轮盘局部结构疲劳试验 图6 双轴加载试验件 图7 叶-盘组装结构试件 图8 轮盘榫槽局部结构试件 图9 轮盘轮毂内孔局部结构试件及试验装置 一些学者通过局部特征模拟试件来模拟轮盘危险部位的真实受力状态,也能够在一定程度上代替真实轮盘试验,通过低成本的试验获得真实轮盘部件的疲劳性能。刘若楠等设计了能够模拟轮盘裂纹扩展过程的V型缺口模拟件,结合等效试验载荷谱,有效地模拟了轮盘的裂纹扩展过程。 魏大盛等将周向应力和轴向应力比值和轮盘中心孔处周向应力沿径向的应力梯度作为设计指标,设计了反映双轴应力状态的多轴模拟件和反映应力梯度的平板缺口模拟件(如图10所示),建立了轮盘中心孔疲劳模拟件的设计方法。万江艳等设计了反映轮盘榫槽底部应力分布状态的局部模拟试件,通过模拟件试验建立了基于材料延伸率的轮盘破裂准则。 图10 轮盘中心孔模拟试验件 刘廷毅等以实际轮盘构件的最大主应力与应力梯度为设计变量,设计了压气机Ⅰ级轮盘榫槽的模拟件,完成了轮盘模拟件的疲劳试验。刘胜等根据涡轮盘的榫槽特征设计了缺口模拟件,完成了涡轮盘模拟件的高温疲劳、持久及蠕变疲劳试验,研究了蠕变载荷对缺口件疲劳寿命的影响和疲劳载荷与持久载荷的交互损伤规律。 张成龙等将模拟件尺寸作为设计变量、主应力和应力梯度作为优化条件,通过有限元仿真优化轮盘模拟试件,获得了与轮盘榫槽应力状态相似的模拟试件。郑小梅等提出了一种高压涡轮盘螺栓孔低循环疲劳模拟件设计准则,即模拟件与螺栓孔虚拟裂纹内第一主应力和第一主应变分布一致、最大应力点的第二主应力与第一主应力的比值一致。 现有的模拟件设计方法通常保证危险点一定范围内的应力/应变分布与真实构件的一致,但这些方法对“一定范围”的定义缺乏理论依据且未能形成统一认识,对此,赵淼东等提出了一种临界距离范围内SWT参量分布一致的模拟件设计方法,建立了轮盘盘心、螺栓孔、端齿等危险部位的模拟件设计方法,完成了模拟件的低周疲劳试验(如图11所示)。与部件级疲劳试验相比,模拟件试验能够有效地减少载荷控制难度和试验成本,已经在强度测试评估方面展现了良好效果,具有广阔的应用前景。 图11 轮盘低周疲劳模拟件 Filippini等从轮盘的锻造部件中切割试样,完成了轮盘材料的高温多轴疲劳试验(如图12所示),评估了多轴疲劳寿命预测模型的准确性。 图12 轮盘锻造部件高温多轴疲劳试验 Madariaga等通过电火花切割方式从全尺寸涡轮盘本体中提取试样,在配有感应加热系统的MTS试验机上完成了高温低周疲劳试验(如图13所示)。 图14 涡轮盘本体取样示意图 Prasad等通过电火花切割方式从全尺寸涡轮盘的轮缘、轮毂和孔三个位置提取试样,对三种试样分别进行了高温低周疲劳试验,研究了718合金涡轮盘的低周疲劳-蠕变损伤演化过程。Hu等从实际涡轮盘的边缘区域沿环向切割试验样本,通过蠕变疲劳试验研究了GH720Li高温合金涡轮盘在不同保持时间下的微观组织及蠕变疲劳行为。 轴疲劳试验 航空发动机的轴类零件主要起到支撑与传递动力的作用,其篦齿、花键等应力集中部位易发生疲劳失效。航空发动机轴类零件疲劳试验是通过模拟发动机中的真实支撑状态,并施加相应的循环载荷来实现对轴类零件的考核。 在服役过程中,轴类零件的受载情况复杂,主要承受扭矩、轴向力、弯矩、振动扭矩、陀螺力矩、转子惯性力等载荷作用。其中,扭矩和轴向力为低循环载荷;振动扭矩、陀螺力矩和惯性力为高循环载荷。在试验器加载过程中,扭矩、振动扭矩载荷通过套齿及花键等部位传到轴上;轴向力、弯矩和陀螺力矩载荷通过联轴器和支撑位置传到轴上。 在轴类零件环境载荷模拟方面,我国的轴类零件疲劳试验器功能较为全面,能同时施加扭矩、轴向力、振动扭矩和弯矩等载荷,可以较好地模拟轴类零件的实际边界条件。 成都发动机公司研制的主轴立式综合加载试验器(如图15所示)是我国航空发动机轴试验中应用最为广泛的试验器,该试验器可对发动机主轴同时施加轴向力、扭矩、弯矩、振动扭矩等载荷,较好地实现了双转子发动机涡轮轴的载荷模拟和边界条件模拟(如双转子发动机涡轮轴多支承的全模拟、涡轮轴与涡轮盘联结处的全模拟),可用于确定涡轮和涡桨发动机主轴寿命,也可对同类主轴进行强度极限、屈服强度和刚度的验证试验。 国内其它单位也在发动机轴类零件试验器研制方面取得了一定的进展。成都四二零厂研制了一种可以同时施加轴向力、弯矩、扭矩和振动扭矩的全尺寸轴疲劳试验器,完成了五根低压轴和五根高压轴的全尺寸疲劳寿命考核试验,确定了涡轮轴在标准循环载荷下的安全使用寿命。电子科技大学设计了一种五通道协调加载涡轮轴疲劳试验机,可以同时模拟扭矩、振动扭矩、惯性力、陀螺力矩和气动轴向力的综合作用。陕西理工学院研制了一种基于电液伺服系统的涡轮轴疲劳试验台,通过电液伺服阀有效地实现了扭矩载荷与弯矩载荷的同步加载过程,利用计算机测控系统实现了测试过程中多种循环加载方式以及载荷大小的控制调整。 对于轴类零件的高低周复合疲劳试验的多载荷模拟技术研究,中国飞机强度研究所设计了能够同时施加轴向力、主扭矩、振动扭矩和旋转弯矩载荷的大涵道比涡扇发动机风扇轴试验器,完成了四种载荷联合作用下风扇轴试件的高低周复合疲劳试验。空军第一研究所使用涡轮轴综合加载疲劳试验器对涡轮轴进行了扭矩、轴向力和弯矩三种载荷联合作用下的高低周复合疲劳试验。 湖南动力机械研究所研制了能同时施加轴向力、扭矩、横向力和弯矩载荷的发动机桨轴试验器(如图16所示),完成了某发动机桨轴的高低周复合疲劳试验,提出了基于最差件等寿命曲线的桨轴高低周复合疲劳寿命分析方法。 图16 发动机桨轴试验器 疲劳试验新技术研究进展 随着现代航空发动机飞行任务和环境条件日益苛刻,传统的疲劳试验方法已经无法完全满足现代航空发动机疲劳寿命与可靠性的研究需求。近年来,一些新兴技术逐渐在疲劳试验领域中崭露头角。深入开展新技术与航空发动机关重件疲劳寿命研究的融合,将为提升航空发动机关重件疲劳试验的功能、效率和精度提供新的技术途径。 非接触式状态测试技术 随着疲劳试验需求的不断增加,疲劳损伤的监测和分析逐渐向微观、局部和高精度方向发展。虽然传统的接触式测试技术已经历了长时间的发展与优化,但仍存在固有局限,如干涉问题、灵敏度问题和精度问题等。 随着现代测试技术的发展,非接触式测试技术逐渐崭露头角,为工程试验提供了更为高效、准确且灵活的测试手段。非接触式状态测试技术是指在不直接接触被测对象的情况下,通过利用各种物理信号(如光、热、声、磁等)和先进的传感与数据处理技术,实现对目标状态进行实时监测、分析和评估的测试方法。 相较于传统的接触式测试技术,非接触式状态测试技术具有避免因接触对被测对象产生损害和干扰、环境适应性强和获取数据丰富等优势。通过非接触式状态测试技术获取的精确且丰富的数据能够揭示更多的隐藏信息,从而为航空发动机关重件的设计、优化与维护提供更为深入的参考和支持。 Part.01 数字图像相关技术 数字图像相关技术(DIC技术)是近年来发展起来的一种用于测量全域变形和应变的非干涉、非接触式精密光测力学技术,通过计算变形前后被测试件散斑表面数字图像中的灰度信息来跟踪图像中各点的位置变化,获得被测物体表面的位移场和应变场,可以用于表征结构的疲劳损伤过程。 目前DIC技术在疲劳试验中的应用多集中于疲劳裂纹扩展试验,在试验件的变形测试中展现出了较好的效果。王儒文等应用DIC技术测试不锈钢CT试样典型测量点的相对位移(如图17所示),获得了张开载荷随裂纹长度及应力强度因子的变化关系。 图17 DIC非接触光学测量系统 图18 谐振疲劳短裂纹显微图像采集系统 Part.02 红外测试技术 红外测试技术是一种通过捕捉物体发出的红外辐射来测量其表面温度的非接触式测温技术,具有测试效率高、无接触和无损伤的优点。疲劳过程中产生的能量耗散会导致材料表面发生非均匀温度场变化。红外测试技术能够实时监测试件表面温度场的变化,为疲劳过程研究提供了新的方法和思路。 疲劳过程中,绝大部分累积的塑性功以热量的形式释放出来,热量通过对流、辐射的方式和外界发生交换,同时由于热传导的作用,在材料的内部形成温度场。由热耗散引起的温度场的变化是材料形变过程中能量耗散的标志和度量,因此对温度进行精确测量是研究疲劳过程能量耗散现象的试验基础。 一些学者基于红外测试技术和能量耗散理论,研究材料和结构在疲劳损伤演化过程中的表面温度信号、应力状态和固有耗散等损伤参量的变化规律,实现了对材料和结构疲劳性能参数的快速预测和应力状态评估。夏哲等采用红外高温仪对LY12CZ合金试样在疲劳试验中的温度场进行了测量,据此研究了该材料疲劳试验的热耗散性能。樊俊铃等将固有耗散量和温度信号的变化量作为疲劳损伤参量,建立了疲劳损伤演化状态评估及疲劳极限快速预测方法,为评估热处理工艺对材料疲劳性能的影响提供了新的思路。 研究表明,疲劳裂纹萌生和扩展行为会导致试样表面热量非均匀分布。基于此现象,Dominik等将红外热成像技术应用于铝合金材料的超声疲劳试验中,探究了铝合金材料的温度与裂纹扩展路径/速率的关系。Szymanik等对钢结构的裂纹扩展过程进行监测,取得了较好的效果。 近年来,一些学者将红外测试技术应用于航空发动机关重件的疲劳试验中,避免了应用传统热电偶测温技术在测试航空发动机关重件温度时存在的检测效率低、直观性差、环境适应性差等问题,取得了较好的测试效果。 Furuya等将红外测试技术应用于涡轮叶片的高温疲劳试验(如图22所示),有效地获取了涡轮叶片的瞬态温度场。苏清风等开展了超声红外热像技术原理及试验研究,搭建了超声红外热像检测试验平台,实现了对航空发动机叶片裂纹的有效检测。 Part.03 声发射技术 声发射又称应力波发射,是指材料或物体因内部应力超过屈服极限而进入不可逆的塑性变形阶段或有裂纹形成和扩展、断裂时快速释放出应变能而产生瞬态应力波的现象。声发射技术是用仪器检测、记录、分析声发射信号并利用声发射信号推断声发射源的技术,可以有效地检测材料内部的微观变化过程。当物体内部出现各种不稳定因素,例如裂纹扩展和断裂时,物体本身会发出声波,声发射技术正是基于这一原理,利用换能器直接接收来自被检物体内部声源发出的超声波以判断物体的状态。 目前声发射技术在疲劳试验中的应用多集中于飞机整机及其关键部件的试验。在试验全过程实施无损监测,发现早期裂纹,通过早期预防性维修或者耐久性修理恢复试验飞机的结构完整性,为延长飞机寿命提供科学决策,同时也为飞机(机群)疲劳定寿、确定修理周期、修理方式和未来飞机疲劳细节设计改进提供依据。 耿荣生等首次提出了一种基于声发射监测的裂纹综合无损检测技术,成功监测和预报了两种三代机机群的关键裂纹,在三代机机群的定寿、延寿试验中起到了重要保障和技术支撑作用。崔建国等提出了一种基于声发射技术的飞机水平尾翼裂纹监测方法,可以准确地识别并诊断出飞机水平尾翼的疲劳裂纹。 一些学者将声发射技术用于航空发动机关重件的裂纹检测,杨国安等提出了一种基于声发射技术的叶片裂纹源定位方法,结合VMD相对熵算法和AIC算法实现了叶片故障源区域定位。张瑞琪等应用声发射技术捕捉了压气机叶片的疲劳损伤信号,提出了基于声发射技术的叶片疲劳裂纹扩展寿命预测方法。 Part.04 原位测试技术 传统的疲劳测试技术已经较为成熟,能够基本满足材料强度和疲劳性能等宏观力学性能测试的需求,但其测试原理一般为离位测试,仅能对试件表面及破坏后的断口疲劳行为进行观测,不能对试件在测试过程中的微观组织形貌进行实时动态观测,因此无法获得材料微观组织变化机理与宏观力学性能之间的关联,限制了材料强度及性能研究的进展。 原位测试技术通常指在一个系统、组件或材料的实际工作环境中进行的测试,在强度试验中多指在试验过程中进行的试件表面微观形貌和内部结构状态的动态测试。随着现代测试技术和计算机分析技术的不断发展,具有原位测试技术的试验装置不仅能获得各类材料的力学性能参数,还可以借助数字图像技术、电子显微镜成像技术、红外成像技术等手段,实现从试件表层形貌到其内部结构缺陷等多方面动态监测与分析。 目前国内对于原位测试技术在疲劳试验方面的应用多集中于材料级疲劳试验,并自主研发了多种原位测试装置。近年来,吉林大学在应用原位测试技术测试材料疲劳性能的方面展开了一系列研究,设计了多种用于材料疲劳试验的原位测试装置(如图23、24所示),能够对拉伸、压缩、扭转、弯曲载荷单一作用及复合作用情况下的试验件进行原位测试,为研究材料在多载荷加载和多物理场耦合加载条件下的微观组织形貌、力学性能演变和宏观力学之间的联系提供了有效的手段。 同步辐射光具有亮度高、准直性好、光谱连续、分辨率高等一系列优异特性,能够在亚微米空间和皮秒时间尺度上准确捕捉裂纹的内部缺陷,比工业CT的试验水平高出几个数量级。基于同步辐射光的原位测试装置是目前唯一可穿透大块金属材料开展疲劳损伤演变原位研究的大科学装置。 基于同步辐射光源技术,西南交通大学牵引动力国家重点实验室的吴圣川团队开创性地搭建了集材料力学和疲劳性能研究为一体的功能集成型原位疲劳试验系统(如图25所示),该系统可以根据用户不同需求开展原位拉伸、原位低周疲劳、原位高周疲劳及原位超高周疲劳实验。针对高温下材料内部疲劳损伤的原位表征与测量问题,该团队基于先进光源平台开展了系统的原位加载装置研发工作,率先研制出含温控单元的原位拉伸和疲劳材料试验系统,并在国内首次对激光增材制造铝合金开展了高应力比加载条件下内部缺陷导致的高温低周疲劳响应研究。 图26 原位同步加速器UFT系统 数字孪生技术 随着信息技术水平的提高和数据处理能力的飞跃,将各种物理实体数字化已是大势所趋,这一趋势催生出的代表技术之一就是数字孪生(Digital Twin)。通俗来讲,数字孪生是以数字化的形式对某一物理实体在全生命周期内的行为进行的动态呈现。 数字孪生概念的产生和发展在过去很长一段时间都集中在航空航天领域,特别是利用数字孪生技术对飞行器进行故障/寿命预测和健康管理。2010年美国国家航空航天局在太空技术路线图中首次引入数字孪生概念,并采用数字孪生实现飞行系统的全面诊断和预测功能,具有里程碑意义。 NASA和美国空军联合提出面向未来飞行器的数字孪生范例,并将数字孪生定义为一个集成了多物理场、多尺度、概率性的仿真过程,基于飞行器的物理模型和实时更新技术,实现了飞行器健康状态、剩余使用寿命以及任务可达性的预测。 2011年美国空军研究实验室将数字孪生技术用于飞机结构寿命预测的概念模型,结合历史飞行监测数据进行虚拟飞行,以确保其适航性和安全性,增加飞机可用性。 数字孪生技术更加强调分析模型应具有自我学习和进化的能力,使其可以更真实地反映结构物理实体损伤状态的演化过程,这也是数字孪生技术在健康管理领域应用的一大特点。 目前,国外数字孪生技术已经广泛应用于机械装备的全寿命周期健康管理中,为保证机械装备的长时间、高效、安全运行提供了有力的技术支撑。Allemang和Zuchowski开发了基于飞机机体数字孪生体的虚拟仿真技术。Daniel等建立了一种增材制造涡轮叶片的数字孪生分析模型,通过实时应变测试对叶片数字孪生模型进行动态更新,结合数值模拟方式有效预测了叶片的剩余使用寿命。 一些学者将不确定性因素引入数字孪生模型,Karve等提出了一种不确定条件下容损任务规划的数字孪生方法,将损伤诊断、损伤预测和任务优化融入到数字孪生模型中,以预测单个或多个疲劳载荷所导致的结构疲劳裂纹扩展过程,从而对结构部件的服役任务及维修策略进行指导和优化。 相比于国外,国内数字孪生技术起步略晚。工信部《数字孪生白皮书》认为,数字孪生及其相关技术的发展以2017年为分界点。在此之前,数字孪生处于萌芽积累阶段,在此之后,国内学者开始活跃在数字孪生相关研究中,除了进一步探讨数字孪生概念外,还尝试建立各领域公认的数字孪生定义以及各学科统一的数字孪生模型,学术界、工业界和疲劳分析领域开始了广泛的数字孪生应用研究。 目前,国内对于疲劳试验的数字孪生技术研究工作多围绕于基于传感器数据的数字孪生模型修正与基于数字孪生模型的疲劳寿命预测。张显程等提出了一种基于数字孪生的高温承压氢混原位蠕变疲劳试验系统,将传感器和数据采集系统与数字孪生平台连接,通过数字孪生平台实时监测试验环境、映射试验状态、控制系统安全运维,实现了高温氢混环境下材料原位蠕变疲劳性能测试。宋学官等提出了一种基于结构应力法的焊缝疲劳数字孪生框架,为焊缝结构的疲劳实时监测研究提供了指导。目前国内关于数字孪生技术的研究大多停留在理论层面,相比于国外数字孪生技术在飞机产品的应用深度及广度都还存在一定差距。 小样本试验数据统计分析技术 Part.01 参数估计方法 参数估计是可靠性工程中的一项重要技术,其目标是根据样本数据,使用统计方法对总体分布的参数进行估计。参数估计的精度直接关系到航空发动机关重件的寿命和可靠度等关键指标的精度,对于航空发动机的设计、生产和维护具有重要意义。特别是在面对小样本的情况时,如何准确地估计分布参数成为了可靠性领域中的一个重要难题。 威布尔分布是描述机械零部件疲劳寿命最合理的分布,由于三参数威布尔模型较两参数威布尔分布模型更能反映实际情况,可靠性研究中大量的试验数据采用三参数威布尔分布进行建模分析。应用三参数威布尔分布能更准确地描述结构疲劳寿命,在机械零部件疲劳、磨损寿命评价中具有广泛的应用。研究表明,三参数威布尔分布可以更好地描述轴承和齿轮的疲劳寿命分布。然而,如何准确地估计三参数威布尔分布参数,特别是在样本量不大的情况下,是一项具有挑战性的任务。 国内外学者对威布尔分布的参数估计方法进行了大量的研究,提出了一些参数估计的方法。目前较为常见的参数估计方法有极大似然法、最小二乘法、统计量方法和贝叶斯方法等。一些学者对常用的威布尔分布参数估计方法进行了系统地分析和比较,阐明了由不同方法估计的参数之间存在的显著差异。极大似然法和最小二乘法是参数估计中最常用的方法,一些学者基于这两种方法开发了多种参数估计方法。然而,这些方法在解决非线性、非正则问题时,其估计结果的准确性和稳健性仍有待提高,尤其是在样本量不足够大的情况下。 Part.02 P-S-N曲线拟合方法 P-S-N曲线,即存活率-应力-寿命曲线,在疲劳可靠性领域中扮演着重要的角色。它描述了材料或结构在一定应力水平下的疲劳寿命与可靠性之间的关系,是评估材料或结构在实际工作条件下的疲劳性能的基础。 长期以来,P-S-N曲线拟合方法一直得到统计学者和疲劳研究者的关注。由于疲劳试验耗时长、成本高,一般情况下很少能得到满足传统统计方法要求的大样本数据。Bayes统计方法是较为常用的小样本P-S-N曲线拟合方法,一些学者研究了Bayes方法在小子样疲劳寿命估计中的应用,提出了在对数正态分布条件下的疲劳寿命曲线线性回归分析技术。 但在样本量很小时,如何合理地确定先验分布仍然是一个难题。一些学者致力于通过改进大样本统计方法,使之尽可能适用于小样本问题。此外,还有研究者提出了基于Bootstrap抽样估计P-S-N曲线的小样本方法,以及建立在经典极大似然法Langer模型基础上的三参数P-S-N曲线拟合方法。还有学者应用经典的疲劳理论和数理统计原理,提出了快速或简化的试验方案。金属材料疲劳试验数据统计方案与分析方法国家标准也推荐了可用于处理小样本试验数据的方法。 综上所述,虽然目前P-S-N曲线拟合方法研究已经取得了一些成果,但这些分析方法都有其应用局限性。Bayes统计方法需要合理设定先验分布,这在实际应用中可能存在一定挑战;加权最小二乘法在处理复杂问题时需要更多的调参和优化;Bootstrap抽样方法在计算复杂度和稳定性方面仍有提升空间。由于数学计算繁琐或及稳定性差等原因,目前还没有能很好满足工程应用的方法。 在给定应力条件下,产品寿命完全是由其性能决定的。基于此原则,谢里阳等提出了一种基于“寿命概率分位点一致性原理”的样本聚集方法。对于性能处于其母体性能分布某一分位点的样品,在任何应力水平下的寿命都将处于对应于该应力水平的寿命母体分布的同一概率分位点上,即试验样品个体寿命在其母体寿命概率分布中的“概率分位点”不受应力水平的影响。据此,可以把不同应力水平下的寿命试验数据转换到某一个指定的应力水平上,在该应力水平上形成样本聚集和信息融合效应,形成“等效大样本”数据,进而可以提高寿命概率分布参数估计精度。根据此原理,可以设计出基于小样本试验数据的P-S-N曲线试验方案,用较少的样品试验数据做出精度较高的P-S-N曲线。样本聚集方法实现了不同应力水平上寿命分布信息的共享,有效提高了数据信息利用率,已经在工程中得到了广泛推广和应用。 总结与展望 目前航空发动机关重件疲劳试验技术尚处于发展阶段,仍有很多环节亟待进一步完善。通过梳理当前航机关重件疲劳试验技术和疲劳试验新技术的研究进展,笔者认为以下几个方面将是未来航空发动机关重件疲劳试验技术的重要发展方向: 高精度高效率的疲劳损伤测试技术 随着现代测试技术的不断进步,未来的航机关重件疲劳损伤测试技术将向更为精确、高效的方向发展。多种测试技术的综合应用将进一步提高测试技术的监测能力和应用范围,为新的航空材料及结构的疲劳机理研究提供更有力的支撑。如何将非接触式测试技术应用于航机关重件的疲劳试验中将是未来航机疲劳领域重点关注与研究的方向。 数据驱动的部件级原位试验技术 部件级疲劳试验能够反映材料级疲劳试验无法体现的结构表面状态、局部几何状态、尺寸效应等因素,可以实现更为准确的疲劳试验评估。基于原位测试技术的部件级疲劳试验技术研究将是未来航机关重件疲劳试验研究的重点。在获得更为全面的特征及性能信息的同时,原位测试过程中也会产生海量且复杂的数据,依靠传统的数据分析手段难以挖掘出材料特征与疲劳性能的深层联系,无法满足航机关重件的高精度疲劳寿命分析需求。因此,以大数据为基础,机器学习为核心的数据驱动方法是推动航机关重件原位疲劳试验研究进程的重要手段。 数字孪生赋能的虚拟疲劳试验技术 目前基于数字孪生技术的疲劳寿命预测研究已经取得了一些成果,保障了一定时期的研究工作需要,但还远不能满足当前航空发动机健康管理领域的发展需求。仿真分析技术是数字孪生技术的关键环节,精确、高效的仿真分析模型是实现数字孪生体对物理实体精确映射的关键。因此,建立高精度的数字仿真分析模型,特别是多载荷、多物理场混合仿真模型,以及高效率的仿真求解方法,是未来航机关重件虚拟疲劳试验技术研究的重点。另外,受限于疲劳测试数据特点,现有的数字孪生模型多以受载测试数据作为模型更新数据,鲜有以损伤表征数据作为反馈数据的研究,在模型个性化表征方面的研究深度仍有待进一步提升。 智能稳健的小样本试验数据统计分析技术 由于试验条件及成本限制,航机关重件的试验数据多为小样本数据,现有的试验数据统计分析方法在小样本场合下面临着精度低和适用性不足的问题。因此,应进一步发展基于小样本试验的试验方案和数据统计分析方法,开发更为稳健的小样本数据统计分析技术。此外,未来的试验数据统计分析技术应朝着智能化的方向发展,例如开发智能算法,减少用户的参数设定和调整;融合深度学习技术,挖掘数据潜在规律,有效地处理非线性问题和样本不确定性等问题。
免责声明:本网站所转载的文字、图片与视频资料版权归原创作者所有,如果涉及侵权,请第一时间联系本网删除。
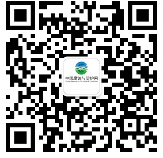
官方微信
《腐蚀与防护网电子期刊》征订启事
- 投稿联系:编辑部
- 电话:010-62316606
- 邮箱:fsfhzy666@163.com
- 腐蚀与防护网官方QQ群:140808414