腐蚀是材料在环境的作用下引起的破坏或变质。金属和合金的腐蚀主要是化学或电化学作用引起的破坏。 金属腐蚀现象或所谓的耐腐蚀性是根据腐蚀性介质的种类、浓度、温度、压力、流速等环境条件,以及金属本身的性质,即含有成分、加工性、热处理等诸因素的差异而分别有不同的腐蚀状态和腐蚀速度。 例如不锈钢具有优良的耐腐蚀性能,可是因为使用条件或腐蚀环境的不同,也可能发生意想不到的腐蚀事故。因此,应充分地了解腐蚀介质和耐腐蚀材料,才能选择合适的耐腐蚀用材料。 对于非金属来说,一般是由化学、物理的作用(如氧化、溶解、溶胀等)引起的腐蚀。金属腐蚀的形态可划分为两大类,但各种形态互相关联,往往实际的腐蚀可能同时包括几种形态。 如表1-4-7所示。腐蚀在金属的全部或大部面积上进行,而且生成腐蚀产物膜,称为全面成膜腐蚀,具有保护性;无膜的全面腐蚀是很危险的,因为它保持一定速度全面进行。一般对均腐蚀的程度用腐蚀率表示。但如何评价则有不同的规定。
按《石油化工管道设计器材选用通则》(SH3059-2001)规定,介质对金属材料的腐蚀速率,管道金属材料的耐腐蚀能力可分为下列四类: 年腐蚀速率不超过0.05mm的材料为充分耐腐蚀材料; 年腐蚀速率在0.05~0.1mm的材料为耐腐蚀性材料; 年腐蚀速率0.1~0.5mm的材料为尚耐腐蚀性材料; 年腐蚀速率超过0.5mm的材料为不耐腐蚀材料。 一般应选择耐腐蚀性和尚耐腐蚀性的材料。当介质对某种金属材料的年腐蚀速率大于0.5mm 时,应经技术、经济比较,确定更换材料或增加腐蚀裕量;当介质对某种金属的年腐蚀速率不超过0.05mm时,应采用常规材料和低限腐蚀裕量。 《腐蚀数据手册》对均匀(全面)腐蚀的耐蚀性用均匀腐蚀率来评价,如表1-4-8所示。
(中国腐蚀与防护学会)的规定如表1-4-9所示。《金属防腐蚀手册》
日本《配管》《装置用配管材料及其选定法》的规定如表1-4-10所示。
1、均匀(全面)腐蚀 全面腐蚀是由于空气中的氧或其他条件在金属表面进行全面腐蚀而产生可溶性盐随着时间的延长,壁厚则减少。一般将不锈钢作为耐全面腐蚀的材料但是它的适用范围有限,必须了解不锈钢对环境的耐腐蚀性能。 上述是全面腐蚀的概要。此外,也有因溶液的流速、涡流、温度、压力、振动等附加条件而引起局部腐蚀的情况,详见局部腐蚀的叙述。 2、局部腐蚀 据调查,在化工装置中,局部腐蚀约占70%,而且一些局部腐蚀常常是突发性和灾难性的,可能引起各类事故。因此,在选材或结构设计时,对局部腐蚀应格外注意。 晶间腐蚀 腐蚀从表面沿品界深入内部,外表看不出腐蚀迹象。晶间腐蚀是由于晶界沉积了杂质或某一元素增多或减少而引起的。以奥氏体不锈钢为例,它在焊接时焊缝两侧2~3mm 处可被加热至400~910℃,这时晶界的铬和碳化合为Cr23C6,从固溶体中析出,由于铬的流动很慢,不易从晶内扩散到品晶界,因此形成贫铬区,在适合的腐蚀溶液中,就形成“碳化铭(阴极)一贫铬区(阳极)”电池,使晶界贫铬区产生腐蚀。 奥氏体不锈钢晶间腐蚀,有三种常用的控制方法: a.热处理,将材料加热至1100℃,随即水淬,即固溶火处理。因在1100℃时碳化铭被溶解,可得到均一的合金; b.加人与碳素的亲合力比铬更强的元素,如Ti和Nb; c.将碳含量降低到0.03%以下,产生的碳化铬量少,就不致引起晶间腐蚀。因此,当使用低碳奥氏体系不锈钢管即稳定化的奥氏体系不锈钢管以外的奥氏体不锈钢管时,由于加工或焊接要加热至碳化物析出的温度,应在最终温度1000~1100℃时急冷,使析出的碳化物固溶,是非常必要的。 当稳定化奥氏体不锈钢管用于浓硝酸等严重的产生品间腐蚀的环境,焊接后原封不动将会引起晶间腐蚀的特殊形态的腐蚀(Knife line attack)。为此,应在840~900℃进行2~4h稳定化处理,使Ti或NbC 充分的析出。 当使用铁素体不锈钢时,于925°以上的温度急冷,在腐蚀环境会产生品间腐蚀,应当注意。 应力腐蚀 金属和合金在腐蚀与应力的同时作用下产生的腐蚀。它只发生于一些特定的“材料一环境”体系,例如“奥氏体不锈钢-Cl-”,“碳钢-NO3”等,当然还必须存在应力(外力或焊接、冷加工等产生的残余应力)。 在“奥氏体不锈钢-Cl-”体系中,溶液中氧的存在是促进全面钝化,而Cl破坏局部钝化,同时进入裂缝尖端,构成盐酸,使腐蚀加速。 一般应力腐蚀的裂纹形态有两种,一种是沿晶界发展,称为晶间破裂;另一种是穿过晶粒,称为穿晶破裂;也有混合型,如主缝为品间型,支缝为穿晶型。 防止应力腐蚀方法,一般通过热处理消除或减少应力;设计中取低于临界应力腐蚀破裂强度值;改进设计结构,避免应力集中;表面施加压应力;采用电化学保护、涂料或缓蚀剂等。 对于奥氏体系不锈钢,腐蚀介质浓度高则易产生裂纹,可是尽管在很稀薄的场所,由于吸收或在高温、高压下局部浓缩,致使局部浓度增高,所以必须规定腐蚀介质浓度的下限值;腐蚀性介质的温度影响极大,尽管其他条件不变,温度高时易于产生裂纹。在沸腾或蒸发温度条件下是易于产生裂纹的苛刻条件。一般在50~60℃时是没有问题的;产生裂纹敏感性大的元素Ni,在8%左右最易产生裂纹,45%以上则不产生裂纹。 缝隙腐蚀 这类腐蚀发生在缝隙内,如焊、铆缝、垫片或沉积物下面,由于滞留的液体构成氧素“浓淡电池”、金属离子“浓淡电池”而产生腐蚀。像不锈钢那样,存在耐蚀性钝态的金属,对缝隙腐蚀则敏感。 缝隙腐蚀的破坏形态为沟缝状,严重的可穿透,是孔蚀的一种特殊形态。缝腐蚀和孔蚀一样,在含Cl-的溶液中最易发生,而且发生之前通常有一个较长的孕育期,一旦发生就迅速进展。防止缝隙腐蚀的最有效的办法是消除缝隙。 孔蚀 孔蚀是一种高度局部的腐蚀形态,孔有大有小,孔径或宽度约为深度的4~10倍,小而深的孔可能使金属板穿透,引起物料流尖、火灾、爆炸等事故,它是破坏性和隐患最大的腐蚀形态之一。 孔蚀通常发生在表面钝化膜或有保护膜的金属,如不锈钢、钛、铝合金等。由于金属表面缺陷或有非金属夹杂物等和溶液内存在能破坏钝化膜的活性离子如Cl-、Br-等,钝化膜在局部微小的膜破口处的金属成为阳极,其电流高度集中,破口周围大面积膜成为阴极,因此腐蚀迅速向内发展,形成蚀孔。 影响孔蚀的因素有环境因素和金属因素之分。 环境因素:Cl-、Br-等卤族元素离子或硫氰盐离子与氧或氧化性金属离子等在适当的氧化剂存在时会产生孔蚀。当溶液的PH值在3以上中性附近时最易产生孔蚀,PH值增大的碱侧则不易发生。通常,当温度上升时孔蚀增加,液体流动则孔蚀减少。由于介质的流动将除去固形物的沉积,对保持钝化膜是有利的。所以流速>1.5m/s、管系没有死角是防止管系产生孔蚀的必要条件。 金属侧因素,不锈钢中的Cr、Ni、Mo、Si、Cu、N等元素含量的增加,将减少孔蚀。但含C量多则易发生孔蚀。 腐蚀疲劳 腐蚀疲劳是由交变应力和腐蚀的共同作用引起的破裂。当铁基合金所承受的交变应力低于一定数值时,可经过无限周期而不产生疲劳破裂,这个临界应力值称为疲劳极限,对于其他合金,疲劳极限为在一定周期下不破裂的最大交变应力。在腐蚀环境中疲劳极限值大大下降,因而在不高的交变应力下就很容易发生腐蚀疲劳。 腐蚀疲劳的特征是:有许多溶蚀孔,裂缝通过蚀孔,可有若干条,方向与应力垂直是典型的穿晶型(在低频率周期应力下,也有晶间型),没有分支裂缝,缝边呈现锯齿形。振动部件,由于温度变化产生周期热应力的换热器管和锅炉管等都易产生腐蚀疲劳。
氢腐蚀 氢腐蚀有低温型和高温型。低温型是在有水溶液的情况下发生的,被认为是电化学腐蚀。金属电化学反应生成的原子氢渗透到金属内,然后结合为分子,形成鼓泡。这就是低温氢腐蚀。 在产生氢鼓泡的腐蚀环境中,通常含有硫化物、砷化合物、化物、含磷离子等毒素阻止了放氢反应(H+H→H2),石油化工生产流体中常含有这类毒素。因此在石油化工工业中氢鼓泡是一个重要问题。消除这类毒素是有效的防氢鼓泡的方法。 也可选用没有空穴的镇静钢代替有许多空穴的沸腾钢,采用对氢渗透低的奥氏体不锈钢或镍的衬里层,或橡胶、塑料保护层、瓷砖衬里和加人缓蚀剂等。 高温型氢腐蚀是高温氢侵入低碳钢内,在无水溶液的情况下进行,与低温氢腐蚀有本质上的不同。高温氢分子扩散到钢的内部会产生氢脆和氢蚀。所谓氢脆,是在高温、高压下分子氢部分分解变成原子氢,或者是氢气在湿的腐蚀性气体中经过电化学反应而生成氢原子这些氢原子渗透到钢里之后,使钢材晶粒间的原子结合力降低,造成钢材的延伸率、断面收缩率降低,强度也出现变化,这种现象叫氢脆。 所谓氢蚀是钢材长期与高温、高压氢气接触之后,氢原子或分子通过晶格和晶间而向钢内扩散,这些氢与钢中的碳化物(渗碳体)发生化学反应生成甲烷(Fe,C+2H,--3Fe+CH。),即钢材的内部脱碳。甲烷气体不能从钢中扩散出去,而聚积在品间形成局部高压,造成应力集中,晶间变宽,致使产生微小裂纹或起泡。开始时,裂纹微小,但时间久后,无数裂纹相连,使钢材的强度及韧性下降失去原有塑性变脆,这就叫氢蚀。氢脆是一次脆化,是可逆现象。而氢蚀是永久的脆化,是不可逆的。 钢材在高温高压下的氢蚀破坏是有一段潜伏期的,超过潜伏期则产生裂纹并降低强度和韧性。潜伏期的长短,根据不同的钢种、受腐蚀的程度、温度、压力、冷变形程度等因素而异。在极苛刻的条件下,潜伏期仅几小时,潜伏期的长短将决定钢材在临氢工况下安全使用的年限。 对于耐高温高压氢气的材料选择,一般均以纳尔逊(NELSON)曲线为准,例如美国埃索(ESSO)标准规定,选择临氢材料必须执行NELSON曲线。在法国、意大利、日本等的多数工程公司的临氢管道材料选用标准,基本上也是以NELSON曲线为基础而编制的。我国的抗氢材料选择的依据也是NELSON曲线。如图1-4-3所示。 图中上部的虚线表示钢材与氢接触后表面有脱碳倾向。图中实线表示钢材内部脱碳。产生甲烷而开裂的倾向。所谓表面脱碳,是气体中有氢或氧存在时,钢材表面的碳与氢反应生成甲烷或与氧反应生成一氧化碳等含碳的气体,结果形成表面脱碳。通常表面脱碳的结果可使钢材的强度及硬度稍为降低,并不产生龟裂。
图中实曲线的上边是内部脱碳产生裂纹而破坏的范围。实曲线的下边和左边是碳钢和各种合金钢耐氢腐蚀的使用范围。 在曲线上标注的材料是选择所需最小合金含量,并非为标准合金。在埃索标准上并规定当温度和氢分压落在图1-4-3(a)所示任一曲线上时,则应选用更高一条曲线所示的所需最小合金含量。 据资料介绍,在稍高于0.7MPa的压力下,经过长期和氢接触的碳素钢管焊接部位有蚀的情况。一根煨弯的弯管,氢蚀集中在受过热的弯头部位,而未加热的直管段未受氢蚀。奥氏体不锈钢在所有温度、压力下都耐氢蚀。图1-4-3(a)的横座标分压仅以气相为基准,氢分压等于气相中氢分子分数乘系统总压力。 图中曲线的绘制是对铸钢、退火钢和正火钢进行应力评价而得出的。 纳尔逊曲线是1967年由纳尔逊绘制的,再版权授与了API。纳尔逊曲线在1969年1977年、1983年和1996年曾进行了修改,本图是2004年API出版物941中的纳尔逊曲线,即临氢作业用钢防止脱碳和裂纹的操作极限,它是截至目前最新的版本,将高温临氢作业用Cr-0.5Mo和1.25Cr-0.5Mo钢使用经验另绘图,如图1-4-3(b)所示。 一般抗氢蚀钢管,不仅要满足常温时对强度、延性及韧性的要求还要满足高温机械性能的要求;不仅要满足在交货状态时对机械性能的要求,还要考虑在使用时的性能退化(如回火脆性、石墨化)等因素。例如对催化重整装置中设计温度540℃、氢分压1.25MPa的工艺管道,从NELSON曲线中,可选用1.25Cr-0.5Mo合金管,不必选用5.0Cr-0.5Mo合金钢管。 表1-4-11是1.25Cr-0.5Mo及5.0Cr-0.5Mo钢管的力学性能数据。 1.25Cr-0.5Mo及5.0Cr-0.5Mo合金钢均属耐热钢,1.25Cr-0.5Mo是一种较经济的钢种,其价格约为5.0Cr -0.5Mo的1/2,有较高的蠕变强度,抗氧化温度593℃,在≤550℃时1.25Cr-0.5Mo钢最大许用应力均比5.0Cr-0.5Mo高。在≤550℃时1.25Cr-0.5Mo钢的高温短时拉伸强度不低于5.0Cr-0.5Mo钢,而塑性和延伸率基本相当。5.0Cr-0.5Mo钢抗腐蚀性能好,具有较高的蠕变断裂强度,抗氧化温度为648℃。 但是,在650℃范围内,1.25Cr-0.5Mo钢比5.0Cr-0.5Mo钢有较高的蠕变断裂强度。从NELSON曲线查得,当氢分压1.37MPa(200psi)和2.07MPa(300psi)条件下1.25Cr-0.5Mo钢的脱碳温度分别为600℃和590℃,完全满足目前催化重整反应部分操作条件(温度510~540℃、氢分压1.25MPa)。 1979年,日本压力容器研究委员会氢脆分会对日本催化装置高温氢蚀情况进行了总结,认为那些氢蚀发生的条件在NELSON曲线相应钢种操作极限以下的情况中:很大一部分氢蚀发生在焊缝处。未经热处理焊缝的残余应力和高硬度的激冷组织,对氢蚀的敏感均比母材高,因而易在焊缝处发生氢蚀现象。 氢分子尤其氢原子,有很高的扩散率,在300℃时,铁晶格中的扩散率近14-4cm2/s。在高温时,由于氢分子的分解,焊接质量不高的焊缝处的气孔,不连续处和夹杂物,就成为氢和甲烷聚集的场所,由于甲烷不能向钢内部扩散,所以在内部形成高压,即在焊缝不够致密的地方造成裂纹或鼓泡。因此,焊缝和热影响区是抗氢蚀的薄弱部位。大多数情况下,氢蚀不发生在母材上而是在焊缝和热影响区。在选择和使用抗氢蚀钢时,要特别重视施工时的焊接质量,采用合适的焊接工艺,必要的焊前预热和焊后热处理。 生产实践和试验表明,Cr-Mo钢对焊接热作用相当敏感。对Cr-Mo钢进行焊接时热影响区会出现马氏体组织而产生明显的脆化。例如Cr-Mo钢母材的布氏硬度约为200,经焊接的热作用后希氏硬度增加至450以上。表征热影响区塑性的弯曲角由180°下降到不足 30°,这种脆化现象随Cr-Mo钢中Cr 含量的增加而增加。 5.0Cr-0.5Mo钢的脆化现象就比1.25Cr -0.5Mo钢更为严重。如果使用环境的分压偏高,将加剧脆化作用。为稳定和提高高温强度,增强耐蚀性,提高焊接区的延性和韧性,松弛焊接残余应力,确保焊接区的高温耐氢蚀性能,必须进行焊后热处理。各国标准中有关1.25Cr-0.5Mo及5.0Cr-0.5Mo钢焊前预热、层间温度、焊后热处理的规定如表1-4-12和表1-4-13 所示。
免责声明:本网站所转载的文字、图片与视频资料版权归原创作者所有,如果涉及侵权,请第一时间联系本网删除。
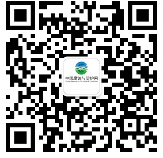
官方微信
《腐蚀与防护网电子期刊》征订启事
- 投稿联系:编辑部
- 电话:010-62316606
- 邮箱:fsfhzy666@163.com
- 腐蚀与防护网官方QQ群:140808414